Page 1177 of 3573
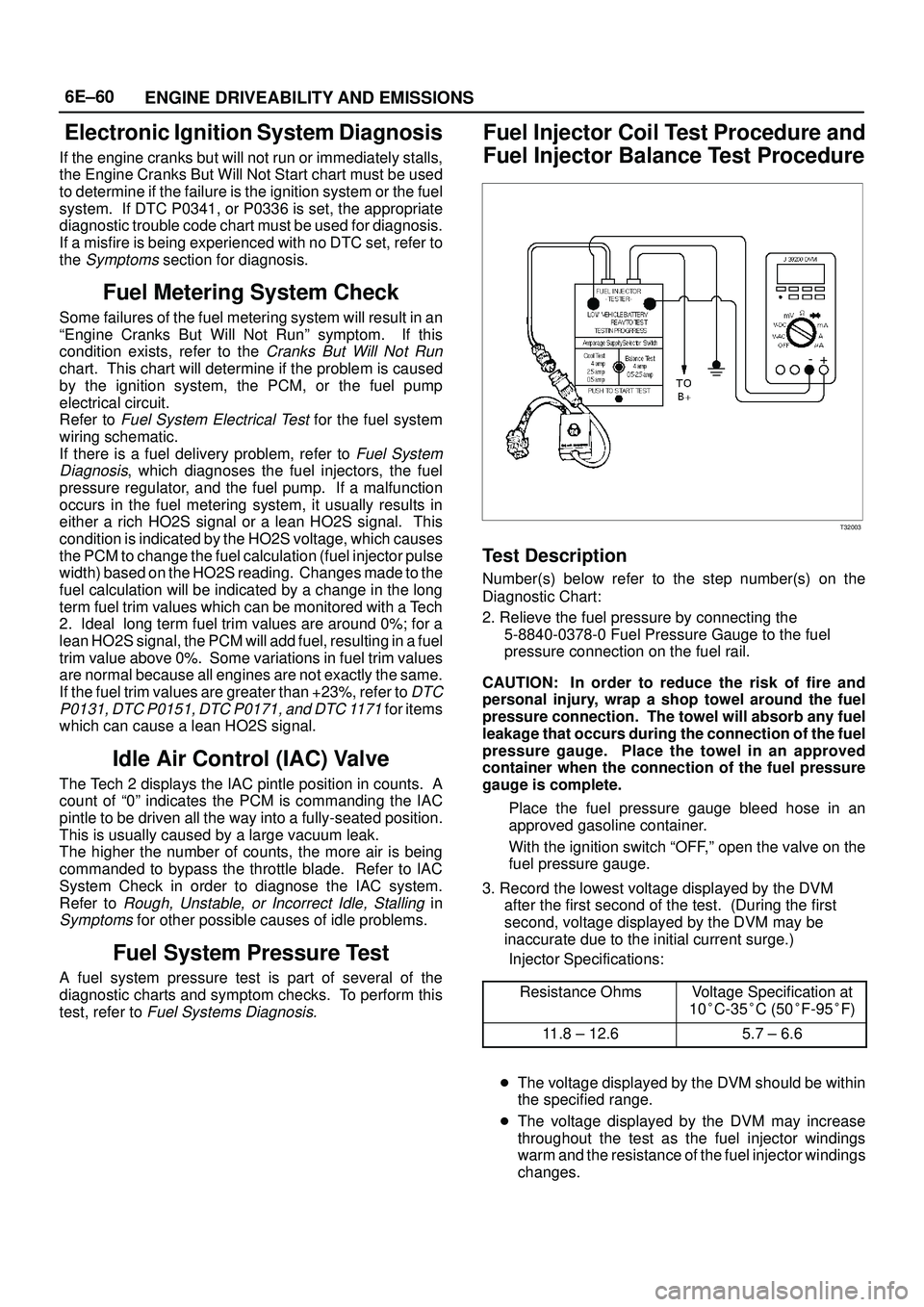
6E±60
ENGINE DRIVEABILITY AND EMISSIONS
Electronic Ignition System Diagnosis
If the engine cranks but will not run or immediately stalls,
the Engine Cranks But Will Not Start chart must be used
to determine if the failure is the ignition system or the fuel
system. If DTC P0341, or P0336 is set, the appropriate
diagnostic trouble code chart must be used for diagnosis.
If a misfire is being experienced with no DTC set, refer to
the
Symptoms section for diagnosis.
Fuel Metering System Check
Some failures of the fuel metering system will result in an
ªEngine Cranks But Will Not Runº symptom. If this
condition exists, refer to the
Cranks But Will Not Run
chart. This chart will determine if the problem is caused
by the ignition system, the PCM, or the fuel pump
electrical circuit.
Refer to
Fuel System Electrical Test for the fuel system
wiring schematic.
If there is a fuel delivery problem, refer to
Fuel System
Diagnosis
, which diagnoses the fuel injectors, the fuel
pressure regulator, and the fuel pump. If a malfunction
occurs in the fuel metering system, it usually results in
either a rich HO2S signal or a lean HO2S signal. This
condition is indicated by the HO2S voltage, which causes
the PCM to change the fuel calculation (fuel injector pulse
width) based on the HO2S reading. Changes made to the
fuel calculation will be indicated by a change in the long
term fuel trim values which can be monitored with a Tech
2. Ideal long term fuel trim values are around 0%; for a
lean HO2S signal, the PCM will add fuel, resulting in a fuel
trim value above 0%. Some variations in fuel trim values
are normal because all engines are not exactly the same.
If the fuel trim values are greater than +23%, refer to
DTC
P0131, DTC P0151, DTC P0171, and DTC 1171
for items
which can cause a lean HO2S signal.
Idle Air Control (IAC) Valve
The Tech 2 displays the IAC pintle position in counts. A
count of ª0º indicates the PCM is commanding the IAC
pintle to be driven all the way into a fully-seated position.
This is usually caused by a large vacuum leak.
The higher the number of counts, the more air is being
commanded to bypass the throttle blade. Refer to IAC
System Check in order to diagnose the IAC system.
Refer to
Rough, Unstable, or Incorrect Idle, Stalling in
Symptoms for other possible causes of idle problems.
Fuel System Pressure Test
A fuel system pressure test is part of several of the
diagnostic charts and symptom checks. To perform this
test, refer to
Fuel Systems Diagnosis.
