Page 3313 of 4284
(10) Remove side gear (Fig. 117).
(11) Remove side gear thrust washer (Fig. 118).ASSEMBLY
(1) Install side gear thrust washer (Fig. 119).
(2) Install differential side gear (Fig. 120).
Fig. 117 Differential Side Gear
1 - DIFFERENTIAL SIDE GEAR
Fig. 118 Side Gear Thrust Washer
1 - SIDE GEAR THRUST WASHER
Fig. 119 Side Gear Thrust Washer
1 - SIDE GEAR THRUST WASHER
Fig. 120 Differential Side Gear
1 - DIFFERENTIAL SIDE GEAR
RGT850 MANUAL TRANSAXLE21a-47
DIFFERENTIAL (Continued)
Page 3314 of 4284
(3) Install four (4) pinion gears and thrust washers
(Fig. 121).
(4) Install pinion shaft retaining ring (Fig. 122).(5) Install two (2) short pinion shafts (Fig. 123).
(6) Install one (1) long pinion shaft (Fig. 124).
(7) Install differential side gear.
(8) Install side gear thrust washer (Fig. 125).
(9) Install differential support plate. Align support
plate to differential case with alignment pins 8470
(Fig. 126).
Fig. 121 Pinion Gear and Thrust Washer
1 - THRUST WASHER (4)
2 - PINION GEAR (4)
Fig. 122 Pinion Shaft Retaining Ring
1 - RETAINING RING
Fig. 123 Short Pinion Shaft (2)
1 - PINION SHAFT (SHORT (2))
