Page 2089 of 4284
Fig. 2 WIRING DIAGRAM EXAMPLE 2
RG8W-01 WIRING DIAGRAM INFORMATION8Wa-01-3
WIRING DIAGRAM INFORMATION (Continued)
Page 2090 of 4284
Fig. 3 WIRING DIAGRAM SYMBOLS
8Wa - 01 - 4 8W-01 WIRING DIAGRAM INFORMATIONRG
WIRING DIAGRAM INFORMATION (Continued)
Page 2091 of 4284
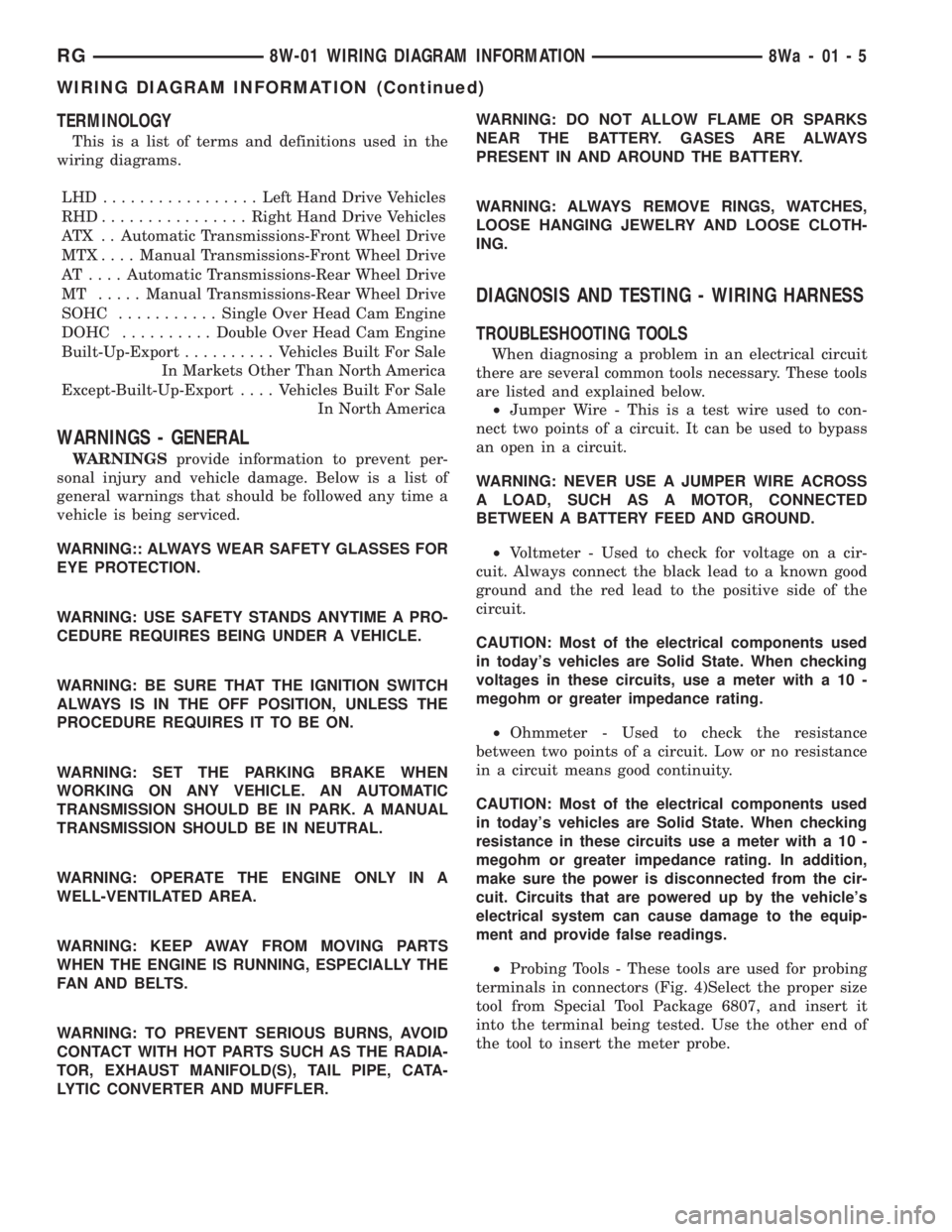
TERMINOLOGY
This is a list of terms and definitions used in the
wiring diagrams.
