Page 2705 of 4770
FI6510FI6607A00113
KNK Signal Waveforms
0.5 V
/Division
5 msec./Division
100 msec./Division 0 V
200 mV
/Division
0 V
± DIAGNOSTICSENGINE (1MZ±FE)
DI±285
520 Author: Date:
Reference INSPECTION USING OSCILLOSCOPE
With the engine racing (4,000 rpm), measure between
terminals KNKR, KNKL of the ECM connector and body
ground.
HINT:
The correct waveforms are as shown.
Spread the time on the horizontal axis, and confirm that
period of the wave is 141 msec.
(Normal mode vibration frequency of knock sensor:
7.1 kHz)
HINT:
If normal mode vibration frequency is not 7.1 kHz, the sensor
is malfunctioning.
Type II Go to step 3 .
Type I
2 Check for open and short in harness and connector between EC1 connector and
ECM (See page IN±31).
NG Repair or replace harness or connector.
OK
Check and replace ECM (See page IN±31).
Page 2706 of 4770
DI±286
± DIAGNOSTICSENGINE (1MZ±FE)
521 Author: Date:
3 Check for open and short in harness and connector between EC1 connector and
knock sensor (See page IN±31).
HINT:
If DTC P0325 has changed to P0330, check the knock sensor circuit on the right bank side.
If DTC P0330 has changed to P0325, check the knock sensor circuit on the left bank side.
NG Repair or replace harness or connector.
OK
Replace knock sensor.
Page 2707 of 4770
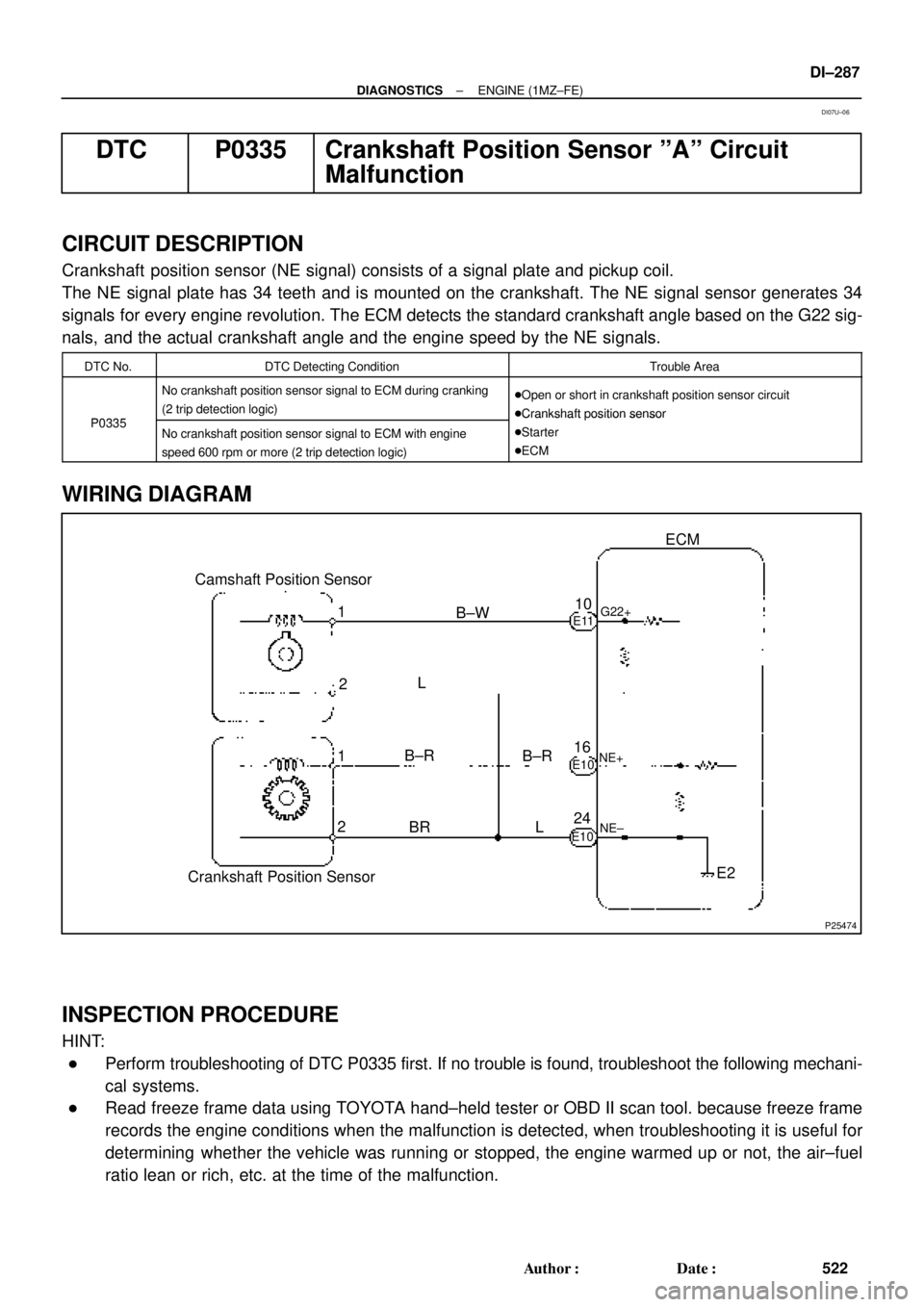
P25474
Camshaft Position Sensor
1
2
1
2B±W
B±RL
BR LECM
G22+
NE+
NE±
E2
E10
E10E11
2410
Crankshaft Position SensorB±R16
± DIAGNOSTICSENGINE (1MZ±FE)
DI±287
522 Author: Date:
DTC P0335 Crankshaft Position Sensor ºAº Circuit
Malfunction
CIRCUIT DESCRIPTION
Crankshaft position sensor (NE signal) consists of a signal plate and pickup coil.
The NE signal plate has 34 teeth and is mounted on the crankshaft. The NE signal sensor generates 34
signals for every engine revolution. The ECM detects the standard crankshaft angle based on the G22 sig-
