Page 2689 of 3039
Pedestrian Protection System - Pedestrian Impact Sensor
Removal and Installation
Removal
NOTE: Removal steps in this procedure may contain installation details. Published: 11-May-2011
1. Refer to: Front Bumper Cover (501-19 Bumpers, Removal and Installation).
Installation
2. Torque: 3 Nm
1. To install, reverse the removal procedure. www.JagDocs.com
Page 2690 of 3039
Published: 11-May-2011
Pedestrian Protection System - Pedestrian Protection Hood Actuator LH
Removal and Installation
Removal
NOTE: Removal steps in this procedure may contain installation details.
1. Disconnect the battery ground cable.
Refer to: Battery Disconnect and Connect (414-01 Battery, Mounting and Cables, General Procedures).
2. Remove the cowl vent screen.
Refer to: Cowl Vent Screen (501-02 Front End Body Panels, Removal and Installation).
Installation
3. Torque: 8 Nm
1. Install is the reverse of removal.
Page 2691 of 3039
Published: 11-May-2011
Pedestrian Protection System - Pedestrian Protection Hood Actuator RH
Removal and Installation
Removal
NOTE: Removal steps in this procedure may contain installation details.
1. Disconnect the battery ground cable.
Refer to: Battery Disconnect and Connect (414-01 Battery, Mounting and Cables, General Procedures).
2. Remove the cowl vent screen.
Refer to: Cowl Vent Screen (501-02 Front End Body Panels, Removal and Installation).
Installation
3. NOTE: Left-hand shown, right-hand similar.
Torque: 8 Nm
1. Install is the reverse of removal.
Page 2692 of 3039
Pedestrian Protection System - Pedestrian Protection Module
Removal and Installation
Removal
NOTE: Removal steps in this procedure may contain installation details. Published: 11-May-2011
1. Refer to: Battery Disconnect and Connect (414-01 Battery, Mounting and Cables, General Procedures).
2.
3.
Page 2693 of 3039
1. To install, reverse the removal procedure.
Page 2694 of 3039
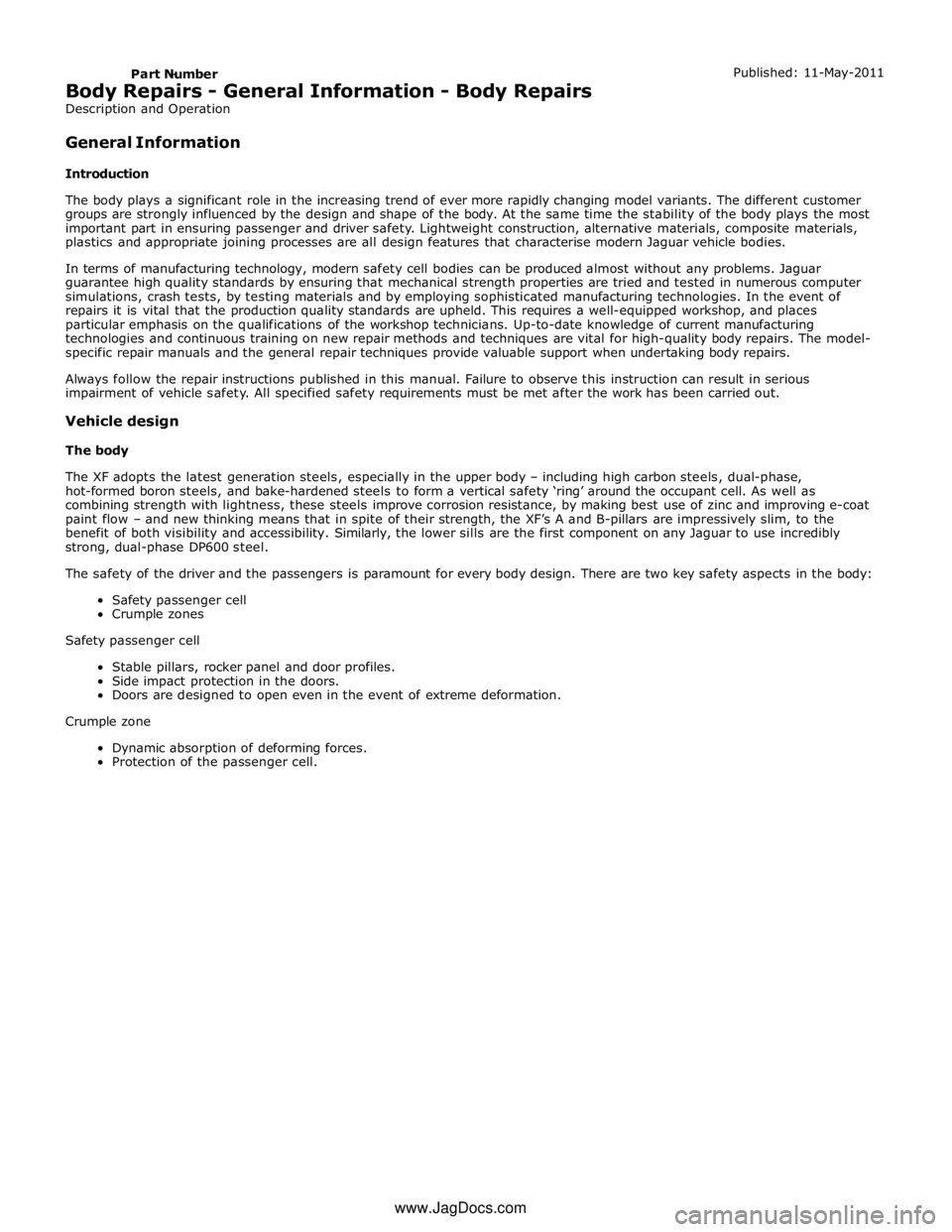
Part N-umber
Body Repairs - General Information - Body Repairs
Description and Operation
General Information
Introduction Published: 11-May-2011
The body plays a significant role in the increasing trend of ever more rapidly changing model variants. The different customer
groups are strongly influenced by the design and shape of the body. At the same time the stability of the body plays the most
