Page 513 of 3573
4A2B±10DIFFERENTIAL (REAR 244mm)
Disassembled View
415RW002
Legend
(1) Flange Nut and Washer
(2) Flange
(3) Oil Seal
(4) Oil Seal Slinger
(5) Outer Bearing
(6) Outer Bearing Outer Race
(7) Diff Carrier
(8) Bearing Cap
(9) Bolt(10) Inner Bearing Outer Race
(11) Collapsible Spacer
(12) Inner Bearing
(13) Adjust Shim (Pinion Position)
(14) Drive Pinion Shaft
(15) Adjust Shim (Diff Cage Assembly)
(16) Diff Preload/Backlash
(17) Side Bearing
(18) Side Bearing Outer Race
Page 514 of 3573
DIFFERENTIAL (REAR 244mm)
4A2B±11
Disassembly
1. Using holding fixture 5±8840±2029±0 and holding
fixture base 5±8840±0003±0, fix the differential
assembly to the bench.
425RW058
2. Apply a setting mark to the side bearing cap and the
differential carrier then remove bearing cap.
425RS009
3. Remove differential cage assembly.
4. Remove side bearing outer race. After removal, keep
the right and left hand side bearing assemblies
separate to maintain inner and outer race
combinations.
5. Remove side bearing by using remover
5±8840±2587±0 and adapter 5±8840±2576±0.
Select collet halves 44803 in remover kit
5±8840±2587±0 for side bearing removal and insert
is not required for this operation.
415RW041
6. Note the thickness and position of the shims then
remove adjust shim.
7. Remove the flange nut and washer by using pinion
flange holder 5±8840±0133±0 after raising up its
staked parts completely.
415RW040
Page 515 of 3573
4A2B±12DIFFERENTIAL (REAR 244mm)
8. Removed flange assembly.
9. Remove the drive pinion assembly using a soft metal
