Page 753 of 3573
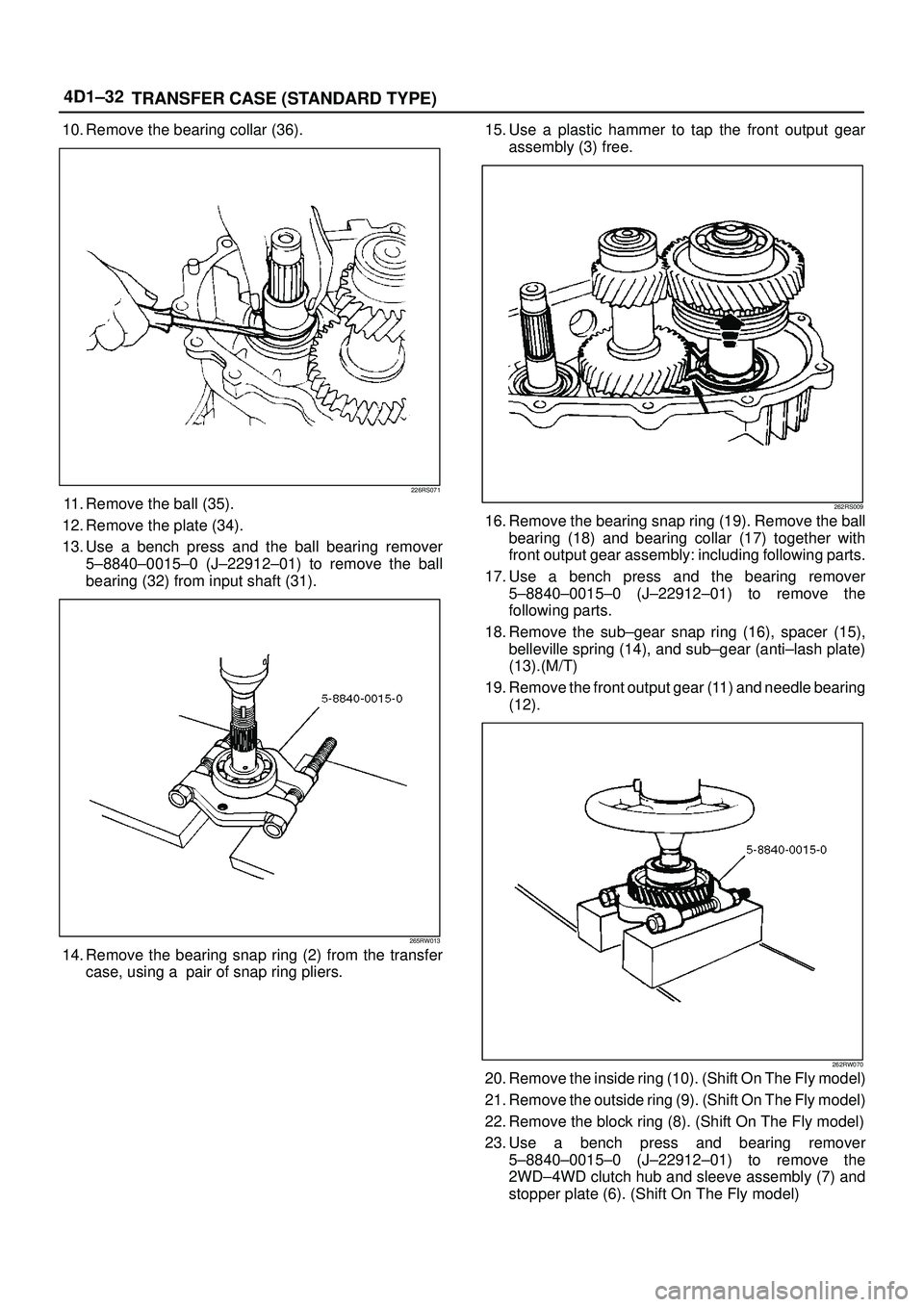
4D1±32
TRANSFER CASE (STANDARD TYPE)
10. Remove the bearing collar (36).
226RS071
11. Remove the ball (35).
12. Remove the plate (34).
13. Use a bench press and the ball bearing remover
5±8840±0015±0 (J±22912±01) to remove the ball
bearing (32) from input shaft (31).
