Page 3065 of 4449
FFD-30
FRONT FINAL DRIVE ASSEMBLY
Revision: 2004 November 2004 FX35/FX45
TOOTH CONTACT INSPECTION
Checking gear tooth contact pattern is necessary to verify correct relationship between drive gear and drive
pinion.
Hypoid gears which are not positioned in proper arrangement may be noisy and/or have a short life. Check
gear tooth contact pattern to obtain the best contact for low noise and long life.
1. Thoroughly clean drive gear and drive pinion teeth.
2. Lightly apply a mixture of powdered ferric oxide and oil or the
equivalent. Apply it to 3 or 4 teeth on the drive side of drive
gear.
3. Hold companion flange steady by hand and rotate the drive gear
in both directions.
4. Check the tooth contact on both sides (drive side and coast
side).
NOTE:
Refer to FFD-31, "
TOOTH CONTACT PATTERN AND HEIGHT
ADJUSTING WASHER SELECTION" for detail of tooth contact
pattern.
SDIA0054J
SDIA1711E
Page 3066 of 4449
FRONT FINAL DRIVE ASSEMBLY
FFD-31
C
E
F
G
H
I
J
K
L
MA
B
FFD
Revision: 2004 November 2004 FX35/FX45
TOOTH CONTACT PATTERN AND HEIGHT ADJUSTING WASHER SELECTION
TOOTH CONTACT ADJUSTMENT
1. If tooth contact is incorrect, adjust tooth contact by replacing
drive pinion height adjusting washer.
SDIA1673E
SDIA0057J
Page 3067 of 4449
FFD-32
FRONT FINAL DRIVE ASSEMBLY
Revision: 2004 November 2004 FX35/FX45
2. If there is heel contact or face contact, increase point height
adjusting washer in order to bring drive pinion close to drive
gear.
3. If there is toe contact or flank contact, decrease pinion adjusting
washer in order to make drive pinion go away from drive gear.
4. Set dial indicator to the drive gear face and measure the bak-
clash.
If the measured value out of standard, adjust the backlash by
replacing the side bearing adjusting shim (carrier case side).
–If backlash too large, decrease side bearing adjusting shim
