Page 329 of 3039
Front Suspension - Front Suspension - Component Location
Description and Operation
COMPONENT LOCATION Published: 11-May-2011
Item Description 1 Subframe 2 Spring and damper assembly 3 Upper control arm 4 Wheel knuckle 5 Wheel hub and bearing assembly 6 Lower lateral control arm 7 Lower forward control arm 8 Stabilizer bar 9 Stabilizer bar link www.JagDocs.com
Page 330 of 3039
Description and Operation).
Page 331 of 3039
1 Subframe 2 Spring and damper assembly 3 Upper control arm 4 Wheel knuckle 5 Stabilizer bar link 6 Wheel hub and bearing assembly 7 Lower lateral control arm 8 Lower forward control arm 9 Stabilizer bar
Page 332 of 3039
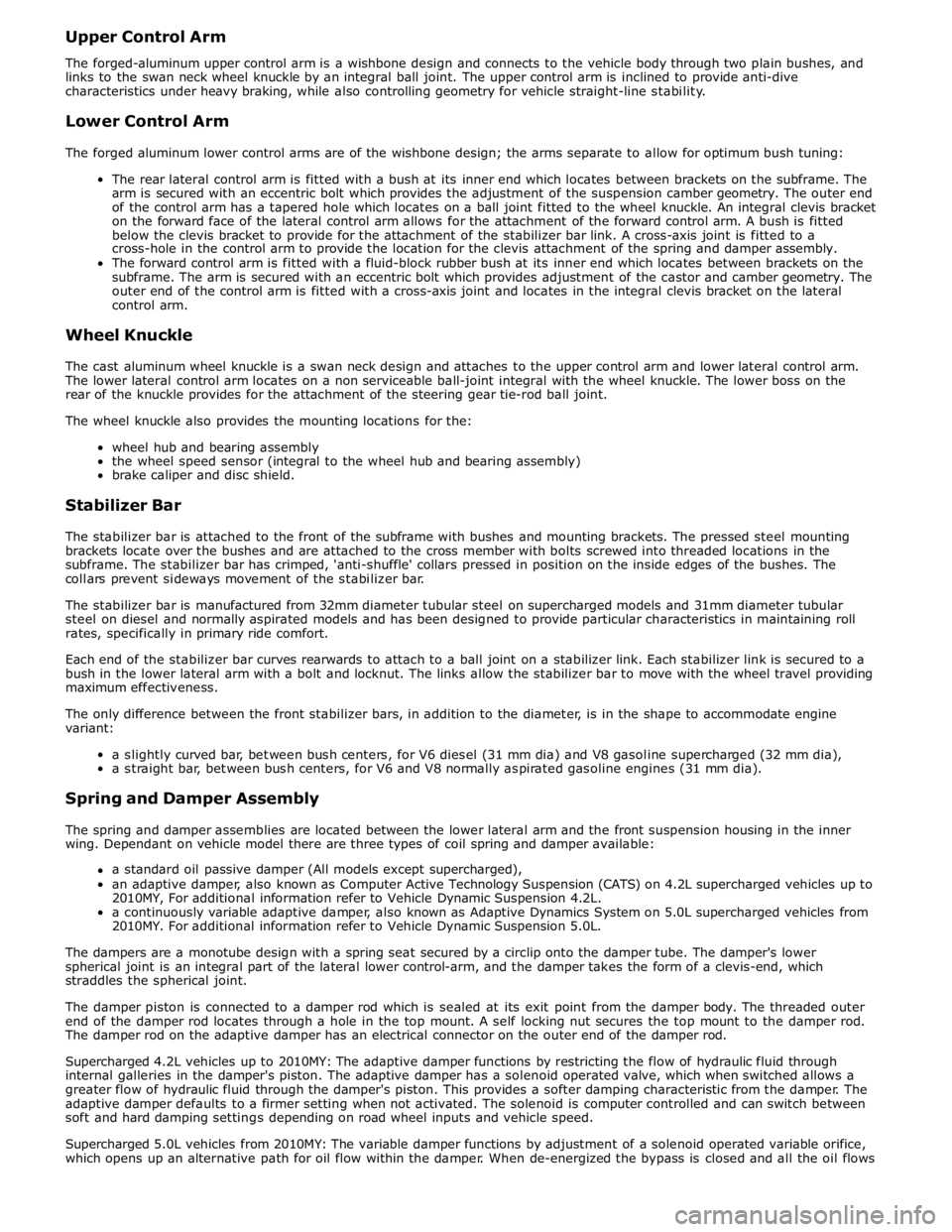
Upper Control Arm
The forged-aluminum upper control arm is a wishbone design and connects to the vehicle body through two plain bushes, and
links to the swan neck wheel knuckle by an integral ball joint. The upper control arm is inclined to provide anti-dive
characteristics under heavy braking, while also controlling geometry for vehicle straight-line stability.