265RW013
14. Remove the bearing snap ring (2) from the transfer
case, using a pair of snap ring pliers.15. Use a plastic hammer to tap the front output gear
assembly (3) free.
262RS009
16. Remove the bearing snap ring (19). Remove the ball
bearing (18) and bearing collar (17) together with
front output gear assembly: including following parts.
17. Use a bench press and the bearing remover
5±8840±0015±0 (J±22912±01) to remove the
following parts.
18. Remove the sub±gear snap ring (16), spacer (15),
belleville spring (14), and sub±gear (anti±lash plate)
(13).(M/T)
19. Remove the front output gear (11) and needle bearing
(12).
262RW070
20. Remove the inside ring (10). (Shift On The Fly model)
21. Remove the outside ring (9). (Shift On The Fly model)
22. Remove the block ring (8). (Shift On The Fly model)
23. Use a bench press and bearing remover
5±8840±0015±0 (J±22912±01) to remove the
2WD±4WD clutch hub and sleeve assembly (7) and
stopper plate (6). (Shift On The Fly model)
Page 754 of 3573

TRANSFER CASE (STANDARD TYPE)
4D1±33
NOTE: Do not reuse the stopper plate. (Shift On The Fly
model)
24. Disassemble the 2WD±4WD clutch hub and sleeve
assembly.
Springs (1) (Shift On The Fly model)
Inserts (2) (Shift On The Fly model)
Clutch Hub (3)
Sleeve (4)
226RW133
25. Use a bench press and the ball bearing remover
5±8840±0015±0 (J±22912±01) to remove the ball
bearing (4) from front output shaft (5).
262RW071
26. Remove bearing snap ring (29) from transfer case.
27. Remove the counter gear assembly (28) from the
transfer case (1).
28. Use a pair of snap ring pliers to remove the snap ring
(20).29. Use a bench press and the bearing remover
5±8840±0015±0 (J±22912±01) to remove the ball
bearing (21).
30. Use a pair of snap ring pliers to remove the snap ring
(27).
31. Use a bench press and the bearing remover
5±8840±0015±0 (J±22912±01) to remove the ball
bearing (26).
226RW191
32. Remove the spacer (25).
33. Remove the belleville spring (24).
34. Remove the sub±gear (anti±lash plate) (23) from the
counter gear (22).
Inspection and Repair
1. Make the necessary repair or parts replacement if
wear, damage or any other abnormal conditions are
found during inspection.
2. Wash all parts thoroughly in clean solvent. Be sure all
old lubricant, metallic particles, dirt, or foreign
material are removed from the surfaces of every part.
Apply compressed air to each oil feed port and
channel in each case half to remove any obstructions
or cleaning solvent residue.
Gears
1. Inspect all the gear teeth for signs of excessive wear
or damage and check all the gear splines for burrs,
nicks, wear or damage. Remove the minor nicks or
scratches on an oil stone. Replace any part exhibiting
excessive wear or damage.
Front Output Gear Inside Diameter
1. Use an inside dial indicator to measure the gear inside
diameter.
