Page 3201 of 4284
(6) Using Miller Special Tool L-4518, remove the
differential bearing race from the extension housing.
(7) Using Miller Special Tool 6062A, remove the
differential bearing race from the bearing retainer
(Fig. 185) (Fig. 186).
(8) Remove ring gear-to-differential case bolts and
floating pinion shaft retainers (Fig. 187).
(9) Separate ring gear from differential case (Fig.
188).
Fig. 185 Position Bearing Cup Remover Tool in
Retainer
1 - SPECIAL TOOL 6062A
2 - DIFFERENTIAL BEARING RETAINER
Fig. 186 Remove Bearing Cup
1 - SPECIAL TOOL 6062A
2 - DIFFERENTIAL BEARING RETAINER
Fig. 187 Ring Gear-to-Case Bolts
1 - DIFFERENTIAL CASE
2 - PINION SHAFT RETAINER
3 - RING GEAR
4 - RING GEAR-TO-CASE BOLT
Fig. 188 Ring Gear Removal
1 - DIFFERENTIAL CASE
2 - RING GEAR
RSAUTOMATIC - 41TE21 - 237
FINAL DRIVE (Continued)
Page 3202 of 4284
(10) Separate differential cover from case using
suitable screwdrivers at position shown in (Fig. 189)
(11) Lift support from case (Fig. 190).(12) Remove side gear thrust washer (Fig. 191).
(13) Remove side gear (Fig. 192).
Fig. 189 Separating Differential Support with
Screwdrivers
1 - DIFFERENTIAL SUPPORT
2 - DIFFERENTIAL CASE
3 - SCREWDRIVER
4 - RELIEF (2 @ 180É APART)
Fig. 190 Differential Support Removal
1 - DIFFERENTIAL SUPPORT
2 - DIFFERENTIAL CASE
Fig. 191 Side Gear Thrust Washer Removal
1 - SIDE GEAR THRUST WASHER
Fig. 192 Side Gear Removal
1 - DIFFERENTIAL SIDE GEAR
21 - 238 AUTOMATIC - 41TERS
FINAL DRIVE (Continued)
Page 3203 of 4284
(14) Remove pinion shaft (Fig. 193).
(15) Remove pinion gears and tabbed washers
(Fig. 194).(16) Remove differential side gear (Fig. 195).
(17) Remove side gear thrust washer (Fig. 196).
(18) Inspect all components for excessive wear.
Fig. 193 Pinion Shaft Removal
1 - PINION SHAFT
Fig. 194 Pinion Gear and Washer Removal
1 - PINION GEAR
2 - TABBED WASHER
3 - LOCATING TAB
4 - NOTCH
Fig. 195 Side Gear Removal
1 - DIFFERENTIAL SIDE GEAR
Fig. 196 Side Gear Thrust Washer Removal
1 - THRUST WASHER
RSAUTOMATIC - 41TE21 - 239
FINAL DRIVE (Continued)
Page 3204 of 4284
ASSEMBLY
NOTE: The differential is serviced as an assembly.
Differential service is limited to bearing cups and
cones. Any other differential component failure
must be remedied by differential assembly and
transfer shaft replacement.
(1) Install side gear thrust washer to differential
case (Fig. 197).
(2) Install side gear to differential case (Fig. 198).(3) Install both pinion gears and washers to case,
while orientating washer tabs to notch in case (Fig.
199).
(4) Install pinion shaft (Fig. 200).
Fig. 197 Thrust Washer Installation
1 - THRUST WASHER
Fig. 198 Side Gear Installation
1 - DIFFERENTIAL SIDE GEAR
Fig. 199 Pinion Gear and Washer Installation
1 - PINION GEAR
2 - TABBED WASHER
3 - LOCATING TAB
4 - NOTCH
Fig. 200 Pinion Shaft Installation
1 - PINION SHAFT
21 - 240 AUTOMATIC - 41TERS
FINAL DRIVE (Continued)
Page 3205 of 4284
(5) Install side gear to case (Fig. 201).
(6) Install side gear thrust washer to case (Fig.
202).(7) Install differential support into position, while
aligning through-holes (Fig. 203).
(8) Install differential ring gear to case (Fig. 204).
