Page 281 of 3573
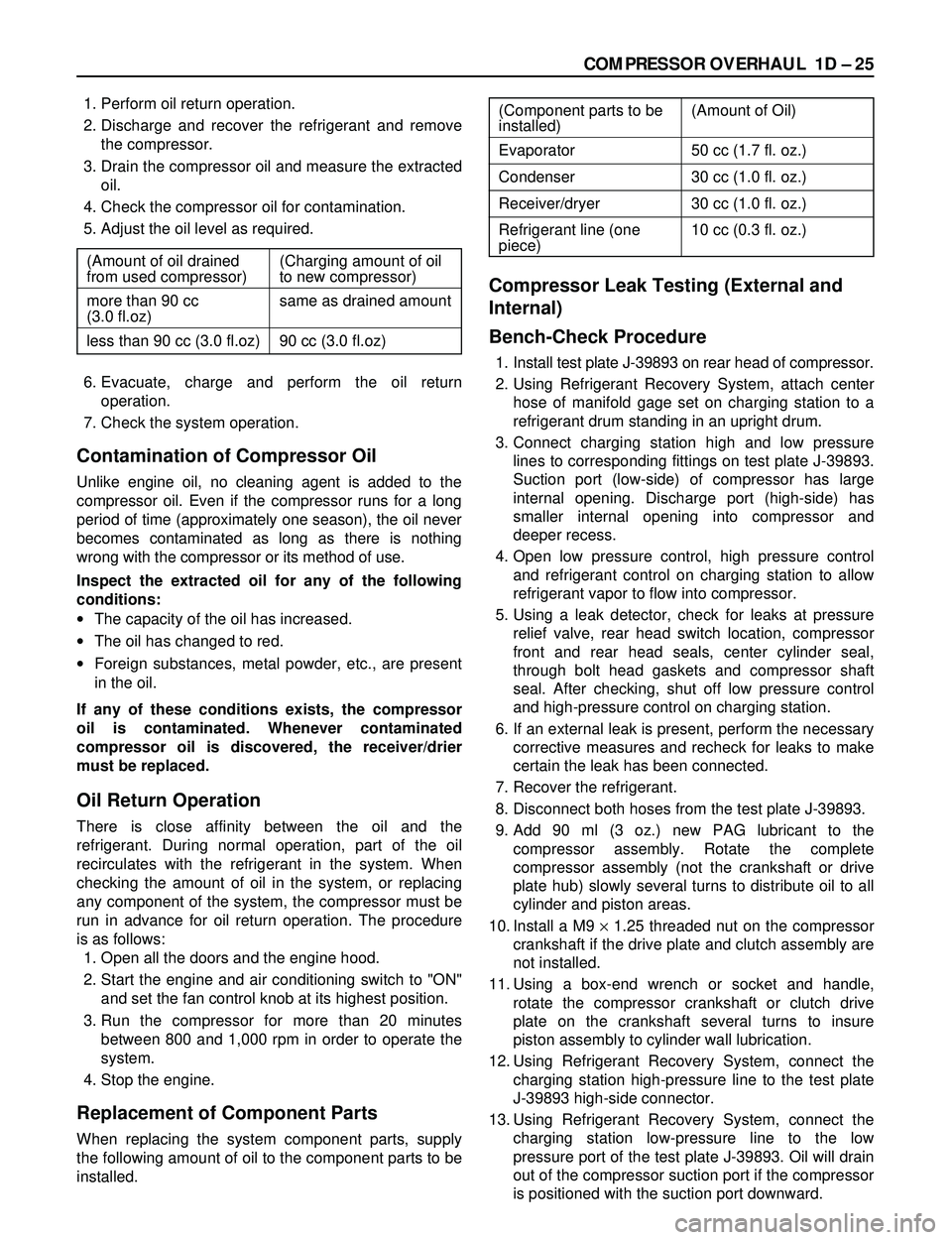
COMPRESSOR OVERHAUL 1D Ð 25
1. Perform oil return operation.
2. Discharge and recover the refrigerant and remove
the compressor.
3. Drain the compressor oil and measure the extracted
oil.
4. Check the compressor oil for contamination.
5. Adjust the oil level as required.
6. Evacuate, charge and perform the oil return
operation.
