Page 3089 of 4284
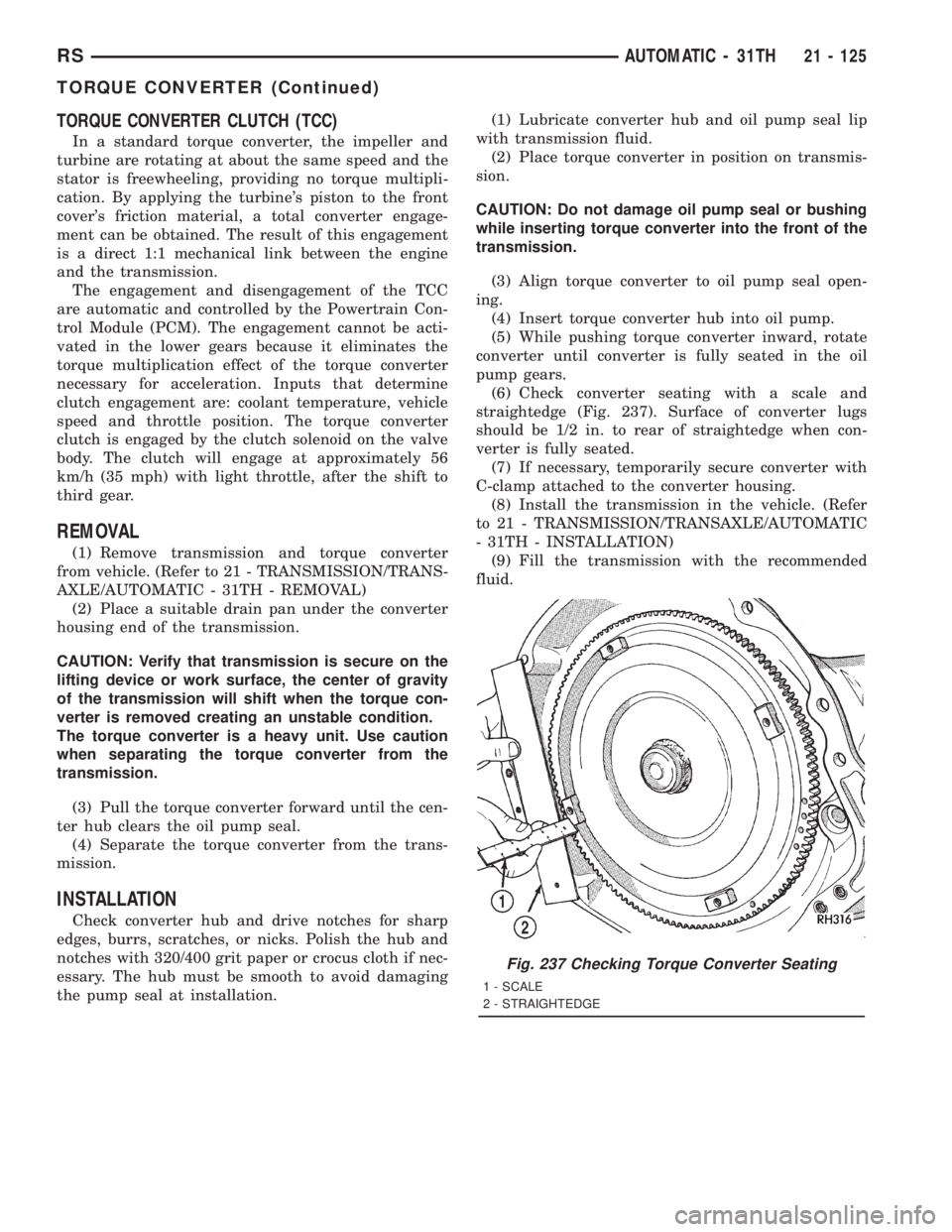
TORQUE CONVERTER CLUTCH (TCC)
In a standard torque converter, the impeller and
turbine are rotating at about the same speed and the
stator is freewheeling, providing no torque multipli-
cation. By applying the turbine's piston to the front
cover's friction material, a total converter engage-
ment can be obtained. The result of this engagement
is a direct 1:1 mechanical link between the engine
and the transmission.
