Page 1209 of 3573
6E±92
ENGINE DRIVEABILITY AND EMISSIONS
Fuel System Diagnosis
StepNo Ye s Value(s) Action
221. Command the fuel pump ªONº with Tech 2.
2. Using suitable pliers which will not damage the fuel
hose, gradually apply pressure with the pliers to
pinch the flexible fuel return hose closed.
CAUTION: Do not let the fuel pressure exceed
the second specified value.
Does the fuel pressure indicated by the fuel pressure
gauge rise above the first specified value?
376 kPa
(55 psi)
414 kPa
(60 psi)
Go to Step 11Go to Step 7
231. Command the fuel pump ªONº with Tech 2.
2. Remove the fuel filler cap and listen for the sound of
the fuel pump running.
3. Turn the pump off.
Was the fuel pump running?
ÐGo to Step 7
Go to Fuel
System
Electrical Test
Chart
Page 1210 of 3573
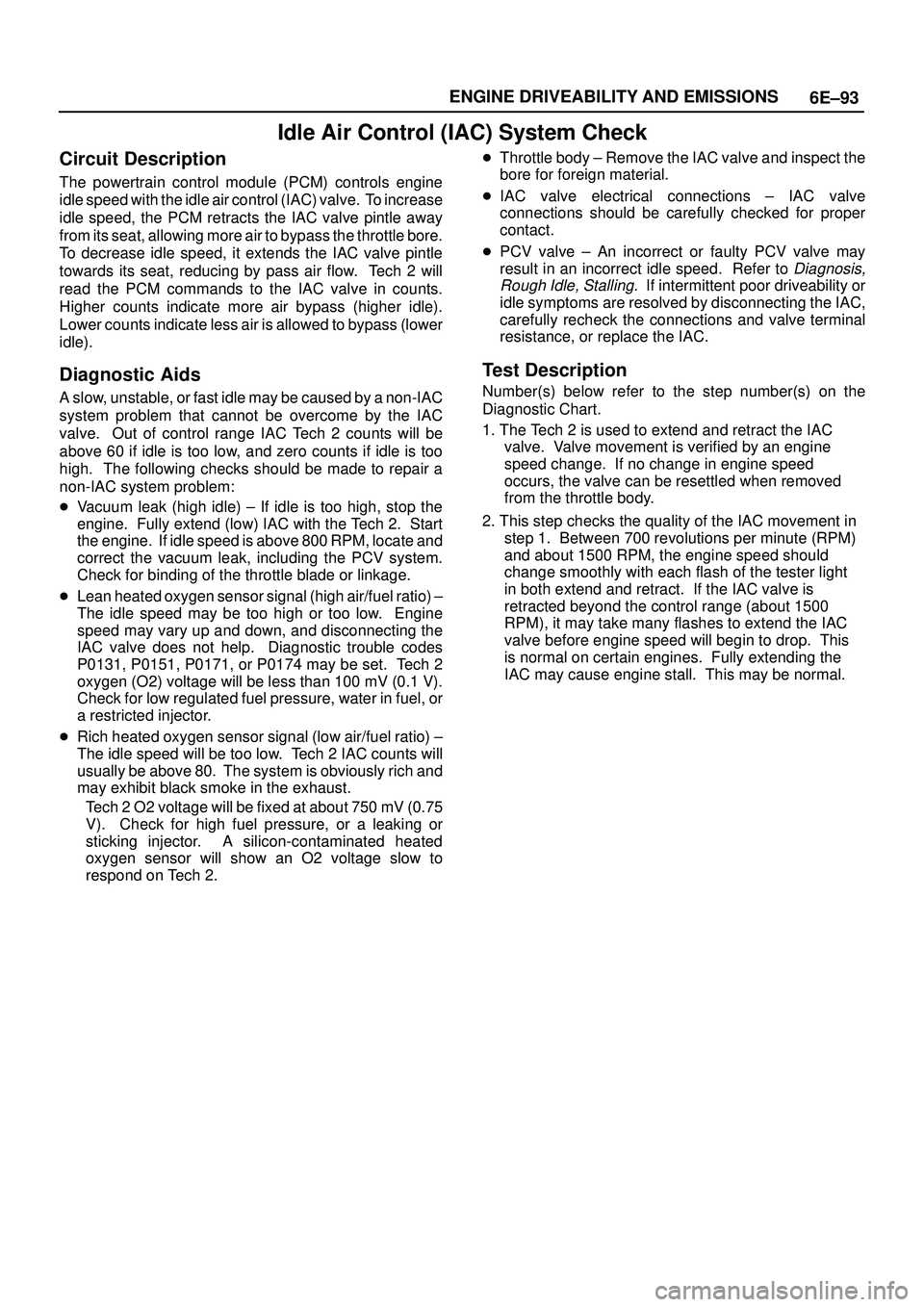
6E±93 ENGINE DRIVEABILITY AND EMISSIONS
Idle Air Control (IAC) System Check
Circuit Description
The powertrain control module (PCM) controls engine
idle speed with the idle air control (IAC) valve. To increase
idle speed, the PCM retracts the IAC valve pintle away
from its seat, allowing more air to bypass the throttle bore.
