Page 113 of 3039
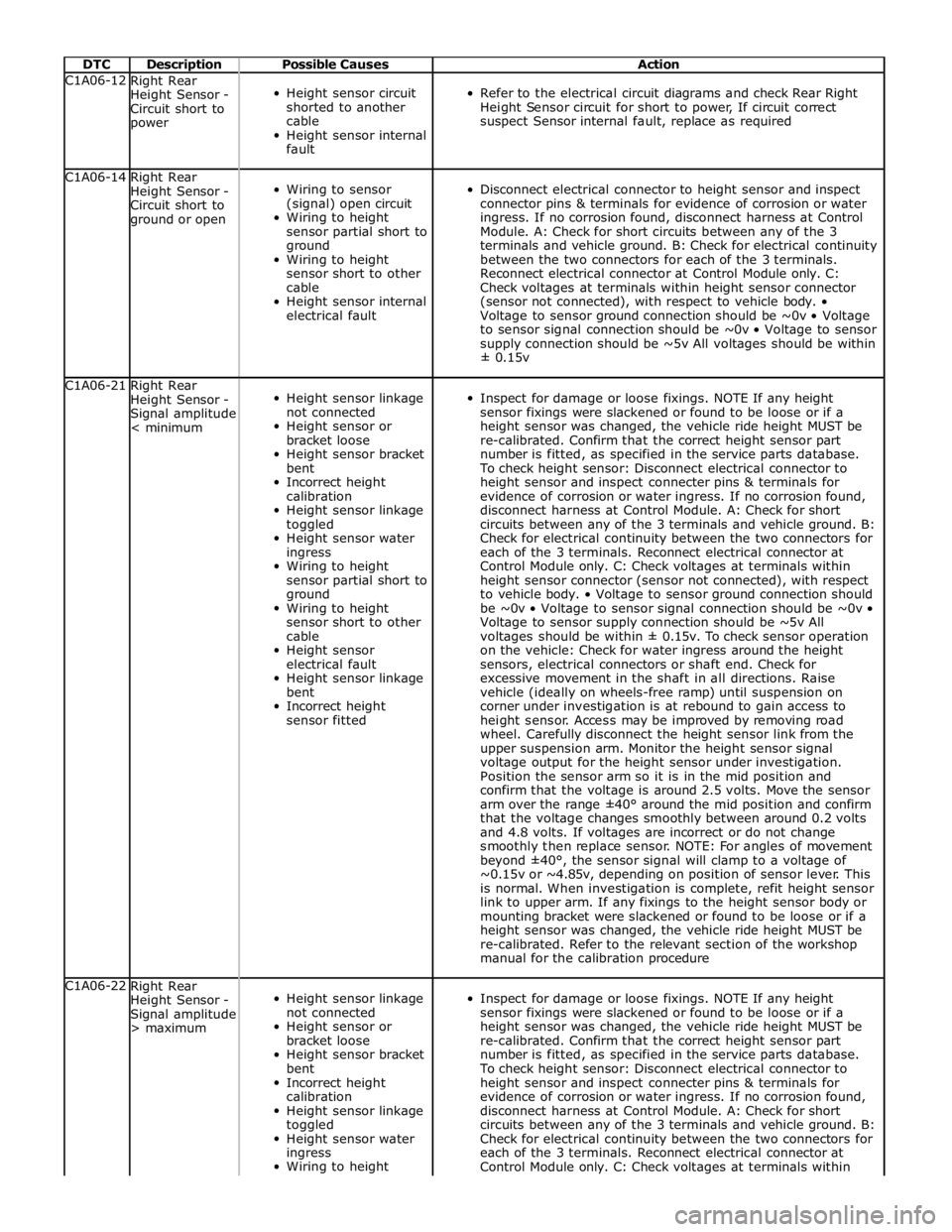
DTC Description Possible Causes Action C1A06-12
Right Rear
Height Sensor -
Circuit short to
power
Height sensor circuit
shorted to another
cable
Height sensor internal
fault
Refer to the electrical circuit diagrams and check Rear Right
Height Sensor circuit for short to power, If circuit correct
suspect Sensor internal fault, replace as required C1A06-14
Right Rear
Height Sensor -
Circuit short to
ground or open
Wiring to sensor
(signal) open circuit
Wiring to height
sensor partial short to
ground
Wiring to height
sensor short to other
cable
Height sensor internal
electrical fault
Disconnect electrical connector to height sensor and inspect
connector pins & terminals for evidence of corrosion or water
ingress. If no corrosion found, disconnect harness at Control
Module. A: Check for short circuits between any of the 3
terminals and vehicle ground. B: Check for electrical continuity
between the two connectors for each of the 3 terminals.
Reconnect electrical connector at Control Module only. C:
Check voltages at terminals within height sensor connector
(sensor not connected), with respect to vehicle body. •
Voltage to sensor ground connection should be ~0v • Voltage
to sensor signal connection should be ~0v • Voltage to sensor
supply connection should be ~5v All voltages should be within
± 0.15v C1A06-21
Right Rear
Height Sensor -
Signal amplitude
< minimum
Height sensor linkage
not connected
Height sensor or
bracket loose
Height sensor bracket
bent
Incorrect height
calibration
Height sensor linkage
toggled
Height sensor water
ingress
Wiring to height
sensor partial short to
ground
Wiring to height
sensor short to other
cable
Height sensor
electrical fault
Height sensor linkage
bent
Incorrect height
sensor fitted
Inspect for damage or loose fixings. NOTE If any height
sensor fixings were slackened or found to be loose or if a
height sensor was changed, the vehicle ride height MUST be
re-calibrated. Confirm that the correct height sensor part
number is fitted, as specified in the service parts database.
To check height sensor: Disconnect electrical connector to
height sensor and inspect connecter pins & terminals for
evidence of corrosion or water ingress. If no corrosion found,
disconnect harness at Control Module. A: Check for short
circuits between any of the 3 terminals and vehicle ground. B:
Check for electrical continuity between the two connectors for
each of the 3 terminals. Reconnect electrical connector at
Control Module only. C: Check voltages at terminals within
height sensor connector (sensor not connected), with respect
to vehicle body. • Voltage to sensor ground connection should
be ~0v • Voltage to sensor signal connection should be ~0v •
Voltage to sensor supply connection should be ~5v All
voltages should be within ± 0.15v. To check sensor operation
on the vehicle: Check for water ingress around the height
sensors, electrical connectors or shaft end. Check for
excessive movement in the shaft in all directions. Raise
vehicle (ideally on wheels-free ramp) until suspension on
corner under investigation is at rebound to gain access to
height sensor. Access may be improved by removing road
wheel. Carefully disconnect the height sensor link from the
upper suspension arm. Monitor the height sensor signal
voltage output for the height sensor under investigation.
