Page 817 of 4449
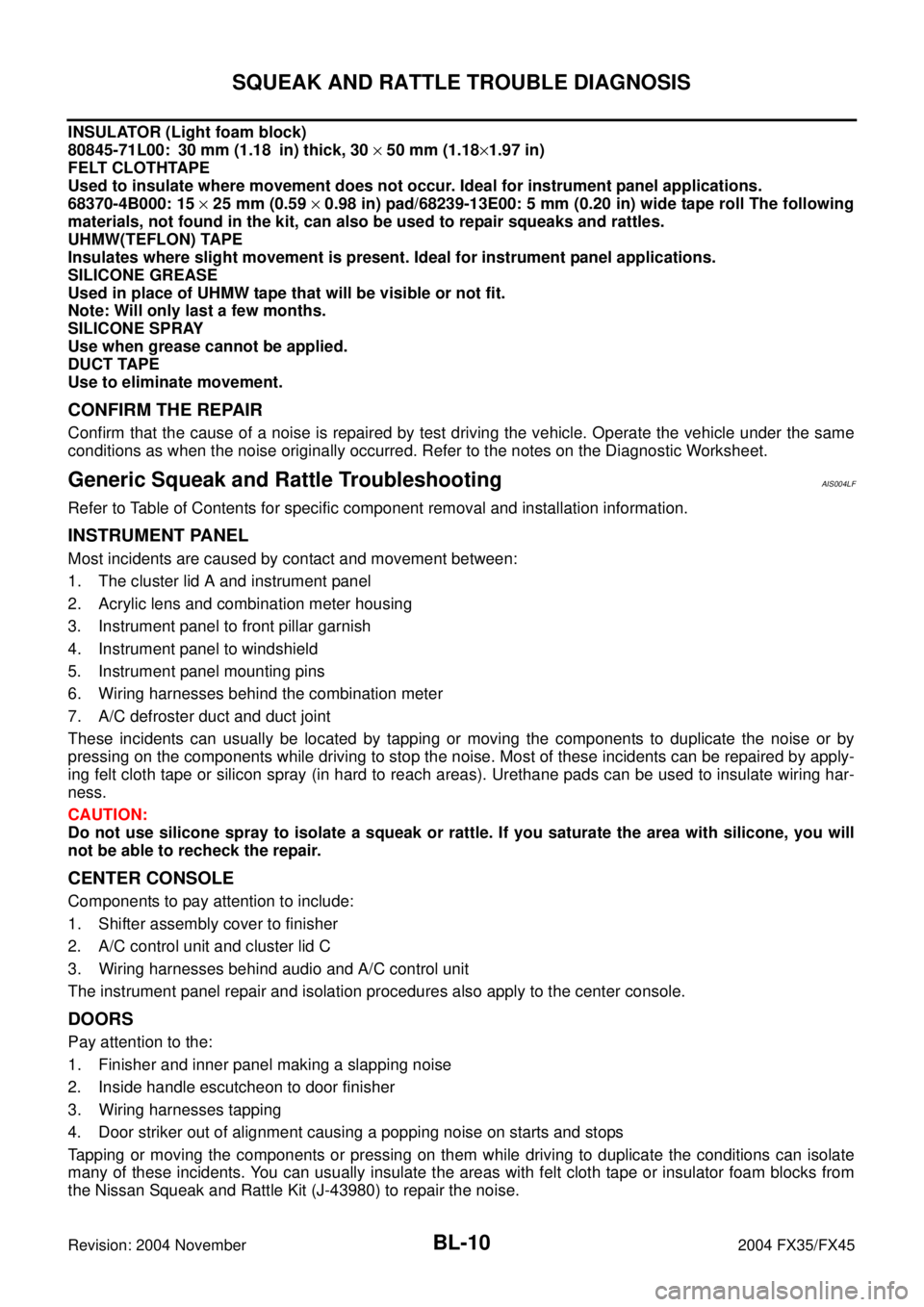
BL-10
SQUEAK AND RATTLE TROUBLE DIAGNOSIS
Revision: 2004 November 2004 FX35/FX45
INSULATOR (Light foam block)
80845-71L00: 30 mm (1.18 in) thick, 30 × 50 mm (1.18×1.97 in)
FELT CLOTHTAPE
Used to insulate where movement does not occur. Ideal for instrument panel applications.
68370-4B000: 15 × 25 mm (0.59 × 0.98 in) pad/68239-13E00: 5 mm (0.20 in) wide tape roll The following
materials, not found in the kit, can also be used to repair squeaks and rattles.
