Page 3401 of 5621
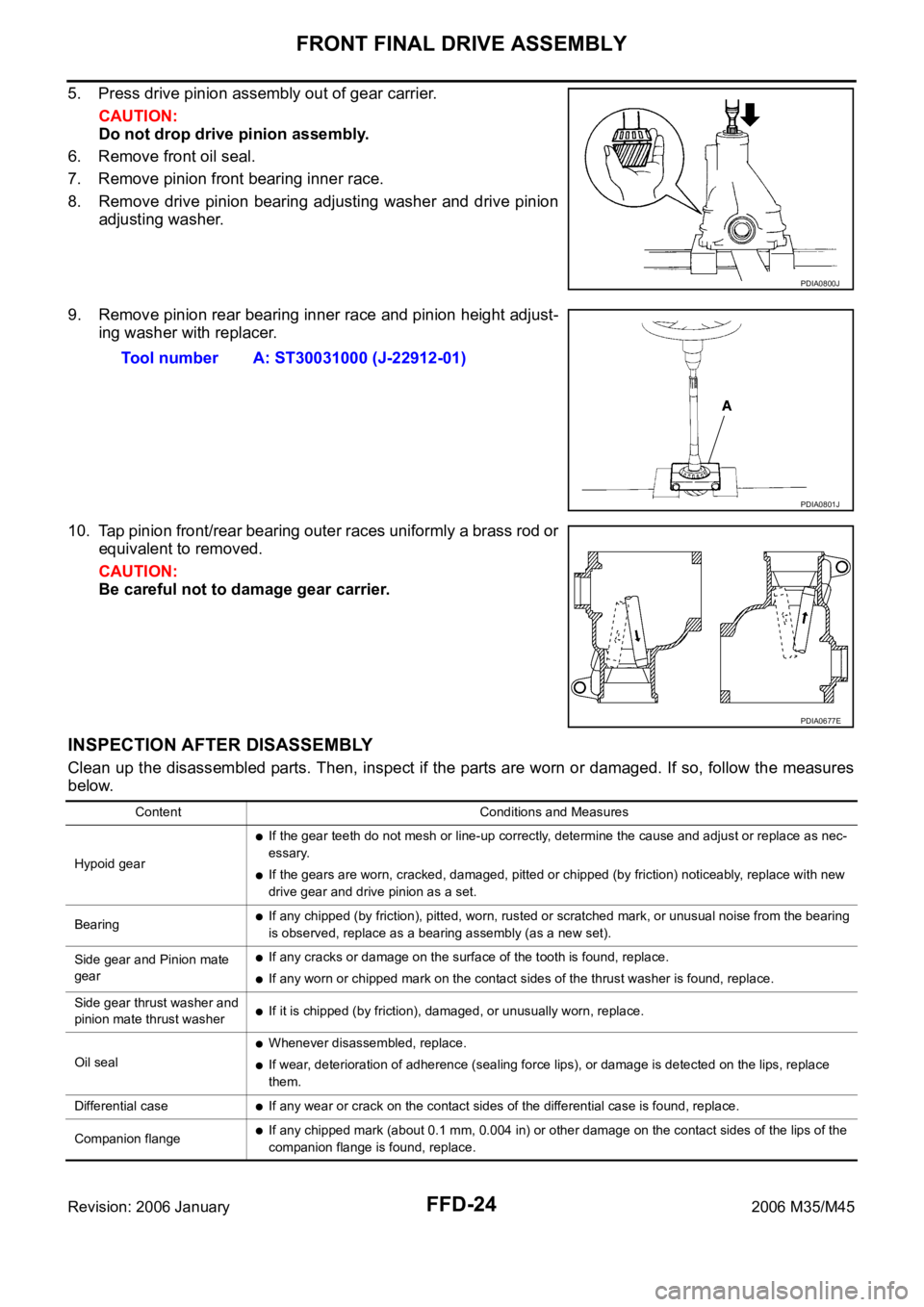
FFD-24
FRONT FINAL DRIVE ASSEMBLY
Revision: 2006 January2006 M35/M45
5. Press drive pinion assembly out of gear carrier.
CAUTION:
Do not drop drive pinion assembly.
6. Remove front oil seal.
7. Remove pinion front bearing inner race.
8. Remove drive pinion bearing adjusting washer and drive pinion
adjusting washer.
9. Remove pinion rear bearing inner race and pinion height adjust-
ing washer with replacer.
10. Tap pinion front/rear bearing outer races uniformly a brass rod or
equivalent to removed.
CAUTION:
Be careful not to damage gear carrier.
INSPECTION AFTER DISASSEMBLY
Clean up the disassembled parts. Then, inspect if the parts are worn or damaged. If so, follow the measures
below.
PDIA0800J
Tool number A: ST30031000 (J-22912-01)
PDIA0801J
PDIA0677E
Content Conditions and Measures
Hypoid gear
If the gear teeth do not mesh or line-up correctly, determine the cause and adjust or replace as nec-
essary.
If the gears are worn, cracked, damaged, pitted or chipped (by friction) noticeably, replace with new
drive gear and drive pinion as a set.
Bearing
If any chipped (by friction), pitted, worn, rusted or scratched mark, or unusual noise from the bearing
is observed, replace as a bearing assembly (as a new set).
