Page 433 of 3573
3E – 2 WHEELS AND TIRES
GENERAL DESCRIPTION
Replacement wheels or tires must be equivalent to
the originals in load capacity, specified dimension
and mounting configuration. Improper size or type
may affect bearing life, brake performance,
speedometer/odometer calibration, vehicle ground
clearance and tire clearance to the body and
chassis.All models are equipped with metric sized steel
belted radial tires. Correct tire pressures and
driving habits have an important influence on tire
life. Heavy cornering, excessively rapid
acceleration and unnecessary sharp braking
increase premature and uneven wear.
Page 434 of 3573
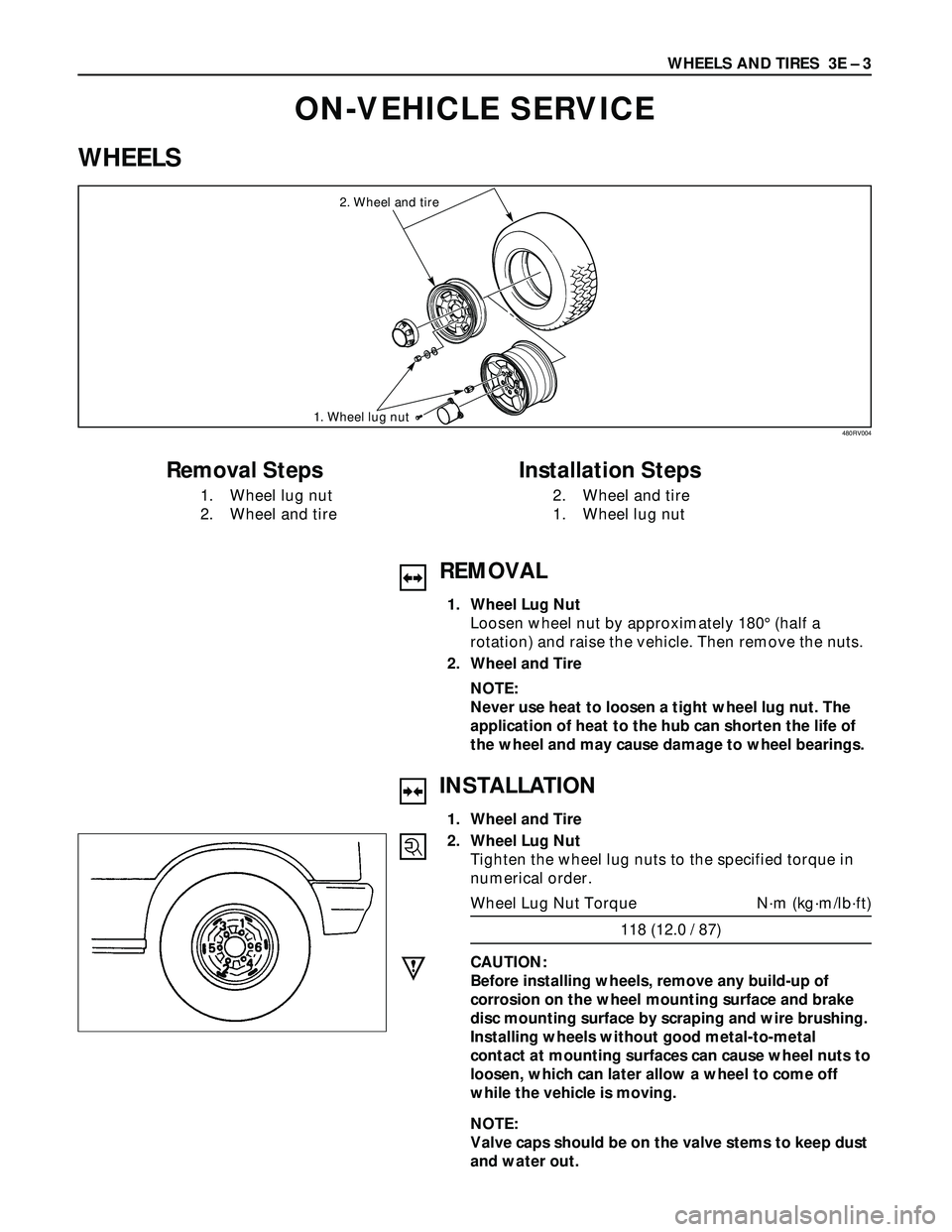
WHEELS AND TIRES 3E – 3
ON-VEHICLE SERVICE
WHEELS
2. Wheel and tire
1. Wheel lug nut
Removal Steps
1. Wheel lug nut
2. Wheel and tire
Installation Steps
2. Wheel and tire
1. Wheel lug nut
480RV004
REMOVAL
1. Wheel Lug Nut
Loosen wheel nut by approximately 180° (half a
rotation) and raise the vehicle. Then remove the nuts.