nals, and the actual crankshaft angle and the engine speed by the NE signals.
DTC No.DTC Detecting ConditionTrouble Area
P0335
No crankshaft position sensor signal to ECM during cranking
(2 trip detection logic)Open or short in crankshaft position sensor circuit
Crankshaft position sensor
P0335No crankshaft position sensor signal to ECM with engine
speed 600 rpm or more (2 trip detection logic)
Crankshaft osition sensor
Starter
ECM
WIRING DIAGRAM
INSPECTION PROCEDURE
HINT:
Perform troubleshooting of DTC P0335 first. If no trouble is found, troubleshoot the following mechani-
cal systems.
Read freeze frame data using TOYOTA hand±held tester or OBD II scan tool. because freeze frame
records the engine conditions when the malfunction is detected, when troubleshooting it is useful for
determining whether the vehicle was running or stopped, the engine warmed up or not, the air±fuel
ratio lean or rich, etc. at the time of the malfunction.
DI07U±06
Page 2708 of 4770
FI7059
FI7060
A00069
G22, NE Signal Waveforms
G22
G22NE
NE5 V
/Division
5 V
/Division 20 msec./Division (Idling)
10 msec./Division (Idling)
DI±288
± DIAGNOSTICSENGINE (1MZ±FE)
523 Author: Date:
1 Check resistance of crankshaft position sensor (See page IG±12).
Reference INSPECTION USING OSCILLOSCOPE
During cranking or idling, check between terminals G22+ and
NE±, NE and NE± of the ECM connector.
HINT:
The correct waveforms are as shown.
NG Replace crankshaft position sensor.
OK
2 Check for open and short in harness and connector between ECM and
crankshaft position sensor (See page IN±31).
NG Repair or replace harness or connector.
OK
Page 2709 of 4770
± DIAGNOSTICSENGINE (1MZ±FE)
DI±289
524 Author: Date:
3 Inspect sensor installation and teeth of crankshaft timing pulley.
NG Tighten the sensor.
