Page 1553 of 3573
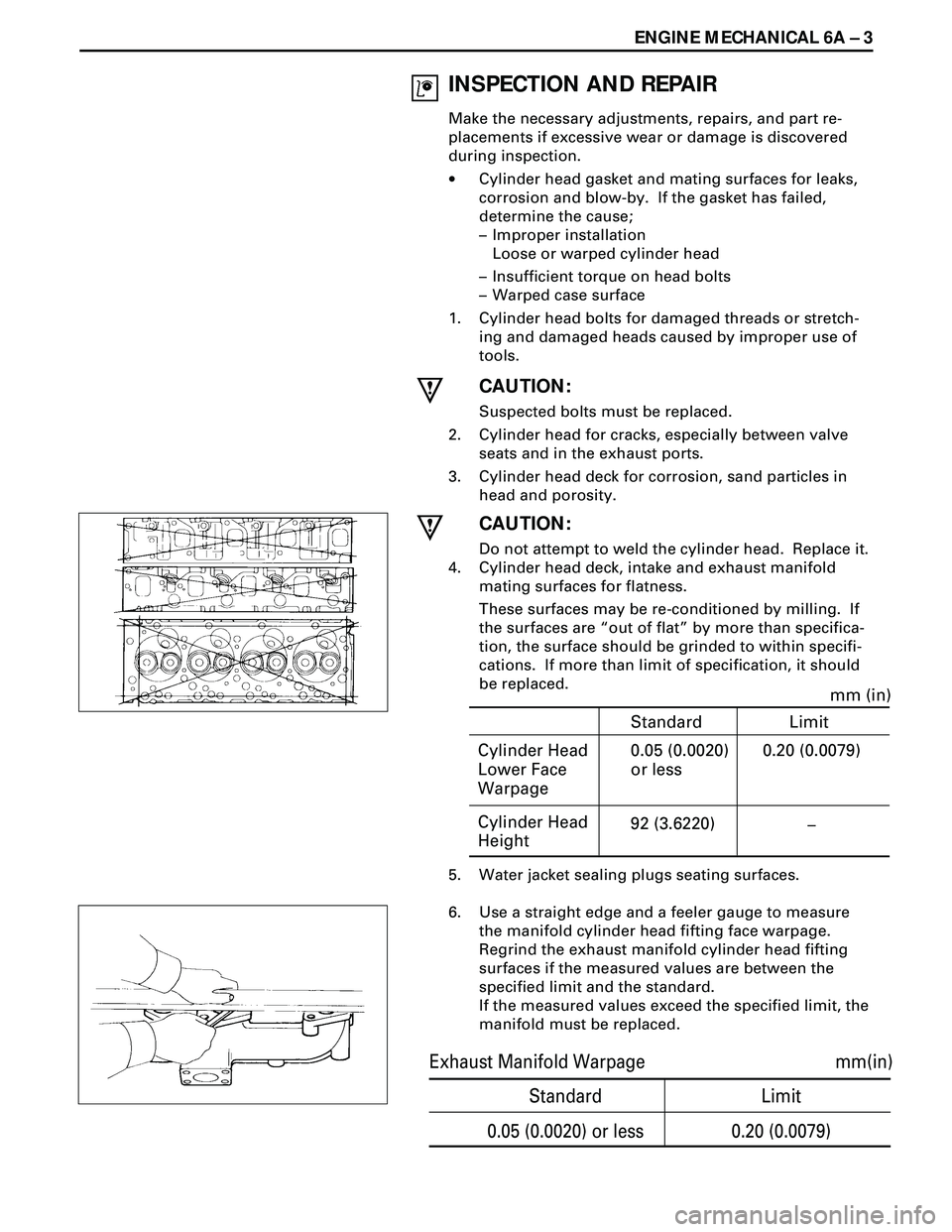
ENGINE MECHANICAL 6A Ð 3
INSPECTION AND REPAIR
Make the necessary adjustments, repairs, and part re-
placements if excessive wear or damage is discovered
during inspection.