2. Wheel and Tire
NOTE:
Never use heat to loosen a tight wheel lug nut. The
application of heat to the hub can shorten the life of
the wheel and may cause damage to wheel bearings.
INSTALLATION
1. Wheel and Tire
2. Wheel Lug Nut
Tighten the wheel lug nuts to the specified torque in
numerical order.
Wheel Lug Nut Torque N·m (kg·m/lb·ft)
118 (12.0 / 87)
CAUTION:
Before installing wheels, remove any build-up of
corrosion on the wheel mounting surface and brake
disc mounting surface by scraping and wire brushing.
Installing wheels without good metal-to-metal
contact at mounting surfaces can cause wheel nuts to
loosen, which can later allow a wheel to come off
while the vehicle is moving.
NOTE:
Valve caps should be on the valve stems to keep dust
and water out.
Page 435 of 3573
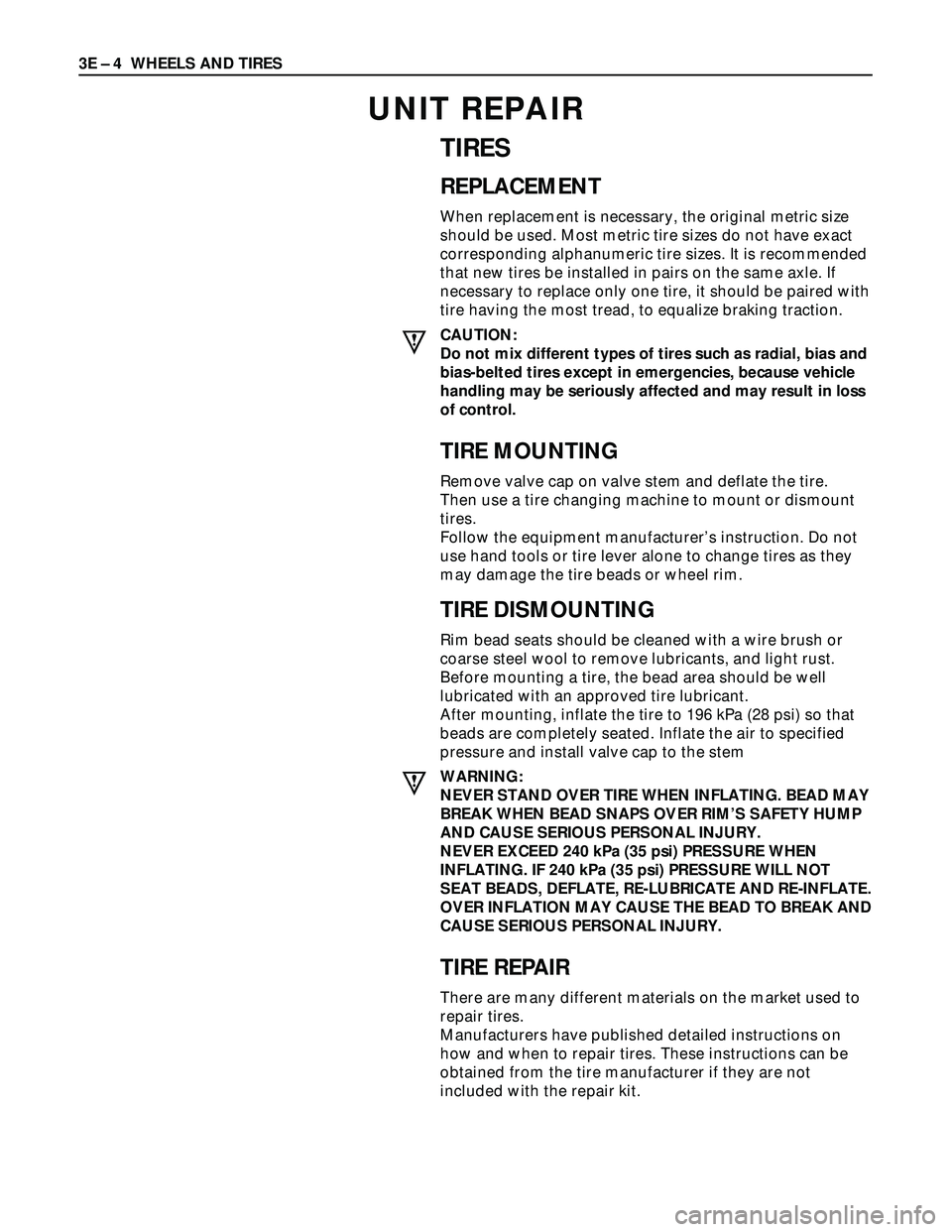
3E – 4 WHEELS AND TIRES
TIRES
REPLACEMENT
When replacement is necessary, the original metric size
should be used. Most metric tire sizes do not have exact
corresponding alphanumeric tire sizes. It is recommended
that new tires be installed in pairs on the same axle. If
necessary to replace only one tire, it should be paired with
tire having the most tread, to equalize braking traction.
CAUTION:
Do not mix different types of tires such as radial, bias and
bias-belted tires except in emergencies, because vehicle