7. Check the system operation.
Contamination of Compressor Oil
Unlike engine oil, no cleaning agent is added to the
compressor oil. Even if the compressor runs for a long
period of time (approximately one season), the oil never
becomes contaminated as long as there is nothing
wrong with the compressor or its method of use.
Inspect the extracted oil for any of the following
conditions:
·The capacity of the oil has increased.
·The oil has changed to red.
·Foreign substances, metal powder, etc., are present
in the oil.
If any of these conditions exists, the compressor
oil is contaminated. Whenever contaminated
compressor oil is discovered, the receiver/drier
must be replaced.
Oil Return Operation
There is close affinity between the oil and the
refrigerant. During normal operation, part of the oil
recirculates with the refrigerant in the system. When
checking the amount of oil in the system, or replacing
any component of the system, the compressor must be
run in advance for oil return operation. The procedure
is as follows:
1. Open all the doors and the engine hood.
2. Start the engine and air conditioning switch to "ON"
and set the fan control knob at its highest position.
3. Run the compressor for more than 20 minutes
between 800 and 1,000 rpm in order to operate the
system.
4. Stop the engine.
Replacement of Component Parts
When replacing the system component parts, supply
the following amount of oil to the component parts to be
installed.
Compressor Leak Testing (External and
Internal)
Bench-Check Procedure
1. Install test plate J-39893 on rear head of compressor.
2. Using Refrigerant Recovery System, attach center
hose of manifold gage set on charging station to a
refrigerant drum standing in an upright drum.
3. Connect charging station high and low pressure
lines to corresponding fittings on test plate J-39893.
Suction port (low-side) of compressor has large
internal opening. Discharge port (high-side) has
smaller internal opening into compressor and
deeper recess.
4. Open low pressure control, high pressure control
and refrigerant control on charging station to allow
refrigerant vapor to flow into compressor.
5. Using a leak detector, check for leaks at pressure
relief valve, rear head switch location, compressor
front and rear head seals, center cylinder seal,
through bolt head gaskets and compressor shaft
seal. After checking, shut off low pressure control
and high-pressure control on charging station.
6. If an external leak is present, perform the necessary
corrective measures and recheck for leaks to make
certain the leak has been connected.
7. Recover the refrigerant.
8. Disconnect both hoses from the test plate J-39893.
9. Add 90 ml (3 oz.) new PAG lubricant to the
compressor assembly. Rotate the complete
compressor assembly (not the crankshaft or drive
plate hub) slowly several turns to distribute oil to all
cylinder and piston areas.
10. Install a M9 ´1.25 threaded nut on the compressor
crankshaft if the drive plate and clutch assembly are
not installed.
11. Using a box-end wrench or socket and handle,
rotate the compressor crankshaft or clutch drive
plate on the crankshaft several turns to insure
piston assembly to cylinder wall lubrication.
12. Using Refrigerant Recovery System, connect the
charging station high-pressure line to the test plate
J-39893 high-side connector.
13. Using Refrigerant Recovery System, connect the
charging station low-pressure line to the low
pressure port of the test plate J-39893. Oil will drain
out of the compressor suction port if the compressor
is positioned with the suction port downward. (Component parts to be (Amount of Oil)
installed)
Evaporator 50 cc (1.7 fl. oz.)
Condenser 30 cc (1.0 fl. oz.)
Receiver/dryer 30 cc (1.0 fl. oz.)
Refrigerant line (one 10 cc (0.3 fl. oz.)
piece)
(Amount of oil drained (Charging amount of oil
from used compressor) to new compressor)
more than 90 cc same as drained amount
(3.0 fl.oz)
less than 90 cc (3.0 fl.oz) 90 cc (3.0 fl.oz)
Page 282 of 3573

1D Ð 26 COMPRESSOR OVERHAUL
14. Attach the compressor to the J-34992 holding
fixture and mount the compressor in a vise so that
the compressor will be in a horizontal position and
the shaft can be turned with a wrench.
15. Using a wrench, rotate the compressor crankshaft
or drive plate hub ten complete revolutions at a
speed of approximately one-revolution per second
turning the compressor at less than one-revolution
per second can result in a lower pump-up pressure
and disqualify a good pumping compressor.