To decrease idle speed, it extends the IAC valve pintle
towards its seat, reducing by pass air flow. Tech 2 will
read the PCM commands to the IAC valve in counts.
Higher counts indicate more air bypass (higher idle).
Lower counts indicate less air is allowed to bypass (lower
idle).
Diagnostic Aids
A slow, unstable, or fast idle may be caused by a non-IAC
system problem that cannot be overcome by the IAC
valve. Out of control range IAC Tech 2 counts will be
above 60 if idle is too low, and zero counts if idle is too
high. The following checks should be made to repair a
non-IAC system problem:
Vacuum leak (high idle) ± If idle is too high, stop the
engine. Fully extend (low) IAC with the Tech 2. Start
the engine. If idle speed is above 800 RPM, locate and
correct the vacuum leak, including the PCV system.
Check for binding of the throttle blade or linkage.
Lean heated oxygen sensor signal (high air/fuel ratio) ±
The idle speed may be too high or too low. Engine
speed may vary up and down, and disconnecting the
IAC valve does not help. Diagnostic trouble codes
P0131, P0151, P0171, or P0174 may be set. Tech 2
oxygen (O2) voltage will be less than 100 mV (0.1 V).
Check for low regulated fuel pressure, water in fuel, or
a restricted injector.
Rich heated oxygen sensor signal (low air/fuel ratio) ±
The idle speed will be too low. Tech 2 IAC counts will
usually be above 80. The system is obviously rich and
may exhibit black smoke in the exhaust.
Tech 2 O2 voltage will be fixed at about 750 mV (0.75
V). Check for high fuel pressure, or a leaking or
sticking injector. A silicon-contaminated heated
oxygen sensor will show an O2 voltage slow to
respond on Tech 2.Throttle body ± Remove the IAC valve and inspect the
bore for foreign material.
IAC valve electrical connections ± IAC valve
connections should be carefully checked for proper
contact.
PCV valve ± An incorrect or faulty PCV valve may
result in an incorrect idle speed. Refer to
Diagnosis,
Rough Idle, Stalling.
If intermittent poor driveability or
idle symptoms are resolved by disconnecting the IAC,
carefully recheck the connections and valve terminal
resistance, or replace the IAC.
Test Description
Number(s) below refer to the step number(s) on the
Diagnostic Chart.
1. The Tech 2 is used to extend and retract the IAC
valve. Valve movement is verified by an engine
speed change. If no change in engine speed
occurs, the valve can be resettled when removed
from the throttle body.
2. This step checks the quality of the IAC movement in
step 1. Between 700 revolutions per minute (RPM)
and about 1500 RPM, the engine speed should
change smoothly with each flash of the tester light
in both extend and retract. If the IAC valve is
retracted beyond the control range (about 1500
RPM), it may take many flashes to extend the IAC
valve before engine speed will begin to drop. This
is normal on certain engines. Fully extending the
IAC may cause engine stall. This may be normal.