Fuel Injector Coil Test Procedure and
Fuel Injector Balance Test Procedure
T32003
Test Description
Number(s) below refer to the step number(s) on the
Diagnostic Chart:
2. Relieve the fuel pressure by connecting the
5-8840-0378-0 Fuel Pressure Gauge to the fuel
pressure connection on the fuel rail.
CAUTION: In order to reduce the risk of fire and
personal injury, wrap a shop towel around the fuel
pressure connection. The towel will absorb any fuel
leakage that occurs during the connection of the fuel
pressure gauge. Place the towel in an approved
container when the connection of the fuel pressure
gauge is complete.
Place the fuel pressure gauge bleed hose in an
approved gasoline container.
With the ignition switch ªOFF,º open the valve on the
fuel pressure gauge.
3. Record the lowest voltage displayed by the DVM
after the first second of the test. (During the first
second, voltage displayed by the DVM may be
inaccurate due to the initial current surge.)
Injector Specifications:
Resistance Ohms
Voltage Specification at
10C-35C (50F-95F)
11.8 ± 12.65.7 ± 6.6
The voltage displayed by the DVM should be within
the specified range.
The voltage displayed by the DVM may increase
throughout the test as the fuel injector windings
warm and the resistance of the fuel injector windings
changes.
Page 1178 of 3573
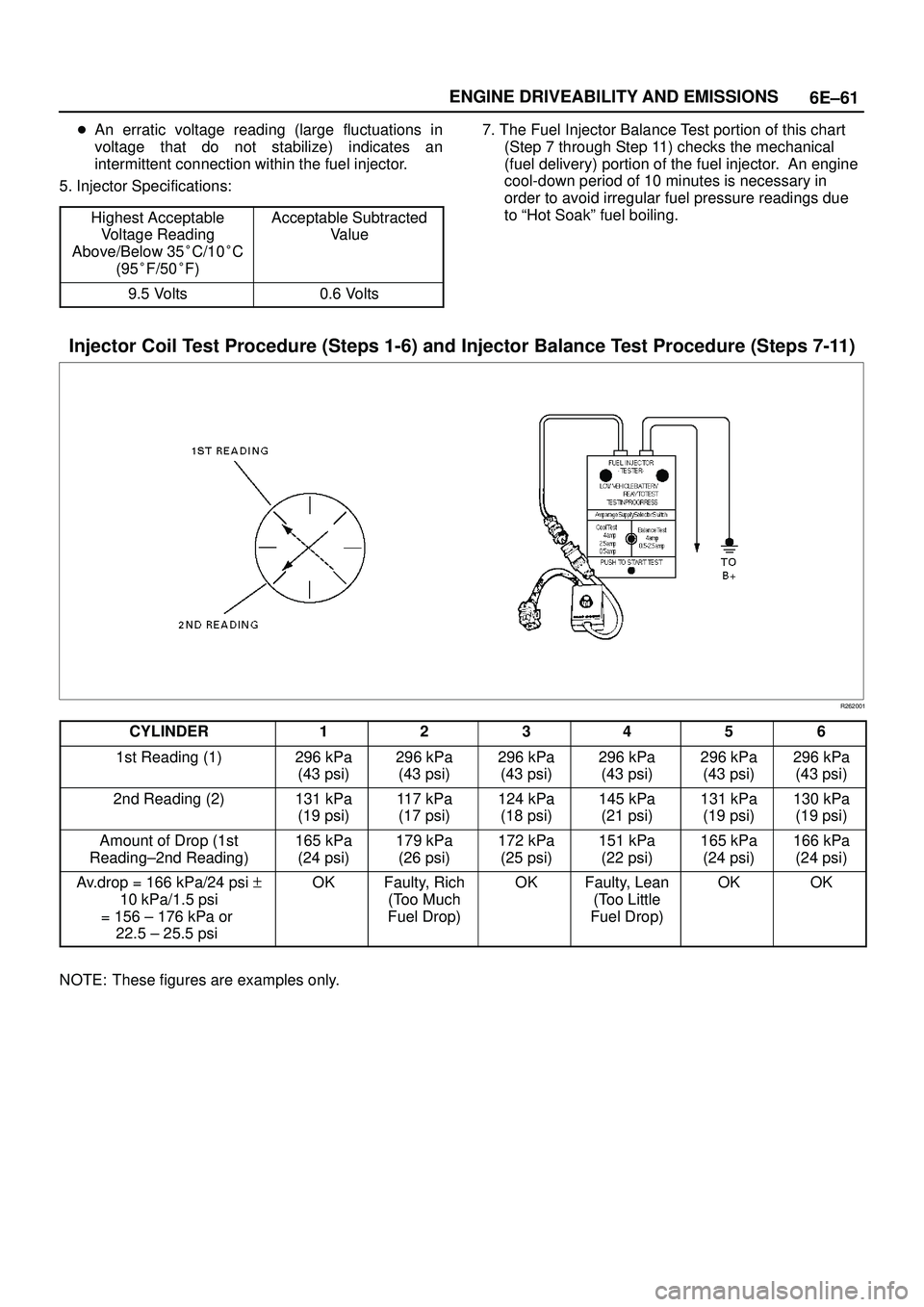
6E±61 ENGINE DRIVEABILITY AND EMISSIONS
An erratic voltage reading (large fluctuations in
voltage that do not stabilize) indicates an
intermittent connection within the fuel injector.
5. Injector Specifications:
Highest Acceptable
Voltage Reading
Above/Below 35C/10C
(95F/50F)
Acceptable Subtracted
Value
9.5 Volts0.6 Volts
7. The Fuel Injector Balance Test portion of this chart
(Step 7 through Step 11) checks the mechanical
(fuel delivery) portion of the fuel injector. An engine
cool-down period of 10 minutes is necessary in
order to avoid irregular fuel pressure readings due
to ªHot Soakº fuel boiling.
