Page 2729 of 4449
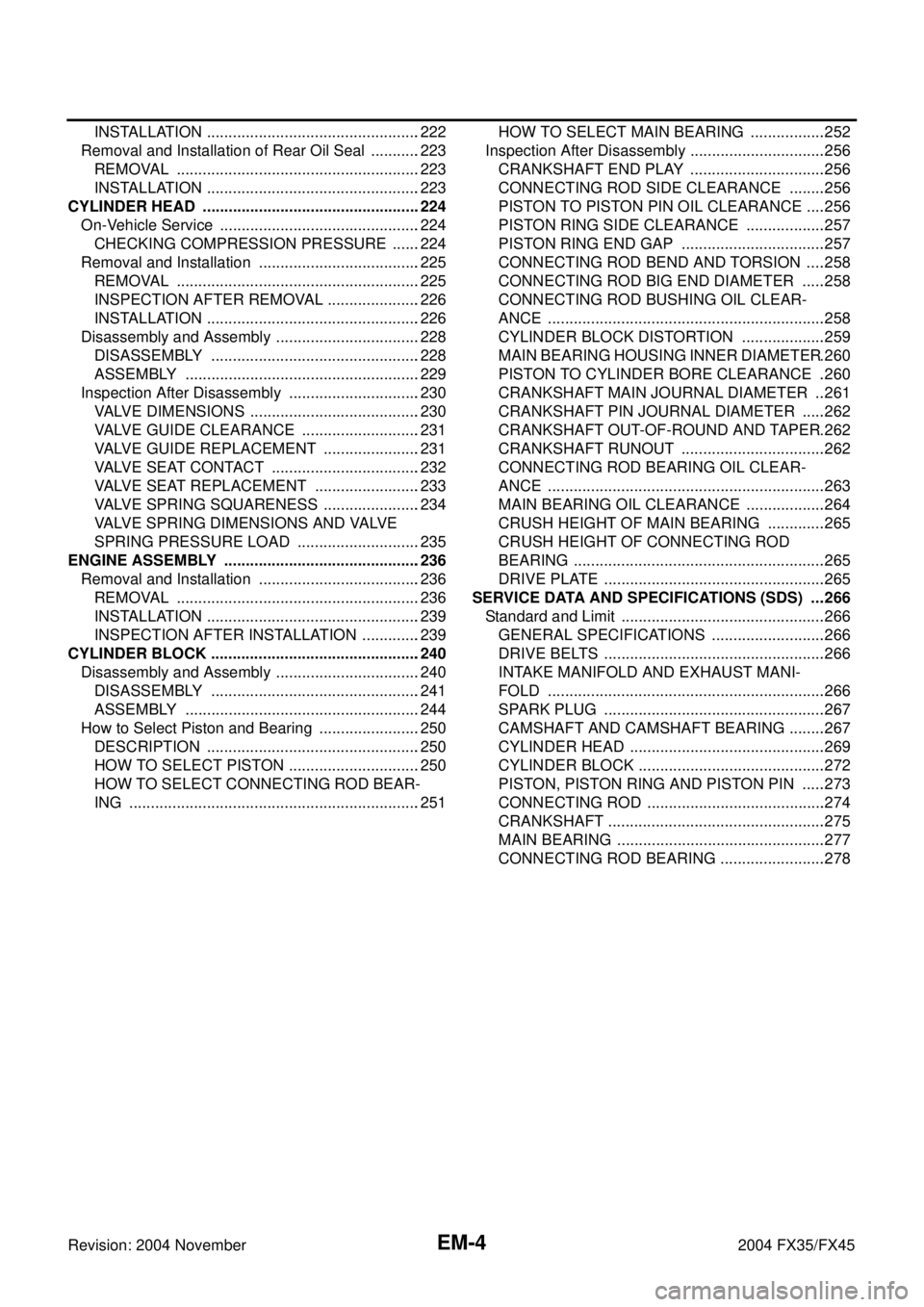
EM-4Revision: 2004 November 2004 FX35/FX45INSTALLATION ..................................................222
Removal and Installation of Rear Oil Seal ............223
REMOVAL .........................................................223
INSTALLATION ..................................................223
CYLINDER HEAD ...................................................224
On-Vehicle Service ...............................................224
CHECKING COMPRESSION PRESSURE .......224
Removal and Installation ......................................225
REMOVAL .........................................................225
INSPECTION AFTER REMOVAL ......................226
INSTALLATION ..................................................226
Disassembly and Assembly ..................................228
DISASSEMBLY .................................................228
ASSEMBLY .......................................................229
Inspection After Disassembly ...............................230
VALVE DIMENSIONS ........................................230
VALVE GUIDE CLEARANCE ............................231
VALVE GUIDE REPLACEMENT .......................231
VALVE SEAT CONTACT ...................................232
VALVE SEAT REPLACEMENT .........................233
VALVE SPRING SQUARENESS .......................234
VALVE SPRING DIMENSIONS AND VALVE
SPRING PRESSURE LOAD .............................235
ENGINE ASSEMBLY ..............................................236
Removal and Installation ......................................236
REMOVAL .........................................................236
INSTALLATION ..................................................239
INSPECTION AFTER INSTALLATION ..............239
CYLINDER BLOCK .................................................240
Disassembly and Assembly ..................................240
DISASSEMBLY .................................................241
ASSEMBLY .......................................................244
How to Select Piston and Bearing ........................250
DESCRIPTION ..................................................250
HOW TO SELECT PISTON ...............................250
HOW TO SELECT CONNECTING ROD BEAR-
ING ....................................................................251HOW TO SELECT MAIN BEARING ..................252
Inspection After Disassembly ................................256
CRANKSHAFT END PLAY ................................256
CONNECTING ROD SIDE CLEARANCE .........256
PISTON TO PISTON PIN OIL CLEARANCE .....256
PISTON RING SIDE CLEARANCE ...................257
