Page 1985 of 3383
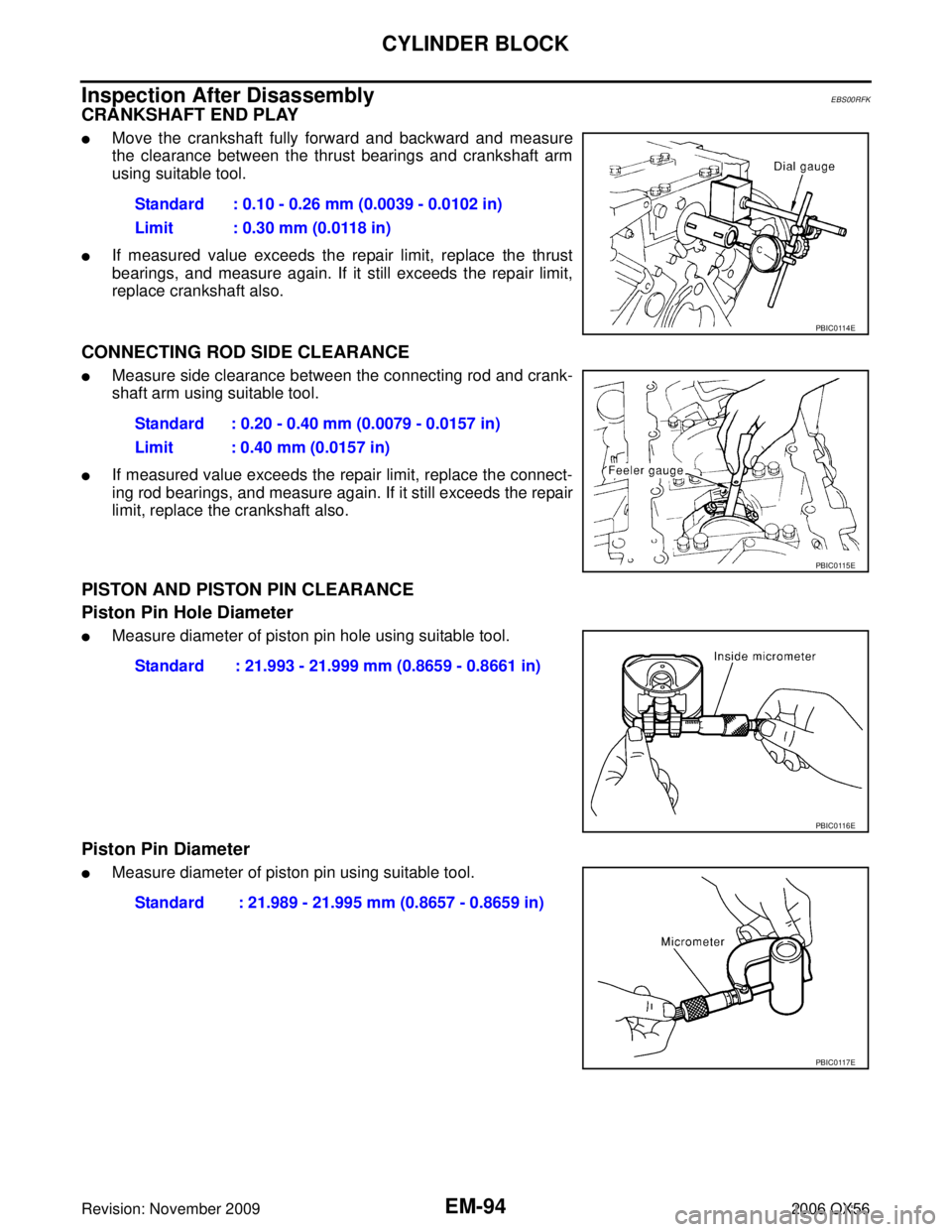
EM-94Revision: November 2009
CYLINDER BLOCK
2006 QX56
Inspection After DisassemblyEBS00RFK
CRANKSHAFT END PLAY
Move the crankshaft fully forward and backward and measure
the clearance between the thrust bearings and crankshaft arm
using suitable tool.
