Page 4169 of 4770
SF08N±03
S04740
EGR Gas Temperature
Sensor Connector EGR Gas Temperature
Sensor Bracket
Air Cleaner Hose Gasket
Throttle Body
Throttle Position
Sensor Connector
IAC Valve Connector
Water Bypass Hose
Air Assist Hose EGR Gas Temperature Sensor
Accelerator Cable
(A/T)
Throttle Cable
N´m (kgf´cm, ft´lbf): Specified torque
Non±reusable partWater Bypass Hose
19.5 (200, 14)
± SFI (1MZ±FE)EXHAUST GAS RECIRCULATION (EGR) GAS
TEMPERATURE SENSORSF±69
1568 Author: Date:
EXHAUST GAS RECIRCULATION (EGR) GAS
TEMPERATURE SENSOR
COMPONENTS
Page 4170 of 4770
SF08O±04
S04504
P03193
Oil
Ohmmeter SF±70
± SFI (1MZ±FE)EXHAUST GAS RECIRCULATION (EGR) GAS
TEMPERATURE SENSOR
1569 Author: Date:
INSPECTION
1. REMOVE THROTTLE BODY (See page SF±39)
2. REMOVE EGR GAS TEMPERATURE SENSOR
3. INSPECT EGR GAS TEMPERATURE SENSOR
Using an ohmmeter, measure the resistance between the ter-
minals.
Resistance:
At 50°C (122°F)64 ± 97 kW
At 100°C (212°F)11 ± 16 kW
At 150°C (302°F)2 ± 4 kW
If the resistance is not as specified, replace the sensor.
4. REINSTALL EGR GAS TEMPERATURE SENSOR
5. REINSTALL THROTTLE BODY (See page SF±41)
Page 4171 of 4770
S05042
Bank 1 Sensor 1
Bank 2 Sensor 1+B
HTOhmmeter
+B HTOhmmeter
SF08P±04
± SFI (1MZ±FE)HEATED OXYGEN SENSOR (Bank 1,2 Sensor 1)
SF±71
1570 Author: Date:
HEATED OXYGEN SENSOR (Bank
1,2 Sensor 1)
INSPECTION
Except California A/T:
INSPECT HEATER RESISTANCE OF HEATED OXYGEN
SENSORS (Bank 1 Sensor 1, Bank 2 Sensor 1)
(a) Disconnect the oxygen sensor connector.
(b) Using an ohmmeter, measure the resistance between the
terminals +B and HT.
Resistance:
At 20°C (68°F)11 ± 16 W
At 800°C (1,472°F)23 ± 32 W
If the resistance is not as specified, replace the sensor.
Torque: 44 N´m (450 kgf´cm, 32 ft´lbf)
(c) Reconnect the oxygen sensor connector.
Page 4172 of 4770
S05163
Ohmmeter
+B
HTSF08Q±03
SF±72
± SFI (1MZ±FE)HEATED OXYGEN SENSOR (Bank 1 Sensor 2)
1571 Author: Date:
HEATED OXYGEN SENSOR (Bank
1 Sensor 2)
INSPECTION
INSPECT HEATER RESISTANCE OF HEATED OXYGEN
SENSOR (Bank 1 Sensor 2)
(a) Remove the driver's seat.
(b) Take out the floor carpet.
(c) Disconnect the oxygen sensor connector.
(d) Using an ohmmeter, measure the resistance between the
terminals +B and HT.
Resistance:
At 20°C (68°F)11 ± 16 W
At 800°C (1,472°F)23 ± 32 W
If the resistance is not as specified, replace the sensor.
(e) Reconnect the oxygen sensor connector.
Torque: 44 N´m (450 kgf´cm, 32 ft´lbf)
(f) Reinstall the floor carpet.
(g) Reinstall the driver's seat.
