Page 1569 of 3573
ENGINE MECHANICAL 6A Ð 19
ROCKER ARM ASSEMBLY
DISASSEMBLY
1. Rocker Arm Shaft Assembly
2. Rocker Arm Shaft Snap Ring
3. Rocker Arm
4. Rocker Arm Shaft Bracket
5. Rocker Arm
6. Rocker Arm Shaft Spring
7. Rocker Arm Shaft
INSPECTION AND REPAIR
Make the necessary adjustments, repairs, and part replacements if excessive wear or damage is discovered
during inspection.
Use a micrometer to measure the rocker shaft outside
diameter at the point where the rocker arm moves on the
rocker shaft.
Replace the rocker shaft if the diameter exceeds the
specified limit.
Standard Limit
mm(in) Rocker Arm Shaft Outside Diameter
18.98 – 19.00
(0.7472 – 0.7480)18.9 (0.7441)
Page 1570 of 3573
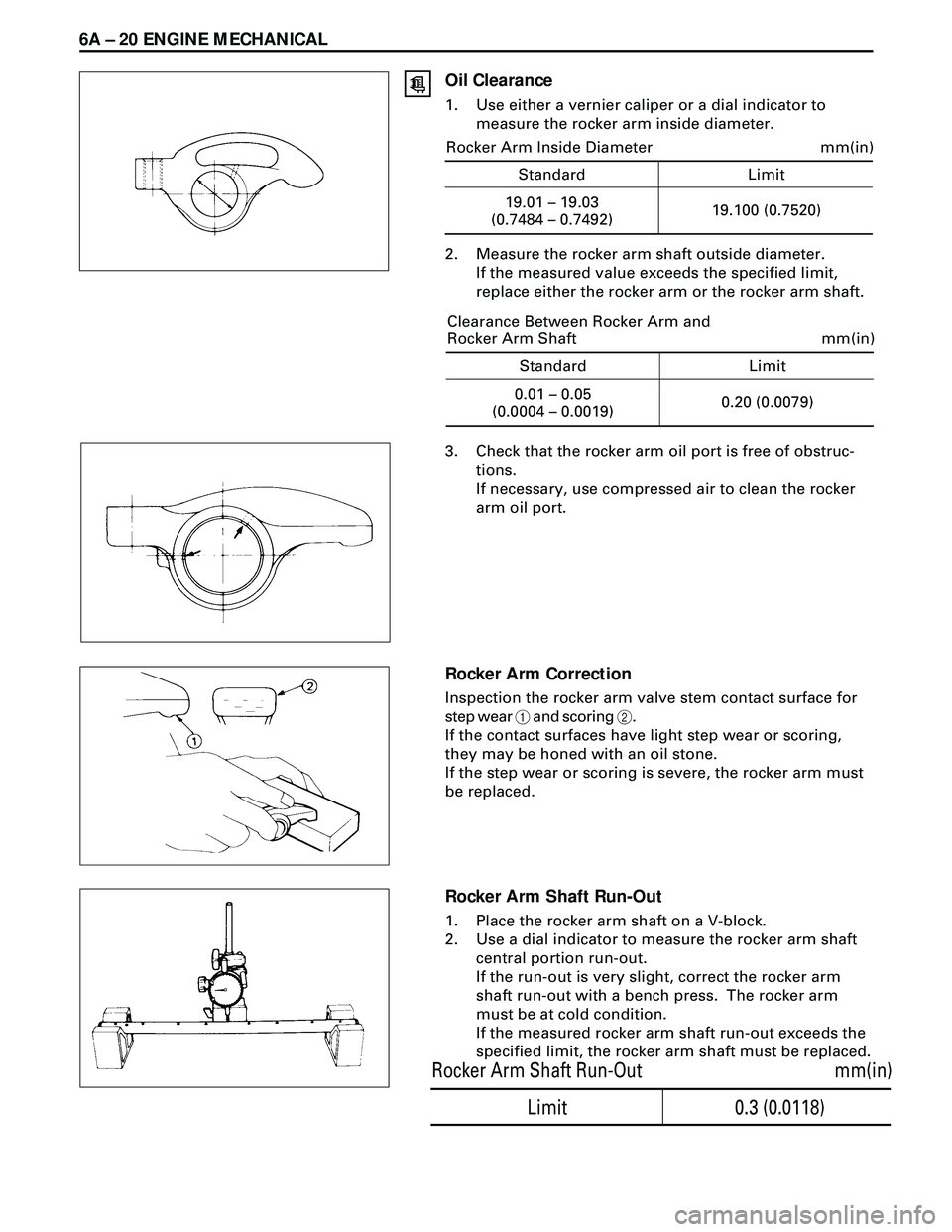
6A Ð 20 ENGINE MECHANICAL
Oil Clearance
1. Use either a vernier caliper or a dial indicator to
measure the rocker arm inside diameter.