If measured value exceeds the repair limit, replace the thrust
bearings, and measure again. If it still exceeds the repair limit,
replace crankshaft also.
CONNECTING ROD SIDE CLEARANCE
Measure side clearance between the connecting rod and crank-
shaft arm using suitable tool.
If measured value exceeds the repair limit, replace the connect-
ing rod bearings, and measure again. If it still exceeds the repair
limit, replace the crankshaft also.
PISTON AND PISTON PIN CLEARANCE
Piston Pin Hole Diameter
Measure diameter of piston pin hole using suitable tool.
Piston Pin Diameter
Measure diameter of piston pin using suitable tool.Standard : 0.10 - 0.26 mm (0.0039 - 0.0102 in)
Limit : 0.30 mm (0.0118 in)
PBIC0114E
Standard : 0.20 - 0.40 mm (0.0079 - 0.0157 in)
Limit : 0.40 mm (0.0157 in)
PBIC0115E
Standard : 21.993 - 21.999 mm (0.8659 - 0.8661 in)
PBIC0116E
Standard : 21.989 - 21.995 mm (0.8657 - 0.8659 in)
PBIC0117E
Page 1986 of 3383
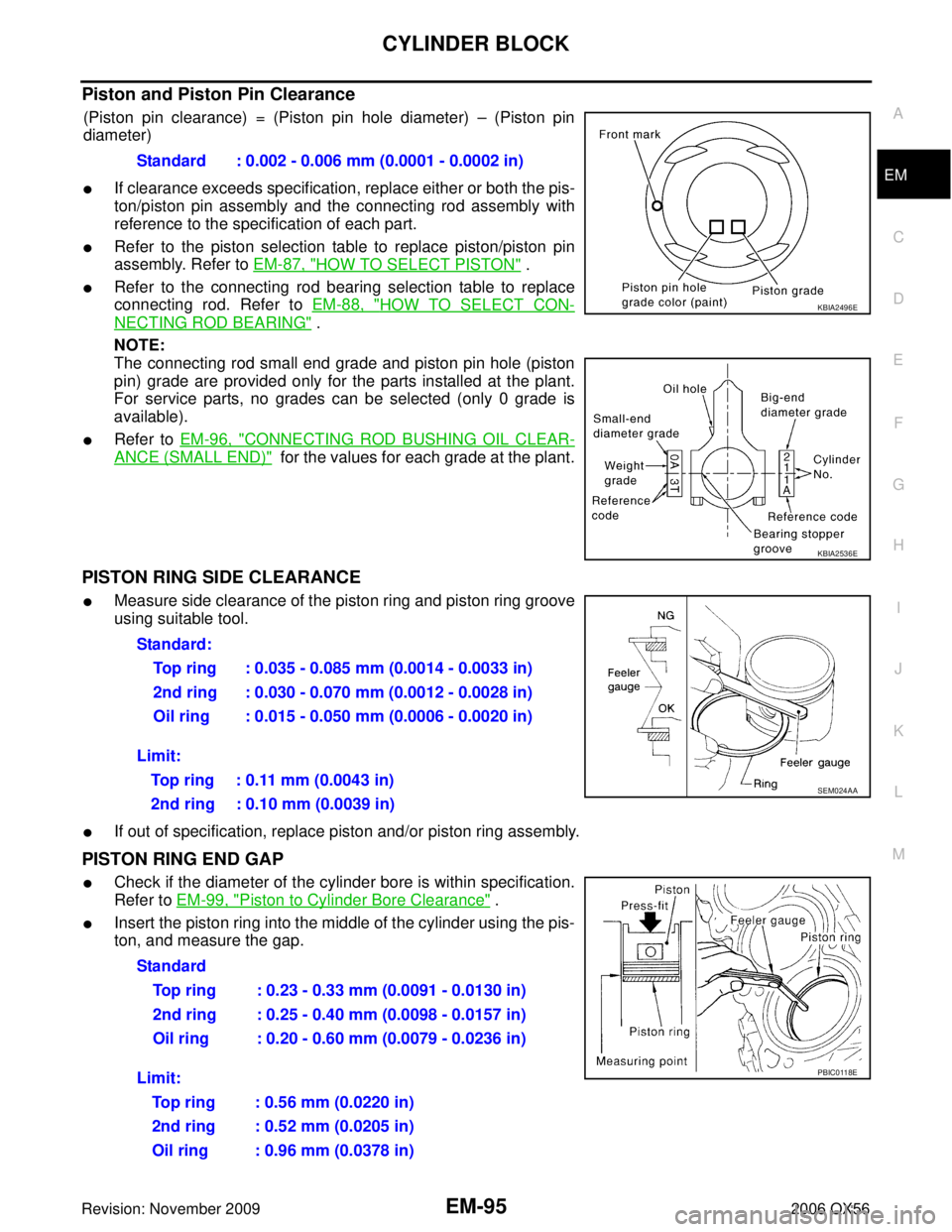
CYLINDER BLOCKEM-95
C
DE
F
G H
I
J
K L
M A
EM
Revision: November 2009 2006 QX56
Piston and Piston Pin Clearance
(Piston pin clearance) = (Piston pin hole diameter) – (Piston pin
diameter)
If clearance exceeds specification, replace either or both the pis-
ton/piston pin assembly and the connecting rod assembly with
reference to the specification of each part.
Refer to the piston selection table to replace piston/piston pin
assembly. Refer to EM-87, "
HOW TO SELECT PISTON" .
Refer to the connecting rod bearing selection table to replace
connecting rod. Refer to EM-88, "
HOW TO SELECT CON-
NECTING ROD BEARING" .
NOTE:
The connecting rod small end grade and piston pin hole (piston
pin) grade are provided only for the parts installed at the plant.
