Page 417 of 3383
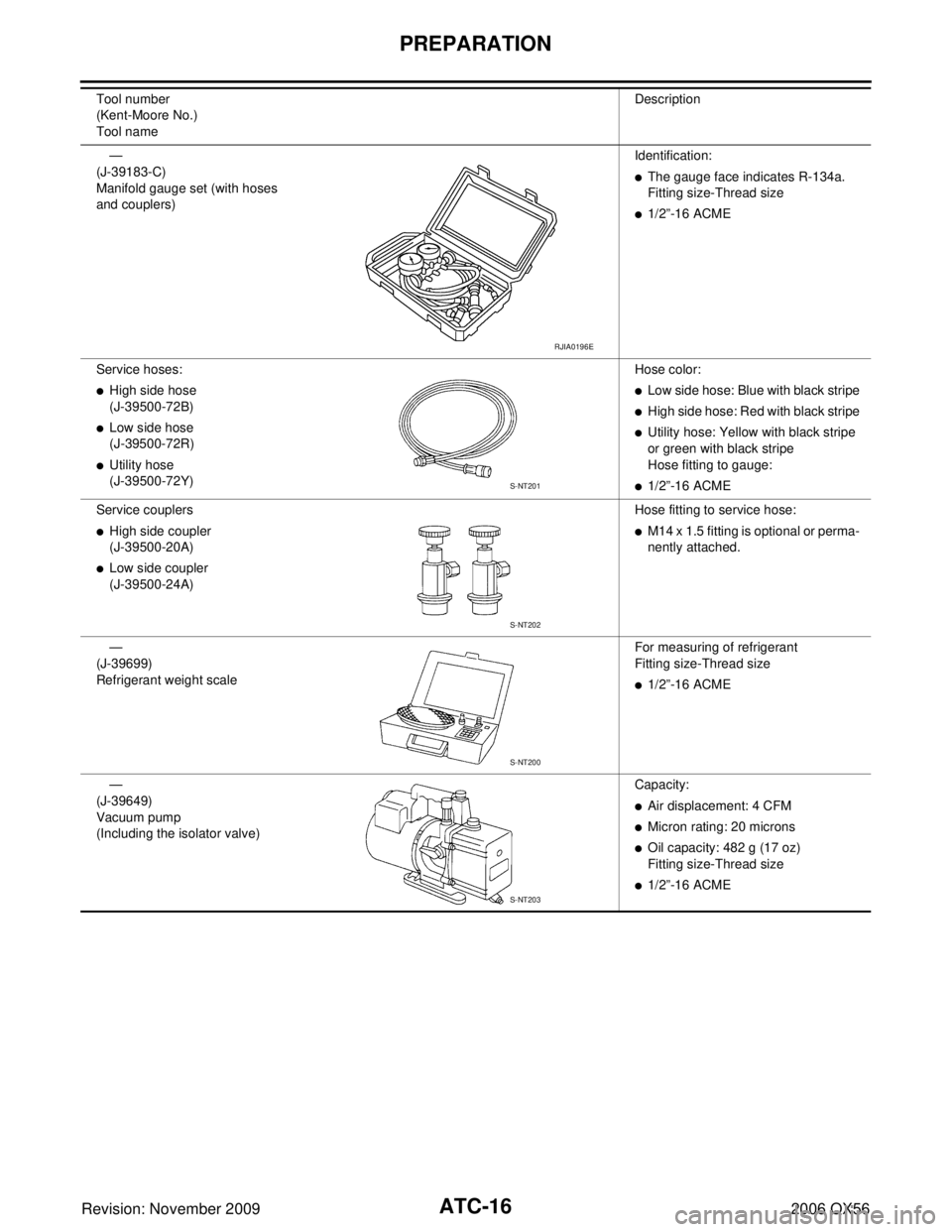
ATC-16
PREPARATION
Revision: November 20092006 QX56
—
(J-39183-C)
Manifold gauge set (with hoses
and couplers) Identification:
The gauge face indicates R-134a.