handling may be seriously affected and may result in loss
of control.
TIRE MOUNTING
Remove valve cap on valve stem and deflate the tire.
Then use a tire changing machine to mount or dismount
tires.
Follow the equipment manufacturer’s instruction. Do not
use hand tools or tire lever alone to change tires as they
may damage the tire beads or wheel rim.
TIRE DISMOUNTING
Rim bead seats should be cleaned with a wire brush or
coarse steel wool to remove lubricants, and light rust.
Before mounting a tire, the bead area should be well
lubricated with an approved tire lubricant.
After mounting, inflate the tire to 196 kPa (28 psi) so that
beads are completely seated. Inflate the air to specified
pressure and install valve cap to the stem
WARNING:
NEVER STAND OVER TIRE WHEN INFLATING. BEAD MAY
BREAK WHEN BEAD SNAPS OVER RIM’S SAFETY HUMP
AND CAUSE SERIOUS PERSONAL INJURY.
NEVER EXCEED 240 kPa (35 psi) PRESSURE WHEN
INFLATING. IF 240 kPa (35 psi) PRESSURE WILL NOT
SEAT BEADS, DEFLATE, RE-LUBRICATE AND RE-INFLATE.
OVER INFLATION MAY CAUSE THE BEAD TO BREAK AND
CAUSE SERIOUS PERSONAL INJURY.
TIRE REPAIR
There are many different materials on the market used to
repair tires.
Manufacturers have published detailed instructions on
how and when to repair tires. These instructions can be
obtained from the tire manufacturer if they are not
included with the repair kit.