Page 1211 of 3573
6E±94
ENGINE DRIVEABILITY AND EMISSIONS
Idle Air Control (IAC) System Check
StepActionValue(s)Ye sNo
11. Ignition ªOFF.º
2. Connect the Tech 2.
3. Set the parking brake.
4. Block the wheels.
5. Turn the air conditioning ªOFF.º
6. Idle the engine in Park (A/T) or Neutral (M/T).
7. Operate the IAC test.
8. The engine speed should decrease and increase as
the IAC is cycled.
Does the RPM change?
ÐGo to Step 2Go to Step 3
2RPM should change smoothly.
Does the RPM change within the range specified?700-1500
RPM
ÐGo to Step 3
3Check the IAC passages.
Are the IAC passages OK?
ÐGo to Step 4Go to Step 5
4Clear any obstruction from the IAC passages.
Is the action complete?
ÐVerify repairÐ
5Replace the IAC. Refer to On-Vehicle Service, Idle Air
Control Valve.
Is the action complete?ÐVerify repairÐ
Page 1212 of 3573
6E±95 ENGINE DRIVEABILITY AND EMISSIONS
Knock Sensor (KS) System Check
(Engine Knock, Poor Performance, or Poor Economy)
D06RW035
Circuit Description
The knock sensor (KS) sends an AC voltage signal to the
powertrain control module (PCM). As the KS detects
engine knock, the signal to the PCM changes in amplitude
and frequency. The PCM retards timing if the engine
speed is over 900 RPM.
Diagnostic Aids
If the KS system checks OK, but detonation is the
complaint, refer to
Diagnosis, Detonation/Spark Knock.
Test Description
The numbers below refer to the step numbers on the
Diagnostic Chart.
9. The change in signal speed depends on how hard
the tapping is done. Normally there is about 1.5 to
10 mV at PCM pin A2 with the engine off. Loud
tapping should be able to make the reading jump to
20-25 mV AC.
Page 1213 of 3573
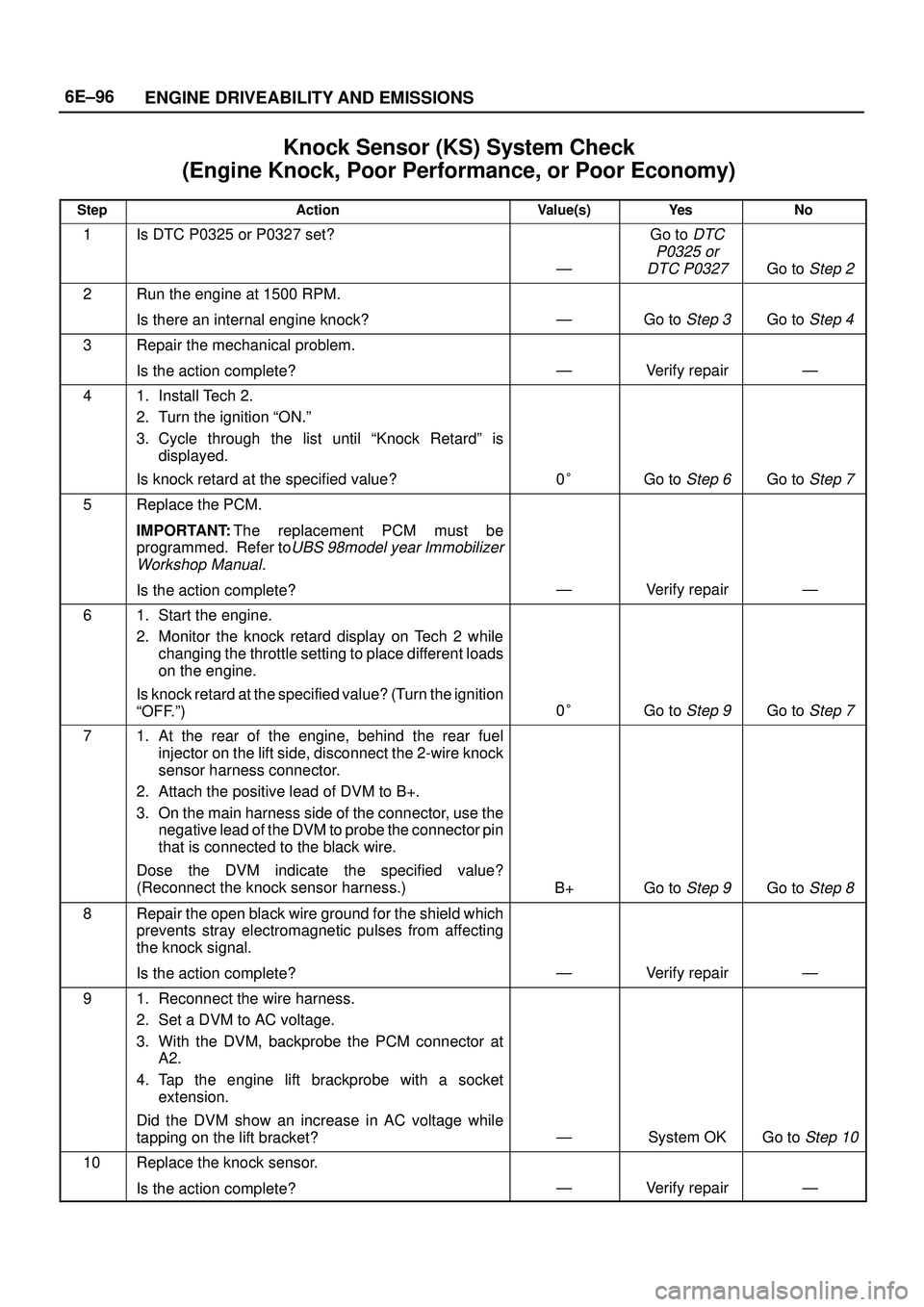
6E±96
ENGINE DRIVEABILITY AND EMISSIONS
Knock Sensor (KS) System Check