thickness.
–If backlash too small, increase side bearing adjusting shim
thickness.
SDIA1712E
SDIA1713E
Standard drive gear back-
lash: 0.10 - 0.15 mm
(0.0039 - 0.0059 in)
SDIA0009J
Page 3068 of 4449
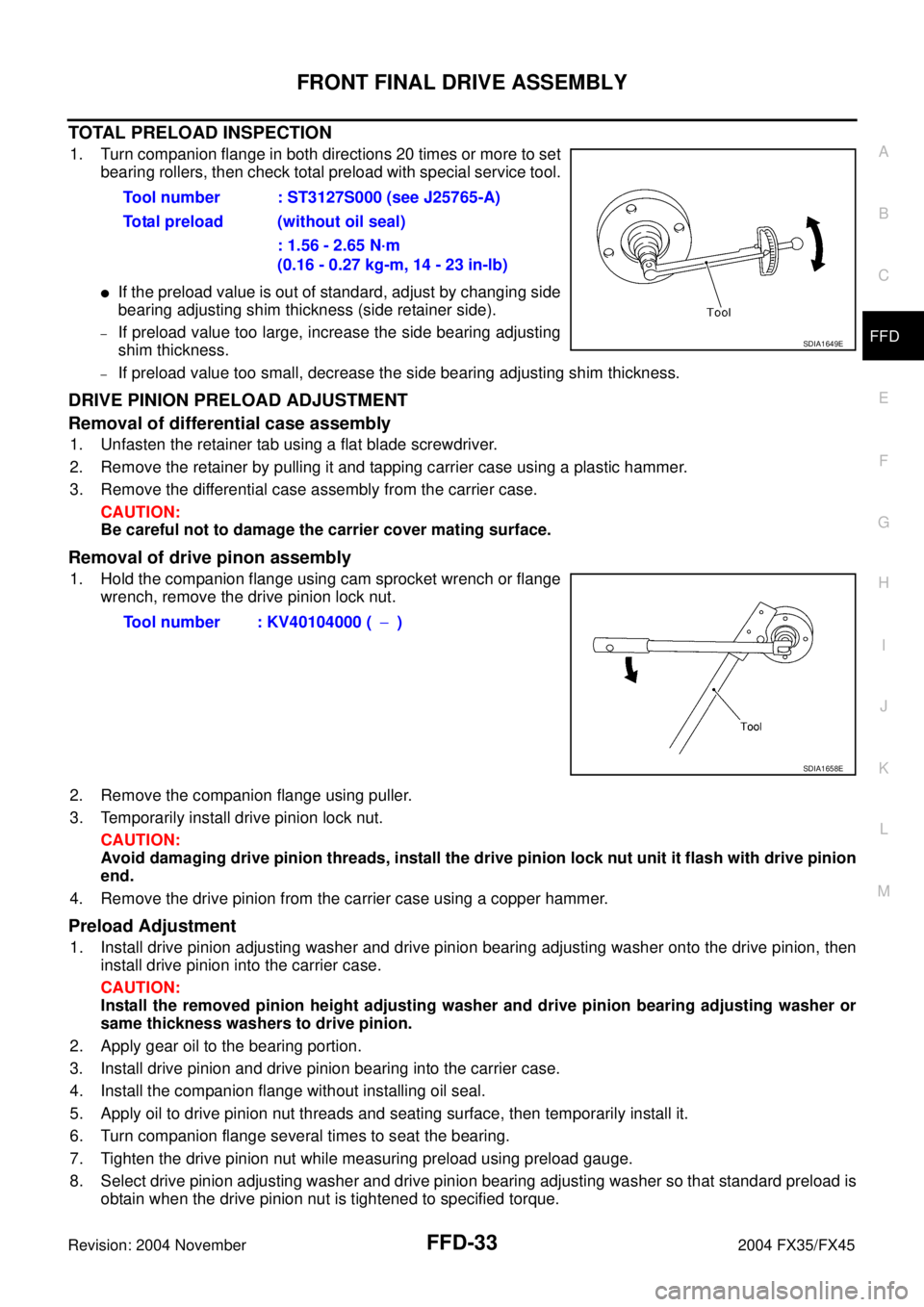
FRONT FINAL DRIVE ASSEMBLY
FFD-33
C
E
F
G
H
I
J
K
L
MA
B
FFD
Revision: 2004 November 2004 FX35/FX45
TOTAL PRELOAD INSPECTION
1. Turn companion flange in both directions 20 times or more to set
bearing rollers, then check total preload with special service tool.
If the preload value is out of standard, adjust by changing side
bearing adjusting shim thickness (side retainer side).
–If preload value too large, increase the side bearing adjusting
shim thickness.
–If preload value too small, decrease the side bearing adjusting shim thickness.
DRIVE PINION PRELOAD ADJUSTMENT
Removal of differential case assembly
1. Unfasten the retainer tab using a flat blade screwdriver.
2. Remove the retainer by pulling it and tapping carrier case using a plastic hammer.
3. Remove the differential case assembly from the carrier case.
CAUTION:
Be careful not to damage the carrier cover mating surface.
Removal of drive pinon assembly
1. Hold the companion flange using cam sprocket wrench or flange
wrench, remove the drive pinion lock nut.
2. Remove the companion flange using puller.
3. Temporarily install drive pinion lock nut.
CAUTION:
Avoid damaging drive pinion threads, install the drive pinion lock nut unit it flash with drive pinion
end.
4. Remove the drive pinion from the carrier case using a copper hammer.
Preload Adjustment
1. Install drive pinion adjusting washer and drive pinion bearing adjusting washer onto the drive pinion, then
install drive pinion into the carrier case.
CAUTION:
Install the removed pinion height adjusting washer and drive pinion bearing adjusting washer or
same thickness washers to drive pinion.