Fitting size-Thread size
1/2”
-16 ACME
Service hoses:
High side hose
(J-39500-72B)
Low side hose
(J-39500-72R)
Utility hose
(J-39500-72Y) Hose color:
Low side hose: Blue with black stripe
High side hose: Red with black stripe
Utility hose: Yellow with black stripe
or green with black stripe
Hose fitting to gauge:
1/2”
-16 ACME
Service couplers
High side coupler
(J-39500-20A)
Low side coupler
(J-39500-24A) Hose fitting to service hose:
M14 x 1.5 fitting is optional or perma-
nently attached.
—
(J-39699)
Refrigerant weight scale For measuring of refrigerant
Fitting size-Thread size
1/2”
-16 ACME
—
(J-39649)
Vacuum pump
(Including the isolator valve) Capacity:
Air displacement: 4 CFM
Micron rating: 20 microns
Oil capacity: 482 g (17 oz)
Fitting size-Thread size
1/2”
-16 ACME
Tool number
(Kent-Moore No.)
Tool name
Description
RJIA0196E
S-NT201
S-NT202
S-NT200
S-NT203
Page 418 of 3383
PREPARATIONATC-17
C
DE
F
G H
I
K L
M A
B
AT C
Revision: November 2009 2006 QX56
Commercial Service ToolsEJS003X0
Tool nameDescription
(J-41810-NI)
Refrigerant identifier equipment (R-
134a) For checking refrigerant purity and
system contamination
Power tool Loosening bolts and nuts
(J-44614)
Clutch disc holding tool Clutch disc holding tool
RJIA0197E
PBIC0190E
WHA230
Page 419 of 3383
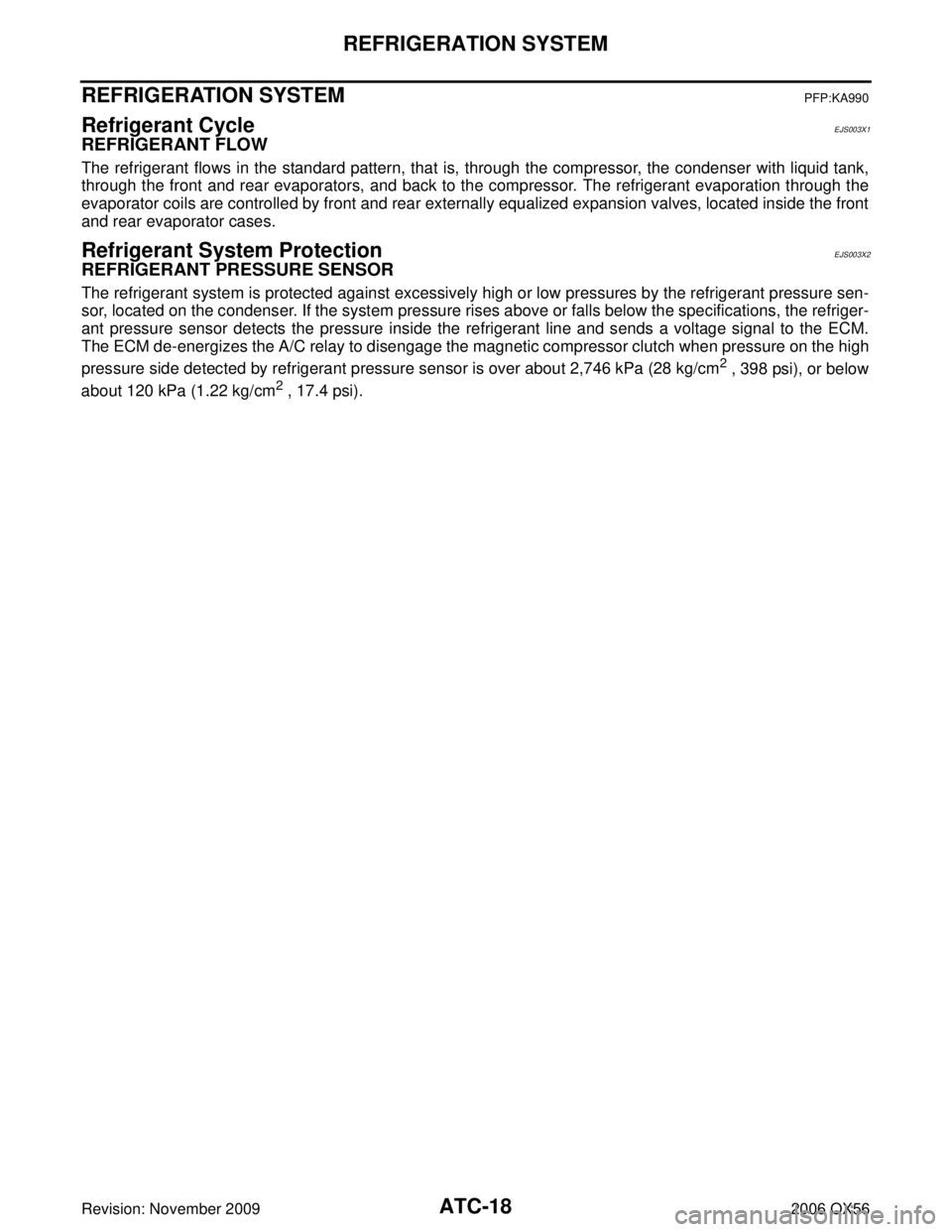
ATC-18
REFRIGERATION SYSTEM
Revision: November 20092006 QX56
REFRIGERATION SYSTEMPFP:KA990
Refrigerant CycleEJS003X1
REFRIGERANT FLOW