rod and a hammer.
425RS012
10. Remove collapsible spacer.
11. Remove the inner bearing by using remover
5±8840±2587±0. Select insert 303174 and collet
halves 44803 in remover kit 5±8840±2587±0 for inner
bearing removal.
415RW042
12. Remove adjust shim.
13. Remove oil seal.
14. Remove oil seal slinger.
15. Remove outer bearing.
16. Remove the inner bearing outer race (1) and the outer
bearing outer race (2) by using a brass bar and a
hammer.
425RS014
425RS015
Page 516 of 3573
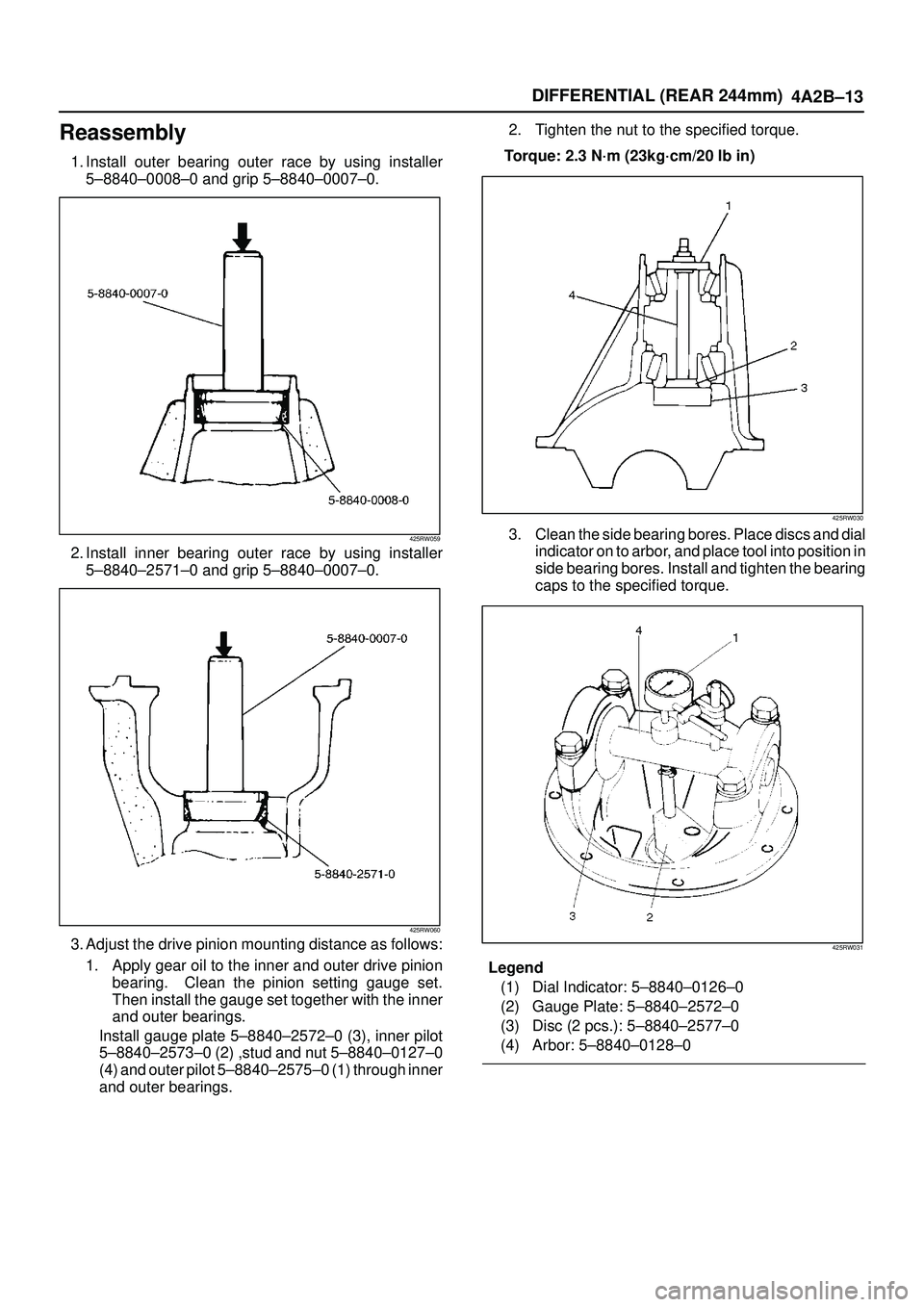
DIFFERENTIAL (REAR 244mm)
4A2B±13
Reassembly
1. Install outer bearing outer race by using installer
5±8840±0008±0 and grip 5±8840±0007±0.
425RW059
2. Install inner bearing outer race by using installer
5±8840±2571±0 and grip 5±8840±0007±0.
425RW060
3. Adjust the drive pinion mounting distance as follows:
1. Apply gear oil to the inner and outer drive pinion
bearing. Clean the pinion setting gauge set.
Then install the gauge set together with the inner
and outer bearings.
Install gauge plate 5±8840±2572±0 (3), inner pilot
5±8840±2573±0 (2) ,stud and nut 5±8840±0127±0
(4) and outer pilot 5±8840±2575±0 (1) through inner
and outer bearings.2. Tighten the nut to the specified torque.
Torque: 2.3 N´m (23kg´cm/20 lb in)
425RW030
3. Clean the side bearing bores. Place discs and dial
indicator on to arbor, and place tool into position in
side bearing bores. Install and tighten the bearing
caps to the specified torque.
425RW031
Legend
(1) Dial Indicator: 5±8840±0126±0