UNIT REPAIR
Page 436 of 3573
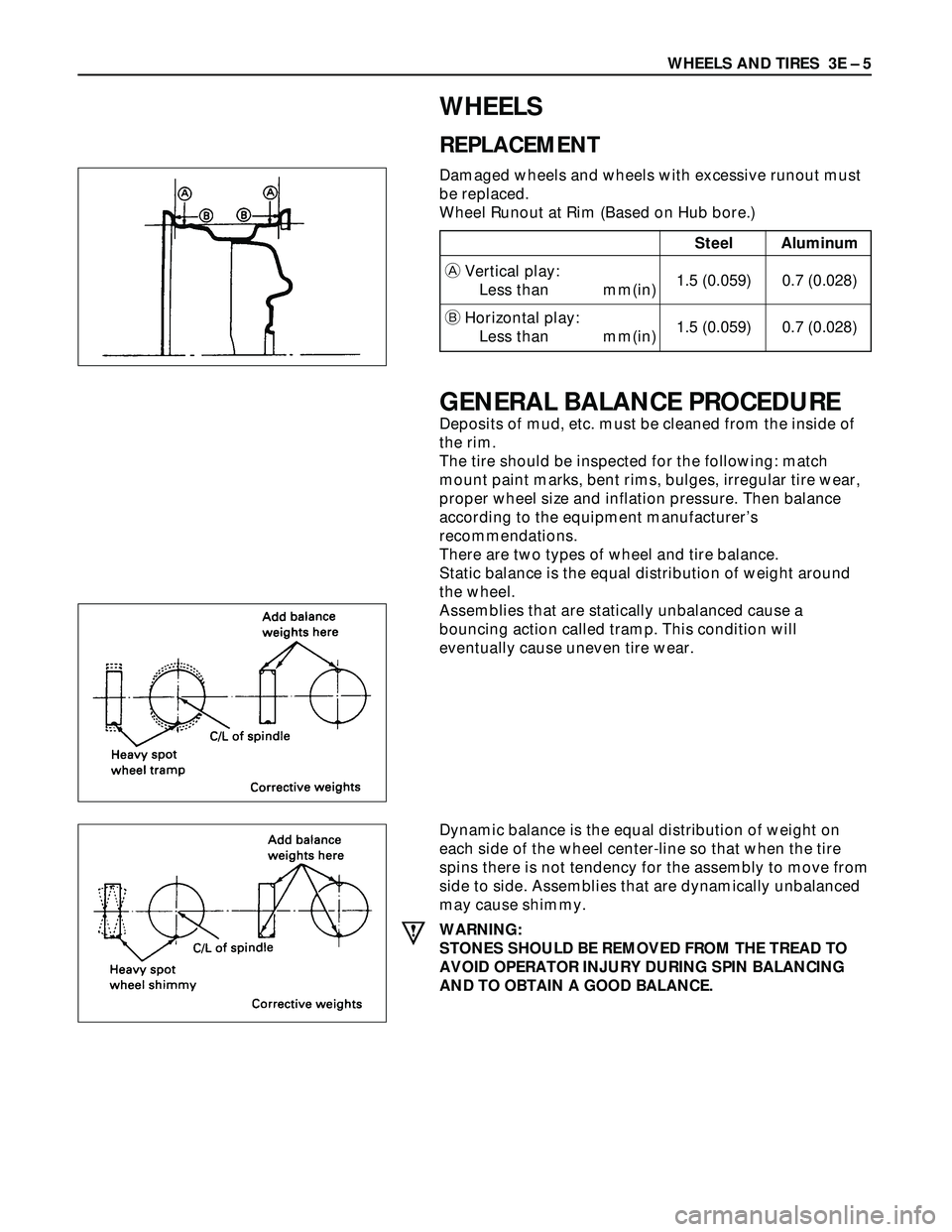
WHEELS AND TIRES 3E – 5
WHEELS
REPLACEMENT
Damaged wheels and wheels with excessive runout must
be replaced.
Wheel Runout at Rim (Based on Hub bore.)
GENERAL BALANCE PROCEDURE
Deposits of mud, etc. must be cleaned from the inside of
the rim.
The tire should be inspected for the following: match
mount paint marks, bent rims, bulges, irregular tire wear,
proper wheel size and inflation pressure. Then balance
according to the equipment manufacturer’s
recommendations.
There are two types of wheel and tire balance.
Static balance is the equal distribution of weight around
the wheel.
Assemblies that are statically unbalanced cause a
bouncing action called tramp. This condition will
eventually cause uneven tire wear.
Dynamic balance is the equal distribution of weight on
each side of the wheel center-line so that when the tire
spins there is not tendency for the assembly to move from
side to side. Assemblies that are dynamically unbalanced
may cause shimmy.