2. Apply gear oil to the bearing portion.
3. Install drive pinion and drive pinion bearing into the carrier case.
4. Install the companion flange without installing oil seal.
5. Apply oil to drive pinion nut threads and seating surface, then temporarily install it.
6. Turn companion flange several times to seat the bearing.
7. Tighten the drive pinion nut while measuring preload using preload gauge.
8. Select drive pinion adjusting washer and drive pinion bearing adjusting washer so that standard preload is
obtain when the drive pinion nut is tightened to specified torque.Tool number : ST3127S000 (see J25765-A)
Total preload (without oil seal)
: 1.56 - 2.65 N·m
(0.16 - 0.27 kg-m, 14 - 23 in-lb)
SDIA1649E
Tool number : KV40104000 (−)
SDIA1658E
Page 3069 of 4449
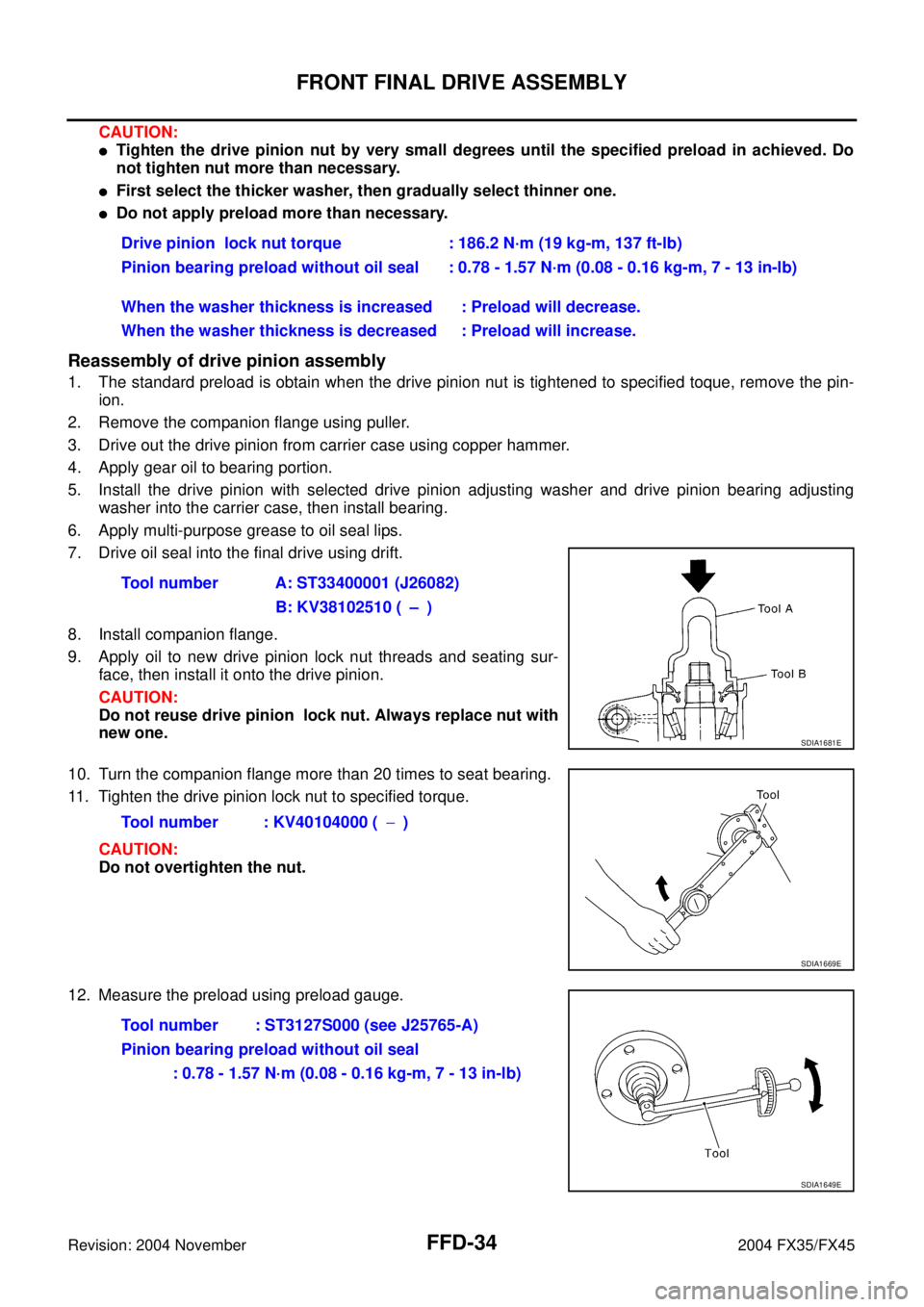
FFD-34
FRONT FINAL DRIVE ASSEMBLY
Revision: 2004 November 2004 FX35/FX45
CAUTION:
Tighten the drive pinion nut by very small degrees until the specified preload in achieved. Do
not tighten nut more than necessary.
