Page 3929 of 4449
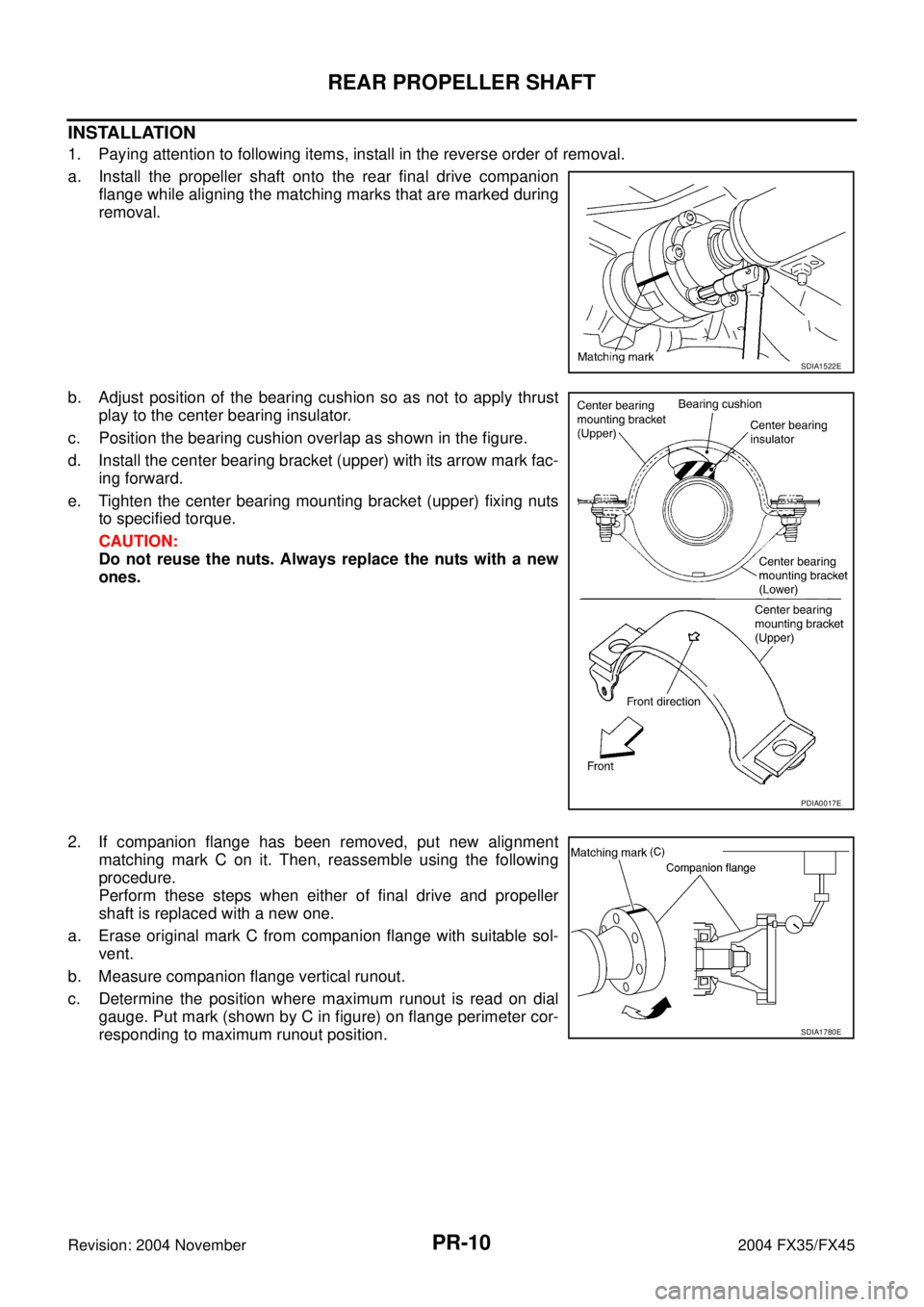
PR-10
REAR PROPELLER SHAFT
Revision: 2004 November 2004 FX35/FX45
INSTALLATION
1. Paying attention to following items, install in the reverse order of removal.
a. Install the propeller shaft onto the rear final drive companion
flange while aligning the matching marks that are marked during
removal.
b. Adjust position of the bearing cushion so as not to apply thrust
play to the center bearing insulator.
c. Position the bearing cushion overlap as shown in the figure.
d. Install the center bearing bracket (upper) with its arrow mark fac-
ing forward.
e. Tighten the center bearing mounting bracket (upper) fixing nuts
to specified torque.
CAUTION:
Do not reuse the nuts. Always replace the nuts with a new
ones.
2. If companion flange has been removed, put new alignment
matching mark C on it. Then, reassemble using the following
procedure.
