Page 3457 of 5621
![INFINITI M35 2006 Factory Service Manual FSU-30
[AWD]
COIL SPRING AND SHOCK ABSORBER
Revision: 2006 January2006 M35/M45
CAUTION:
Install coil spring as shown in the figure with large diame-
ter side [100 mm (3.94 in)] up and small diameter s INFINITI M35 2006 Factory Service Manual FSU-30
[AWD]
COIL SPRING AND SHOCK ABSORBER
Revision: 2006 January2006 M35/M45
CAUTION:
Install coil spring as shown in the figure with large diame-
ter side [100 mm (3.94 in)] up and small diameter s](/manual-img/42/57023/w960_57023-3456.png)
FSU-30
[AWD]
COIL SPRING AND SHOCK ABSORBER
Revision: 2006 January2006 M35/M45
CAUTION:
Install coil spring as shown in the figure with large diame-
ter side [100 mm (3.94 in)] up and small diameter side [90
mm (3.54 in)] down. (Distinction marks are 4.75 and 5.75
turn from the lower side end.)
Be sure a spring compress or is securely attached to coil
spring. Compress coil spring.
3. Apply soapy water to bound bumper. Insert bound bumper into
shock absorber mounting bracket, and then install it to shock
absorber together with rubber seat.
CAUTION:
Do not use machine oil.
Install shock absorber mounting bracket as shown in the fig-
ure.
CAUTION:
Coil spring is securely seated in spring mounting groove
of rubber seat.
The bottom part of spring should be at the position of A
point of spring seat.
4. Secure piston rod tip so that piston rod does not turn, then
tighten piston rod lock nut with specified torque.
5. Gradually release a spring compressor, and remove coil spring.
CAUTION:
Loosen while making sure coil spring attachment position
does not move.
6. Remove the strut attachment from shock absorber.
SEIA0661E
SEIA0662E
Page 3458 of 5621
![INFINITI M35 2006 Factory Service Manual TRANSVERSE LINK
FSU-31
[AWD]
C
D
F
G
H
I
J
K
L
MA
B
FSU
Revision: 2006 January2006 M35/M45
TRANSVERSE LINKPFP:54500
Removal and InstallationNES000IW
REMOVAL
1. Remove tires from vehicle with a power t INFINITI M35 2006 Factory Service Manual TRANSVERSE LINK
FSU-31
[AWD]
C
D
F
G
H
I
J
K
L
MA
B
FSU
Revision: 2006 January2006 M35/M45
TRANSVERSE LINKPFP:54500
Removal and InstallationNES000IW
REMOVAL
1. Remove tires from vehicle with a power t](/manual-img/42/57023/w960_57023-3457.png)
TRANSVERSE LINK
FSU-31
[AWD]
C
D
F
G
H
I
J
K
L
MA
B
FSU
Revision: 2006 January2006 M35/M45
TRANSVERSE LINKPFP:54500
Removal and InstallationNES000IW
REMOVAL
1. Remove tires from vehicle with a power tool.
2. Remove undercover with a power tool.
3. Remove the mounting nut on the upper side of stabilizer connecting rod with a power tool, and then
remove stabilizer connecting rod from transverse link.
4. Remove the mounting nut and bolt on the lower side of shock absorber arm with a power tool, and then
remove shock absorber arm from transverse link.
5. Remove front cross bar. Refer to FSU-25, "
Components" .
6. Remove transverse link from steering knuckle. Refer to FAX-5, "
Removal and Installation" .
7. Remove mounting nuts and bolts, and then remove transverse link from vehicle.
INSPECTION AFTER REMOVAL
Visual Inspection
Check the following:
Transverse link and bushing for deformation, cracks or damage. Replace it if a malfunction is detected.
Ball joint boot for cracks or other damage, and also for grease leakage. Replace it if a malfunction is
detected.
Ball Joint Inspection
Manually move ball stud to confirm it moves smoothly with no binding.
Swing Torque Inspection
NOTE:
Before measurement, move ball stud at least ten times by hand to check for smooth movement.
Hook a spring balance at cotter pin mounting hole. Confirm
spring balance measurement value is within specifications when
ball stud begins moving.
If it is outside the specified range, replace transverse link
assembly.
Rotating Torque Inspection
Attach mounting nut to ball stud. Make sure that rotating torque
is within specifications with a preload gauge [SST].
If it is outside the specified range, replace transverse link
assembly.
Axial End Play Inspection
Move tip of ball stud in axial direction to check for looseness.