Side gear and Pinion mate
gear
If any cracks or damage on the surface of the tooth is found, replace.
If any worn or chipped mark on the contact sides of the thrust washer is found, replace.
Side gear thrust washer and
pinion mate thrust washer
If it is chipped (by friction), damaged, or unusually worn, replace.
Oil seal
Whenever disassembled, replace.
If wear, deterioration of adherence (sealing force lips), or damage is detected on the lips, replace
them.
Differential case
If any wear or crack on the contact sides of the differential case is found, replace.
Companion flange
If any chipped mark (about 0.1 mm, 0.004 in) or other damage on the contact sides of the lips of the
companion flange is found, replace.
Page 3402 of 5621
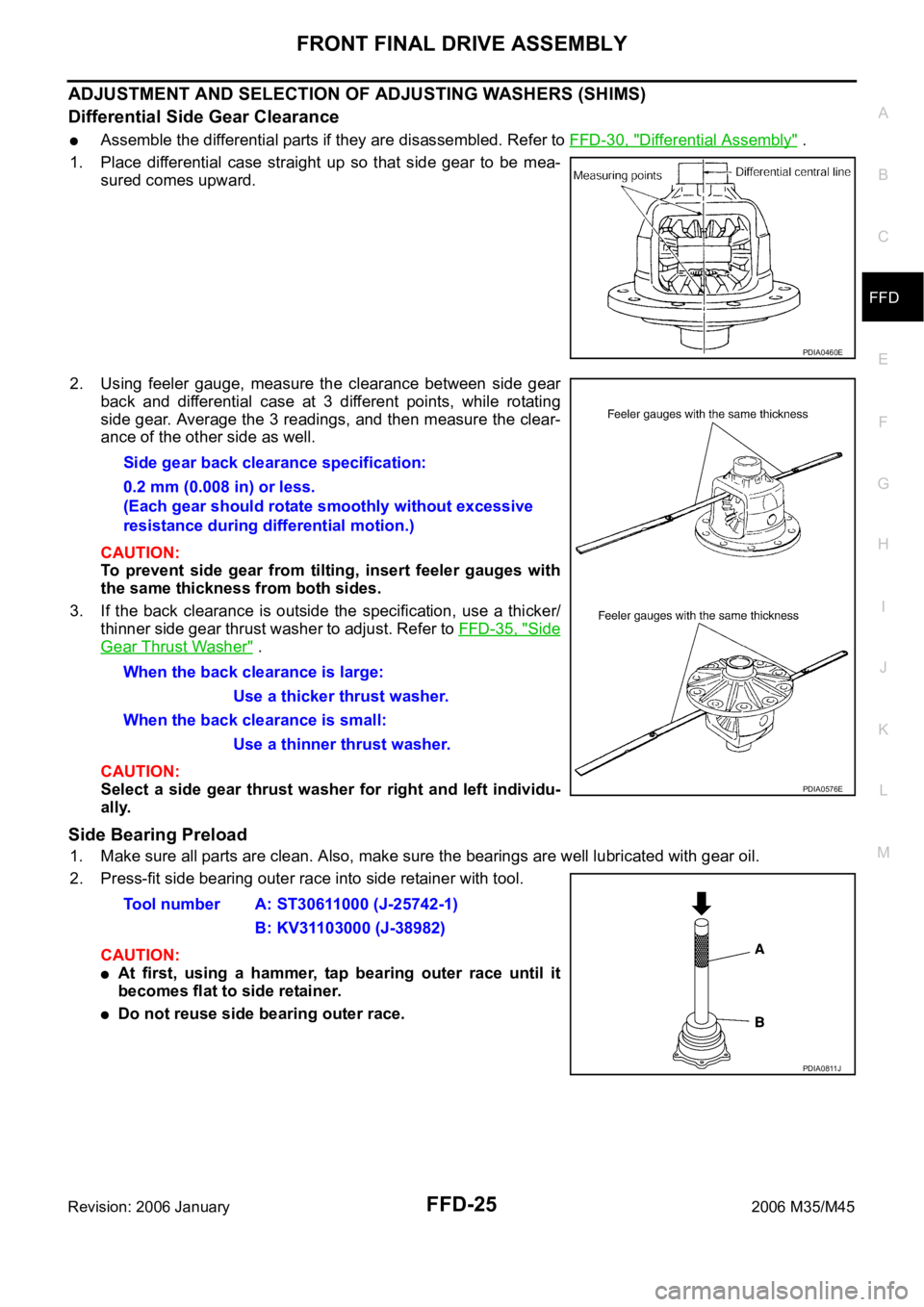
FRONT FINAL DRIVE ASSEMBLY
FFD-25
C
E
F
G
H
I
J
K
L
MA
B
FFD
Revision: 2006 January2006 M35/M45
ADJUSTMENT AND SELECTION OF ADJUSTING WASHERS (SHIMS)
Differential Side Gear Clearance
Assemble the differential parts if they are disassembled. Refer to FFD-30, "Differential Assembly" .
1. Place differential case straight up so that side gear to be mea-
sured comes upward.
2. Using feeler gauge, measure the clearance between side gear
back and differential case at 3 different points, while rotating
side gear. Average the 3 readings, and then measure the clear-
ance of the other side as well.