UHMW(TEFLON) TAPE
Insulates where slight movement is present. Ideal for instrument panel applications.
SILICONE GREASE
Used in place of UHMW tape that will be visible or not fit.
Note: Will only last a few months.
SILICONE SPRAY
Use when grease cannot be applied.
DUCT TAPE
Use to eliminate movement.
CONFIRM THE REPAIR
Confirm that the cause of a noise is repaired by test driving the vehicle. Operate the vehicle under the same
conditions as when the noise originally occurred. Refer to the notes on the Diagnostic Worksheet.
Generic Squeak and Rattle TroubleshootingAIS004LF
Refer to Table of Contents for specific component removal and installation information.
INSTRUMENT PANEL
Most incidents are caused by contact and movement between:
1. The cluster lid A and instrument panel
2. Acrylic lens and combination meter housing
3. Instrument panel to front pillar garnish
4. Instrument panel to windshield
5. Instrument panel mounting pins
6. Wiring harnesses behind the combination meter
7. A/C defroster duct and duct joint
These incidents can usually be located by tapping or moving the components to duplicate the noise or by
pressing on the components while driving to stop the noise. Most of these incidents can be repaired by apply-
ing felt cloth tape or silicon spray (in hard to reach areas). Urethane pads can be used to insulate wiring har-
ness.
CAUTION:
Do not use silicone spray to isolate a squeak or rattle. If you saturate the area with silicone, you will
not be able to recheck the repair.
CENTER CONSOLE
Components to pay attention to include:
1. Shifter assembly cover to finisher
2. A/C control unit and cluster lid C
3. Wiring harnesses behind audio and A/C control unit
The instrument panel repair and isolation procedures also apply to the center console.
DOORS
Pay attention to the:
1. Finisher and inner panel making a slapping noise
2. Inside handle escutcheon to door finisher
3. Wiring harnesses tapping
4. Door striker out of alignment causing a popping noise on starts and stops
Tapping or moving the components or pressing on them while driving to duplicate the conditions can isolate
many of these incidents. You can usually insulate the areas with felt cloth tape or insulator foam blocks from
the Nissan Squeak and Rattle Kit (J-43980) to repair the noise.
Page 818 of 4449

SQUEAK AND RATTLE TROUBLE DIAGNOSIS
BL-11
C
D
E
F
G
H
J
K
L
MA
B
BL
Revision: 2004 November 2004 FX35/FX45
TRUNK
Trunk noises are often caused by a loose jack or loose items put into the trunk by the owner.
In addition look for:
1. Trunk lid dumpers out of adjustment
2. Trunk lid striker out of adjustment
3. The trunk lid torsion bars knocking together
4. A loose license plate or bracket
Most of these incidents can be repaired by adjusting, securing or insulating the item(s) or component(s) caus-
ing the noise.
SUNROOF/HEADLINING
Noises in the sunroof/headlining area can often be traced to one of the following:
1. Sunroof lid, rail, linkage or seals making a rattle or light knocking noise
2. Sunvisor shaft shaking in the holder
3. Front or rear windshield touching headlining and squeaking
Again, pressing on the components to stop the noise while duplicating the conditions can isolate most of these
incidents. Repairs usually consist of insulating with felt cloth tape.
SEATS
When isolating seat noise it's important to note the position the seat is in and the load placed on the seat when
the noise is present. These conditions should be duplicated when verifying and isolating the cause of the
noise.
Cause of seat noise include:
1. Headrest rods and holder
2. A squeak between the seat pad cushion and frame
3. The rear seatback lock and bracket
These noises can be isolated by moving or pressing on the suspected components while duplicating the con-
ditions under which the noise occurs. Most of these incidents can be repaired by repositioning the component
or applying urethane tape to the contact area.
UNDERHOOD
Some interior noise may be caused by components under the hood or on the engine wall. The noise is then
transmitted into the passenger room.
Causes of transmitted underhood noise include:
1. Any component mounted to the engine wall
2. Components that pass through the engine wall
3. Engine wall mounts and connectors
4. Loose radiator mounting pins
5. Hood bumpers out of adjustment
6. Hood striker out of adjustment
These noises can be difficult to isolate since they cannot be reached from the interior of the vehicle. The best
method is to secure, move or insulate one component at a time and test drive the vehicle. Also, engine RPM
or load can be changed to isolate the noise. Repairs can usually be made by moving, adjusting securing, or
insulating the component causing the noise.
