Page 1777 of 3573
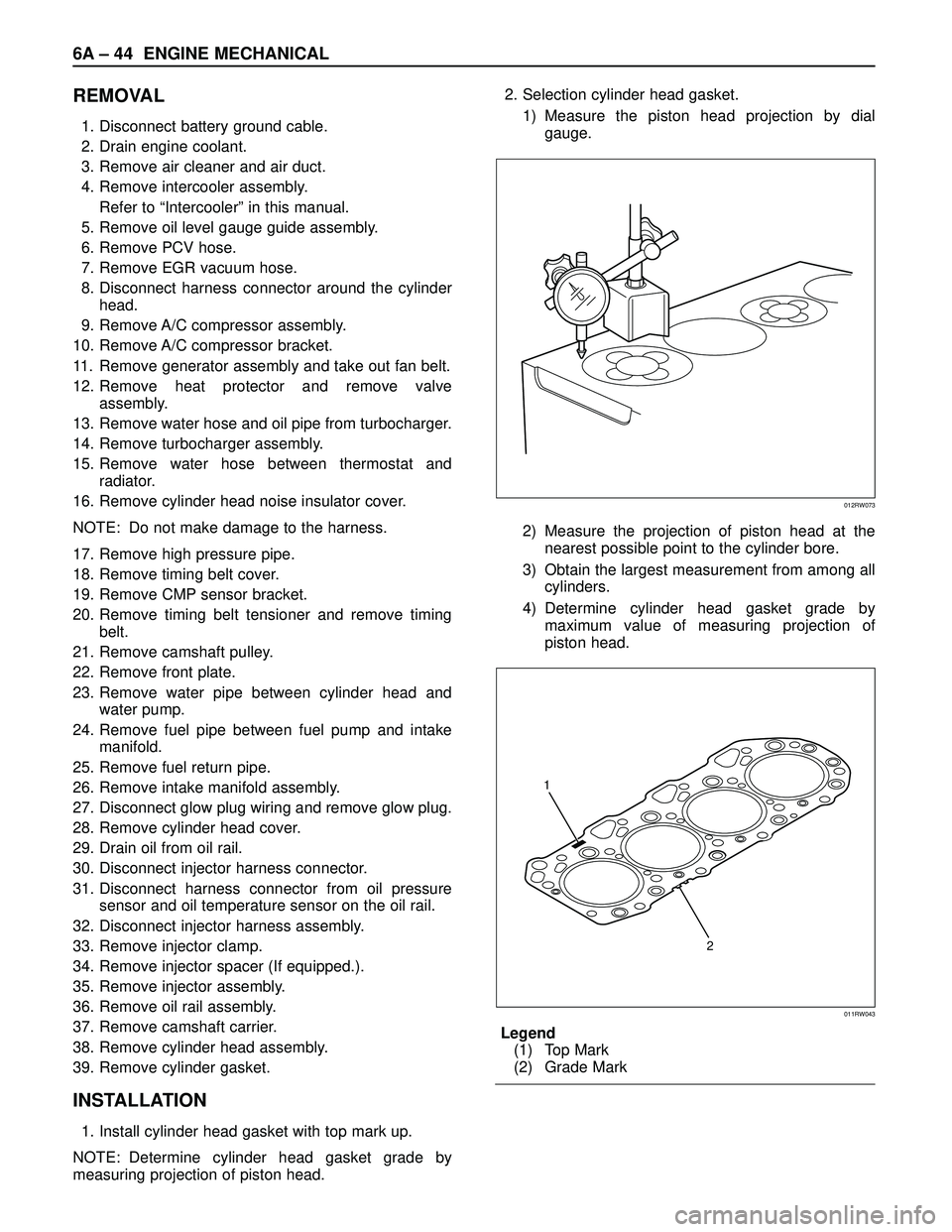
6A – 44 ENGINE MECHANICAL
REMOVAL
1. Disconnect battery ground cable.
2. Drain engine coolant.
3. Remove air cleaner and air duct.
4. Remove intercooler assembly.
Refer to “Intercooler” in this manual.
5. Remove oil level gauge guide assembly.
6. Remove PCV hose.
7. Remove EGR vacuum hose.
8. Disconnect harness connector around the cylinder
head.
9. Remove A/C compressor assembly.
10. Remove A/C compressor bracket.
11. Remove generator assembly and take out fan belt.
12. Remove heat protector and remove valve
assembly.
13. Remove water hose and oil pipe from turbocharger.
14. Remove turbocharger assembly.
15. Remove water hose between thermostat and
radiator.