The refrigerant flows in the standard pattern, that is, through the compressor, the condenser with liquid tank,
through the front and rear evaporators, and back to the compressor. The refrigerant evaporation through the
evaporator coils are controlled by front and rear externally equalized expansion valves, located inside the front
and rear evaporator cases.
Refrigerant System ProtectionEJS003X2
REFRIGERANT PRESSURE SENSOR
The refrigerant system is protected against excessively high or low pressures by the refrigerant pressure sen-
sor, located on the condenser. If the system pressure rises above or falls below the specifications, the refriger-
ant pressure sensor detects the pressure inside the refrigerant line and sends a voltage signal to the ECM.
The ECM de-energizes the A/C relay to disengage the magnetic compressor clutch when pressure on the high
pressure side detected by refrigerant pressure sensor is over about 2,746 kPa (28 kg/cm
2 , 398 psi), or below
about 120 kPa (1.22 kg/cm
2 , 17.4 psi).
Page 420 of 3383
REFRIGERATION SYSTEMATC-19
C
DE
F
G H
I
K L
M A
B
AT C
Revision: November 2009 2006 QX56
PRESSURE RELIEF VALVE
The refrigerant system is also protected by a pressure relief valve, located in the rear head of the compressor.
When the pressure of refrigerant in the system increases to an abnormal level [more than 2,990 kPa (30.5 kg/
cm
2 , 433.6 psi)], the release port on the pressure relief valve automatically opens and releases refrigerant
into the atmosphere.