Page 819 of 4449
BL-12
SQUEAK AND RATTLE TROUBLE DIAGNOSIS
Revision: 2004 November 2004 FX35/FX45
Diagnostic WorksheetAIS004LG
SBT860
Page 820 of 4449
SQUEAK AND RATTLE TROUBLE DIAGNOSIS
BL-13
C
D
E
F
G
H
J
K
L
MA
B
BL
Revision: 2004 November 2004 FX35/FX45
SBT844
Page 821 of 4449
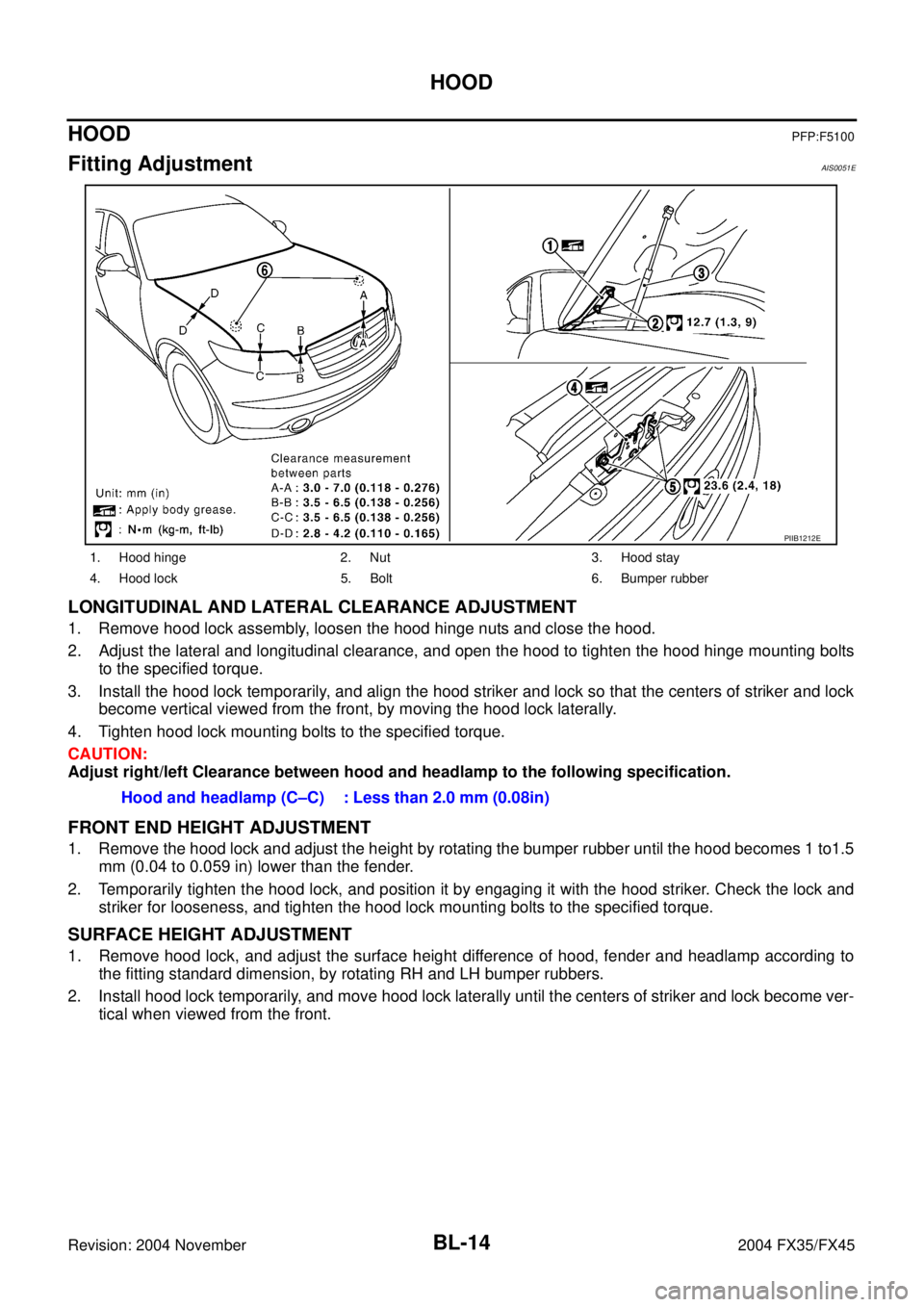
BL-14
HOOD
Revision: 2004 November 2004 FX35/FX45
HOODPFP:F5100
Fitting AdjustmentAIS0051E
LONGITUDINAL AND LATERAL CLEARANCE ADJUSTMENT
1. Remove hood lock assembly, loosen the hood hinge nuts and close the hood.
2. Adjust the lateral and longitudinal clearance, and open the hood to tighten the hood hinge mounting bolts
to the specified torque.