(Engine Knock, Poor Performance, or Poor Economy)
StepActionValue(s)Ye sNo
1Is DTC P0325 or P0327 set?
Ð
Go to DTC
P0325 or
DTC P0327
Go to Step 2
2Run the engine at 1500 RPM.
Is there an internal engine knock?
ÐGo to Step 3Go to Step 4
3Repair the mechanical problem.
Is the action complete?
ÐVerify repairÐ
41. Install Tech 2.
2. Turn the ignition ªON.º
3. Cycle through the list until ªKnock Retardº is
displayed.
Is knock retard at the specified value?
0Go to Step 6Go to Step 7
5Replace the PCM.
IMPORTANT:The replacement PCM must be
programmed. Refer to
UBS 98model year Immobilizer
Workshop Manual.
Is the action complete?ÐVerify repairÐ
61. Start the engine.
2. Monitor the knock retard display on Tech 2 while
changing the throttle setting to place different loads
on the engine.
Is knock retard at the specified value? (Turn the ignition
ªOFF.º)
0Go to Step 9Go to Step 7
71. At the rear of the engine, behind the rear fuel
injector on the lift side, disconnect the 2-wire knock
sensor harness connector.
2. Attach the positive lead of DVM to B+.
3. On the main harness side of the connector, use the
negative lead of the DVM to probe the connector pin
that is connected to the black wire.
Dose the DVM indicate the specified value?
(Reconnect the knock sensor harness.)
B+Go to Step 9Go to Step 8
8Repair the open black wire ground for the shield which
prevents stray electromagnetic pulses from affecting
the knock signal.
Is the action complete?
ÐVerify repairÐ
91. Reconnect the wire harness.
2. Set a DVM to AC voltage.
3. With the DVM, backprobe the PCM connector at
A2.
4. Tap the engine lift brackprobe with a socket
extension.
Did the DVM show an increase in AC voltage while
tapping on the lift bracket?
ÐSystem OKGo to Step 10
10Replace the knock sensor.
Is the action complete?