2. Measure the rocker arm shaft outside diameter.
If the measured value exceeds the specified limit,
replace either the rocker arm or the rocker arm shaft.
3. Check that the rocker arm oil port is free of obstruc-
tions.
If necessary, use compressed air to clean the rocker
arm oil port.
Rocker Arm Correction
Inspection the rocker arm valve stem contact surface for
step wear 1 and scoring 2.
If the contact surfaces have light step wear or scoring,
they may be honed with an oil stone.
If the step wear or scoring is severe, the rocker arm must
be replaced.
Rocker Arm Shaft Run-Out
1. Place the rocker arm shaft on a V-block.
2. Use a dial indicator to measure the rocker arm shaft
central portion run-out.
If the run-out is very slight, correct the rocker arm
shaft run-out with a bench press. The rocker arm
must be at cold condition.
If the measured rocker arm shaft run-out exceeds the
specified limit, the rocker arm shaft must be replaced.
0.3 (0.0118)
mm(in) Rocker Arm Shaft Run-Out
Limit
Standard Limit
mm(in)
19.01 – 19.03
(0.7484 – 0.7492)19.100 (0.7520) Rocker Arm Inside Diameter
Standard Limit
mm(in)
0.01 – 0.05
(0.0004 – 0.0019)0.20 (0.0079) Clearance Between Rocker Arm and
Rocker Arm Shaft
Page 1571 of 3573
ENGINE MECHANICAL 6A Ð 21
REASSEMBLY
7. Rocker Arm Shaft
¥ Apply a light coat of engine oil to the rocker arm
shafts.
¥ Position the rocker arm shaft with the large oil
hole (4
f) facing the front of the engine.
¥ Install the rocker shaft together with the rocker
arm, the rocker arm shaft bracket, and the spring.
6. Rocker Arm Shaft Spring
5. Rocker Arm
4. Rocker Arm Shaft Bracket
3. Rocker Arm
2. Rocker Arm Shaft Snap Ring
1. Rocker Arm Shaft Assembly
¥ Install the rocker arm shaft assembly in cylinder
head.
¥ Tighten the rocker arm shaft fixing bolts to the
specified torque.