If it is outside the specified range, replace transverse link assembly. Swing torque
: 0.5 - 3.6 Nꞏm (0.06 - 0.36 kg-m, 5 - 31 in-lb)
Spring balance measurement
: 7.8 - 56.3 N (0.8 - 5.7 kg, 1.8 - 12.5 lb)
SEIA0523E
Rotating torque
: 0.5 - 3.9 Nꞏm (0.06 - 0.39 kg-m, 5 - 34 in-lb)
SDIA1150E
Axial end play : 0 mm (0 in)
Page 3459 of 5621
FSU-32
[AWD]
TRANSVERSE LINK
Revision: 2006 January2006 M35/M45
INSTALLATION
Installation is the reverse order of removal. For tightening torque, refer to FSU-25, "Components" .
Perform final tightening of bolts and nuts at the front suspension member installation position and the
shock absorber lower side (rubber bushing) under unladen conditions with tires on level ground. Check
wheel alignment. Refer to FSU-23, "
Wheel Alignment Inspection" .
Adjust neutral position of steering angle sensor after checking wheel alignment. Refer to BRC-6, "Adjust-
ment of Steering Angle Sensor Neutral Position" .
Page 3460 of 5621
![INFINITI M35 2006 Factory Service Manual UPPER LINK
FSU-33
[AWD]
C
D
F
G
H
I
J
K
L
MA
B
FSU
Revision: 2006 January2006 M35/M45
UPPER LINKPFP:54524
Removal and InstallationNES000IX
REMOVAL
1. Remove tires from vehicle with a power tool.
2. Re INFINITI M35 2006 Factory Service Manual UPPER LINK
FSU-33
[AWD]
C
D
F
G
H
I
J
K
L
MA
B
FSU
Revision: 2006 January2006 M35/M45
UPPER LINKPFP:54524
Removal and InstallationNES000IX
REMOVAL
1. Remove tires from vehicle with a power tool.
2. Re](/manual-img/42/57023/w960_57023-3459.png)
UPPER LINK
FSU-33
[AWD]
C
D
F
G
H
I
J
K
L
MA
B
FSU
Revision: 2006 January2006 M35/M45
UPPER LINKPFP:54524
Removal and InstallationNES000IX
REMOVAL
1. Remove tires from vehicle with a power tool.
2. Remove shock absorber. Refer to FSU-28, "
COIL SPRING AND SHOCK ABSORBER" .
3. Remove mounting nut and bolt with a power tool, and then remove upper link from steering knuckle.
4. Remove mounting nuts and bolts, and then remove upper link and stopper rubber from vehicle.
INSPECTION AFTER REMOVAL
Visual Inspection
Check the following:
Upper link and bushing for deformation, cracks or damage. Replace it if a malfunction is detected.
Ball joint boot for cracks or other damage, and also for grease leakage. Replace it if a malfunction is
detected.
Ball Joint Inspection
Manually move ball stud to confirm it moves smoothly with no binding.
Swing Torque Inspection
NOTE:
Before measurement, move ball stud at least ten times by hand to check for smooth movement.
Hook a spring balance at cutout on ball stud. Confirm spring bal-
ance measurement value is within specifications when ball stud
begins moving.
If it is outside the specified range, replace upper link assembly.
Rotating Torque Inspection
Attach mounting nut to ball stud. Make sure that rotating torque
is within specifications with a preload gauge [SST].
If it is outside the specified range, replace upper link assembly.
Axial End Play Inspection
Move tip of ball stud in axial direction to check for looseness.
If it is outside the specified range, replace upper link assembly.
INSTALLATION
Installation is the reverse order of removal. For tightening torque, refer to FSU-25, "Components" .
Perform final tightening of bolts and nuts at the vehicle installation position (rubber bushing) under
unladen conditions with tires on level ground. Check wheel alignment. Refer to FSU-23, "
Wheel Align-
ment Inspection" . Swing torque
: 0 - 2.0 Nꞏm (0 - 0.2 kg-m, 0 - 17 in-lb)
Spring balance measurement
: 0 - 61.5 N (0 - 6.2 kg, 0 - 13.6 lb)
SEIA0523E
Rotating torque
: 0 - 2.0 Nꞏm (0 - 0.2 kg-m, 0 - 17 in-lb)
SDIA1150E
Axial end play : 0 mm (0 in)
Page 3461 of 5621
FSU-34
[AWD]
UPPER LINK
Revision: 2006 January2006 M35/M45
Adjust neutral position of steering angle sensor after checking wheel alignment. Refer to BRC-6, "Adjust-
ment of Steering Angle Sensor Neutral Position" .