CAUTION:
To prevent side gear from tilting, insert feeler gauges with
the same thickness from both sides.
3. If the back clearance is outside the specification, use a thicker/
thinner side gear thrust washer to adjust. Refer to FFD-35, "
Side
Gear Thrust Washer" .
CAUTION:
Select a side gear thrust washer for right and left individu-
ally.
Side Bearing Preload
1. Make sure all parts are clean. Also, make sure the bearings are well lubricated with gear oil.
2. Press-fit side bearing outer race into side retainer with tool.
CAUTION:
At first, using a hammer, tap bearing outer race until it
becomes flat to side retainer.
Do not reuse side bearing outer race.
PDIA0460E
Side gear back clearance specification:
0.2 mm (0.008 in) or less.
(Each gear should rotate smoothly without excessive
resistance during differential motion.)
When the back clearance is large:
Use a thicker thrust washer.
When the back clearance is small:
Use a thinner thrust washer.
PDIA0576E
Tool number A: ST30611000 (J-25742-1)
B: KV31103000 (J-38982)
PDIA0811J
Page 3403 of 5621
FFD-26
FRONT FINAL DRIVE ASSEMBLY
Revision: 2006 January2006 M35/M45
3. Press-fit side bearing outer race into gear carrier with tool.
CAUTION:
At first, using a hammer, tap bearing outer race until it
becomes flat to gear carrier.
Do not reuse side bearing outer race.
4. Place the differential case assembly into gear carrier.
5. Install side bearing adjusting shim before disassembling or shim
which thickness is the same as the one before disassembling.
6. Install side retainer assembly to gear carrier.
CAUTION:
Do not install O-ring.
7. Install side retainer mounting bolts to the specified torque. Refer
to FFD-15, "
COMPONENTS" .
8. Measure the turning torque of the gear carrier at the drive gear
mounting bolts with a spring gauge.Tool number A: ST30611000 (J-25742-1)
B: KV31103000 (J-38982)
PDIA0812J
PDIA0671E
PDIA0678E
PDIA0669E
Tool number : — (J-8129)
Specification:
34.2 - 39.2 N (3.5 - 4.0 kg, 7.7 - 8.8 lb) of pulling force at
the drive gear bolt
SPD194A
Page 3404 of 5621
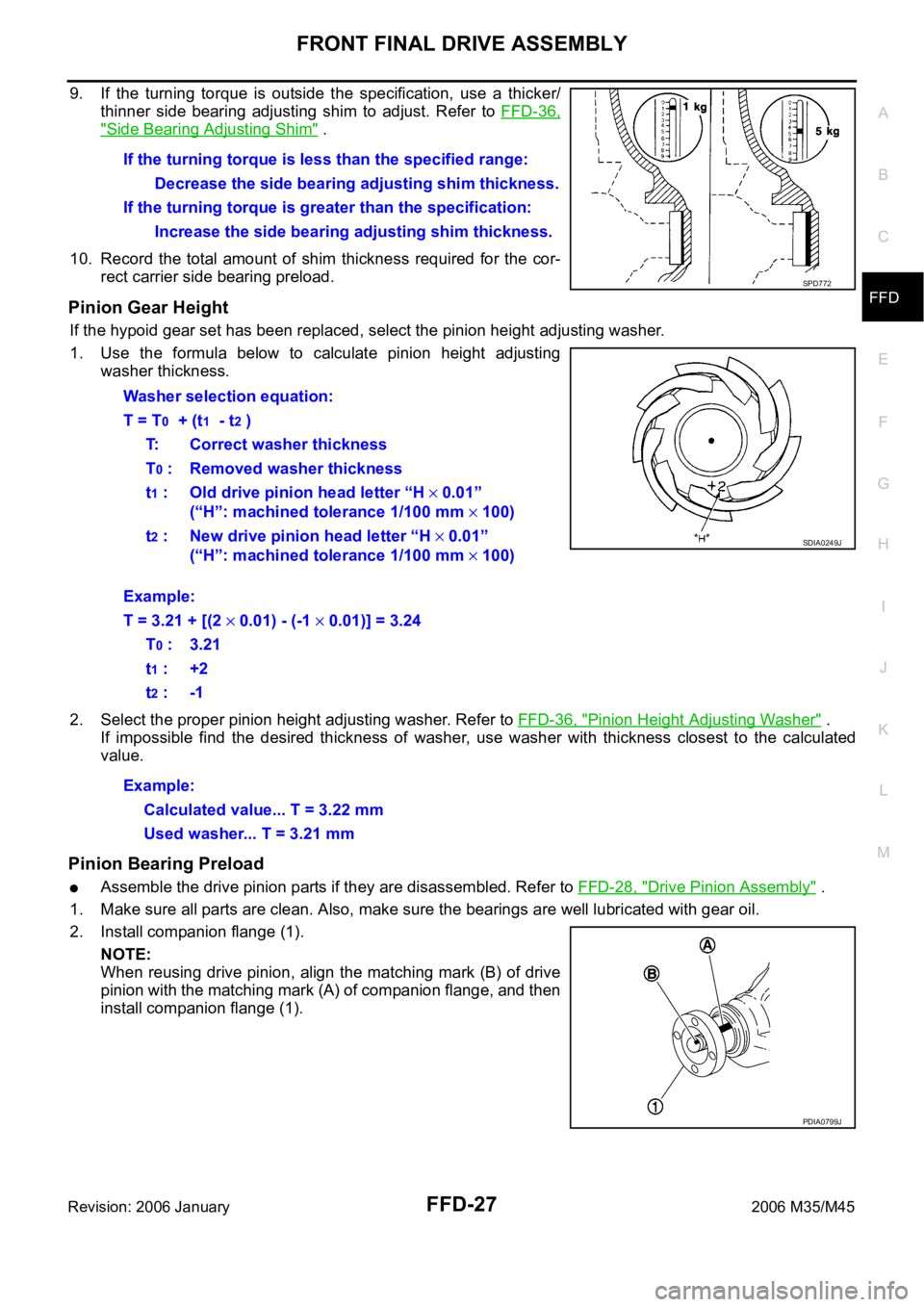
FRONT FINAL DRIVE ASSEMBLY
FFD-27
C
E
F
G
H
I
J
K
L
MA
B
FFD
Revision: 2006 January2006 M35/M45
9. If the turning torque is outside the specification, use a thicker/
thinner side bearing adjusting shim to adjust. Refer to FFD-36,
"Side Bearing Adjusting Shim" .