OIL PUMP
Page 1572 of 3573
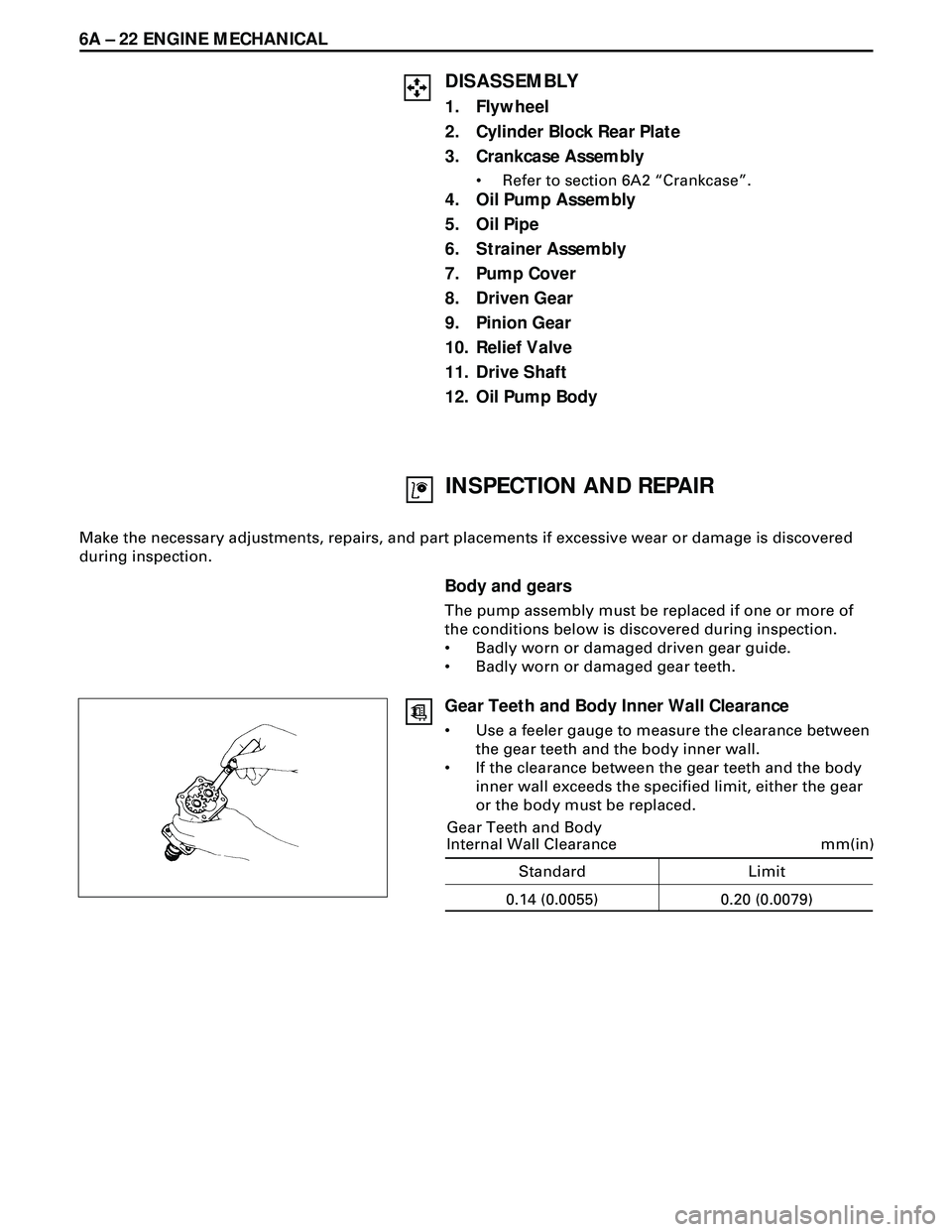
6A Ð 22 ENGINE MECHANICAL
DISASSEMBLY
1. Flywheel
2. Cylinder Block Rear Plate
3. Crankcase Assembly
¥ Refer to section 6A2 ÒCrankcaseÓ.
4. Oil Pump Assembly
5. Oil Pipe
6. Strainer Assembly
7. Pump Cover
8. Driven Gear
9. Pinion Gear
10. Relief Valve
11. Drive Shaft
12. Oil Pump Body
INSPECTION AND REPAIR
Make the necessary adjustments, repairs, and part placements if excessive wear or damage is discovered
during inspection.
Body and gears
The pump assembly must be replaced if one or more of
the conditions below is discovered during inspection.
¥ Badly worn or damaged driven gear guide.
¥ Badly worn or damaged gear teeth.
Gear Teeth and Body Inner Wall Clearance
¥ Use a feeler gauge to measure the clearance between
the gear teeth and the body inner wall.
¥ If the clearance between the gear teeth and the body
inner wall exceeds the specified limit, either the gear
or the body must be replaced.