WARNING:
STONES SHOULD BE REMOVED FROM THE TREAD TO
AVOID OPERATOR INJURY DURING SPIN BALANCING
AND TO OBTAIN A GOOD BALANCE.
Steel Aluminum
AVertical play:
Less than mm(in)1.5 (0.059) 0.7 (0.028)
BHorizontal play:
Less than mm(in)1.5 (0.059) 0.7 (0.028)
Page 437 of 3573
3E – 6 WHEELS AND TIRES
BALANCING WHEEL AND TIRE
ON-VEHICLE BALANCING
On-Vehicle balancing methods vary with equipment and
tool manufacturers. Be sure to follow each manufacturer’s
instructions during balancing operation.
OFF-VEHICLE BALANCING
Most electronic off-vehicle balancers are more accurate
than the on-vehicle spin balancers. They are easy to use
and give a dynamic balance. Although they do not correct
for drum or disc unbalance (as on-vehicle spin balancing
does), they are very accurate.
Page 438 of 3573
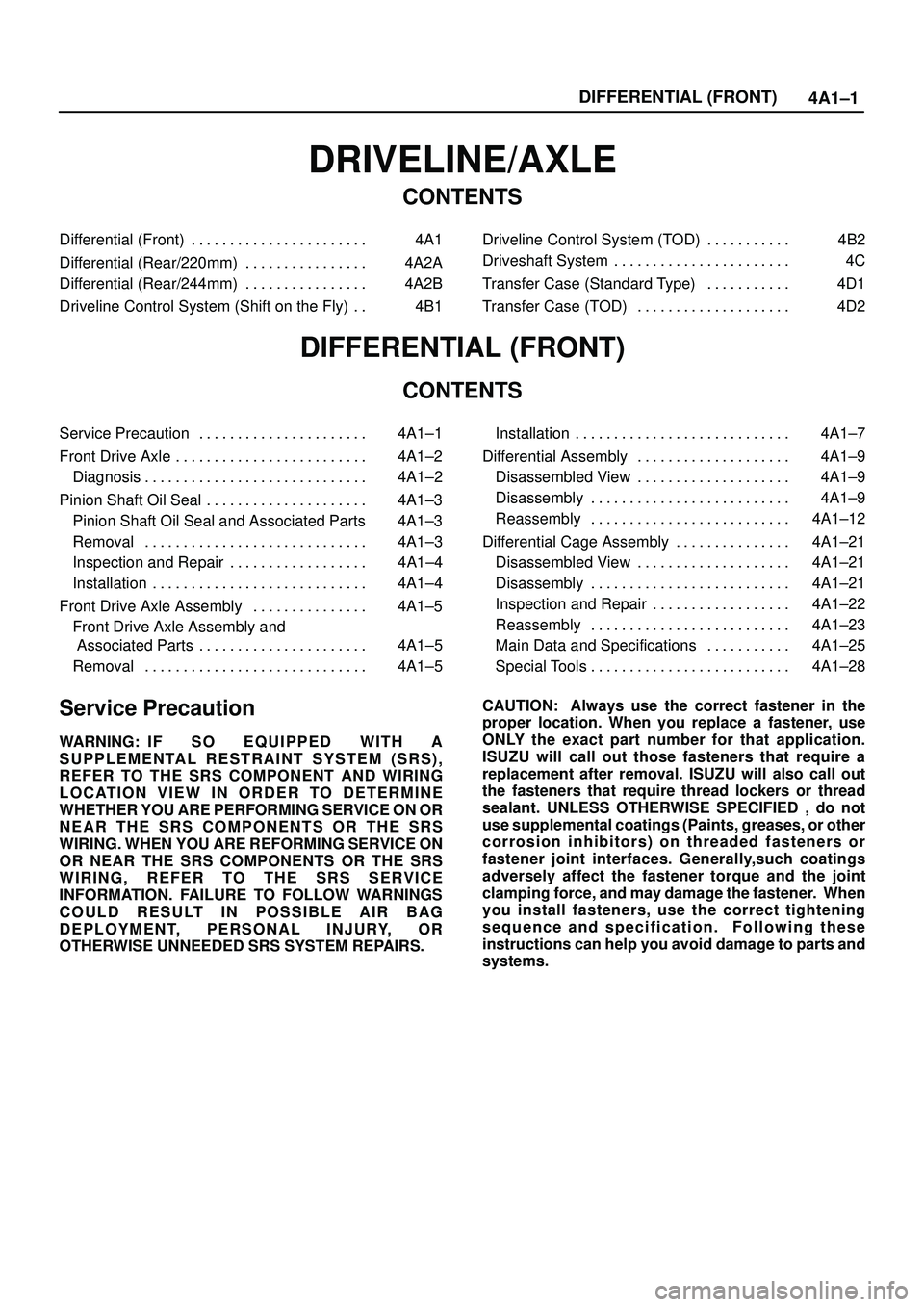
4A1±1 DIFFERENTIAL (FRONT)
DRIVELINE/AXLE
CONTENTS
Differential (Front) 4A1. . . . . . . . . . . . . . . . . . . . . . .