Lower Control Arm
The forged aluminum lower control arms are of the wishbone design; the arms separate to allow for optimum bush tuning:
The rear lateral control arm is fitted with a bush at its inner end which locates between brackets on the subframe. The
arm is secured with an eccentric bolt which provides the adjustment of the suspension camber geometry. The outer end
of the control arm has a tapered hole which locates on a ball joint fitted to the wheel knuckle. An integral clevis bracket
on the forward face of the lateral control arm allows for the attachment of the forward control arm. A bush is fitted
below the clevis bracket to provide for the attachment of the stabilizer bar link. A cross-axis joint is fitted to a
cross-hole in the control arm to provide the location for the clevis attachment of the spring and damper assembly.
The forward control arm is fitted with a fluid-block rubber bush at its inner end which locates between brackets on the
subframe. The arm is secured with an eccentric bolt which provides adjustment of the castor and camber geometry. The
outer end of the control arm is fitted with a cross-axis joint and locates in the integral clevis bracket on the lateral
control arm.
Wheel Knuckle
The cast aluminum wheel knuckle is a swan neck design and attaches to the upper control arm and lower lateral control arm.
The lower lateral control arm locates on a non serviceable ball-joint integral with the wheel knuckle. The lower boss on the
rear of the knuckle provides for the attachment of the steering gear tie-rod ball joint.
The wheel knuckle also provides the mounting locations for the:
wheel hub and bearing assembly
the wheel speed sensor (integral to the wheel hub and bearing assembly)
brake caliper and disc shield.
Stabilizer Bar
The stabilizer bar is attached to the front of the subframe with bushes and mounting brackets. The pressed steel mounting
brackets locate over the bushes and are attached to the cross member with bolts screwed into threaded locations in the
subframe. The stabilizer bar has crimped, 'anti-shuffle' collars pressed in position on the inside edges of the bushes. The
collars prevent sideways movement of the stabilizer bar.
The stabilizer bar is manufactured from 32mm diameter tubular steel on supercharged models and 31mm diameter tubular
steel on diesel and normally aspirated models and has been designed to provide particular characteristics in maintaining roll
rates, specifically in primary ride comfort.
Each end of the stabilizer bar curves rearwards to attach to a ball joint on a stabilizer link. Each stabilizer link is secured to a
bush in the lower lateral arm with a bolt and locknut. The links allow the stabilizer bar to move with the wheel travel providing
maximum effectiveness.
The only difference between the front stabilizer bars, in addition to the diameter, is in the shape to accommodate engine
variant:
a slightly curved bar, between bush centers, for V6 diesel (31 mm dia) and V8 gasoline supercharged (32 mm dia),
a straight bar, between bush centers, for V6 and V8 normally aspirated gasoline engines (31 mm dia).
Spring and Damper Assembly
The spring and damper assemblies are located between the lower lateral arm and the front suspension housing in the inner
wing. Dependant on vehicle model there are three types of coil spring and damper available:
a standard oil passive damper (All models except supercharged),
an adaptive damper, also known as Computer Active Technology Suspension (CATS) on 4.2L supercharged vehicles up to
2010MY, For additional information refer to Vehicle Dynamic Suspension 4.2L.
a continuously variable adaptive damper, also known as Adaptive Dynamics System on 5.0L supercharged vehicles from
2010MY. For additional information refer to Vehicle Dynamic Suspension 5.0L.
The dampers are a monotube design with a spring seat secured by a circlip onto the damper tube. The damper's lower
spherical joint is an integral part of the lateral lower control-arm, and the damper takes the form of a clevis-end, which
straddles the spherical joint.