Fig. 124 Long Pinion Shaft
1 - PINION SHAFT (LONG)
21a - 48 T850 MANUAL TRANSAXLERG
DIFFERENTIAL (Continued)
Page 3315 of 4284
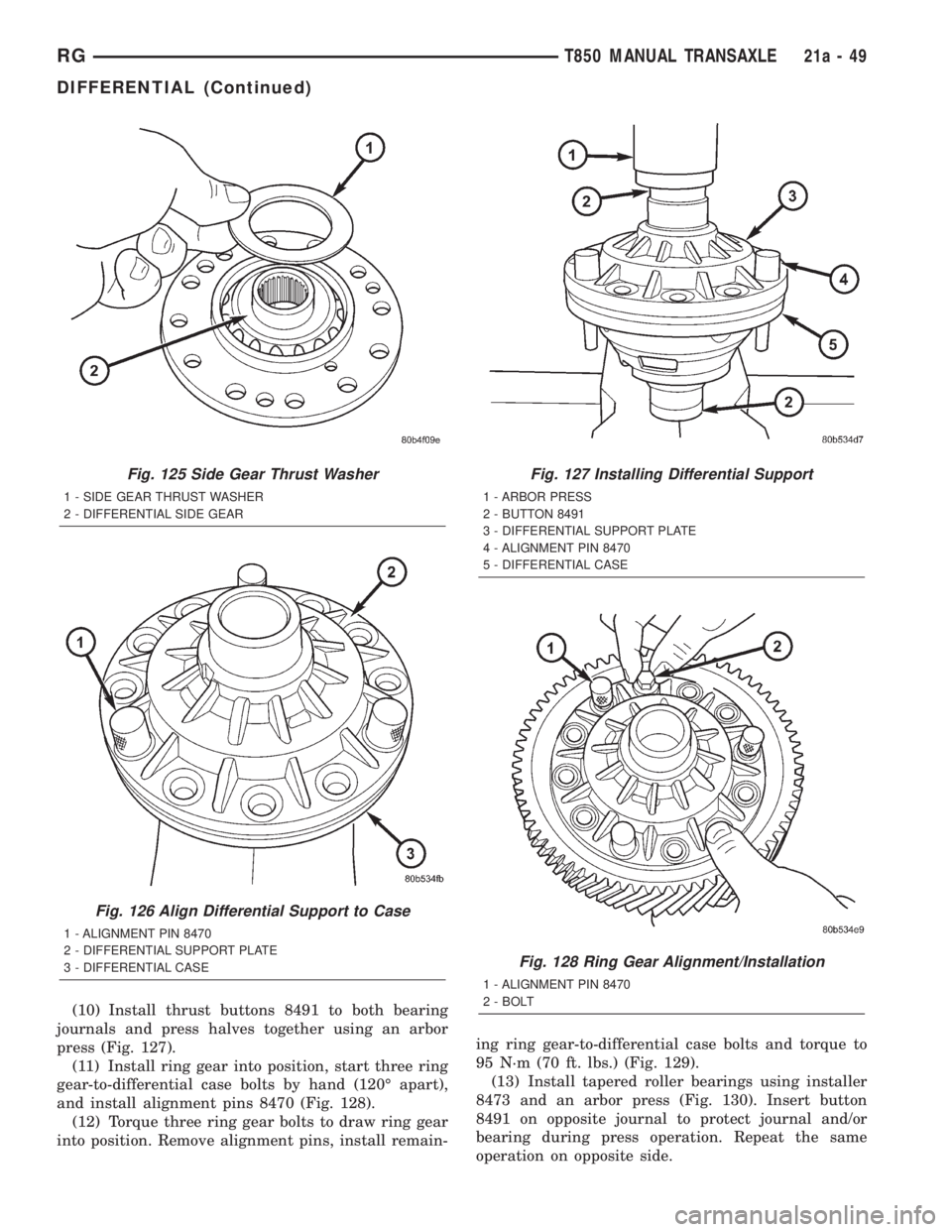
(10) Install thrust buttons 8491 to both bearing
journals and press halves together using an arbor
press (Fig. 127).
(11) Install ring gear into position, start three ring
gear-to-differential case bolts by hand (120É apart),
and install alignment pins 8470 (Fig. 128).
(12) Torque three ring gear bolts to draw ring gear
into position. Remove alignment pins, install remain-ing ring gear-to-differential case bolts and torque to
95 N´m (70 ft. lbs.) (Fig. 129).
(13) Install tapered roller bearings using installer
8473 and an arbor press (Fig. 130). Insert button
8491 on opposite journal to protect journal and/or
bearing during press operation. Repeat the same
operation on opposite side.
Fig. 125 Side Gear Thrust Washer
1 - SIDE GEAR THRUST WASHER
2 - DIFFERENTIAL SIDE GEAR
Fig. 126 Align Differential Support to Case
1 - ALIGNMENT PIN 8470
2 - DIFFERENTIAL SUPPORT PLATE
3 - DIFFERENTIAL CASE
Fig. 127 Installing Differential Support
1 - ARBOR PRESS