Replace crankshaft timing pulley.
OK
Check and replace ECM
(See page IN±31).
Page 2710 of 4770
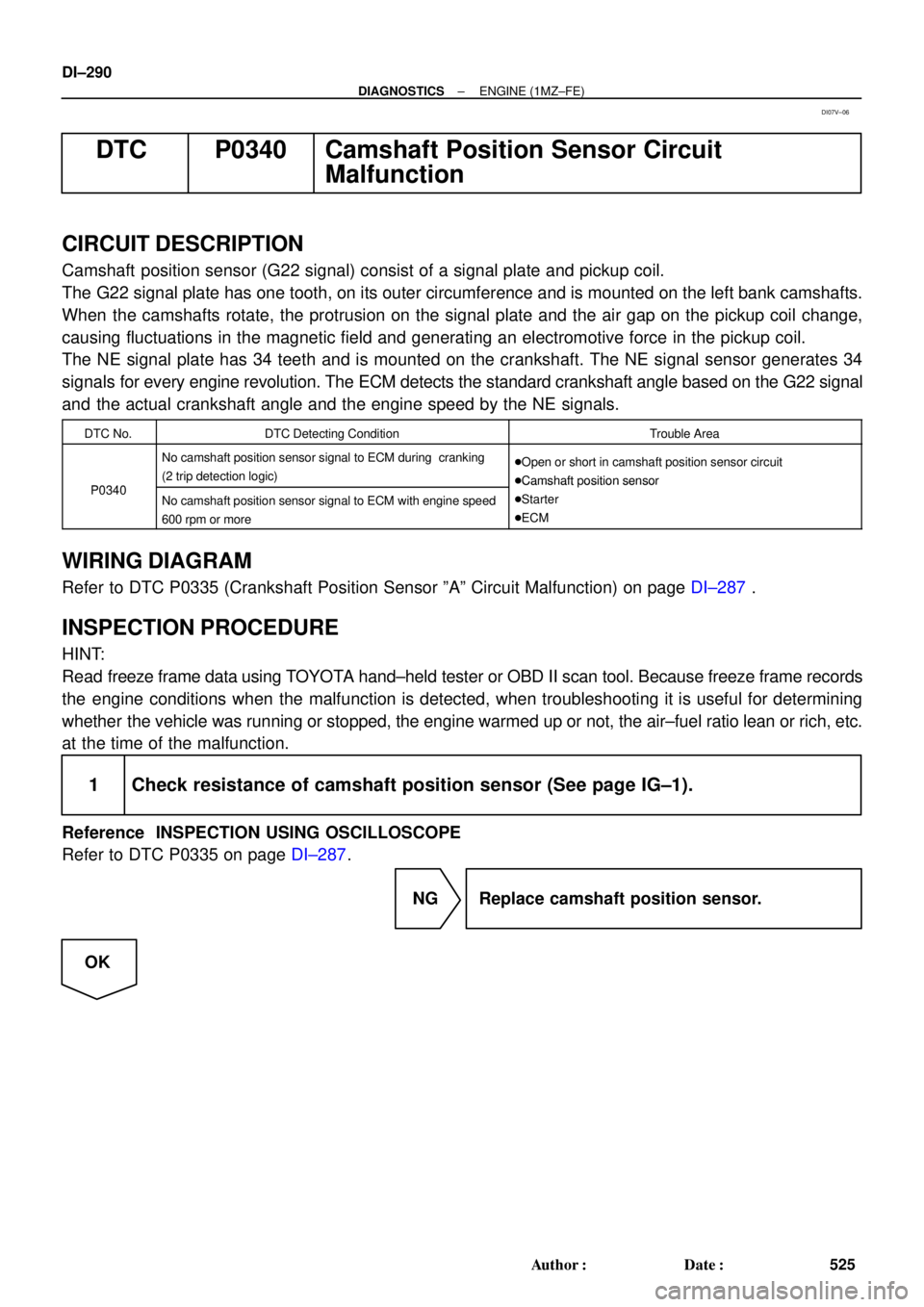
DI±290
± DIAGNOSTICSENGINE (1MZ±FE)
525 Author: Date:
DTC P0340 Camshaft Position Sensor Circuit
Malfunction
CIRCUIT DESCRIPTION
Camshaft position sensor (G22 signal) consist of a signal plate and pickup coil.