ÐVerify repairÐ
Page 1214 of 3573
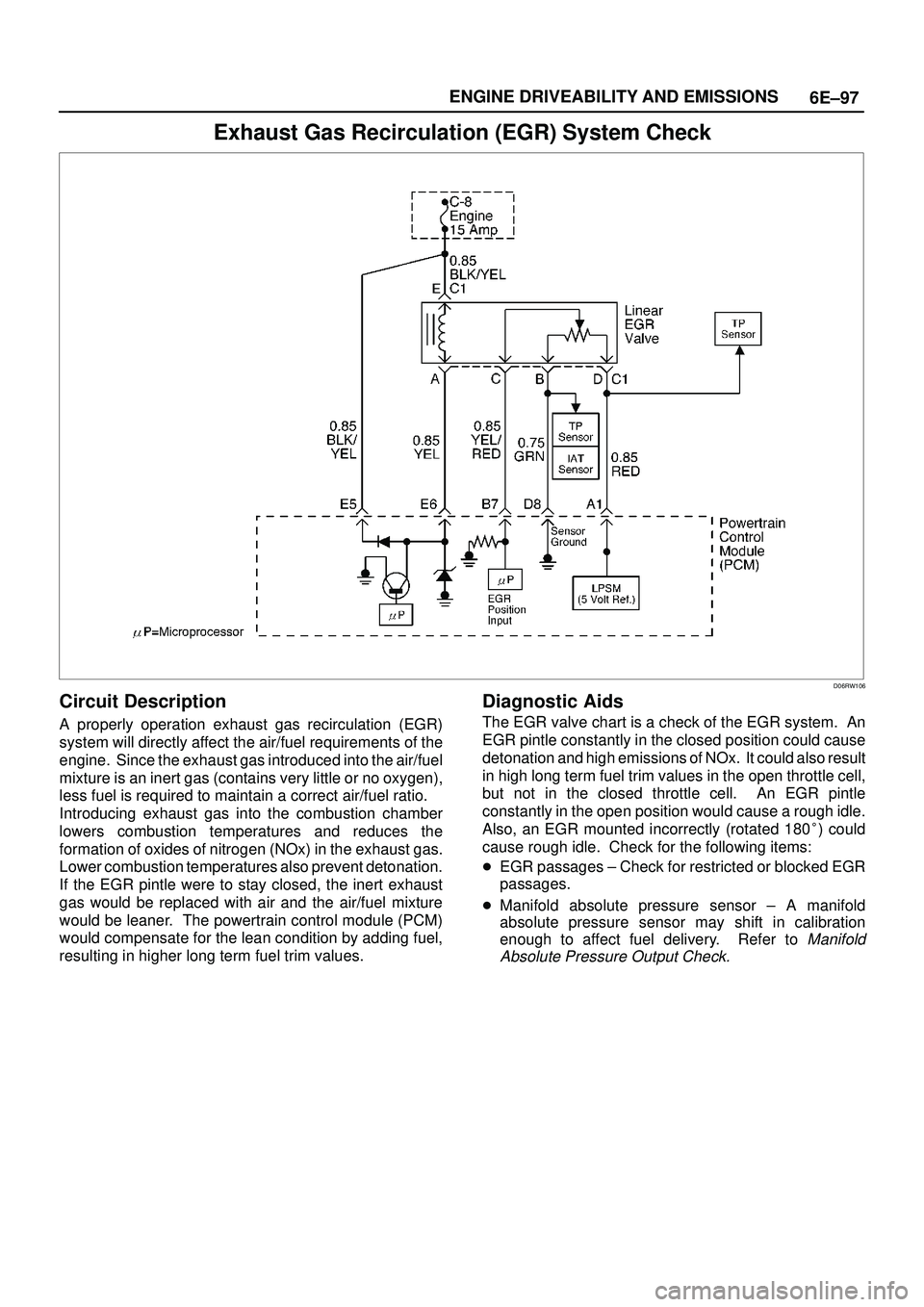
6E±97 ENGINE DRIVEABILITY AND EMISSIONS
Exhaust Gas Recirculation (EGR) System Check
D06RW106
Circuit Description
A properly operation exhaust gas recirculation (EGR)
system will directly affect the air/fuel requirements of the
engine. Since the exhaust gas introduced into the air/fuel
mixture is an inert gas (contains very little or no oxygen),
less fuel is required to maintain a correct air/fuel ratio.
Introducing exhaust gas into the combustion chamber
lowers combustion temperatures and reduces the
formation of oxides of nitrogen (NOx) in the exhaust gas.
Lower combustion temperatures also prevent detonation.
If the EGR pintle were to stay closed, the inert exhaust
gas would be replaced with air and the air/fuel mixture
would be leaner. The powertrain control module (PCM)
would compensate for the lean condition by adding fuel,
resulting in higher long term fuel trim values.