The engagement and disengagement of the TCC
are automatic and controlled by the Powertrain Con-
trol Module (PCM). The engagement cannot be acti-
vated in the lower gears because it eliminates the
torque multiplication effect of the torque converter
necessary for acceleration. Inputs that determine
clutch engagement are: coolant temperature, vehicle
speed and throttle position. The torque converter
clutch is engaged by the clutch solenoid on the valve
body. The clutch will engage at approximately 56
km/h (35 mph) with light throttle, after the shift to
third gear.
REMOVAL
(1) Remove transmission and torque converter
from vehicle. (Refer to 21 - TRANSMISSION/TRANS-
AXLE/AUTOMATIC - 31TH - REMOVAL)
(2) Place a suitable drain pan under the converter
housing end of the transmission.
CAUTION: Verify that transmission is secure on the
lifting device or work surface, the center of gravity
of the transmission will shift when the torque con-
verter is removed creating an unstable condition.
The torque converter is a heavy unit. Use caution
when separating the torque converter from the
transmission.
(3) Pull the torque converter forward until the cen-
ter hub clears the oil pump seal.
(4) Separate the torque converter from the trans-
mission.
INSTALLATION
Check converter hub and drive notches for sharp
edges, burrs, scratches, or nicks. Polish the hub and
notches with 320/400 grit paper or crocus cloth if nec-
essary. The hub must be smooth to avoid damaging
the pump seal at installation.(1) Lubricate converter hub and oil pump seal lip
with transmission fluid.
(2) Place torque converter in position on transmis-
sion.
CAUTION: Do not damage oil pump seal or bushing
while inserting torque converter into the front of the
transmission.
(3) Align torque converter to oil pump seal open-
ing.
(4) Insert torque converter hub into oil pump.
(5) While pushing torque converter inward, rotate
converter until converter is fully seated in the oil
pump gears.
(6) Check converter seating with a scale and
straightedge (Fig. 237). Surface of converter lugs
should be 1/2 in. to rear of straightedge when con-
verter is fully seated.
(7) If necessary, temporarily secure converter with
C-clamp attached to the converter housing.
(8) Install the transmission in the vehicle. (Refer
to 21 - TRANSMISSION/TRANSAXLE/AUTOMATIC
- 31TH - INSTALLATION)
(9) Fill the transmission with the recommended
fluid.
Fig. 237 Checking Torque Converter Seating
1 - SCALE
2 - STRAIGHTEDGE
RSAUTOMATIC - 31TH21 - 125
TORQUE CONVERTER (Continued)
Page 3090 of 4284
TRANSFER SYSTEM - OUTPUT
SHAFT/GEAR/BEARING
REMOVAL
NOTE: Transfer Gear should be removed for repair
of output shaft, to obtain an accurate output shaft
turning torque measurement upon reassembly.
(Refer to 21 - TRANSMISSION/TRANSAXLE/AUTO-
MATIC - 31TH/TRANSFER SYSTEM - REMOVAL)
NOTE: Transaxle geartrain must be removed to gain
access to and service output shaft. (Refer to 21 -
TRANSMISSION/TRANSAXLE/AUTOMATIC - 31TH -
DISASSEMBLY)
(1) Using a suitable punch, bend retaining strap
tabs flat to facilitate bolt removal (Fig. 238).
(2) Remove retaining strap and stirrup-to-gear
bolts (Fig. 239).
(3) Remove retaining strap (Fig. 240).
Fig. 238 Bend Strap Tabs Flat
1 - RETAINING TABS
2 - STRAP
Fig. 239 Remove Strap Bolts
1 - RETAINING BOLTS
2 - STIRRUP
3 - STRAP
Fig. 240 Remove Strap From Stirrup and Gear
1 - OUTPUT GEAR
2 - STRAP
21 - 126 AUTOMATIC - 31THRS
Page 3091 of 4284
(4) Remove stirrup (Fig. 241).
(5) Using Tool L-4434, remove output shaft retain-
ing nut and washer (Fig. 242).(6) Using Tool L-4407 as shown in (Fig. 243),
remove output shaft gear and select shim (Fig. 244).