The G22 signal plate has one tooth, on its outer circumference and is mounted on the left bank camshafts.
When the camshafts rotate, the protrusion on the signal plate and the air gap on the pickup coil change,
causing fluctuations in the magnetic field and generating an electromotive force in the pickup coil.
The NE signal plate has 34 teeth and is mounted on the crankshaft. The NE signal sensor generates 34
signals for every engine revolution. The ECM detects the standard crankshaft angle based on the G22 signal
and the actual crankshaft angle and the engine speed by the NE signals.
DTC No.DTC Detecting ConditionTrouble Area
P0340
No camshaft position sensor signal to ECM during cranking
(2 trip detection logic)Open or short in camshaft position sensor circuit
Camshaft position sensor
P0340No camshaft position sensor signal to ECM with engine speed
600 rpm or more
Camshaft osition sensor
Starter
ECM
WIRING DIAGRAM
Refer to DTC P0335 (Crankshaft Position Sensor ºAº Circuit Malfunction) on page DI±287 .
INSPECTION PROCEDURE
HINT:
Read freeze frame data using TOYOTA hand±held tester or OBD II scan tool. Because freeze frame records
the engine conditions when the malfunction is detected, when troubleshooting it is useful for determining
whether the vehicle was running or stopped, the engine warmed up or not, the air±fuel ratio lean or rich, etc.
at the time of the malfunction.
1 Check resistance of camshaft position sensor (See page IG±1).
Reference INSPECTION USING OSCILLOSCOPE
Refer to DTC P0335 on page DI±287.
NG Replace camshaft position sensor.
OK
DI07V±06
Page 2711 of 4770
± DIAGNOSTICSENGINE (1MZ±FE)
DI±291
526 Author: Date:
2 Check for open and short in harness and connector between ECM and camshaft
position sensor (See page IN±31).
NG Repair or replace harness or connector.
OK