·Cylinder head gasket and mating surfaces for leaks,
corrosion and blow-by. If the gasket has failed,
determine the cause;
Ð Improper installation
Loose or warped cylinder head
Ð Insufficient torque on head bolts
Ð Warped case surface
1. Cylinder head bolts for damaged threads or stretch-
ing and damaged heads caused by improper use of
tools.
CAUTION:
Suspected bolts must be replaced.
2. Cylinder head for cracks, especially between valve
seats and in the exhaust ports.
3. Cylinder head deck for corrosion, sand particles in
head and porosity.
CAUTION:
Do not attempt to weld the cylinder head. Replace it.
4. Cylinder head deck, intake and exhaust manifold
mating surfaces for flatness.
These surfaces may be re-conditioned by milling. If
the surfaces are Òout of flatÓ by more than specifica-
tion, the surface should be grinded to within specifi-
cations. If more than limit of specification, it should
be replaced.
5. Water jacket sealing plugs seating surfaces.
6. Use a straight edge and a feeler gauge to measure
the manifold cylinder head fifting face warpage.
Regrind the exhaust manifold cylinder head fifting
surfaces if the measured values are between the
specified limit and the standard.
If the measured values exceed the specified limit, the
manifold must be replaced.
Cylinder Head
Lower Face
Warpagemm (in)
0.05 (0.0020)
or less0.20 (0.0079)
Cylinder Head
Height92 (3.6220)
–
Standard Limit
Standard Limit
mm(in)
0.05 (0.0020) or less 0.20 (0.0079) Exhaust Manifold Warpage
Page 1554 of 3573
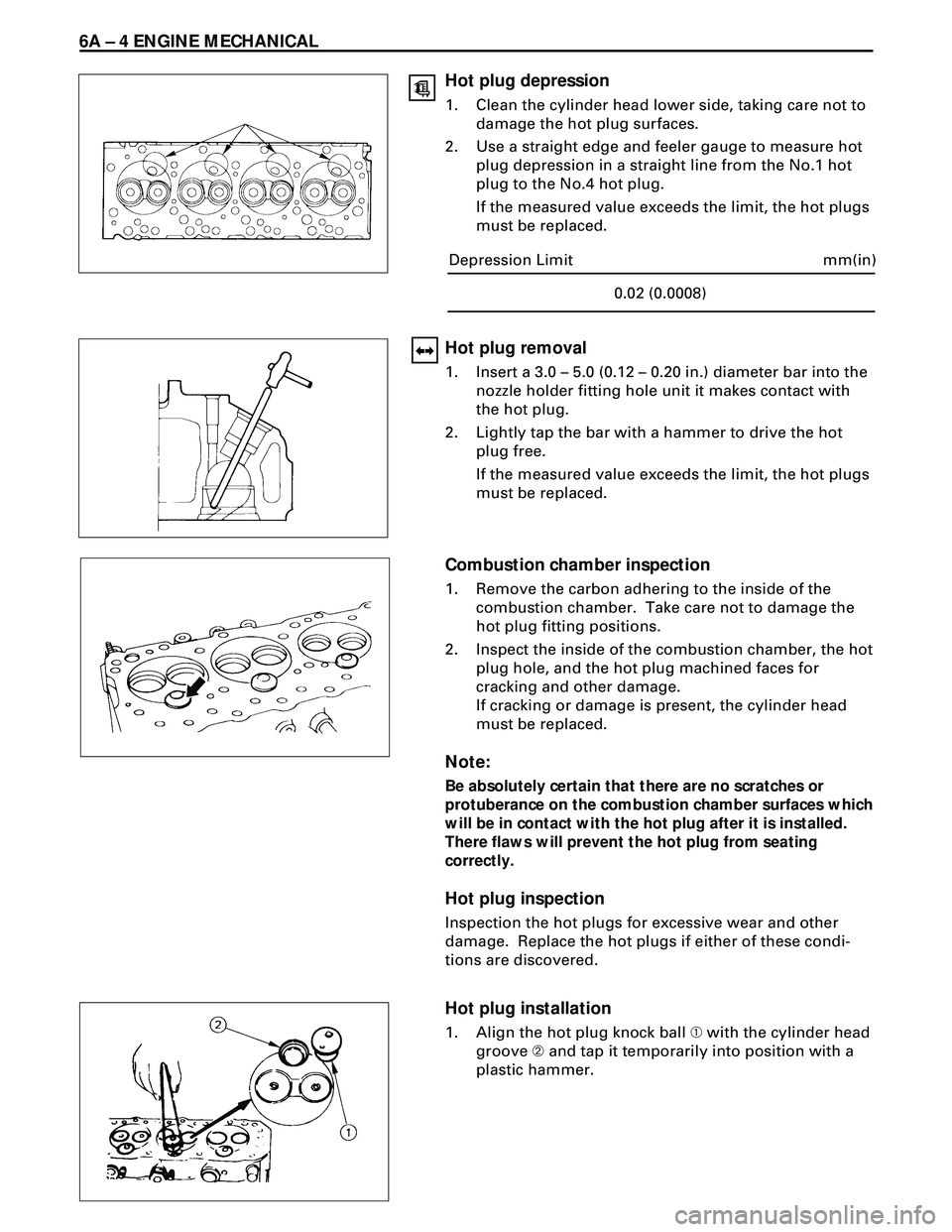
6A Ð 4 ENGINE MECHANICAL
Hot plug depression