Diagnostic Aids
The EGR valve chart is a check of the EGR system. An
EGR pintle constantly in the closed position could cause
detonation and high emissions of NOx. It could also result
in high long term fuel trim values in the open throttle cell,
but not in the closed throttle cell. An EGR pintle
constantly in the open position would cause a rough idle.
Also, an EGR mounted incorrectly (rotated 180) could
cause rough idle. Check for the following items:
EGR passages ± Check for restricted or blocked EGR
passages.
Manifold absolute pressure sensor ± A manifold
absolute pressure sensor may shift in calibration
enough to affect fuel delivery. Refer to
Manifold
Absolute Pressure Output Check.
Page 1215 of 3573
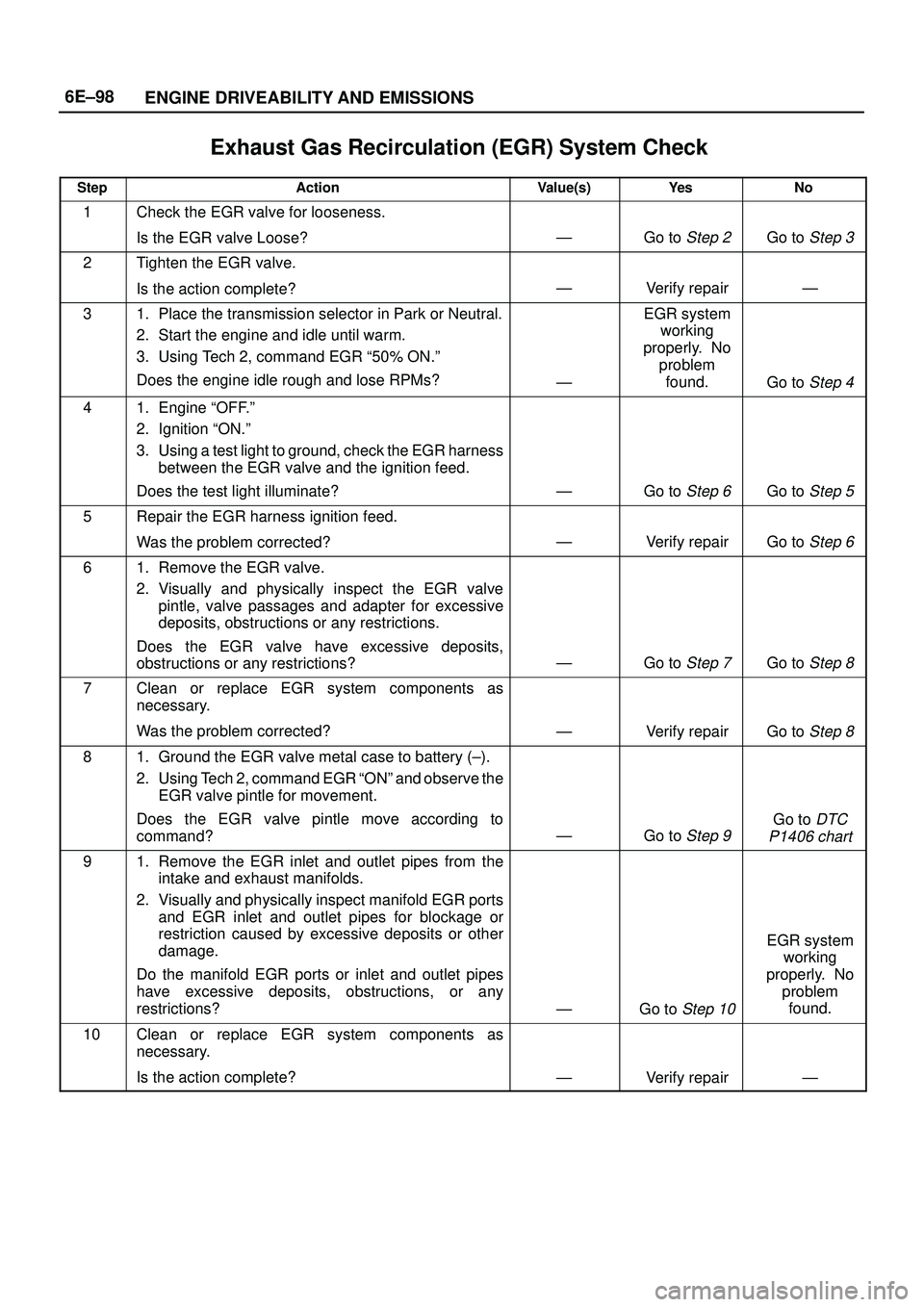
6E±98
ENGINE DRIVEABILITY AND EMISSIONS
Exhaust Gas Recirculation (EGR) System Check
StepActionValue(s)Ye sNo
1Check the EGR valve for looseness.