Page 4173 of 4770
SF08R±03
S05450
ECM
ECM Connector
No.2 Instrument
Lower Panel
Under Cover
Cowl Side TrimFront Door Inside Scuff Plate
± SFI (1MZ±FE)ENGINE CONTROL MODULE (ECM)
SF±73
1572 Author: Date:
ENGINE CONTROL MODULE (ECM)
COMPONENTS
Page 4174 of 4770
SF08S±01
SF±74
± SFI (1MZ±FE)ENGINE CONTROL MODULE (ECM)
1573 Author: Date:
INSPECTION
1. REMOVE ECM
2. INSPECT ECM (See page DI±218)
3. REINSTALL ECM
Page 4175 of 4770
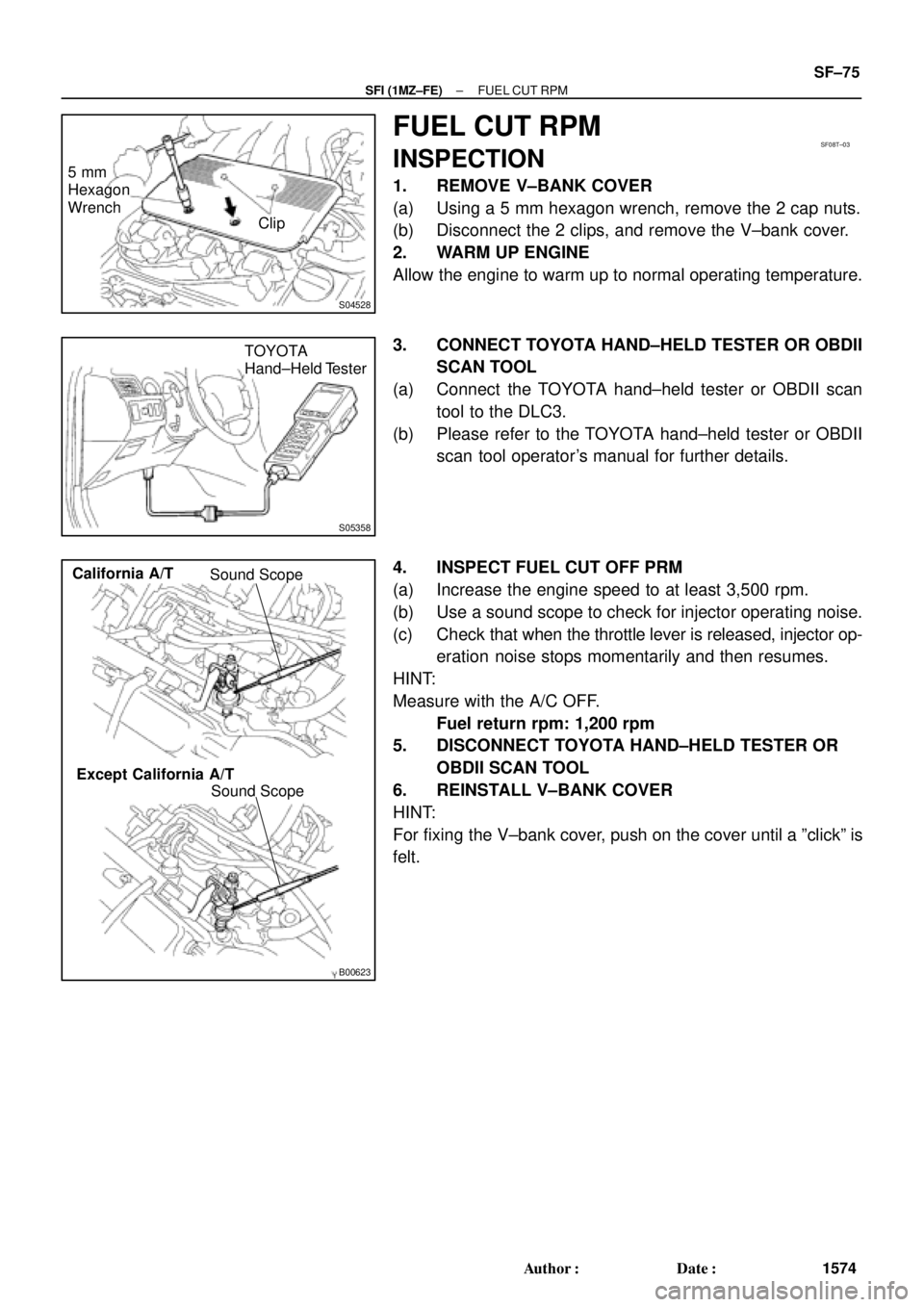
S04528
5 mm
Hexagon
Wrench
Clip
SF08T±03
S05358
TOYOTA
Hand±Held Tester
B00623
Sound Scope
Sound Scope California A/T
Except California A/T
± SFI (1MZ±FE)FUEL CUT RPM
SF±75
1574 Author: Date:
FUEL CUT RPM
INSPECTION
1. REMOVE V±BANK COVER
(a) Using a 5 mm hexagon wrench, remove the 2 cap nuts.