1. Clean the cylinder head lower side, taking care not to
damage the hot plug surfaces.
2. Use a straight edge and feeler gauge to measure hot
plug depression in a straight line from the No.1 hot
plug to the No.4 hot plug.
If the measured value exceeds the limit, the hot plugs
must be replaced.
Hot plug removal
1. Insert a 3.0 Ð 5.0 (0.12 Ð 0.20 in.) diameter bar into the
nozzle holder fitting hole unit it makes contact with
the hot plug.
2. Lightly tap the bar with a hammer to drive the hot
plug free.
If the measured value exceeds the limit, the hot plugs
must be replaced.
mm(in)
0.02 (0.0008) Depression Limit
Combustion chamber inspection
1. Remove the carbon adhering to the inside of the
combustion chamber. Take care not to damage the
hot plug fitting positions.
2. Inspect the inside of the combustion chamber, the hot
plug hole, and the hot plug machined faces for
cracking and other damage.
If cracking or damage is present, the cylinder head
must be replaced.
Note:
Be absolutely certain that there are no scratches or
protuberance on the combustion chamber surfaces which
will be in contact with the hot plug after it is installed.
There flaws will prevent the hot plug from seating
correctly.
Hot plug inspection
Inspection the hot plugs for excessive wear and other
damage. Replace the hot plugs if either of these condi-
tions are discovered.
Hot plug installation
1. Align the hot plug knock ball À with the cylinder head
groove Á and tap it temporarily into position with a
plastic hammer.
Page 1555 of 3573
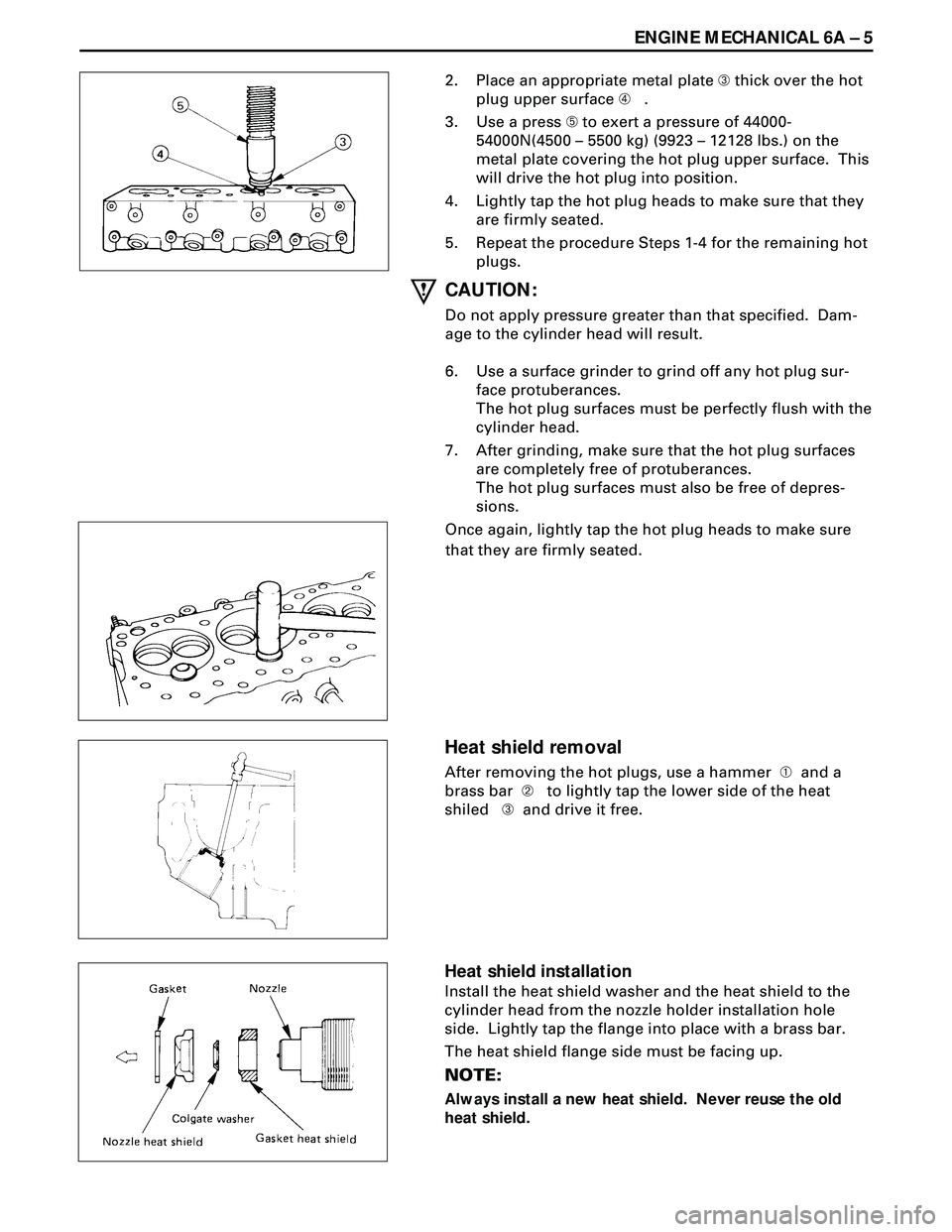
ENGINE MECHANICAL 6A Ð 5