Fig. 201 Side Gear Installation
1 - DIFFERENTIAL SIDE GEAR
Fig. 202 Side Gear Thrust Washer
1 - SIDE GEAR THRUST WASHER
Fig. 203 Diff Support Installation
1 - DIFFERENTIAL SUPPORT
2 - DIFFERENTIAL CASE
Fig. 204 Ring Gear Installation
1 - DIFFERENTIAL CASE
2 - RING GEAR
RSAUTOMATIC - 41TE21 - 241
FINAL DRIVE (Continued)
Page 3206 of 4284
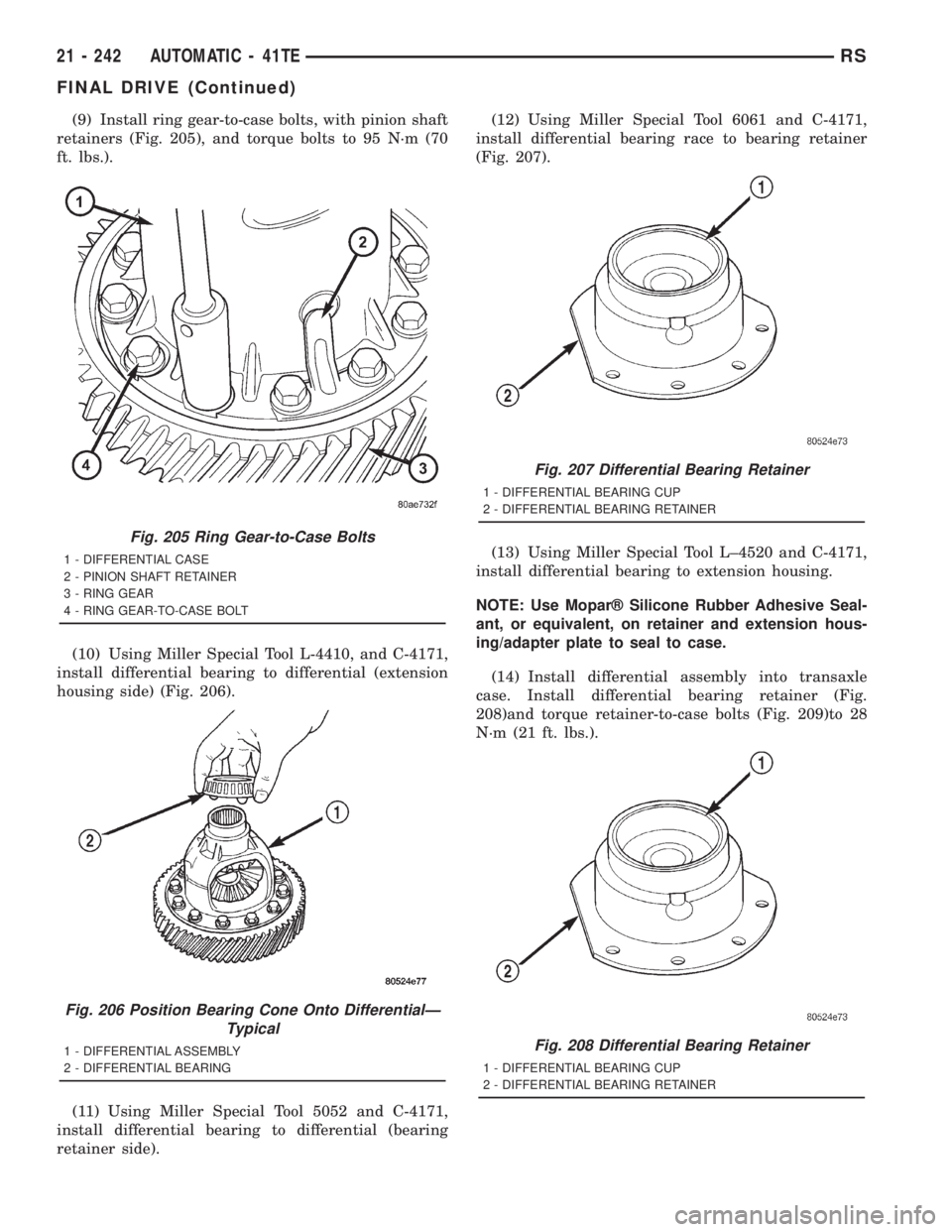
(9) Install ring gear-to-case bolts, with pinion shaft
retainers (Fig. 205), and torque bolts to 95 N´m (70
ft. lbs.).