First select the thicker washer, then gradually select thinner one.
Do not apply preload more than necessary.
Reassembly of drive pinion assembly
1. The standard preload is obtain when the drive pinion nut is tightened to specified toque, remove the pin-
ion.
2. Remove the companion flange using puller.
3. Drive out the drive pinion from carrier case using copper hammer.
4. Apply gear oil to bearing portion.
5. Install the drive pinion with selected drive pinion adjusting washer and drive pinion bearing adjusting
washer into the carrier case, then install bearing.
6. Apply multi-purpose grease to oil seal lips.
7. Drive oil seal into the final drive using drift.
8. Install companion flange.
9. Apply oil to new drive pinion lock nut threads and seating sur-
face, then install it onto the drive pinion.
CAUTION:
Do not reuse drive pinion lock nut. Always replace nut with
new one.
10. Turn the companion flange more than 20 times to seat bearing.
11. Tighten the drive pinion lock nut to specified torque.
CAUTION:
Do not overtighten the nut.
12. Measure the preload using preload gauge.Drive pinion lock nut torque : 186.2 N·m (19 kg-m, 137 ft-lb)
Pinion bearing preload without oil seal : 0.78 - 1.57 N·m (0.08 - 0.16 kg-m, 7 - 13 in-lb)
When the washer thickness is increased : Preload will decrease.
When the washer thickness is decreased : Preload will increase.
Tool number A: ST33400001 (J26082)
B: KV38102510 ( – )
SDIA1681E
Tool number : KV40104000 (−)
SDIA1669E
Tool number : ST3127S000 (see J25765-A)
Pinion bearing preload without oil seal
: 0.78 - 1.57 N·m (0.08 - 0.16 kg-m, 7 - 13 in-lb)
SDIA1649E
Page 3070 of 4449
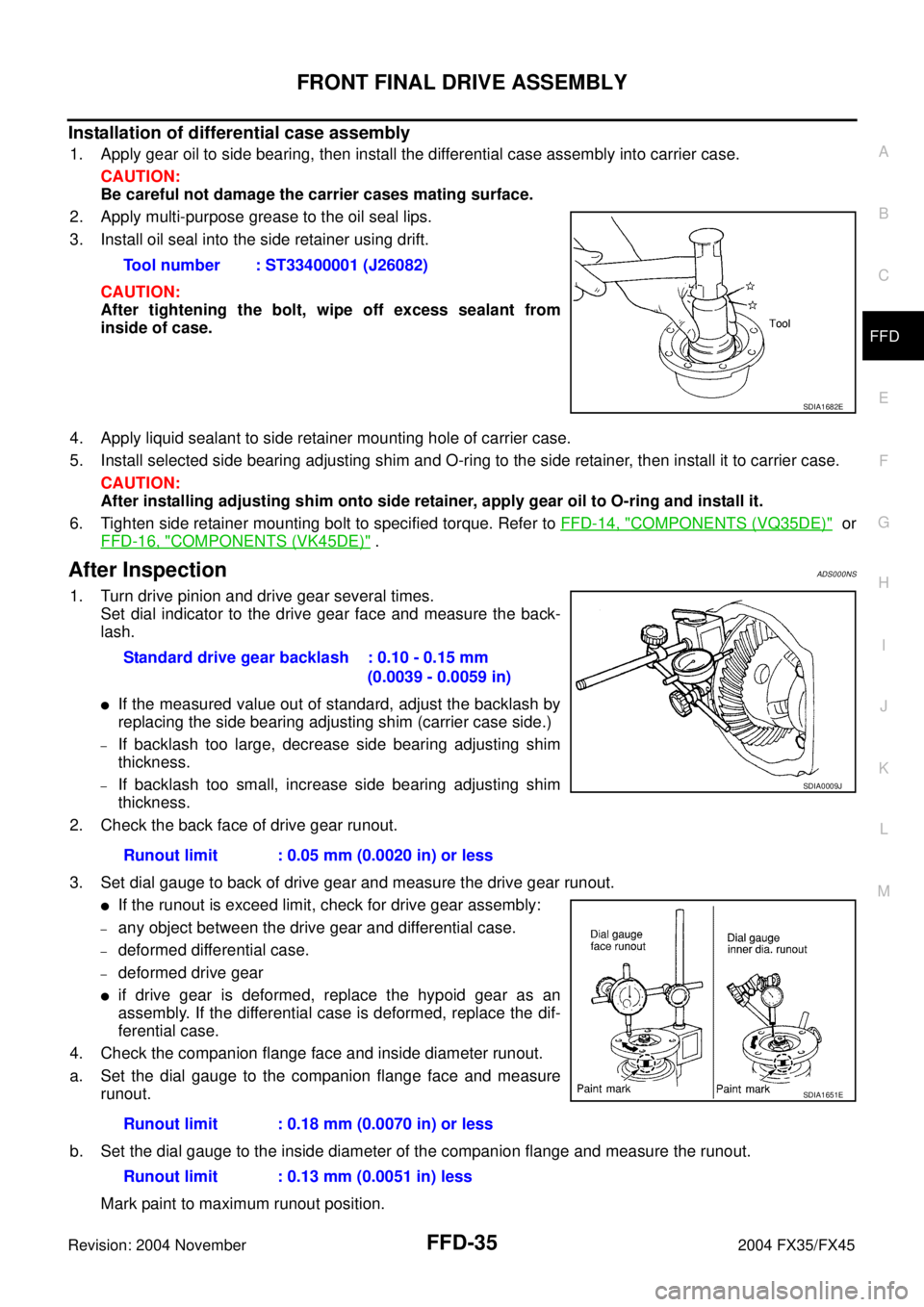
FRONT FINAL DRIVE ASSEMBLY
FFD-35
C
E
F
G
H
I
J
K
L
MA
B
FFD
Revision: 2004 November 2004 FX35/FX45
Installation of differential case assembly