important part in ensuring passenger and driver safety. Lightweight construction, alternative materials, composite materials,
plastics and appropriate joining processes are all design features that characterise modern Jaguar vehicle bodies.
In terms of manufacturing technology, modern safety cell bodies can be produced almost without any problems. Jaguar
guarantee high quality standards by ensuring that mechanical strength properties are tried and tested in numerous computer
simulations, crash tests, by testing materials and by employing sophisticated manufacturing technologies. In the event of
repairs it is vital that the production quality standards are upheld. This requires a well-equipped workshop, and places
particular emphasis on the qualifications of the workshop technicians. Up-to-date knowledge of current manufacturing
technologies and continuous training on new repair methods and techniques are vital for high-quality body repairs. The model-
specific repair manuals and the general repair techniques provide valuable support when undertaking body repairs.
Always follow the repair instructions published in this manual. Failure to observe this instruction can result in serious
impairment of vehicle safety. All specified safety requirements must be met after the work has been carried out.
Vehicle design
The body
The XF adopts the latest generation steels, especially in the upper body – including high carbon steels, dual-phase,
hot-formed boron steels, and bake-hardened steels to form a vertical safety ‘ring’ around the occupant cell. As well as
combining strength with lightness, these steels improve corrosion resistance, by making best use of zinc and improving e-coat
paint flow – and new thinking means that in spite of their strength, the XF’s A and B-pillars are impressively slim, to the
benefit of both visibility and accessibility. Similarly, the lower sills are the first component on any Jaguar to use incredibly
strong, dual-phase DP600 steel.
The safety of the driver and the passengers is paramount for every body design. There are two key safety aspects in the body:
Safety passenger cell
Crumple zones
Safety passenger cell
Stable pillars, rocker panel and door profiles.
Side impact protection in the doors.
Doors are designed to open even in the event of extreme deformation.
Crumple zone
Dynamic absorption of deforming forces.
