Page 2713 of 3039
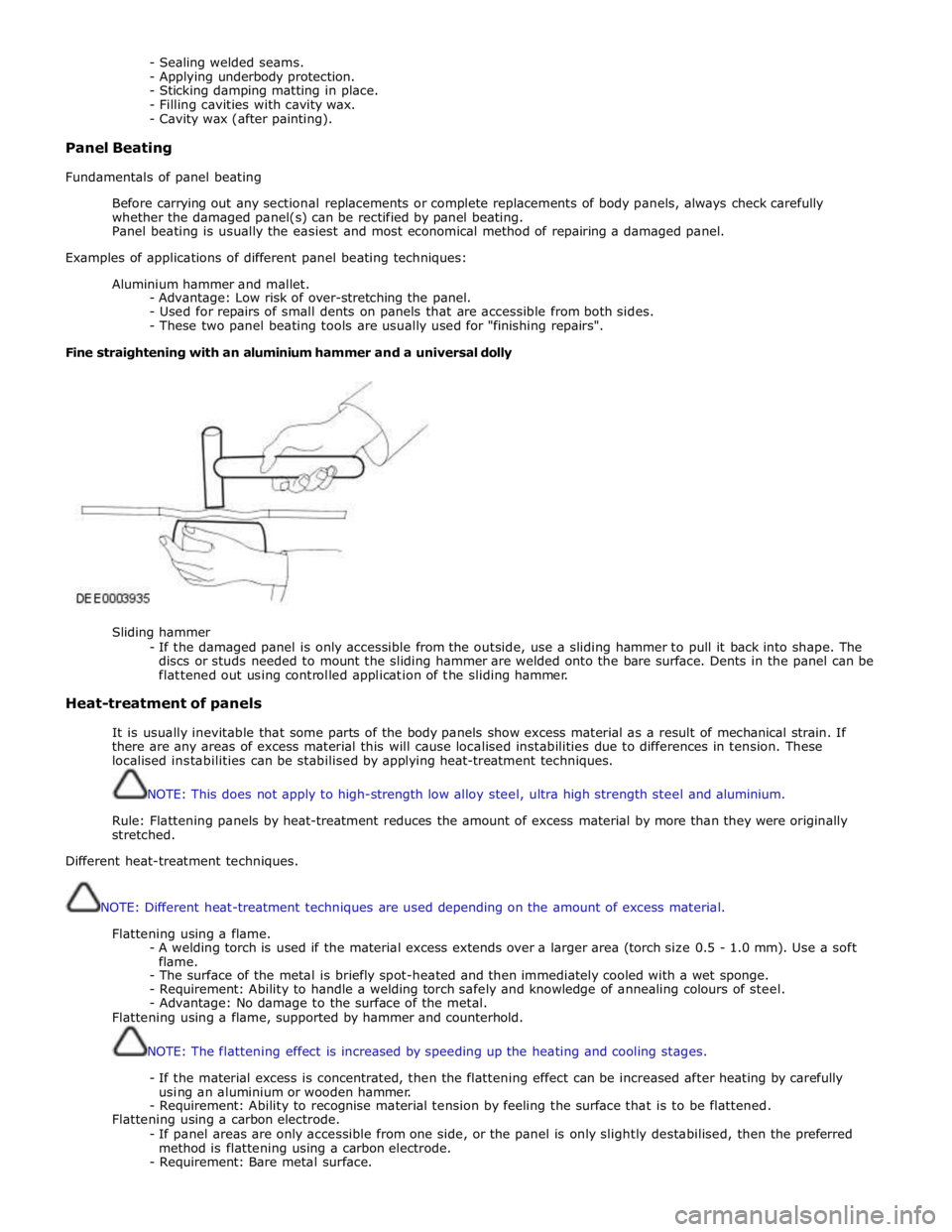
- Sealing welded seams.
- Applying underbody protection.
- Sticking damping matting in place.
- Filling cavities with cavity wax.
- Cavity wax (after painting).
Panel Beating
Fundamentals of panel beating
Before carrying out any sectional replacements or complete replacements of body panels, always check carefully
whether the damaged panel(s) can be rectified by panel beating.
Panel beating is usually the easiest and most economical method of repairing a damaged panel.
Examples of applications of different panel beating techniques:
Aluminium hammer and mallet.
- Advantage: Low risk of over-stretching the panel.
- Used for repairs of small dents on panels that are accessible from both sides.
- These two panel beating tools are usually used for "finishing repairs".
Fine straightening with an aluminium hammer and a universal dolly
Sliding hammer
- If the damaged panel is only accessible from the outside, use a sliding hammer to pull it back into shape. The
discs or studs needed to mount the sliding hammer are welded onto the bare surface. Dents in the panel can be
flattened out using controlled application of the sliding hammer.