10. Record the total amount of shim thickness required for the cor-
rect carrier side bearing preload.
Pinion Gear Height
If the hypoid gear set has been replaced, select the pinion height adjusting washer.
1. Use the formula below to calculate pinion height adjusting
washer thickness.
2. Select the proper pinion height adjusting washer. Refer to FFD-36, "
Pinion Height Adjusting Washer" .
If impossible find the desired thickness of washer, use washer with thickness closest to the calculated
value.
Pinion Bearing Preload
Assemble the drive pinion parts if they are disassembled. Refer to FFD-28, "Drive Pinion Assembly" .
1. Make sure all parts are clean. Also, make sure the bearings are well lubricated with gear oil.
2. Install companion flange (1).
NOTE:
When reusing drive pinion, align the matching mark (B) of drive
pinion with the matching mark (A) of companion flange, and then
install companion flange (1).If the turning torque is less than the specified range:
Decrease the side bearing adjusting shim thickness.
If the turning torque is greater than the specification:
Increase the side bearing adjusting shim thickness.
SPD772
Washer selection equation:
T = T
0 + (t1 - t2 )
T: Correct washer thickness
T
0 : Removed washer thickness
t
1 : Old drive pinion head letter “H 0.01”
(“H”: machined tolerance 1/100 mm
100)
t
2 : New drive pinion head letter “H 0.01”
(“H”: machined tolerance 1/100 mm
100)
Example:
T = 3.21 + [(2
0.01) - (-1 0.01)] = 3.24
T
0 : 3.21
t
1 : +2
t
2 : -1
Example:
Calculated value... T = 3.22 mm
Used washer... T = 3.21 mm
SDIA0249J
PDIA0799J
Page 3405 of 5621
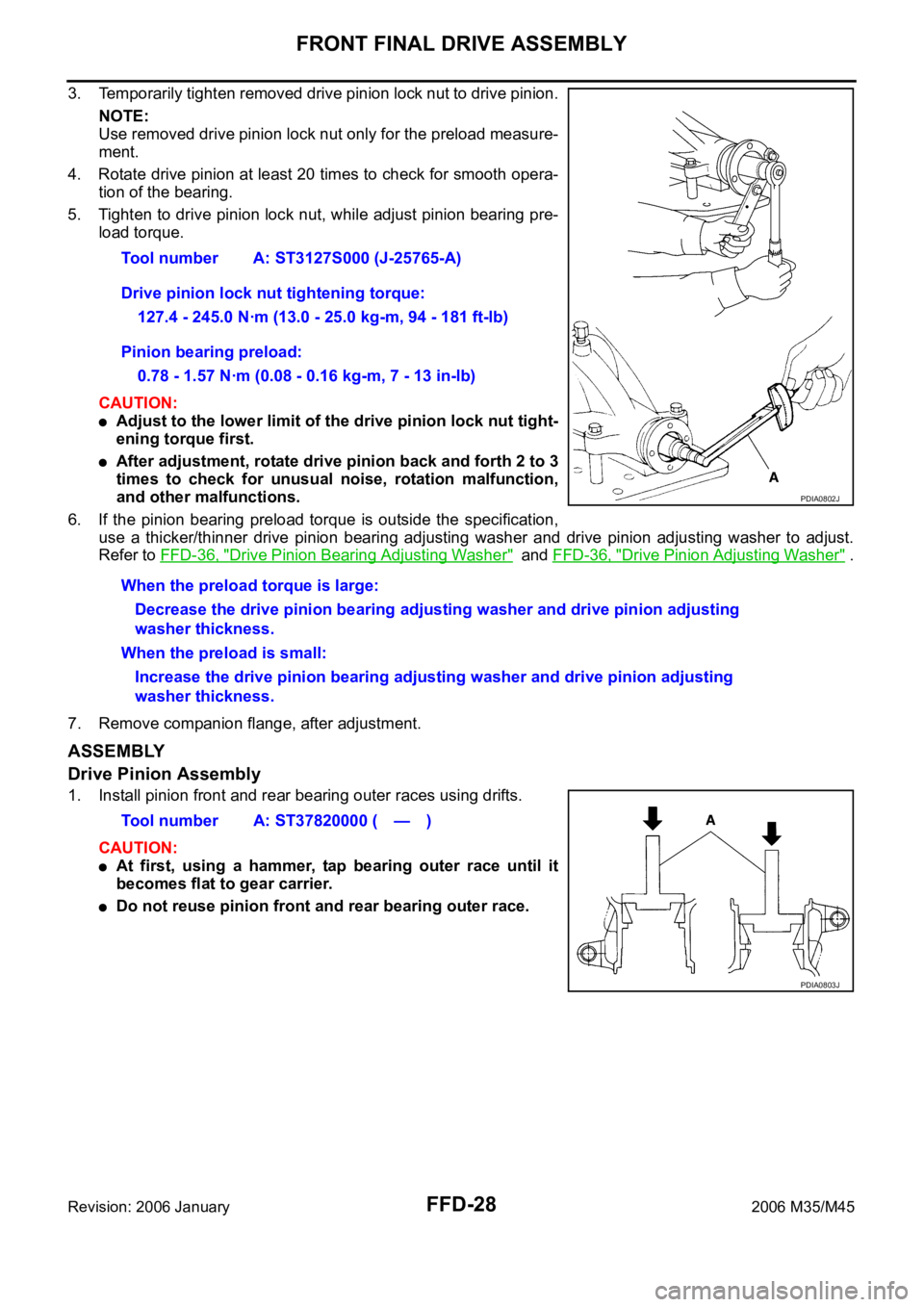
FFD-28
FRONT FINAL DRIVE ASSEMBLY