Position the sensor arm so it is in the mid position and
confirm that the voltage is around 2.5 volts. Move the sensor
arm over the range ±40° around the mid position and confirm
that the voltage changes smoothly between around 0.2 volts
and 4.8 volts. If voltages are incorrect or do not change
smoothly then replace sensor. NOTE: For angles of movement
beyond ±40°, the sensor signal will clamp to a voltage of
~0.15v or ~4.85v, depending on position of sensor lever. This
is normal. When investigation is complete, refit height sensor
link to upper arm. If any fixings to the height sensor body or
mounting bracket were slackened or found to be loose or if a
height sensor was changed, the vehicle ride height MUST be
re-calibrated. Refer to the relevant section of the workshop
manual for the calibration procedure C1A06-22
Right Rear
Height Sensor -
Signal amplitude
> maximum
Height sensor linkage
not connected
Height sensor or
bracket loose
Height sensor bracket
bent
Incorrect height
calibration
Height sensor linkage
toggled
Height sensor water
ingress
Wiring to height
Inspect for damage or loose fixings. NOTE If any height
sensor fixings were slackened or found to be loose or if a
height sensor was changed, the vehicle ride height MUST be
re-calibrated. Confirm that the correct height sensor part
number is fitted, as specified in the service parts database.
To check height sensor: Disconnect electrical connector to
height sensor and inspect connecter pins & terminals for
evidence of corrosion or water ingress. If no corrosion found,
disconnect harness at Control Module. A: Check for short
circuits between any of the 3 terminals and vehicle ground. B:
Check for electrical continuity between the two connectors for
each of the 3 terminals. Reconnect electrical connector at
Control Module only. C: Check voltages at terminals within
Page 114 of 3039
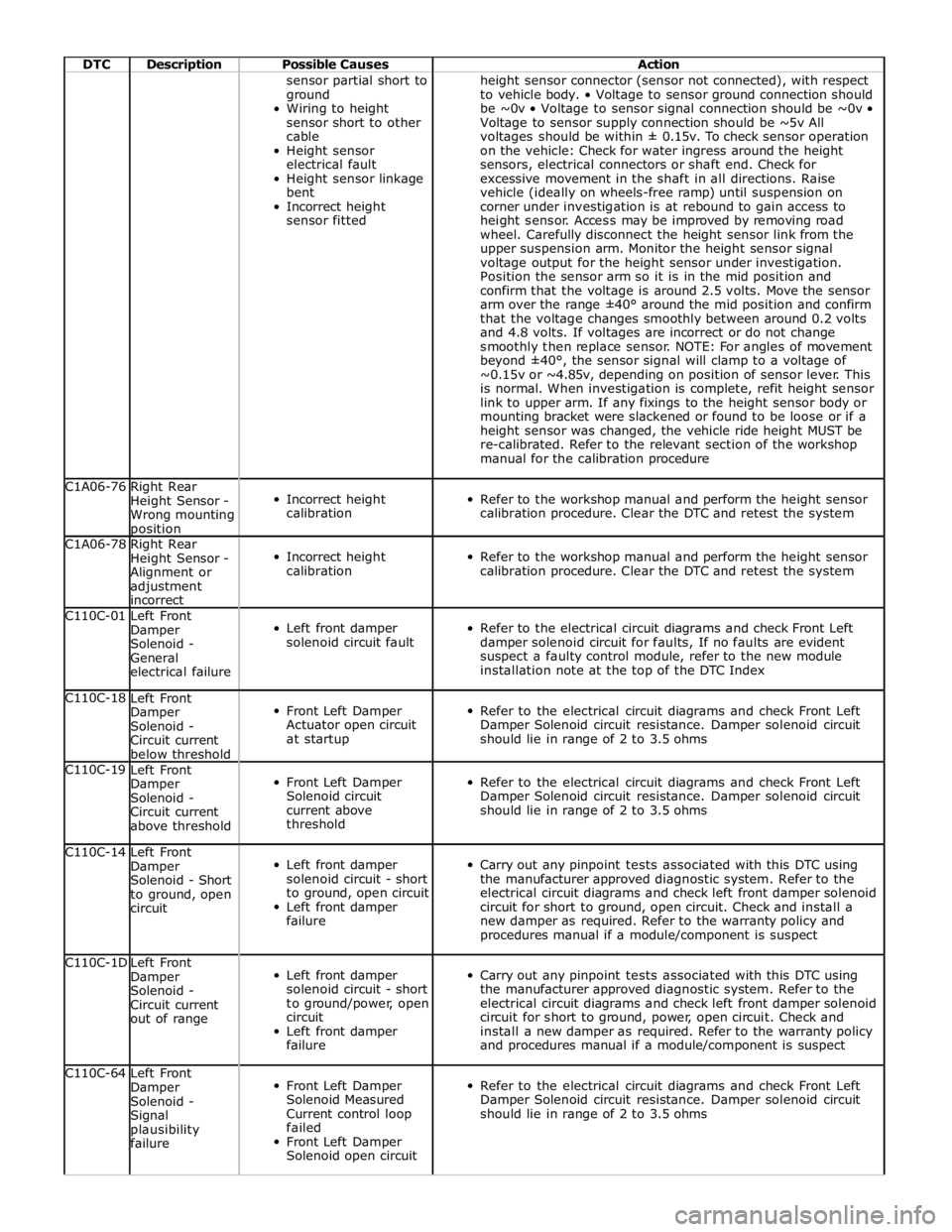
DTC Description Possible Causes Action sensor partial short to
ground
Wiring to height
sensor short to other
cable
Height sensor
electrical fault
Height sensor linkage
bent
Incorrect height
sensor fitted height sensor connector (sensor not connected), with respect
to vehicle body. • Voltage to sensor ground connection should
be ~0v • Voltage to sensor signal connection should be ~0v •
Voltage to sensor supply connection should be ~5v All
voltages should be within ± 0.15v. To check sensor operation
on the vehicle: Check for water ingress around the height
sensors, electrical connectors or shaft end. Check for
excessive movement in the shaft in all directions. Raise
vehicle (ideally on wheels-free ramp) until suspension on
corner under investigation is at rebound to gain access to
height sensor. Access may be improved by removing road
wheel. Carefully disconnect the height sensor link from the
upper suspension arm. Monitor the height sensor signal
voltage output for the height sensor under investigation.