Heat-treatment of panels
It is usually inevitable that some parts of the body panels show excess material as a result of mechanical strain. If
there are any areas of excess material this will cause localised instabilities due to differences in tension. These
localised instabilities can be stabilised by applying heat-treatment techniques.
NOTE: This does not apply to high-strength low alloy steel, ultra high strength steel and aluminium.
Rule: Flattening panels by heat-treatment reduces the amount of excess material by more than they were originally
stretched.
Different heat-treatment techniques.
NOTE: Different heat-treatment techniques are used depending on the amount of excess material.
Flattening using a flame.
- A welding torch is used if the material excess extends over a larger area (torch size 0.5 - 1.0 mm). Use a soft
flame.
- The surface of the metal is briefly spot-heated and then immediately cooled with a wet sponge.
- Requirement: Ability to handle a welding torch safely and knowledge of annealing colours of steel.
- Advantage: No damage to the surface of the metal.
Flattening using a flame, supported by hammer and counterhold.
NOTE: The flattening effect is increased by speeding up the heating and cooling stages.
- If the material excess is concentrated, then the flattening effect can be increased after heating by carefully
using an aluminium or wooden hammer.
- Requirement: Ability to recognise material tension by feeling the surface that is to be flattened.
Flattening using a carbon electrode.
- If panel areas are only accessible from one side, or the panel is only slightly destabilised, then the preferred
method is flattening using a carbon electrode.
- Requirement: Bare metal surface.
Page 2714 of 3039
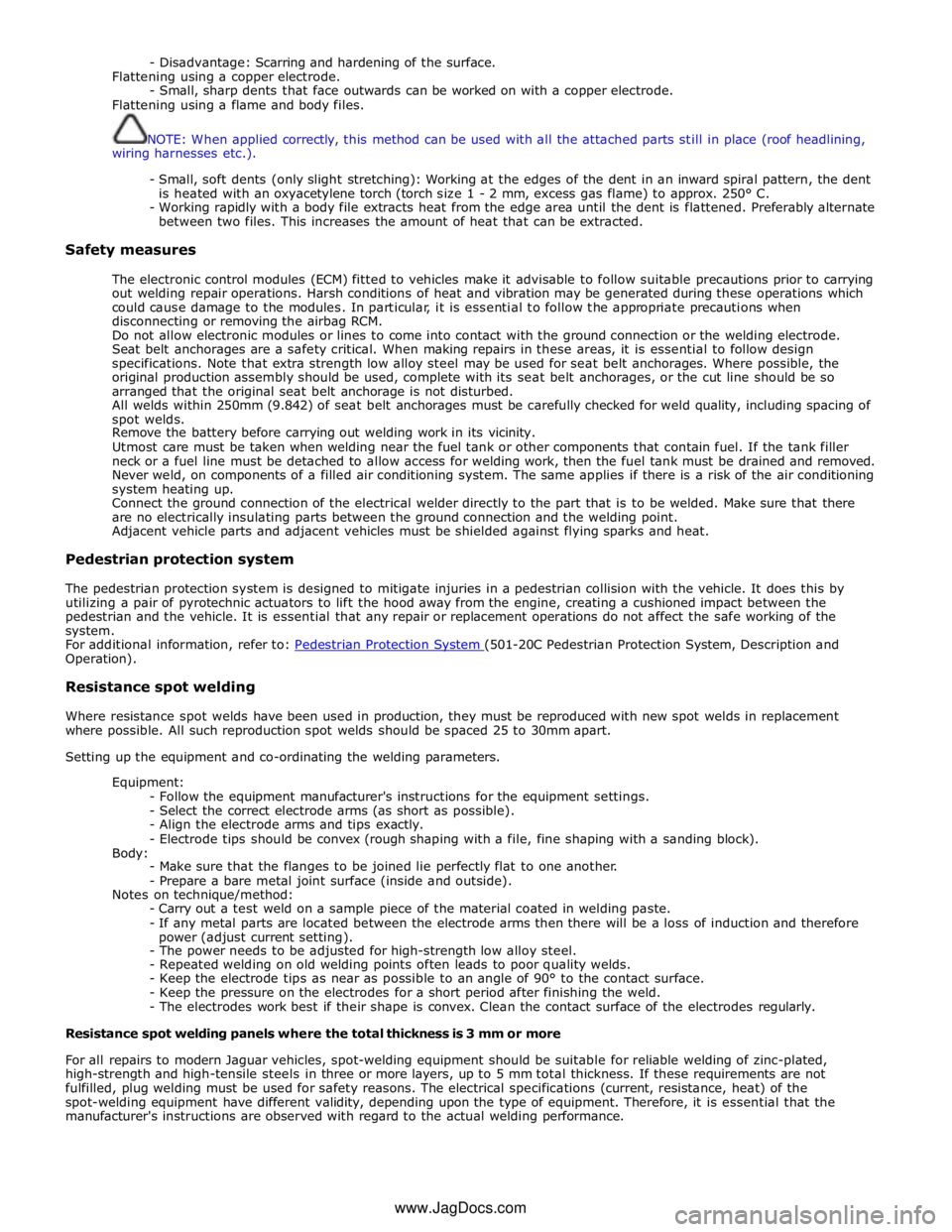
- Disadvantage: Scarring and hardening of the surface.