LHD .................Left Hand Drive Vehicles
RHD................Right Hand Drive Vehicles
ATX . . Automatic Transmissions-Front Wheel Drive
MTX....Manual Transmissions-Front Wheel Drive
AT ....Automatic Transmissions-Rear Wheel Drive
MT .....Manual Transmissions-Rear Wheel Drive
SOHC...........Single Over Head Cam Engine
DOHC..........Double Over Head Cam Engine
Built-Up-Export.......... Vehicles Built For Sale
In Markets Other Than North America
Except-Built-Up-Export.... Vehicles Built For Sale
In North America
WARNINGS - GENERAL
WARNINGSprovide information to prevent per-
sonal injury and vehicle damage. Below is a list of
general warnings that should be followed any time a
vehicle is being serviced.
WARNING:: ALWAYS WEAR SAFETY GLASSES FOR
EYE PROTECTION.
WARNING: USE SAFETY STANDS ANYTIME A PRO-
CEDURE REQUIRES BEING UNDER A VEHICLE.
WARNING: BE SURE THAT THE IGNITION SWITCH
ALWAYS IS IN THE OFF POSITION, UNLESS THE
PROCEDURE REQUIRES IT TO BE ON.
WARNING: SET THE PARKING BRAKE WHEN
WORKING ON ANY VEHICLE. AN AUTOMATIC
TRANSMISSION SHOULD BE IN PARK. A MANUAL
TRANSMISSION SHOULD BE IN NEUTRAL.
WARNING: OPERATE THE ENGINE ONLY IN A
WELL-VENTILATED AREA.
WARNING: KEEP AWAY FROM MOVING PARTS
WHEN THE ENGINE IS RUNNING, ESPECIALLY THE
FAN AND BELTS.
WARNING: TO PREVENT SERIOUS BURNS, AVOID
CONTACT WITH HOT PARTS SUCH AS THE RADIA-
TOR, EXHAUST MANIFOLD(S), TAIL PIPE, CATA-
LYTIC CONVERTER AND MUFFLER.WARNING: DO NOT ALLOW FLAME OR SPARKS
NEAR THE BATTERY. GASES ARE ALWAYS
PRESENT IN AND AROUND THE BATTERY.
WARNING: ALWAYS REMOVE RINGS, WATCHES,
LOOSE HANGING JEWELRY AND LOOSE CLOTH-
ING.
DIAGNOSIS AND TESTING - WIRING HARNESS
TROUBLESHOOTING TOOLS
When diagnosing a problem in an electrical circuit
there are several common tools necessary. These tools
are listed and explained below.
²Jumper Wire - This is a test wire used to con-
nect two points of a circuit. It can be used to bypass
an open in a circuit.
WARNING: NEVER USE A JUMPER WIRE ACROSS
A LOAD, SUCH AS A MOTOR, CONNECTED
BETWEEN A BATTERY FEED AND GROUND.
²Voltmeter - Used to check for voltage on a cir-
cuit. Always connect the black lead to a known good
ground and the red lead to the positive side of the
circuit.
CAUTION: Most of the electrical components used
in today's vehicles are Solid State. When checking
voltages in these circuits, use a meter with a 10 -
megohm or greater impedance rating.
²Ohmmeter - Used to check the resistance
between two points of a circuit. Low or no resistance
in a circuit means good continuity.
CAUTION: Most of the electrical components used
in today's vehicles are Solid State. When checking
resistance in these circuits use a meter with a 10 -
megohm or greater impedance rating. In addition,
make sure the power is disconnected from the cir-
cuit. Circuits that are powered up by the vehicle's
electrical system can cause damage to the equip-
ment and provide false readings.
²Probing Tools - These tools are used for probing
terminals in connectors (Fig. 4)Select the proper size
tool from Special Tool Package 6807, and insert it
into the terminal being tested. Use the other end of
the tool to insert the meter probe.