(10) Using Miller Special Tool L-4410, and C-4171,
install differential bearing to differential (extension
housing side) (Fig. 206).
(11) Using Miller Special Tool 5052 and C-4171,
install differential bearing to differential (bearing
retainer side).(12) Using Miller Special Tool 6061 and C-4171,
install differential bearing race to bearing retainer
(Fig. 207).
(13) Using Miller Special Tool L±4520 and C-4171,
install differential bearing to extension housing.
NOTE: Use Moparž Silicone Rubber Adhesive Seal-
ant, or equivalent, on retainer and extension hous-
ing/adapter plate to seal to case.
(14) Install differential assembly into transaxle
case. Install differential bearing retainer (Fig.
208)and torque retainer-to-case bolts (Fig. 209)to 28
N´m (21 ft. lbs.).
Fig. 205 Ring Gear-to-Case Bolts
1 - DIFFERENTIAL CASE
2 - PINION SHAFT RETAINER
3 - RING GEAR
4 - RING GEAR-TO-CASE BOLT
Fig. 206 Position Bearing Cone Onto DifferentialÐ
Typical
1 - DIFFERENTIAL ASSEMBLY
2 - DIFFERENTIAL BEARING
Fig. 207 Differential Bearing Retainer
1 - DIFFERENTIAL BEARING CUP
2 - DIFFERENTIAL BEARING RETAINER
Fig. 208 Differential Bearing Retainer
1 - DIFFERENTIAL BEARING CUP
2 - DIFFERENTIAL BEARING RETAINER
21 - 242 AUTOMATIC - 41TERS
FINAL DRIVE (Continued)
Page 3207 of 4284
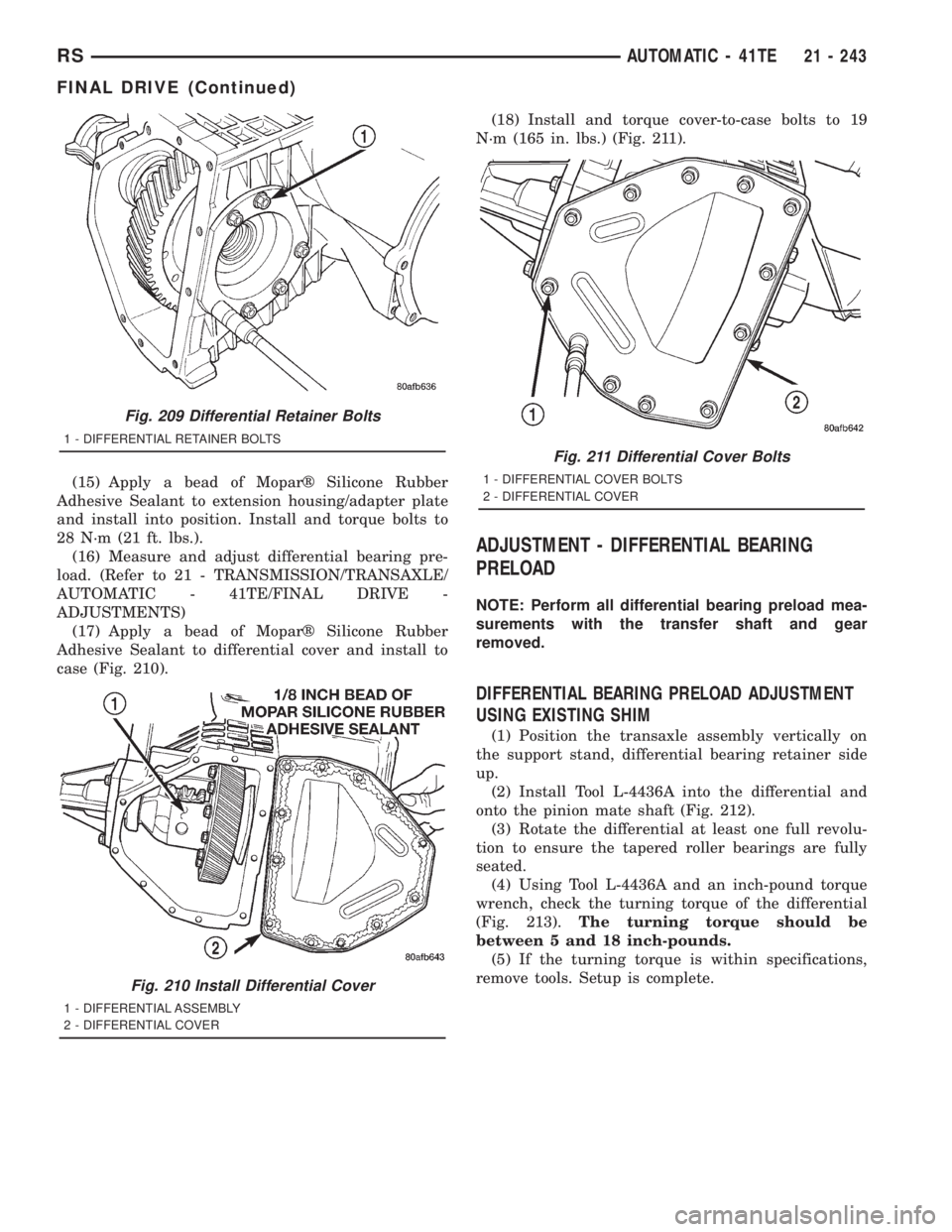
(15) Apply a bead of Moparž Silicone Rubber
Adhesive Sealant to extension housing/adapter plate
and install into position. Install and torque bolts to
28 N´m (21 ft. lbs.).
(16) Measure and adjust differential bearing pre-