Flattening using a copper electrode.
- Small, sharp dents that face outwards can be worked on with a copper electrode.
Flattening using a flame and body files.
NOTE: When applied correctly, this method can be used with all the attached parts still in place (roof headlining,
wiring harnesses etc.).
- Small, soft dents (only slight stretching): Working at the edges of the dent in an inward spiral pattern, the dent
is heated with an oxyacetylene torch (torch size 1 - 2 mm, excess gas flame) to approx. 250° C.
- Working rapidly with a body file extracts heat from the edge area until the dent is flattened. Preferably alternate
between two files. This increases the amount of heat that can be extracted.
Safety measures
The electronic control modules (ECM) fitted to vehicles make it advisable to follow suitable precautions prior to carrying
out welding repair operations. Harsh conditions of heat and vibration may be generated during these operations which
could cause damage to the modules. In particular, it is essential to follow the appropriate precautions when
disconnecting or removing the airbag RCM.
Do not allow electronic modules or lines to come into contact with the ground connection or the welding electrode.
Seat belt anchorages are a safety critical. When making repairs in these areas, it is essential to follow design
specifications. Note that extra strength low alloy steel may be used for seat belt anchorages. Where possible, the
original production assembly should be used, complete with its seat belt anchorages, or the cut line should be so
arranged that the original seat belt anchorage is not disturbed.
All welds within 250mm (9.842) of seat belt anchorages must be carefully checked for weld quality, including spacing of
spot welds.
Remove the battery before carrying out welding work in its vicinity.
Utmost care must be taken when welding near the fuel tank or other components that contain fuel. If the tank filler
neck or a fuel line must be detached to allow access for welding work, then the fuel tank must be drained and removed.
Never weld, on components of a filled air conditioning system. The same applies if there is a risk of the air conditioning
system heating up.
Connect the ground connection of the electrical welder directly to the part that is to be welded. Make sure that there
are no electrically insulating parts between the ground connection and the welding point.
Adjacent vehicle parts and adjacent vehicles must be shielded against flying sparks and heat.
Pedestrian protection system
The pedestrian protection system is designed to mitigate injuries in a pedestrian collision with the vehicle. It does this by
utilizing a pair of pyrotechnic actuators to lift the hood away from the engine, creating a cushioned impact between the
pedestrian and the vehicle. It is essential that any repair or replacement operations do not affect the safe working of the
system.
For additional information, refer to: Pedestrian Protection System (501-20C Pedestrian Protection System, Description and Operation).
Resistance spot welding
Where resistance spot welds have been used in production, they must be reproduced with new spot welds in replacement
where possible. All such reproduction spot welds should be spaced 25 to 30mm apart.
Setting up the equipment and co-ordinating the welding parameters.
Equipment:
- Follow the equipment manufacturer's instructions for the equipment settings.
- Select the correct electrode arms (as short as possible).
- Align the electrode arms and tips exactly.
- Electrode tips should be convex (rough shaping with a file, fine shaping with a sanding block).
Body:
- Make sure that the flanges to be joined lie perfectly flat to one another.
- Prepare a bare metal joint surface (inside and outside).
Notes on technique/method:
- Carry out a test weld on a sample piece of the material coated in welding paste.
- If any metal parts are located between the electrode arms then there will be a loss of induction and therefore
power (adjust current setting).
- The power needs to be adjusted for high-strength low alloy steel.
- Repeated welding on old welding points often leads to poor quality welds.
- Keep the electrode tips as near as possible to an angle of 90° to the contact surface.
- Keep the pressure on the electrodes for a short period after finishing the weld.
- The electrodes work best if their shape is convex. Clean the contact surface of the electrodes regularly.
Resistance spot welding panels where the total thickness is 3 mm or more
For all repairs to modern Jaguar vehicles, spot-welding equipment should be suitable for reliable welding of zinc-plated,
high-strength and high-tensile steels in three or more layers, up to 5 mm total thickness. If these requirements are not
fulfilled, plug welding must be used for safety reasons. The electrical specifications (current, resistance, heat) of the
spot-welding equipment have different validity, depending upon the type of equipment. Therefore, it is essential that the
manufacturer's instructions are observed with regard to the actual welding performance.