Revision: 2006 January2006 M35/M45
3. Temporarily tighten removed drive pinion lock nut to drive pinion.
NOTE:
Use removed drive pinion lock nut only for the preload measure-
ment.
4. Rotate drive pinion at least 20 times to check for smooth opera-
tion of the bearing.
5. Tighten to drive pinion lock nut, while adjust pinion bearing pre-
load torque.
CAUTION:
Adjust to the lower limit of the drive pinion lock nut tight-
ening torque first.
After adjustment, rotate drive pinion back and forth 2 to 3
times to check for unusual noise, rotation malfunction,
and other malfunctions.
6. If the pinion bearing preload torque is outside the specification,
use a thicker/thinner drive pinion bearing adjusting washer and drive pinion adjusting washer to adjust.
Refer to FFD-36, "
Drive Pinion Bearing Adjusting Washer" and FFD-36, "Drive Pinion Adjusting Washer" .
7. Remove companion flange, after adjustment.
ASSEMBLY
Drive Pinion Assembly
1. Install pinion front and rear bearing outer races using drifts.
CAUTION:
At first, using a hammer, tap bearing outer race until it
becomes flat to gear carrier.
Do not reuse pinion front and rear bearing outer race.Tool number A: ST3127S000 (J-25765-A)
Drive pinion lock nut tightening torque:
127.4 - 245.0 Nꞏm (13.0 - 25.0 kg-m, 94 - 181 ft-lb)
Pinion bearing preload:
0.78 - 1.57 Nꞏm (0.08 - 0.16 kg-m, 7 - 13 in-lb)
When the preload torque is large:
Decrease the drive pinion bearing adjusting washer and drive pinion adjusting
washer thickness.
When the preload is small:
Increase the drive pinion bearing adjusting washer and drive pinion adjusting
washer thickness.
PDIA0802J
Tool number A: ST37820000 ( — )
PDIA0803J
Page 3406 of 5621