The damper piston is connected to a damper rod which is sealed at its exit point from the damper body. The threaded outer
end of the damper rod locates through a hole in the top mount. A self locking nut secures the top mount to the damper rod.
The damper rod on the adaptive damper has an electrical connector on the outer end of the damper rod.
Supercharged 4.2L vehicles up to 2010MY: The adaptive damper functions by restricting the flow of hydraulic fluid through
internal galleries in the damper's piston. The adaptive damper has a solenoid operated valve, which when switched allows a
greater flow of hydraulic fluid through the damper's piston. This provides a softer damping characteristic from the damper. The
adaptive damper defaults to a firmer setting when not activated. The solenoid is computer controlled and can switch between
soft and hard damping settings depending on road wheel inputs and vehicle speed.
Supercharged 5.0L vehicles from 2010MY: The variable damper functions by adjustment of a solenoid operated variable orifice,
which opens up an alternative path for oil flow within the damper. When de-energized the bypass is closed and all the oil flows
Page 333 of 3039
Page 334 of 3039
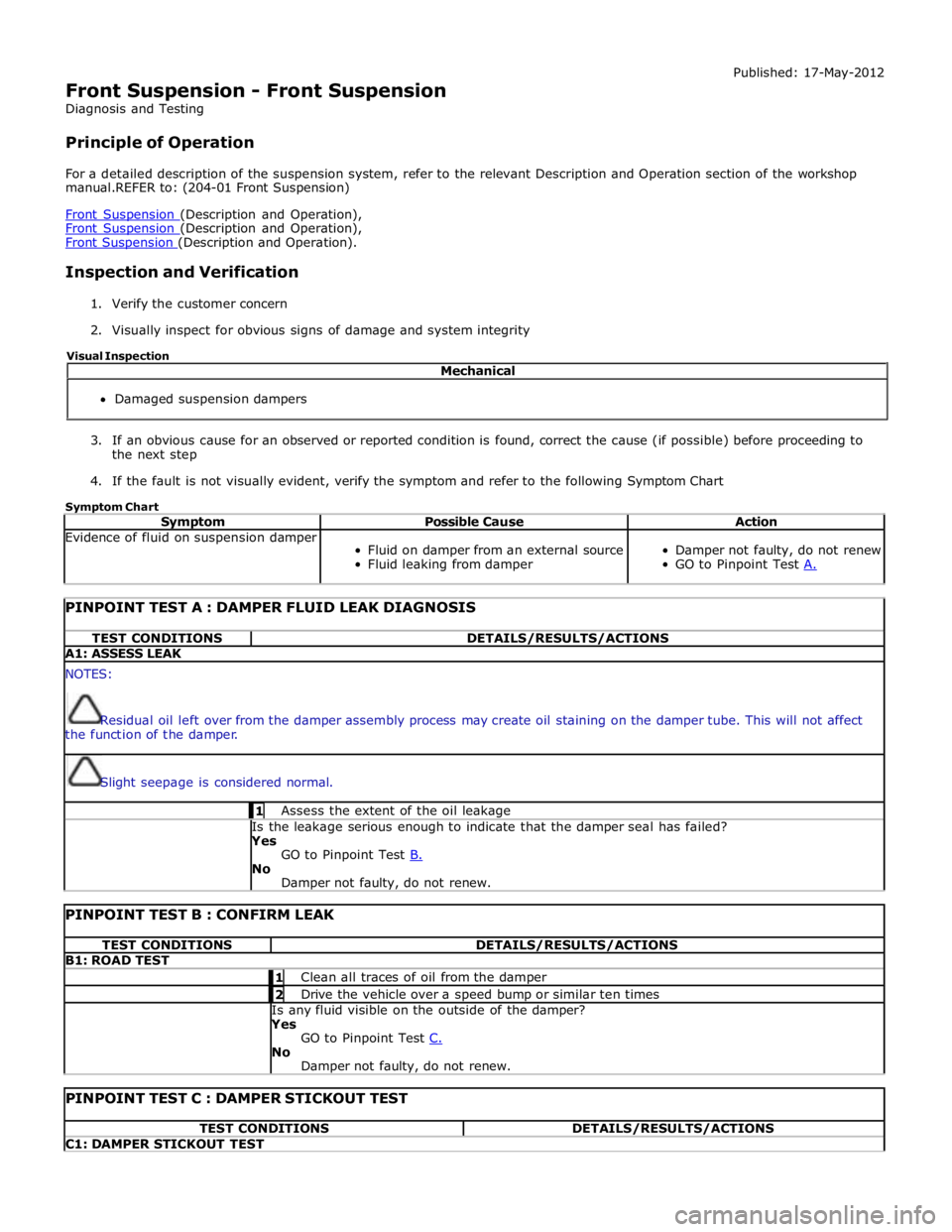
Front Suspension - Front Suspension
Diagnosis and Testing
Principle of Operation Published: 17-May-2012
For a detailed description of the suspension system, refer to the relevant Description and Operation section of the workshop
manual.REFER to: (204-01 Front Suspension)
Front Suspension (Description and Operation), Front Suspension (Description and Operation), Front Suspension (Description and Operation).