Position the sensor arm so it is in the mid position and
confirm that the voltage is around 2.5 volts. Move the sensor
arm over the range ±40° around the mid position and confirm
that the voltage changes smoothly between around 0.2 volts
and 4.8 volts. If voltages are incorrect or do not change
smoothly then replace sensor. NOTE: For angles of movement
beyond ±40°, the sensor signal will clamp to a voltage of
~0.15v or ~4.85v, depending on position of sensor lever. This
is normal. When investigation is complete, refit height sensor
link to upper arm. If any fixings to the height sensor body or
mounting bracket were slackened or found to be loose or if a
height sensor was changed, the vehicle ride height MUST be
re-calibrated. Refer to the relevant section of the workshop
manual for the calibration procedure C1A06-76
Right Rear
Height Sensor -
Wrong mounting position
Incorrect height
calibration
Refer to the workshop manual and perform the height sensor
calibration procedure. Clear the DTC and retest the system C1A06-78
Right Rear
Height Sensor -
Alignment or
adjustment
incorrect
Incorrect height
calibration
Refer to the workshop manual and perform the height sensor
calibration procedure. Clear the DTC and retest the system C110C-01
Left Front
Damper
Solenoid -
General
electrical failure
Left front damper
solenoid circuit fault
Refer to the electrical circuit diagrams and check Front Left
damper solenoid circuit for faults, If no faults are evident
suspect a faulty control module, refer to the new module
installation note at the top of the DTC Index C110C-18
Left Front
Damper
Solenoid -
Circuit current
below threshold
Front Left Damper
Actuator open circuit
at startup
Refer to the electrical circuit diagrams and check Front Left
Damper Solenoid circuit resistance. Damper solenoid circuit
should lie in range of 2 to 3.5 ohms C110C-19
Left Front
Damper
Solenoid -
Circuit current
above threshold
Front Left Damper
Solenoid circuit
current above
threshold
Refer to the electrical circuit diagrams and check Front Left
Damper Solenoid circuit resistance. Damper solenoid circuit
should lie in range of 2 to 3.5 ohms C110C-14
Left Front
Damper
Solenoid - Short
to ground, open
circuit
Left front damper
solenoid circuit - short
to ground, open circuit
Left front damper
failure
Carry out any pinpoint tests associated with this DTC using
the manufacturer approved diagnostic system. Refer to the
electrical circuit diagrams and check left front damper solenoid
circuit for short to ground, open circuit. Check and install a
new damper as required. Refer to the warranty policy and
procedures manual if a module/component is suspect C110C-1D
Left Front
Damper
Solenoid -
Circuit current
out of range
Left front damper
solenoid circuit - short
to ground/power, open
circuit
Left front damper
failure
Carry out any pinpoint tests associated with this DTC using
the manufacturer approved diagnostic system. Refer to the
electrical circuit diagrams and check left front damper solenoid
circuit for short to ground, power, open circuit. Check and
install a new damper as required. Refer to the warranty policy
and procedures manual if a module/component is suspect C110C-64
Left Front
Damper
Solenoid -
Signal
plausibility
failure
Front Left Damper
Solenoid Measured
Current control loop
failed
Front Left Damper
Solenoid open circuit
Refer to the electrical circuit diagrams and check Front Left
Damper Solenoid circuit resistance. Damper solenoid circuit
should lie in range of 2 to 3.5 ohms
Page 115 of 3039
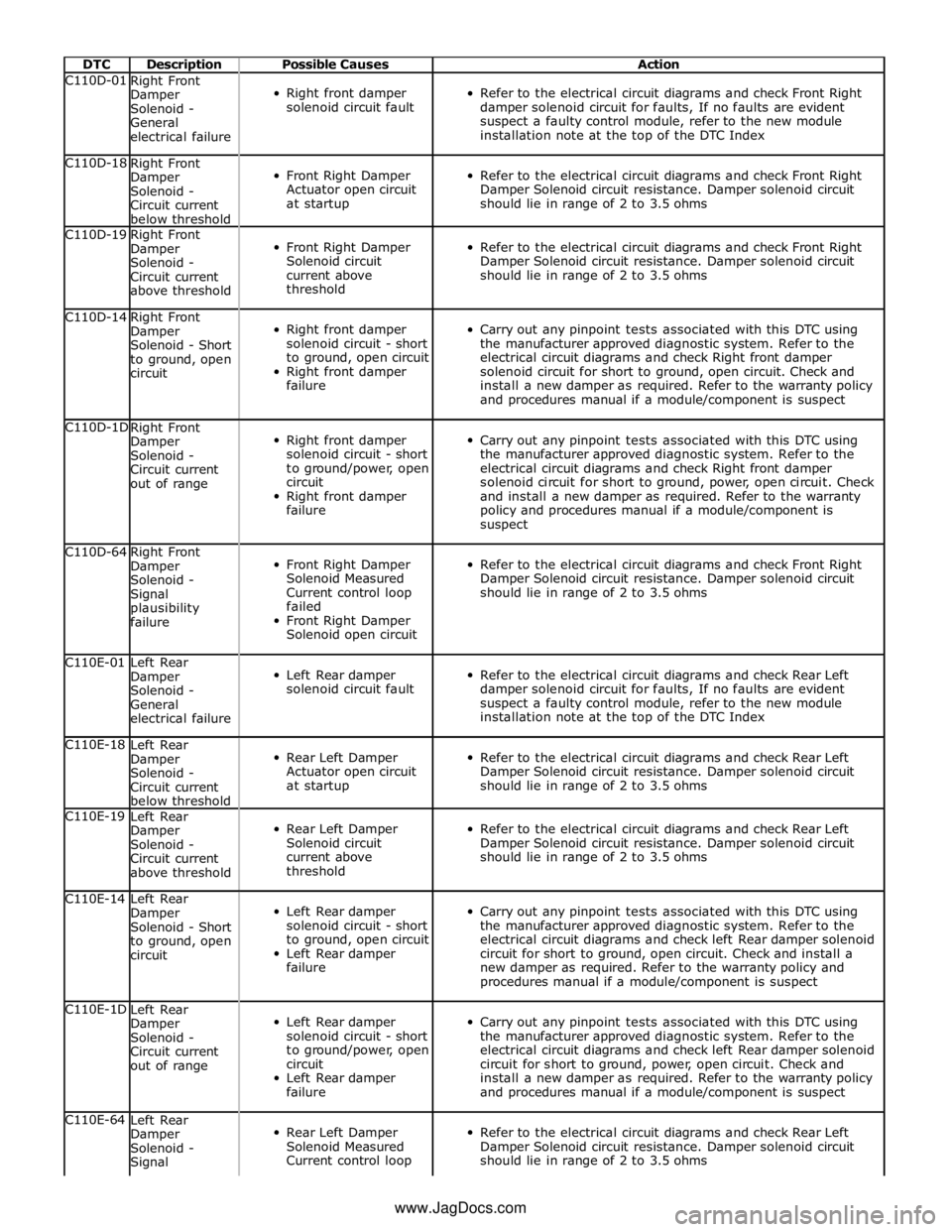
DTC Description Possible Causes Action C110D-01
Right Front
Damper
Solenoid -
General
electrical failure
Right front damper
solenoid circuit fault
Refer to the electrical circuit diagrams and check Front Right
damper solenoid circuit for faults, If no faults are evident
suspect a faulty control module, refer to the new module