PISTON RING END GAP ..................................257
CONNECTING ROD BEND AND TORSION .....258
CONNECTING ROD BIG END DIAMETER ......258
CONNECTING ROD BUSHING OIL CLEAR-
ANCE .................................................................258
CYLINDER BLOCK DISTORTION ....................259
MAIN BEARING HOUSING INNER DIAMETER .260
PISTON TO CYLINDER BORE CLEARANCE ..260
CRANKSHAFT MAIN JOURNAL DIAMETER ...261
CRANKSHAFT PIN JOURNAL DIAMETER ......262
CRANKSHAFT OUT-OF-ROUND AND TAPER .262
CRANKSHAFT RUNOUT ..................................262
CONNECTING ROD BEARING OIL CLEAR-
ANCE .................................................................263
MAIN BEARING OIL CLEARANCE ...................264
CRUSH HEIGHT OF MAIN BEARING ..............265
CRUSH HEIGHT OF CONNECTING ROD
BEARING ...........................................................265
DRIVE PLATE ....................................................265
SERVICE DATA AND SPECIFICATIONS (SDS) ....266
Standard and Limit ................................................266
GENERAL SPECIFICATIONS ...........................266
DRIVE BELTS ....................................................266
INTAKE MANIFOLD AND EXHAUST MANI-
FOLD .................................................................266
SPARK PLUG ....................................................267
CAMSHAFT AND CAMSHAFT BEARING .........267
CYLINDER HEAD ..............................................269
CYLINDER BLOCK ............................................272
PISTON, PISTON RING AND PISTON PIN ......273
CONNECTING ROD ..........................................274
CRANKSHAFT ...................................................275
MAIN BEARING .................................................277
CONNECTING ROD BEARING .........................278
Page 2730 of 4449
![INFINITI FX35 2004 Service Manual PRECAUTIONS
EM-5
[VQ35DE]
C
D
E
F
G
H
I
J
K
L
MA
EM
Revision: 2004 November 2004 FX35/FX45
[VQ35DE]PRECAUTIONSPFP:00001
Precautions Necessary for Steering Wheel Rotation After Battery DisconnectABS00B INFINITI FX35 2004 Service Manual PRECAUTIONS
EM-5
[VQ35DE]
C
D
E
F
G
H
I
J
K
L
MA
EM
Revision: 2004 November 2004 FX35/FX45
[VQ35DE]PRECAUTIONSPFP:00001
Precautions Necessary for Steering Wheel Rotation After Battery DisconnectABS00B](/manual-img/42/57021/w960_57021-2729.png)
PRECAUTIONS
EM-5
[VQ35DE]
C
D
E
F
G
H
I
J
K
L
MA
EM
Revision: 2004 November 2004 FX35/FX45
[VQ35DE]PRECAUTIONSPFP:00001
Precautions Necessary for Steering Wheel Rotation After Battery DisconnectABS00B3I
NOTE:
This Procedure is applied only to models with Intelligent Key system and NVIS/IVIS (NISSAN/INFINITI
VEHICLE IMMOBILIZER SYSTEM - NATS).