load. (Refer to 21 - TRANSMISSION/TRANSAXLE/
AUTOMATIC - 41TE/FINAL DRIVE -
ADJUSTMENTS)
(17) Apply a bead of Moparž Silicone Rubber
Adhesive Sealant to differential cover and install to
case (Fig. 210).(18) Install and torque cover-to-case bolts to 19
N´m (165 in. lbs.) (Fig. 211).
ADJUSTMENT - DIFFERENTIAL BEARING
PRELOAD
NOTE: Perform all differential bearing preload mea-
surements with the transfer shaft and gear
removed.
DIFFERENTIAL BEARING PRELOAD ADJUSTMENT
USING EXISTING SHIM
(1) Position the transaxle assembly vertically on
the support stand, differential bearing retainer side
up.
(2) Install Tool L-4436A into the differential and
onto the pinion mate shaft (Fig. 212).
(3) Rotate the differential at least one full revolu-
tion to ensure the tapered roller bearings are fully
seated.
(4) Using Tool L-4436A and an inch-pound torque
wrench, check the turning torque of the differential
(Fig. 213).The turning torque should be
between 5 and 18 inch-pounds.
(5) If the turning torque is within specifications,
remove tools. Setup is complete.
Fig. 209 Differential Retainer Bolts
1 - DIFFERENTIAL RETAINER BOLTS
Fig. 210 Install Differential Cover
1 - DIFFERENTIAL ASSEMBLY
2 - DIFFERENTIAL COVER
Fig. 211 Differential Cover Bolts
1 - DIFFERENTIAL COVER BOLTS
2 - DIFFERENTIAL COVER
RSAUTOMATIC - 41TE21 - 243
FINAL DRIVE (Continued)
Page 3208 of 4284
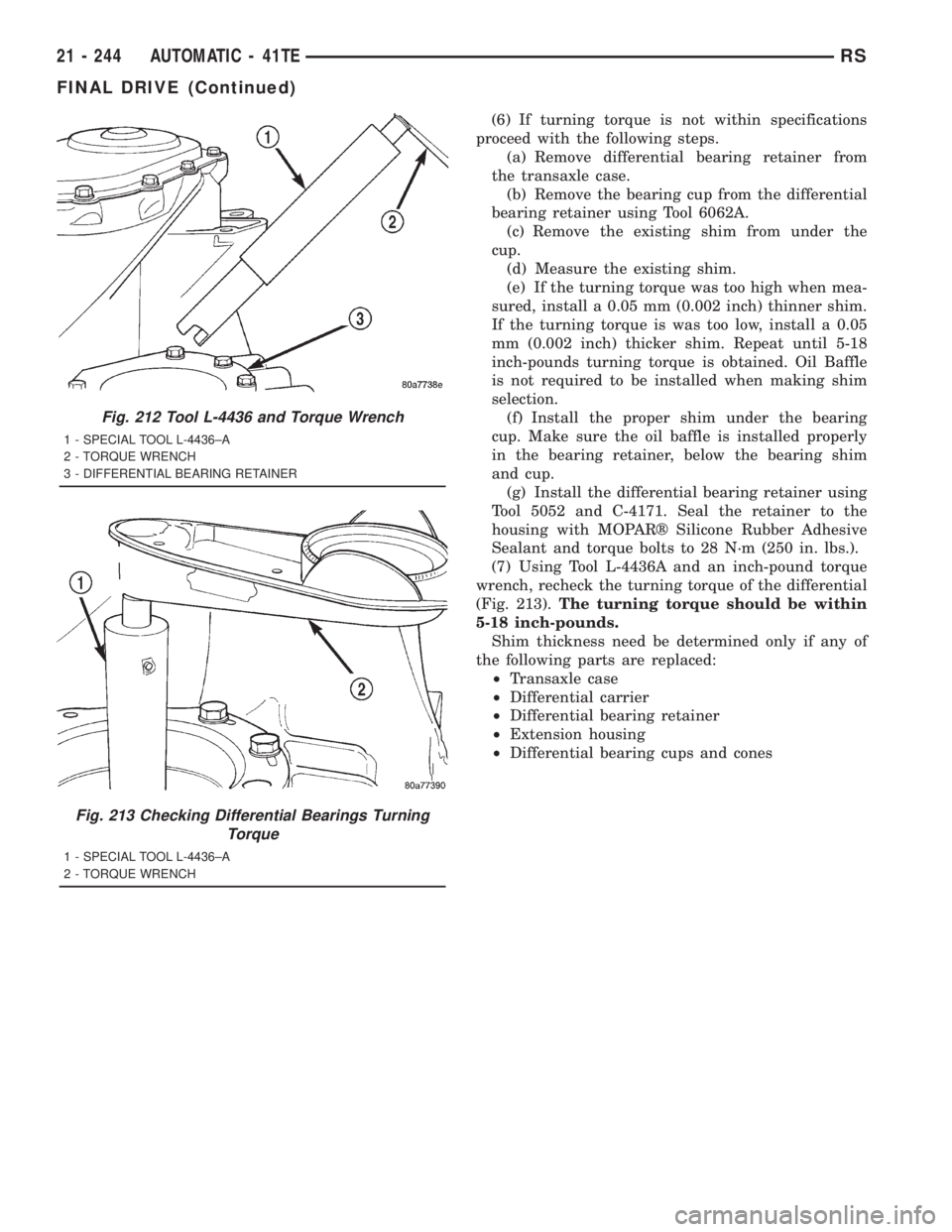
(6) If turning torque is not within specifications
proceed with the following steps.