2. Place an appropriate metal plate  thick over the hot
plug upper surface à .
3. Use a press Ä to exert a pressure of 44000-
54000N(4500 Ð 5500 kg) (9923 Ð 12128 lbs.) on the
metal plate covering the hot plug upper surface. This
will drive the hot plug into position.
4. Lightly tap the hot plug heads to make sure that they
are firmly seated.
5. Repeat the procedure Steps 1-4 for the remaining hot
plugs.
CAUTION:
Do not apply pressure greater than that specified. Dam-
age to the cylinder head will result.
6. Use a surface grinder to grind off any hot plug sur-
face protuberances.
The hot plug surfaces must be perfectly flush with the
cylinder head.
7. After grinding, make sure that the hot plug surfaces
are completely free of protuberances.
The hot plug surfaces must also be free of depres-
sions.
Once again, lightly tap the hot plug heads to make sure
that they are firmly seated.
Heat shield removal
After removing the hot plugs, use a hammer À and a
brass bar Á to lightly tap the lower side of the heat
shiled  and drive it free.
Heat shield installation
Install the heat shield washer and the heat shield to the
cylinder head from the nozzle holder installation hole
side. Lightly tap the flange into place with a brass bar.
The heat shield flange side must be facing up.
NOTE:
Always install a new heat shield. Never reuse the old
heat shield.
Page 1556 of 3573
6A Ð 6 ENGINE MECHANICAL
REASSEMBLY
6. Cylinder Head
¥ Refer to Section 6A2 ÒCylinder headÓ
5. Push Rod
4. Rocker Arm Shaft and Rocker Arm
·Tighten rocker arm shaft fixing bolts
3. Glow Plug and Glow Plug Connector
·Tighten glow plugs.