www.JagDocs.com
Page 2715 of 3039
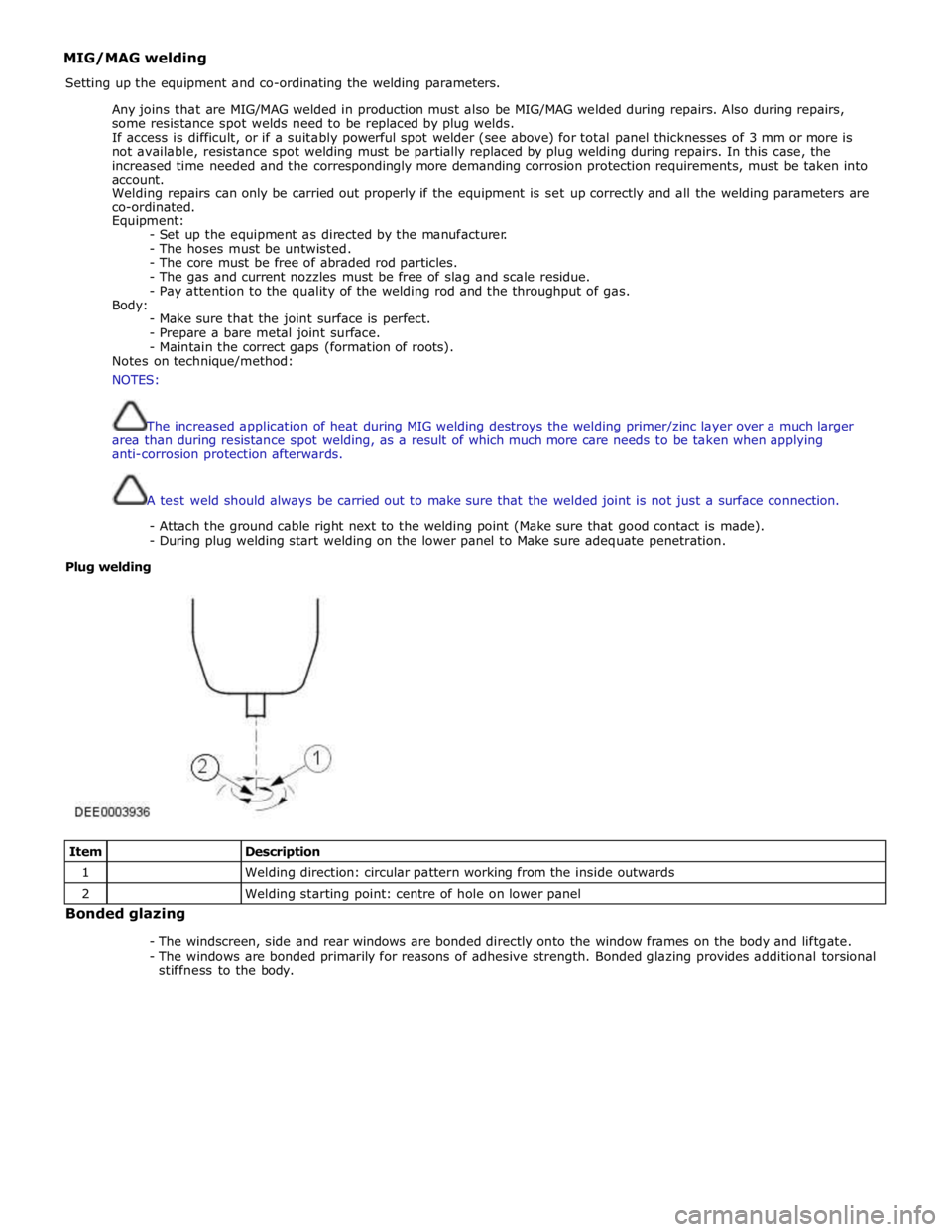
MIG/MAG welding
Setting up the equipment and co-ordinating the welding parameters.
Any joins that are MIG/MAG welded in production must also be MIG/MAG welded during repairs. Also during repairs,
some resistance spot welds need to be replaced by plug welds.
If access is difficult, or if a suitably powerful spot welder (see above) for total panel thicknesses of 3 mm or more is
not available, resistance spot welding must be partially replaced by plug welding during repairs. In this case, the
increased time needed and the correspondingly more demanding corrosion protection requirements, must be taken into
account.
Welding repairs can only be carried out properly if the equipment is set up correctly and all the welding parameters are
co-ordinated.
Equipment:
- Set up the equipment as directed by the manufacturer.
- The hoses must be untwisted.
- The core must be free of abraded rod particles.
- The gas and current nozzles must be free of slag and scale residue.
- Pay attention to the quality of the welding rod and the throughput of gas.
Body:
- Make sure that the joint surface is perfect.
- Prepare a bare metal joint surface.
- Maintain the correct gaps (formation of roots).
Notes on technique/method:
NOTES:
The increased application of heat during MIG welding destroys the welding primer/zinc layer over a much larger
area than during resistance spot welding, as a result of which much more care needs to be taken when applying
anti-corrosion protection afterwards.