2 - BUTTON 8491
3 - DIFFERENTIAL SUPPORT PLATE
4 - ALIGNMENT PIN 8470
5 - DIFFERENTIAL CASE
Fig. 128 Ring Gear Alignment/Installation
1 - ALIGNMENT PIN 8470
2 - BOLT
RGT850 MANUAL TRANSAXLE21a-49
DIFFERENTIAL (Continued)
Page 3316 of 4284
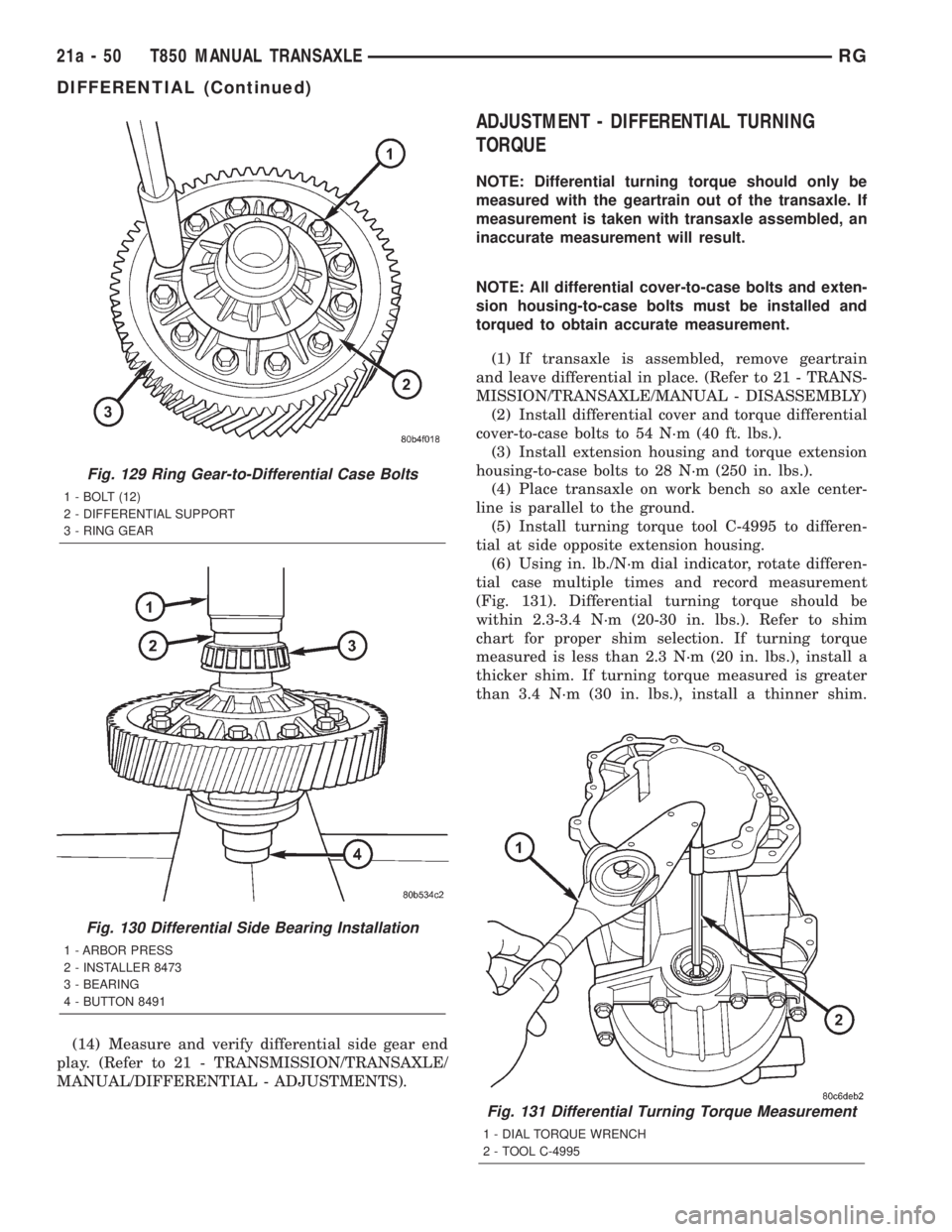
(14) Measure and verify differential side gear end
play. (Refer to 21 - TRANSMISSION/TRANSAXLE/
MANUAL/DIFFERENTIAL - ADJUSTMENTS).
ADJUSTMENT - DIFFERENTIAL TURNING
TORQUE
NOTE: Differential turning torque should only be
measured with the geartrain out of the transaxle. If
measurement is taken with transaxle assembled, an
inaccurate measurement will result.
NOTE: All differential cover-to-case bolts and exten-
sion housing-to-case bolts must be installed and
torqued to obtain accurate measurement.
(1) If transaxle is assembled, remove geartrain
and leave differential in place. (Refer to 21 - TRANS-
MISSION/TRANSAXLE/MANUAL - DISASSEMBLY)
(2) Install differential cover and torque differential
cover-to-case bolts to 54 N´m (40 ft. lbs.).
(3) Install extension housing and torque extension
housing-to-case bolts to 28 N´m (250 in. lbs.).