2. Injection Nozzle Holder
·Refer to Section 6C2 ÒInjection nozzleÓ.
1. Thermostat Housing Assembly
·Tighten thermostat housing assembly fixing bolt
N·m (Kg·m/lb·ft)
54 (5.5/40)
N·m (Kg·m/lb·ft)
23 (2.3/17)
N·m (Kg·m/lb·ft)
19 (1.9/14)
Page 1557 of 3573
ENGINE MECHANICAL 6A Ð 7
VALVE SPRING, VALVE STEM OIL SEAL, VALVE, VALVE GUIDE, PUSH ROD
DISASSEMBLY
1 Rocker Arm Asembly
2 Split Collar
Using special Tool, compress valve spring
Valve spring compressor: 9-8523-1423-0(J-29760)
3. Valve Spring
4. Valve
5. Valve Stem Oil Seal
6. Valve Guide
Valve Guide Replacer: 9-8523-1212-0
Page 1558 of 3573
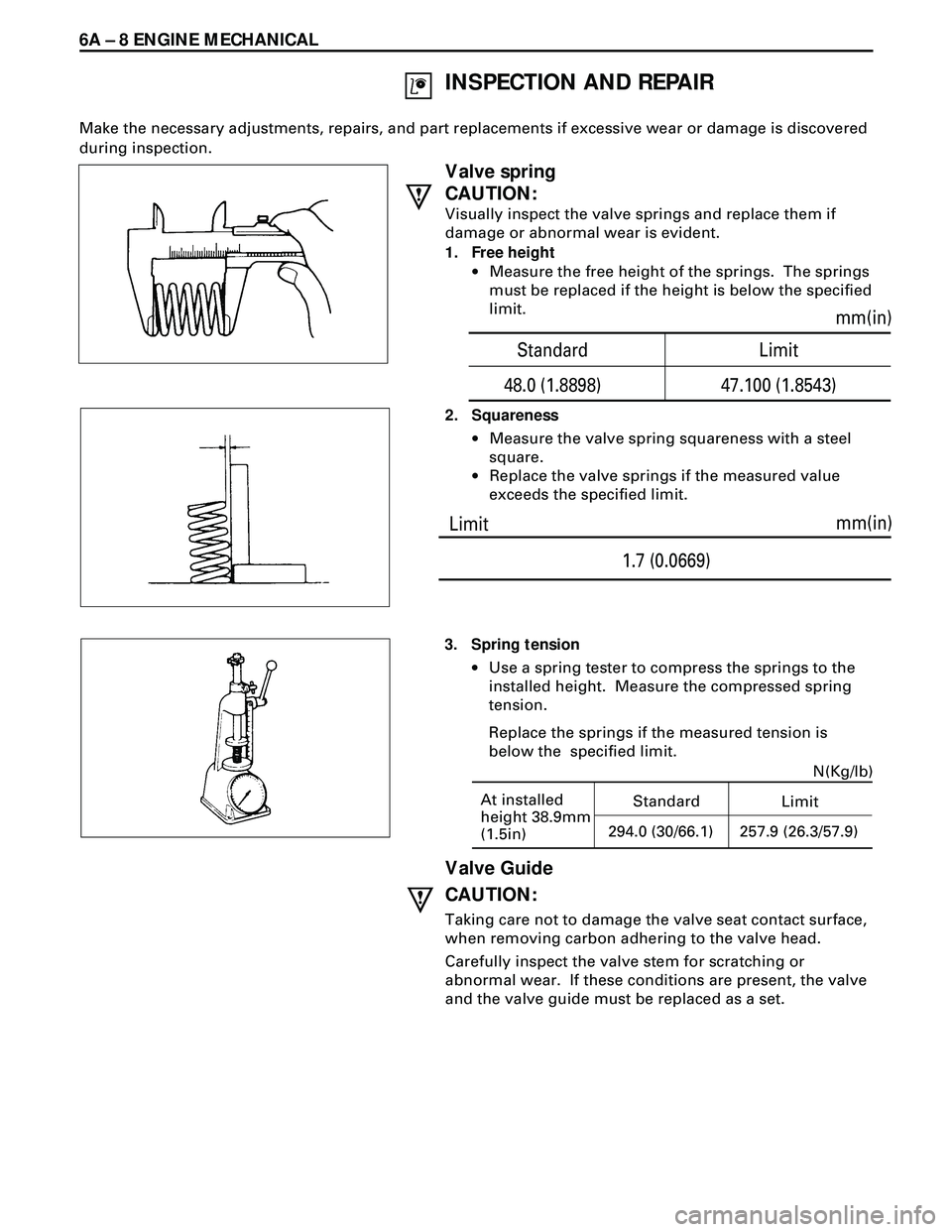
6A Ð 8 ENGINE MECHANICAL
At installed
height 38.9mm
(1.5in)StandardN(Kg/lb)
Limit
294.0 (30/66.1)257.9 (26.3/57.9)
Valve spring
CAUTION:
Visually inspect the valve springs and replace them if
damage or abnormal wear is evident.
