Page 313 of 4770
B. Inspect relay continuity
(a) Using an ohmmeter, check that there is continuity
between terminals 3 and 5.
(b) Check that there is continuity between terminals 2
and 4.
(c) Check that there is no continuity between terminals 1
and 2.
If continuity is not as specified, replace the relay. B. Inspect relay continuity
(a) Using an ohmmeter, check that there is continuity
between terminals 1 and 2.
(b) Check that there is continuity between terminals 3
and 4.
If continuity is not as specified, replace the relay.
C. Inspect relay operation
(a) Apply battery voltage across terminals 1 and 2.
(b) Using an ohmmeter, check that there is no continuity
between terminals 3 and 4.
If operation is not as specified, replace the relay.
D. Reinstall cooling fan relay
3. INSPECT ENGINE MAIN RELAY (ªENG MAINº)
A. Remove engine main relay 2. INSPECT COOLING FAN RELAY (ºFAN')
A. Remove cooling fan relay
± 5S±FE ENGINECOOLING SYSTEMEG1±263
Page 314 of 4770
C. Inspect relay operation
(a) Apply battery voltage across terminals 3 and 5.
(b) Using an ohmmeter, check that there is no continuity
between terminals 2 and 4.
(c) Check that there is continuity between terminals 1
and 2.
If operation is not as specified, replace the relay.
D. Reinstall engine main relay
4. INSPECT COOLING FAN
(a) Connect battery and ammeter to the cooling fan con±
nector.
(b) Check that the cooling fan rotates smoothly, and
check the reading on the ammeter.
Standard amperage:
5.8 ± 7.4 A
COMPONENTS FOR REMOVAL AND
INSTALLATION
± 5S±FE ENGINECOOLING SYSTEMEG1±264
Page 315 of 4770
ELECTRIC COOLING FAN REMOVAL
(See Components for Removal and Installation)
1. DISCONNECT NEGATIVE (±) TERMINAL CABLE
FROM BATTERY
CAUTION: Work must be started after 90 seconds from
the time the ignition switch is turned to the 'LOCK'
position and the negative (±) terminal cable is discon±
nected from the battery.
5. REMOVE ELECTRIC COOLING FAN
(a) Disconnect the engine coolant temperature switch
connector from the radiator.
(b) Disconnect the engine coolant temperature switch
and electric cooling fan connectors from the fan
shroud.
(c) Remove the 4 bolts and cooling fan. 2. DRAIN ENGINE COOLANT (See page EG1±241)
3. w/ CRUISE CONTROL SYSTEM:
REMOVE CRUISE CONTROL ACTUATOR COVER
4. DISCONNECT UPPER RADIATOR HOSE FROM
RADIATOR
COMPONENTS FOR DISASSEMBLY AND
ASSEMBLY
± 5S±FE ENGINECOOLING SYSTEMEG1±265
Page 316 of 4770
ELECTRIC COOLING FAN INSTALLATION
(See Components for Removal and Installation)
1. INSTALL ELECTRIC COOLING FAN
(a) Install the cooling fan with the 4 bolts.
(b) Connect the engine coolant temperature switch and
electric cooling fan connectors to the fan shroud.
(c) Connect the engine coolant temperature switch connector
to the radiator.
2. CONNECT UPPER RADIATOR HOSE TO RADIATOR
3. w/ CRUISE CONTROL SYSTEM:
INSTALL CRUISE CONTROL ACTUATOR COVER
4. FILL WITH ENGINE COOLANT
(See page EG1±241)
5. CONNECT NEGATIVE (±) TERMINAL CABLE TO
BATTERY
6. START ENGINE AND CHECK FOR LEAKS
ELECTRIC COOLING FAN DISASSEMBLY
(See Components for Disassembly and Assembly)
1. REMOVE FAN
Remove the nut and fan.
ELECTRIC COOLING FAN ASSEMBLY
(See Components for Disassembly and Assembly)
1. INSTALL FAN MOTOR
2. INSTALL FAN 2. REMOVE FAN MOTOR
Remove the screws and fan motor.