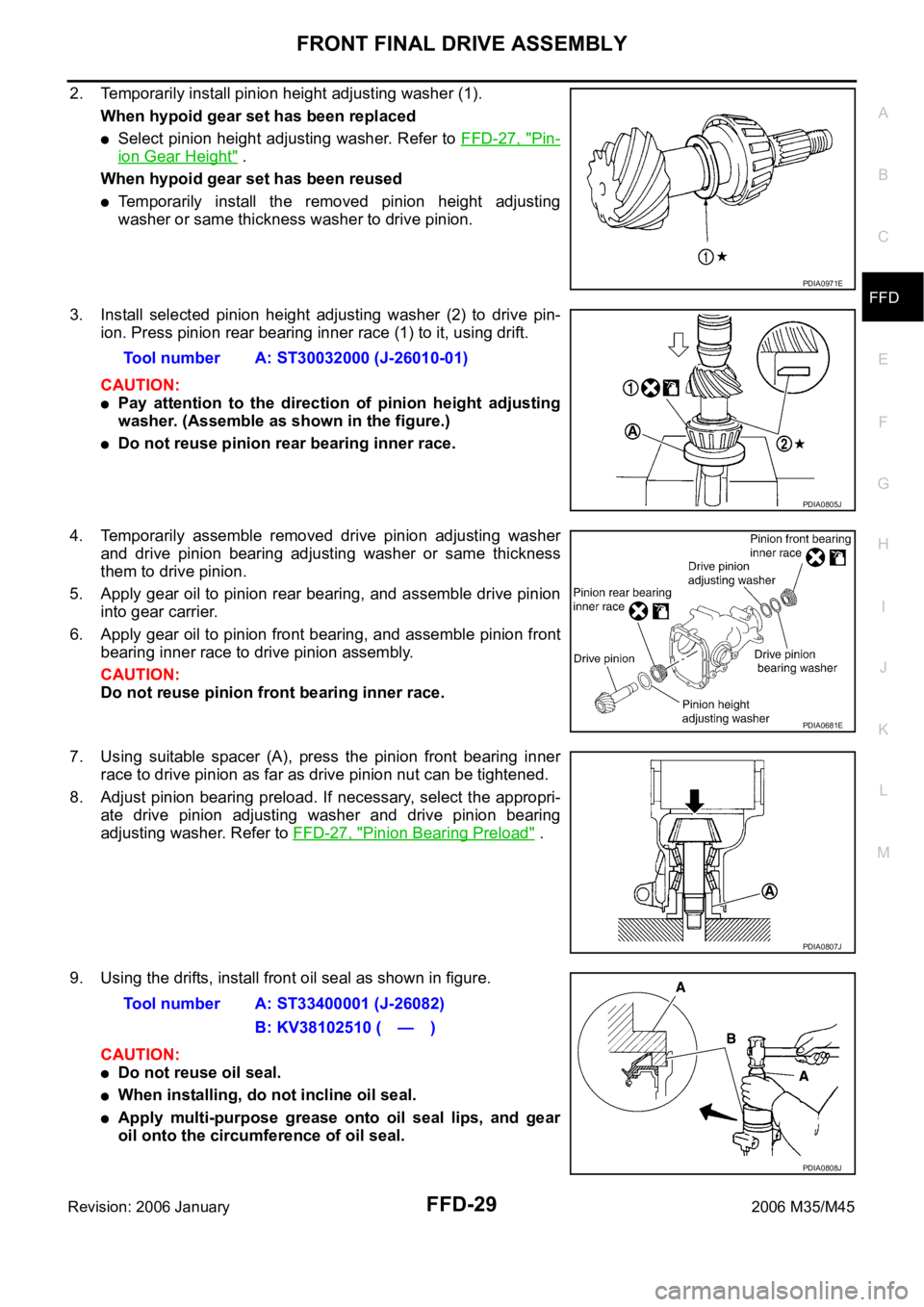
FRONT FINAL DRIVE ASSEMBLY
FFD-29
C
E
F
G
H
I
J
K
L
MA
B
FFD
Revision: 2006 January2006 M35/M45
2. Temporarily install pinion height adjusting washer (1).
When hypoid gear set has been replaced
Select pinion height adjusting washer. Refer to FFD-27, "Pin-
ion Gear Height" .
When hypoid gear set has been reused
Temporarily install the removed pinion height adjusting
washer or same thickness washer to drive pinion.
3. Install selected pinion height adjusting washer (2) to drive pin-
ion. Press pinion rear bearing inner race (1) to it, using drift.
CAUTION:
Pay attention to the direction of pinion height adjusting
washer. (Assemble as shown in the figure.)
Do not reuse pinion rear bearing inner race.
4. Temporarily assemble removed drive pinion adjusting washer
and drive pinion bearing adjusting washer or same thickness
them to drive pinion.
5. Apply gear oil to pinion rear bearing, and assemble drive pinion
into gear carrier.
6. Apply gear oil to pinion front bearing, and assemble pinion front
bearing inner race to drive pinion assembly.
CAUTION:
Do not reuse pinion front bearing inner race.
7. Using suitable spacer (A), press the pinion front bearing inner
race to drive pinion as far as drive pinion nut can be tightened.
8. Adjust pinion bearing preload. If necessary, select the appropri-
ate drive pinion adjusting washer and drive pinion bearing
adjusting washer. Refer to FFD-27, "
Pinion Bearing Preload" .
9. Using the drifts, install front oil seal as shown in figure.
CAUTION:
Do not reuse oil seal.
When installing, do not incline oil seal.
Apply multi-purpose grease onto oil seal lips, and gear
oil onto the circumference of oil seal.