16. Remove cylinder head noise insulator cover.
NOTE: Do not make damage to the harness.
17. Remove high pressure pipe.
18. Remove timing belt cover.
19. Remove CMP sensor bracket.
20. Remove timing belt tensioner and remove timing
belt.
21. Remove camshaft pulley.
22. Remove front plate.
23. Remove water pipe between cylinder head and
water pump.
24. Remove fuel pipe between fuel pump and intake
manifold.
25. Remove fuel return pipe.
26. Remove intake manifold assembly.
27. Disconnect glow plug wiring and remove glow plug.
28. Remove cylinder head cover.
29. Drain oil from oil rail.
30. Disconnect injector harness connector.
31. Disconnect harness connector from oil pressure
sensor and oil temperature sensor on the oil rail.
32. Disconnect injector harness assembly.
33. Remove injector clamp.
34. Remove injector spacer (If equipped.).
35. Remove injector assembly.
36. Remove oil rail assembly.
37. Remove camshaft carrier.
38. Remove cylinder head assembly.
39. Remove cylinder gasket.
INSTALLATION
1. Install cylinder head gasket with top mark up.
NOTE: Determine cylinder head gasket grade by
measuring projection of piston head.2. Selection cylinder head gasket.
1) Measure the piston head projection by dial
gauge.
2) Measure the projection of piston head at the
nearest possible point to the cylinder bore.
3) Obtain the largest measurement from among all
cylinders.
4) Determine cylinder head gasket grade by
maximum value of measuring projection of
piston head.
Legend
(1) Top Mark
(2) Grade Mark
012RW073
2 1
011RW043
Page 1778 of 3573
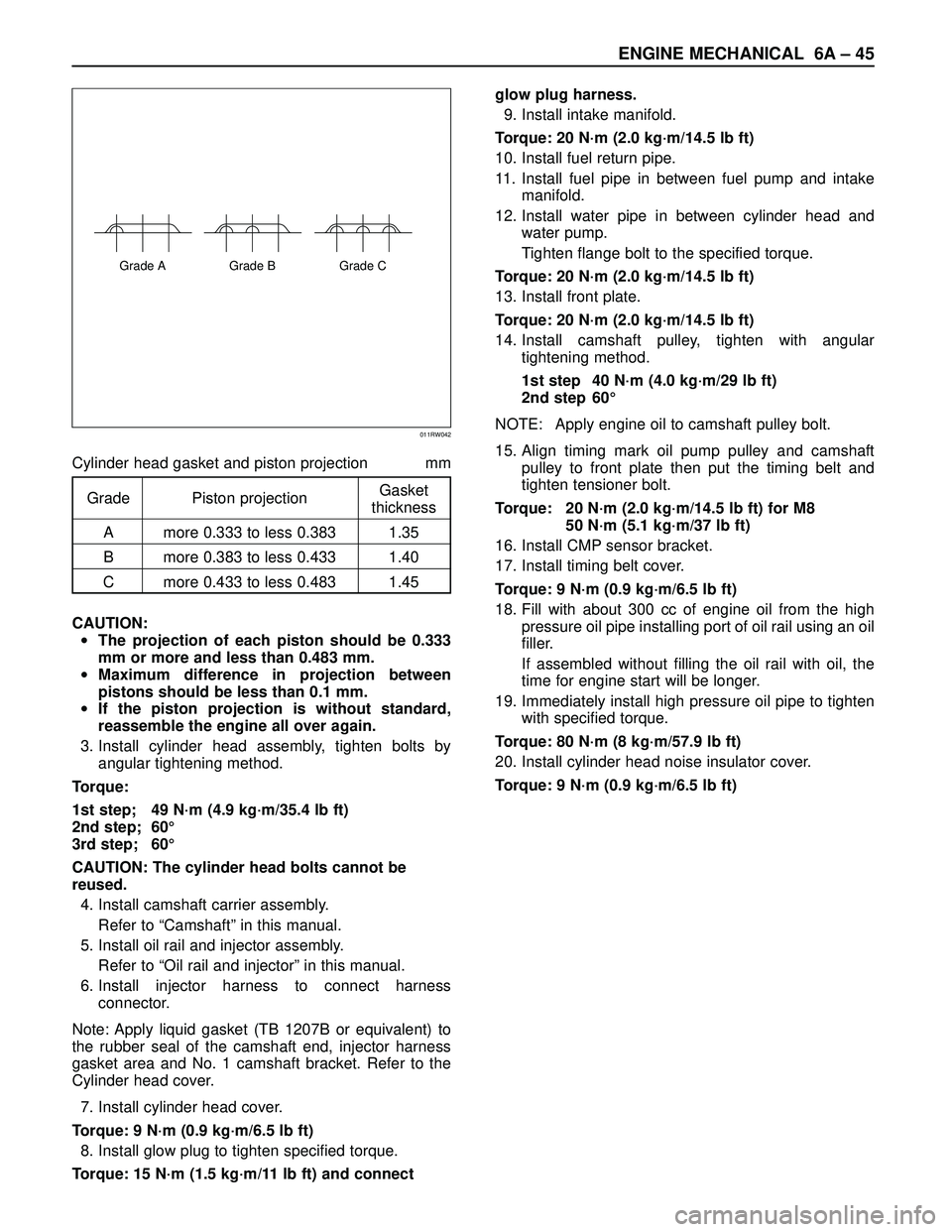
ENGINE MECHANICAL 6A – 45
Cylinder head gasket and piston projection mm
CAUTION:
•The projection of each piston should be 0.333
mm or more and less than 0.483 mm.