1. Free height
·Measure the free height of the springs. The springs
must be replaced if the height is below the specified
limit.
INSPECTION AND REPAIR
Make the necessary adjustments, repairs, and part replacements if excessive wear or damage is discovered
during inspection.
2. Squareness
·Measure the valve spring squareness with a steel
square.
·Replace the valve springs if the measured value
exceeds the specified limit.
3. Spring tension
·Use a spring tester to compress the springs to the
installed height. Measure the compressed spring
tension.
Replace the springs if the measured tension is
below the specified limit.
Valve Guide
CAUTION:
Taking care not to damage the valve seat contact surface,
when removing carbon adhering to the valve head.
Carefully inspect the valve stem for scratching or
abnormal wear. If these conditions are present, the valve
and the valve guide must be replaced as a set.
Limitmm(in)
1.7 (0.0669)
Standard Limit
48.0 (1.8898) 47.100 (1.8543)mm(in)
Page 1559 of 3573
ENGINE MECHANICAL 6A Ð 9
1. Valve Guide Clearance
¥Measure the valve stem diameter with a
micrometer.
If the valve stem diameter is less than the specified
limit, the valve and the valve guide must be
replaced as a set.
¥Measure the inside diameter of the valve guide with
a micrometer.
¥ Subtract the measured outer diameter of the valve
stem from the measured inner diameter of the
valve guide. If the valve exceeds of the valve guide.
If the valve exceeds the specified limit, the valve
and the valve guide must be replaced as a set. Diameter of
Valve stemInlet
mm(in)
7.880
(0.3102)
Standard Limit