WJIA1342E
Page 421 of 3383
ATC-20
REFRIGERATION SYSTEM
Revision: November 20092006 QX56
Component LayoutEJS003X3
FRONT REFRIGERATION SYSTEM
WJIA0956E
Page 422 of 3383
REFRIGERATION SYSTEMATC-21
C
DE
F
G H
I
K L
M A
B
AT C
Revision: November 2009 2006 QX56
REAR REFRIGERATION SYSTEM
1. Defroster nozzle2. LH side demister duct3. LH ventilator duct
4. RH side demister duct 5. RH ventilator duct6. Center ventilator duct
7. Front heater and cooling unit assembly 8. Floor duct 9. Clips
10. Heat duct
1. Rear floor duct 2. Rear heater and cooling unit assembly 3. Rear lower overhead duct
4. Rear upper overhead duct
LJIA0142E
Page 423 of 3383
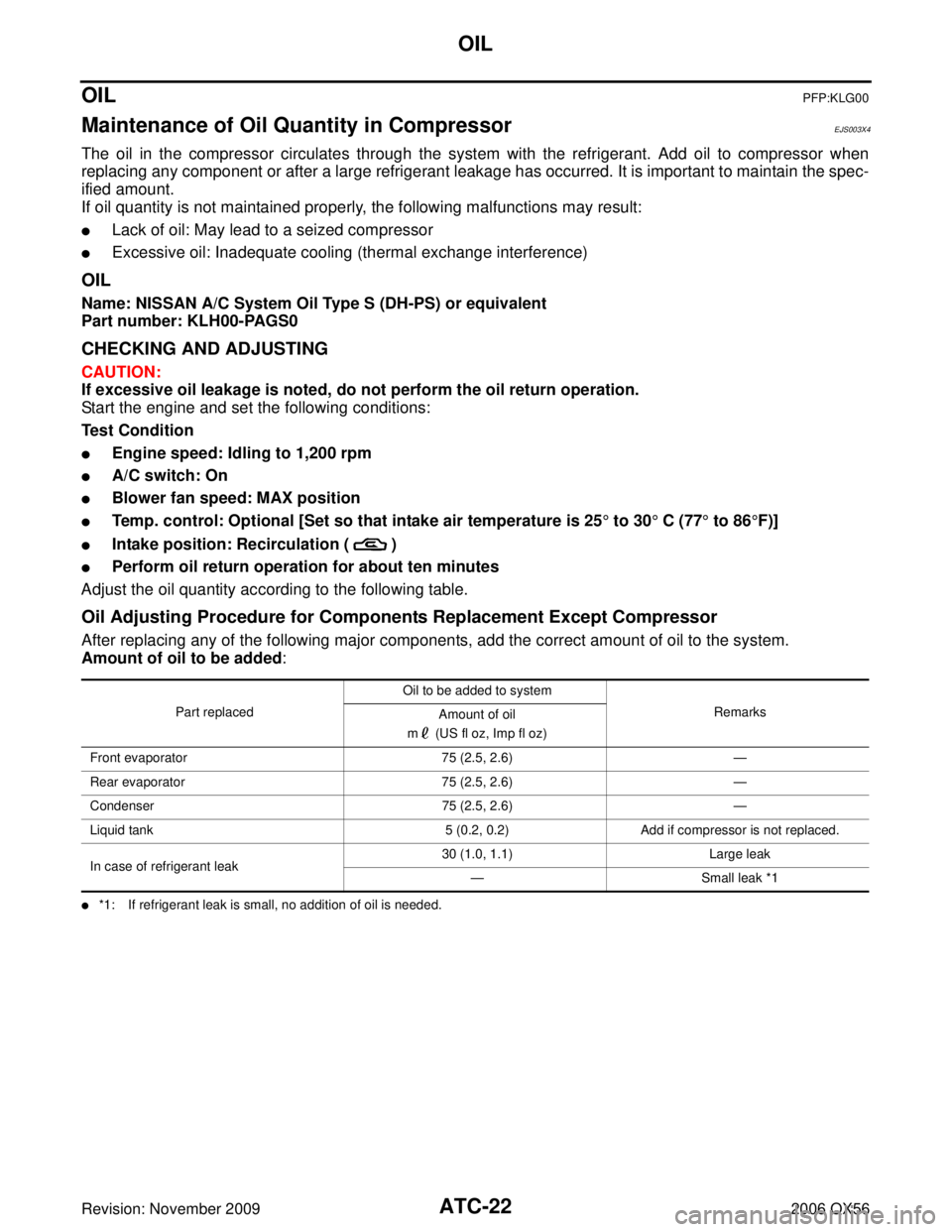
ATC-22
OIL
Revision: November 20092006 QX56
OILPFP:KLG00
Maintenance of Oil Quantity in CompressorEJS003X4
The oil in the compressor circulates through the system with the refrigerant. Add oil to compressor when
replacing any component or after a large refrigerant leakage has occurred. It is important to maintain the spec-
ified amount.