Page 3462 of 5621
![INFINITI M35 2006 Factory Service Manual STABILIZER BAR
FSU-35
[AWD]
C
D
F
G
H
I
J
K
L
MA
B
FSU
Revision: 2006 January2006 M35/M45
STABILIZER BARPFP:54611
Removal and InstallationNES000IY
REMOVAL
1. Remove tires from vehicle with a power too INFINITI M35 2006 Factory Service Manual STABILIZER BAR
FSU-35
[AWD]
C
D
F
G
H
I
J
K
L
MA
B
FSU
Revision: 2006 January2006 M35/M45
STABILIZER BARPFP:54611
Removal and InstallationNES000IY
REMOVAL
1. Remove tires from vehicle with a power too](/manual-img/42/57023/w960_57023-3461.png)
STABILIZER BAR
FSU-35
[AWD]
C
D
F
G
H
I
J
K
L
MA
B
FSU
Revision: 2006 January2006 M35/M45
STABILIZER BARPFP:54611
Removal and InstallationNES000IY
REMOVAL
1. Remove tires from vehicle with a power tool.
2. Remove undercover with a power tool.
3. Remove the mounting nut on the lower side of stabilizer connecting rod with a power tool, and then
remove stabilizer connecting rod from stabilizer bar.
4. If necessary remove the mounting nut on the upper side of stabilizer connecting rod with a power tool, and
then remove stabilizer connecting rod from transverse link.
5. Remove the mounting nuts of stabilizer clamp, and then remove stabilizer clamp and stabilizer bushing.
6. Remove stabilizer bar from vehicle.
INSPECTION AFTER REMOVAL
Check stabilizer bar, stabilizer connecting rod, stabilizer bushing, and stabilizer clamp for deformation, cracks
or damage. Replace it if a malfunction is detected.
INSTALLATION
Installation is the reverse order of removal. For tightening torque, refer to FSU-25, "Components" .
Page 3463 of 5621
![INFINITI M35 2006 Factory Service Manual FSU-36
[AWD]
SERVICE DATA AND SPECIFICATIONS (SDS)
Revision: 2006 January2006 M35/M45
SERVICE DATA AND SPECIFICATIONS (SDS)PFP:00030
Wheel Alignment (Unladen)NES000IZ
Ball JointNES000J0
Wheelarch Heig INFINITI M35 2006 Factory Service Manual FSU-36
[AWD]
SERVICE DATA AND SPECIFICATIONS (SDS)
Revision: 2006 January2006 M35/M45
SERVICE DATA AND SPECIFICATIONS (SDS)PFP:00030
Wheel Alignment (Unladen)NES000IZ
Ball JointNES000J0
Wheelarch Heig](/manual-img/42/57023/w960_57023-3462.png)
FSU-36
[AWD]
SERVICE DATA AND SPECIFICATIONS (SDS)
Revision: 2006 January2006 M35/M45
SERVICE DATA AND SPECIFICATIONS (SDS)PFP:00030
Wheel Alignment (Unladen)NES000IZ
Ball JointNES000J0
Wheelarch Height (Unladen*)NES000J1
*: Fuel, engine coolant and lubricant are full. Spare tire, jack, hand tools and mats are in designated positions. Camber
Degree minute (Decimal degree)Minimum – 1
00 (– 1.00)
Nominal – 0
15 (– 0.25)
Maximum 0
30 (– 0.50)
Left and right difference 33
(0.55) or less
Caster
Degree minute (Decimal degree)Minimum 3
05 (3.08)
Nominal 3
50 (3.83)
Maximum 4
35(4.58)
Left and right difference 39
(0.65) or less
Kingpin inclination
Degree minute (Decimal degree)Minimum 6
30 (6.50)
Nominal 7
15 (7.25)
Maximum 8
00 (8.00)
Total toe-inDistanceMinimum 0 mm (0 in)
Nominal 1 mm (0.04 in)
Maximum 2 mm (0.08 in)