3. Install the hood lock temporarily, and align the hood striker and lock so that the centers of striker and lock
become vertical viewed from the front, by moving the hood lock laterally.
4. Tighten hood lock mounting bolts to the specified torque.
CAUTION:
Adjust right/left Clearance between hood and headlamp to the following specification.
FRONT END HEIGHT ADJUSTMENT
1. Remove the hood lock and adjust the height by rotating the bumper rubber until the hood becomes 1 to1.5
mm (0.04 to 0.059 in) lower than the fender.
2. Temporarily tighten the hood lock, and position it by engaging it with the hood striker. Check the lock and
striker for looseness, and tighten the hood lock mounting bolts to the specified torque.
SURFACE HEIGHT ADJUSTMENT
1. Remove hood lock, and adjust the surface height difference of hood, fender and headlamp according to
the fitting standard dimension, by rotating RH and LH bumper rubbers.
2. Install hood lock temporarily, and move hood lock laterally until the centers of striker and lock become ver-
tical when viewed from the front.
1. Hood hinge 2. Nut 3. Hood stay
4. Hood lock 5. Bolt 6. Bumper rubber
PIIB1212E
Hood and headlamp (C–C) : Less than 2.0 mm (0.08in)
Page 822 of 4449
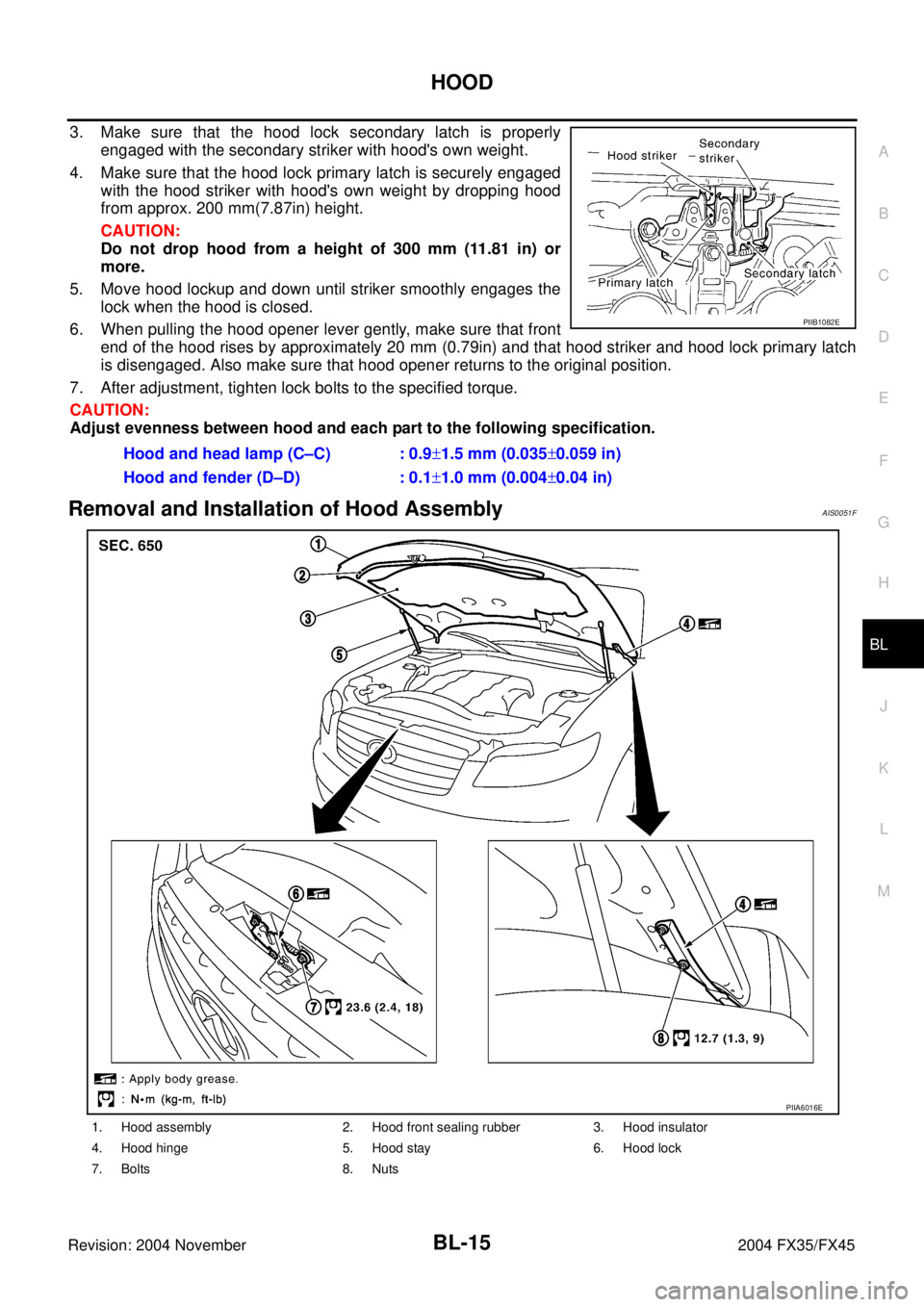
HOOD
BL-15
C
D
E
F
G
H
J
K
L
MA
B
BL
Revision: 2004 November 2004 FX35/FX45
3. Make sure that the hood lock secondary latch is properly
engaged with the secondary striker with hood's own weight.