If oil quantity is not maintained properly, the following malfunctions may result:
Lack of oil: May lead to a seized compressor
Excessive oil: Inadequate cooling (thermal exchange interference)
OIL
Name: NISSAN A/C System Oil Type S (DH-PS) or equivalent
Part number: KLH00-PAGS0
CHECKING AND ADJUSTING
CAUTION:
If excessive oil leakage is noted, do not perform the oil return operation.
Start the engine and set the following conditions:
Test Condition
Engine speed: Idling to 1,200 rpm
A/C switch: On
Blower fan speed: MAX position
Temp. control: Optional [Set so that intake air temperature is 25° to 30 ° C (77 ° to 86 °F)]
Intake position: Recirculation ( )
Perform oil return operation for about ten minutes
Adjust the oil quantity according to the following table.
Oil Adjusting Procedure for Components Replacement Except Compressor
After replacing any of the following major components, add the correct amount of oil to the system.
Amount of oil to be added :
*1: If refrigerant leak is small, no addition of oil is needed.
Part replaced Oil to be added to system
Remarks
Amount of oil
m (US fl oz, Imp fl oz)
Front evaporator 75 (2.5, 2.6)—
Rear evaporator 75 (2.5, 2.6)—
Condenser 75 (2.5, 2.6)—
Liquid tank 5 (0.2, 0.2)Add if compressor is not replaced.
In case of refrigerant leak 30 (1.0, 1.1)
Large leak
— Small leak *1
Page 424 of 3383
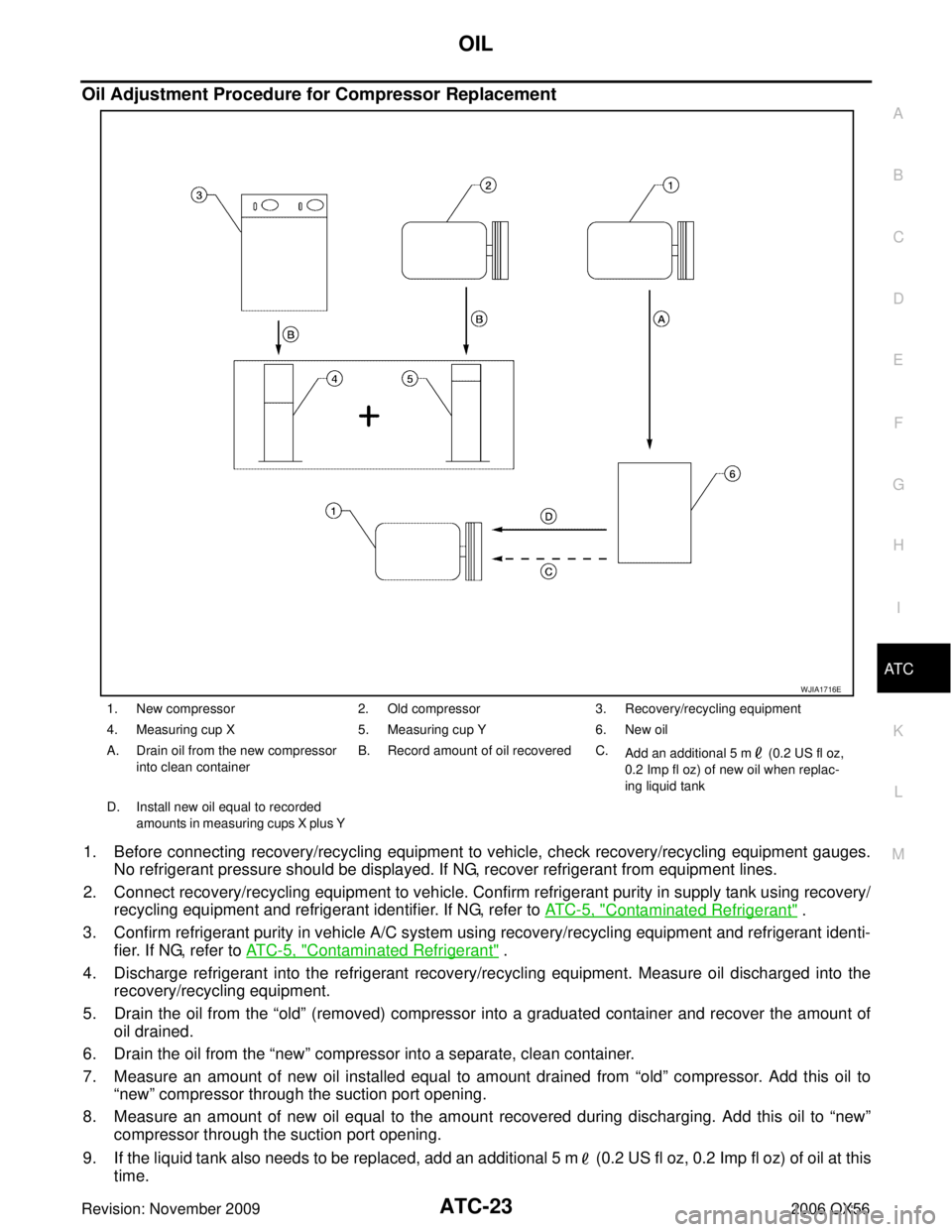
OIL
ATC-23
C
D E
F
G H
I
K L
M A
B
AT C
Revision: November 2009 2006 QX56
Oil Adjustment Procedure for Compressor Replacement
1. Before connecting recovery/recycling equipment to vehicle, check recovery/recycling equipment gauges.