installation note at the top of the DTC Index C110D-18
Right Front
Damper
Solenoid -
Circuit current
below threshold
Front Right Damper
Actuator open circuit
at startup
Refer to the electrical circuit diagrams and check Front Right
Damper Solenoid circuit resistance. Damper solenoid circuit
should lie in range of 2 to 3.5 ohms C110D-19
Right Front
Damper
Solenoid -
Circuit current
above threshold
Front Right Damper
Solenoid circuit
current above
threshold
Refer to the electrical circuit diagrams and check Front Right
Damper Solenoid circuit resistance. Damper solenoid circuit
should lie in range of 2 to 3.5 ohms C110D-14
Right Front
Damper
Solenoid - Short
to ground, open
circuit
Right front damper
solenoid circuit - short
to ground, open circuit
Right front damper
failure
Carry out any pinpoint tests associated with this DTC using
the manufacturer approved diagnostic system. Refer to the
electrical circuit diagrams and check Right front damper
solenoid circuit for short to ground, open circuit. Check and
install a new damper as required. Refer to the warranty policy
and procedures manual if a module/component is suspect C110D-1D
Right Front
Damper
Solenoid -
Circuit current
out of range
Right front damper
solenoid circuit - short
to ground/power, open
circuit
Right front damper
failure
Carry out any pinpoint tests associated with this DTC using
the manufacturer approved diagnostic system. Refer to the
electrical circuit diagrams and check Right front damper
solenoid circuit for short to ground, power, open circuit. Check
and install a new damper as required. Refer to the warranty
policy and procedures manual if a module/component is
suspect C110D-64
Right Front
Damper
Solenoid -
Signal
plausibility
failure
Front Right Damper
Solenoid Measured
Current control loop
failed
Front Right Damper
Solenoid open circuit
Refer to the electrical circuit diagrams and check Front Right
Damper Solenoid circuit resistance. Damper solenoid circuit
should lie in range of 2 to 3.5 ohms C110E-01
Left Rear
Damper
Solenoid -
General
electrical failure
Left Rear damper
solenoid circuit fault
Refer to the electrical circuit diagrams and check Rear Left
damper solenoid circuit for faults, If no faults are evident
suspect a faulty control module, refer to the new module
installation note at the top of the DTC Index C110E-18
Left Rear
Damper
Solenoid -
Circuit current
below threshold
Rear Left Damper
Actuator open circuit
at startup
Refer to the electrical circuit diagrams and check Rear Left
Damper Solenoid circuit resistance. Damper solenoid circuit
should lie in range of 2 to 3.5 ohms C110E-19
Left Rear
Damper
Solenoid -
Circuit current
above threshold
Rear Left Damper
Solenoid circuit
current above
threshold
Refer to the electrical circuit diagrams and check Rear Left
Damper Solenoid circuit resistance. Damper solenoid circuit
should lie in range of 2 to 3.5 ohms C110E-14
Left Rear
Damper
Solenoid - Short
to ground, open
circuit
Left Rear damper
solenoid circuit - short
to ground, open circuit
Left Rear damper
failure
Carry out any pinpoint tests associated with this DTC using
the manufacturer approved diagnostic system. Refer to the
electrical circuit diagrams and check left Rear damper solenoid
circuit for short to ground, open circuit. Check and install a
new damper as required. Refer to the warranty policy and
procedures manual if a module/component is suspect C110E-1D
Left Rear
Damper
Solenoid -
Circuit current
out of range
Left Rear damper
solenoid circuit - short
to ground/power, open
circuit
Left Rear damper
failure
Carry out any pinpoint tests associated with this DTC using
the manufacturer approved diagnostic system. Refer to the
electrical circuit diagrams and check left Rear damper solenoid
circuit for short to ground, power, open circuit. Check and
install a new damper as required. Refer to the warranty policy