(b) Disconnect the 2 clips, and remove the V±bank cover.
2. WARM UP ENGINE
Allow the engine to warm up to normal operating temperature.
3. CONNECT TOYOTA HAND±HELD TESTER OR OBDII
SCAN TOOL
(a) Connect the TOYOTA hand±held tester or OBDII scan
tool to the DLC3.
(b) Please refer to the TOYOTA hand±held tester or OBDII
scan tool operator's manual for further details.
4. INSPECT FUEL CUT OFF PRM
(a) Increase the engine speed to at least 3,500 rpm.
(b) Use a sound scope to check for injector operating noise.
(c) Check that when the throttle lever is released, injector op-
eration noise stops momentarily and then resumes.
HINT:
Measure with the A/C OFF.
Fuel return rpm: 1,200 rpm
5. DISCONNECT TOYOTA HAND±HELD TESTER OR
OBDII SCAN TOOL
6. REINSTALL V±BANK COVER
HINT:
For fixing the V±bank cover, push on the cover until a ºclickº is
felt.
Page 4176 of 4770
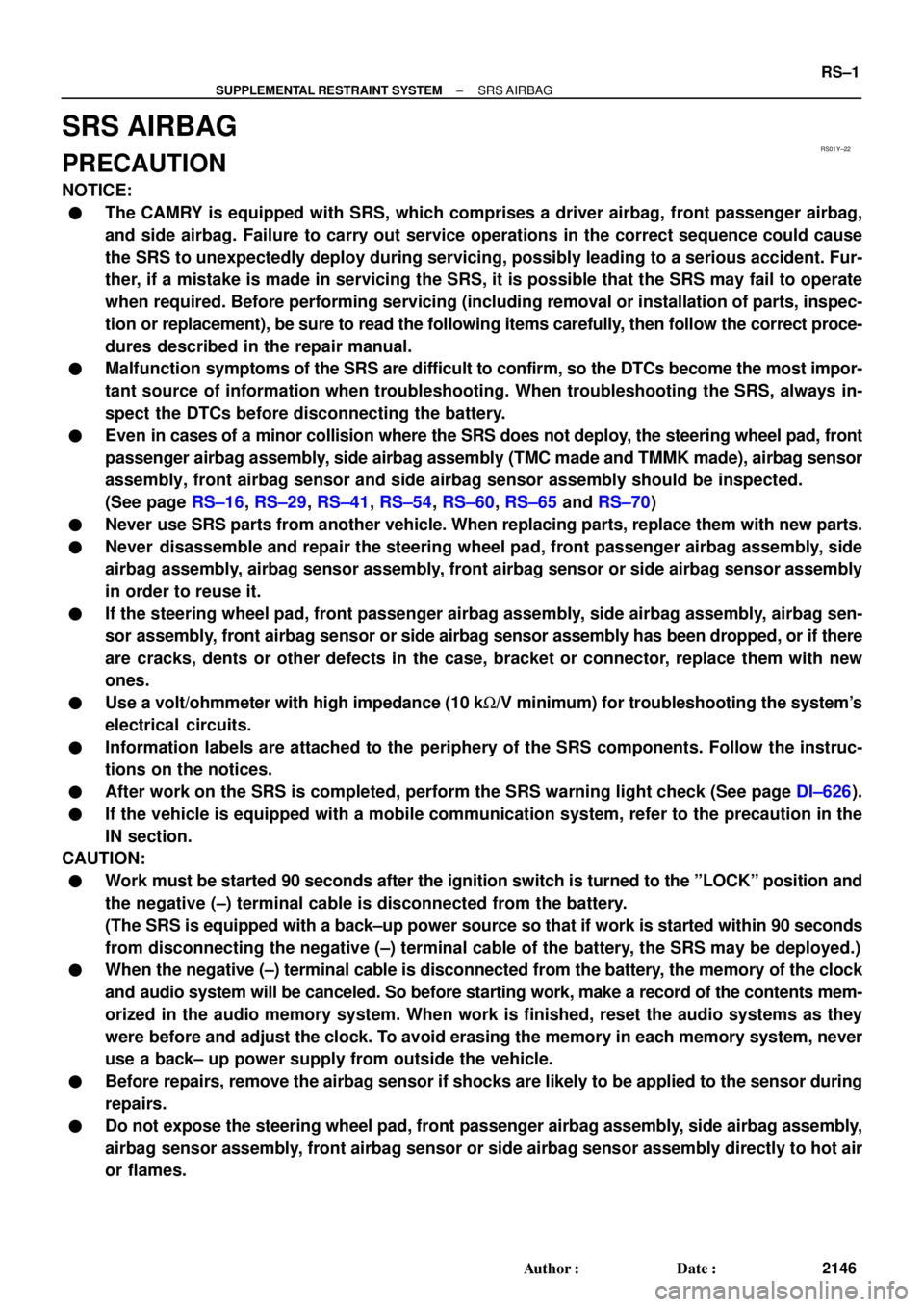
RS01Y±22
± SUPPLEMENTAL RESTRAINT SYSTEMSRS AIRBAG
RS±1
2146 Author: Date:
SRS AIRBAG
PRECAUTION
NOTICE:
The CAMRY is equipped with SRS, which comprises a driver airbag, front passenger airbag,
and side airbag. Failure to carry out service operations in the correct sequence could cause
the SRS to unexpectedly deploy during servicing, possibly leading to a serious accident. Fur-
ther, if a mistake is made in servicing the SRS, it is possible that the SRS may fail to operate
when required. Before performing servicing (including removal or installation of parts, inspec-
tion or replacement), be sure to read the following items carefully, then follow the correct proce-
dures described in the repair manual.
Malfunction symptoms of the SRS are difficult to confirm, so the DTCs become the most impor-
tant source of information when troubleshooting. When troubleshooting the SRS, always in-
spect the DTCs before disconnecting the battery.
Even in cases of a minor collision where the SRS does not deploy, the steering wheel pad, front
passenger airbag assembly, side airbag assembly (TMC made and TMMK made), airbag sensor
assembly, front airbag sensor and side airbag sensor assembly should be inspected.