± 5S±FE ENGINECOOLING SYSTEMEG1±266
Page 317 of 4770
SERVICE SPECIFICATIONS
SERVICE DATA
TORQUE SPECIFICATIONS
Valve opening temperature
Valve lift
Water bypass pipe x Water pump cover
Radiator oil cooler x Radiator lower tank Water pump x Water pump cover
No.2 idler pulley x Cylinder block Water inlet x Water pump coverRelief valve opening pressure
Water pump x Cylinder blockCylinder block x Drain plug
Water inlet x Water pump
Radiator oil cooler pipe
Radiator support boltElectric
cooling fanRotating amperage
Part tightened Radiator cap
Plate height Thermostat
Radiator
± 5S±FE ENGINECOOLING SYSTEMEG1±267
Page 318 of 4770
DESCRIPTION
A fully pressurized, fully filtered lubrication system has been adopted for this engine.
OPERATION LUBRICATION SYSTEM
± 5S±FE ENGINELUBRICATION SYSTEMEG1±268
Page 319 of 4770
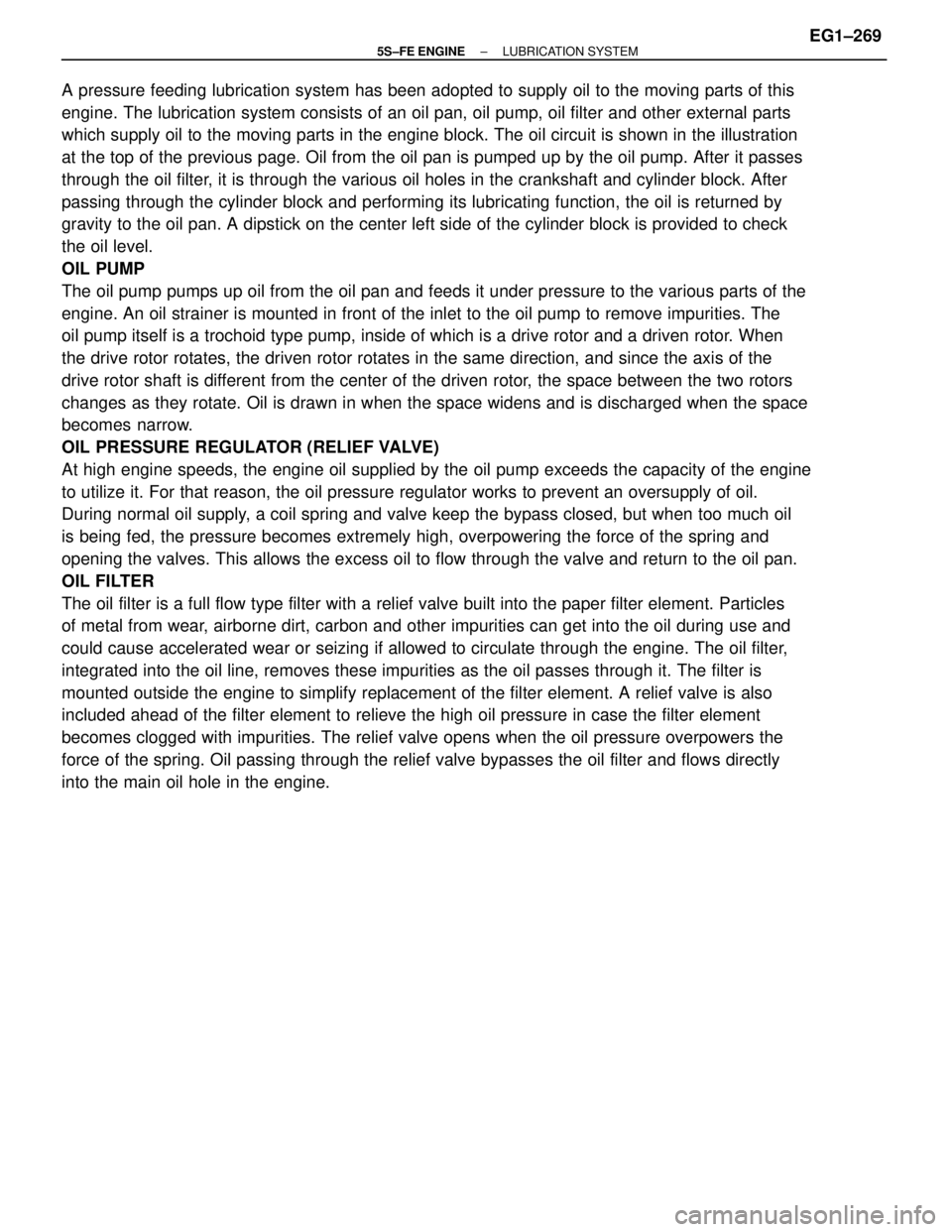
A pressure feeding lubrication system has been adopted to supply oil to the moving parts of this
engine. The lubrication system consists of an oil pan, oil pump, oil filter and other external parts
which supply oil to the moving parts in the engine block. The oil circuit is shown in the illustration
at the top of the previous page. Oil from the oil pan is pumped up by the oil pump. After it passes
through the oil filter, it is through the various oil holes in the crankshaft and cylinder block. After
passing through the cylinder block and performing its lubricating function, the oil is returned by
gravity to the oil pan. A dipstick on the center left side of the cylinder block is provided to check
the oil level.
OIL PUMP
The oil pump pumps up oil from the oil pan and feeds it under pressure to the various parts of the
engine. An oil strainer is mounted in front of the inlet to the oil pump to remove impurities. The
oil pump itself is a trochoid type pump, inside of which is a drive rotor and a driven rotor. When
the drive rotor rotates, the driven rotor rotates in the same direction, and since the axis of the
drive rotor shaft is different from the center of the driven rotor, the space between the two rotors