and procedures manual if a module/component is suspect C110E-64
Left Rear
Damper
Solenoid -
Signal
Rear Left Damper
Solenoid Measured
Current control loop
Refer to the electrical circuit diagrams and check Rear Left
Damper Solenoid circuit resistance. Damper solenoid circuit
should lie in range of 2 to 3.5 ohms www.JagDocs.com
Page 116 of 3039
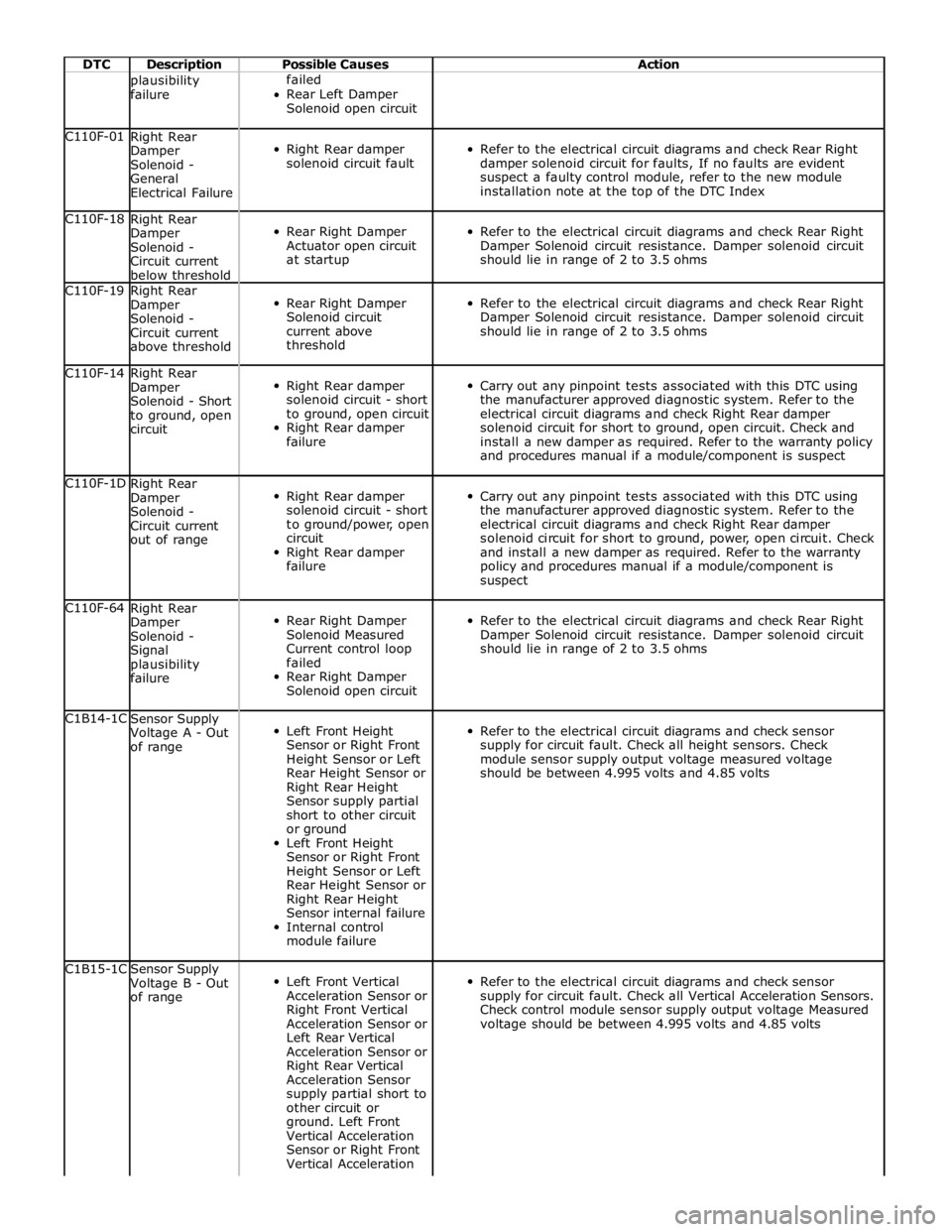
DTC Description Possible Causes Action plausibility
failure failed
Rear Left Damper
Solenoid open circuit C110F-01
Right Rear
Damper
Solenoid -
General
Electrical Failure
Right Rear damper
solenoid circuit fault
Refer to the electrical circuit diagrams and check Rear Right
damper solenoid circuit for faults, If no faults are evident
suspect a faulty control module, refer to the new module
installation note at the top of the DTC Index C110F-18
Right Rear
Damper
Solenoid -
Circuit current
below threshold
Rear Right Damper
Actuator open circuit
at startup
Refer to the electrical circuit diagrams and check Rear Right
Damper Solenoid circuit resistance. Damper solenoid circuit
should lie in range of 2 to 3.5 ohms C110F-19
Right Rear
Damper
Solenoid -
Circuit current
above threshold
Rear Right Damper
Solenoid circuit
current above
threshold
Refer to the electrical circuit diagrams and check Rear Right
Damper Solenoid circuit resistance. Damper solenoid circuit
should lie in range of 2 to 3.5 ohms C110F-14
Right Rear
Damper
Solenoid - Short
to ground, open
circuit
Right Rear damper
solenoid circuit - short
to ground, open circuit
Right Rear damper
failure
Carry out any pinpoint tests associated with this DTC using
the manufacturer approved diagnostic system. Refer to the
electrical circuit diagrams and check Right Rear damper
solenoid circuit for short to ground, open circuit. Check and
install a new damper as required. Refer to the warranty policy
and procedures manual if a module/component is suspect C110F-1D
Right Rear
Damper
Solenoid -
Circuit current
out of range
Right Rear damper
solenoid circuit - short
to ground/power, open
circuit
Right Rear damper
failure
Carry out any pinpoint tests associated with this DTC using
the manufacturer approved diagnostic system. Refer to the
electrical circuit diagrams and check Right Rear damper
solenoid circuit for short to ground, power, open circuit. Check
and install a new damper as required. Refer to the warranty
policy and procedures manual if a module/component is
suspect C110F-64
Right Rear
Damper
Solenoid -
Signal
plausibility
failure
Rear Right Damper
Solenoid Measured
Current control loop
failed
Rear Right Damper
Solenoid open circuit
Refer to the electrical circuit diagrams and check Rear Right
Damper Solenoid circuit resistance. Damper solenoid circuit
should lie in range of 2 to 3.5 ohms C1B14-1C
Sensor Supply
Voltage A - Out
of range
Left Front Height
Sensor or Right Front
Height Sensor or Left
Rear Height Sensor or
Right Rear Height
Sensor supply partial
short to other circuit
or ground
Left Front Height
Sensor or Right Front
Height Sensor or Left
Rear Height Sensor or
Right Rear Height
Sensor internal failure
Internal control
module failure
Refer to the electrical circuit diagrams and check sensor
supply for circuit fault. Check all height sensors. Check
module sensor supply output voltage measured voltage
should be between 4.995 volts and 4.85 volts C1B15-1C
Sensor Supply
Voltage B - Out
of range
Left Front Vertical
Acceleration Sensor or
Right Front Vertical
Acceleration Sensor or
Left Rear Vertical
Acceleration Sensor or
Right Rear Vertical
Acceleration Sensor
supply partial short to
other circuit or
ground. Left Front
Vertical Acceleration
Sensor or Right Front
Vertical Acceleration
Refer to the electrical circuit diagrams and check sensor
supply for circuit fault. Check all Vertical Acceleration Sensors.
Check control module sensor supply output voltage Measured