1. Apply gear oil to side bearing, then install the differential case assembly into carrier case.
CAUTION:
Be careful not damage the carrier cases mating surface.
2. Apply multi-purpose grease to the oil seal lips.
3. Install oil seal into the side retainer using drift.
CAUTION:
After tightening the bolt, wipe off excess sealant from
inside of case.
4. Apply liquid sealant to side retainer mounting hole of carrier case.
5. Install selected side bearing adjusting shim and O-ring to the side retainer, then install it to carrier case.
CAUTION:
After installing adjusting shim onto side retainer, apply gear oil to O-ring and install it.
6. Tighten side retainer mounting bolt to specified torque. Refer to FFD-14, "
COMPONENTS (VQ35DE)" or
FFD-16, "
COMPONENTS (VK45DE)" .
After InspectionADS000NS
1. Turn drive pinion and drive gear several times.
Set dial indicator to the drive gear face and measure the back-
lash.
If the measured value out of standard, adjust the backlash by
replacing the side bearing adjusting shim (carrier case side.)
–If backlash too large, decrease side bearing adjusting shim
thickness.
–If backlash too small, increase side bearing adjusting shim
thickness.
2. Check the back face of drive gear runout.
3. Set dial gauge to back of drive gear and measure the drive gear runout.
If the runout is exceed limit, check for drive gear assembly:
–any object between the drive gear and differential case.
–deformed differential case.
–deformed drive gear
if drive gear is deformed, replace the hypoid gear as an
assembly. If the differential case is deformed, replace the dif-
ferential case.
4. Check the companion flange face and inside diameter runout.
a. Set the dial gauge to the companion flange face and measure
runout.
b. Set the dial gauge to the inside diameter of the companion flange and measure the runout.