RG8W-01 WIRING DIAGRAM INFORMATION8Wa-01-5
WIRING DIAGRAM INFORMATION (Continued)
Page 2092 of 4284
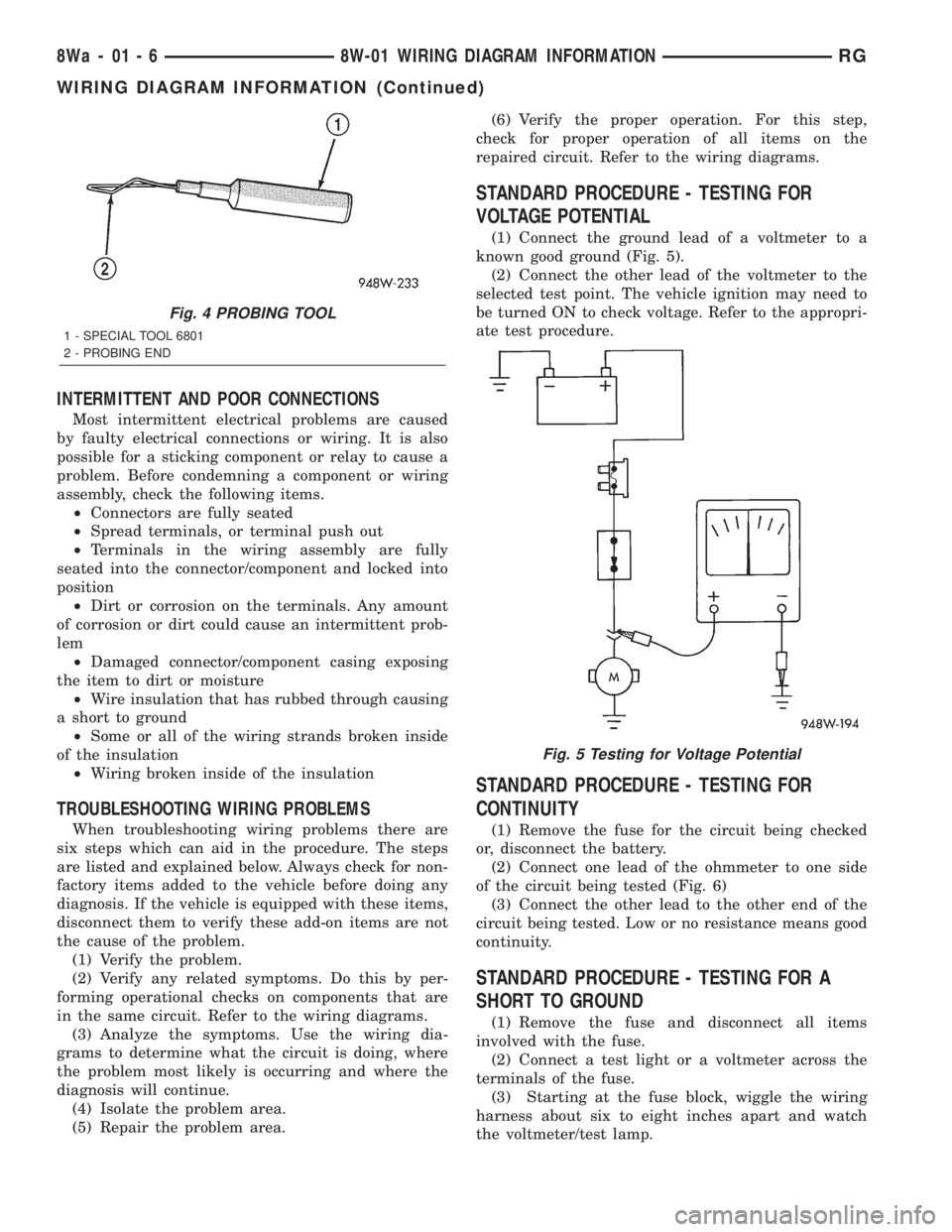
INTERMITTENT AND POOR CONNECTIONS
Most intermittent electrical problems are caused
by faulty electrical connections or wiring. It is also
possible for a sticking component or relay to cause a
problem. Before condemning a component or wiring
assembly, check the following items.