Fig. 241 Remove Stirrup From Gear
1 - OUTPUT GEAR
2 - STIRRUP
Fig. 242 Remove Output Shaft Retaining Nut and
Washer
1 - SPECIAL TOOL L-4434
2 - OUTPUT SHAFT GEAR
Fig. 243 Remove Output Shaft Gear
1 - OUTPUT GEAR
2 - TOOL L-4407A
Fig. 244 Output Shaft Gear and (Select) Shim
1 - BEARING CUP
2 - SHIM (SELECT)
3 - BEARING CONE
4 - OUTPUT SHAFT GEAR
5 - OUTPUT SHAFT
RSAUTOMATIC - 31TH21 - 127
TRANSFER SYSTEM - OUTPUT SHAFT/GEAR/BEARING (Continued)
Page 3092 of 4284
(7) Remove output shaft/rear annulus gear assem-
bly (Fig. 245).
(8) Remove output shaft gear bearing cone using
Tool L-4406-1 and adapters L-4406-2 (Fig. 246).(9) Using an arbor press, remove output shaft from
rear annulus gear (Fig. 247).
(10) Using Tool L-4406-1 and adapters L-4406-2,
remove rear planetary annulus gear bearing cone
(Fig. 248).
Fig. 245 Remove Output Shaft and Rear Annulus
Gear Assembly
1 - BEARING CUP
2 - REAR ANNULUS GEAR
3 - OUTPUT SHAFT
Fig. 246 Remove Output Shaft Gear Bearing Cone
1 - SPECIAL TOOL L-4406-1 WITH ADAPTERS L-4406-2
2 - OUTPUT SHAFT GEAR
Fig. 247 Remove Output Shaft
1 - ARBOR PRESS RAM
2 - CAUTION: SUPPORT ANNULUS GEAR UNDERNEATH, NEAR