(4) Place transaxle on work bench so axle center-
line is parallel to the ground.
(5) Install turning torque tool C-4995 to differen-
tial at side opposite extension housing.
(6) Using in. lb./N´m dial indicator, rotate differen-
tial case multiple times and record measurement
(Fig. 131). Differential turning torque should be
within 2.3-3.4 N´m (20-30 in. lbs.). Refer to shim
chart for proper shim selection. If turning torque
measured is less than 2.3 N´m (20 in. lbs.), install a
thicker shim. If turning torque measured is greater
than 3.4 N´m (30 in. lbs.), install a thinner shim.
Fig. 129 Ring Gear-to-Differential Case Bolts
1 - BOLT (12)
2 - DIFFERENTIAL SUPPORT
3 - RING GEAR
Fig. 130 Differential Side Bearing Installation
1 - ARBOR PRESS
2 - INSTALLER 8473
3 - BEARING
4 - BUTTON 8491
Fig. 131 Differential Turning Torque Measurement
1 - DIAL TORQUE WRENCH
2 - TOOL C-4995
21a - 50 T850 MANUAL TRANSAXLERG
DIFFERENTIAL (Continued)
Page 3317 of 4284
DIFFERENTIAL BEARING SHIM CHART
PART NUMBERSHIM THICKNESS
METRIC (MM) STANDARD (STD)
4659242 0.50 0.0197
4659243 0.54 0.0213
4659247 0.58 0.0228
4659248 0.62 0.0244
4659249 0.66 0.0260
4659250 0.70 0.0276
4659251 0.74 0.0291
4659252 0.78 0.0307
4659253 0.82 0.0322
4659254 0.86 0.0339
4659255 0.90 0.0354
4659256 0.94 0.0370
4659257 0.98 0.0386
4659258 1.02 0.0402
4659259 1.06 0.0418
4659260 1.10 0.0434
4659261 1.14 0.0449
4659262 1.18 0.0465
4659263 1.22 0.0481
4659264 1.26 0.0497
4659265 1.30 0.0512
4659266 1.34 0.0528
4659267 1.38 0.0544
4659268 1.42 0.0560
4659269 1.46 0.0575