Injector Coil Test Procedure (Steps 1-6) and Injector Balance Test Procedure (Steps 7-11)
R262001
CYLINDER123456
1st Reading (1)296 kPa
(43 psi)296 kPa
(43 psi)296 kPa
(43 psi)296 kPa
(43 psi)296 kPa
(43 psi)296 kPa
(43 psi)
2nd Reading (2)131 kPa
(19 psi)117 kPa
(17 psi)124 kPa
(18 psi)145 kPa
(21 psi)131 kPa
(19 psi)130 kPa
(19 psi)
Amount of Drop (1st
Reading±2nd Reading)165 kPa
(24 psi)179 kPa
(26 psi)172 kPa
(25 psi)151 kPa
(22 psi)165 kPa
(24 psi)166 kPa
(24 psi)
Av.drop = 166 kPa/24 psi +
10 kPa/1.5 psi
= 156 ± 176 kPa or
22.5 ± 25.5 psiOKFaulty, Rich
(Too Much
Fuel Drop)OKFaulty, Lean
(Too Little
Fuel Drop)OKOK
NOTE: These figures are examples only.
Page 1179 of 3573
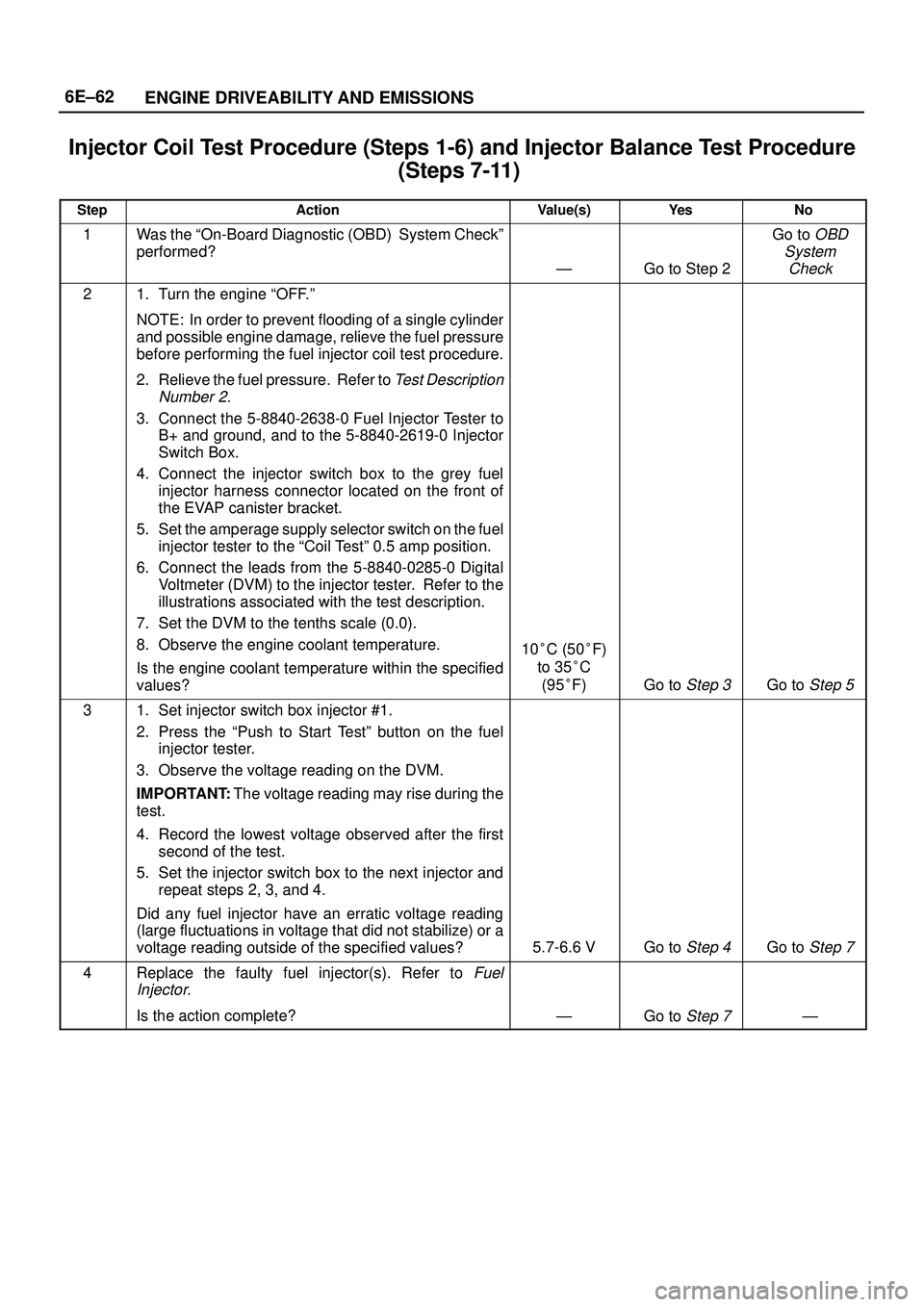
6E±62
ENGINE DRIVEABILITY AND EMISSIONS
Injector Coil Test Procedure (Steps 1-6) and Injector Balance Test Procedure
(Steps 7-11)
StepActionValue(s)Ye sNo
1Was the ªOn-Board Diagnostic (OBD) System Checkº
performed?
ÐGo to Step 2
Go to OBD
System
Check
21. Turn the engine ªOFF.º
NOTE: In order to prevent flooding of a single cylinder
and possible engine damage, relieve the fuel pressure
before performing the fuel injector coil test procedure.
2. Relieve the fuel pressure. Refer to
Test Description
Number 2.
3. Connect the 5-8840-2638-0 Fuel Injector Tester to
B+ and ground, and to the 5-8840-2619-0 Injector
Switch Box.
4. Connect the injector switch box to the grey fuel
injector harness connector located on the front of
the EVAP canister bracket.
5. Set the amperage supply selector switch on the fuel
injector tester to the ªCoil Testº 0.5 amp position.
6. Connect the leads from the 5-8840-0285-0 Digital
Voltmeter (DVM) to the injector tester. Refer to the
illustrations associated with the test description.
7. Set the DVM to the tenths scale (0.0).
8. Observe the engine coolant temperature.
Is the engine coolant temperature within the specified
values?
10C (50F)
to 35C
(95F)
Go to Step 3Go to Step 5
31. Set injector switch box injector #1.
2. Press the ªPush to Start Testº button on the fuel
injector tester.
3. Observe the voltage reading on the DVM.
IMPORTANT:The voltage reading may rise during the
test.
4. Record the lowest voltage observed after the first
second of the test.
5. Set the injector switch box to the next injector and
repeat steps 2, 3, and 4.
Did any fuel injector have an erratic voltage reading
(large fluctuations in voltage that did not stabilize) or a
voltage reading outside of the specified values?