Inspection and Verification
1. Verify the customer concern
2. Visually inspect for obvious signs of damage and system integrity
3. If an obvious cause for an observed or reported condition is found, correct the cause (if possible) before proceeding to
the next step
4. If the fault is not visually evident, verify the symptom and refer to the following Symptom Chart
Symptom Chart
Symptom Possible Cause Action Evidence of fluid on suspension damper
Fluid on damper from an external source
Fluid leaking from damper
Damper not faulty, do not renew
GO to Pinpoint Test A.
PINPOINT TEST A : DAMPER FLUID LEAK DIAGNOSIS TEST CONDITIONS DETAILS/RESULTS/ACTIONS A1: ASSESS LEAK NOTES:
Residual oil left over from the damper assembly process may create oil staining on the damper tube. This will not affect
the function of the damper.
Slight seepage is considered normal. 1 Assess the extent of the oil leakage Is the leakage serious enough to indicate that the damper seal has failed? Yes
GO to Pinpoint Test B. No
Damper not faulty, do not renew.
PINPOINT TEST B : CONFIRM LEAK TEST CONDITIONS DETAILS/RESULTS/ACTIONS B1: ROAD TEST 1 Clean all traces of oil from the damper 2 Drive the vehicle over a speed bump or similar ten times Is any fluid visible on the outside of the damper? Yes
GO to Pinpoint Test C. No
Damper not faulty, do not renew.
PINPOINT TEST C : DAMPER STICKOUT TEST TEST CONDITIONS DETAILS/RESULTS/ACTIONS C1: DAMPER STICKOUT TEST Mechanical
Damaged suspension dampers Visual Inspection
Page 335 of 3039
NOTE: If a significant quantity of fluid has leaked out of the damper, the dividing piston will be displaced upwards in the
tube by the pressure of the gas below it. This will limit the downward travel of the piston. 1 Remove the suspension strut assembly REFER to: Front Shock Absorber (204-01 Front Suspension, Removal and Installation). 2 Remove the spring 3 Remove the bump stop 4 Push the damper piston fully into the damper tube
5 Measure and record the stickout dimension (the distance between the damper tube cap and the piston rod shoulder) Is the stickout dimension greater than 12.0mm?
Yes
Damper unserviceable. Install a new suspension damper.
Enclose a record of the stickout dimension with the returned
part.
No
Damper serviceable. Re-assemble and re-install the
suspension strut
REFER to: Front Shock Absorber (204-01 Front Suspension, Removal and Installation).