4659270 1.50 0.0591
4659271 1.54 0.0607
4659272 1.58 0.0623
4659273 1.62 0.0638
4659274 1.66 0.0654
4659275 1.70 0.0670
4659283 2.02 0.0796
4659284 2.06 0.0812
RGT850 MANUAL TRANSAXLE21a-51
DIFFERENTIAL (Continued)
Page 3318 of 4284
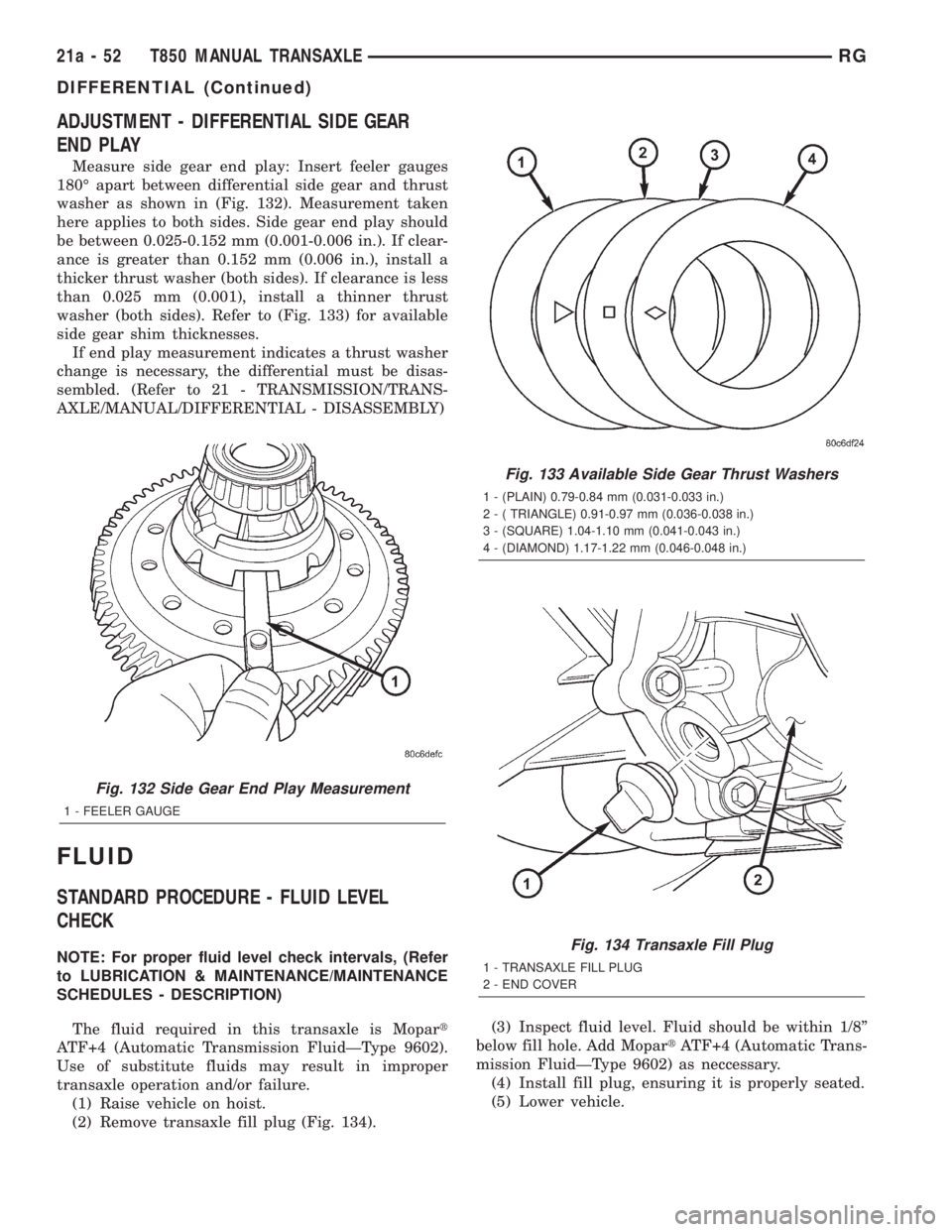
ADJUSTMENT - DIFFERENTIAL SIDE GEAR
END PLAY
Measure side gear end play: Insert feeler gauges
180É apart between differential side gear and thrust
washer as shown in (Fig. 132). Measurement taken
here applies to both sides. Side gear end play should
be between 0.025-0.152 mm (0.001-0.006 in.). If clear-
ance is greater than 0.152 mm (0.006 in.), install a
thicker thrust washer (both sides). If clearance is less
than 0.025 mm (0.001), install a thinner thrust
washer (both sides). Refer to (Fig. 133) for available
side gear shim thicknesses.
If end play measurement indicates a thrust washer
change is necessary, the differential must be disas-
sembled. (Refer to 21 - TRANSMISSION/TRANS-
AXLE/MANUAL/DIFFERENTIAL - DISASSEMBLY)
FLUID
STANDARD PROCEDURE - FLUID LEVEL
CHECK
NOTE: For proper fluid level check intervals, (Refer
to LUBRICATION & MAINTENANCE/MAINTENANCE
SCHEDULES - DESCRIPTION)
The fluid required in this transaxle is Mopart
ATF+4 (Automatic Transmission FluidÐType 9602).
Use of substitute fluids may result in improper
transaxle operation and/or failure.
(1) Raise vehicle on hoist.
(2) Remove transaxle fill plug (Fig. 134).(3) Inspect fluid level. Fluid should be within 1/8º
below fill hole. Add MopartATF+4 (Automatic Trans-
mission FluidÐType 9602) as neccessary.