•Maximum difference in projection between
pistons should be less than 0.1 mm.
•If the piston projection is without standard,
reassemble the engine all over again.
3. Install cylinder head assembly, tighten bolts by
angular tightening method.
Torque:
1st step; 49 N·m (4.9 kg·m/35.4 lb ft)
2nd step; 60°
3rd step; 60°
CAUTION: The cylinder head bolts cannot be
reused.
4. Install camshaft carrier assembly.
Refer to “Camshaft” in this manual.
5. Install oil rail and injector assembly.
Refer to “Oil rail and injector” in this manual.
6. Install injector harness to connect harness
connector.
Note: Apply liquid gasket (TB 1207B or equivalent) to
the rubber seal of the camshaft end, injector harness
gasket area and No. 1 camshaft bracket. Refer to the
Cylinder head cover.
7. Install cylinder head cover.
Torque: 9 N·m (0.9 kg·m/6.5 lb ft)
8. Install glow plug to tighten specified torque.
Torque: 15 N·m (1.5 kg·m/11 lb ft) and connectglow plug harness.
9. Install intake manifold.
Torque: 20 N·m (2.0 kg·m/14.5 lb ft)
10. Install fuel return pipe.
11. Install fuel pipe in between fuel pump and intake
manifold.
12. Install water pipe in between cylinder head and
water pump.
Tighten flange bolt to the specified torque.
Torque: 20 N·m (2.0 kg·m/14.5 lb ft)
13. Install front plate.
Torque: 20 N·m (2.0 kg·m/14.5 lb ft)
14. Install camshaft pulley, tighten with angular
tightening method.
1st step 40 N·m (4.0 kg·m/29 lb ft)
2nd step 60°
NOTE: Apply engine oil to camshaft pulley bolt.
15. Align timing mark oil pump pulley and camshaft
pulley to front plate then put the timing belt and
tighten tensioner bolt.
Torque: 20 N·m (2.0 kg·m/14.5 lb ft) for M8
50 N·m (5.1 kg·m/37 lb ft)
16. Install CMP sensor bracket.
17. Install timing belt cover.
Torque: 9 N·m (0.9 kg·m/6.5 lb ft)
18. Fill with about 300 cc of engine oil from the high
pressure oil pipe installing port of oil rail using an oil
filler.
If assembled without filling the oil rail with oil, the
time for engine start will be longer.
19. Immediately install high pressure oil pipe to tighten
with specified torque.
Torque: 80 N·m (8 kg·m/57.9 lb ft)