Remove and install all control units after disconnecting both battery cables with the ignition knob in the
″LOCK″ position.
Always use CONSULT-II to perform self-diagnosis as a part of each function inspection after finishing
work. If DTC is detected, perform trouble diagnosis according to self-diagnostic results.
For models equipped with the Intelligent Key system and NVIS/IVIS, an electrically controlled steering lock
mechanism is adopted on the key cylinder.
For this reason, if the battery is disconnected or if the battery is discharged, the steering wheel will lock and
steering wheel rotation will become impossible.
If steering wheel rotation is required when battery power is interrupted, follow the procedure below before
starting the repair operation.
OPERATION PROCEDURE
1. Connect both battery cables.
NOTE:
Supply power using jumper cables if battery is discharged.
2. Use the Intelligent Key or mechanical key to turn the ignition switch to the ″ACC″ position. At this time, the
steering lock will be released.
3. Disconnect both battery cables. The steering lock will remain released and the steering wheel can be
rotated.
4. Perform the necessary repair operation.
5. When the repair work is completed, return the ignition switch to the ″LOCK″ position before connecting
the battery cables. (At this time, the steering lock mechanism will engage.)
6. Perform a self-diagnosis check of all control units using CONSULT-II.
Precautions for Drain Engine CoolantABS005ZK
Drain engine coolant when engine is cooled.
Precautions for Disconnecting Fuel PipingABS005ZL
Before starting work, make sure no fire or spark producing items are in the work area.
Release fuel pressure before disconnecting and disassembly.
After disconnecting pipes, plug openings to stop fuel leakage.
Precautions for Removal and DisassemblyABS005ZM
When instructed to use special service tools, use the specified tools. Always be careful to work safely,
avoid forceful or uninstructed operations.
Exercise maximum care to avoid damage to mating or sliding surfaces.
Cover openings of engine system with tape or the equivalent, if necessary, to seal out foreign materials.
Mark and arrange disassembly parts in an organized way for easy troubleshooting and re-assembly.
When loosening nuts and bolts, as a basic rule, start with the one furthest outside, then the one diagonally
opposite, and so on. If the order of loosening is specified, do exactly as specified. Power tools may be
used where noted in the step.
Precautions for Inspection, Repair and ReplacementABS005ZN
Before repairing or replacing, thoroughly inspect parts. Inspect new replacement parts in the same way, and
replace if necessary.
Precautions for Assembly and InstallationABS005ZO
Use torque wrench to tighten bolts or nuts to specification.
Page 2731 of 4449
![INFINITI FX35 2004 Service Manual EM-6
[VQ35DE]
PRECAUTIONS
Revision: 2004 November 2004 FX35/FX45
When tightening nuts and bolts, as a basic rule, equally tighten in several different steps starting with the
ones in center, then one INFINITI FX35 2004 Service Manual EM-6
[VQ35DE]
PRECAUTIONS
Revision: 2004 November 2004 FX35/FX45
When tightening nuts and bolts, as a basic rule, equally tighten in several different steps starting with the
ones in center, then one](/manual-img/42/57021/w960_57021-2730.png)
EM-6
[VQ35DE]
PRECAUTIONS
Revision: 2004 November 2004 FX35/FX45
When tightening nuts and bolts, as a basic rule, equally tighten in several different steps starting with the
ones in center, then ones on inside and outside diagonally in this order. If the order of tightening is speci-
fied, do exactly as specified.
Replace with new liquid gasket, packing, oil seal or O-ring.
Thoroughly wash, clean, and air-blow each part. Carefully check engine oil or engine coolant passages for
any restriction and blockage.
Avoid damaging sliding or mating surfaces. Completely remove foreign materials such as cloth lint or dust.
Before assembly, oil sliding surfaces well.
Release air within route when refilling after draining engine coolant.
Before starting engine, apply fuel pressure to fuel lines with turning ignition switch “ON” (with engine
stopped). Then make sure that there are no leaks at fuel line connections.
After repairing, start engine and increase engine speed to check engine coolant, fuel, engine oil and
exhaust systems for leakage.