²Connectors are fully seated
²Spread terminals, or terminal push out
²Terminals in the wiring assembly are fully
seated into the connector/component and locked into
position
²Dirt or corrosion on the terminals. Any amount
of corrosion or dirt could cause an intermittent prob-
lem
²Damaged connector/component casing exposing
the item to dirt or moisture
²Wire insulation that has rubbed through causing
a short to ground
²Some or all of the wiring strands broken inside
of the insulation
²Wiring broken inside of the insulation
TROUBLESHOOTING WIRING PROBLEMS
When troubleshooting wiring problems there are
six steps which can aid in the procedure. The steps
are listed and explained below. Always check for non-
factory items added to the vehicle before doing any
diagnosis. If the vehicle is equipped with these items,
disconnect them to verify these add-on items are not
the cause of the problem.
(1) Verify the problem.
(2) Verify any related symptoms. Do this by per-
forming operational checks on components that are
in the same circuit. Refer to the wiring diagrams.
(3) Analyze the symptoms. Use the wiring dia-
grams to determine what the circuit is doing, where
the problem most likely is occurring and where the
diagnosis will continue.
(4) Isolate the problem area.
(5) Repair the problem area.(6) Verify the proper operation. For this step,
check for proper operation of all items on the
repaired circuit. Refer to the wiring diagrams.
STANDARD PROCEDURE - TESTING FOR
VOLTAGE POTENTIAL
(1) Connect the ground lead of a voltmeter to a
known good ground (Fig. 5).
(2) Connect the other lead of the voltmeter to the
selected test point. The vehicle ignition may need to
be turned ON to check voltage. Refer to the appropri-
ate test procedure.
STANDARD PROCEDURE - TESTING FOR
CONTINUITY
(1) Remove the fuse for the circuit being checked
or, disconnect the battery.
(2) Connect one lead of the ohmmeter to one side
of the circuit being tested (Fig. 6)
(3) Connect the other lead to the other end of the
circuit being tested. Low or no resistance means good