Perform these steps when either of final drive and propeller
shaft is replaced with a new one.
a. Erase original mark C from companion flange with suitable sol-
vent.
b. Measure companion flange vertical runout.
c. Determine the position where maximum runout is read on dial
gauge. Put mark (shown by C in figure) on flange perimeter cor-
responding to maximum runout position.
SDIA1522E
PDIA0017E
SDIA1780E
Page 3930 of 4449
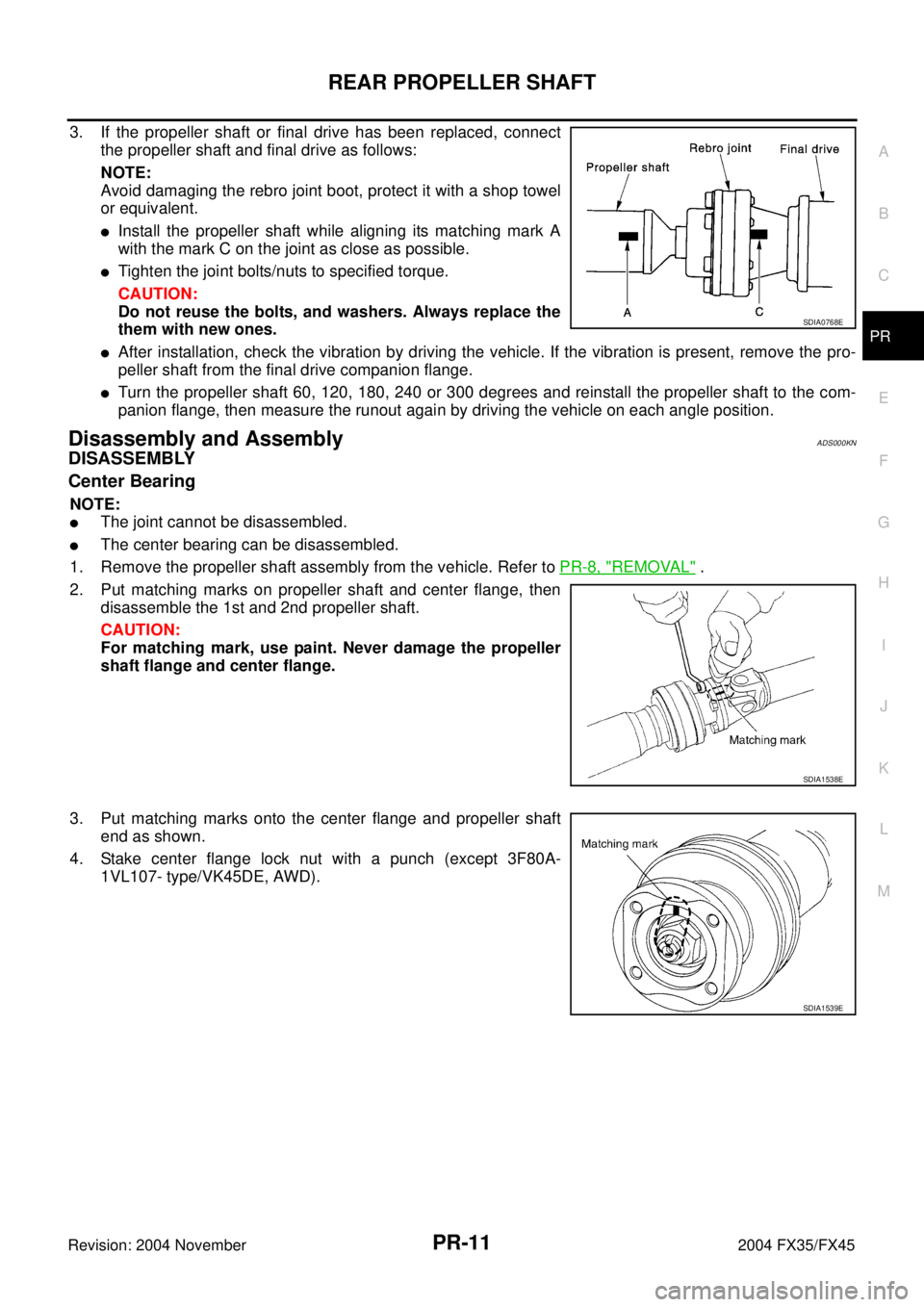
REAR PROPELLER SHAFT
PR-11
C
E
F
G
H
I
J
K
L
MA
B
PR
Revision: 2004 November 2004 FX35/FX45
3. If the propeller shaft or final drive has been replaced, connect
the propeller shaft and final drive as follows:
NOTE:
Avoid damaging the rebro joint boot, protect it with a shop towel
or equivalent.
Install the propeller shaft while aligning its matching mark A
with the mark C on the joint as close as possible.