(a) Remove differential bearing retainer from
the transaxle case.
(b) Remove the bearing cup from the differential
bearing retainer using Tool 6062A.
(c) Remove the existing shim from under the
cup.
(d) Measure the existing shim.
(e) If the turning torque was too high when mea-
sured, install a 0.05 mm (0.002 inch) thinner shim.
If the turning torque is was too low, install a 0.05
mm (0.002 inch) thicker shim. Repeat until 5-18
inch-pounds turning torque is obtained. Oil Baffle
is not required to be installed when making shim
selection.
(f) Install the proper shim under the bearing
cup. Make sure the oil baffle is installed properly
in the bearing retainer, below the bearing shim
and cup.
(g) Install the differential bearing retainer using
Tool 5052 and C-4171. Seal the retainer to the
housing with MOPARž Silicone Rubber Adhesive
Sealant and torque bolts to 28 N´m (250 in. lbs.).
(7) Using Tool L-4436A and an inch-pound torque
wrench, recheck the turning torque of the differential
(Fig. 213).The turning torque should be within
5-18 inch-pounds.
Shim thickness need be determined only if any of
the following parts are replaced:
²Transaxle case
²Differential carrier
²Differential bearing retainer
²Extension housing
²Differential bearing cups and cones
Fig. 212 Tool L-4436 and Torque Wrench
1 - SPECIAL TOOL L-4436±A
2 - TORQUE WRENCH
3 - DIFFERENTIAL BEARING RETAINER
Fig. 213 Checking Differential Bearings Turning
Torque
1 - SPECIAL TOOL L-4436±A
2 - TORQUE WRENCH
21 - 244 AUTOMATIC - 41TERS
FINAL DRIVE (Continued)