Standard Limit
mm(in)
0.14 (0.0055) Gear Teeth and Body
Internal Wall Clearance
0.20 (0.0079)
Page 1573 of 3573
ENGINE MECHANICAL 6A Ð 23
Drive Shaft and Oil Pump Body Clearance
¥ Use a micrometer to measure the drive shaft outside
diameter.
¥ Use an inside dial indicator to measure the pump
body inside diameter.
¥ If the clearance between the drive shaft and the oil
pump body exceeds the specified limit, the oil pump
assembly must be replaced.
Gear and Body Clearance
¥ Use a feeler gauge to measure the clearance between
the body and the gear.
¥ If the clearance between the gear and the body
exceeds the specified limit, the body must be re-
placed.
Standard Limit
mm(in)
0.06 (0.0024) Gear and Body Clearance
0.15 (0.0059)
Standard Limit
mm(in)
0.04 (0.0016) Drive Shaft and Oil Pump Body Clearance
0.20 (0.0079)
REASSEMBLY
12. Oil Pump Body
11. Drive Shaft
10. Relief Valve
9. Pinion Gear
8. Driven Gear
7. Pump Cover
6. Strainer Assembly
¥ Install the strainer assembly and tighten the
strainer assembly fixing bolts.
5. Oil Pipe
16 (1.6/12)
N·m(kg·m/lb·ft)
Page 1574 of 3573
6A Ð 24 ENGINE MECHANICAL
4. Oil Pump Assembly
¥ Apply molybdenum mixed engine oil to drive
gear of camshaft and driven gear of oil pump.
¥ Tighten the oil pump fixing bolt to the specified
torque
3. Crankcase Assembly
¥ Refer to Section 6A2 ÒCrankcaseÓ.
2. Cylinder Block Rear Plate
¥ Align the rear plate with the cylinder body knock
pins. Tighten the rear plate to the specified
torque.
1. Flywheel
¥ Refer to Section 6A2 ÒCrankshaft and Main
BearingÓ.
19 (1.9/14)
N·m(kg·m/lb·ft)
82 (8.4/61)
N·m(kg·m/lb·ft)
Page 1575 of 3573
ENGINE MECHANICAL 6A Ð 25
CRANKSHAFT
DISASSEMBLY
1. Cylinder Head
·Refer to ÒCylinder headÓ in Section 6A2.
2. Camshaft Timing Gear
·Refer to ÒCamshaftÓ in Section 6A2.
3. Crankshaft Timing Gear