Tighten the joint bolts/nuts to specified torque.
CAUTION:
Do not reuse the bolts, and washers. Always replace the
them with new ones.
After installation, check the vibration by driving the vehicle. If the vibration is present, remove the pro-
peller shaft from the final drive companion flange.
Turn the propeller shaft 60, 120, 180, 240 or 300 degrees and reinstall the propeller shaft to the com-
panion flange, then measure the runout again by driving the vehicle on each angle position.
Disassembly and AssemblyADS000KN
DISASSEMBLY
Center Bearing
NOTE:
The joint cannot be disassembled.
The center bearing can be disassembled.
1. Remove the propeller shaft assembly from the vehicle. Refer to PR-8, "
REMOVAL" .
2. Put matching marks on propeller shaft and center flange, then
disassemble the 1st and 2nd propeller shaft.
CAUTION:
For matching mark, use paint. Never damage the propeller
shaft flange and center flange.
3. Put matching marks onto the center flange and propeller shaft
end as shown.
4. Stake center flange lock nut with a punch (except 3F80A-
1VL107- type/VK45DE, AWD).
SDIA0768E
SDIA1538E
SDIA1539E
Page 3931 of 4449
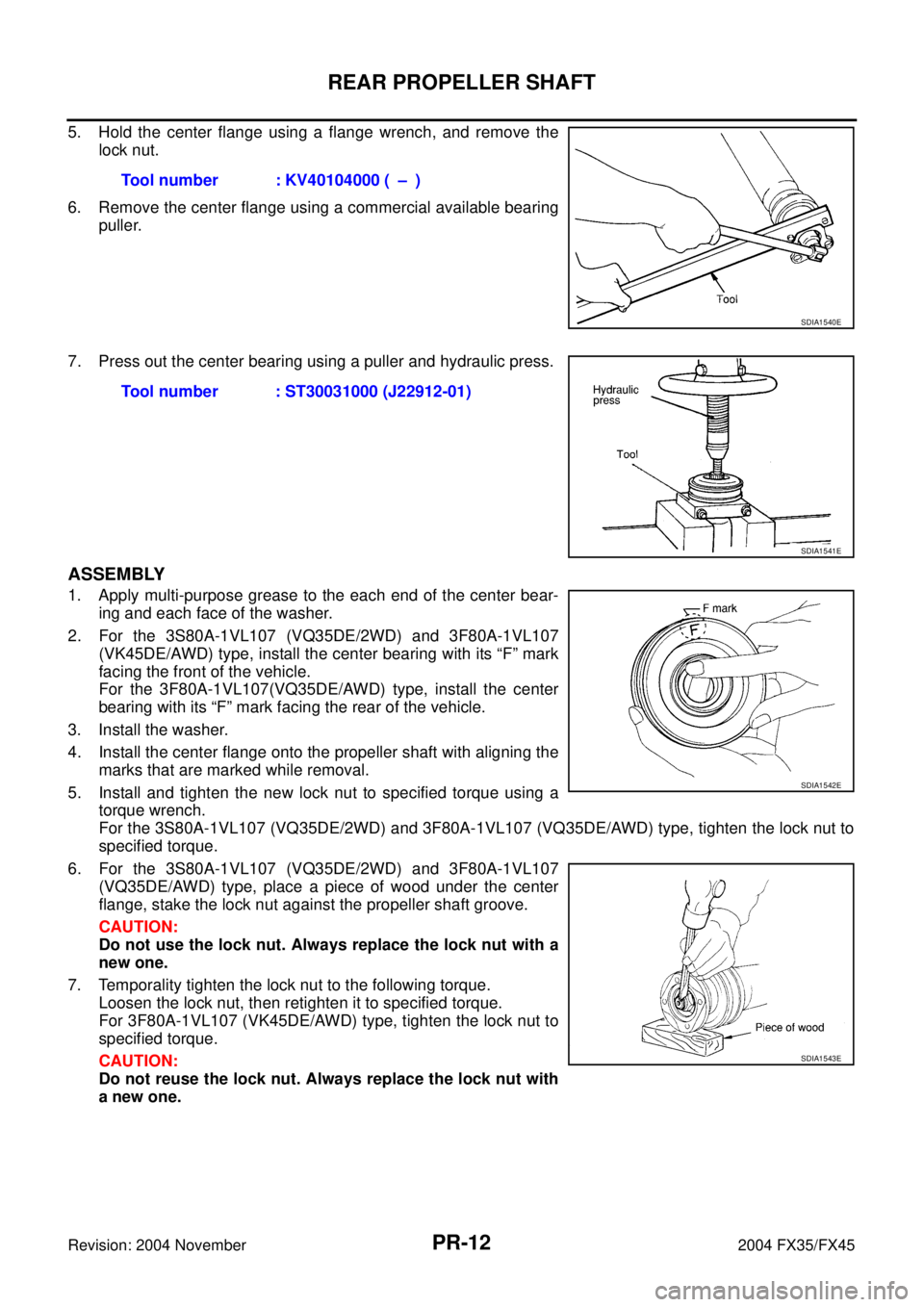
PR-12
REAR PROPELLER SHAFT
Revision: 2004 November 2004 FX35/FX45
5. Hold the center flange using a flange wrench, and remove the
lock nut.