(4) Install fill plug, ensuring it is properly seated.
(5) Lower vehicle.
Fig. 132 Side Gear End Play Measurement
1 - FEELER GAUGE
Fig. 133 Available Side Gear Thrust Washers
1 - (PLAIN) 0.79-0.84 mm (0.031-0.033 in.)
2 - ( TRIANGLE) 0.91-0.97 mm (0.036-0.038 in.)
3 - (SQUARE) 1.04-1.10 mm (0.041-0.043 in.)
4 - (DIAMOND) 1.17-1.22 mm (0.046-0.048 in.)
Fig. 134 Transaxle Fill Plug
1 - TRANSAXLE FILL PLUG
2 - END COVER
21a - 52 T850 MANUAL TRANSAXLERG
DIFFERENTIAL (Continued)
Page 3319 of 4284
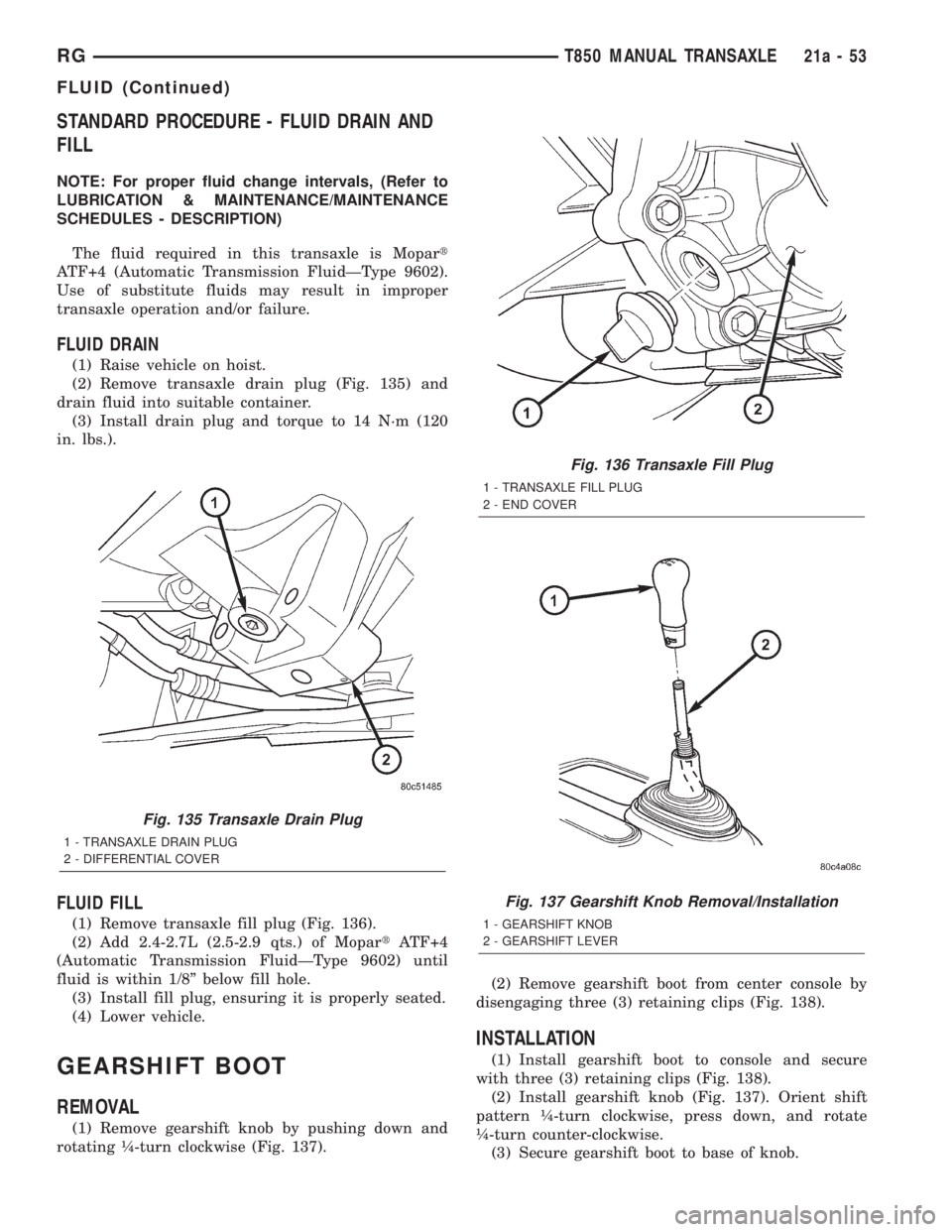
STANDARD PROCEDURE - FLUID DRAIN AND
FILL
NOTE: For proper fluid change intervals, (Refer to
LUBRICATION & MAINTENANCE/MAINTENANCE
SCHEDULES - DESCRIPTION)
The fluid required in this transaxle is Mopart
ATF+4 (Automatic Transmission FluidÐType 9602).