voltage should be between 4.995 volts and 4.85 volts
Page 117 of 3039
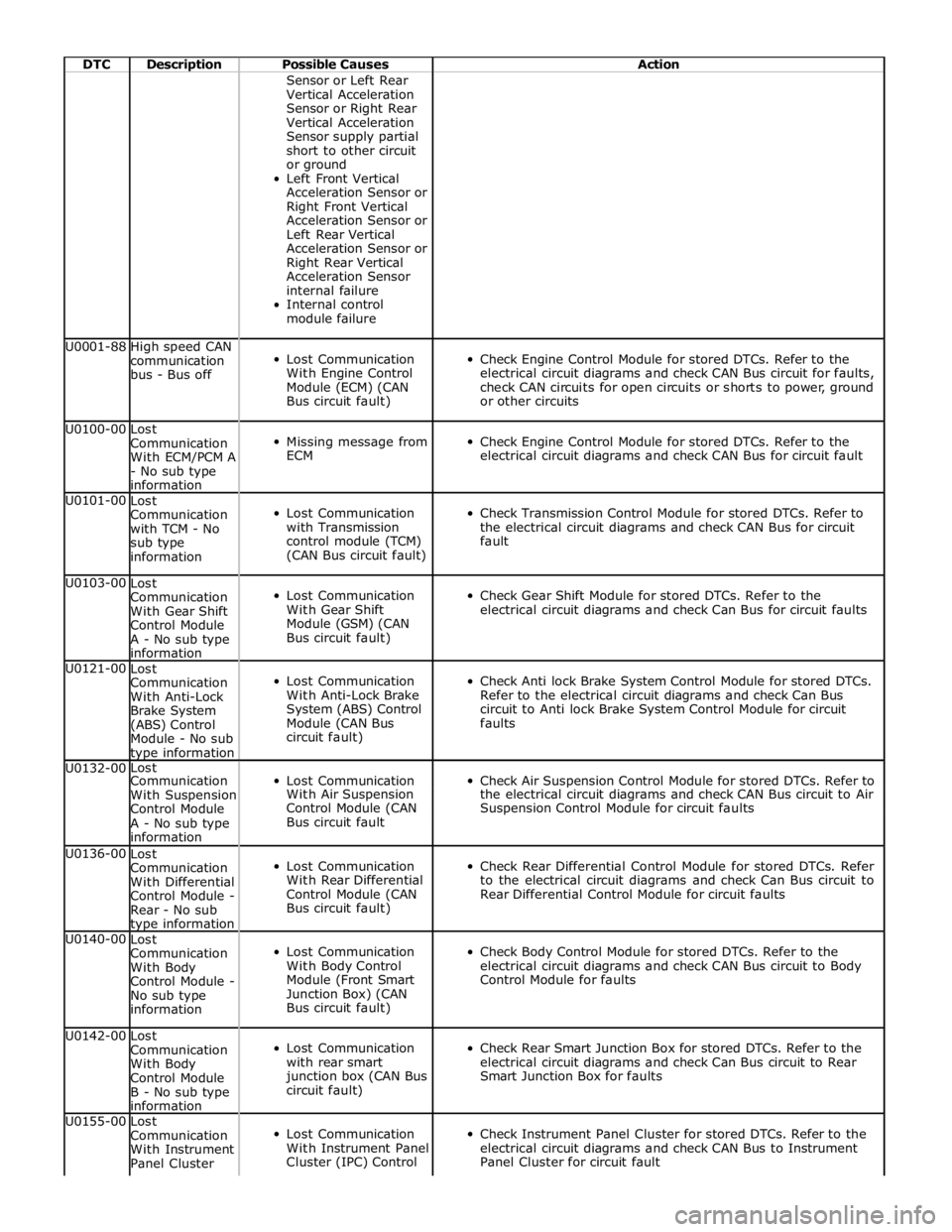
DTC Description Possible Causes Action Sensor or Left Rear
Vertical Acceleration
Sensor or Right Rear
Vertical Acceleration
Sensor supply partial
short to other circuit
or ground
Left Front Vertical
Acceleration Sensor or
Right Front Vertical
Acceleration Sensor or
Left Rear Vertical
Acceleration Sensor or
Right Rear Vertical
Acceleration Sensor
internal failure
Internal control
module failure U0001-88
High speed CAN
communication
bus - Bus off
Lost Communication
With Engine Control
Module (ECM) (CAN
Bus circuit fault)
Check Engine Control Module for stored DTCs. Refer to the
electrical circuit diagrams and check CAN Bus circuit for faults,
check CAN circuits for open circuits or shorts to power, ground
or other circuits U0100-00
Lost
Communication
With ECM/PCM A
- No sub type
information
Missing message from
ECM
Check Engine Control Module for stored DTCs. Refer to the
electrical circuit diagrams and check CAN Bus for circuit fault U0101-00
Lost
Communication
with TCM - No
sub type
information
Lost Communication
with Transmission
control module (TCM)
(CAN Bus circuit fault)
Check Transmission Control Module for stored DTCs. Refer to
the electrical circuit diagrams and check CAN Bus for circuit
fault U0103-00
Lost
Communication
With Gear Shift
Control Module
A - No sub type
information
Lost Communication
With Gear Shift
Module (GSM) (CAN
Bus circuit fault)
Check Gear Shift Module for stored DTCs. Refer to the
electrical circuit diagrams and check Can Bus for circuit faults U0121-00
Lost
Communication
With Anti-Lock
Brake System
(ABS) Control
Module - No sub type information
Lost Communication
With Anti-Lock Brake
System (ABS) Control
Module (CAN Bus
circuit fault)
Check Anti lock Brake System Control Module for stored DTCs.
Refer to the electrical circuit diagrams and check Can Bus
circuit to Anti lock Brake System Control Module for circuit
faults U0132-00 Lost
Lost Communication
Check Air Suspension Control Module for stored DTCs. Refer to Communication With Suspension With Air Suspension the electrical circuit diagrams and check CAN Bus circuit to Air Control Module Control Module (CAN Suspension Control Module for circuit faults A - No sub type Bus circuit fault information U0136-00
Lost
Communication
With Differential
Control Module -
Rear - No sub type information
Lost Communication
With Rear Differential
Control Module (CAN
Bus circuit fault)
Check Rear Differential Control Module for stored DTCs. Refer
to the electrical circuit diagrams and check Can Bus circuit to
Rear Differential Control Module for circuit faults U0140-00
Lost
Communication
With Body
Control Module -
No sub type
information
Lost Communication
With Body Control
Module (Front Smart
Junction Box) (CAN
Bus circuit fault)
Check Body Control Module for stored DTCs. Refer to the
electrical circuit diagrams and check CAN Bus circuit to Body
Control Module for faults U0142-00
Lost
Communication
With Body
Control Module
B - No sub type
information
Lost Communication
with rear smart
junction box (CAN Bus
circuit fault)
Check Rear Smart Junction Box for stored DTCs. Refer to the
electrical circuit diagrams and check Can Bus circuit to Rear
Smart Junction Box for faults U0155-00
Lost
Communication
With Instrument
Panel Cluster
Lost Communication
With Instrument Panel
Cluster (IPC) Control
Check Instrument Panel Cluster for stored DTCs. Refer to the
electrical circuit diagrams and check CAN Bus to Instrument
Panel Cluster for circuit fault
Page 118 of 3039

DTC Description Possible Causes Action (IPC) Control
Module - No sub
type information Module (CAN bus
circuit fault) U0300-00
Internal control
module software
incompatibility -
No sub type
information
CAN master
configuration ID
incorrect
Check Front Smart Junction Box vehicle configuration file,