GEAR CENTER.
3 - BEARING CONE
4 - REAR ANNULUS GEAR
5 - OUTPUT SHAFT
Fig. 248 Remove Rear Planetary Annulus Gear
Bearing Cone
1 - SPECIAL TOOL L-4406-1 WITH ADAPTERS L-4406-2
2 - REAR PLANETARY ANNULUS GEAR
21 - 128 AUTOMATIC - 31THRS
TRANSFER SYSTEM - OUTPUT SHAFT/GEAR/BEARING (Continued)
Page 3093 of 4284
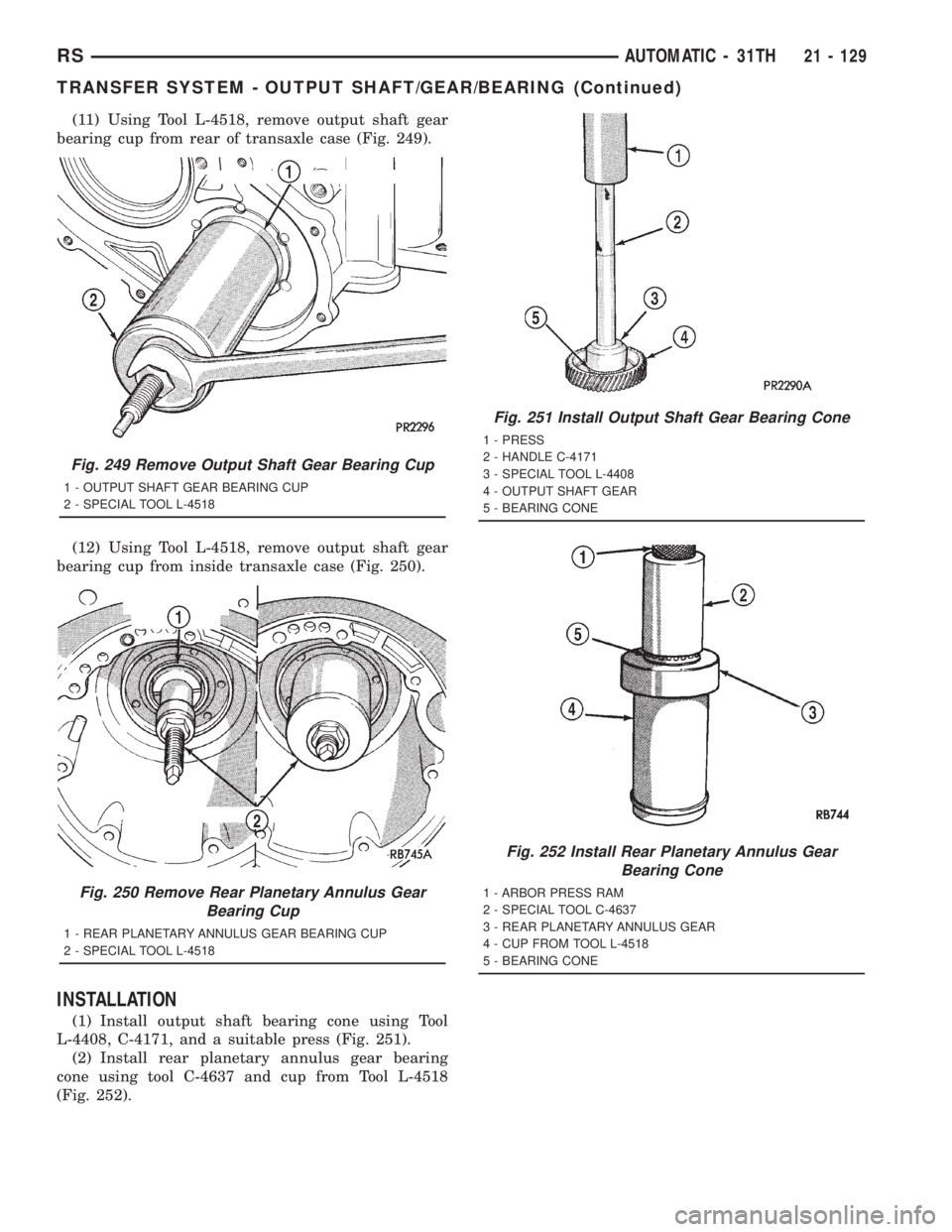
(11) Using Tool L-4518, remove output shaft gear
bearing cup from rear of transaxle case (Fig. 249).
(12) Using Tool L-4518, remove output shaft gear
bearing cup from inside transaxle case (Fig. 250).
INSTALLATION
(1) Install output shaft bearing cone using Tool
L-4408, C-4171, and a suitable press (Fig. 251).
(2) Install rear planetary annulus gear bearing
cone using tool C-4637 and cup from Tool L-4518
(Fig. 252).
Fig. 249 Remove Output Shaft Gear Bearing Cup
1 - OUTPUT SHAFT GEAR BEARING CUP
2 - SPECIAL TOOL L-4518
Fig. 250 Remove Rear Planetary Annulus Gear
Bearing Cup
1 - REAR PLANETARY ANNULUS GEAR BEARING CUP
2 - SPECIAL TOOL L-4518
Fig. 251 Install Output Shaft Gear Bearing Cone
1 - PRESS
2 - HANDLE C-4171
3 - SPECIAL TOOL L-4408
4 - OUTPUT SHAFT GEAR
5 - BEARING CONE