A test weld should always be carried out to make sure that the welded joint is not just a surface connection.
- Attach the ground cable right next to the welding point (Make sure that good contact is made).
- During plug welding start welding on the lower panel to Make sure adequate penetration.
Plug welding
Item
Description 1
Welding direction: circular pattern working from the inside outwards 2
Welding starting point: centre of hole on lower panel Bonded glazing
- The windscreen, side and rear windows are bonded directly onto the window frames on the body and liftgate.
- The windows are bonded primarily for reasons of adhesive strength. Bonded glazing provides additional torsional
stiffness to the body.
Page 2716 of 3039
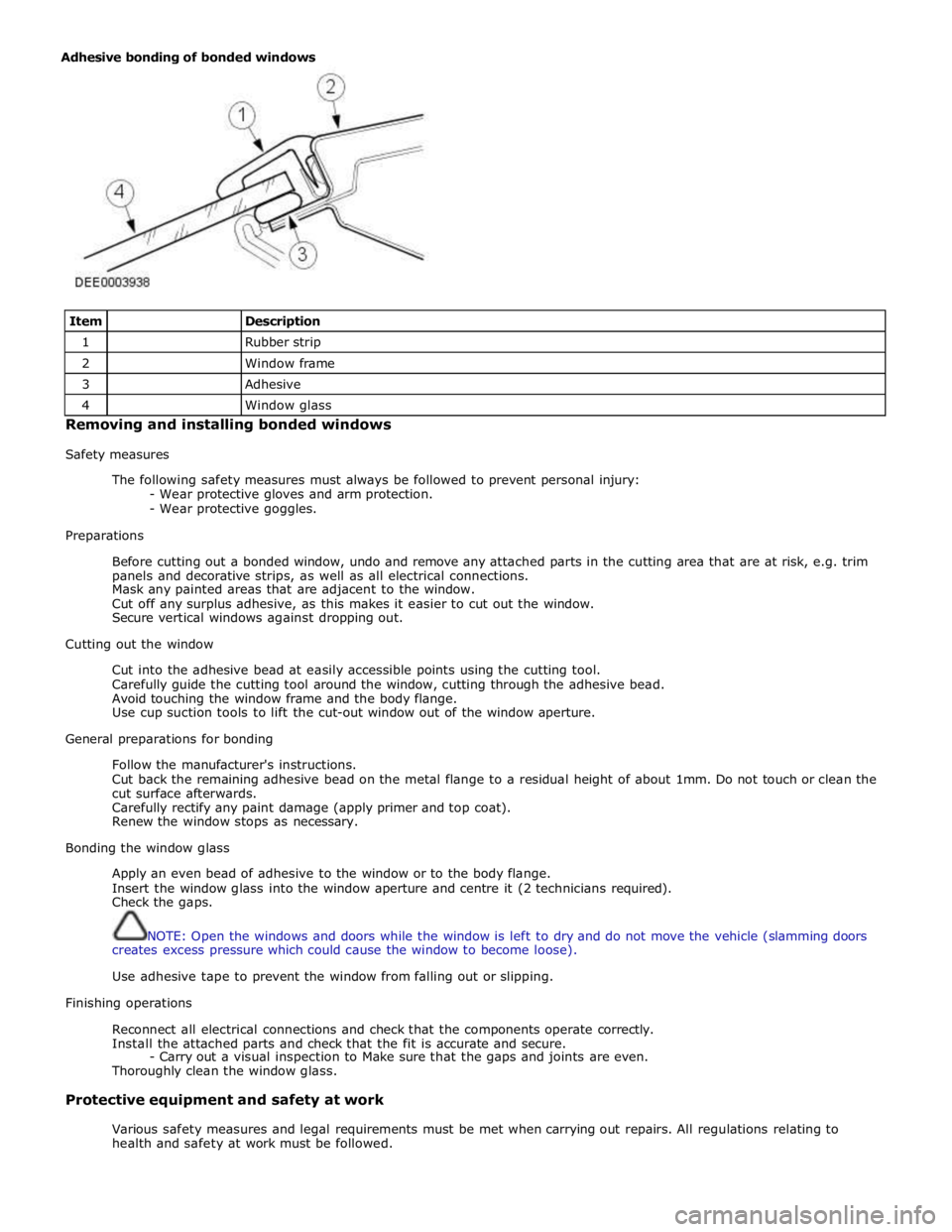
Item
Description 1
Rubber strip 2
Window frame 3
Adhesive 4
Window glass Removing and installing bonded windows
Safety measures
The following safety measures must always be followed to prevent personal injury:
- Wear protective gloves and arm protection.
- Wear protective goggles.
Preparations
Before cutting out a bonded window, undo and remove any attached parts in the cutting area that are at risk, e.g. trim
panels and decorative strips, as well as all electrical connections.