20. Install cylinder head noise insulator cover.
Torque: 9 N·m (0.9 kg·m/6.5 lb ft)
Grade A Grade B Grade C
011RW042
Grade Piston projectionGasket
thickness
A more 0.333 to less 0.383 1.35
B more 0.383 to less 0.433 1.40
C more 0.433 to less 0.483 1.45
Page 1779 of 3573
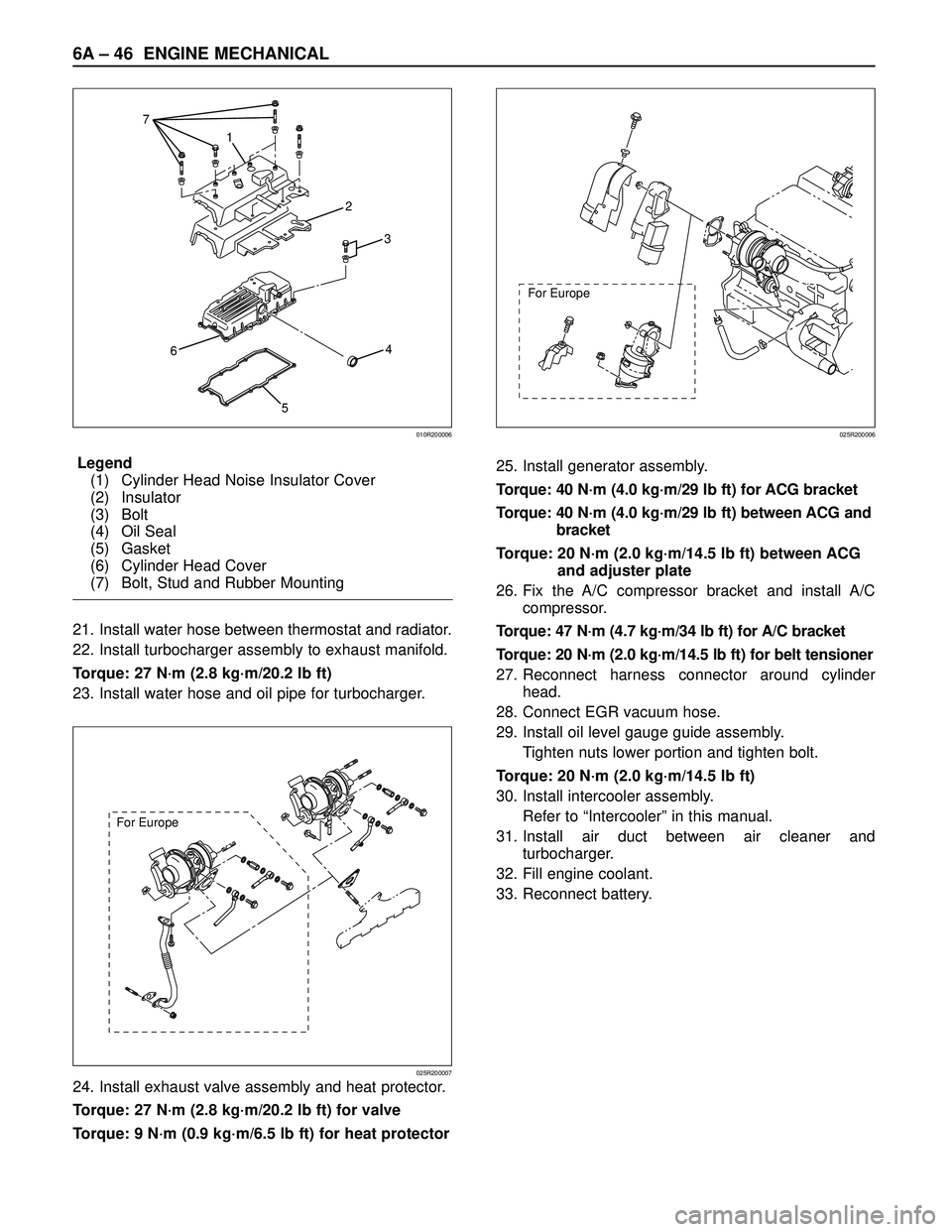
6A – 46 ENGINE MECHANICAL
Legend
(1) Cylinder Head Noise Insulator Cover
(2) Insulator
(3) Bolt
(4) Oil Seal
(5) Gasket
(6) Cylinder Head Cover
(7) Bolt, Stud and Rubber Mounting
21. Install water hose between thermostat and radiator.
22. Install turbocharger assembly to exhaust manifold.
Torque: 27 N·m (2.8 kg·m/20.2 lb ft)
23. Install water hose and oil pipe for turbocharger.
24. Install exhaust valve assembly and heat protector.
Torque: 27 N·m (2.8 kg·m/20.2 lb ft) for valve
Torque: 9 N·m (0.9 kg·m/6.5 lb ft) for heat protector25. Install generator assembly.
Torque: 40 N·m (4.0 kg·m/29 lb ft) for ACG bracket
Torque: 40 N·m (4.0 kg·m/29 lb ft) between ACG and
bracket
Torque: 20 N·m (2.0 kg·m/14.5 lb ft) between ACG
and adjuster plate
26. Fix the A/C compressor bracket and install A/C
compressor.
Torque: 47 N·m (4.7 kg·m/34 lb ft) for A/C bracket
Torque: 20 N·m (2.0 kg·m/14.5 lb ft) for belt tensioner
27. Reconnect harness connector around cylinder
head.
28. Connect EGR vacuum hose.
29. Install oil level gauge guide assembly.
Tighten nuts lower portion and tighten bolt.