Page 755 of 3573
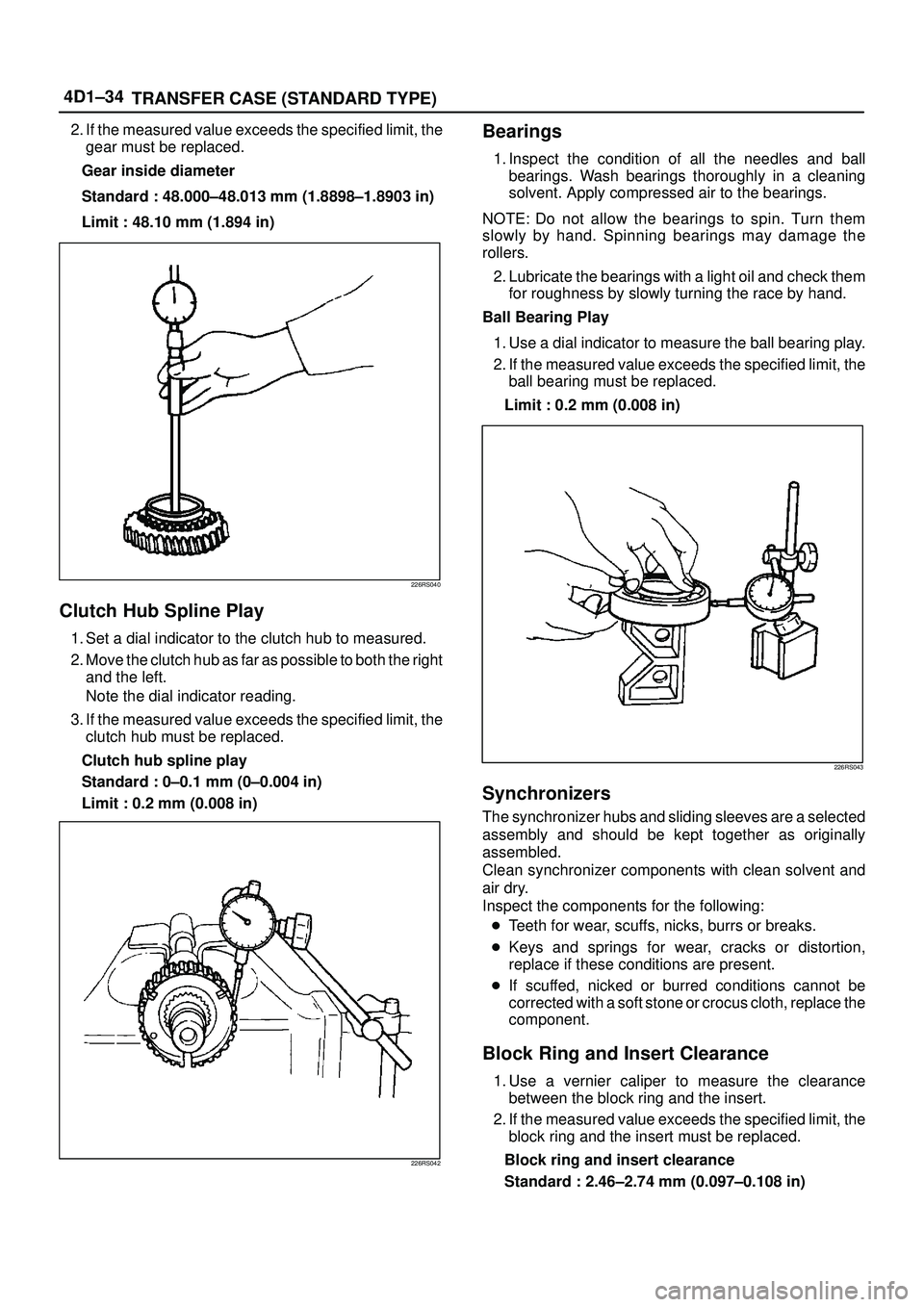
4D1±34
TRANSFER CASE (STANDARD TYPE)
2. If the measured value exceeds the specified limit, the
gear must be replaced.
Gear inside diameter
Standard : 48.000±48.013 mm (1.8898±1.8903 in)
Limit : 48.10 mm (1.894 in)
226RS040
Clutch Hub Spline Play
1. Set a dial indicator to the clutch hub to measured.
2. Move the clutch hub as far as possible to both the right
and the left.