Protection of the passenger cell. www.JagDocs.com
Page 2695 of 3039
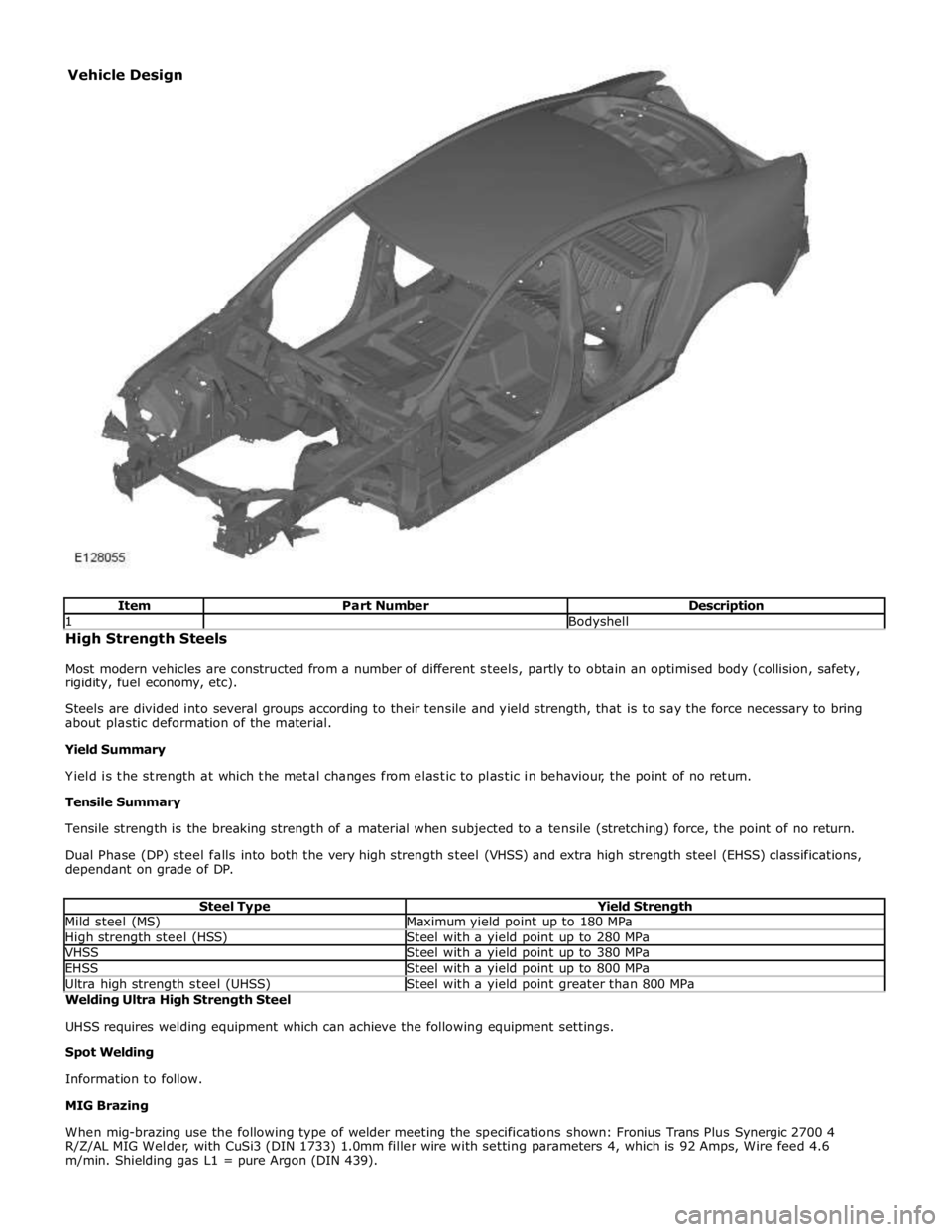
1 Bodyshell High Strength Steels
Most modern vehicles are constructed from a number of different steels, partly to obtain an optimised body (collision, safety,
rigidity, fuel economy, etc).
Steels are divided into several groups according to their tensile and yield strength, that is to say the force necessary to bring
about plastic deformation of the material.
Yield Summary
Yield is the strength at which the metal changes from elastic to plastic in behaviour, the point of no return.
Tensile Summary
Tensile strength is the breaking strength of a material when subjected to a tensile (stretching) force, the point of no return.
Dual Phase (DP) steel falls into both the very high strength steel (VHSS) and extra high strength steel (EHSS) classifications,
dependant on grade of DP.
Steel Type Yield Strength Mild steel (MS) Maximum yield point up to 180 MPa High strength steel (HSS) Steel with a yield point up to 280 MPa VHSS Steel with a yield point up to 380 MPa EHSS Steel with a yield point up to 800 MPa Ultra high strength steel (UHSS) Steel with a yield point greater than 800 MPa Welding Ultra High Strength Steel
UHSS requires welding equipment which can achieve the following equipment settings.
Spot Welding
Information to follow.
MIG Brazing
When mig-brazing use the following type of welder meeting the specifications shown: Fronius Trans Plus Synergic 2700 4
R/Z/AL MIG Welder, with CuSi3 (DIN 1733) 1.0mm filler wire with setting parameters 4, which is 92 Amps, Wire feed 4.6
m/min. Shielding gas L1 = pure Argon (DIN 439). Vehicle Design
Page 2696 of 3039
MS1+Z Mild steel with zinc IF220+Z Interstitial free steel - 220 MPa with zinc MS2+Z Mild steel with zinc