Torque: 20 N·m (2.0 kg·m/14.5 lb ft)
30. Install intercooler assembly.
Refer to “Intercooler” in this manual.
31. Install air duct between air cleaner and
turbocharger.
32. Fill engine coolant.
33. Reconnect battery.
For Europe
025R200007
For Europe
025R200006
1 7
2
3
4
5 6
010R200006
Page 1780 of 3573
ENGINE MECHANICAL 6A – 47
CAMSHAFT
2 1
6With
spacer type
Without
spacer type
13 14
8
12
11
109
3
4
7
5
012R200004
Legend
(1) Nut and Washer
(2) Injector Clamp
(3) Nut
(4) Bolt
(5) Oil Rail Assembly
(6) Spacer (If equipped) and Bolt
(7) Injector Assembly(8) Camshaft
(9) Camshaft Carrier
(10) Plug
(11) Oil Seal
(12) Camshaft Bracket
(13) Gasket
(14) Gasket
Page 1781 of 3573
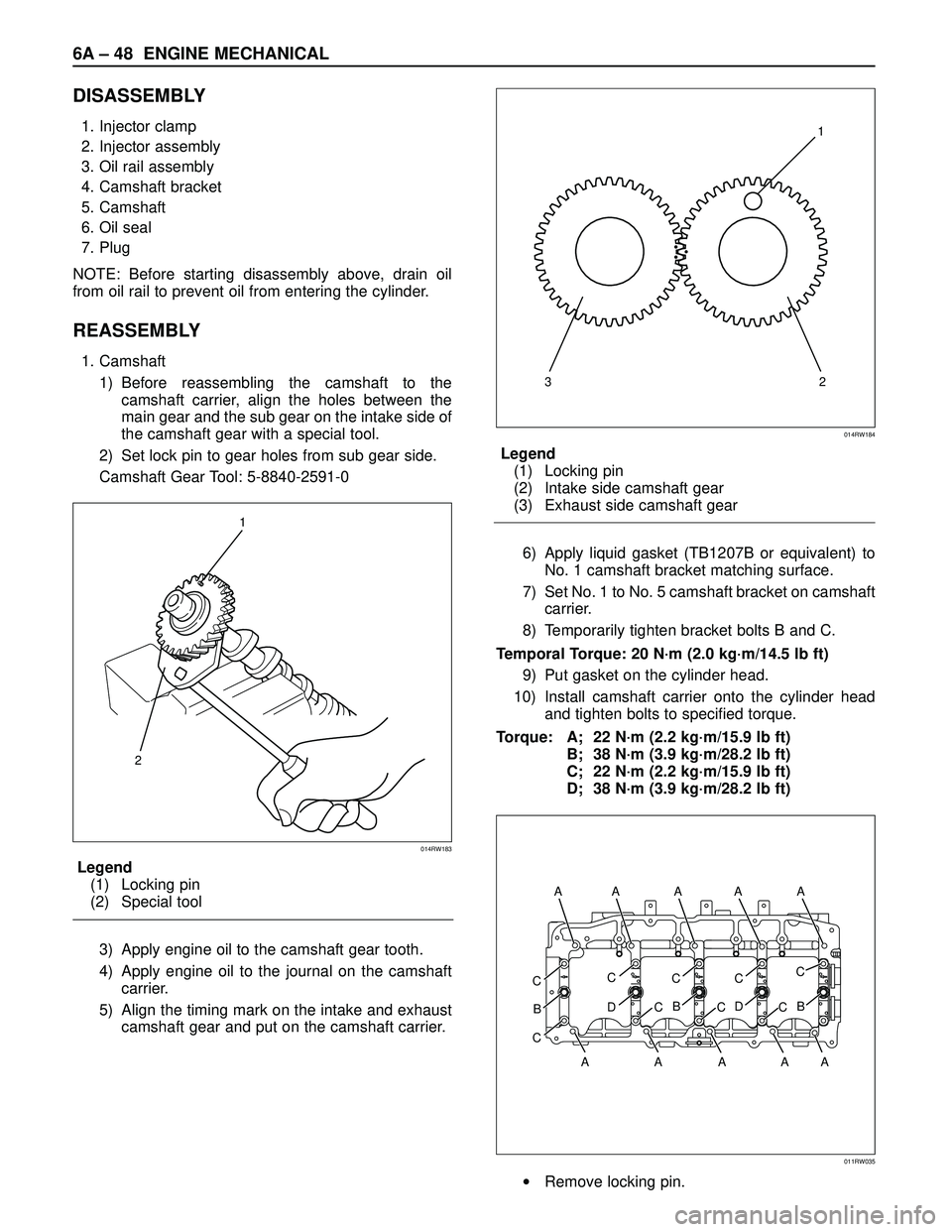
6A – 48 ENGINE MECHANICAL
DISASSEMBLY
1. Injector clamp
2. Injector assembly
3. Oil rail assembly
4. Camshaft bracket
5. Camshaft
6. Oil seal
7. Plug
NOTE: Before starting disassembly above, drain oil
from oil rail to prevent oil from entering the cylinder.