4. Crankshaft Front Oil Seal
5. Timing Gear Case
6. Flywheel
7. Cylinder Block Rear Plate
Page 1576 of 3573
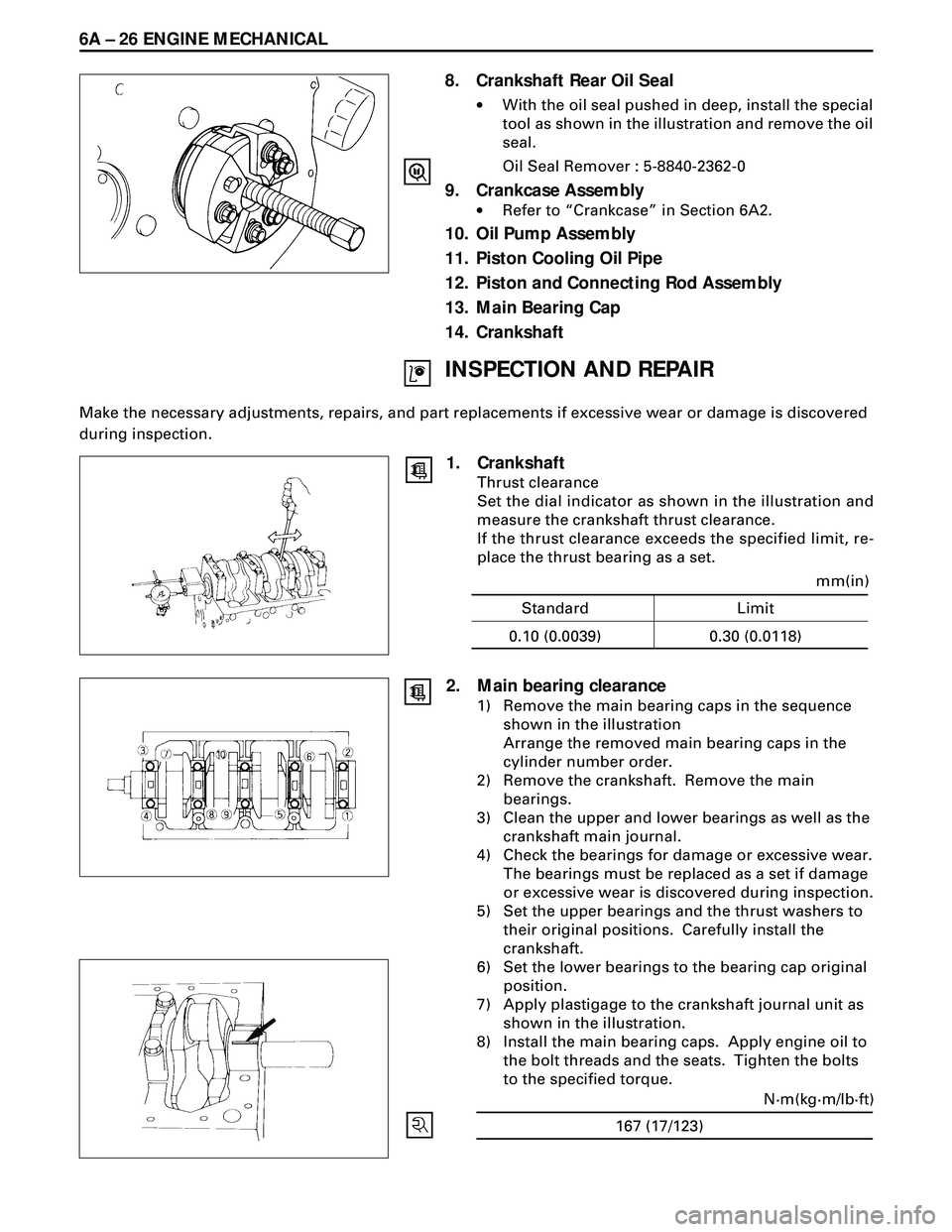
6A Ð 26 ENGINE MECHANICAL
8. Crankshaft Rear Oil Seal
·With the oil seal pushed in deep, install the special
tool as shown in the illustration and remove the oil
seal.
Oil Seal Remover : 5-8840-2362-0
9. Crankcase Assembly
·Refer to ÒCrankcaseÓ in Section 6A2.
10. Oil Pump Assembly
11. Piston Cooling Oil Pipe
12. Piston and Connecting Rod Assembly
13. Main Bearing Cap
14. Crankshaft
INSPECTION AND REPAIR
Make the necessary adjustments, repairs, and part replacements if excessive wear or damage is discovered
during inspection.
1. Crankshaft
Thrust clearance
Set the dial indicator as shown in the illustration and
measure the crankshaft thrust clearance.
If the thrust clearance exceeds the specified limit, re-
place the thrust bearing as a set.
Standard Limit
mm(in)
0.10 (0.0039) 0.30 (0.0118)
167 (17/123)N·m(kg·m/lb·ft)
2. Main bearing clearance
1) Remove the main bearing caps in the sequence
shown in the illustration
Arrange the removed main bearing caps in the
cylinder number order.
2) Remove the crankshaft. Remove the main
bearings.
3) Clean the upper and lower bearings as well as the
crankshaft main journal.
4) Check the bearings for damage or excessive wear.
The bearings must be replaced as a set if damage
or excessive wear is discovered during inspection.
5) Set the upper bearings and the thrust washers to
their original positions. Carefully install the
crankshaft.
6) Set the lower bearings to the bearing cap original
position.
7) Apply plastigage to the crankshaft journal unit as
shown in the illustration.
8) Install the main bearing caps. Apply engine oil to
the bolt threads and the seats. Tighten the bolts
to the specified torque.