Is the EGR valve Loose?
ÐGo to Step 2Go to Step 3
2Tighten the EGR valve.
Is the action complete?
ÐVerify repairÐ
31. Place the transmission selector in Park or Neutral.
2. Start the engine and idle until warm.
3. Using Tech 2, command EGR ª50% ON.º
Does the engine idle rough and lose RPMs?
Ð
EGR system
working
properly. No
problem
found.
Go to Step 4
41. Engine ªOFF.º
2. Ignition ªON.º
3. Using a test light to ground, check the EGR harness
between the EGR valve and the ignition feed.
Does the test light illuminate?
ÐGo to Step 6Go to Step 5
5Repair the EGR harness ignition feed.
Was the problem corrected?
ÐVerify repairGo to Step 6
61. Remove the EGR valve.
2. Visually and physically inspect the EGR valve
pintle, valve passages and adapter for excessive
deposits, obstructions or any restrictions.
Does the EGR valve have excessive deposits,
obstructions or any restrictions?
ÐGo to Step 7Go to Step 8
7Clean or replace EGR system components as
necessary.
Was the problem corrected?
ÐVerify repairGo to Step 8
81. Ground the EGR valve metal case to battery (±).
2. Using Tech 2, command EGR ªONº and observe the
EGR valve pintle for movement.
Does the EGR valve pintle move according to
command?
ÐGo to Step 9
Go to DTC
P1406 chart
91. Remove the EGR inlet and outlet pipes from the
intake and exhaust manifolds.
2. Visually and physically inspect manifold EGR ports
and EGR inlet and outlet pipes for blockage or
restriction caused by excessive deposits or other
damage.
Do the manifold EGR ports or inlet and outlet pipes
have excessive deposits, obstructions, or any
restrictions?
ÐGo to Step 10
EGR system
working
properly. No
problem
found.
10Clean or replace EGR system components as
necessary.
Is the action complete?
ÐVerify repairÐ
Page 1216 of 3573
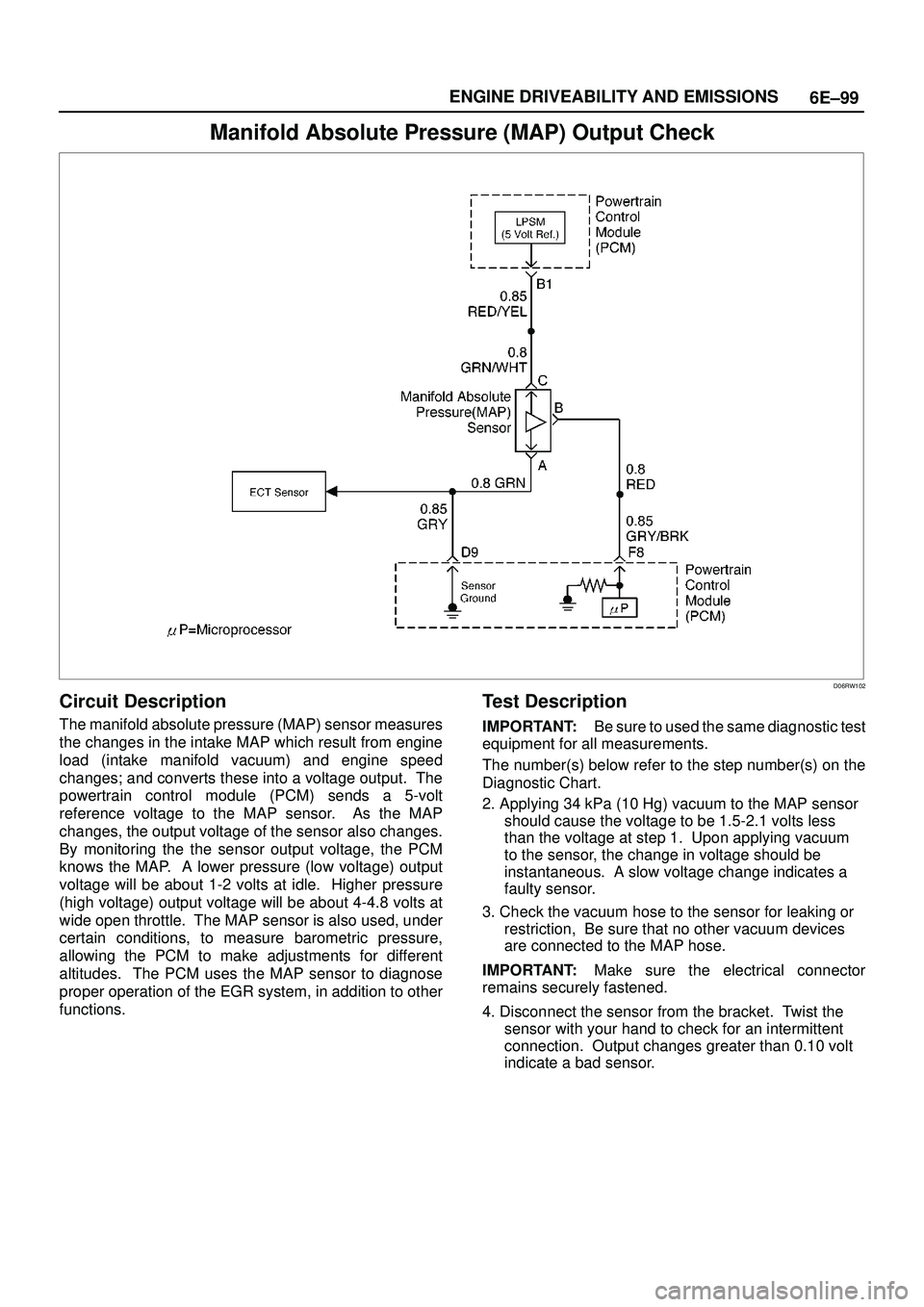