Differential (Rear/220mm) 4A2A. . . . . . . . . . . . . . . .
Differential (Rear/244mm) 4A2B. . . . . . . . . . . . . . . .
Driveline Control System (Shift on the Fly) 4B1. . Driveline Control System (TOD) 4B2. . . . . . . . . . .
Driveshaft System 4C. . . . . . . . . . . . . . . . . . . . . . .
Transfer Case (Standard Type) 4D1. . . . . . . . . . .
Transfer Case (TOD) 4D2. . . . . . . . . . . . . . . . . . . .
DIFFERENTIAL (FRONT)
CONTENTS
Service Precaution 4A1±1. . . . . . . . . . . . . . . . . . . . . .
Front Drive Axle 4A1±2. . . . . . . . . . . . . . . . . . . . . . . . .
Diagnosis 4A1±2. . . . . . . . . . . . . . . . . . . . . . . . . . . . .
Pinion Shaft Oil Seal 4A1±3. . . . . . . . . . . . . . . . . . . . .
Pinion Shaft Oil Seal and Associated Parts 4A1±3
Removal 4A1±3. . . . . . . . . . . . . . . . . . . . . . . . . . . . .
Inspection and Repair 4A1±4. . . . . . . . . . . . . . . . . .
Installation 4A1±4. . . . . . . . . . . . . . . . . . . . . . . . . . . .
Front Drive Axle Assembly 4A1±5. . . . . . . . . . . . . . .
Front Drive Axle Assembly and
Associated Parts 4A1±5. . . . . . . . . . . . . . . . . . . . . .
Removal 4A1±5. . . . . . . . . . . . . . . . . . . . . . . . . . . . . Installation 4A1±7. . . . . . . . . . . . . . . . . . . . . . . . . . . .
Differential Assembly 4A1±9. . . . . . . . . . . . . . . . . . . .
Disassembled View 4A1±9. . . . . . . . . . . . . . . . . . . .
Disassembly 4A1±9. . . . . . . . . . . . . . . . . . . . . . . . . .
Reassembly 4A1±12. . . . . . . . . . . . . . . . . . . . . . . . . .
Differential Cage Assembly 4A1±21. . . . . . . . . . . . . . .
Disassembled View 4A1±21. . . . . . . . . . . . . . . . . . . .
Disassembly 4A1±21. . . . . . . . . . . . . . . . . . . . . . . . . .
Inspection and Repair 4A1±22. . . . . . . . . . . . . . . . . .
Reassembly 4A1±23. . . . . . . . . . . . . . . . . . . . . . . . . .
Main Data and Specifications 4A1±25. . . . . . . . . . .
Special Tools 4A1±28. . . . . . . . . . . . . . . . . . . . . . . . . .