check part number of adaptive damping control module U0401-68
Invalid Data
Received from
ECM/PCM A -
Event
information
Invalid Data Received
from Engine Control
Module
Check Engine Control Module for DTCs. Refer to the relevant
DTC index U0402-68
Invalid Data
Received from TCM - Event
information
Invalid Data Received
from Transmission
control module
Check for Transmission Control Module DTCs. Refer to relevant
DTC index U0404-68
Invalid Data
Received from
Gear Shift
Control Module
A - Event
information
Invalid data received
from gear shift control
module
Check Gear Shift Control Module for DTCs. Refer to the
relevant DTC index U0415-68
Invalid Data
Received From
Anti-Lock Brake
System (ABS)
Control Module -
Event
information
Invalid Data Received
From Anti-Lock Brake
System (ABS) Control
Module
Check for Anti lock Brake System DTCs. Refer to the relevant
DTC index U0421-68
Invalid Data
Received from
Suspension
Control Module
A - Event
information
Invalid Data Received
From Air Suspension
Control Module
Check Air Suspension Control Module for stored DTCs. Refer to
the relevant DTC index U0422-68
Invalid Data
Received From
Body Control
Module - Event
information
Invalid Data Received
From Body Control
Module (Front Smart
Junction Box)
Check Body Control Module (Front Smart Junction Box) for
stored DTCs. Refer to the relevant DTC index U0437-68
Invalid Data
Received From
Differential
Control Module -
Rear - Event
information
Invalid Data Received
From Rear Differential
Control Module
Check Rear Differential Control Module for stored DTCs. Refer
to the relevant DTC index U0443-68
Invalid Data
Received From
Body Control
Module B -
Event
information
Invalid Data Received
From body control
module B (Rear Smart
Junction Box)
Check rear smart junction box for DTCs and refer to relevant
DTC index U1A14-00 CAN
initialization
failure - No sub type information
CAN network harness
short, disconnected
Refer to circuit diagrams and check CAN Bus circuit for fault
(short to power, ground or open circuit) U2100-00
Initial
Configuration
Not Complete -
No sub type
information
Car Configuration
Data not loaded (New
Body Control Module
(Front Smart Junction
Box) fitted to vehicle
and not initialized)
Internal Body Control
Module (Front Smart
Junction Box) failure
Install car config to Front Smart Junction Box. Clear DTC and
retest systems U2101-00
Control Module
Configuration
Incompatible -
No sub type
information
Car Configuration
Data transmitted over
CAN does not match
adaptive damping
control module
internal config
Carry out the new module software installation procedure
Page 119 of 3039
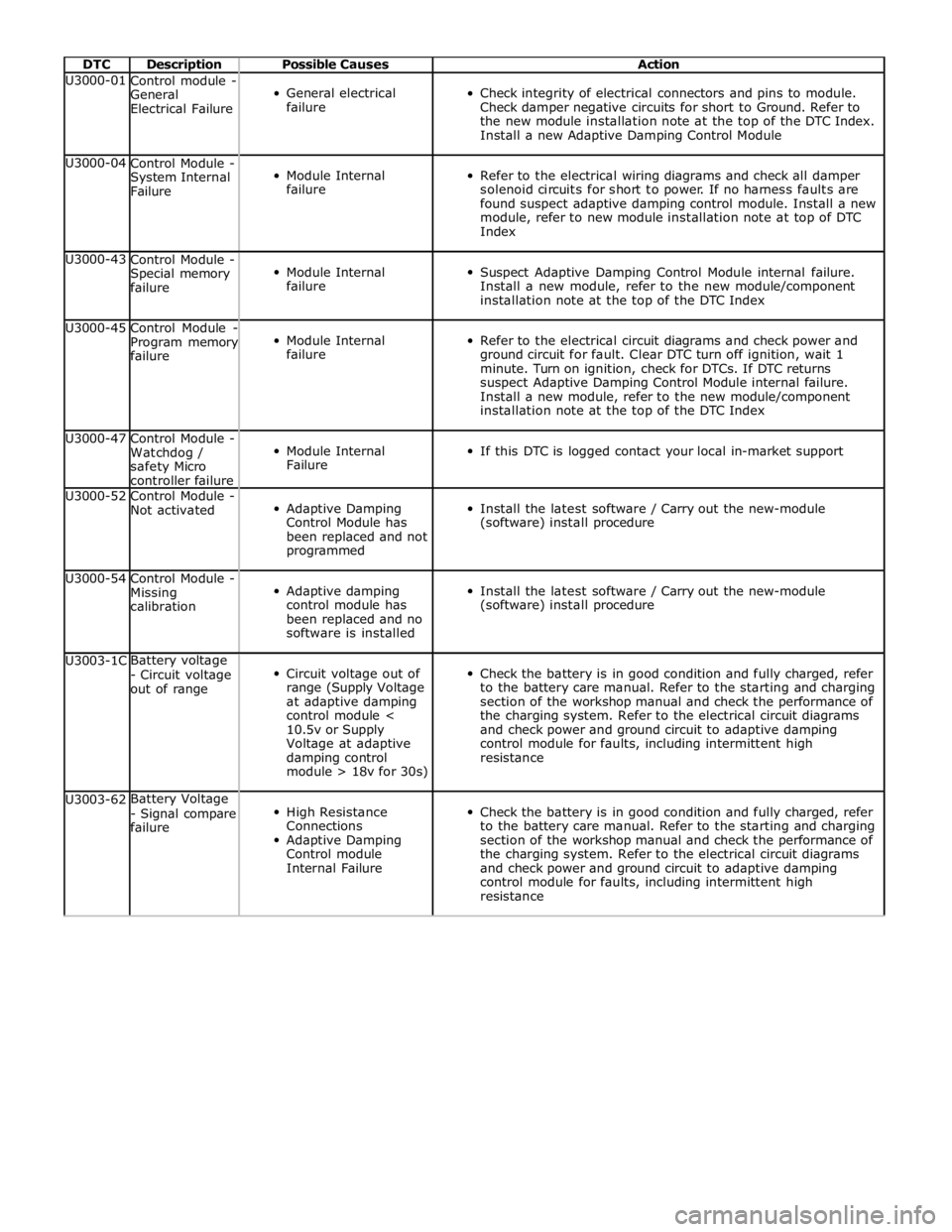
DTC Description Possible Causes Action U3000-01
Control module -
General
Electrical Failure
General electrical
failure
Check integrity of electrical connectors and pins to module.
Check damper negative circuits for short to Ground. Refer to
the new module installation note at the top of the DTC Index.
Install a new Adaptive Damping Control Module U3000-04
Control Module -
System Internal
Failure
Module Internal
failure
Refer to the electrical wiring diagrams and check all damper
solenoid circuits for short to power. If no harness faults are
found suspect adaptive damping control module. Install a new
module, refer to new module installation note at top of DTC
Index U3000-43
Control Module -
Special memory
failure
Module Internal
failure
Suspect Adaptive Damping Control Module internal failure.
Install a new module, refer to the new module/component
installation note at the top of the DTC Index U3000-45
Control Module -
Program memory
failure
Module Internal
failure
Refer to the electrical circuit diagrams and check power and
ground circuit for fault. Clear DTC turn off ignition, wait 1
minute. Turn on ignition, check for DTCs. If DTC returns
suspect Adaptive Damping Control Module internal failure.