continuity.
STANDARD PROCEDURE - TESTING FOR A
SHORT TO GROUND
(1) Remove the fuse and disconnect all items
involved with the fuse.
(2) Connect a test light or a voltmeter across the
terminals of the fuse.
(3) Starting at the fuse block, wiggle the wiring
harness about six to eight inches apart and watch
the voltmeter/test lamp.
Fig. 4 PROBING TOOL
1 - SPECIAL TOOL 6801
2 - PROBING END
Fig. 5 Testing for Voltage Potential
8Wa - 01 - 6 8W-01 WIRING DIAGRAM INFORMATIONRG
WIRING DIAGRAM INFORMATION (Continued)
Page 2093 of 4284
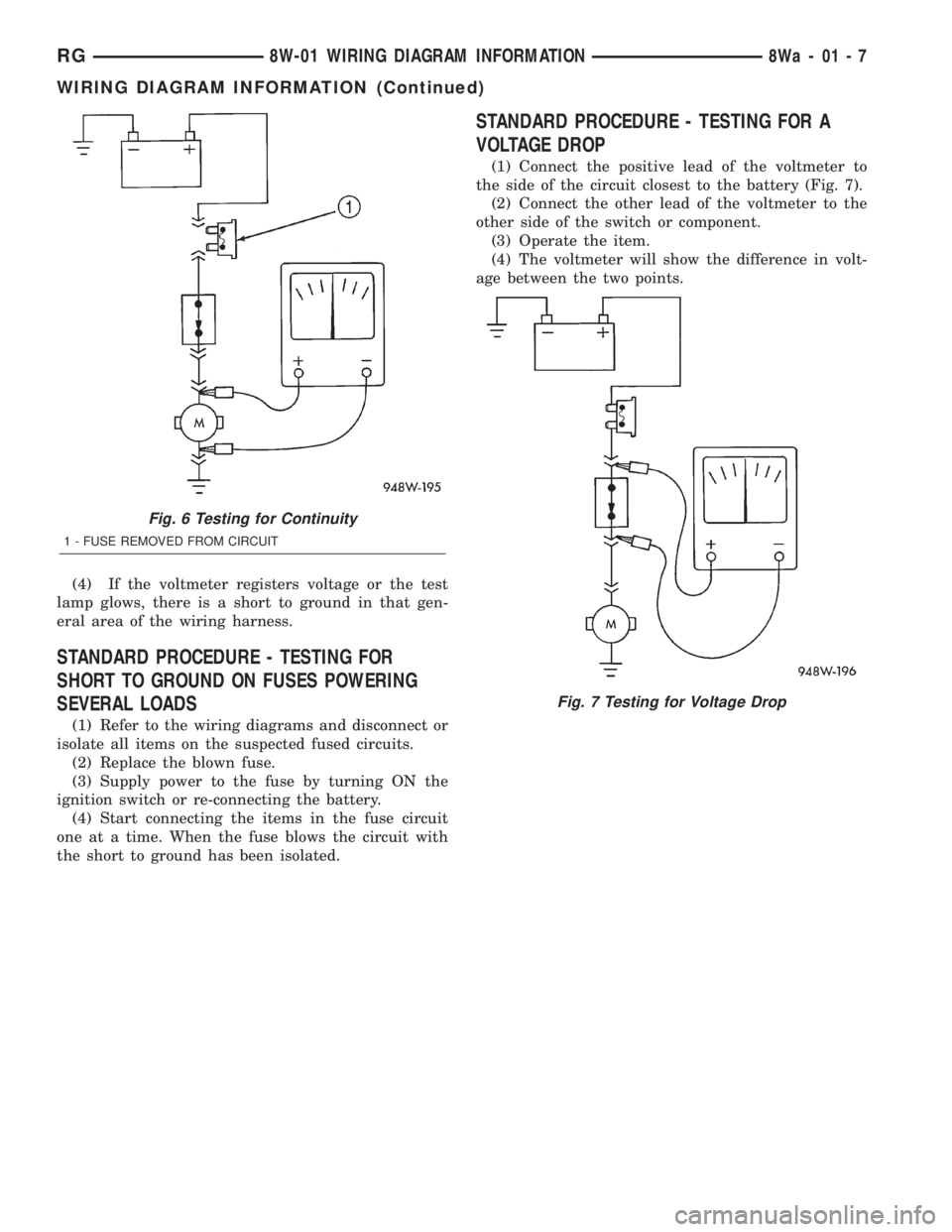
(4) If the voltmeter registers voltage or the test
lamp glows, there is a short to ground in that gen-
eral area of the wiring harness.
STANDARD PROCEDURE - TESTING FOR
SHORT TO GROUND ON FUSES POWERING
SEVERAL LOADS
(1) Refer to the wiring diagrams and disconnect or
isolate all items on the suspected fused circuits.
(2) Replace the blown fuse.
(3) Supply power to the fuse by turning ON the
ignition switch or re-connecting the battery.
(4) Start connecting the items in the fuse circuit
one at a time. When the fuse blows the circuit with
the short to ground has been isolated.
STANDARD PROCEDURE - TESTING FOR A
VOLTAGE DROP
(1) Connect the positive lead of the voltmeter to
the side of the circuit closest to the battery (Fig. 7).
(2) Connect the other lead of the voltmeter to the
other side of the switch or component.
(3) Operate the item.
(4) The voltmeter will show the difference in volt-
age between the two points.
Fig. 6 Testing for Continuity
1 - FUSE REMOVED FROM CIRCUIT
Fig. 7 Testing for Voltage Drop
RG8W-01 WIRING DIAGRAM INFORMATION8Wa-01-7
WIRING DIAGRAM INFORMATION (Continued)
Page 2094 of 4284
SPECIAL TOOLS
SPECIAL TOOLS - WIRING/TERMINALCONNECTOR - AUGAT
REMOVAL
(1) Disconnect battery.
(2) Disconnect the connector from its mating half/
component.
(3) Push down on the yellow connector locking tab
to release the terminals (Fig. 8).
(4) Using special tool 6932, push the terminal to
remove it from the connector (Fig. 9).