3 Inspect sensor installation and tooth of left bank camshaft timing pulley.
NG Tighten the sensor.
Replace left bank camshaft timing pulley.
OK
Check and replace ECM (See page IN±31).
Page 2712 of 4770
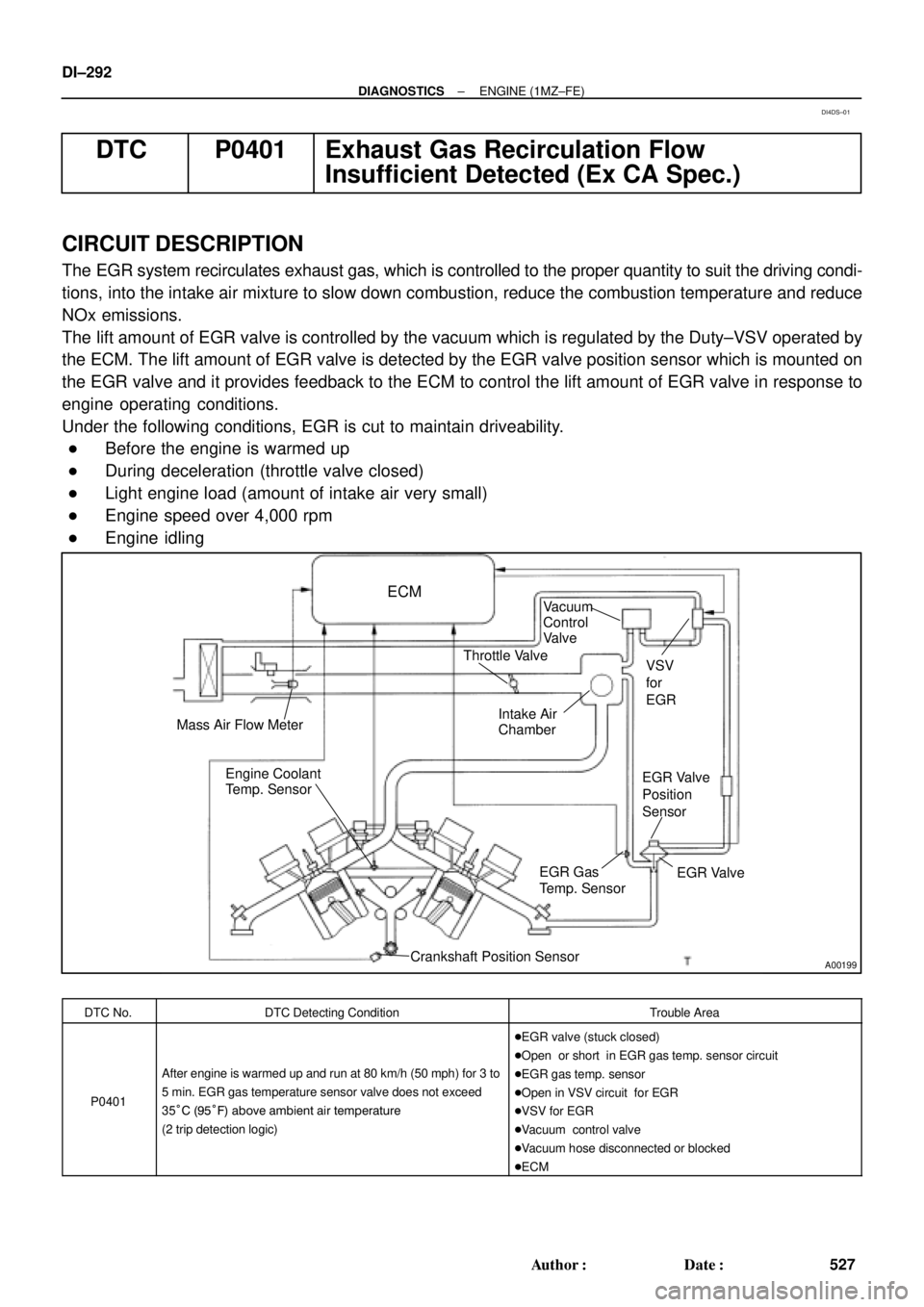
A00199
ECM
Mass Air Flow MeterVSV
for
EGR
EGR Valve
Position
Sensor
EGR Valve EGR Gas
Temp. Sensor
Crankshaft Position Sensor Engine Coolant
Temp. SensorIntake Air
Chamber Throttle ValveVacuum
Control
Valve
DI±292
± DIAGNOSTICSENGINE (1MZ±FE)
527 Author: Date:
DTC P0401 Exhaust Gas Recirculation Flow
Insufficient Detected (Ex CA Spec.)
CIRCUIT DESCRIPTION
The EGR system recirculates exhaust gas, which is controlled to the proper quantity to suit the driving condi-
tions, into the intake air mixture to slow down combustion, reduce the combustion temperature and reduce
NOx emissions.
The lift amount of EGR valve is controlled by the vacuum which is regulated by the Duty±VSV operated by
the ECM. The lift amount of EGR valve is detected by the EGR valve position sensor which is mounted on
the EGR valve and it provides feedback to the ECM to control the lift amount of EGR valve in response to
engine operating conditions.
Under the following conditions, EGR is cut to maintain driveability.
Before the engine is warmed up
During deceleration (throttle valve closed)
Light engine load (amount of intake air very small)
Engine speed over 4,000 rpm
Engine idling
DTC No.DTC Detecting ConditionTrouble Area
P0401
After engine is warmed up and run at 80 km/h (50 mph) for 3 to
5 min. EGR gas temperature sensor valve does not exceed
35°C (95°F) above ambient air temperature
(2 trip detection logic)
EGR valve (stuck closed)
Open or short in EGR gas temp. sensor circuit
EGR gas temp. sensor
Open in VSV circuit for EGR
VSV for EGR
Vacuum control valve
Vacuum hose disconnected or blocked
ECM
DI4DS±01