5.7-6.6 VGo to Step 4Go to Step 7
4Replace the faulty fuel injector(s). Refer to Fuel
Injector.
Is the action complete?ÐGo to Step 7Ð
Page 1180 of 3573
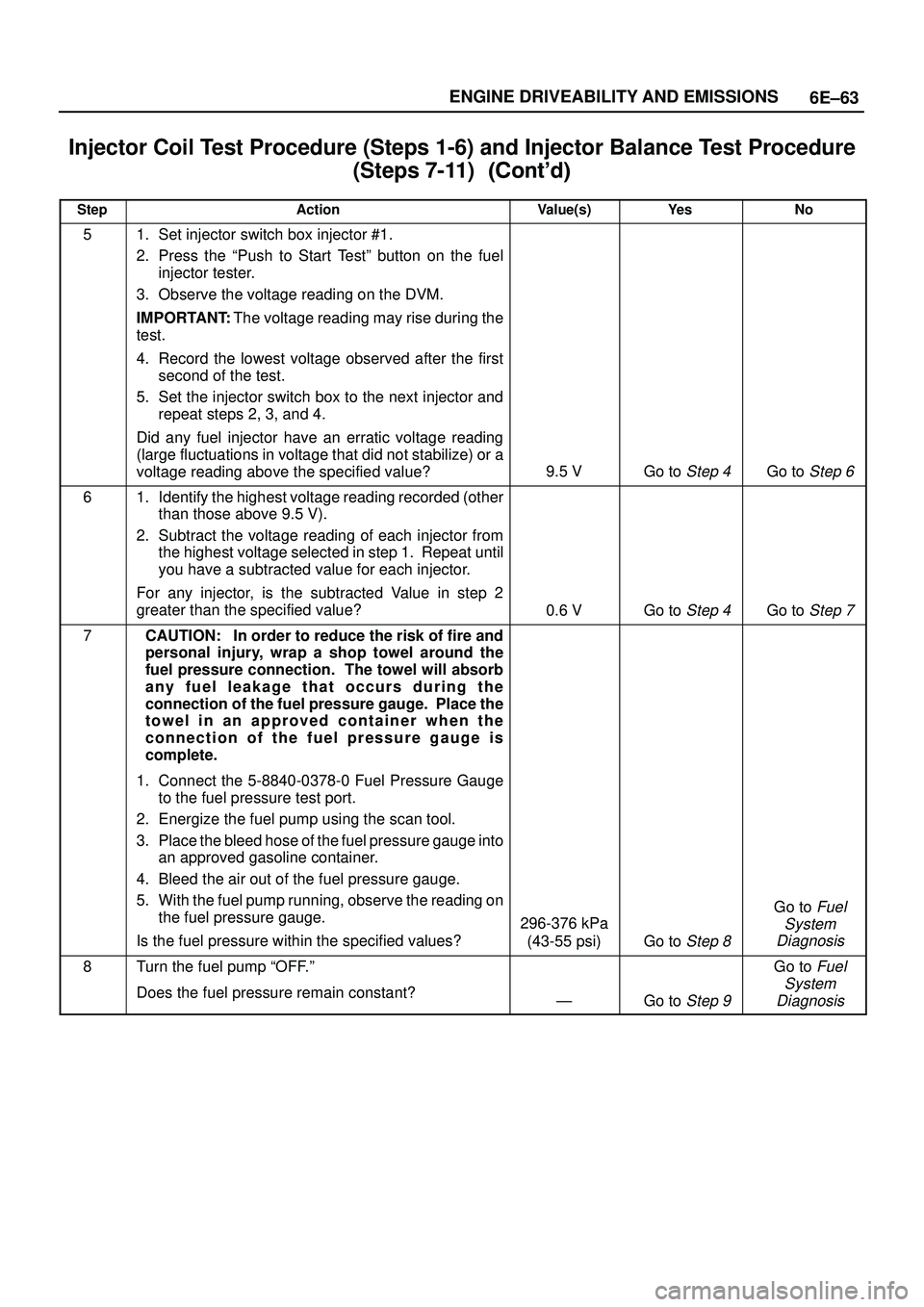
6E±63 ENGINE DRIVEABILITY AND EMISSIONS
Injector Coil Test Procedure (Steps 1-6) and Injector Balance Test Procedure
(Steps 7-11)
StepNo Ye s Value(s) Action
51. Set injector switch box injector #1.
2. Press the ªPush to Start Testº button on the fuel
injector tester.
3. Observe the voltage reading on the DVM.
IMPORTANT:The voltage reading may rise during the
test.
4. Record the lowest voltage observed after the first
second of the test.
5. Set the injector switch box to the next injector and
repeat steps 2, 3, and 4.
Did any fuel injector have an erratic voltage reading
(large fluctuations in voltage that did not stabilize) or a
voltage reading above the specified value?
9.5 VGo to Step 4Go to Step 6
61. Identify the highest voltage reading recorded (other
than those above 9.5 V).
2. Subtract the voltage reading of each injector from
the highest voltage selected in step 1. Repeat until
you have a subtracted value for each injector.
For any injector, is the subtracted Value in step 2
greater than the specified value?
0.6 VGo to Step 4Go to Step 7
7CAUTION: In order to reduce the risk of fire and
personal injury, wrap a shop towel around the
fuel pressure connection. The towel will absorb
any fuel leakage that occurs during the
connection of the fuel pressure gauge. Place the
towel in an approved container when the
connection of the fuel pressure gauge is
complete.
1. Connect the 5-8840-0378-0 Fuel Pressure Gauge
to the fuel pressure test port.
2. Energize the fuel pump using the scan tool.
3. Place the bleed hose of the fuel pressure gauge into
an approved gasoline container.
4. Bleed the air out of the fuel pressure gauge.
5. With the fuel pump running, observe the reading on
the fuel pressure gauge.
Is the fuel pressure within the specified values?
296-376 kPa
(43-55 psi)
Go to Step 8
Go to Fuel
System
Diagnosis
8Turn the fuel pump ªOFF.º
Does the fuel pressure remain constant?