Fig. 252 Install Rear Planetary Annulus Gear
Bearing Cone
1 - ARBOR PRESS RAM
2 - SPECIAL TOOL C-4637
3 - REAR PLANETARY ANNULUS GEAR
4 - CUP FROM TOOL L-4518
5 - BEARING CONE
RSAUTOMATIC - 31TH21 - 129
TRANSFER SYSTEM - OUTPUT SHAFT/GEAR/BEARING (Continued)
Page 3094 of 4284
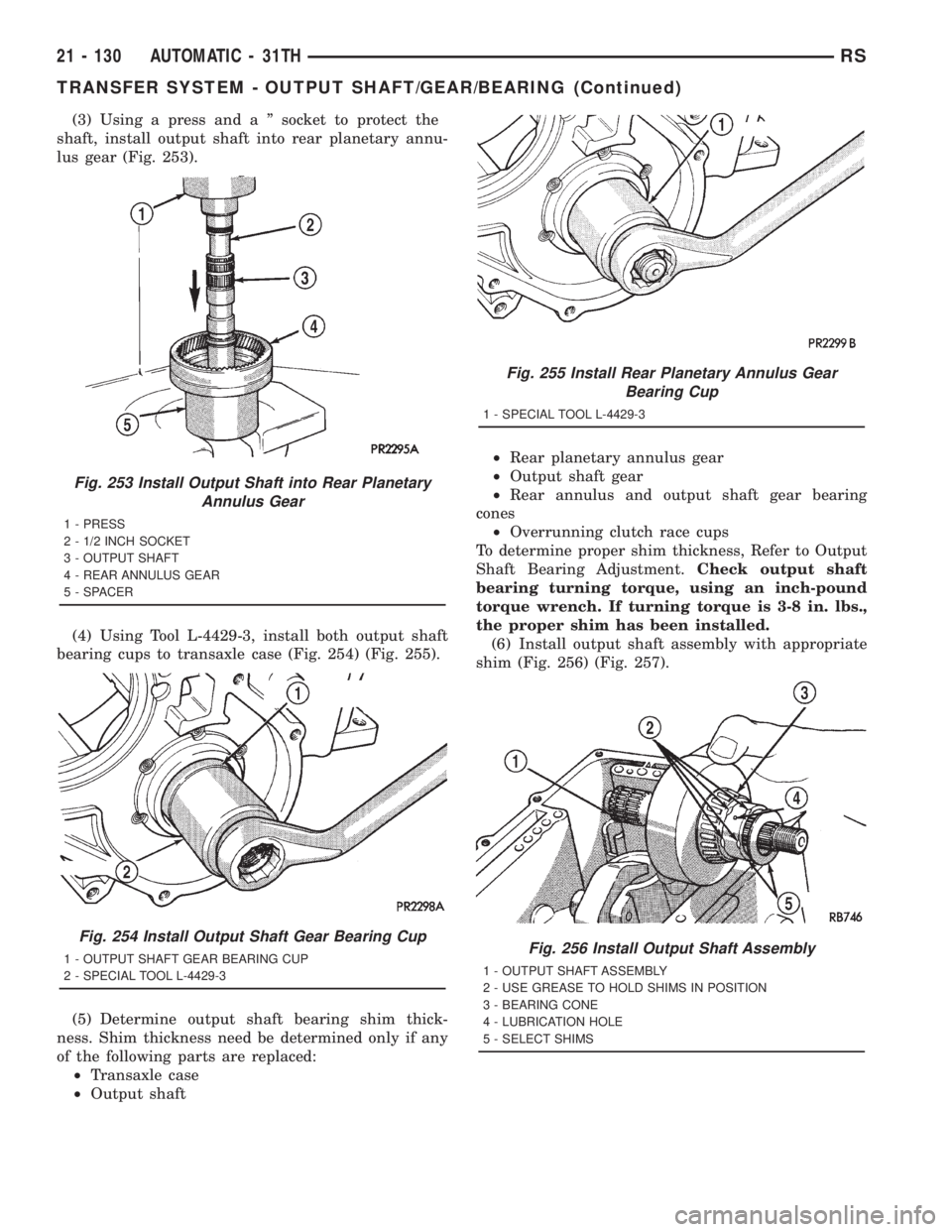
(3) Using a press and a º socket to protect the
shaft, install output shaft into rear planetary annu-
lus gear (Fig. 253).
(4) Using Tool L-4429-3, install both output shaft
bearing cups to transaxle case (Fig. 254) (Fig. 255).
(5) Determine output shaft bearing shim thick-
ness. Shim thickness need be determined only if any
of the following parts are replaced:
²Transaxle case
²Output shaft²Rear planetary annulus gear
²Output shaft gear
²Rear annulus and output shaft gear bearing
cones
²Overrunning clutch race cups
To determine proper shim thickness, Refer to Output
Shaft Bearing Adjustment.Check output shaft
bearing turning torque, using an inch-pound
torque wrench. If turning torque is 3-8 in. lbs.,
the proper shim has been installed.
(6) Install output shaft assembly with appropriate
shim (Fig. 256) (Fig. 257).