Note the dial indicator reading.
3. If the measured value exceeds the specified limit, the
clutch hub must be replaced.
Clutch hub spline play
Standard : 0±0.1 mm (0±0.004 in)
Limit : 0.2 mm (0.008 in)
226RS042
Bearings
1. Inspect the condition of all the needles and ball
bearings. Wash bearings thoroughly in a cleaning
solvent. Apply compressed air to the bearings.
NOTE: Do not allow the bearings to spin. Turn them
slowly by hand. Spinning bearings may damage the
rollers.
2. Lubricate the bearings with a light oil and check them
for roughness by slowly turning the race by hand.
Ball Bearing Play
1. Use a dial indicator to measure the ball bearing play.
2. If the measured value exceeds the specified limit, the
ball bearing must be replaced.
Limit : 0.2 mm (0.008 in)
226RS043
Synchronizers
The synchronizer hubs and sliding sleeves are a selected
assembly and should be kept together as originally
assembled.
Clean synchronizer components with clean solvent and
air dry.
Inspect the components for the following:
Teeth for wear, scuffs, nicks, burrs or breaks.
Keys and springs for wear, cracks or distortion,
replace if these conditions are present.
If scuffed, nicked or burred conditions cannot be
corrected with a soft stone or crocus cloth, replace the
component.
Block Ring and Insert Clearance
1. Use a vernier caliper to measure the clearance
between the block ring and the insert.
2. If the measured value exceeds the specified limit, the
block ring and the insert must be replaced.
Block ring and insert clearance
Standard : 2.46±2.74 mm (0.097±0.108 in)
Page 756 of 3573
TRANSFER CASE (STANDARD TYPE)
4D1±35
Limit : 3.0 mm (0.118 in)
226RS037
2WD±4WD 3±Cone Synchronizer (Shift On
The Fly model)
1. Use a thickness gauge to measure the clearance
between the block ring and the dog teeth.
2. If the measured value exceeds the specified limit, the
2WD±4WD synchronizer assembly must be
replaced.
Block ring and insert clearance
Standard : 1.5 mm (0.059 in)
Limit : 0.8 mm (0.031 in)
226RW142
Clutch Hub and Insert Clearance
1. Use a thickness gauge to measure the clearance
between the clutch hub and the insert.
2. If the measured value exceeds the specified limit, the
clutch hub and the insert must be replaced.
Clutch hub and insert clearance
Standard : 0.01±0.19 mm (0.0004±0.0075 in)
Limit : 0.3 mm (0.012 in)
226RS038
Detent Springs
1. Inspect the springs for distortion, cracks or wear.
Replace if these conditions are present.
Detent Spring Free Length
1. Use a vernier caliper to measure the detent spring
free length.