6E±99 ENGINE DRIVEABILITY AND EMISSIONS
Manifold Absolute Pressure (MAP) Output Check
D06RW102
Circuit Description
The manifold absolute pressure (MAP) sensor measures
the changes in the intake MAP which result from engine
load (intake manifold vacuum) and engine speed
changes; and converts these into a voltage output. The
powertrain control module (PCM) sends a 5-volt
reference voltage to the MAP sensor. As the MAP
changes, the output voltage of the sensor also changes.
By monitoring the the sensor output voltage, the PCM
knows the MAP. A lower pressure (low voltage) output
voltage will be about 1-2 volts at idle. Higher pressure
(high voltage) output voltage will be about 4-4.8 volts at
wide open throttle. The MAP sensor is also used, under
certain conditions, to measure barometric pressure,
allowing the PCM to make adjustments for different
altitudes. The PCM uses the MAP sensor to diagnose
proper operation of the EGR system, in addition to other
functions.
Test Description
IMPORTANT:Be sure to used the same diagnostic test
equipment for all measurements.
The number(s) below refer to the step number(s) on the
Diagnostic Chart.
2. Applying 34 kPa (10 Hg) vacuum to the MAP sensor
should cause the voltage to be 1.5-2.1 volts less
than the voltage at step 1. Upon applying vacuum
to the sensor, the change in voltage should be
instantaneous. A slow voltage change indicates a
faulty sensor.
3. Check the vacuum hose to the sensor for leaking or
restriction, Be sure that no other vacuum devices
are connected to the MAP hose.
IMPORTANT:Make sure the electrical connector
remains securely fastened.
4. Disconnect the sensor from the bracket. Twist the
sensor with your hand to check for an intermittent
connection. Output changes greater than 0.10 volt
indicate a bad sensor.