(5) Repair or replace the terminal as necessary.
INSTALLATION
(1) Reset the terminal locking tang.
PROBING TOOL PACKAGE 6807
TERMINAL PICK 6680
TERMINAL REMOVING TOOL 6932
TERMINAL REMOVING TOOL 6934
Fig. 8 AUGAT CONNECTOR REPAIR
1 - LOCKING TAB
2 - CONNECTOR
Fig. 9 USING SPECIAL TOOL 6932
1 - SPECIAL TOOL 6932
2 - CONNECTOR
8Wa - 01 - 8 8W-01 WIRING DIAGRAM INFORMATIONRG
WIRING DIAGRAM INFORMATION (Continued)
Page 2095 of 4284
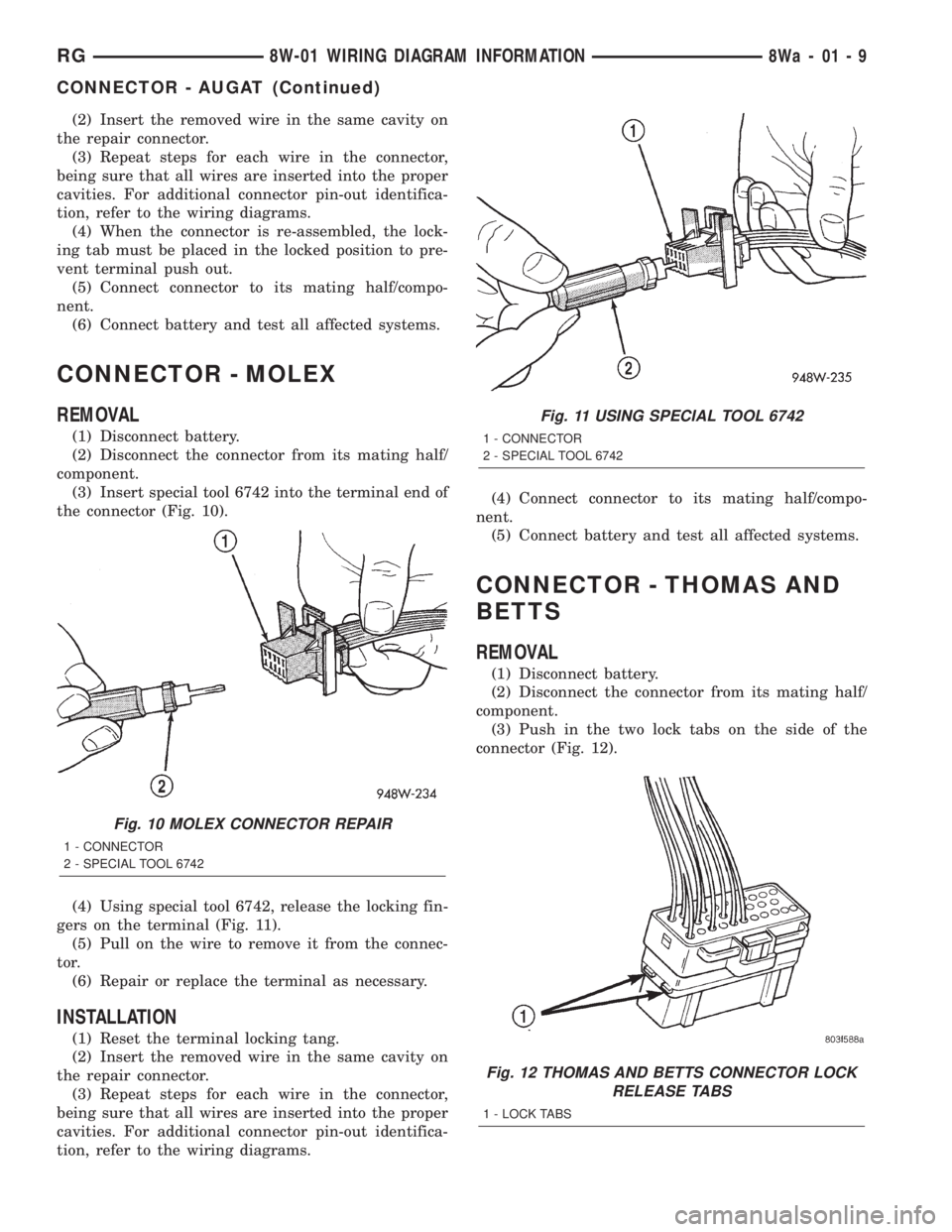
(2) Insert the removed wire in the same cavity on
the repair connector.