16. Observe the reading on high-pressure gauge at the
completion of the tenth revolution of the
compressor. The pressure reading for a good
pumping compressor should be 690 kPa (100 psi)
or above. A pressure reading of less than 620 kPa
(90 psi) would indicate one or more suction and/or
discharge valves leaking an internal leak, or an
inoperative valve, and the refrigerant must be
recovered and the compressor disassembled and
checked for cause of leak. Repair as needed,
reassemble and repeat the pump-up test. Externally
leak test.
17. When the pressure pump-up test is completed,
recover the refrigerant from the high-side and
remove the test plate J-39893.
18. Tilt the compressor so that the compressor suction
and discharge ports are down. Drain the PAG
lubricant from the compressor.
19. Allow the compressor to drain for 10 minutes, then
refill with the proper amount of PAG lubricant, per
oil balance procedure described previously. The
PAG lubricant may be poured into the suction port.
If further assembly or processing is required, a
shipping plate or test plate J-39893 should be
installed to keep out air, dirt and moisture until the
compressor is installed.
Page 283 of 3573
SERVICE INFORMATION 00 – 1
SECTION 00
SERVICE INFORMATION
CONTENTS
PAGE
Troubleshooting ............................................................................................................... 00 – 3
Main Data and Specifications ......................................................................................... 00 – 11
Service Standard.............................................................................................................. 00 – 12
Servicing ........................................................................................................................... 00 – 13
Fixing Torque.................................................................................................................... 00 – 15
Special Tools .................................................................................................................... 00 – 19
Page 284 of 3573
00 – 2 SERVICE INFORMATION
MEMO
Page 285 of 3573
SERVICE INFORMATION 00 – 3
TROUBLESHOOTING
CONTENTS
PAGE
General Information ........................................................................................................ 00 – 4
General Troubleshooting ................................................................................................ 00 – 4
Power Steering System .................................................................................................. 00 – 7
Power Steering Pump ..................................................................................................... 00 – 8