(See page RS±16, RS±29, RS±41, RS±54, RS±60, RS±65 and RS±70)
Never use SRS parts from another vehicle. When replacing parts, replace them with new parts.
Never disassemble and repair the steering wheel pad, front passenger airbag assembly, side
airbag assembly, airbag sensor assembly, front airbag sensor or side airbag sensor assembly
in order to reuse it.
If the steering wheel pad, front passenger airbag assembly, side airbag assembly, airbag sen-
sor assembly, front airbag sensor or side airbag sensor assembly has been dropped, or if there
are cracks, dents or other defects in the case, bracket or connector, replace them with new
ones.
Use a volt/ohmmeter with high impedance (10 kW/V minimum) for troubleshooting the system's
electrical circuits.
Information labels are attached to the periphery of the SRS components. Follow the instruc-
tions on the notices.
After work on the SRS is completed, perform the SRS warning light check (See page DI±626).
If the vehicle is equipped with a mobile communication system, refer to the precaution in the
IN section.
CAUTION:
Work must be started 90 seconds after the ignition switch is turned to the ºLOCKº position and
the negative (±) terminal cable is disconnected from the battery.
(The SRS is equipped with a back±up power source so that if work is started within 90 seconds
from disconnecting the negative (±) terminal cable of the battery, the SRS may be deployed.)
When the negative (±) terminal cable is disconnected from the battery, the memory of the clock
and audio system will be canceled. So before starting work, make a record of the contents mem-
orized in the audio memory system. When work is finished, reset the audio systems as they
were before and adjust the clock. To avoid erasing the memory in each memory system, never
use a back± up power supply from outside the vehicle.
Before repairs, remove the airbag sensor if shocks are likely to be applied to the sensor during
repairs.
Do not expose the steering wheel pad, front passenger airbag assembly, side airbag assembly,
airbag sensor assembly, front airbag sensor or side airbag sensor assembly directly to hot air
or flames.