(3) Repeat steps for each wire in the connector,
being sure that all wires are inserted into the proper
cavities. For additional connector pin-out identifica-
tion, refer to the wiring diagrams.
(4) When the connector is re-assembled, the lock-
ing tab must be placed in the locked position to pre-
vent terminal push out.
(5) Connect connector to its mating half/compo-
nent.
(6) Connect battery and test all affected systems.
CONNECTOR - MOLEX
REMOVAL
(1) Disconnect battery.
(2) Disconnect the connector from its mating half/
component.
(3) Insert special tool 6742 into the terminal end of
the connector (Fig. 10).
(4) Using special tool 6742, release the locking fin-
gers on the terminal (Fig. 11).
(5) Pull on the wire to remove it from the connec-
tor.
(6) Repair or replace the terminal as necessary.
INSTALLATION
(1) Reset the terminal locking tang.
(2) Insert the removed wire in the same cavity on
the repair connector.
(3) Repeat steps for each wire in the connector,
being sure that all wires are inserted into the proper
cavities. For additional connector pin-out identifica-
tion, refer to the wiring diagrams.(4) Connect connector to its mating half/compo-
nent.
(5) Connect battery and test all affected systems.
CONNECTOR - THOMAS AND
BETTS
REMOVAL
(1) Disconnect battery.
(2) Disconnect the connector from its mating half/
component.
(3) Push in the two lock tabs on the side of the
connector (Fig. 12).
Fig. 10 MOLEX CONNECTOR REPAIR
1 - CONNECTOR
2 - SPECIAL TOOL 6742
Fig. 11 USING SPECIAL TOOL 6742
1 - CONNECTOR
2 - SPECIAL TOOL 6742
Fig. 12 THOMAS AND BETTS CONNECTOR LOCK
RELEASE TABS
1 - LOCK TABS
RG8W-01 WIRING DIAGRAM INFORMATION8Wa-01-9
CONNECTOR - AUGAT (Continued)
Page 2096 of 4284
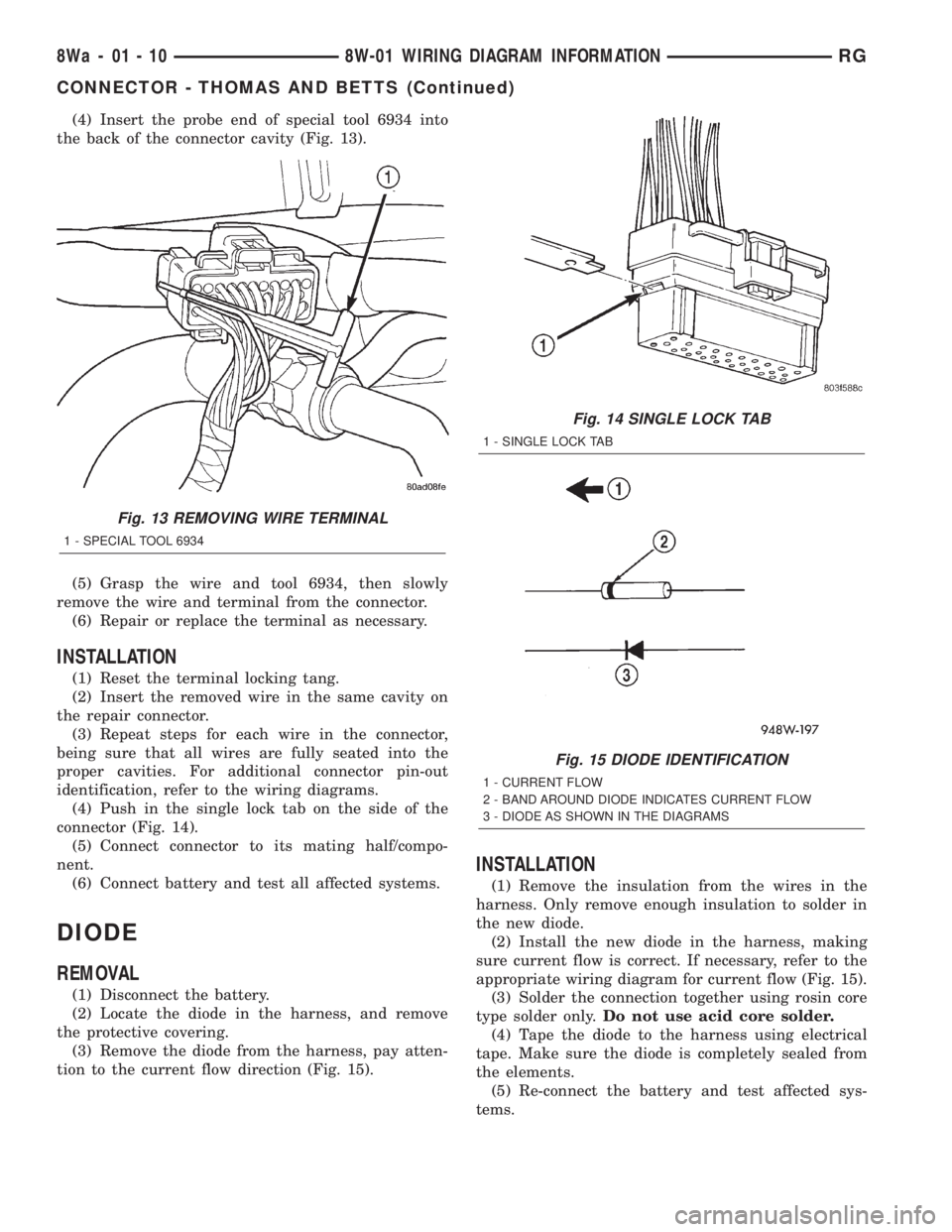
(4) Insert the probe end of special tool 6934 into