ÐGo to Step 9
Go to Fuel
System
Diagnosis
Page 1181 of 3573
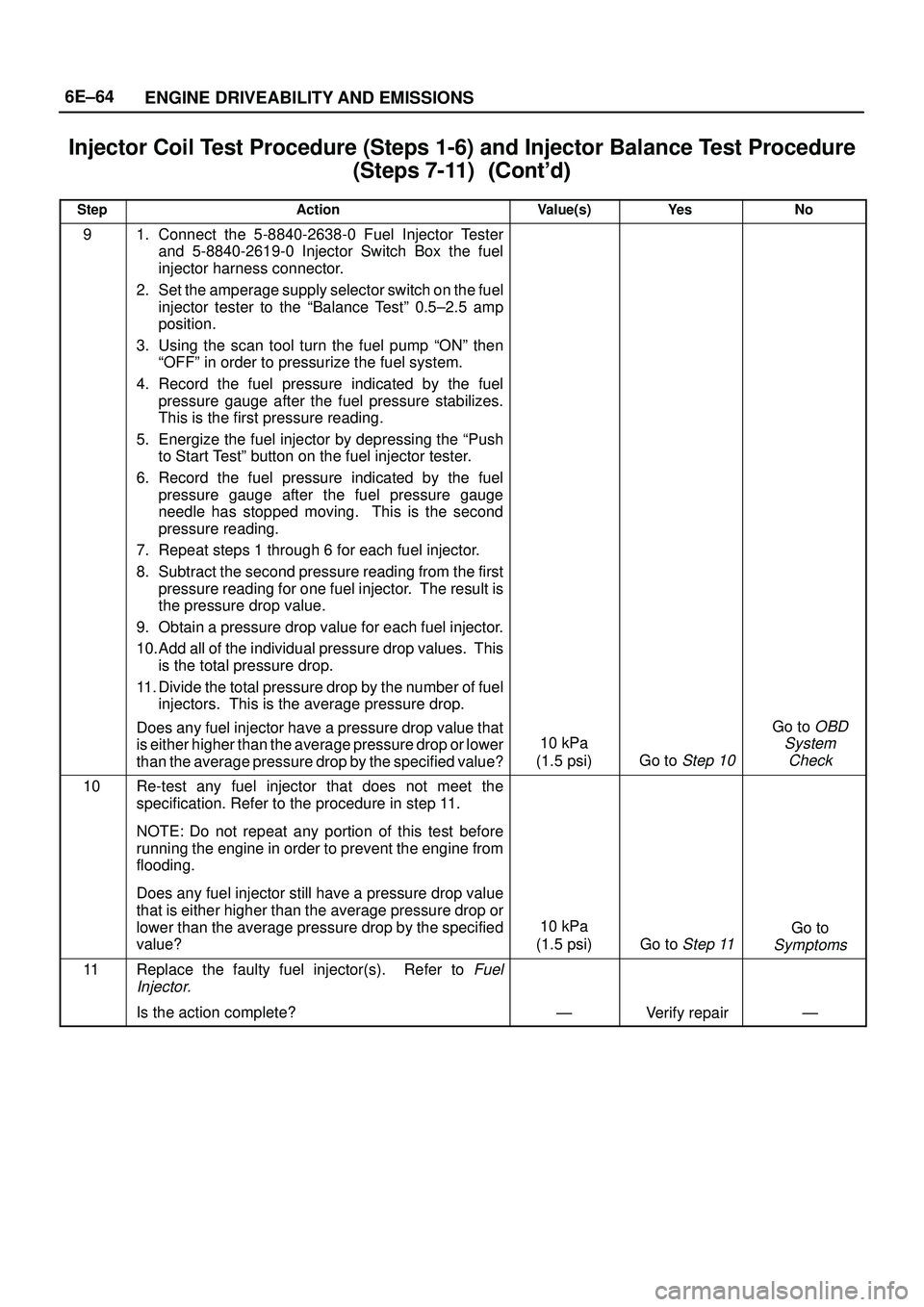
6E±64
ENGINE DRIVEABILITY AND EMISSIONS
Injector Coil Test Procedure (Steps 1-6) and Injector Balance Test Procedure
(Steps 7-11)
StepNo Ye s Value(s) Action
91. Connect the 5-8840-2638-0 Fuel Injector Tester
and 5-8840-2619-0 Injector Switch Box the fuel
injector harness connector.
2. Set the amperage supply selector switch on the fuel
injector tester to the ªBalance Testº 0.5±2.5 amp
position.
3. Using the scan tool turn the fuel pump ªONº then
ªOFFº in order to pressurize the fuel system.
4. Record the fuel pressure indicated by the fuel
pressure gauge after the fuel pressure stabilizes.
This is the first pressure reading.
5. Energize the fuel injector by depressing the ªPush
to Start Testº button on the fuel injector tester.
6. Record the fuel pressure indicated by the fuel
pressure gauge after the fuel pressure gauge
needle has stopped moving. This is the second
pressure reading.
7. Repeat steps 1 through 6 for each fuel injector.
8. Subtract the second pressure reading from the first
pressure reading for one fuel injector. The result is
the pressure drop value.
9. Obtain a pressure drop value for each fuel injector.
10.Add all of the individual pressure drop values. This
is the total pressure drop.
11. Divide the total pressure drop by the number of fuel
injectors. This is the average pressure drop.
Does any fuel injector have a pressure drop value that
is either higher than the average pressure drop or lower
than the average pressure drop by the specified value?
10 kPa
(1.5 psi)
Go to Step 10
Go to OBD
System
Check
10Re-test any fuel injector that does not meet the
specification. Refer to the procedure in step 11.
NOTE: Do not repeat any portion of this test before
running the engine in order to prevent the engine from
flooding.
Does any fuel injector still have a pressure drop value
that is either higher than the average pressure drop or
lower than the average pressure drop by the specified
value?
10 kPa
(1.5 psi)
Go to Step 11
Go to
Symptoms
11Replace the faulty fuel injector(s). Refer to Fuel
Injector.