Parts Requiring Angle TighteningABS005ZP
Use an angle wrench [SST: KV10112100 (BT8653-A)] for the final tightening of the following engine parts:
–Cylinder head bolts
–Main bearing cap bolts
–Connecting rod cap bolts
–Crankshaft pulley bolt (No angle wrench is required as the bolt flange is provided with notches for angle
tightening)
Do not use a torque value for final tightening.
The torque value for these parts are for a preliminary step.
Ensure thread and seat surfaces are clean and coated with engine oil.
Precautions for Liquid GasketABS005ZQ
REMOVAL OF LIQUID GASKET SEALING
After removing mounting bolts and nuts, separate the mating
surface using a seal cutter (SST) and remove old liquid gasket
sealing.
CAUTION:
Be careful not to damage the mating surfaces.
Tap seal cutter to insert it, and then slide it by tapping on the
side as shown in the figure.
In areas where seal cutter is difficult to use, use plastic hammer
to lightly tap the areas where the liquid gasket is applied.
CAUTION:
If for some unavoidable reason tool such as screwdriver is
used, be careful not to damage the mating surfaces.
LIQUID GASKET APPLICATION PROCEDURE
1. Using a scraper, remove old liquid gasket adhering to liquid gas-
ket application surface and the mating surface.
Remove liquid gasket completely from the groove of the liquid
gasket application surface, mounting bolts, and bolt holes.
2. Wipe liquid gasket application surface and the mating surface
with white gasoline (lighting and heating use) to remove adher-
ing moisture, grease and foreign materials.
PBIC0002E
PBIC0003E
Page 2732 of 4449
![INFINITI FX35 2004 Service Manual PRECAUTIONS
EM-7
[VQ35DE]
C
D
E
F
G
H
I
J
K
L
MA
EM
Revision: 2004 November 2004 FX35/FX45
3. Attach liquid gasket tube to tube presser [SST: WS39930000 ( –
)].
Use Genuine RTV Silicone Sealant or e INFINITI FX35 2004 Service Manual PRECAUTIONS
EM-7
[VQ35DE]
C
D
E
F
G
H
I
J
K
L
MA
EM
Revision: 2004 November 2004 FX35/FX45
3. Attach liquid gasket tube to tube presser [SST: WS39930000 ( –
)].
Use Genuine RTV Silicone Sealant or e](/manual-img/42/57021/w960_57021-2731.png)
PRECAUTIONS
EM-7
[VQ35DE]
C
D
E
F
G
H
I
J
K
L
MA
EM
Revision: 2004 November 2004 FX35/FX45
3. Attach liquid gasket tube to tube presser [SST: WS39930000 ( –
)].
Use Genuine RTV Silicone Sealant or equivalent. Refer to
GI-48, "
RECOMMENDED CHEMICAL PRODUCTS AND
SEALANTS" .
4. Apply liquid gasket without breaks to the specified location with
the specified dimensions.
If there is a groove for the liquid gasket application, apply liq-
uid gasket to the groove.
As for the bolt holes, normally apply liquid gasket inside the
holes. Occasionally, it should be applied outside the holes.
Make sure to read the text of service manual.
Within five minutes of liquid gasket application, install the mat-
ing component.
If liquid gasket protrudes, wipe it off immediately.
Do not retighten mounting bolts and nuts after the installation.
After 30 minutes or more have passed from the installation, fill
engine oil and engine coolant.
CAUTION:
If there are specific instructions in this manual, observe them.
EMA0622D
SEM159F
Page 2733 of 4449
![INFINITI FX35 2004 Service Manual EM-8
[VQ35DE]
PREPARATION
Revision: 2004 November 2004 FX35/FX45
PREPARATIONPFP:00002
Special Service ToolsABS004TT
The actual shapes of Kent-Moore tools may differ from those of special service tools INFINITI FX35 2004 Service Manual EM-8
[VQ35DE]
PREPARATION
Revision: 2004 November 2004 FX35/FX45
PREPARATIONPFP:00002
Special Service ToolsABS004TT
The actual shapes of Kent-Moore tools may differ from those of special service tools](/manual-img/42/57021/w960_57021-2732.png)
EM-8
[VQ35DE]
PREPARATION
Revision: 2004 November 2004 FX35/FX45
PREPARATIONPFP:00002
Special Service ToolsABS004TT
The actual shapes of Kent-Moore tools may differ from those of special service tools illustrated here.