6. Remove the center flange using a commercial available bearing
puller.
7. Press out the center bearing using a puller and hydraulic press.
ASSEMBLY
1. Apply multi-purpose grease to the each end of the center bear-
ing and each face of the washer.
2. For the 3S80A-1VL107 (VQ35DE/2WD) and 3F80A-1VL107
(VK45DE/AWD) type, install the center bearing with its “F” mark
facing the front of the vehicle.
For the 3F80A-1VL107(VQ35DE/AWD) type, install the center
bearing with its “F” mark facing the rear of the vehicle.
3. Install the washer.
4. Install the center flange onto the propeller shaft with aligning the
marks that are marked while removal.
5. Install and tighten the new lock nut to specified torque using a
torque wrench.
For the 3S80A-1VL107 (VQ35DE/2WD) and 3F80A-1VL107 (VQ35DE/AWD) type, tighten the lock nut to
specified torque.
6. For the 3S80A-1VL107 (VQ35DE/2WD) and 3F80A-1VL107
(VQ35DE/AWD) type, place a piece of wood under the center
flange, stake the lock nut against the propeller shaft groove.
CAUTION:
Do not use the lock nut. Always replace the lock nut with a
new one.
7. Temporality tighten the lock nut to the following torque.
Loosen the lock nut, then retighten it to specified torque.
For 3F80A-1VL107 (VK45DE/AWD) type, tighten the lock nut to
specified torque.
CAUTION:
Do not reuse the lock nut. Always replace the lock nut with
a new one.Tool number : KV40104000 ( – )
SDIA1540E
Tool number : ST30031000 (J22912-01)
SDIA1541E
SDIA1542E
SDIA1543E
Page 3932 of 4449
REAR PROPELLER SHAFT
PR-13
C
E
F
G
H
I
J
K
L
MA
B
PR
Revision: 2004 November 2004 FX35/FX45
8. Assemble the 1st and 2nd shaft propeller shafts while aligning
the matching marks that are marked during removal.
9. Install and tighten the bolts/nuts and tighten them to specified
torque.
CAUTION:
Do not reuse the bolts, nuts and washers. Always replace
the them with new ones.
10. Recheck the tightening torque using a torque wrench.
11. Install the propeller shaft assembly. Refer to PR-10, "
INSTALLA-
TION" .SDIA1538E
Page 3933 of 4449
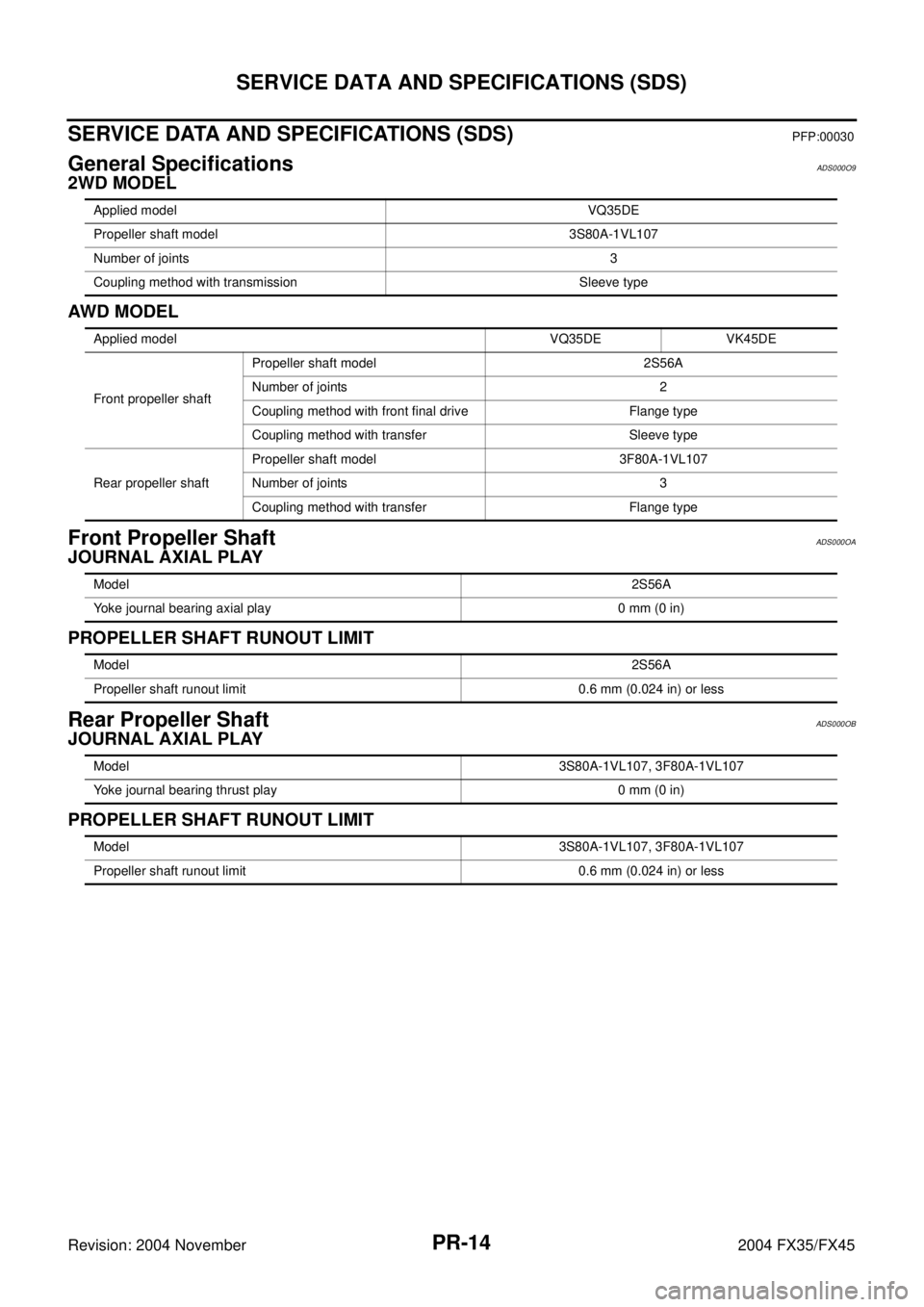
PR-14
SERVICE DATA AND SPECIFICATIONS (SDS)
Revision: 2004 November 2004 FX35/FX45
SERVICE DATA AND SPECIFICATIONS (SDS)PFP:00030
General SpecificationsADS000O9
2WD MODEL
AW D M OD E L
Front Propeller ShaftADS000OA
JOURNAL AXIAL PLAY
PROPELLER SHAFT RUNOUT LIMIT
Rear Propeller ShaftADS000OB
JOURNAL AXIAL PLAY
PROPELLER SHAFT RUNOUT LIMIT
Applied model VQ35DE
Propeller shaft model 3S80A-1VL107