Is the action complete?ÐVerify repairÐ
Page 1182 of 3573
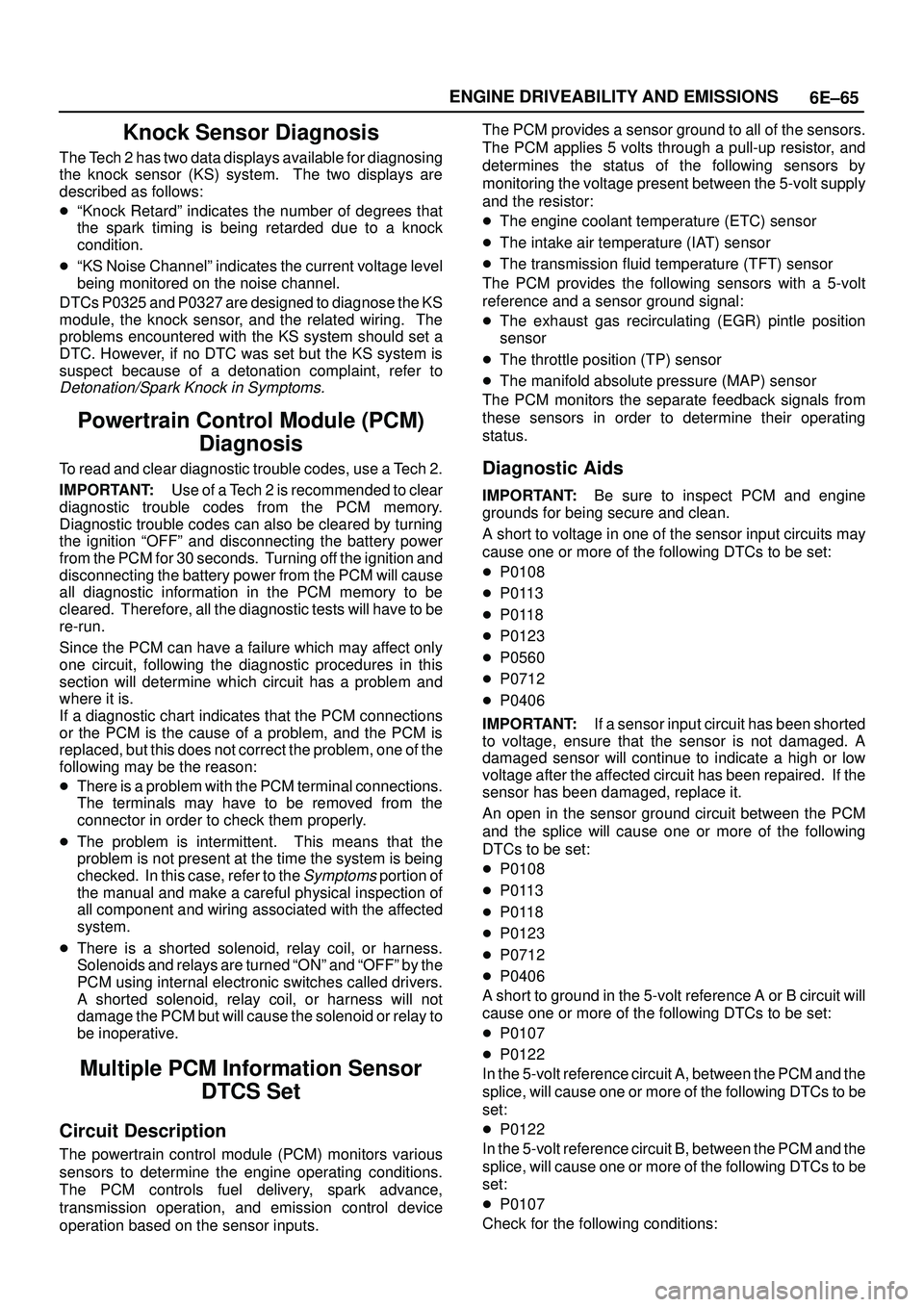
6E±65 ENGINE DRIVEABILITY AND EMISSIONS
Knock Sensor Diagnosis
The Tech 2 has two data displays available for diagnosing
the knock sensor (KS) system. The two displays are
described as follows:
ªKnock Retardº indicates the number of degrees that
the spark timing is being retarded due to a knock
condition.
ªKS Noise Channelº indicates the current voltage level
being monitored on the noise channel.
DTCs P0325 and P0327 are designed to diagnose the KS
module, the knock sensor, and the related wiring. The
problems encountered with the KS system should set a
DTC. However, if no DTC was set but the KS system is
suspect because of a detonation complaint, refer to
Detonation/Spark Knock in Symptoms.
Powertrain Control Module (PCM)
Diagnosis
To read and clear diagnostic trouble codes, use a Tech 2.
IMPORTANT:Use of a Tech 2 is recommended to clear
diagnostic trouble codes from the PCM memory.
Diagnostic trouble codes can also be cleared by turning
the ignition ªOFFº and disconnecting the battery power
from the PCM for 30 seconds. Turning off the ignition and
disconnecting the battery power from the PCM will cause
all diagnostic information in the PCM memory to be
cleared. Therefore, all the diagnostic tests will have to be
re-run.
Since the PCM can have a failure which may affect only
one circuit, following the diagnostic procedures in this
section will determine which circuit has a problem and
where it is.
If a diagnostic chart indicates that the PCM connections
or the PCM is the cause of a problem, and the PCM is
replaced, but this does not correct the problem, one of the
following may be the reason:
There is a problem with the PCM terminal connections.
The terminals may have to be removed from the
connector in order to check them properly.
The problem is intermittent. This means that the
problem is not present at the time the system is being
checked. In this case, refer to the
Symptoms portion of
the manual and make a careful physical inspection of
all component and wiring associated with the affected
system.
There is a shorted solenoid, relay coil, or harness.
Solenoids and relays are turned ªONº and ªOFFº by the
PCM using internal electronic switches called drivers.
A shorted solenoid, relay coil, or harness will not
damage the PCM but will cause the solenoid or relay to
be inoperative.
Multiple PCM Information Sensor
DTCS Set
Circuit Description
The powertrain control module (PCM) monitors various
sensors to determine the engine operating conditions.
The PCM controls fuel delivery, spark advance,
transmission operation, and emission control device
operation based on the sensor inputs.The PCM provides a sensor ground to all of the sensors.
The PCM applies 5 volts through a pull-up resistor, and
determines the status of the following sensors by
monitoring the voltage present between the 5-volt supply
and the resistor:
The engine coolant temperature (ETC) sensor
The intake air temperature (IAT) sensor
The transmission fluid temperature (TFT) sensor
The PCM provides the following sensors with a 5-volt
reference and a sensor ground signal:
The exhaust gas recirculating (EGR) pintle position
sensor
The throttle position (TP) sensor
The manifold absolute pressure (MAP) sensor
The PCM monitors the separate feedback signals from
these sensors in order to determine their operating
status.
Diagnostic Aids
IMPORTANT:Be sure to inspect PCM and engine
grounds for being secure and clean.