Exhaust7.946 – 7.961
(0.3128 – 0.3134)
7.850
(0.3091) 7.921 – 7.936
(0.3118 – 0.3124)
Inlet clearance
mm(in)
0.200
(0.0079)
Standard Limit
Exhaust clearance0.039 – 0.071
(0.0015 – 0.0028)
0.250
(0.0098) 0.064 – 0.096
(0.0025 – 0.0038)
Page 1560 of 3573
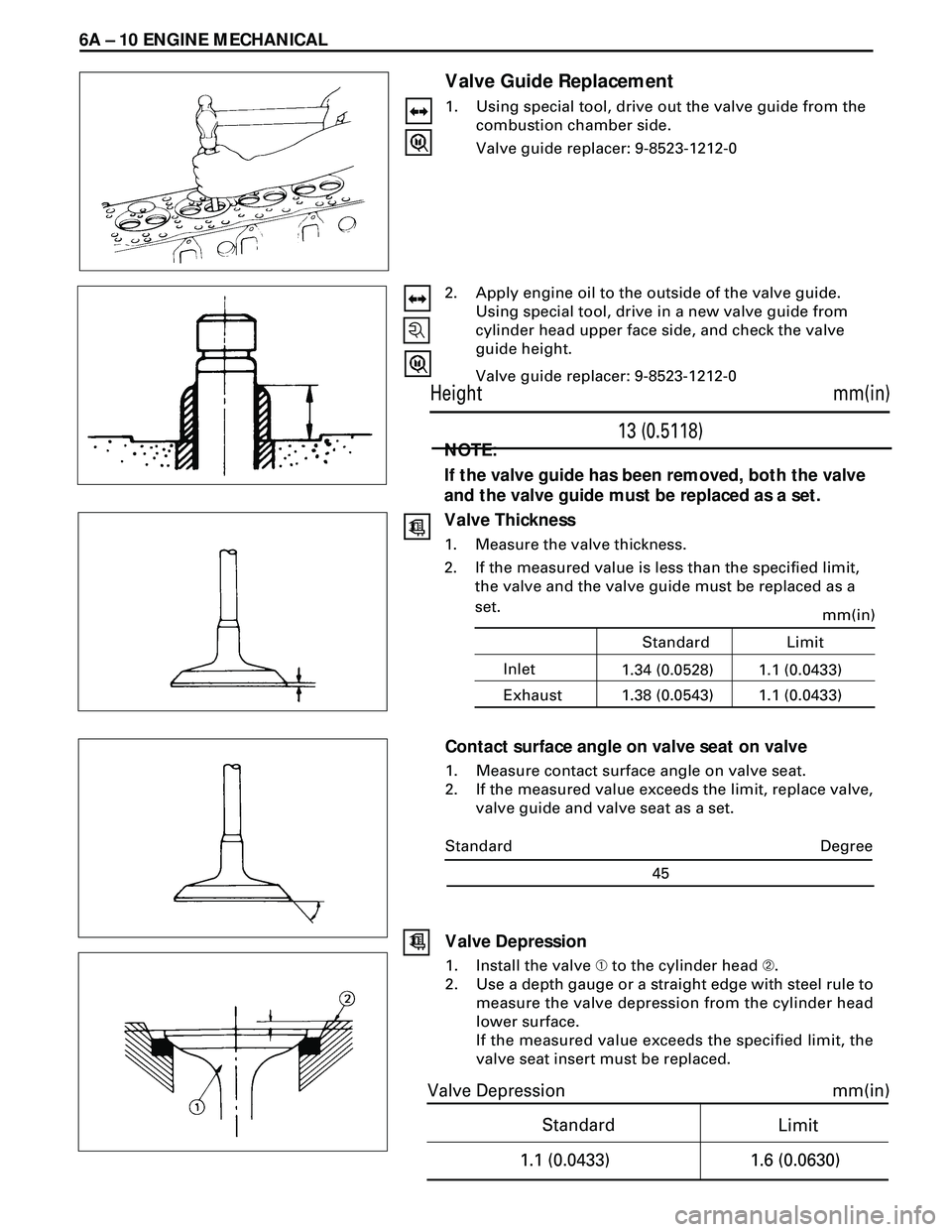
6A Ð 10 ENGINE MECHANICAL
Valve Guide Replacement
1. Using special tool, drive out the valve guide from the
combustion chamber side.
Valve guide replacer: 9-8523-1212-0
2. Apply engine oil to the outside of the valve guide.
Using special tool, drive in a new valve guide from
cylinder head upper face side, and check the valve
guide height.
Valve guide replacer: 9-8523-1212-0
NOTE:
If the valve guide has been removed, both the valve
and the valve guide must be replaced as a set.
Valve Thickness
1. Measure the valve thickness.
2. If the measured value is less than the specified limit,
the valve and the valve guide must be replaced as a
set.
Contact surface angle on valve seat on valve
1. Measure contact surface angle on valve seat.
2. If the measured value exceeds the limit, replace valve,
valve guide and valve seat as a set.
mm(in)
13 (0.5118) Height
Standard
mm(in)
Limit
1.1 (0.0433)
1.6 (0.0630)
Valve Depression
Degree
45 Standard
Valve Depression
1. Install the valve À to the cylinder head Á.
2. Use a depth gauge or a straight edge with steel rule to
measure the valve depression from the cylinder head
lower surface.
If the measured value exceeds the specified limit, the
valve seat insert must be replaced.
Inletmm(in)1.1 (0.0433) Standard Limit
Exhaust1.34 (0.0528)
1.1 (0.0433) 1.38 (0.0543)