the back of the connector cavity (Fig. 13).
(5) Grasp the wire and tool 6934, then slowly
remove the wire and terminal from the connector.
(6) Repair or replace the terminal as necessary.
INSTALLATION
(1) Reset the terminal locking tang.
(2) Insert the removed wire in the same cavity on
the repair connector.
(3) Repeat steps for each wire in the connector,
being sure that all wires are fully seated into the
proper cavities. For additional connector pin-out
identification, refer to the wiring diagrams.
(4) Push in the single lock tab on the side of the
connector (Fig. 14).
(5) Connect connector to its mating half/compo-
nent.
(6) Connect battery and test all affected systems.
DIODE
REMOVAL
(1) Disconnect the battery.
(2) Locate the diode in the harness, and remove
the protective covering.
(3) Remove the diode from the harness, pay atten-
tion to the current flow direction (Fig. 15).
INSTALLATION
(1) Remove the insulation from the wires in the
harness. Only remove enough insulation to solder in
the new diode.
(2) Install the new diode in the harness, making
sure current flow is correct. If necessary, refer to the
appropriate wiring diagram for current flow (Fig. 15).
(3) Solder the connection together using rosin core
type solder only.Do not use acid core solder.
(4) Tape the diode to the harness using electrical
tape. Make sure the diode is completely sealed from
the elements.
(5) Re-connect the battery and test affected sys-
tems.
Fig. 13 REMOVING WIRE TERMINAL
1 - SPECIAL TOOL 6934
Fig. 14 SINGLE LOCK TAB
1 - SINGLE LOCK TAB
Fig. 15 DIODE IDENTIFICATION
1 - CURRENT FLOW
2 - BAND AROUND DIODE INDICATES CURRENT FLOW
3 - DIODE AS SHOWN IN THE DIAGRAMS
8Wa - 01 - 10 8W-01 WIRING DIAGRAM INFORMATIONRG
CONNECTOR - THOMAS AND BETTS (Continued)