4. Make sure that the hood lock primary latch is securely engaged
with the hood striker with hood's own weight by dropping hood
from approx. 200 mm(7.87in) height.
CAUTION:
Do not drop hood from a height of 300 mm (11.81 in) or
more.
5. Move hood lockup and down until striker smoothly engages the
lock when the hood is closed.
6. When pulling the hood opener lever gently, make sure that front
end of the hood rises by approximately 20 mm (0.79in) and that hood striker and hood lock primary latch
is disengaged. Also make sure that hood opener returns to the original position.
7. After adjustment, tighten lock bolts to the specified torque.
CAUTION:
Adjust evenness between hood and each part to the following specification.
Removal and Installation of Hood AssemblyAIS0051F
Hood and head lamp (C–C) : 0.9±1.5 mm (0.035±0.059 in)
Hood and fender (D–D) : 0.1±1.0 mm (0.004±0.04 in)
PIIB1082E
1. Hood assembly 2. Hood front sealing rubber 3. Hood insulator
4. Hood hinge 5. Hood stay 6. Hood lock
7. Bolts 8. Nuts
PIIA6016E
Page 823 of 4449
BL-16
HOOD
Revision: 2004 November 2004 FX35/FX45
REMOVAL
1. Support the hood striker with a proper material to prevent it from
falling.
WARNING:
Body injury may occur if no supporting rod is holding the
hood open when removing the hood stay.
2. Remove the hood stays from the stud balls on the body side.
3. Remove the hinge mounting nuts on the hood to remove the hood assembly.
CAUTION:
Operate with two workers, because of its heavy weight.
INSTALLATION
Install in the reverse order of removal.
Removal and Installation of Hood Lock ControlAIS0051G
REMOVAL
1. Remove the front grill. Refer to EI-23, "Removal and Installation" .
2. Remove the front fender protector (LH). Refer to EI-25, "
Removal and Installation" .
3. Disconnect the hood lock cable from the hood lock, and clip it from the radiator core support upper and
hood ledge.