REASSEMBLY
1. Camshaft
1) Before reassembling the camshaft to the
camshaft carrier, align the holes between the
main gear and the sub gear on the intake side of
the camshaft gear with a special tool.
2) Set lock pin to gear holes from sub gear side.
Camshaft Gear Tool: 5-8840-2591-0
Legend
(1) Locking pin
(2) Special tool
3) Apply engine oil to the camshaft gear tooth.
4) Apply engine oil to the journal on the camshaft
carrier.
5) Align the timing mark on the intake and exhaust
camshaft gear and put on the camshaft carrier.Legend
(1) Locking pin
(2) Intake side camshaft gear
(3) Exhaust side camshaft gear
6) Apply liquid gasket (TB1207B or equivalent) to
No. 1 camshaft bracket matching surface.
7) Set No. 1 to No. 5 camshaft bracket on camshaft
carrier.
8) Temporarily tighten bracket bolts B and C.
Temporal Torque: 20 N·m (2.0 kg·m/14.5 lb ft)
9) Put gasket on the cylinder head.
10) Install camshaft carrier onto the cylinder head
and tighten bolts to specified torque.
Torque: A; 22 N·m (2.2 kg·m/15.9 lb ft)
B; 38 N·m (3.9 kg·m/28.2 lb ft)
C; 22 N·m (2.2 kg·m/15.9 lb ft)
D; 38 N·m (3.9 kg·m/28.2 lb ft)
•Remove locking pin.
1
2
014RW183
321
014RW184
CC
D
B
CC
B
CC
D
CC
B
C
A AA A A A
AAAA
011RW035
Page 1782 of 3573
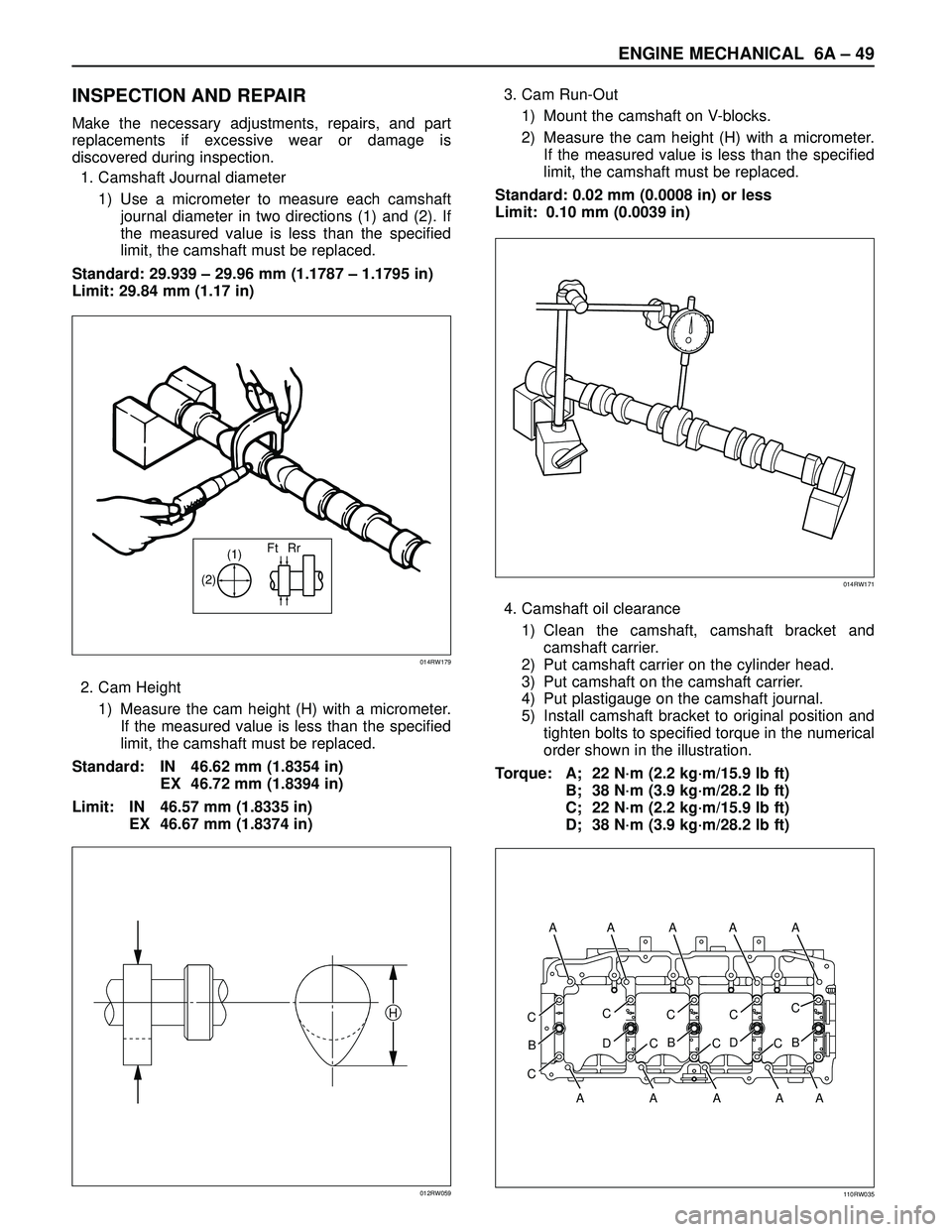
ENGINE MECHANICAL 6A – 49
INSPECTION AND REPAIR
Make the necessary adjustments, repairs, and part
replacements if excessive wear or damage is
discovered during inspection.