Number of joints3
Coupling method with transmission Sleeve type
Applied model VQ35DE VK45DE
Front propeller shaftPropeller shaft model 2S56A
Number of joints 2
Coupling method with front final drive Flange type
Coupling method with transfer Sleeve type
Rear propeller shaftPropeller shaft model 3F80A-1VL107
Number of joints 3
Coupling method with transfer Flange type
Model2S56A
Yoke journal bearing axial play 0 mm (0 in)
Model2S56A
Propeller shaft runout limit 0.6 mm (0.024 in) or less
Model3S80A-1VL107, 3F80A-1VL107
Yoke journal bearing thrust play 0 mm (0 in)
Model3S80A-1VL107, 3F80A-1VL107
Propeller shaft runout limit 0.6 mm (0.024 in) or less
Page 3934 of 4449
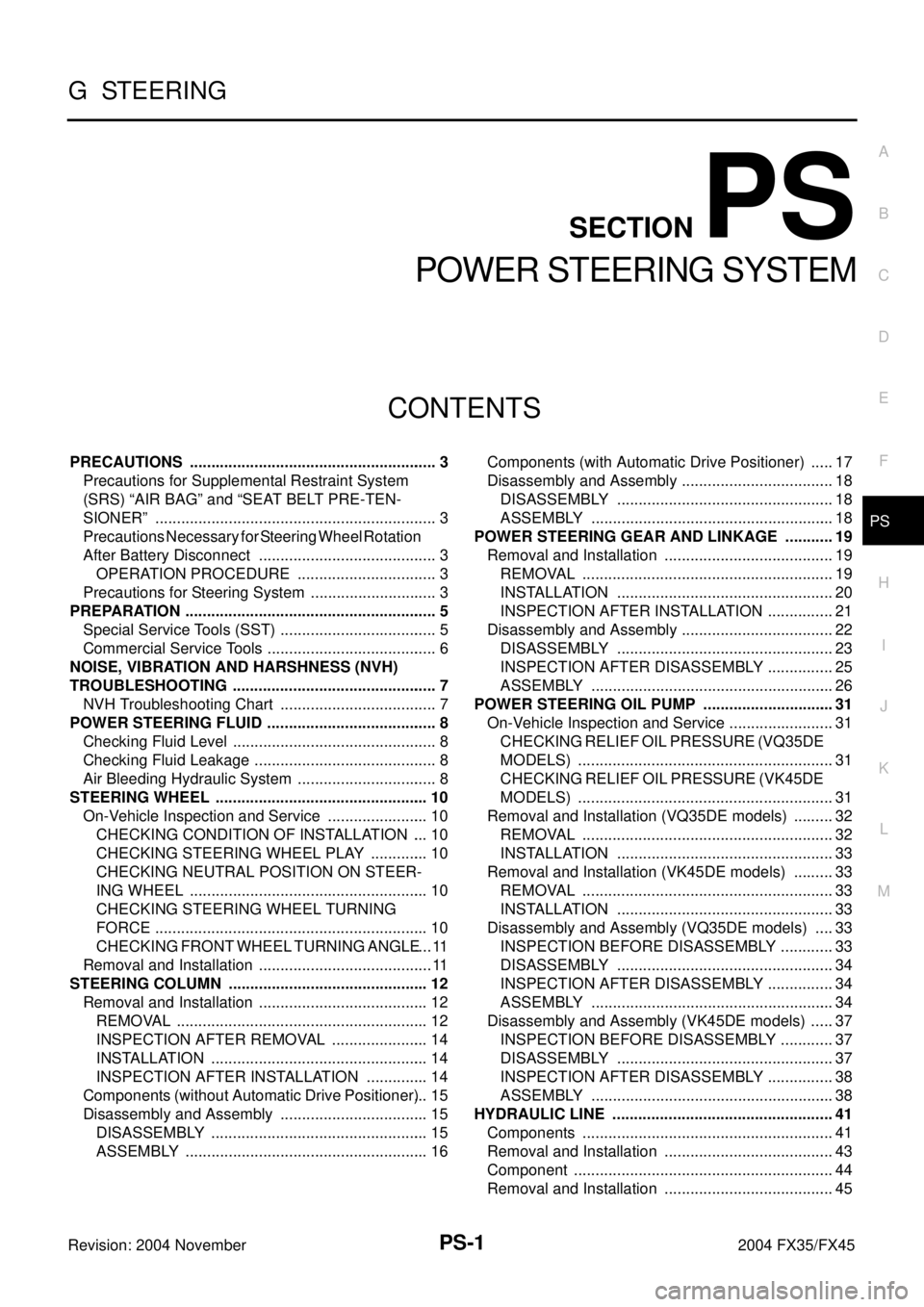
PS-1
POWER STEERING SYSTEM
G STEERING
CONTENTS
C
D
E
F
H
I
J
K
L
M
SECTION PS
A
B
PS
Revision: 2004 November 2004 FX35/FX45
POWER STEERING SYSTEM
PRECAUTIONS .......................................................... 3
Precautions for Supplemental Restraint System
(SRS) “AIR BAG” and “SEAT BELT PRE-TEN-
SIONER” .................................................................. 3
Precautions Necessary for Steering Wheel Rotation
After Battery Disconnect .......................................... 3
OPERATION PROCEDURE ................................. 3
Precautions for Steering System .............................. 3
PREPARATION ........................................................... 5
Special Service Tools (SST) ..................................... 5
Commercial Service Tools ........................................ 6
NOISE, VIBRATION AND HARSHNESS (NVH)
TROUBLESHOOTING ................................................ 7
NVH Troubleshooting Chart ..................................... 7
POWER STEERING FLUID ........................................ 8
Checking Fluid Level ................................................ 8
Checking Fluid Leakage ........................................... 8
Air Bleeding Hydraulic System ................................. 8
STEERING WHEEL .................................................. 10
On-Vehicle Inspection and Service ........................ 10
CHECKING CONDITION OF INSTALLATION .... 10
CHECKING STEERING WHEEL PLAY .............. 10
CHECKING NEUTRAL POSITION ON STEER-
ING WHEEL ........................................................ 10
CHECKING STEERING WHEEL TURNING
FORCE ................................................................ 10
CHECKING FRONT WHEEL TURNING ANGLE .... 11
