Page 1673 of 3573
FUEL SYSTEM 6C Ð 7
ON-VEHICLE SERVICE
FUEL FILTER ASSEMBLY
REMOVAL
Preparation: Disconnect battery ground cable.
1. Fuel Filler Cap
2. Lead Switch Harness Connecter
3. Fuel Hose
·Disconnect fuel hose from filter body.
Plug the hose ends to prevent fuel spillage.
4. Remove the Bolt on Fuel Filter Bracket.
5. Fuel Filter Assembly
INSTALLATION
5. Fuel Filter Assembly
·Install the filter
4. Tighten the Fuel Filter Bracket Fixing Bolt.
3. Fuel Hose
·Connect hoses to filter body.
2. Lead Switch Harness Connecter
1. Fuel Filler Cap
·Connect the battery ground cable.
·Feed fuel to the injection pump by weans of the
priming, and bleed the fuel system.
Page 1674 of 3573
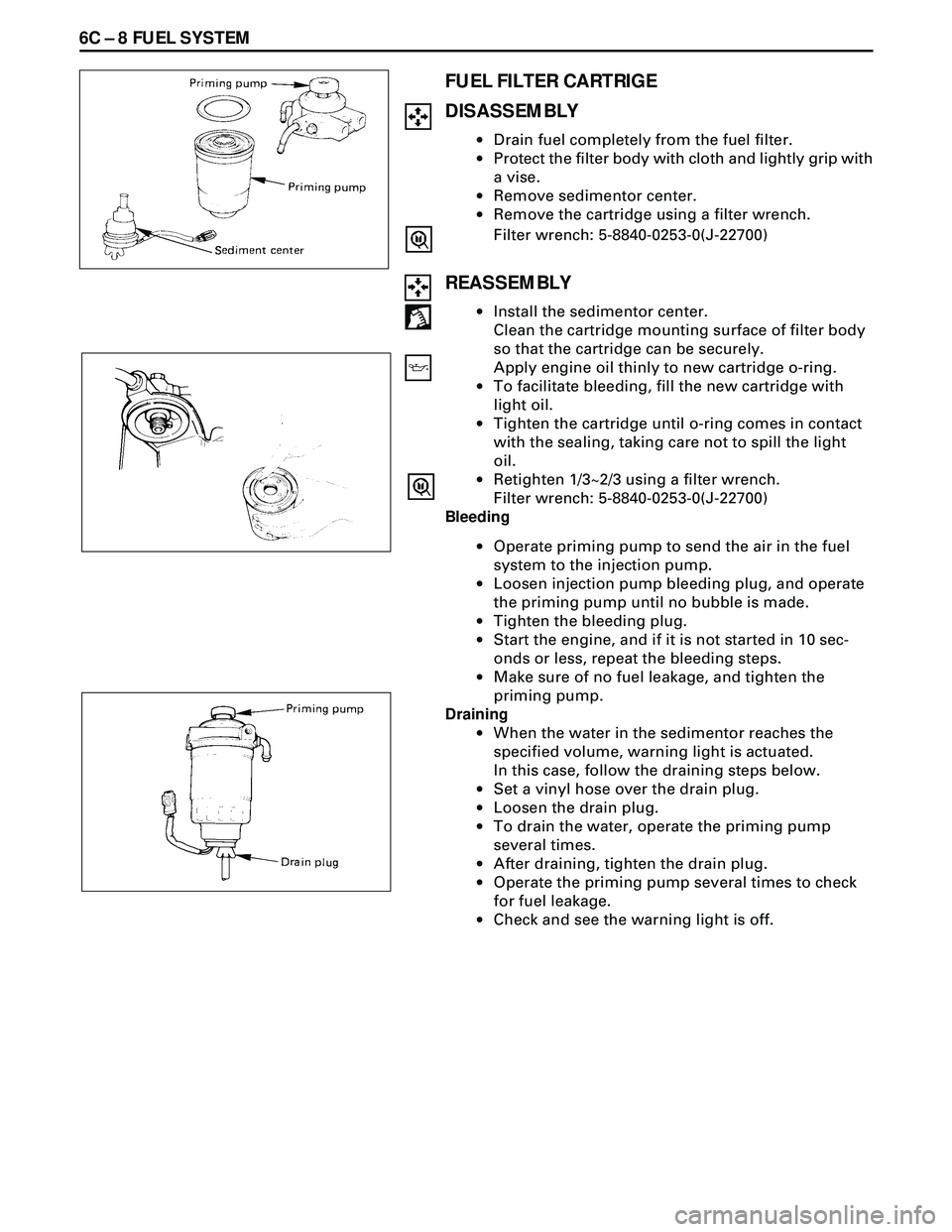
6C Ð 8 FUEL SYSTEM
FUEL FILTER CARTRIGE
DISASSEMBLY
·Drain fuel completely from the fuel filter.