Use of substitute fluids may result in improper
transaxle operation and/or failure.
FLUID DRAIN
(1) Raise vehicle on hoist.
(2) Remove transaxle drain plug (Fig. 135) and
drain fluid into suitable container.
(3) Install drain plug and torque to 14 N´m (120
in. lbs.).
FLUID FILL
(1) Remove transaxle fill plug (Fig. 136).
(2) Add 2.4-2.7L (2.5-2.9 qts.) of MopartATF+4
(Automatic Transmission FluidÐType 9602) until
fluid is within 1/8º below fill hole.
(3) Install fill plug, ensuring it is properly seated.
(4) Lower vehicle.
GEARSHIFT BOOT
REMOVAL
(1) Remove gearshift knob by pushing down and
rotating ò-turn clockwise (Fig. 137).(2) Remove gearshift boot from center console by
disengaging three (3) retaining clips (Fig. 138).
INSTALLATION
(1) Install gearshift boot to console and secure
with three (3) retaining clips (Fig. 138).
(2) Install gearshift knob (Fig. 137). Orient shift
pattern ò-turn clockwise, press down, and rotate
ò-turn counter-clockwise.
(3) Secure gearshift boot to base of knob.
Fig. 135 Transaxle Drain Plug
1 - TRANSAXLE DRAIN PLUG
2 - DIFFERENTIAL COVER
Fig. 136 Transaxle Fill Plug
1 - TRANSAXLE FILL PLUG
2 - END COVER
Fig. 137 Gearshift Knob Removal/Installation
1 - GEARSHIFT KNOB
2 - GEARSHIFT LEVER
RGT850 MANUAL TRANSAXLE21a-53
FLUID (Continued)
Page 3320 of 4284
GEARSHIFT CABLE -
CROSSOVER
REMOVAL
(1) Disconnect battery negative cable.
(2) Remove gearshift knob by pushing down and
rotating ò-turn clock-wise (Fig. 139).(3) Remove gearshift boot from center console by
disengaging at three (3) retaining clips (Fig. 140).
(4) Apply park brake to allow park brake handle to
clear center console upon removal.
(5) Remove two (2) cupholder bottom plugs (Fig.
141).
(6) Remove four (4) center console-to-gearshift
mechanism screws. Remove console assembly (Fig.
142).
Fig. 138 Gearshift Boot Removal/Installation
1 - GEARSHIFT BOOT
2 - CENTER CONSOLE
Fig. 139 Gearshift Knob Removal/Installation
1 - GEARSHIFT KNOB
2 - GEARSHIFT LEVER
Fig. 140 Gearshift Boot Removal/Installation
1 - GEARSHIFT BOOT
2 - CENTER CONSOLE
Fig. 141 Cup Holder Plugs
1 - CUPHOLDER PLUG (2)
21a - 54 T850 MANUAL TRANSAXLERG
GEARSHIFT BOOT (Continued)