PDIA0971E
Tool number A: ST30032000 (J-26010-01)
PDIA0805J
PDIA0681E
PDIA0807J
Tool number A: ST33400001 (J-26082)
B: KV38102510 ( — )
PDIA0808J
Page 3407 of 5621
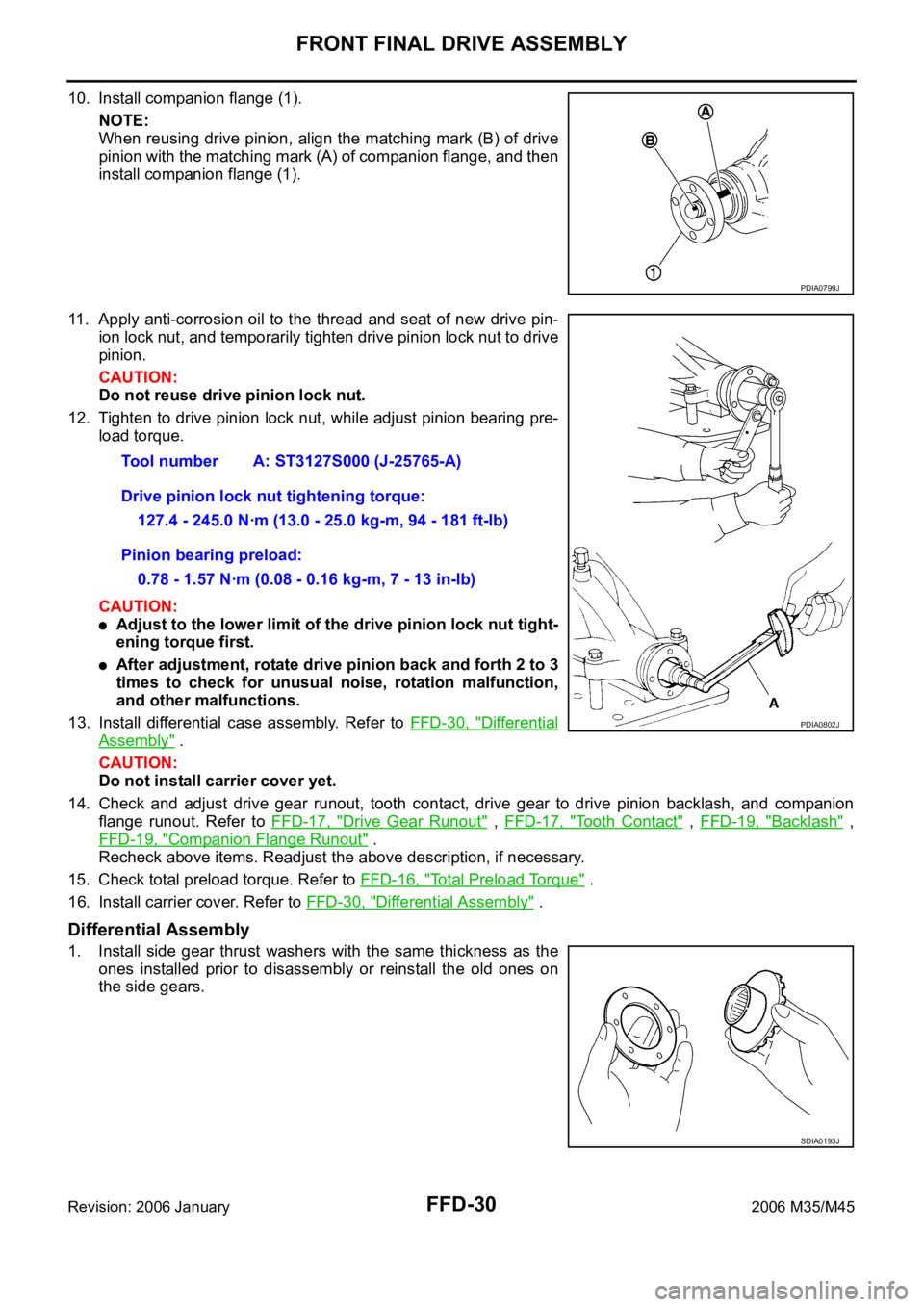
FFD-30
FRONT FINAL DRIVE ASSEMBLY
Revision: 2006 January2006 M35/M45
10. Install companion flange (1).
NOTE:
When reusing drive pinion, align the matching mark (B) of drive
pinion with the matching mark (A) of companion flange, and then
install companion flange (1).
11. Apply anti-corrosion oil to the thread and seat of new drive pin-
ion lock nut, and temporarily tighten drive pinion lock nut to drive
pinion.
CAUTION:
Do not reuse drive pinion lock nut.
12. Tighten to drive pinion lock nut, while adjust pinion bearing pre-
load torque.
CAUTION:
Adjust to the lower limit of the drive pinion lock nut tight-
ening torque first.
After adjustment, rotate drive pinion back and forth 2 to 3
times to check for unusual noise, rotation malfunction,
and other malfunctions.
13. Install differential case assembly. Refer to FFD-30, "
Differential
Assembly" .
CAUTION:
Do not install carrier cover yet.
14. Check and adjust drive gear runout, tooth contact, drive gear to drive pinion backlash, and companion
flange runout. Refer to FFD-17, "
Drive Gear Runout" , FFD-17, "Tooth Contact" , FFD-19, "Backlash" ,
FFD-19, "
Companion Flange Runout" .
Recheck above items. Readjust the above description, if necessary.
15. Check total preload torque. Refer to FFD-16, "
Total Preload Torque" .
16. Install carrier cover. Refer to FFD-30, "
Differential Assembly" .
Differential Assembly
1. Install side gear thrust washers with the same thickness as the
ones installed prior to disassembly or reinstall the old ones on
the side gears.