(2) Gauge Plate: 5±8840±2572±0
(3) Disc (2 pcs.): 5±8840±2577±0
(4) Arbor: 5±8840±0128±0
Page 517 of 3573
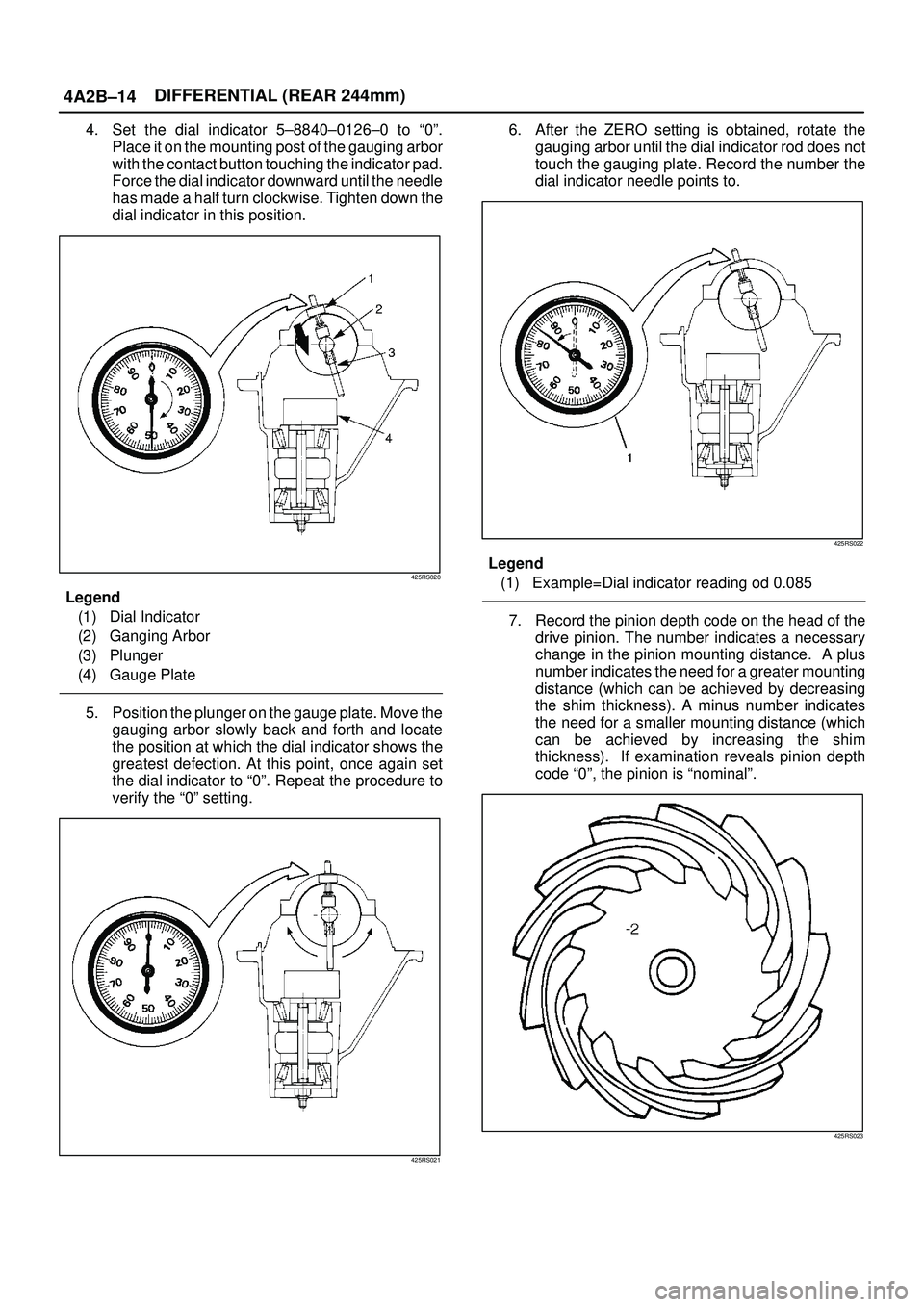
4A2B±14DIFFERENTIAL (REAR 244mm)
4. Set the dial indicator 5±8840±0126±0 to ª0º.
Place it on the mounting post of the gauging arbor
with the contact button touching the indicator pad.
Force the dial indicator downward until the needle
has made a half turn clockwise. Tighten down the
dial indicator in this position.
425RS020
Legend
(1) Dial Indicator
(2) Ganging Arbor
(3) Plunger
(4) Gauge Plate
5. Position the plunger on the gauge plate. Move the
gauging arbor slowly back and forth and locate
the position at which the dial indicator shows the
greatest defection. At this point, once again set
the dial indicator to ª0º. Repeat the procedure to
verify the ª0º setting.
425RS021
6. After the ZERO setting is obtained, rotate the
gauging arbor until the dial indicator rod does not
touch the gauging plate. Record the number the
dial indicator needle points to.
425RS022
Legend
(1) Example=Dial indicator reading od 0.085
7. Record the pinion depth code on the head of the
drive pinion. The number indicates a necessary
change in the pinion mounting distance. A plus
number indicates the need for a greater mounting
distance (which can be achieved by decreasing
the shim thickness). A minus number indicates
the need for a smaller mounting distance (which
can be achieved by increasing the shim
thickness). If examination reveals pinion depth
code ª0º, the pinion is ªnominalº.