changes as they rotate. Oil is drawn in when the space widens and is discharged when the space
becomes narrow.
OIL PRESSURE REGULATOR (RELIEF VALVE)
At high engine speeds, the engine oil supplied by the oil pump exceeds the capacity of the engine
to utilize it. For that reason, the oil pressure regulator works to prevent an oversupply of oil.
During normal oil supply, a coil spring and valve keep the bypass closed, but when too much oil
is being fed, the pressure becomes extremely high, overpowering the force of the spring and
opening the valves. This allows the excess oil to flow through the valve and return to the oil pan.
OIL FILTER
The oil filter is a full flow type filter with a relief valve built into the paper filter element. Particles
of metal from wear, airborne dirt, carbon and other impurities can get into the oil during use and
could cause accelerated wear or seizing if allowed to circulate through the engine. The oil filter,
integrated into the oil line, removes these impurities as the oil passes through it. The filter is
mounted outside the engine to simplify replacement of the filter element. A relief valve is also
included ahead of the filter element to relieve the high oil pressure in case the filter element
becomes clogged with impurities. The relief valve opens when the oil pressure overpowers the
force of the spring. Oil passing through the relief valve bypasses the oil filter and flows directly
into the main oil hole in the engine.
± 5S±FE ENGINELUBRICATION SYSTEMEG1±269
Page 320 of 4770
PREPARATION
SST (SPECIAL SERVICE TOOLS)
(09627±30010) Steering Sector Shaft Bushing
Replacer09226±10010 Crankshaft Front & Rear Bearing
Replacer
(09631±00020) Handle09616±30011 Steering Worm Bearing Adjusting
Screw Wrench
RECOMMENDED TOOLS
Oil pump oil seal
Oil pump oil seal 09620±30010 Steering Gear Box Replacer Set
09090±04000 Engine Sling Device
09200±00010 Engine Adjust Kit09032±00100 Oil Pan Seat Cutter
09905±00013 Snap Ring Pliers09228±06500 Oil Filter wrench
Precision straight edge
EQUIPMENT
Oil pressure gaugeFor suspending engineCrankshaft front oil seal
Torque wrenchOil pump pulley
Oil pump
± 5S±FE ENGINELUBRICATION SYSTEMEG1±270