PDIA0799J
Tool number A: ST3127S000 (J-25765-A)
Drive pinion lock nut tightening torque:
127.4 - 245.0 Nꞏm (13.0 - 25.0 kg-m, 94 - 181 ft-lb)
Pinion bearing preload:
0.78 - 1.57 Nꞏm (0.08 - 0.16 kg-m, 7 - 13 in-lb)
PDIA0802J
SDIA0193J
Page 3408 of 5621
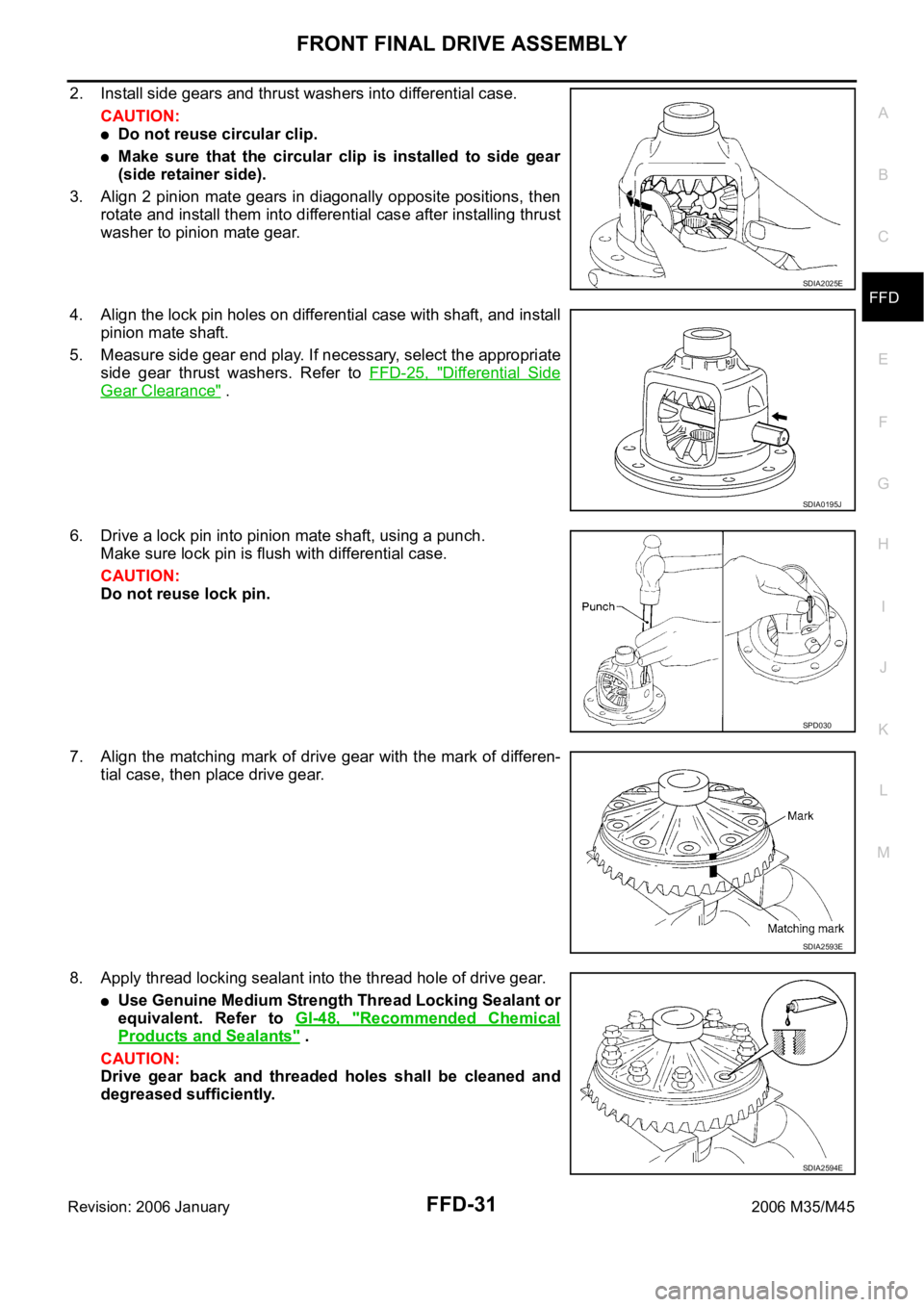
FRONT FINAL DRIVE ASSEMBLY
FFD-31
C
E
F
G
H
I
J
K
L
MA
B
FFD
Revision: 2006 January2006 M35/M45
2. Install side gears and thrust washers into differential case.
CAUTION:
Do not reuse circular clip.
Make sure that the circular clip is installed to side gear
(side retainer side).
3. Align 2 pinion mate gears in diagonally opposite positions, then
rotate and install them into differential case after installing thrust
washer to pinion mate gear.
4. Align the lock pin holes on differential case with shaft, and install
pinion mate shaft.
5. Measure side gear end play. If necessary, select the appropriate
side gear thrust washers. Refer to FFD-25, "
Differential Side
Gear Clearance" .
6. Drive a lock pin into pinion mate shaft, using a punch.
Make sure lock pin is flush with differential case.
CAUTION:
Do not reuse lock pin.
7. Align the matching mark of drive gear with the mark of differen-
tial case, then place drive gear.
8. Apply thread locking sealant into the thread hole of drive gear.
Use Genuine Medium Strength Thread Locking Sealant or
equivalent. Refer to GI-48, "
Recommended Chemical
Products and Sealants" .
CAUTION:
Drive gear back and threaded holes shall be cleaned and
degreased sufficiently.
SDIA2025E
SDIA0195J
SPD030
SDIA2593E
SDIA2594E