1. Camshaft Journal diameter
1) Use a micrometer to measure each camshaft
journal diameter in two directions (1) and (2). If
the measured value is less than the specified
limit, the camshaft must be replaced.
Standard: 29.939 – 29.96 mm (1.1787 – 1.1795 in)
Limit: 29.84 mm (1.17 in)
2. Cam Height
1) Measure the cam height (H) with a micrometer.
If the measured value is less than the specified
limit, the camshaft must be replaced.
Standard: IN 46.62 mm (1.8354 in)
EX 46.72 mm (1.8394 in)
Limit: IN 46.57 mm (1.8335 in)
EX 46.67 mm (1.8374 in)3. Cam Run-Out
1) Mount the camshaft on V-blocks.
2) Measure the cam height (H) with a micrometer.
If the measured value is less than the specified
limit, the camshaft must be replaced.
Standard: 0.02 mm (0.0008 in) or less
Limit: 0.10 mm (0.0039 in)
4. Camshaft oil clearance
1) Clean the camshaft, camshaft bracket and
camshaft carrier.
2) Put camshaft carrier on the cylinder head.
3) Put camshaft on the camshaft carrier.
4) Put plastigauge on the camshaft journal.
5) Install camshaft bracket to original position and
tighten bolts to specified torque in the numerical
order shown in the illustration.
Torque: A; 22 N·m (2.2 kg·m/15.9 lb ft)
B; 38 N·m (3.9 kg·m/28.2 lb ft)
C; 22 N·m (2.2 kg·m/15.9 lb ft)
D; 38 N·m (3.9 kg·m/28.2 lb ft)
(1)Ft Rr
(2)
014RW179
H
012RW059
014RW171
CC
D
B
CC
B
CC
D
CC
B
C
A AA A A A
AAAA
110RW035
Page 1783 of 3573
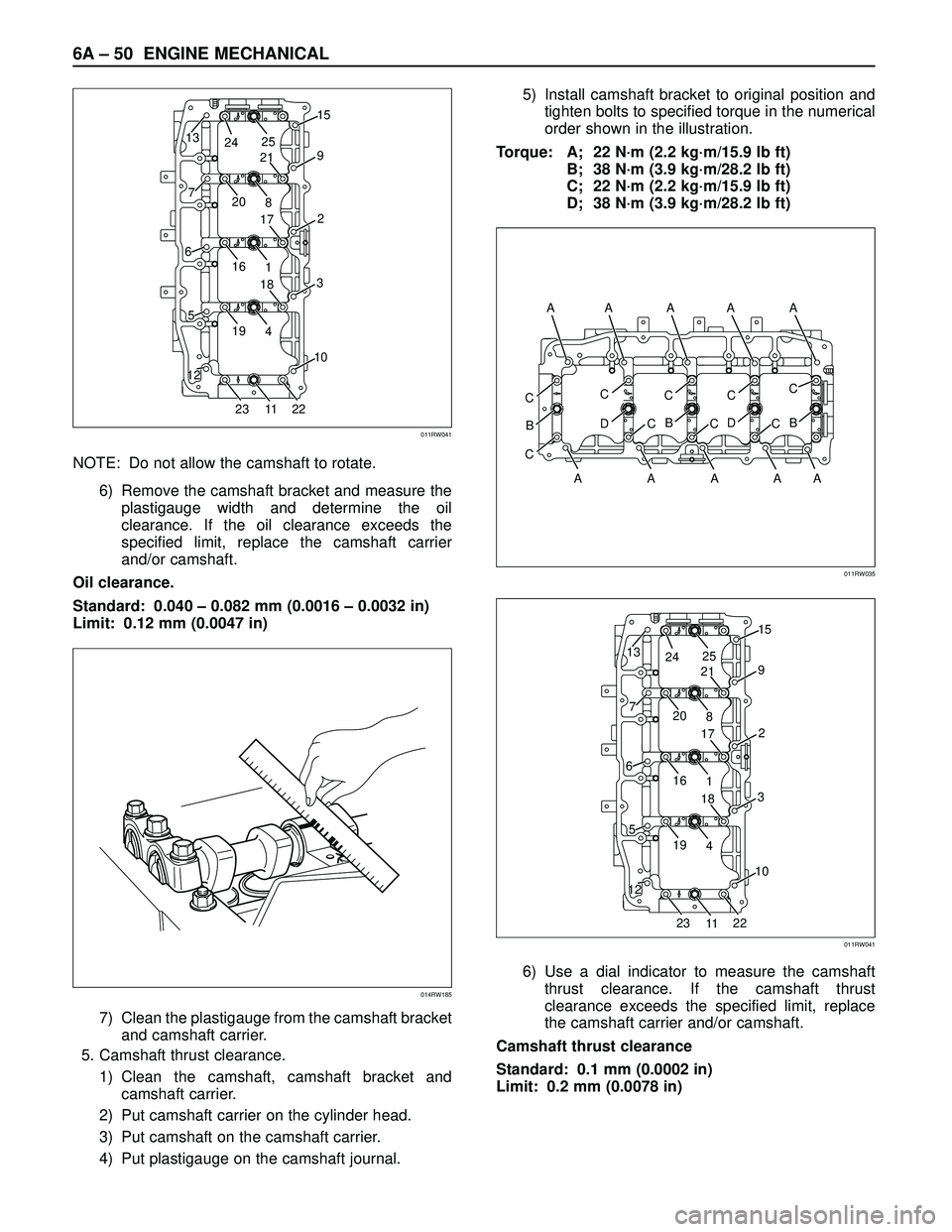