·Protect the filter body with cloth and lightly grip with
a vise.
·Remove sedimentor center.
·Remove the cartridge using a filter wrench.
Filter wrench: 5-8840-0253-0(J-22700)
REASSEMBLY
·Install the sedimentor center.
Clean the cartridge mounting surface of filter body
so that the cartridge can be securely.
Apply engine oil thinly to new cartridge o-ring.
·To facilitate bleeding, fill the new cartridge with
light oil.
·Tighten the cartridge until o-ring comes in contact
with the sealing, taking care not to spill the light
oil.
·Retighten 1/3~2/3 using a filter wrench.
Filter wrench: 5-8840-0253-0(J-22700)
Bleeding
·Operate priming pump to send the air in the fuel
system to the injection pump.
·Loosen injection pump bleeding plug, and operate
the priming pump until no bubble is made.
·Tighten the bleeding plug.
·Start the engine, and if it is not started in 10 sec-
onds or less, repeat the bleeding steps.
·Make sure of no fuel leakage, and tighten the
priming pump.
Draining
·When the water in the sedimentor reaches the
specified volume, warning light is actuated.
In this case, follow the draining steps below.
·Set a vinyI hose over the drain plug.
·Loosen the drain plug.
·To drain the water, operate the priming pump
several times.
·After draining, tighten the drain plug.
·Operate the priming pump several times to check
for fuel leakage.
·Check and see the warning light is off.
Page 1675 of 3573
FUEL SYSTEM 6C Ð 9
INJECTION NOZZLE
REMOVAL
Preparation:
·Disconnect battery ground cable.
1. Intercooler Assembly (4JG2-T Only)
·(Refer to intercooler removal steps in section 6A2)
2. Air Cleaner Cover & Air Duct
3. Injection Pipe
·Release injection pipe clip.
·Loosen the flare nut on the injection pump side.
·Loosen the flare nut on the injection nozzle side,
disconnect and put aside the pipe.
4. Leak Off Pipe
5. Injection Nozzle
INSPECTION
·Set the nozzle in a nozzle tester.
Check there is no fuel leak in the nozzle seal when
a fuel pressure of 14710 kpa (150kg/cm
2/2133 psi) is
applied.
If there is leak, replace.
Page 1676 of 3573
6C Ð 10 FUEL SYSTEM
DISASSEMBLY
·Grip nozzle holder with a vise, loosen retaining nut
and disassemble.
·Loosen holder nut and remove the nozzle.
CAUTION
·Be careful not to damage the needle valve.
·Remove spacer, positioning pin, and push rod.
·Remove spring and adjusting shim.
CAUTION
·Wash all the parts removed and arrange them on a
cylinder basis, care should be taken not to miss any
parts.
·Soak the nozzle assembly in a parts receptacle filled
with light oil.
·Care should be taken not to miss shim, if used.