Steering Column .............................................................................................................. 00 – 9
Page 286 of 3573
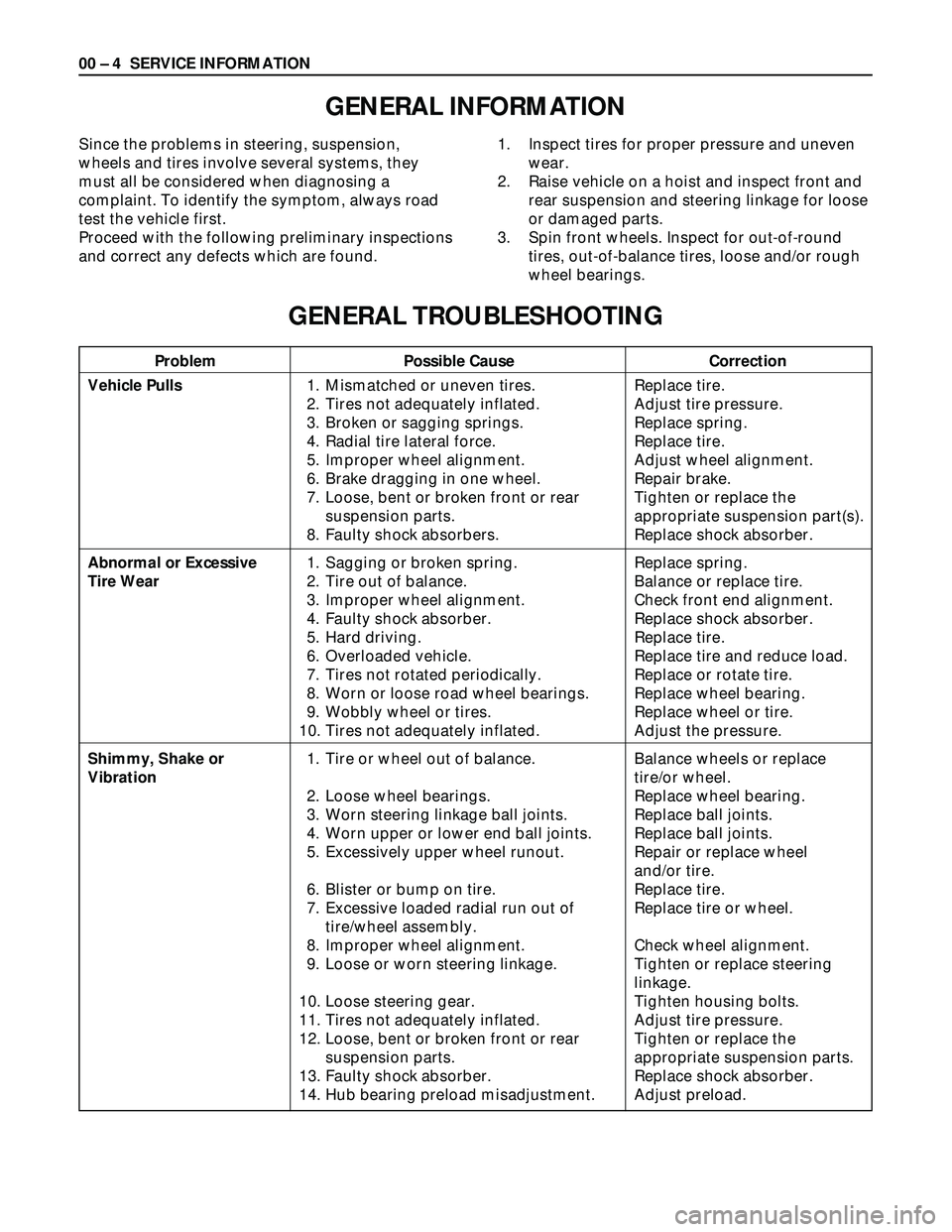
Problem Possible Cause Correction
00 – 4 SERVICE INFORMATION
GENERAL INFORMATION
Since the problems in steering, suspension,
wheels and tires involve several systems, they
must all be considered when diagnosing a
complaint. To identify the symptom, always road
test the vehicle first.
Proceed with the following preliminary inspections
and correct any defects which are found.1. Inspect tires for proper pressure and uneven
wear.
2. Raise vehicle on a hoist and inspect front and
rear suspension and steering linkage for loose
or damaged parts.
3. Spin front wheels. Inspect for out-of-round
tires, out-of-balance tires, loose and/or rough
wheel bearings.
GENERAL TROUBLESHOOTING
Vehicle Pulls
Abnormal or Excessive
Tire Wear
Shimmy, Shake or
Vibration1. Mismatched or uneven tires.
2. Tires not adequately inflated.
3. Broken or sagging springs.
4. Radial tire lateral force.
5. Improper wheel alignment.
6. Brake dragging in one wheel.
7. Loose, bent or broken front or rear
suspension parts.
8. Faulty shock absorbers.
1. Sagging or broken spring.
2. Tire out of balance.
3. Improper wheel alignment.
4. Faulty shock absorber.
5. Hard driving.
6. Overloaded vehicle.
7. Tires not rotated periodically.
8. Worn or loose road wheel bearings.
9. Wobbly wheel or tires.
10. Tires not adequately inflated.
1. Tire or wheel out of balance.
2. Loose wheel bearings.
3. Worn steering linkage ball joints.
4. Worn upper or lower end ball joints.
5. Excessively upper wheel runout.
6. Blister or bump on tire.
7. Excessive loaded radial run out of
tire/wheel assembly.
8. Improper wheel alignment.
9. Loose or worn steering linkage.
10. Loose steering gear.
11. Tires not adequately inflated.
12. Loose, bent or broken front or rear
suspension parts.
13. Faulty shock absorber.
14. Hub bearing preload misadjustment.Replace tire.
Adjust tire pressure.
Replace spring.
Replace tire.
Adjust wheel alignment.
Repair brake.
Tighten or replace the
appropriate suspension part(s).
Replace shock absorber.
Replace spring.
Balance or replace tire.
Check front end alignment.
Replace shock absorber.
Replace tire.
Replace tire and reduce load.
Replace or rotate tire.
Replace wheel bearing.
Replace wheel or tire.
Adjust the pressure.
Balance wheels or replace
tire/or wheel.
Replace wheel bearing.
Replace ball joints.
Replace ball joints.
Repair or replace wheel
and/or tire.
Replace tire.
Replace tire or wheel.
Check wheel alignment.
Tighten or replace steering
linkage.