425RS023
Page 518 of 3573
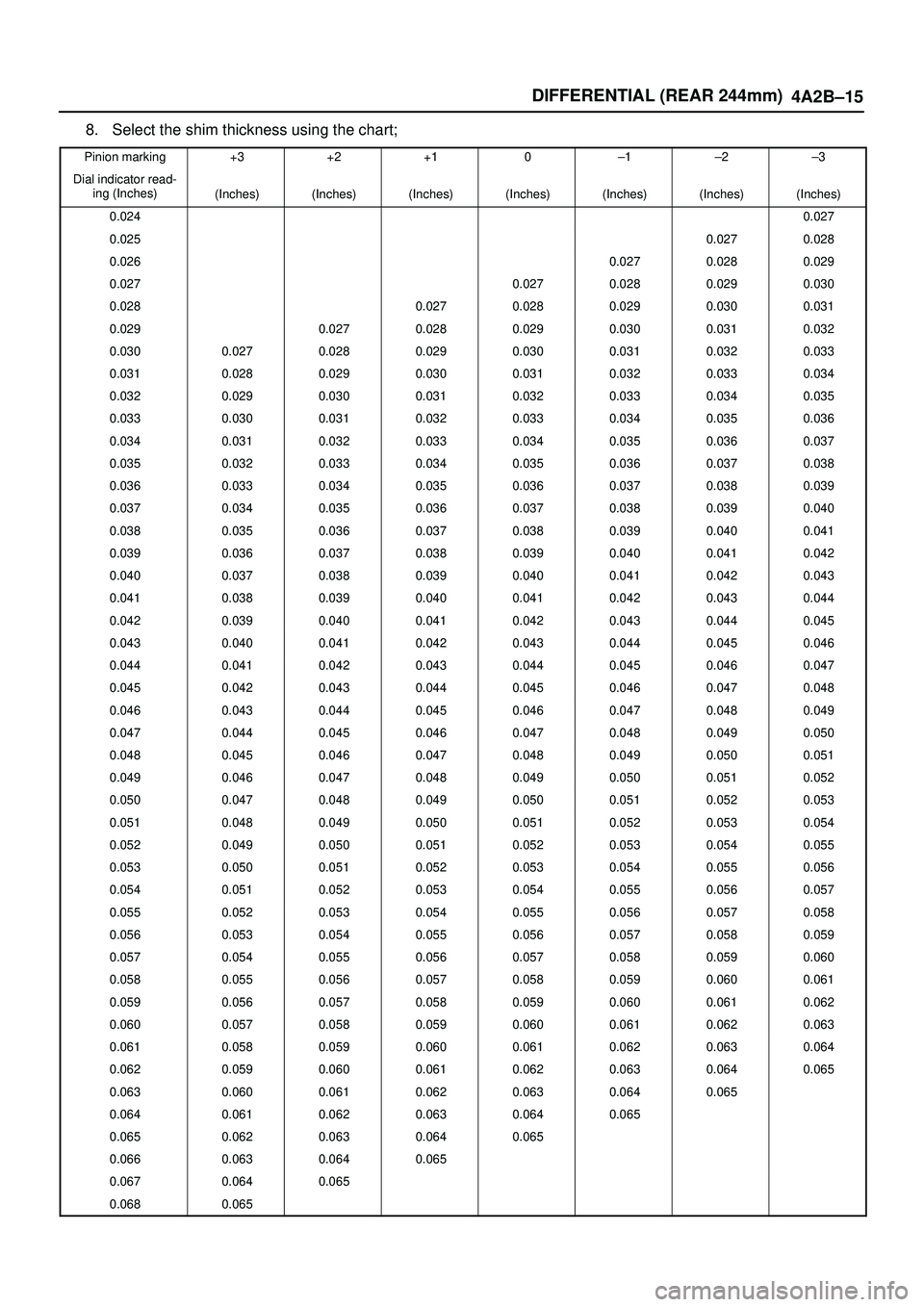
DIFFERENTIAL (REAR 244mm)
4A2B±15
8. Select the shim thickness using the chart;
Pinion marking+3+2+10±1±2±3
Dial indicator read-
ing (Inches)(Inches)(Inches)(Inches)(Inches)(Inches)(Inches)(Inches)
0.0240.027
0.0250.0270.028
0.0260.0270.0280.029
0.0270.0270.0280.0290.030
0.0280.0270.0280.0290.0300.031
0.0290.0270.0280.0290.0300.0310.032
0.0300.0270.0280.0290.0300.0310.0320.033
0.0310.0280.0290.0300.0310.0320.0330.034
0.0320.0290.0300.0310.0320.0330.0340.035
0.0330.0300.0310.0320.0330.0340.0350.036
0.0340.0310.0320.0330.0340.0350.0360.037
0.0350.0320.0330.0340.0350.0360.0370.038
0.0360.0330.0340.0350.0360.0370.0380.039
0.0370.0340.0350.0360.0370.0380.0390.040
0.0380.0350.0360.0370.0380.0390.0400.041
0.0390.0360.0370.0380.0390.0400.0410.042
0.0400.0370.0380.0390.0400.0410.0420.043
0.0410.0380.0390.0400.0410.0420.0430.044
0.0420.0390.0400.0410.0420.0430.0440.045
0.0430.0400.0410.0420.0430.0440.0450.046
0.0440.0410.0420.0430.0440.0450.0460.047
0.0450.0420.0430.0440.0450.0460.0470.048
0.0460.0430.0440.0450.0460.0470.0480.049
0.0470.0440.0450.0460.0470.0480.0490.050
0.0480.0450.0460.0470.0480.0490.0500.051
0.0490.0460.0470.0480.0490.0500.0510.052
0.0500.0470.0480.0490.0500.0510.0520.053
0.0510.0480.0490.0500.0510.0520.0530.054
0.0520.0490.0500.0510.0520.0530.0540.055
0.0530.0500.0510.0520.0530.0540.0550.056
0.0540.0510.0520.0530.0540.0550.0560.057
0.0550.0520.0530.0540.0550.0560.0570.058
0.0560.0530.0540.0550.0560.0570.0580.059
0.0570.0540.0550.0560.0570.0580.0590.060
0.0580.0550.0560.0570.0580.0590.0600.061
0.0590.0560.0570.0580.0590.0600.0610.062
0.0600.0570.0580.0590.0600.0610.0620.063
0.0610.0580.0590.0600.0610.0620.0630.064
0.0620.0590.0600.0610.0620.0630.0640.065
0.0630.0600.0610.0620.0630.0640.065
0.0640.0610.0620.0630.0640.065
0.0650.0620.0630.0640.065
0.0660.0630.0640.065
0.0670.0640.065
0.0680.065
Page 519 of 3573

4A2B±16DIFFERENTIAL (REAR 244mm)
4. Place the shim (1) on the drive pinion, then install the
inner bearing (2) onto the pinion by using installer