Removal and Installation ......................................... 11
STEERING COLUMN ............................................... 12
Removal and Installation ........................................ 12
REMOVAL ........................................................... 12
INSPECTION AFTER REMOVAL ....................... 14
INSTALLATION ................................................... 14
INSPECTION AFTER INSTALLATION ............... 14
Components (without Automatic Drive Positioner) ... 15
Disassembly and Assembly ................................... 15
DISASSEMBLY ................................................... 15
ASSEMBLY ......................................................... 16Components (with Automatic Drive Positioner) ...... 17
Disassembly and Assembly .................................... 18
DISASSEMBLY ................................................... 18
ASSEMBLY ......................................................... 18
POWER STEERING GEAR AND LINKAGE ............ 19
Removal and Installation ........................................ 19
REMOVAL ........................................................... 19
INSTALLATION ................................................... 20
INSPECTION AFTER INSTALLATION ................ 21
Disassembly and Assembly .................................... 22
DISASSEMBLY ................................................... 23
INSPECTION AFTER DISASSEMBLY ................ 25
ASSEMBLY ......................................................... 26
POWER STEERING OIL PUMP ............................... 31
On-Vehicle Inspection and Service ......................... 31
CHECKING RELIEF OIL PRESSURE (VQ35DE
MODELS) ............................................................ 31
CHECKING RELIEF OIL PRESSURE (VK45DE
MODELS) ............................................................ 31
Removal and Installation (VQ35DE models) .......... 32
REMOVAL ........................................................... 32
INSTALLATION ................................................... 33
Removal and Installation (VK45DE models) .......... 33
REMOVAL ........................................................... 33
INSTALLATION ................................................... 33
Disassembly and Assembly (VQ35DE models) ..... 33
INSPECTION BEFORE DISASSEMBLY ............. 33
DISASSEMBLY ................................................... 34
INSPECTION AFTER DISASSEMBLY ................ 34