Page 757 of 3573
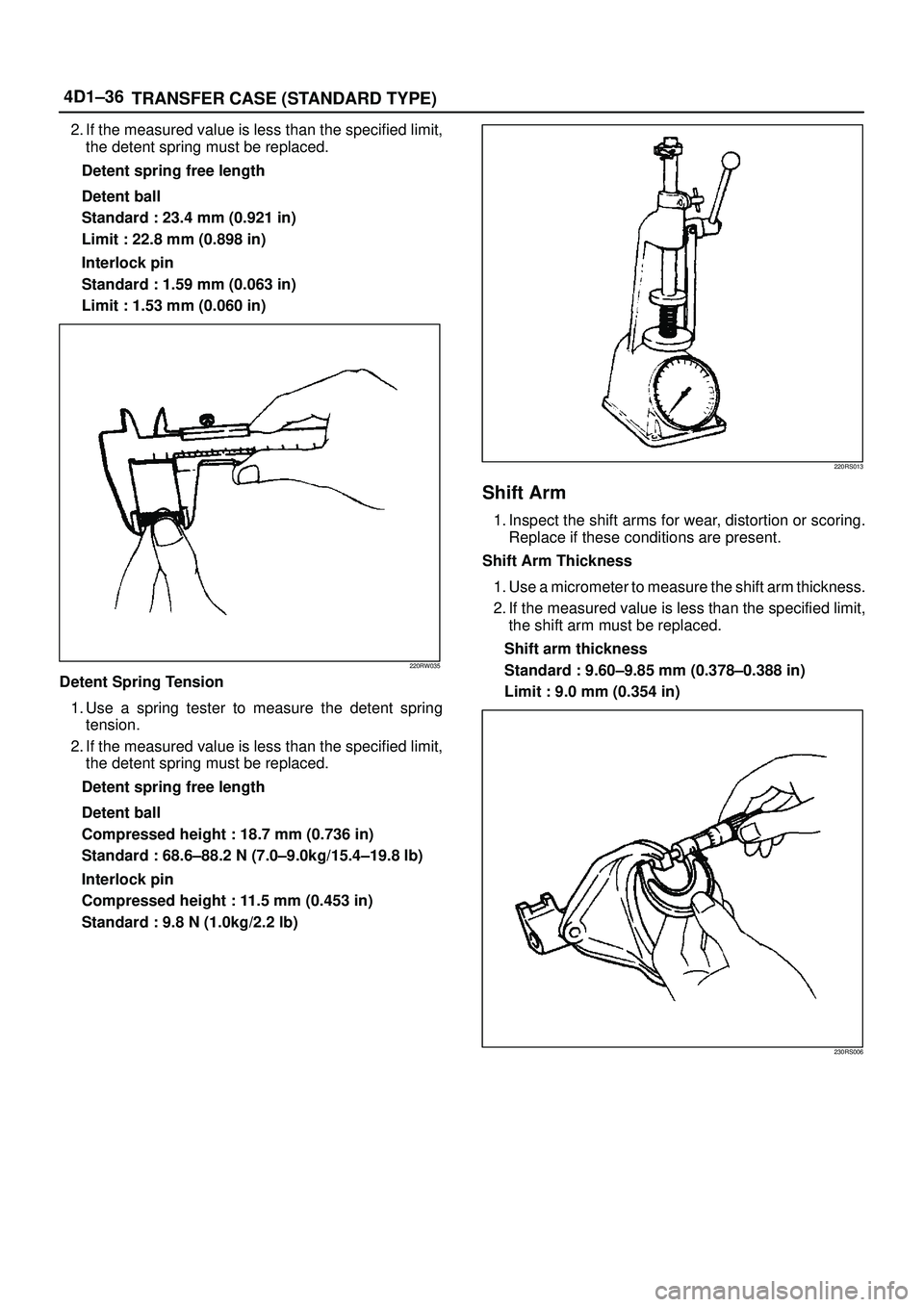
4D1±36
TRANSFER CASE (STANDARD TYPE)
2. If the measured value is less than the specified limit,
the detent spring must be replaced.
Detent spring free length
Detent ball
Standard : 23.4 mm (0.921 in)
Limit : 22.8 mm (0.898 in)
Interlock pin
Standard : 1.59 mm (0.063 in)
Limit : 1.53 mm (0.060 in)
220RW035
Detent Spring Tension
1. Use a spring tester to measure the detent spring
tension.
2. If the measured value is less than the specified limit,
the detent spring must be replaced.
Detent spring free length
Detent ball
Compressed height : 18.7 mm (0.736 in)
Standard : 68.6±88.2 N (7.0±9.0kg/15.4±19.8 lb)
Interlock pin
Compressed height : 11.5 mm (0.453 in)
Standard : 9.8 N (1.0kg/2.2 lb)
220RS013
Shift Arm
1. Inspect the shift arms for wear, distortion or scoring.
Replace if these conditions are present.
Shift Arm Thickness
1. Use a micrometer to measure the shift arm thickness.
2. If the measured value is less than the specified limit,
the shift arm must be replaced.