Angle (left plus right)
Degree minute (Degree)Minimum 0
(0)
Nominal 3
(0.05)
Maximum 6
(0.10)
Swing torqueTransverse link 0.5 - 3.6 Nꞏm (0.06 - 0.36 kg-m, 5 - 31 in-lb)
Upper link 0 - 2.0 Nꞏm (0 - 0.2 kg-m, 0 - 17 in-lb)
Measurement on spring balanceTransverse link 7.8 - 56.3 N (0.8 - 5.7 kg, 1.8 - 12.5 lb)
Upper link 0 - 61.5 N (0 - 6.2 kg, 0 - 13.6 lb)
Rotating torqueTransverse link 0.5 - 3.9 Nꞏm (0.06 - 0.39 kg-m, 5 - 34 in-lb)
Upper link 0 - 2.0 Nꞏm (0 - 0.2 kg-m, 0 - 17 in-lb)
Axial end play0 mm (0 in)
Tire245/45R18
Front (Hf)USA 731 mm (28.78 in)
CANADA 732 mm (28.82 in)
Rear (Hr)USA 725 mm (28.54 in)
CANADA 726 mm (28.58 in)
SFA818A
Page 3464 of 5621
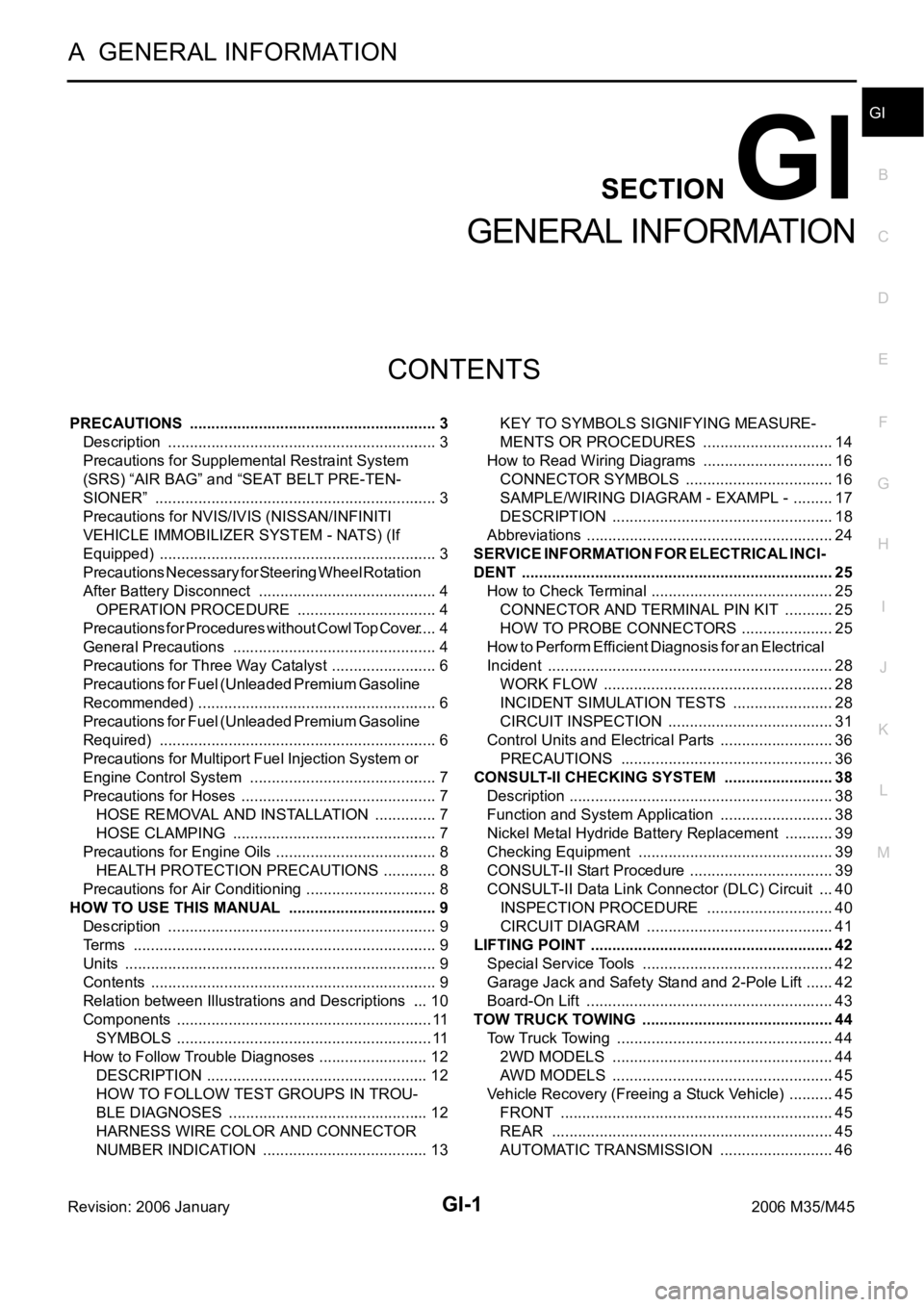
GI-1
GENERAL INFORMATION
A GENERAL INFORMATION
CONTENTS
C
D
E
F
G
H
I
J
K
L
MB
GI
SECTION GI
Revision: 2006 January2006 M35/M45
GENERAL INFORMATION
PRECAUTIONS .......................................................... 3
Description ............................................................... 3
Precautions for Supplemental Restraint System
(SRS) “AIR BAG” and “SEAT BELT PRE-TEN-
SIONER” .................................................................. 3
Precautions for NVIS/IVIS (NISSAN/INFINITI
VEHICLE IMMOBILIZER SYSTEM - NATS) (If
Equipped) ................................................................. 3
Precautions Necessary for Steering Wheel Rotation
After Battery Disconnect .......................................... 4
OPERATION PROCEDURE ................................. 4
Precautions for Procedures without Cowl Top Cover ..... 4
General Precautions ................................................ 4
Precautions for Three Way Catalyst ......................... 6
Precautions for Fuel (Unleaded Premium Gasoline
Recommended) ...................................................
..... 6
Precautions for Fuel (Unleaded Premium Gasoline
Required) ................................................................. 6
Precautions for Multiport Fuel Injection System or
Engine Control System ............................................ 7
Precautions for Hoses .............................................. 7
HOSE REMOVAL AND INSTALLATION ............... 7
HOSE CLAMPING ................................................ 7
Precautions for Engine Oils ...................................... 8
HEALTH PROTECTION PRECAUTIONS ............. 8
Precautions for Air Conditioning ............................... 8
HOW TO USE THIS MANUAL ................................... 9
Description ............................................................... 9
Terms ....................................................................... 9
Units ......................................................................... 9
Contents ................................................................... 9
Relation between Illustrations and Descriptions .... 10
Components ............................................................ 11