Fig. 253 Install Output Shaft into Rear Planetary
Annulus Gear
1 - PRESS
2 - 1/2 INCH SOCKET
3 - OUTPUT SHAFT
4 - REAR ANNULUS GEAR
5 - SPACER
Fig. 254 Install Output Shaft Gear Bearing Cup
1 - OUTPUT SHAFT GEAR BEARING CUP
2 - SPECIAL TOOL L-4429-3
Fig. 255 Install Rear Planetary Annulus Gear
Bearing Cup
1 - SPECIAL TOOL L-4429-3
Fig. 256 Install Output Shaft Assembly
1 - OUTPUT SHAFT ASSEMBLY
2 - USE GREASE TO HOLD SHIMS IN POSITION
3 - BEARING CONE
4 - LUBRICATION HOLE
5 - SELECT SHIMS
21 - 130 AUTOMATIC - 31THRS
TRANSFER SYSTEM - OUTPUT SHAFT/GEAR/BEARING (Continued)
Page 3095 of 4284
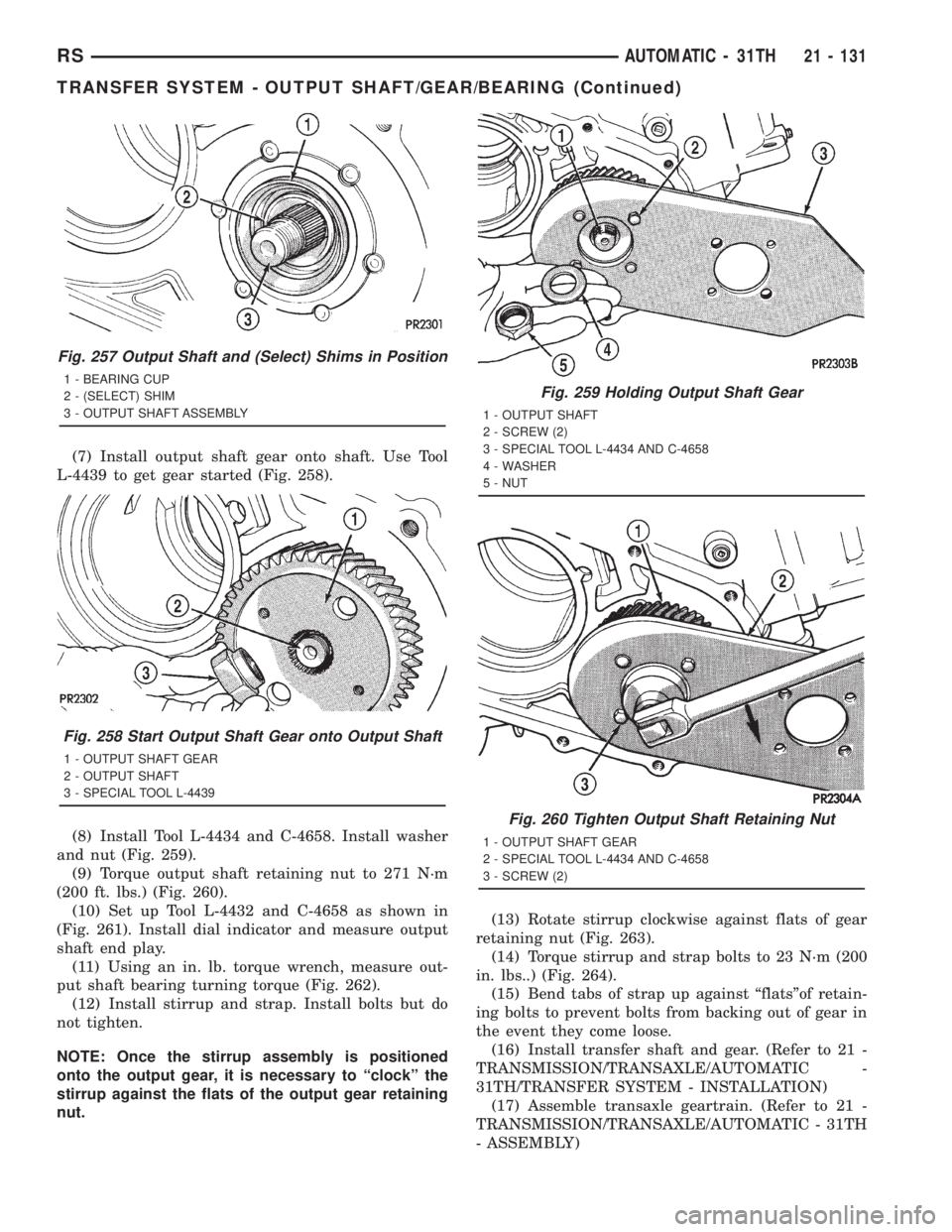
(7) Install output shaft gear onto shaft. Use Tool
L-4439 to get gear started (Fig. 258).