A short to voltage in one of the sensor input circuits may
cause one or more of the following DTCs to be set:
P0108
P0113
P0118
P0123
P0560
P0712
P0406
IMPORTANT:If a sensor input circuit has been shorted
to voltage, ensure that the sensor is not damaged. A
damaged sensor will continue to indicate a high or low
voltage after the affected circuit has been repaired. If the
sensor has been damaged, replace it.
An open in the sensor ground circuit between the PCM
and the splice will cause one or more of the following
DTCs to be set:
P0108
P0113
P0118
P0123
P0712
P0406
A short to ground in the 5-volt reference A or B circuit will
cause one or more of the following DTCs to be set:
P0107
P0122
In the 5-volt reference circuit A, between the PCM and the
splice, will cause one or more of the following DTCs to be
set:
P0122
In the 5-volt reference circuit B, between the PCM and the
splice, will cause one or more of the following DTCs to be
set:
P0107
Check for the following conditions:
Page 1183 of 3573
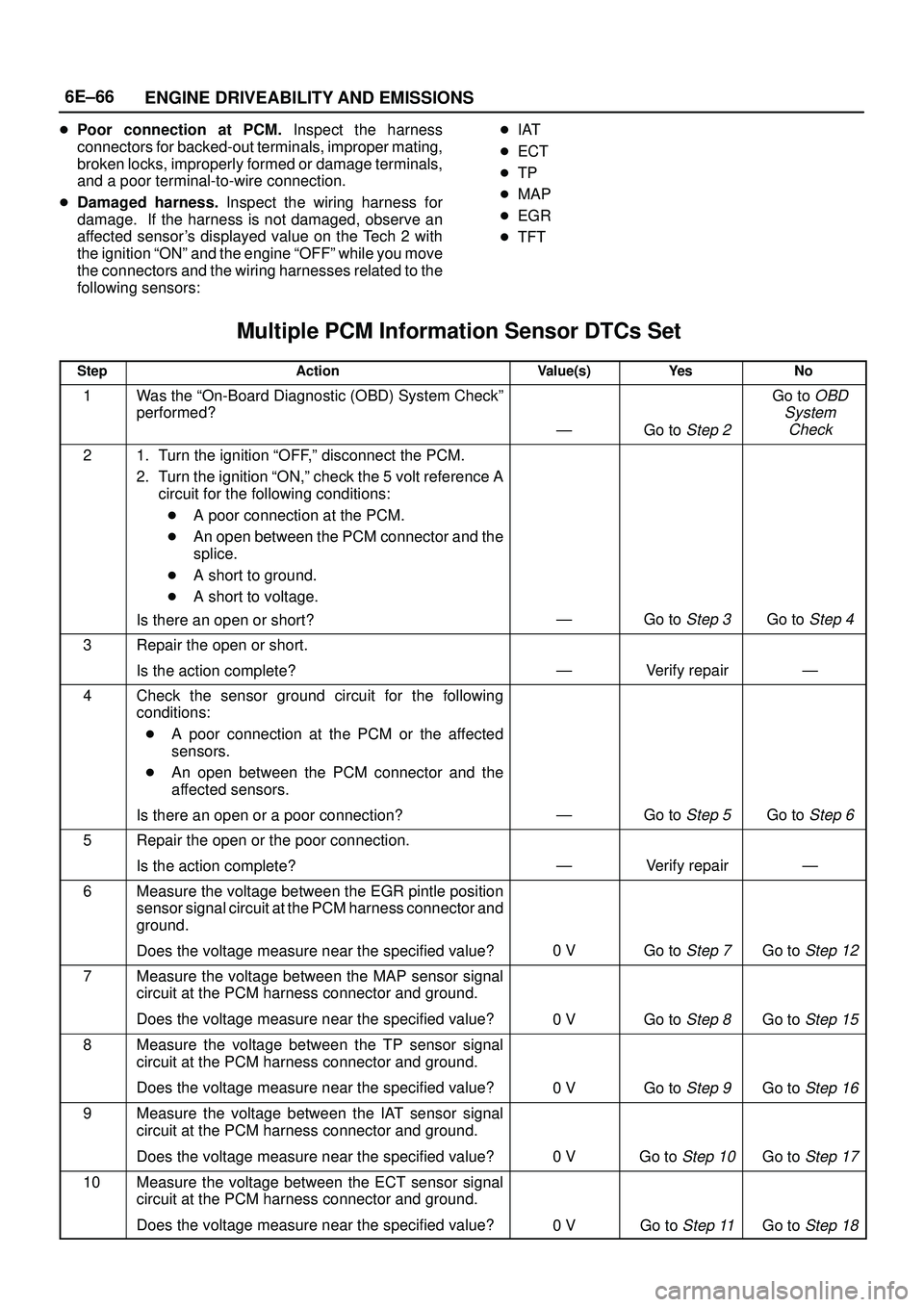
6E±66
ENGINE DRIVEABILITY AND EMISSIONS
Poor connection at PCM. Inspect the harness
connectors for backed-out terminals, improper mating,
broken locks, improperly formed or damage terminals,
and a poor terminal-to-wire connection.
Damaged harness. Inspect the wiring harness for
damage. If the harness is not damaged, observe an
affected sensor's displayed value on the Tech 2 with
the ignition ªONº and the engine ªOFFº while you move
the connectors and the wiring harnesses related to the
following sensors:IAT
ECT
TP
MAP
EGR
TFT
Multiple PCM Information Sensor DTCs Set
StepActionValue(s)Ye sNo
1Was the ªOn-Board Diagnostic (OBD) System Checkº
performed?
ÐGo to Step 2
Go to OBD
System
Check
21. Turn the ignition ªOFF,º disconnect the PCM.
2. Turn the ignition ªON,º check the 5 volt reference A
circuit for the following conditions:
A poor connection at the PCM.
An open between the PCM connector and the
splice.
A short to ground.
A short to voltage.
Is there an open or short?
ÐGo to Step 3Go to Step 4
3Repair the open or short.
Is the action complete?
ÐVerify repairÐ
4Check the sensor ground circuit for the following
conditions:
A poor connection at the PCM or the affected
sensors.
An open between the PCM connector and the
affected sensors.
Is there an open or a poor connection?
ÐGo to Step 5Go to Step 6
5Repair the open or the poor connection.
Is the action complete?