Page 336 of 3039
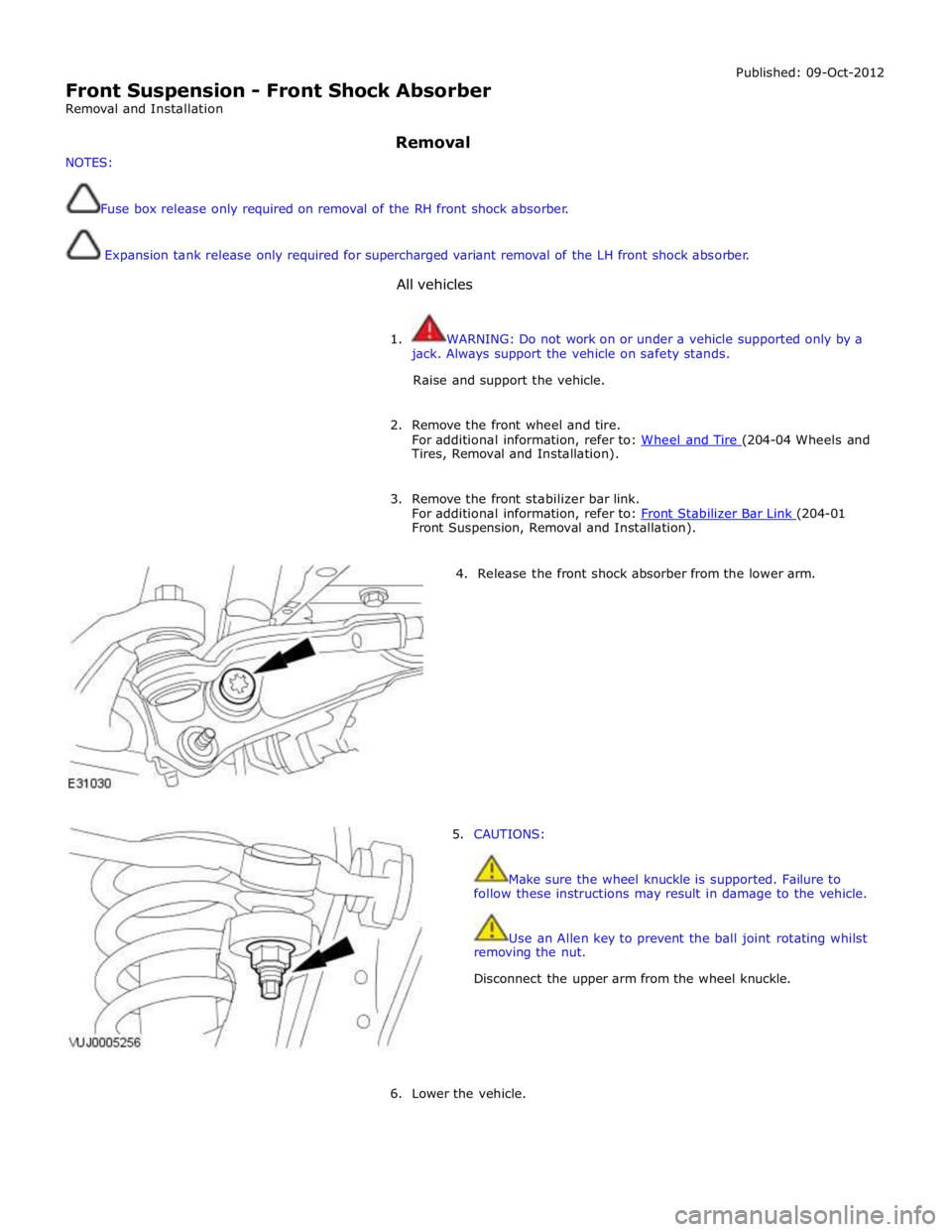
Front Suspension - Front Shock Absorber
Removal and Installation Published: 09-Oct-2012
NOTES: Removal
Fuse box release only required on removal of the RH front shock absorber.
Expansion tank release only required for supercharged variant removal of the LH front shock absorber.
All vehicles
1. WARNING: Do not work on or under a vehicle supported only by a
jack. Always support the vehicle on safety stands.
Raise and support the vehicle.
2. Remove the front wheel and tire.
For additional information, refer to: Wheel and Tire (204-04 Wheels and Tires, Removal and Installation).
3. Remove the front stabilizer bar link.
For additional information, refer to: Front Stabilizer Bar Link (204-01 Front Suspension, Removal and Installation).
4. Release the front shock absorber from the lower arm.
5. CAUTIONS:
Make sure the wheel knuckle is supported. Failure to
follow these instructions may result in damage to the vehicle.
Use an Allen key to prevent the ball joint rotating whilst
removing the nut.
Disconnect the upper arm from the wheel knuckle.
6. Lower the vehicle.