Install a new module, refer to the new module/component
installation note at the top of the DTC Index U3000-47
Control Module -
Watchdog /
safety Micro
controller failure
Module Internal
Failure
If this DTC is logged contact your local in-market support U3000-52
Control Module -
Not activated
Adaptive Damping
Control Module has
been replaced and not
programmed
Install the latest software / Carry out the new-module
(software) install procedure U3000-54
Control Module -
Missing
calibration
Adaptive damping
control module has
been replaced and no
software is installed
Install the latest software / Carry out the new-module
(software) install procedure U3003-1C Battery voltage
- Circuit voltage
out of range
Circuit voltage out of
range (Supply Voltage
at adaptive damping
control module <
10.5v or Supply
Voltage at adaptive
damping control
module > 18v for 30s)
Check the battery is in good condition and fully charged, refer
to the battery care manual. Refer to the starting and charging
section of the workshop manual and check the performance of
the charging system. Refer to the electrical circuit diagrams
and check power and ground circuit to adaptive damping
control module for faults, including intermittent high
resistance U3003-62 Battery Voltage
- Signal compare
failure
High Resistance
Connections
Adaptive Damping
Control module
Internal Failure
Check the battery is in good condition and fully charged, refer
to the battery care manual. Refer to the starting and charging
section of the workshop manual and check the performance of
the charging system. Refer to the electrical circuit diagrams
and check power and ground circuit to adaptive damping
control module for faults, including intermittent high
resistance
Page 120 of 3039
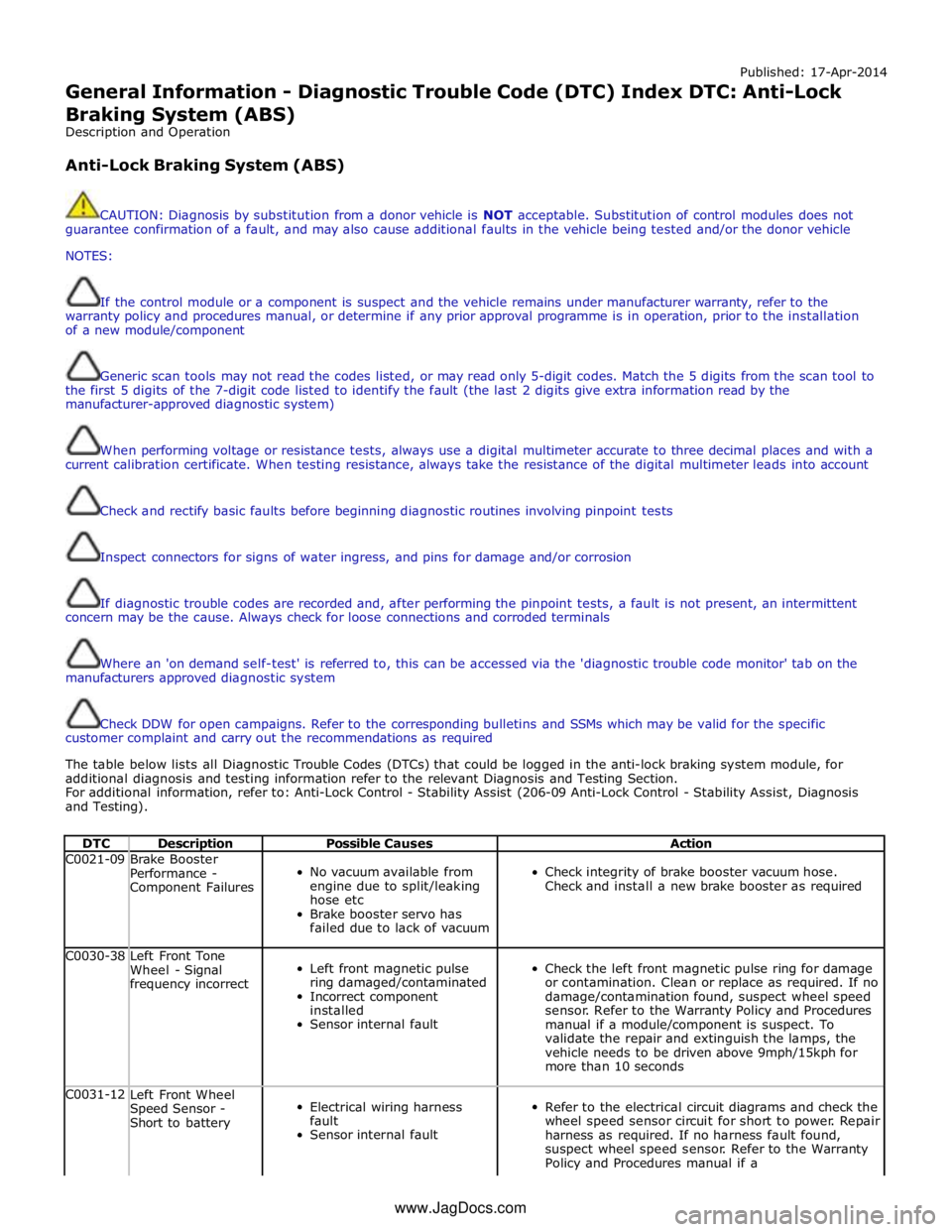
Published: 17-Apr-2014
General Information - Diagnostic Trouble Code (DTC) Index DTC: Anti-Lock Braking System (ABS)
Description and Operation
Anti-Lock Braking System (ABS)
CAUTION: Diagnosis by substitution from a donor vehicle is NOT acceptable. Substitution of control modules does not
guarantee confirmation of a fault, and may also cause additional faults in the vehicle being tested and/or the donor vehicle
NOTES:
If the control module or a component is suspect and the vehicle remains under manufacturer warranty, refer to the
warranty policy and procedures manual, or determine if any prior approval programme is in operation, prior to the installation
of a new module/component
Generic scan tools may not read the codes listed, or may read only 5-digit codes. Match the 5 digits from the scan tool to
the first 5 digits of the 7-digit code listed to identify the fault (the last 2 digits give extra information read by the
manufacturer-approved diagnostic system)
When performing voltage or resistance tests, always use a digital multimeter accurate to three decimal places and with a
current calibration certificate. When testing resistance, always take the resistance of the digital multimeter leads into account
Check and rectify basic faults before beginning diagnostic routines involving pinpoint tests
Inspect connectors for signs of water ingress, and pins for damage and/or corrosion
If diagnostic trouble codes are recorded and, after performing the pinpoint tests, a fault is not present, an intermittent
concern may be the cause. Always check for loose connections and corroded terminals
Where an 'on demand self-test' is referred to, this can be accessed via the 'diagnostic trouble code monitor' tab on the
manufacturers approved diagnostic system
Check DDW for open campaigns. Refer to the corresponding bulletins and SSMs which may be valid for the specific
customer complaint and carry out the recommendations as required
The table below lists all Diagnostic Trouble Codes (DTCs) that could be logged in the anti-lock braking system module, for
additional diagnosis and testing information refer to the relevant Diagnosis and Testing Section.
For additional information, refer to: Anti-Lock Control - Stability Assist (206-09 Anti-Lock Control - Stability Assist, Diagnosis
and Testing).
DTC Description Possible Causes Action C0021-09
Brake Booster
Performance -
Component Failures
No vacuum available from
engine due to split/leaking
hose etc
Brake booster servo has
failed due to lack of vacuum
Check integrity of brake booster vacuum hose.
Check and install a new brake booster as required C0030-38
Left Front Tone
Wheel - Signal
frequency incorrect
Left front magnetic pulse
ring damaged/contaminated
Incorrect component
installed
Sensor internal fault
Check the left front magnetic pulse ring for damage
or contamination. Clean or replace as required. If no
damage/contamination found, suspect wheel speed
sensor. Refer to the Warranty Policy and Procedures
manual if a module/component is suspect. To
validate the repair and extinguish the lamps, the
vehicle needs to be driven above 9mph/15kph for
more than 10 seconds C0031-12
Left Front Wheel
Speed Sensor -
Short to battery
Electrical wiring harness
fault
Sensor internal fault
Refer to the electrical circuit diagrams and check the
wheel speed sensor circuit for short to power. Repair
harness as required. If no harness fault found,
suspect wheel speed sensor. Refer to the Warranty
Policy and Procedures manual if a www.JagDocs.com