6A – 50 ENGINE MECHANICAL
NOTE: Do not allow the camshaft to rotate.
6) Remove the camshaft bracket and measure the
plastigauge width and determine the oil
clearance. If the oil clearance exceeds the
specified limit, replace the camshaft carrier
and/or camshaft.
Oil clearance.
Standard: 0.040 – 0.082 mm (0.0016 – 0.0032 in)
Limit: 0.12 mm (0.0047 in)
7) Clean the plastigauge from the camshaft bracket
and camshaft carrier.
5. Camshaft thrust clearance.
1) Clean the camshaft, camshaft bracket and
camshaft carrier.
2) Put camshaft carrier on the cylinder head.
3) Put camshaft on the camshaft carrier.
4) Put plastigauge on the camshaft journal.5) Install camshaft bracket to original position and
tighten bolts to specified torque in the numerical
order shown in the illustration.
Torque: A; 22 N·m (2.2 kg·m/15.9 lb ft)
B; 38 N·m (3.9 kg·m/28.2 lb ft)
C; 22 N·m (2.2 kg·m/15.9 lb ft)
D; 38 N·m (3.9 kg·m/28.2 lb ft)
6) Use a dial indicator to measure the camshaft
thrust clearance. If the camshaft thrust
clearance exceeds the specified limit, replace
the camshaft carrier and/or camshaft.
Camshaft thrust clearance
Standard: 0.1 mm (0.0002 in)
Limit: 0.2 mm (0.0078 in)
13
7
6
5
1215
2
3
10
9
20
8
19
2322
4
161
11 25
24
21
17
18
011RW041
014RW185
CC
D
B
CC
B
CC
D
CC
B
C
A AA A A A
AAAA
011RW035
13
7
6
5
1215
2
3
10
9
20
8
19
2322
4
161
11 25
24
21
17
18
011RW041
Page 1784 of 3573
ENGINE MECHANICAL 6A – 51
014RW001