Shift arm thickness
Standard : 9.60±9.85 mm (0.378±0.388 in)
Limit : 9.0 mm (0.354 in)
230RS006
Page 758 of 3573
TRANSFER CASE (STANDARD TYPE)
4D1±37
Reassembly
1. Put the transfer case (with oil seal) as the following
illustration.
Input shaft oil seal (1) replacement
1. Remove the oil seal from the transfer case.
2. Apply engine oil to the oil seal outer surfaces.
3. Apply recommended grease (BESCO L2) or
equivalent to the oil seal lip.
4. Use the oil seal installer 5±8840±2279±0
(J±38592) to install the oil seal to the transfer
case.
220RW106
Front output shaft oil seal (2) replacement
1. Remove the oil seal from the transfer case.
2. Apply engine oil to the oil seal outer surfaces.
3. Apply recommended grease (BESCO L2) or
equivalent to the oil seal lip.
4. Use the oil seal installer 5±8840±2281±0
(J±38594) to install the oil seal to the transfer
case.
220RW107
Legend
(2) Front output shaft oil seal
2. Apply chassis grease (3) to the sub±gear (23) and the
counter gear (22) thrust surfaces.
226RW134
Page 759 of 3573
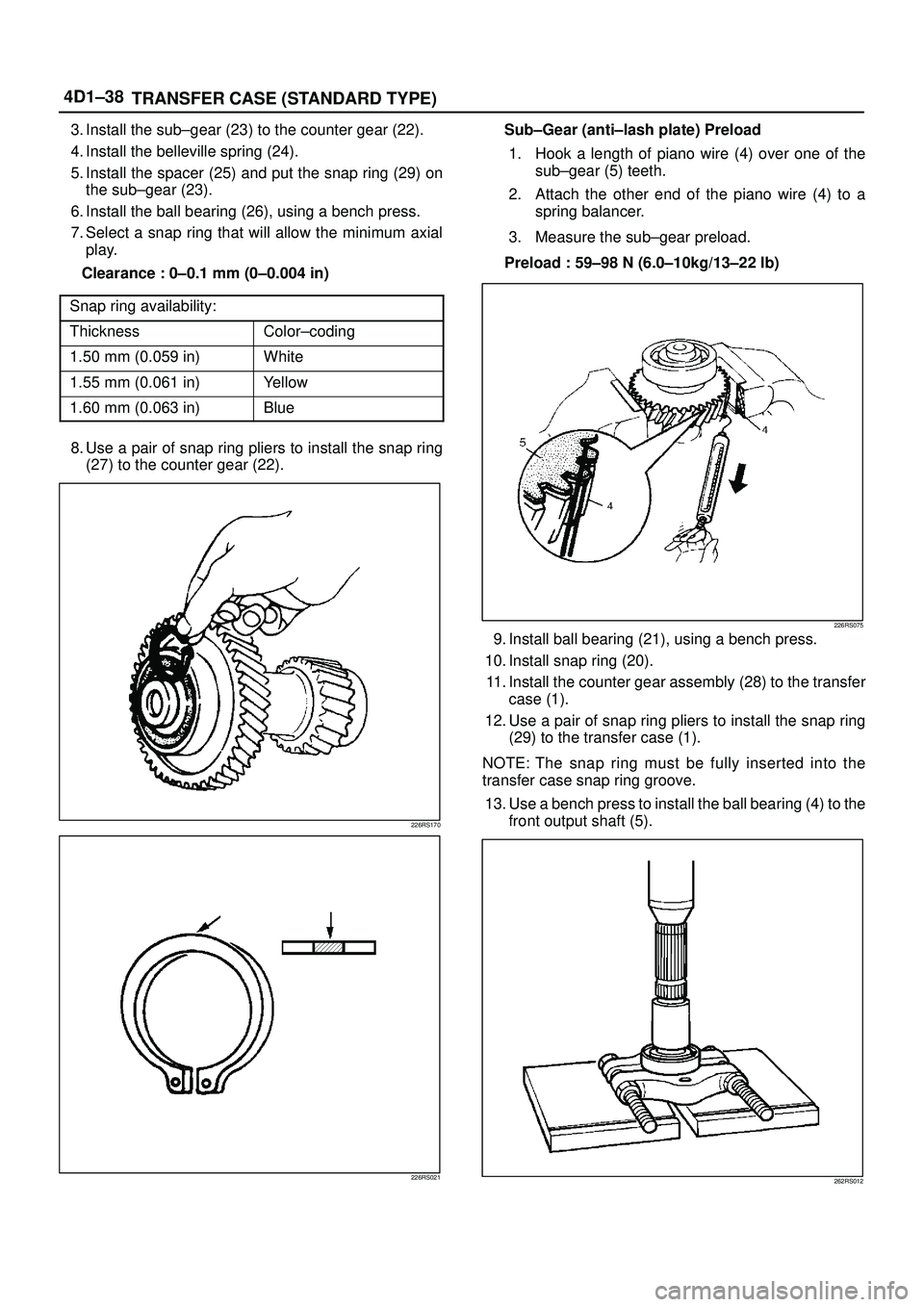
4D1±38
TRANSFER CASE (STANDARD TYPE)
3. Install the sub±gear (23) to the counter gear (22).