Service Precaution
WARNING: I F S O E Q U IPPED WITH A
SUPPLEMENTAL RESTRAINT SYSTEM (SRS),
REFER TO THE SRS COMPONENT AND WIRING
LOCATION VIEW IN ORDER TO DETERMINE
WHETHER YOU ARE PERFORMING SERVICE ON OR
NEAR THE SRS COMPONENTS OR THE SRS
WIRING. WHEN YOU ARE REFORMING SERVICE ON
OR NEAR THE SRS COMPONENTS OR THE SRS
WIRING, REFER TO THE SRS SERVICE
INFORMATION. FAILURE TO FOLLOW WARNINGS
COULD RESULT IN POSSIBLE AIR BAG
DEPLOYMENT, PERSONAL INJURY, OR
OTHERWISE UNNEEDED SRS SYSTEM REPAIRS.CAUTION: Always use the correct fastener in the
proper location. When you replace a fastener, use
ONLY the exact part number for that application.
ISUZU will call out those fasteners that require a
replacement after removal. ISUZU will also call out
the fasteners that require thread lockers or thread
sealant. UNLESS OTHERWISE SPECIFIED , do not
use supplemental coatings (Paints, greases, or other
corrosion inhibitors) on threaded fasteners or
fastener joint interfaces. Generally,such coatings
adversely affect the fastener torque and the joint
clamping force, and may damage the fastener. When
you install fasteners, use the correct tightening
sequence and specification. Following these
instructions can help you avoid damage to parts and
systems.
Page 439 of 3573
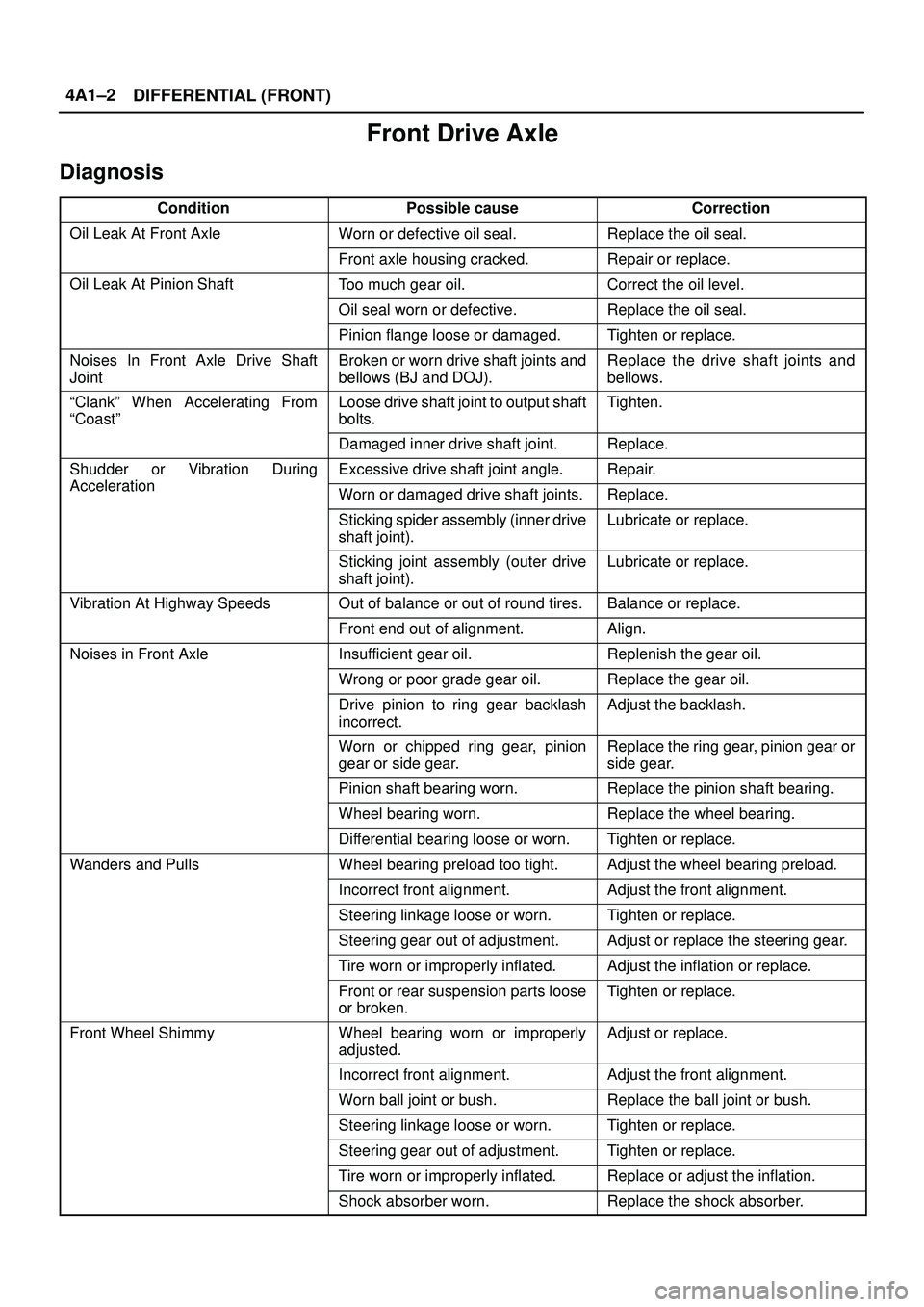
DIFFERENTIAL (FRONT) 4A1±2
Front Drive Axle
Diagnosis
ConditionPossible causeCorrection
Oil Leak At Front AxleWorn or defective oil seal.Replace the oil seal.
Front axle housing cracked.Repair or replace.
Oil Leak At Pinion ShaftToo much gear oil.Correct the oil level.
Oil seal worn or defective.Replace the oil seal.
Pinion flange loose or damaged.Tighten or replace.
Noises In Front Axle Drive Shaft
JointBroken or worn drive shaft joints and
bellows (BJ and DOJ).Replace the drive shaft joints and
bellows.
ªClankº When Accelerating From
ªCoastºLoose drive shaft joint to output shaft
bolts.Tighten.
Damaged inner drive shaft joint.Replace.
Shudder or Vibration During
Acceleration