ÐVerify repairÐ
6Measure the voltage between the EGR pintle position
sensor signal circuit at the PCM harness connector and
ground.
Does the voltage measure near the specified value?
0 VGo to Step 7Go to Step 12
7Measure the voltage between the MAP sensor signal
circuit at the PCM harness connector and ground.
Does the voltage measure near the specified value?
0 VGo to Step 8Go to Step 15
8Measure the voltage between the TP sensor signal
circuit at the PCM harness connector and ground.
Does the voltage measure near the specified value?
0 VGo to Step 9Go to Step 16
9Measure the voltage between the IAT sensor signal
circuit at the PCM harness connector and ground.
Does the voltage measure near the specified value?
0 VGo to Step 10Go to Step 17
10Measure the voltage between the ECT sensor signal
circuit at the PCM harness connector and ground.
Does the voltage measure near the specified value?
0 VGo to Step 11Go to Step 18
Page 1184 of 3573
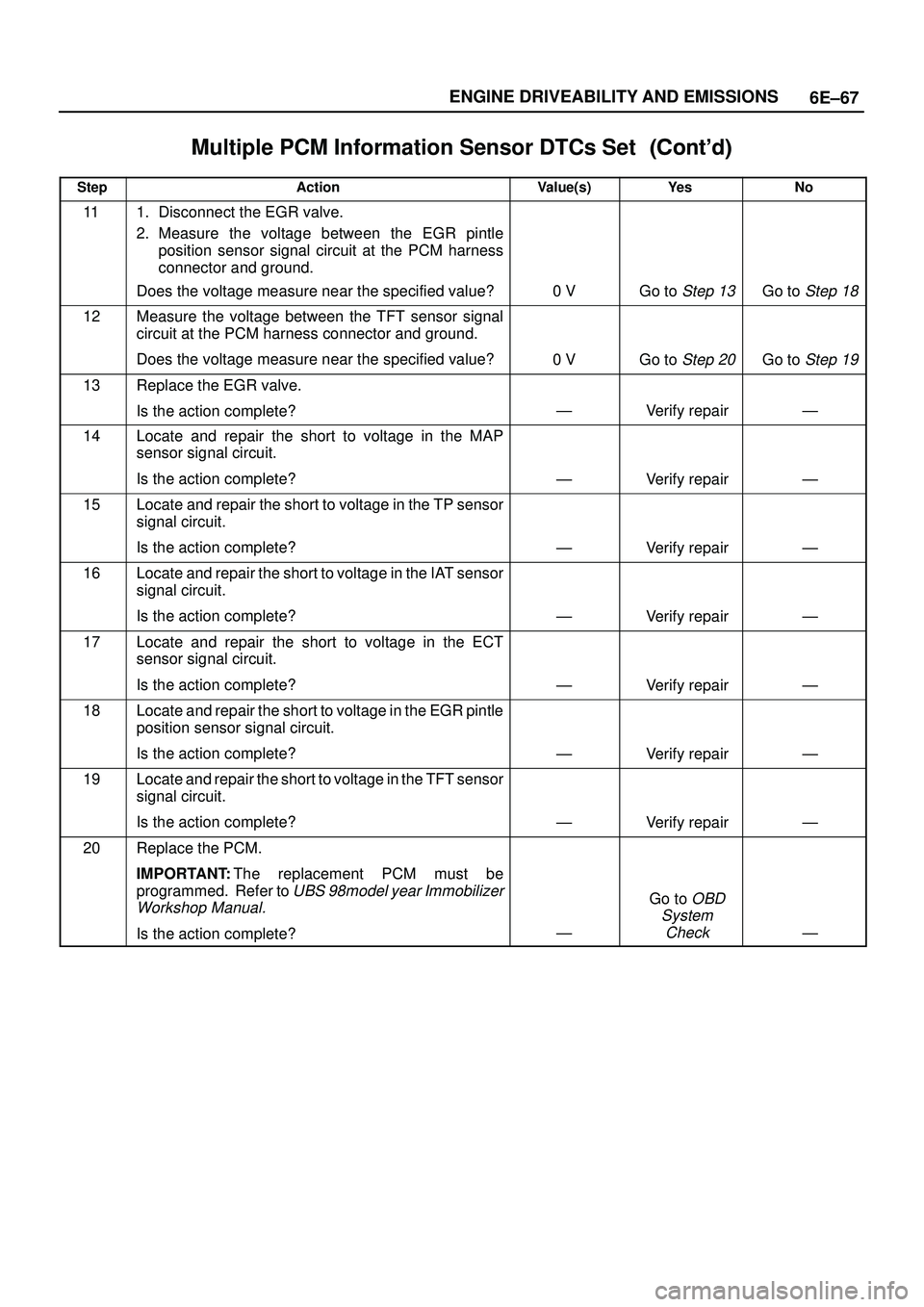
6E±67 ENGINE DRIVEABILITY AND EMISSIONS
Multiple PCM Information Sensor DTCs Set
StepNo Ye s Value(s) Action
111. Disconnect the EGR valve.
2. Measure the voltage between the EGR pintle
position sensor signal circuit at the PCM harness
connector and ground.
Does the voltage measure near the specified value?
0 VGo to Step 13Go to Step 18
12Measure the voltage between the TFT sensor signal
circuit at the PCM harness connector and ground.
Does the voltage measure near the specified value?
0 VGo to Step 20Go to Step 19
13Replace the EGR valve.
Is the action complete?
ÐVerify repairÐ
14Locate and repair the short to voltage in the MAP
sensor signal circuit.
Is the action complete?
ÐVerify repairÐ
15Locate and repair the short to voltage in the TP sensor
signal circuit.
Is the action complete?
ÐVerify repairÐ
16Locate and repair the short to voltage in the IAT sensor
signal circuit.
Is the action complete?
ÐVerify repairÐ
17Locate and repair the short to voltage in the ECT
sensor signal circuit.
Is the action complete?
ÐVerify repairÐ
18Locate and repair the short to voltage in the EGR pintle
position sensor signal circuit.
Is the action complete?
ÐVerify repairÐ
19Locate and repair the short to voltage in the TFT sensor
signal circuit.
Is the action complete?
ÐVerify repairÐ
20Replace the PCM.
IMPORTANT:The replacement PCM must be
programmed. Refer to
UBS 98model year Immobilizer
Workshop Manual.
Is the action complete?Ð
Go to OBD
System
Check
Ð