4. Install the belleville spring (24).
5. Install the spacer (25) and put the snap ring (29) on
the sub±gear (23).
6. Install the ball bearing (26), using a bench press.
7. Select a snap ring that will allow the minimum axial
play.
Clearance : 0±0.1 mm (0±0.004 in)
Snap ring availability:
ThicknessColor±coding
1.50 mm (0.059 in)White
1.55 mm (0.061 in)Yellow
1.60 mm (0.063 in)Blue
8. Use a pair of snap ring pliers to install the snap ring
(27) to the counter gear (22).
226RS170
226RS021
Sub±Gear (anti±lash plate) Preload
1. Hook a length of piano wire (4) over one of the
sub±gear (5) teeth.
2. Attach the other end of the piano wire (4) to a
spring balancer.
3. Measure the sub±gear preload.
Preload : 59±98 N (6.0±10kg/13±22 lb)
226RS075
9. Install ball bearing (21), using a bench press.
10. Install snap ring (20).
11. Install the counter gear assembly (28) to the transfer
case (1).
12. Use a pair of snap ring pliers to install the snap ring
(29) to the transfer case (1).
NOTE: The snap ring must be fully inserted into the
transfer case snap ring groove.
13. Use a bench press to install the ball bearing (4) to the
front output shaft (5).