ASSEMBLY ......................................................... 34
Disassembly and Assembly (VK45DE models) ...... 37
INSPECTION BEFORE DISASSEMBLY ............. 37
DISASSEMBLY ................................................... 37
INSPECTION AFTER DISASSEMBLY ................ 38
ASSEMBLY ......................................................... 38
HYDRAULIC LINE .................................................... 41
Components ........................................................... 41
Removal and Installation ........................................ 43
Component ............................................................. 44
Removal and Installation ........................................ 45
Page 3935 of 4449
PS-2Revision: 2004 November 2004 FX35/FX45 SERVICE DATA AND SPECIFICATIONS (SDS) ...... 46
Steering Wheel ....................................................... 46
Steering Angle ........................................................ 46
Steering Column ..................................................... 46Steering Outer Socket and Inner Socket ................. 46
Steering Gear .......................................................... 47
Oil Pump ................................................................. 47
Steering Fluid .......................................................... 47
Page 3936 of 4449
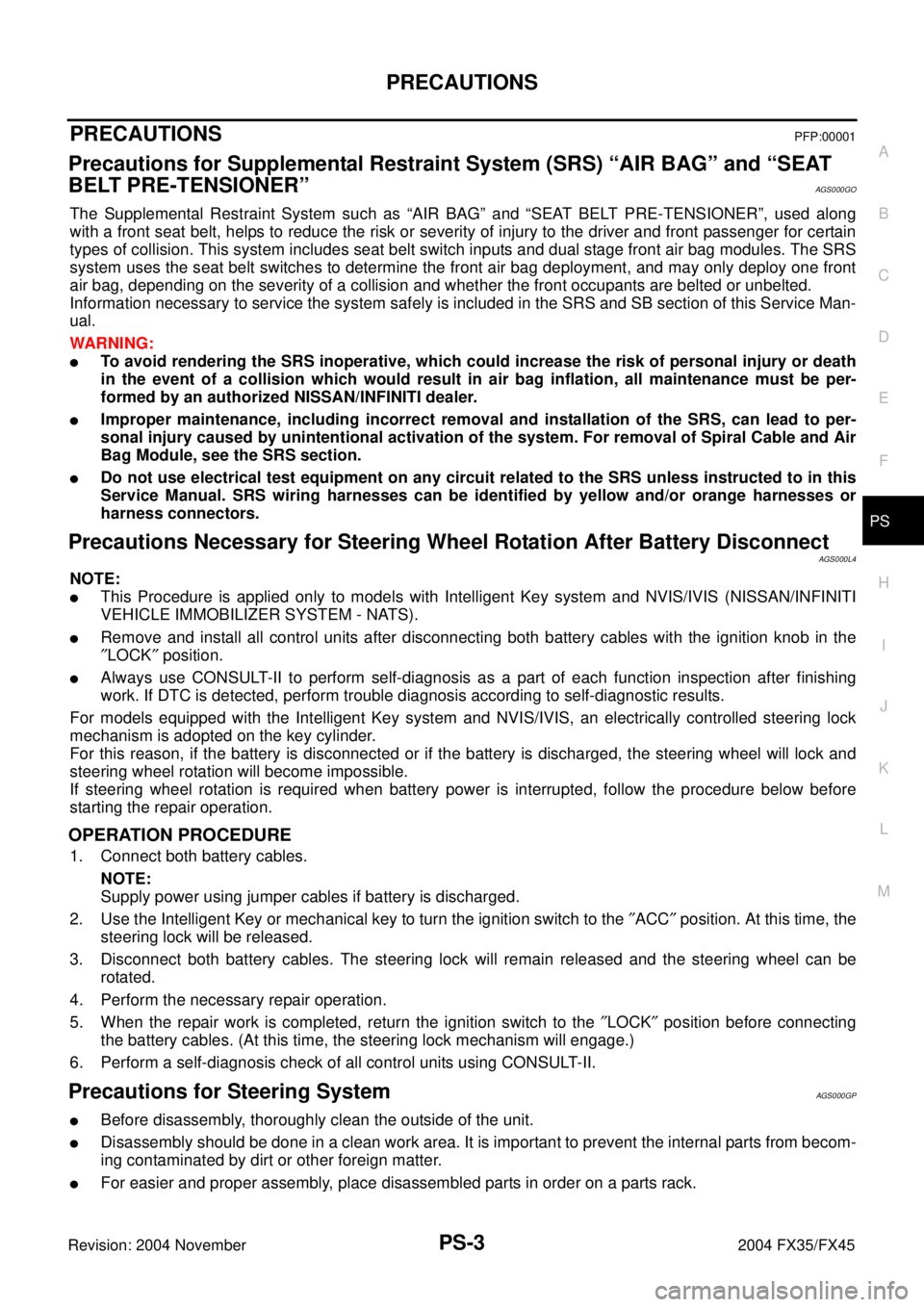
PRECAUTIONS
PS-3
C
D
E
F
H
I
J
K
L
MA
B
PS
Revision: 2004 November 2004 FX35/FX45
PRECAUTIONSPFP:00001
Precautions for Supplemental Restraint System (SRS) “AIR BAG” and “SEAT
BELT PRE-TENSIONER”
AGS000GO
The Supplemental Restraint System such as “AIR BAG” and “SEAT BELT PRE-TENSIONER”, used along
with a front seat belt, helps to reduce the risk or severity of injury to the driver and front passenger for certain
types of collision. This system includes seat belt switch inputs and dual stage front air bag modules. The SRS
system uses the seat belt switches to determine the front air bag deployment, and may only deploy one front
air bag, depending on the severity of a collision and whether the front occupants are belted or unbelted.
Information necessary to service the system safely is included in the SRS and SB section of this Service Man-
ual.
WARNING:
To avoid rendering the SRS inoperative, which could increase the risk of personal injury or death
in the event of a collision which would result in air bag inflation, all maintenance must be per-
formed by an authorized NISSAN/INFINITI dealer.