Tool number
(Kent-Moore No.)
Tool nameDescription
ST0501S000
(—)
Engine stand assembly
1. ST05011000
(—)
Engine stand
2. ST05012000
(—)
BaseDisassembling and assembling
KV10106500
(—)
Engine stand shaft
KV10117000
(J-41262)
Engine sub-attachmentKV10117000 has been replaced with
KV10117001 (KV10117000 is no longer in
production, but it is usable).
KV10117001
(—)
Engine sub-attachmentInstalling on cylinder block
KV10116200
(J-26336-A)
Valve spring compressor
1. KV10115900
(J-26336-20)
Attachment
2. KV10109220
(—)
AdapterDisassembling valve mechanism
Part (1) is a component of KV10116200
(J-26336-A), but Part (2) is not so.
KV10107902
(J-38959)
Valve oil seal puller
1. KV10116100
(—)
Valve oil seal puller adapterReplacing valve oil seal
NT042
NT028
NT373
NT372
PBIC1650E
S-NT605
Page 2734 of 4449
PREPARATION
EM-9
[VQ35DE]
C
D
E
F
G
H
I
J
K
L
MA
EM
Revision: 2004 November 2004 FX35/FX45(J-39386)
Valve oil seal driftInstalling valve oil seal
EM03470000
(J-8037)
Piston ring compressorInstalling piston assembly into cylinder bore
ST16610001
(J-23907)
Pilot bushing pullerRemoving crankshaft pilot converter
KV10111100
(J-37228)
Seal cutterRemoving steel oil pan (lower and upper) and
front and rear timing chain case
WS39930000
(—)
Tube presserPressing tube of liquid gasket
KV10112100
(BT8653-A)
Angle wrenchTightening bolts for bearing cap, cylinder
head, etc. in angle
KV10117100
(J-3647-A)
Heated oxygen sensor wrenchLoosening or tightening heated oxygen
sensor 2
For 22 mm (0.87 in) width hexagon nut Tool number
(Kent-Moore No.)
Tool nameDescription
NT024
NT044
NT045
NT046
NT052
NT014
NT379
Page 2735 of 4449
EM-10
[VQ35DE]
PREPARATION
Revision: 2004 November 2004 FX35/FX45
Commercial Service ToolsABS004TU
KV10114400
(J-38365)
Heated oxygen sensor wrenchLoosening or tightening heated oxygen
sensor
a: 22 mm (0.87 in)
KV10117700
(J-44716)
Ring gear stopperRemoving and installing crankshaft pulley
10006 31U00
(—)
Engine rear slingerRemoving and installing oil pan (upper) for on
vehicle service
—
(J-45488)
Quick connector releaseRemoving fuel tube quick connectors in
engine room (Right member side) Tool number
(Kent-Moore No.)
Tool nameDescription
NT636
NT822
SBIA0530E
PBIC0198E
(Kent-Moore No.)
Tool nameDescription
Power toolLoosening bolts and nuts
Manual lift table caddy Removing and installing engine
PBIC0190E
ZZA1210D
Page 2736 of 4449
PREPARATION
EM-11
[VQ35DE]
C
D
E
F
G
H
I
J
K
L
MA
EM
Revision: 2004 November 2004 FX35/FX45
(BT3373-F)
Belt tension gaugeChecking drive belt tension
(J-24239-01)
Cylinder head bolt wrenchLoosening and tightening cylinder head bolt,
and used with angle wrench
[SST: KV10112100 (BT8653-A)]
a: 13 (0.51) dia.
b: 12 (0.47)
c: 10 (0.39)
Unit: mm (in)
Spark plug wrench Removing and installing spark plug
Valve seat cutter set Finishing valve seat dimensions
Piston ring expander Removing and installing piston ring
Valve guide drift Removing and installing valve guide
Intake & Exhaust
a: 9.5 mm (0.374 in) dia.
b: 5.5 mm (0.217 in) dia.
Valve guide reamer Reaming valve guide with (1) or hole for
oversize valve guide with (2)
Intake & Exhaust
d
1 : 6.0 mm (0.236 in) dia.
d
2: 10.2 mm (0.402 in) dia. (Kent-Moore No.)
Tool nameDescription
AMA126
NT583
NT047
NT048
NT030
NT015
NT016