Mask any painted areas that are adjacent to the window.
Cut off any surplus adhesive, as this makes it easier to cut out the window.
Secure vertical windows against dropping out.
Cutting out the window
Cut into the adhesive bead at easily accessible points using the cutting tool.
Carefully guide the cutting tool around the window, cutting through the adhesive bead.
Avoid touching the window frame and the body flange.
Use cup suction tools to lift the cut-out window out of the window aperture.
General preparations for bonding
Follow the manufacturer's instructions.
Cut back the remaining adhesive bead on the metal flange to a residual height of about 1mm. Do not touch or clean the
cut surface afterwards.
Carefully rectify any paint damage (apply primer and top coat).
Renew the window stops as necessary.
Bonding the window glass
Apply an even bead of adhesive to the window or to the body flange.
Insert the window glass into the window aperture and centre it (2 technicians required).
Check the gaps.
NOTE: Open the windows and doors while the window is left to dry and do not move the vehicle (slamming doors
creates excess pressure which could cause the window to become loose).
Use adhesive tape to prevent the window from falling out or slipping.
Finishing operations
Reconnect all electrical connections and check that the components operate correctly.
Install the attached parts and check that the fit is accurate and secure.
- Carry out a visual inspection to Make sure that the gaps and joints are even.
Thoroughly clean the window glass.
Protective equipment and safety at work
Various safety measures and legal requirements must be met when carrying out repairs. All regulations relating to
health and safety at work must be followed. Adhesive bonding of bonded windows
Page 2717 of 3039
Page 2718 of 3039
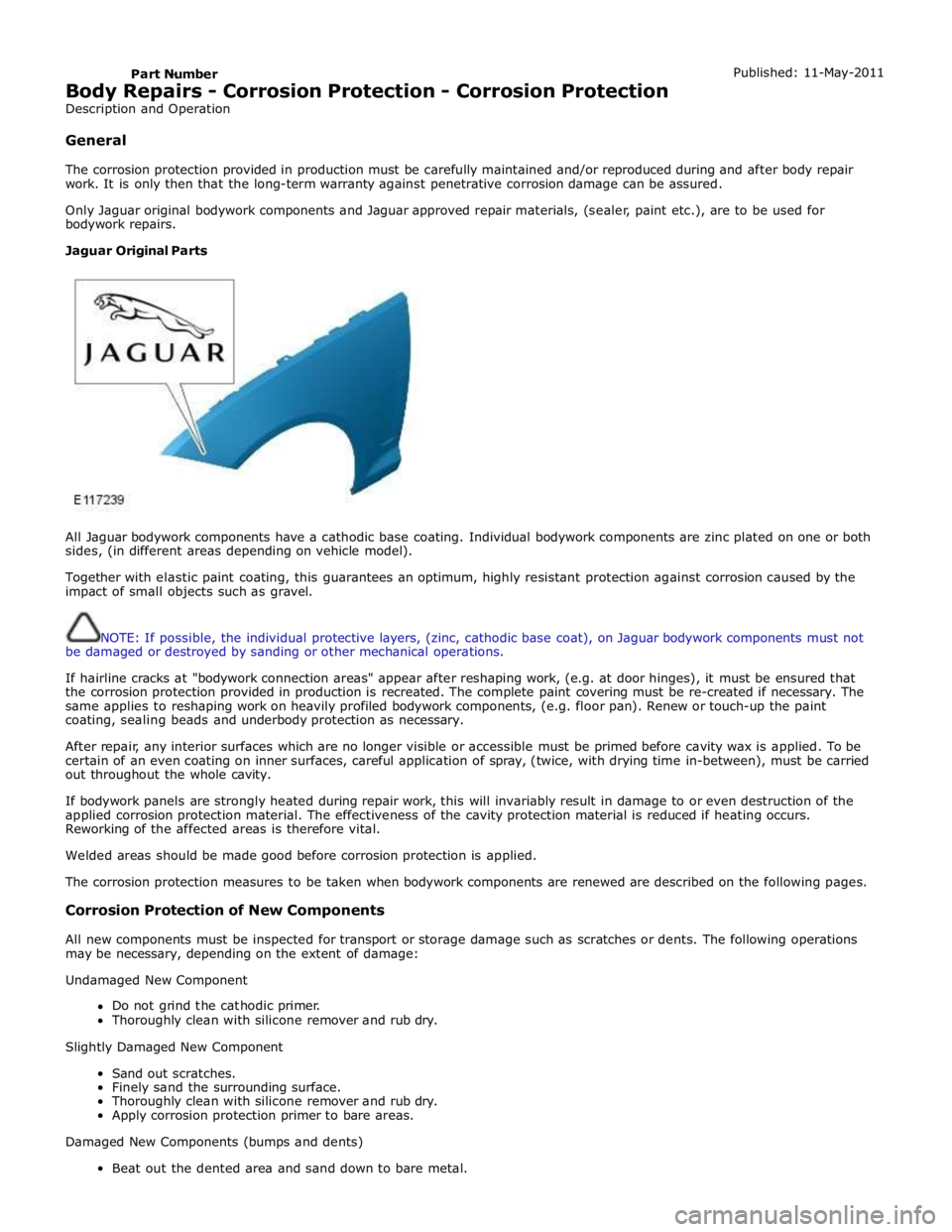
Part N-umber
Body Repairs - Corrosion Protection - Corrosion Protection
Description and Operation
General Published: 11-May-2011
The corrosion protection provided in production must be carefully maintained and/or reproduced during and after body repair
work. It is only then that the long-term warranty against penetrative corrosion damage can be assured.