Improper maintenance, including incorrect removal and installation of the SRS, can lead to per-
sonal injury caused by unintentional activation of the system. For removal of Spiral Cable and Air
Bag Module, see the SRS section.
Do not use electrical test equipment on any circuit related to the SRS unless instructed to in this
Service Manual. SRS wiring harnesses can be identified by yellow and/or orange harnesses or
harness connectors.
Precautions Necessary for Steering Wheel Rotation After Battery DisconnectAGS000L4
NOTE:
This Procedure is applied only to models with Intelligent Key system and NVIS/IVIS (NISSAN/INFINITI
VEHICLE IMMOBILIZER SYSTEM - NATS).
Remove and install all control units after disconnecting both battery cables with the ignition knob in the
″LOCK″ position.
Always use CONSULT-II to perform self-diagnosis as a part of each function inspection after finishing
work. If DTC is detected, perform trouble diagnosis according to self-diagnostic results.
For models equipped with the Intelligent Key system and NVIS/IVIS, an electrically controlled steering lock
mechanism is adopted on the key cylinder.
For this reason, if the battery is disconnected or if the battery is discharged, the steering wheel will lock and
steering wheel rotation will become impossible.
If steering wheel rotation is required when battery power is interrupted, follow the procedure below before
starting the repair operation.
OPERATION PROCEDURE
1. Connect both battery cables.
NOTE:
Supply power using jumper cables if battery is discharged.
2. Use the Intelligent Key or mechanical key to turn the ignition switch to the ″ACC″ position. At this time, the
steering lock will be released.
3. Disconnect both battery cables. The steering lock will remain released and the steering wheel can be
rotated.
4. Perform the necessary repair operation.
5. When the repair work is completed, return the ignition switch to the ″LOCK″ position before connecting
the battery cables. (At this time, the steering lock mechanism will engage.)
6. Perform a self-diagnosis check of all control units using CONSULT-II.
Precautions for Steering SystemAGS000GP
Before disassembly, thoroughly clean the outside of the unit.
Disassembly should be done in a clean work area. It is important to prevent the internal parts from becom-
ing contaminated by dirt or other foreign matter.
For easier and proper assembly, place disassembled parts in order on a parts rack.