(8) Install Tool L-4434 and C-4658. Install washer
and nut (Fig. 259).
(9) Torque output shaft retaining nut to 271 N´m
(200 ft. lbs.) (Fig. 260).
(10) Set up Tool L-4432 and C-4658 as shown in
(Fig. 261). Install dial indicator and measure output
shaft end play.
(11) Using an in. lb. torque wrench, measure out-
put shaft bearing turning torque (Fig. 262).
(12) Install stirrup and strap. Install bolts but do
not tighten.
NOTE: Once the stirrup assembly is positioned
onto the output gear, it is necessary to ªclockº the
stirrup against the flats of the output gear retaining
nut.(13) Rotate stirrup clockwise against flats of gear
retaining nut (Fig. 263).
(14) Torque stirrup and strap bolts to 23 N´m (200
in. lbs..) (Fig. 264).
(15) Bend tabs of strap up against ªflatsºof retain-
ing bolts to prevent bolts from backing out of gear in
the event they come loose.
(16) Install transfer shaft and gear. (Refer to 21 -
TRANSMISSION/TRANSAXLE/AUTOMATIC -
31TH/TRANSFER SYSTEM - INSTALLATION)
(17) Assemble transaxle geartrain. (Refer to 21 -
TRANSMISSION/TRANSAXLE/AUTOMATIC - 31TH
- ASSEMBLY)
Fig. 257 Output Shaft and (Select) Shims in Position
1 - BEARING CUP
2 - (SELECT) SHIM
3 - OUTPUT SHAFT ASSEMBLY
Fig. 258 Start Output Shaft Gear onto Output Shaft
1 - OUTPUT SHAFT GEAR
2 - OUTPUT SHAFT
3 - SPECIAL TOOL L-4439
Fig. 259 Holding Output Shaft Gear
1 - OUTPUT SHAFT
2 - SCREW (2)
3 - SPECIAL TOOL L-4434 AND C-4658
4 - WASHER
5 - NUT
Fig. 260 Tighten Output Shaft Retaining Nut
1 - OUTPUT SHAFT GEAR
2 - SPECIAL TOOL L-4434 AND C-4658
3 - SCREW (2)
RSAUTOMATIC - 31TH21 - 131
TRANSFER SYSTEM - OUTPUT SHAFT/GEAR/BEARING (Continued)
Page 3096 of 4284