No refrigerant pressure should be displayed. If NG, recover refrigerant from equipment lines.
2. Connect recovery/recycling equipment to vehicle. Confirm refrigerant purity in supply tank using recovery/ recycling equipment and refrigerant identifier. If NG, refer to AT C - 5 , "
Contaminated Refrigerant" .
3. Confirm refrigerant purity in vehicle A/C system using recovery/recycling equipment and refrigerant identi- fier. If NG, refer to AT C - 5 , "
Contaminated Refrigerant" .
4. Discharge refrigerant into the refrigerant recovery/recycling equipment. Measure oil discharged into the recovery/recycling equipment.
5. Drain the oil from the “old” (removed) compressor into a graduated container and recover the amount of
oil drained.
6. Drain the oil from the “new ” compressor into a separate, clean container.
7. Measure an amount of new oil installed equal to amount drained from “old” compressor. Add this oil to
“new ” compressor through the suction port opening.
8. Measure an amount of new oil equal to the amount recovered during discharging. Add this oil to “new”
compressor through the suction port opening.
9. If the liquid tank also needs to be replaced, add an additional 5 m (0.2 US fl oz, 0.2 Imp fl oz) of oil at this time.
1. New compressor 2. Old compressor3. Recovery/recycling equipment
4. Measuring cup X 5. Measuring cup Y6. New oil
A. Drain oil from the new compressor into clean container B. Record amount of oil recovered C.
Add an additional 5 m (0.2 US fl oz,
0.2 Imp fl oz) of new oil when replac-
ing liquid tank
D. Install new oil equal to recorded amounts in measuring cups X plus Y
WJIA1716E