INSPECTION
Nozzle
·Soak the nozzle removed in clean light oil, wash
nozzle body and needle valve separately, and check
and see that the needle valve slide smoothly in the
nozzle body.
Page 1677 of 3573
FUEL SYSTEM 6C Ð 11
CAUTION
·If the needle valve does not slide smoothly repair
or replace with a new nozzle assembly.
Nozzle lapping procedure
·Apply thinly a compound (Chrome oxide kneaded
with an animal oil) to the seat of needle valve and
lap.
CAUTION
·Excess compound may cause worn needle valve,
and be sure to wash out the compound after
lapping.
Nozzle body & needle
·Check nozzle body end for seizure.
If significantly seized, replace as a nozzle assembly
basis. Also replace as a nozzle assembly basis, if
needle valve end is deformed or seized.
CAUTION
·
If either nozzle body or needle valve is faulty,
replace with a new nozzle assembly.
·DFIÕs sub hole is very small, care should be taken
not to allow foreign matter to get in.
REASSEMBLY
To reassemble, follow the removal steps in the reverse
order, noting the following point.
CAUTION
·Be careful to fit spacer because positioning pins
are set off.
Page 1678 of 3573
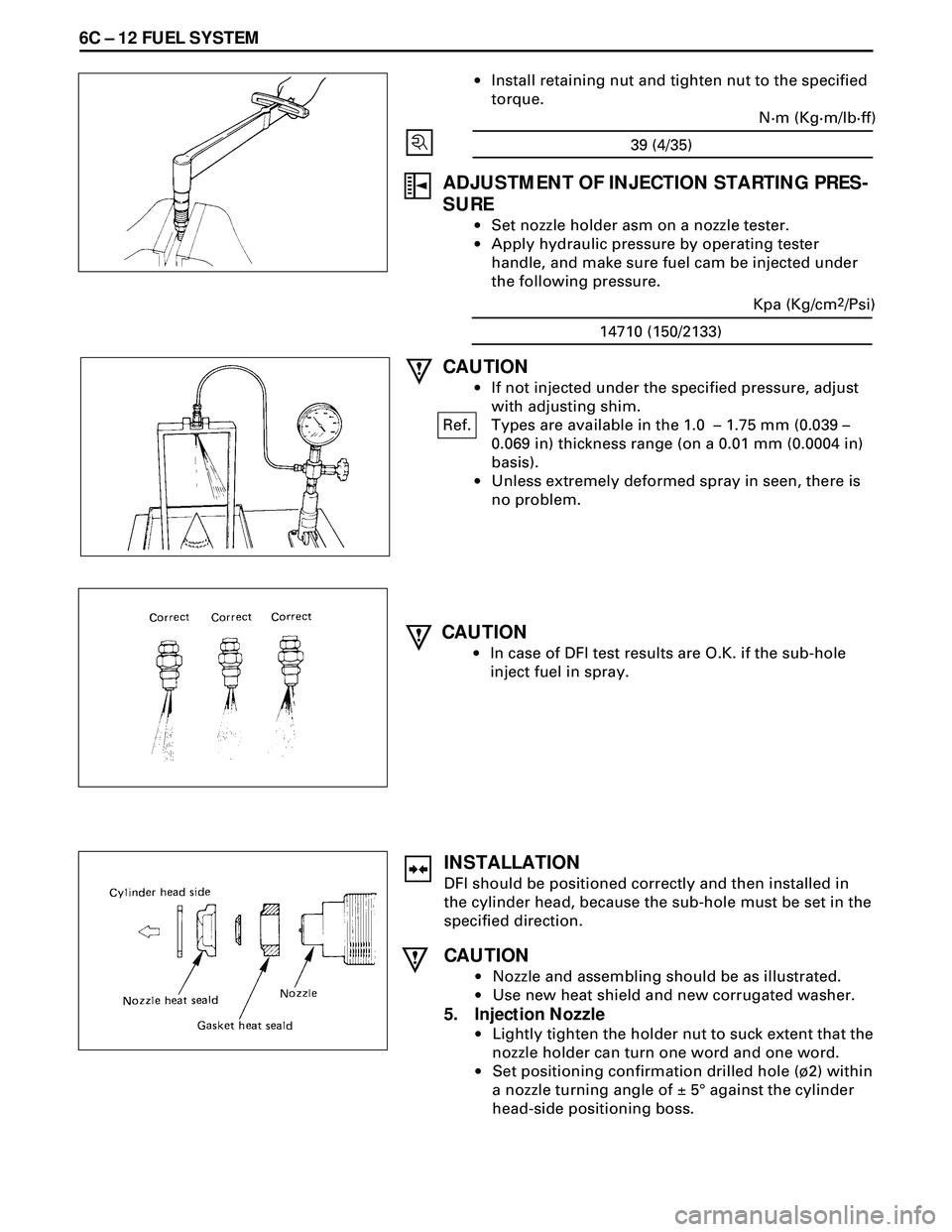
6C Ð 12 FUEL SYSTEM
·Install retaining nut and tighten nut to the specified
torque.