SYMBOLS ........................................................
.... 11
How to Follow Trouble Diagnoses .......................... 12
DESCRIPTION .................................................... 12
HOW TO FOLLOW TEST GROUPS IN TROU-
BLE DIAGNOSES ............................................... 12
HARNESS WIRE COLOR AND CONNECTOR
NUMBER INDICATION ....................................... 13KEY TO SYMBOLS SIGNIFYING MEASURE-
MENTS OR PROCEDURES ............................... 14
How to Read Wiring Diagrams ............................... 16
CONNECTOR SYMBOLS ................................... 16
SAMPLE/WIRING DIAGRAM - EXAMPL - .......... 17
DESCRIPTION .................................................... 18
Abbreviations .......................................................... 24
SERVICE INFORMATION FOR ELECTRICAL INCI-
DENT ......................................................................... 25
How to Check Terminal ........................................... 25
CONNECTOR AND TERMINAL PIN KIT ............ 25
HOW TO PROBE CONNECTORS ...................... 25
How to Perform Efficient Diagnosis for an Electrical
Incident ................................................................... 28
WORK FLOW ...................................................... 28
INCIDENT SIMULATION TESTS ........................ 28
CIRCUIT INSPECTION ....................................
... 31
Control Units and Electrical Parts ........................... 36
PRECAUTIONS .................................................. 36
CONSULT-II CHECKING SYSTEM .......................... 38
Description .............................................................. 38
Function and System Application ........................... 38
Nickel Metal Hydride Battery Replacement ............ 39
Checking Equipment .............................................. 39
CONSULT-II Start Procedure .................................. 39
CONSULT-II Data Link Connector (DLC) Circuit .... 40
INSPECTION PROCEDURE .............................. 40
CIRCUIT DIAGRAM ............................................ 41
LIFTING POINT ......................................................... 42
Special Service Tools ............................................. 42
Garage Jack and Safety Stand and 2-Pole Lift ....... 42
Board-On Lift .......................................................... 43
TOW TRUCK TOWING ............................................. 44
Tow Truck Towing ................................................... 44
2WD MODELS .................................................... 44
AWD MODELS .................................................... 45
Vehicle Recovery (Freeing a Stuck Vehicle) ........... 45
FRONT ................................................................ 45
REAR .................................................................. 45
AUTOMATIC TRANSMISSION ........................... 46