Excessive drive shaft joint angle.Repair.
AccelerationWorn or damaged drive shaft joints.Replace.
Sticking spider assembly (inner drive
shaft joint).Lubricate or replace.
Sticking joint assembly (outer drive
shaft joint).Lubricate or replace.
Vibration At Highway SpeedsOut of balance or out of round tires.Balance or replace.
Front end out of alignment.Align.
Noises in Front AxleInsufficient gear oil.Replenish the gear oil.
Wrong or poor grade gear oil.Replace the gear oil.
Drive pinion to ring gear backlash
incorrect.Adjust the backlash.
Worn or chipped ring gear, pinion
gear or side gear.Replace the ring gear, pinion gear or
side gear.
Pinion shaft bearing worn.Replace the pinion shaft bearing.
Wheel bearing worn.Replace the wheel bearing.
Differential bearing loose or worn.Tighten or replace.
Wanders and PullsWheel bearing preload too tight.Adjust the wheel bearing preload.
Incorrect front alignment.Adjust the front alignment.
Steering linkage loose or worn.Tighten or replace.
Steering gear out of adjustment.Adjust or replace the steering gear.
Tire worn or improperly inflated.Adjust the inflation or replace.
Front or rear suspension parts loose
or broken.Tighten or replace.
Front Wheel ShimmyWheel bearing worn or improperly
adjusted.Adjust or replace.
Incorrect front alignment.Adjust the front alignment.
Worn ball joint or bush.Replace the ball joint or bush.
Steering linkage loose or worn.Tighten or replace.
Steering gear out of adjustment.Tighten or replace.
Tire worn or improperly inflated.Replace or adjust the inflation.
Shock absorber worn.Replace the shock absorber.
Page 440 of 3573
4A1±3 DIFFERENTIAL (FRONT)
Pinion Shaft Oil Seal
Pinion Shaft Oil Seal and Associated Parts
415RW015
Legend
(1) Flange Nut
(2) Flange(3) Oil Seal
(4) Outer Bearing
(5) Collapsible Spacer
Removal
1. Raise the vehicle and support it at the frame.
The hoist must remain under the front axle housing.
2. Drain the front axle oil by loosening the drain plug(1).
412RS001