5±8840±2574±0 and a press .
NOTE: Do not apply pressure to the roller cage. Apply
pressure only to the inner race.
425RW061
5. Install collapsible spacer. Discard the used
collapsible spacer and install a new one.
6. Install drive pinion shaft assembly.
7. Install outer bearing and oil seal slinger.
8. Use oil seal installer 5±8840±2165±0 to install a new
oil seal that has grease on seal lip.
415RW029
9. Install flange assembly.10. Install flange nut and washer.
1. Apply lubricant to the pinion threads.
2. Using the pinion flange holder 5±8840±0133±0,
tighten the nut only enough to remove the shaft
end play.
NOTE: Discard used flange nut and install new one.
415RW006
3. Adjust pinion bearing preload.
a. Measure the bearing preload by using a torque
meter and note the scale reading required to
rotate the flange.
b. Continue tightening flange nut until the specified
starting torque is obtained.
Starting torque: 1.1±1.6 N´m (11±16kg´cm/10±14
lb in)
NOTE:
a. Do not overtighten or loosen and then retighten the
nut.
b. Pinion nut torque should be in the range of
298±380 N´m (30.4±38.8kg´m/220±281 Ib ft).
425RW018
Page 520 of 3573
DIFFERENTIAL (REAR 244mm)
4A2B±17
4. Using punch 5±8840±2293±0, stake the flange
nut at two points.
NOTE: When staking, be sure to turn the nut to ensure
that there is no change in bearing preload. Make sure of
preload again as instructed in 3).
425RW062
11. Adjust ring gear backlash.
1. Attach the side bearing to the differential
assembly without shims by using installer
5±8840±2570±0 and grip 5±8840±0007±0.
425RW063
2. Insert the differential cage assembly with bearing
outer races into the side bearing bores of the
carrier.
425RS030
3. Using two sets of feeler gauges, insert a feeler
stock of sufficient thickness between each
bearing outer race and the carrier to remove all
end play. Make certain the feeler stock is pushed
to the bottom of the bearing bores.
Mount the dial indicator 5±8840±0126±0 on the
carrier so that the indicator stem is at right angles to
a tooth on the ring gear.
425RW049