Tighten housing bolts.
Adjust tire pressure.
Tighten or replace the
appropriate suspension parts.
Replace shock absorber.
Adjust preload.
Page 287 of 3573

SERVICE INFORMATION 00 – 5
Problem Possible Cause Correction
GENERAL TROUBLESHOOTING (CONT.)
Wheel Tramp or Hop
Hard Steering
Too Much Play In
Steering
Poor Steering Wheel
Returnability
Abnormal Noise1. Blister or bump on tire.
2. Improper shock absorber operation
1. Bind in steering linkage ball studs,
upper or lower end ball joint.
2. Improper wheel alignment.
3. Steering gear misadjustment.
4. Tire not adequately inflated.
5. Bind in steering column or shaft.
6. Improper power steering system
operation.
1. Wheel bearings worn.
2. Loose steering gear or linkage.
3. Steering gear misadjustment.
4. Worn or loose steering shaft universal
joint.
5. Worn steering linkage ball joints.
6. Worn upper or lower end ball joints.
1. Bind in steering linkage ball joints.
2. Bind in upper or lower end ball joints.
3. Bind in steering column and shaft.
4. Bind in steering gear.
5. Improper wheel alignment.
6. Tires not adequately inflated.
7. Loose steering wheel nut.
8. Worn wheel bearing.
1. Worn, sticky or loose upper or lower
end ball joint, steering linkage ball
joints or drive axle joints.
2. Faulty shock absorbers.
3. Worn upper or lower control arm bushing.
4. Loose stabilizer bar.
5. Loose wheel nuts.
6. Loose suspension bolts or nuts.
7. Broken or otherwise damaged wheel
bearings.
8. Broken suspension springs.
9. Loose steering gear.
10. Faulty steering gear.Replace tire.
Replace shock absorber.
Replace ball joints.
Check wheel alignment.
Check and adjust steering gear
preload.
Inflate tires to proper pressure.
Repair or replace.
Repair or replace.
Refer to "Power steering
system troubleshooting."
Replace wheel bearings.
Retighten or repair.
Inspect and adjust steering
gear preload.
Retighten or replace steering
shaft.
Replace ball joints.
Replace ball joints.
Replace ball joints.
Replace ball joints.
Repair or replace.
Check and repair steering gear.
Adjust wheel alignment.