Mark paint to maximum runout position.Tool number : ST33400001 (J26082)
SDIA1682E
Standard drive gear backlash : 0.10 - 0.15 mm
(0.0039 - 0.0059 in)
Runout limit : 0.05 mm (0.0020 in) or less
Runout limit : 0.18 mm (0.0070 in) or less
Runout limit : 0.13 mm (0.0051 in) less
SDIA0009J
SDIA1651E
Page 3071 of 4449
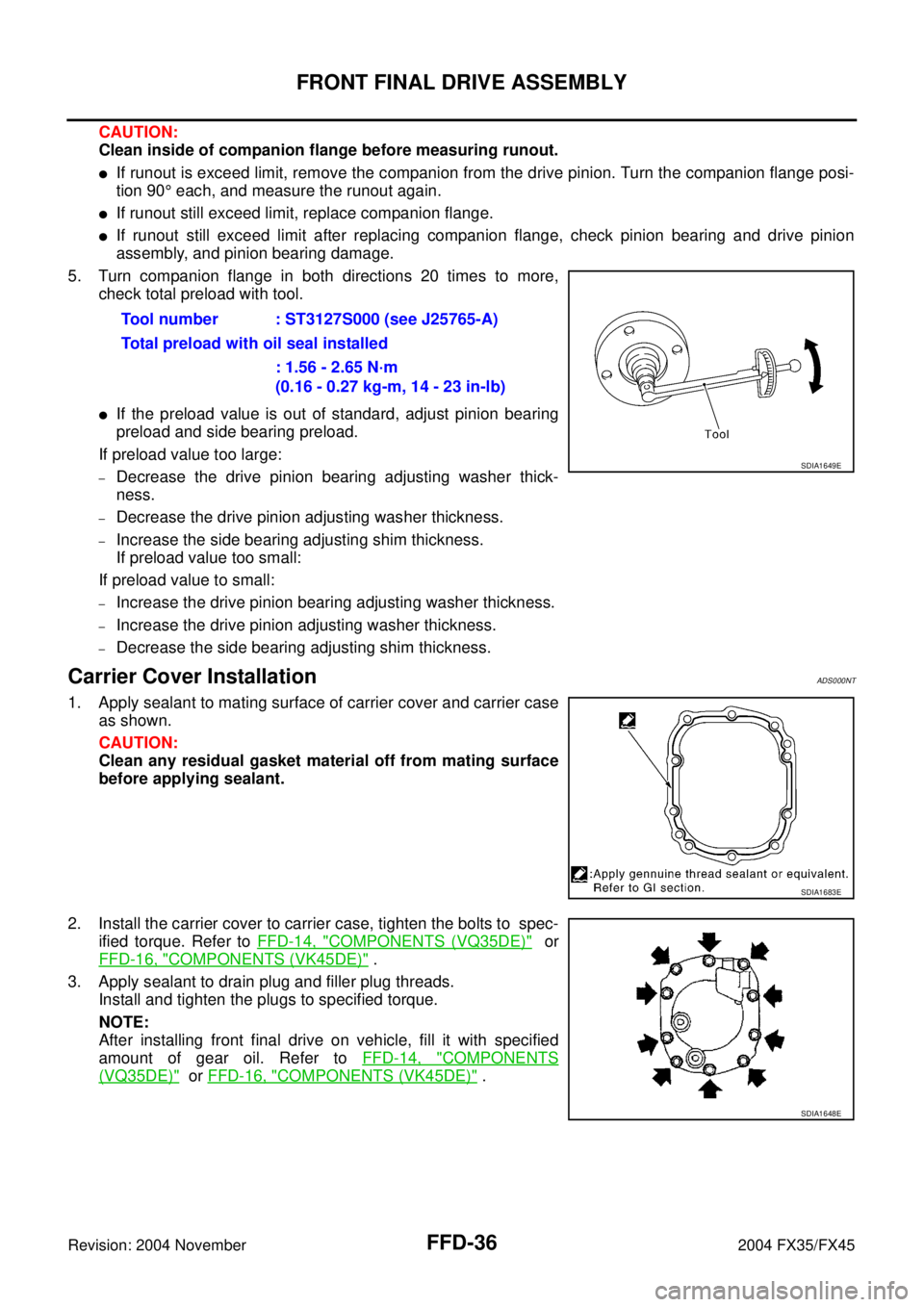
FFD-36
FRONT FINAL DRIVE ASSEMBLY
Revision: 2004 November 2004 FX35/FX45
CAUTION:
Clean inside of companion flange before measuring runout.