ADJUSTMENT OF INJECTION STARTING PRES-
SURE
·Set nozzle holder asm on a nozzle tester.
·Apply hydraulic pressure by operating tester
handle, and make sure fuel cam be injected under
the following pressure.
CAUTION
·In case of DFI test results are O.K. if the sub-hole
inject fuel in spray.
14710 (150/2133)Kpa (Kg/cm
2/Psi)
CAUTION
·If not injected under the specified pressure, adjust
with adjusting shim.
Ref. Types are available in the 1.0 Ð 1.75 mm (0.039 Ð
0.069 in) thickness range (on a 0.01 mm (0.0004 in)
basis).
·Unless extremely deformed spray in seen, there is
no problem.
INSTALLATION
DFI should be positioned correctly and then installed in
the cylinder head, because the sub-hole must be set in the
specified direction.
CAUTION
·Nozzle and assembling should be as illustrated.
·Use new heat shield and new corrugated washer.
5. Injection Nozzle
·Lightly tighten the holder nut to suck extent that the
nozzle holder can turn one word and one word.
·Set positioning confirmation drilled hole (¿2) within
a nozzle turning angle of ± 5¡ against the cylinder
head-side positioning boss.
39 (4/35)N·m (Kg·m/lb·ff)
Page 1679 of 3573
FUEL SYSTEM 6C Ð 13
·Apply a wrench as illustrated, and tighten the
holder nut to the specified torque using a special
tool.
wrench: nozzle holder 5-8840-0259-0
CAUTION
·After tightening the holder nut, make sure that the
drilled hole makes ± 5¡ or smaller with the cylinder
head-side positioning boss.
·When mounting leak off pipe, injection nozzle and
pipe, clean then with air so that dust may not enter.
4. Leak Off Pipe
·Mount using a new copper waker
3. Injection Pipe
·Connect injection pipe to nozzle holder.
·Tighten the injection pump side.
·Fit pipe clip in specified position.
2. Air Cleaner Cover & Air duct
1. Intercooler Assembly
·Refer to ÒIntercoolerÓ installation in section 6A2.
64 (6.5/47)N·m (Kg·m/lb.ft)
Page 1680 of 3573
6C Ð 14 FUEL SYSTEM
INJECTION PUMP ASSEMBLY
Removal Steps
1. Air cleaner cover & air duct
2. Intercooler assembly
3. Radiator assembly
4. Cooling fan assembly
5. P/S pump drive belt
6. AC generator drive belt7. Timing gear
8. Fuel filter assembly
9. Injection pump harness
10. Fuel hose and CSD hose
11. Injection pump Control cable
12. Injection pipe
13. Injection pump assembly
Installation Steps
To install, follow the removal steps in
the reverse order.