Adjust tire pressure.
Retighten.
Replace.
Replace.
Replace or repair.
Replace.
Retighten bolts.
Tighten nuts. Check for
elongated wheel nut holes.
Replace wheel if required.
Retighten suspension bolts or
nuts.
Replace wheel bearing.
Replace spring.
Retighten mounting bolt.
Check and adjust steering gear.
Page 288 of 3573
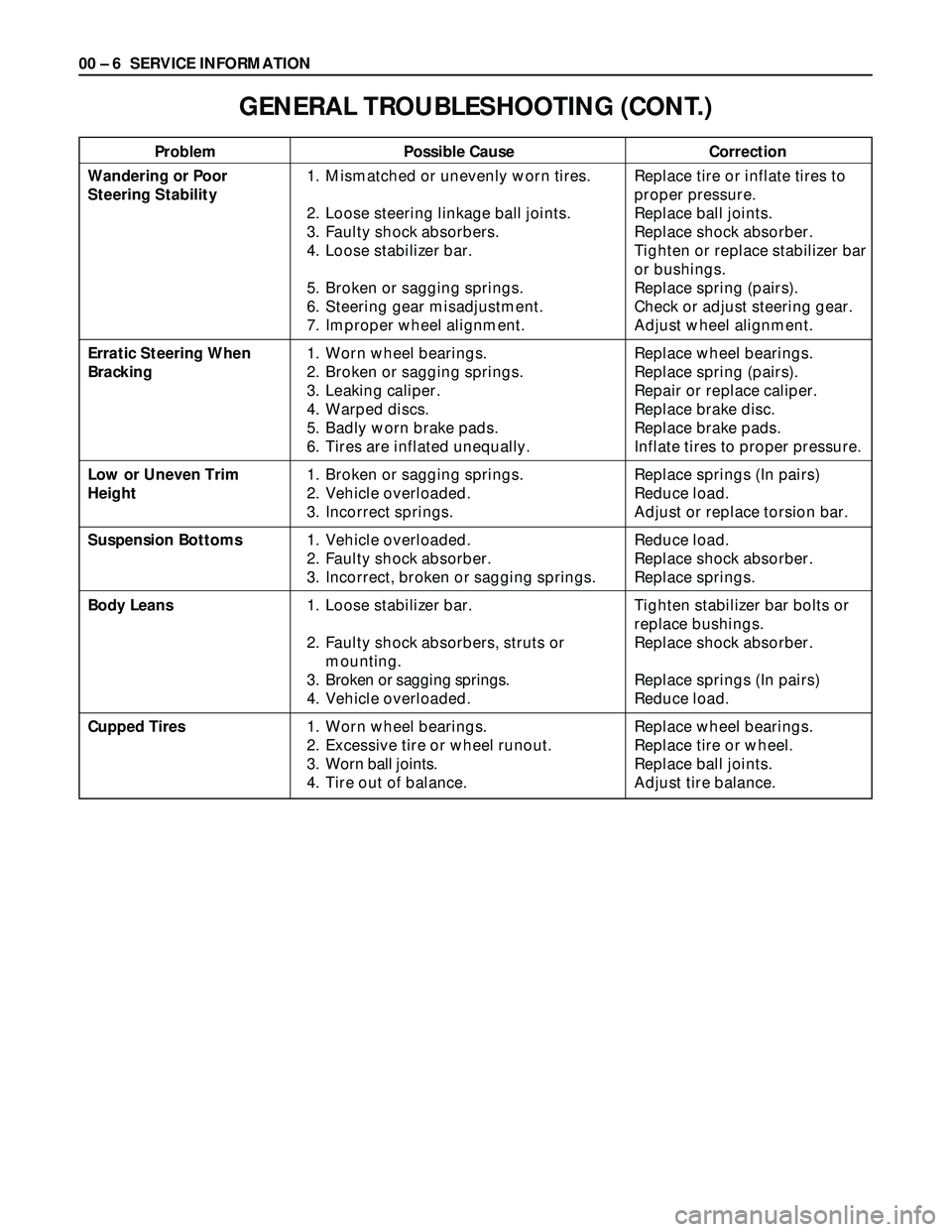
00 – 6 SERVICE INFORMATION
Problem Possible Cause Correction
GENERAL TROUBLESHOOTING (CONT.)
Wandering or Poor
Steering Stability
Erratic Steering When
Bracking
Low or Uneven Trim
Height
Suspension Bottoms
Body Leans
Cupped Tires1. Mismatched or unevenly worn tires.
2. Loose steering linkage ball joints.
3. Faulty shock absorbers.
4. Loose stabilizer bar.
5. Broken or sagging springs.
6. Steering gear misadjustment.
7. Improper wheel alignment.
1. Worn wheel bearings.
2. Broken or sagging springs.
3. Leaking caliper.
4. Warped discs.
5. Badly worn brake pads.
6. Tires are inflated unequally.
1. Broken or sagging springs.
2. Vehicle overloaded.
3. Incorrect springs.
1. Vehicle overloaded.
2. Faulty shock absorber.
3. Incorrect, broken or sagging springs.
1. Loose stabilizer bar.
2. Faulty shock absorbers, struts or
mounting.
3. Broken or sagging springs.
4. Vehicle overloaded.
1. Worn wheel bearings.
2. Excessive tire or wheel runout.
3. Worn ball joints.
4. Tire out of balance.Replace tire or inflate tires to
proper pressure.
Replace ball joints.
Replace shock absorber.
Tighten or replace stabilizer bar
or bushings.
Replace spring (pairs).
Check or adjust steering gear.
Adjust wheel alignment.
Replace wheel bearings.
Replace spring (pairs).
Repair or replace caliper.
Replace brake disc.
Replace brake pads.
Inflate tires to proper pressure.
Replace springs (In pairs)
Reduce load.
Adjust or replace torsion bar.
Reduce load.
Replace shock absorber.
Replace springs.
Tighten stabilizer bar bolts or
replace bushings.
Replace shock absorber.
Replace springs (In pairs)
Reduce load.
Replace wheel bearings.
Replace tire or wheel.
Replace ball joints.
Adjust tire balance.