PIIA6058E
1. Hood lock 2. Hood lock cable 3. Clip
4. Hood ledge upper front LH 5. Dash lower cross member reinforce LH
PIIA6017E
Page 824 of 4449
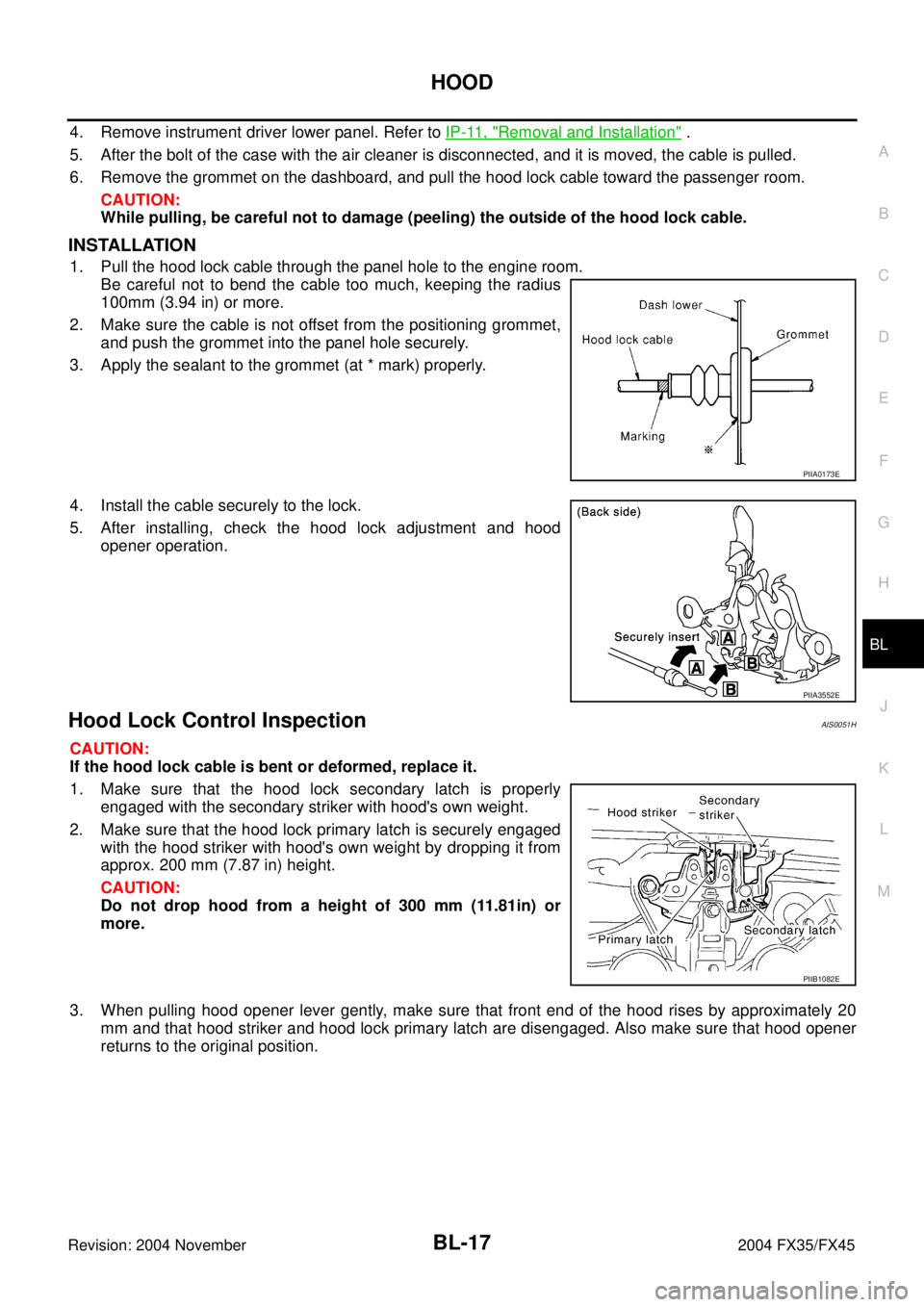
HOOD
BL-17
C
D
E
F
G
H
J
K
L
MA
B
BL
Revision: 2004 November 2004 FX35/FX45
4. Remove instrument driver lower panel. Refer to IP-11, "Removal and Installation" .
5. After the bolt of the case with the air cleaner is disconnected, and it is moved, the cable is pulled.
6. Remove the grommet on the dashboard, and pull the hood lock cable toward the passenger room.
CAUTION:
While pulling, be careful not to damage (peeling) the outside of the hood lock cable.
INSTALLATION
1. Pull the hood lock cable through the panel hole to the engine room.
Be careful not to bend the cable too much, keeping the radius
100mm (3.94 in) or more.
2. Make sure the cable is not offset from the positioning grommet,
and push the grommet into the panel hole securely.
3. Apply the sealant to the grommet (at * mark) properly.
4. Install the cable securely to the lock.
5. After installing, check the hood lock adjustment and hood
opener operation.
Hood Lock Control InspectionAIS0051H
CAUTION:
If the hood lock cable is bent or deformed, replace it.
1. Make sure that the hood lock secondary latch is properly
engaged with the secondary striker with hood's own weight.
2. Make sure that the hood lock primary latch is securely engaged
with the hood striker with hood's own weight by dropping it from
approx. 200 mm (7.87 in) height.
CAUTION:
Do not drop hood from a height of 300 mm (11.81in) or
more.
3. When pulling hood opener lever gently, make sure that front end of the hood rises by approximately 20
mm and that hood striker and hood lock primary latch are disengaged. Also make sure that hood opener
returns to the original position.
PIIA0173E
PIIA3552E
PIIB1082E