If runout is exceed limit, remove the companion from the drive pinion. Turn the companion flange posi-
tion 90° each, and measure the runout again.
If runout still exceed limit, replace companion flange.
If runout still exceed limit after replacing companion flange, check pinion bearing and drive pinion
assembly, and pinion bearing damage.
5. Turn companion flange in both directions 20 times to more,
check total preload with tool.
If the preload value is out of standard, adjust pinion bearing
preload and side bearing preload.
If preload value too large:
–Decrease the drive pinion bearing adjusting washer thick-
ness.
–Decrease the drive pinion adjusting washer thickness.
–Increase the side bearing adjusting shim thickness.
If preload value too small:
If preload value to small:
–Increase the drive pinion bearing adjusting washer thickness.
–Increase the drive pinion adjusting washer thickness.
–Decrease the side bearing adjusting shim thickness.
Carrier Cover InstallationADS000NT
1. Apply sealant to mating surface of carrier cover and carrier case
as shown.
CAUTION:
Clean any residual gasket material off from mating surface
before applying sealant.
2. Install the carrier cover to carrier case, tighten the bolts to spec-
ified torque. Refer to FFD-14, "
COMPONENTS (VQ35DE)" or
FFD-16, "
COMPONENTS (VK45DE)" .
3. Apply sealant to drain plug and filler plug threads.
Install and tighten the plugs to specified torque.
NOTE:
After installing front final drive on vehicle, fill it with specified
amount of gear oil. Refer to FFD-14, "
COMPONENTS
(VQ35DE)" or FFD-16, "COMPONENTS (VK45DE)" . Tool number : ST3127S000 (see J25765-A)
Total preload with oil seal installed
: 1.56 - 2.65 N·m
(0.16 - 0.27 kg-m, 14 - 23 in-lb)
SDIA1649E