Only Jaguar original bodywork components and Jaguar approved repair materials, (sealer, paint etc.), are to be used for
bodywork repairs.
Jaguar Original Parts
All Jaguar bodywork components have a cathodic base coating. Individual bodywork components are zinc plated on one or both
sides, (in different areas depending on vehicle model).
Together with elastic paint coating, this guarantees an optimum, highly resistant protection against corrosion caused by the
impact of small objects such as gravel.
NOTE: If possible, the individual protective layers, (zinc, cathodic base coat), on Jaguar bodywork components must not
be damaged or destroyed by sanding or other mechanical operations.
If hairline cracks at "bodywork connection areas" appear after reshaping work, (e.g. at door hinges), it must be ensured that
the corrosion protection provided in production is recreated. The complete paint covering must be re-created if necessary. The
same applies to reshaping work on heavily profiled bodywork components, (e.g. floor pan). Renew or touch-up the paint
coating, sealing beads and underbody protection as necessary.
After repair, any interior surfaces which are no longer visible or accessible must be primed before cavity wax is applied. To be
certain of an even coating on inner surfaces, careful application of spray, (twice, with drying time in-between), must be carried
out throughout the whole cavity.
If bodywork panels are strongly heated during repair work, this will invariably result in damage to or even destruction of the
applied corrosion protection material. The effectiveness of the cavity protection material is reduced if heating occurs.
Reworking of the affected areas is therefore vital.
Welded areas should be made good before corrosion protection is applied.
The corrosion protection measures to be taken when bodywork components are renewed are described on the following pages.
Corrosion Protection of New Components
All new components must be inspected for transport or storage damage such as scratches or dents. The following operations
may be necessary, depending on the extent of damage:
Undamaged New Component
Do not grind the cathodic primer.
Thoroughly clean with silicone remover and rub dry.
Slightly Damaged New Component
Sand out scratches.
Finely sand the surrounding surface.
Thoroughly clean with silicone remover and rub dry.
Apply corrosion protection primer to bare areas.
Damaged New Components (bumps and dents)
Beat out the dented area and sand down to bare metal.
Page 2719 of 3039
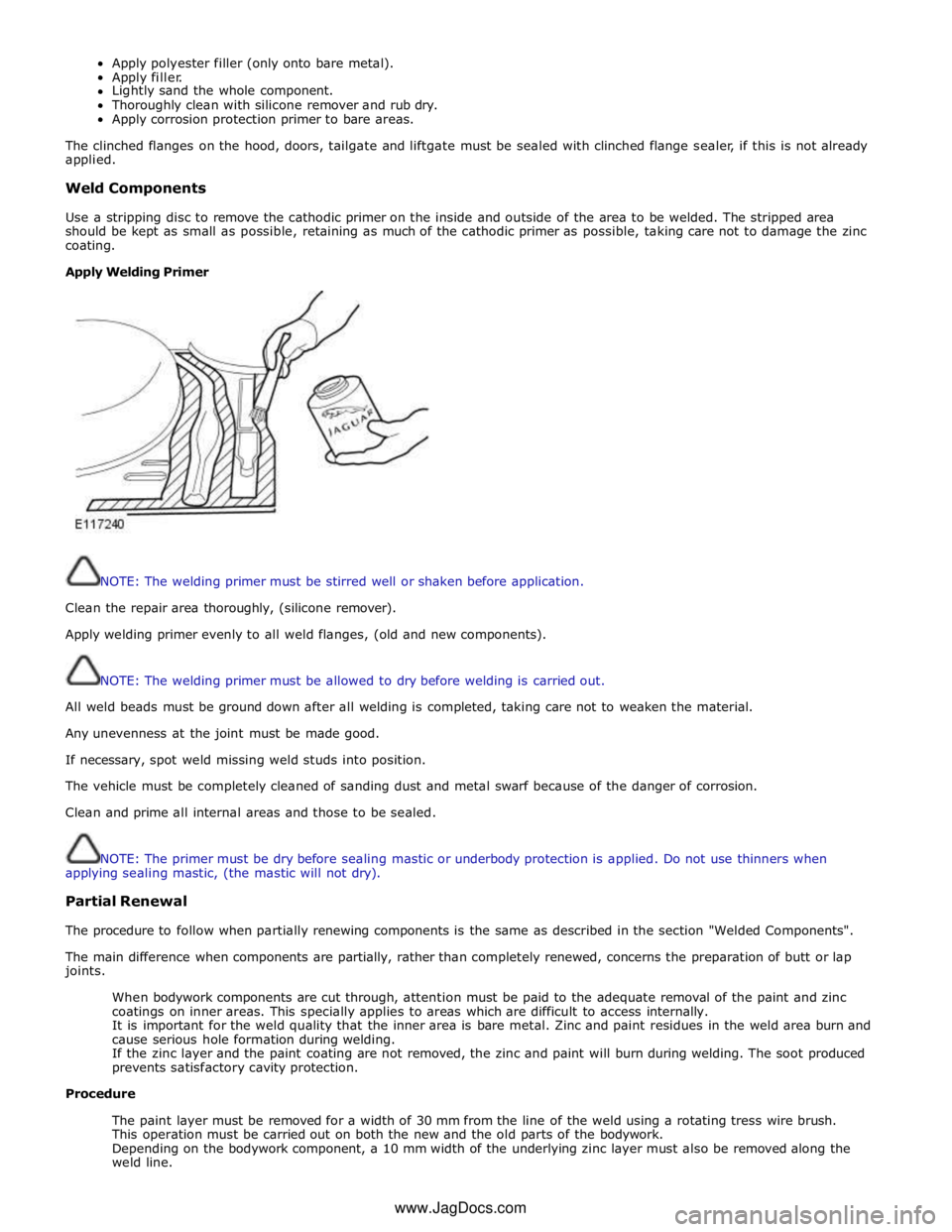
Apply polyester filler (only onto bare metal).
Apply filler.
Lightly sand the whole component.
Thoroughly clean with silicone remover and rub dry.
Apply corrosion protection primer to bare areas.
The clinched flanges on the hood, doors, tailgate and liftgate must be sealed with clinched flange sealer, if this is not already
applied.
Weld Components
Use a stripping disc to remove the cathodic primer on the inside and outside of the area to be welded. The stripped area