262RS012
Page 760 of 3573
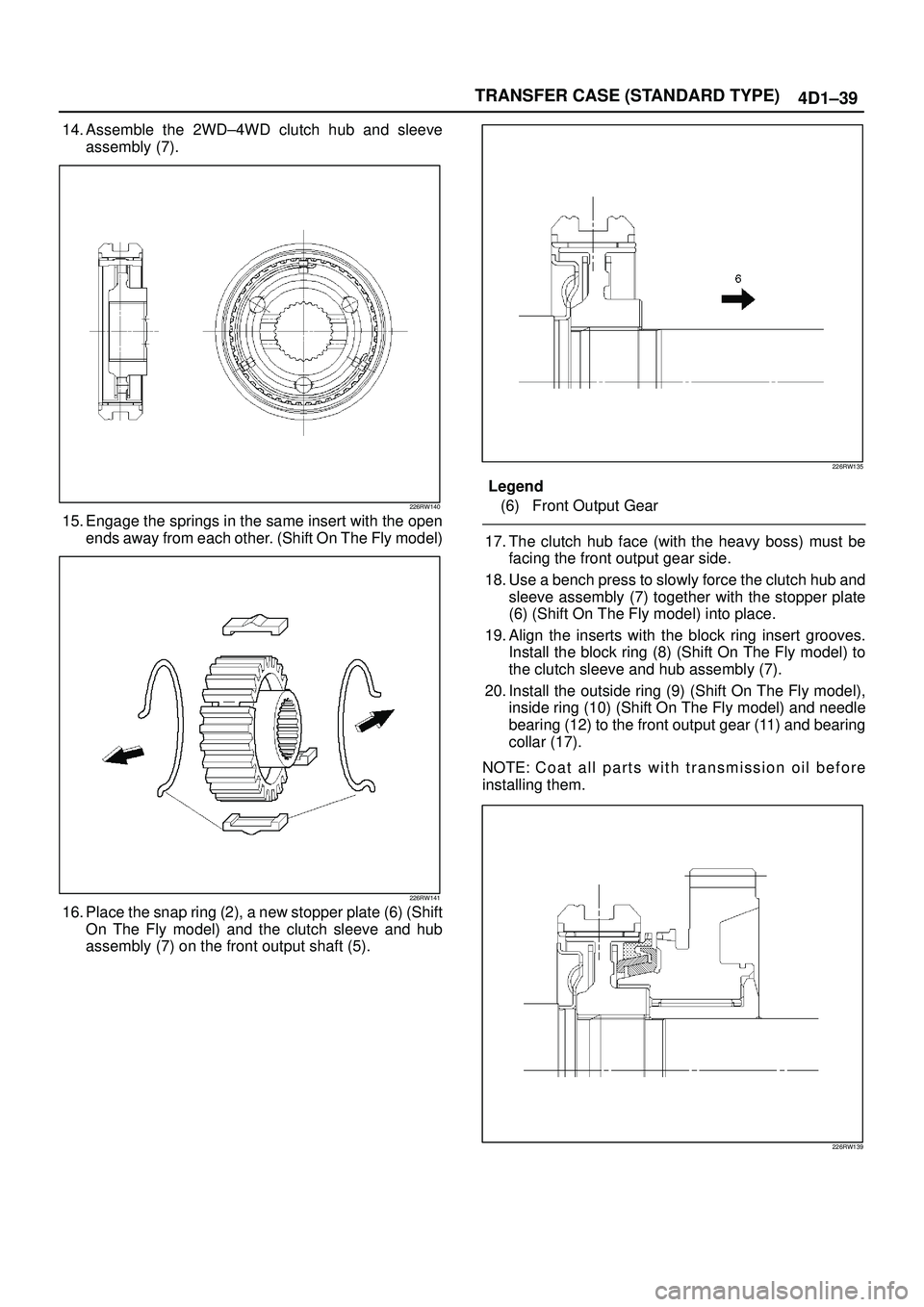
TRANSFER CASE (STANDARD TYPE)
4D1±39
14. Assemble the 2WD±4WD clutch hub and sleeve
assembly (7).
226RW140
15. Engage the springs in the same insert with the open
ends away from each other. (Shift On The Fly model)
226RW141
16. Place the snap ring (2), a new stopper plate (6) (Shift
On The Fly model) and the clutch sleeve and hub
assembly (7) on the front output shaft (5).
226RW135
Legend
(6) Front Output Gear
17. The clutch hub face (with the heavy boss) must be
facing the front output gear side.
18. Use a bench press to slowly force the clutch hub and
sleeve assembly (7) together with the stopper plate
(6) (Shift On The Fly model) into place.
19. Align the inserts with the block ring insert grooves.
Install the block ring (8) (Shift On The Fly model) to
the clutch sleeve and hub assembly (7).
20. Install the outside ring (9) (Shift On The Fly model),
inside ring (10) (Shift On The Fly model) and needle
bearing (12) to the front output gear (11) and bearing
collar (17).
NOTE: C o a t a l l p a r t s w i t h t r a n s mission oil before
installing them.
226RW139