SDIA1683E
SDIA1648E
Page 3072 of 4449
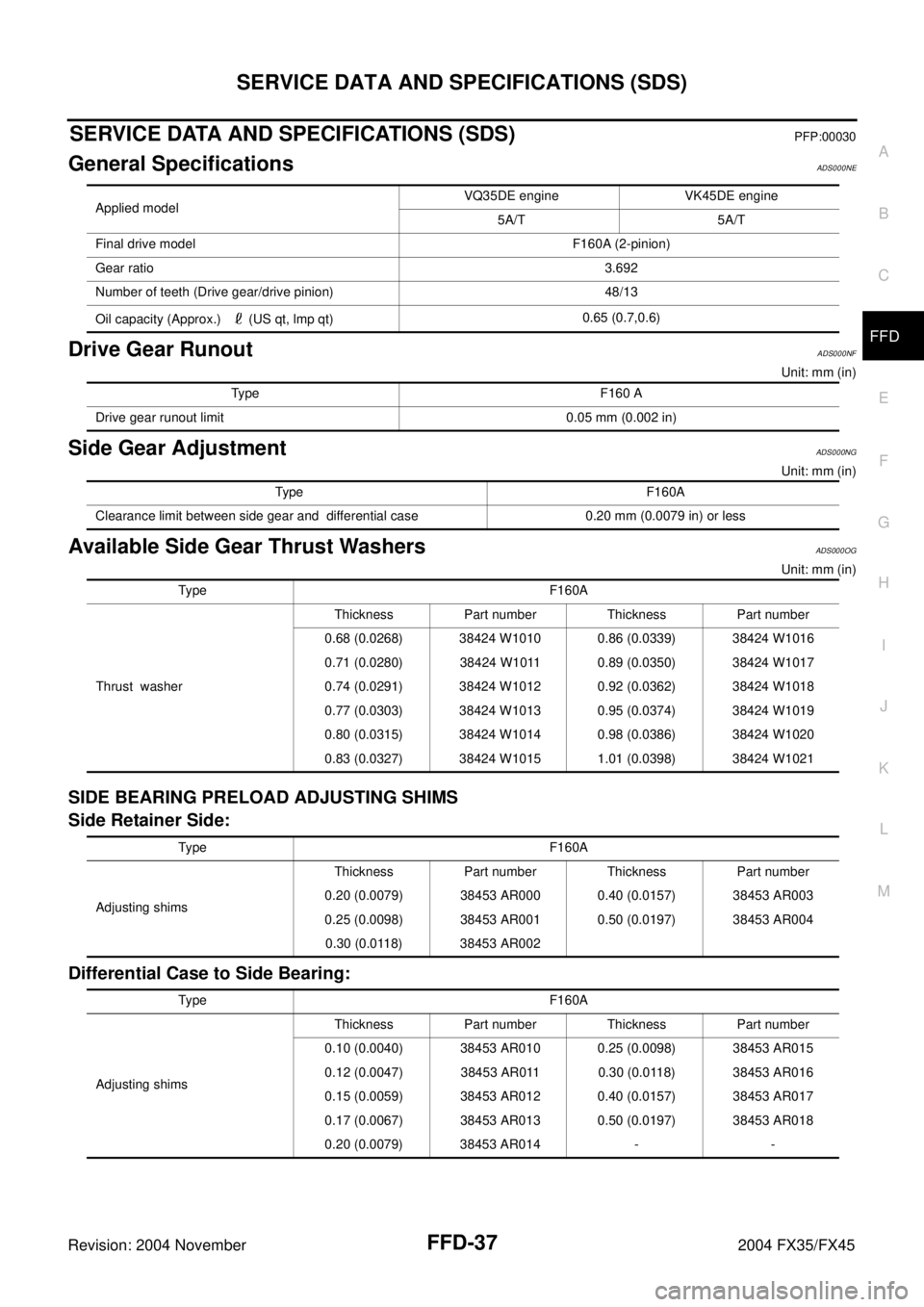
SERVICE DATA AND SPECIFICATIONS (SDS)
FFD-37
C
E
F
G
H
I
J
K
L
MA
B
FFD
Revision: 2004 November 2004 FX35/FX45
SERVICE DATA AND SPECIFICATIONS (SDS)PFP:00030
General SpecificationsADS000NE
Drive Gear RunoutADS000NF
Unit: mm (in)
Side Gear Adjustment ADS000NG
Unit: mm (in)
Available Side Gear Thrust WashersADS000OG
Unit: mm (in)
SIDE BEARING PRELOAD ADJUSTING SHIMS
Side Retainer Side:
Differential Case to Side Bearing:
Applied modelVQ35DE engine VK45DE engine
5A/T 5A/T
Final drive model F160A (2-pinion)
Gear ratio3.692
Number of teeth (Drive gear/drive pinion) 48/13
Oil capacity (Approx.) (US qt, lmp qt)0.65 (0.7,0.6)
Type F160 A
Drive gear runout limit 0.05 mm (0.002 in)
Type F16 0A
Clearance limit between side gear and differential case 0.20 mm (0.0079 in) or less
Type F16 0A
Thrust washerThickness Part number Thickness Part number
0.68 (0.0268) 38424 W1010 0.86 (0.0339) 38424 W1016
0.71 (0.0280) 38424 W1011 0.89 (0.0350) 38424 W1017
0.74 (0.0291) 38424 W1012 0.92 (0.0362) 38424 W1018
0.77 (0.0303) 38424 W1013 0.95 (0.0374) 38424 W1019
0.80 (0.0315) 38424 W1014 0.98 (0.0386) 38424 W1020
0.83 (0.0327) 38424 W1015 1.01 (0.0398) 38424 W1021
Type F16 0A
Adjusting shimsThickness Part number Thickness Part number
0.20 (0.0079) 38453 AR000 0.40 (0.0157) 38453 AR003
0.25 (0.0098) 38453 AR001 0.50 (0.0197) 38453 AR004
0.30 (0.0118) 38453 AR002
Type F16 0A
Adjusting shimsThickness Part number Thickness Part number
0.10 (0.0040) 38453 AR010 0.25 (0.0098) 38453 AR015
0.12 (0.0047) 38453 AR011 0.30 (0.0118) 38453 AR016
0.15 (0.0059) 38453 AR012 0.40 (0.0157) 38453 AR017
0.17 (0.0067) 38453 AR013 0.50 (0.0197) 38453 AR018
0.20 (0.0079) 38453 AR014 - -