should be kept as small as possible, retaining as much of the cathodic primer as possible, taking care not to damage the zinc
coating.
Apply Welding Primer
NOTE: The welding primer must be stirred well or shaken before application.
Clean the repair area thoroughly, (silicone remover).
Apply welding primer evenly to all weld flanges, (old and new components).
NOTE: The welding primer must be allowed to dry before welding is carried out.
All weld beads must be ground down after all welding is completed, taking care not to weaken the material.
Any unevenness at the joint must be made good.
If necessary, spot weld missing weld studs into position.
The vehicle must be completely cleaned of sanding dust and metal swarf because of the danger of corrosion.
Clean and prime all internal areas and those to be sealed.
NOTE: The primer must be dry before sealing mastic or underbody protection is applied. Do not use thinners when
applying sealing mastic, (the mastic will not dry).
Partial Renewal
The procedure to follow when partially renewing components is the same as described in the section "Welded Components".
The main difference when components are partially, rather than completely renewed, concerns the preparation of butt or lap
joints.
When bodywork components are cut through, attention must be paid to the adequate removal of the paint and zinc
coatings on inner areas. This specially applies to areas which are difficult to access internally.
It is important for the weld quality that the inner area is bare metal. Zinc and paint residues in the weld area burn and
cause serious hole formation during welding.
If the zinc layer and the paint coating are not removed, the zinc and paint will burn during welding. The soot produced
prevents satisfactory cavity protection.
Procedure
The paint layer must be removed for a width of 30 mm from the line of the weld using a rotating tress wire brush.
This operation must be carried out on both the new and the old parts of the bodywork.
Depending on the bodywork component, a 10 mm width of the underlying zinc layer must also be removed along the
weld line. www.JagDocs.com
Page 2720 of 3039
NOTE: A flat scraper or a wire brush can be used instead of the rotating brush if the cavity is small. Do not use an angle
grinder, which would weaken the structure.
Application of Cavity Wax Protection on a Rocker Panel After Partial Repair
Item
Description 1
Weld bead 2
Spray head 3
Distance maintainer 4
Spray gun
Classification of the different corrosion protection measures for dent removal
Corrosion Protection Method Exterior Surfaces Accessible Inner Surfaces Inaccessible Inner Surfaces Painting X X Cavity protection X Classification of Different Corrosion Protection Measures for Installation of New Components
Corrosion Protection
Method Weld Flanges Before Welding in Place (contact surfaces) All Bare Sanded
Areas Weld Flange Area
Accessible Weld Flange Area Not
Accessible Welding primer X Painting X X Clinched flange protection X
Cavity protection X