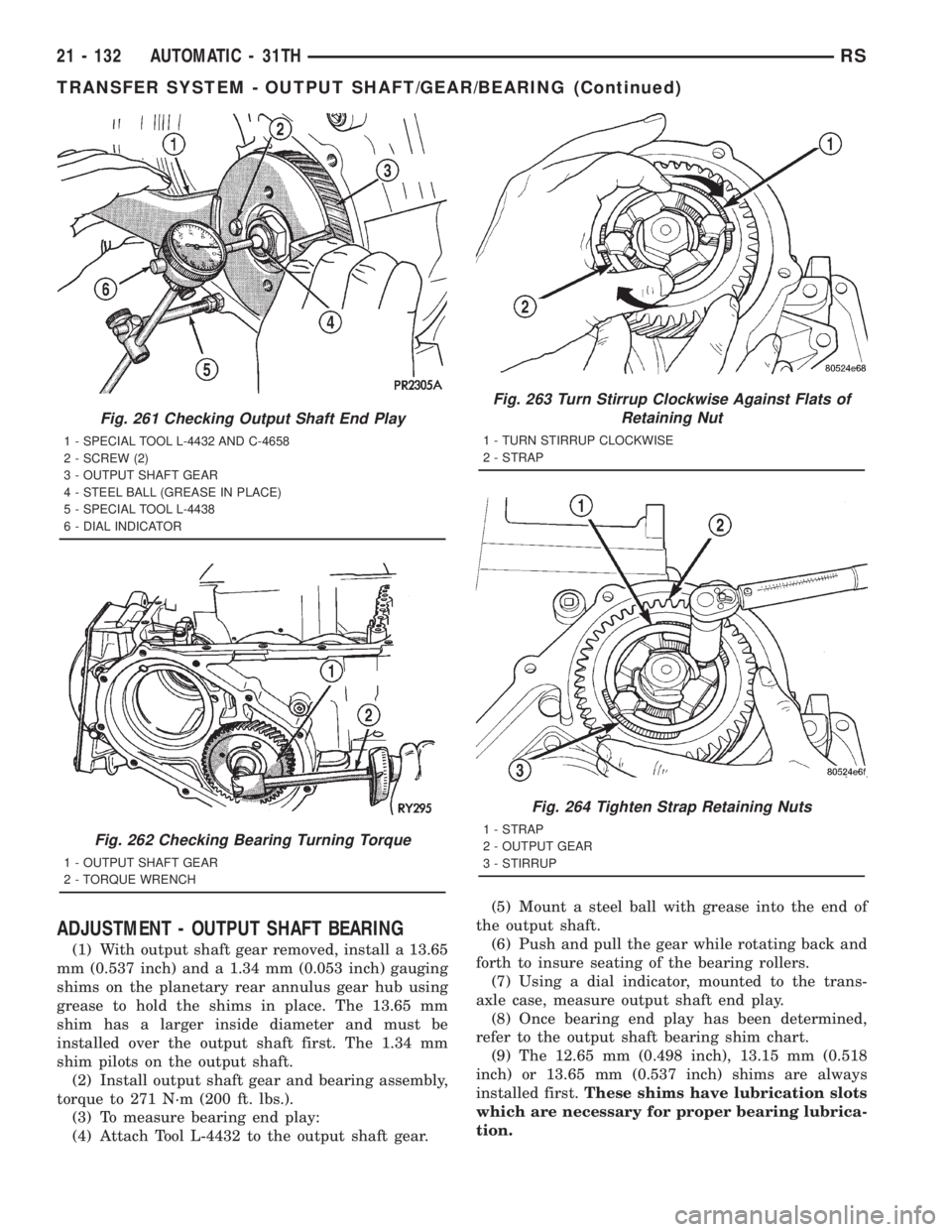
ADJUSTMENT - OUTPUT SHAFT BEARING
(1) With output shaft gear removed, install a 13.65
mm (0.537 inch) and a 1.34 mm (0.053 inch) gauging
shims on the planetary rear annulus gear hub using
grease to hold the shims in place. The 13.65 mm
shim has a larger inside diameter and must be
installed over the output shaft first. The 1.34 mm
shim pilots on the output shaft.
(2) Install output shaft gear and bearing assembly,
torque to 271 N´m (200 ft. lbs.).
(3) To measure bearing end play:
(4) Attach Tool L-4432 to the output shaft gear.(5) Mount a steel ball with grease into the end of
the output shaft.
(6) Push and pull the gear while rotating back and
forth to insure seating of the bearing rollers.
(7) Using a dial indicator, mounted to the trans-
axle case, measure output shaft end play.
(8) Once bearing end play has been determined,
refer to the output shaft bearing shim chart.
(9) The 12.65 mm (0.498 inch), 13.15 mm (0.518
inch) or 13.65 mm (0.537 inch) shims are always
installed first.These shims have lubrication slots
which are necessary for proper bearing lubrica-
tion.
Fig. 261 Checking Output Shaft End Play
1 - SPECIAL TOOL L-4432 AND C-4658
2 - SCREW (2)
3 - OUTPUT SHAFT GEAR
4 - STEEL BALL (GREASE IN PLACE)
5 - SPECIAL TOOL L-4438
6 - DIAL INDICATOR
Fig. 262 Checking Bearing Turning Torque
1 - OUTPUT SHAFT GEAR
2 - TORQUE WRENCH
Fig. 263 Turn Stirrup Clockwise Against Flats of
Retaining Nut
1 - TURN STIRRUP CLOCKWISE
2 - STRAP
Fig. 264 Tighten Strap Retaining Nuts
1 - STRAP
2 - OUTPUT GEAR
3 - STIRRUP
21 - 132 AUTOMATIC - 31THRS
TRANSFER SYSTEM - OUTPUT SHAFT/GEAR/BEARING (Continued)