For service parts, no grades can be selected (only 0 grade is
available).
Refer to EM-96, "CONNECTING ROD BUSHING OIL CLEAR-
ANCE (SMALL END)" for the values for each grade at the plant.
PISTON RING SIDE CLEARANCE
Measure side clearance of the piston ring and piston ring groove
using suitable tool.
If out of specification, replace piston and/or piston ring assembly.
PISTON RING END GAP
Check if the diameter of the cylinder bore is within specification.
Refer to EM-99, "
Piston to Cylinder Bore Clearance" .
Insert the piston ring into the middle of the cylinder using the pis-
ton, and measure the gap.Standard : 0.002 - 0.006 mm (0.0001 - 0.0002 in)
KBIA2496E
KBIA2536E
Standard:
Top ring : 0.035 - 0.085 mm (0.0014 - 0.0033 in)
2nd ring : 0.030 - 0.070 mm (0.0012 - 0.0028 in)
Oil ring : 0.015 - 0.050 mm (0.0006 - 0.0020 in)
Limit: Top ring : 0.11 mm (0.0043 in)
2nd ring : 0.10 mm (0.0039 in)
SEM024AA
Standard Top ring : 0.23 - 0.33 mm (0.0091 - 0.0130 in)
2nd ring : 0.25 - 0.40 mm (0.0098 - 0.0157 in)
Oil ring : 0.20 - 0.60 mm (0.0079 - 0.0236 in)
Limit: Top ring : 0.56 mm (0.0220 in)
2nd ring : 0.52 mm (0.0205 in)
Oil ring : 0.96 mm (0.0378 in)
PBIC0118E
Page 1987 of 3383

EM-96Revision: November 2009
CYLINDER BLOCK
2006 QX56
If out of specification, replace piston ring. If the gap still exceeds the limit even with a new ring, re-bore the
cylinder and use oversized piston and piston ring.
CONNECTING ROD BEND AND TORSION
Check connecting rod alignment using suitable tool.
If measurement exceeds the limit, replace connecting rod
assembly.
CONNECTING ROD BEARING (BIG END)
Install the connecting rod cap without the connecting rod bearing
installed. After tightening the connecting rod bolt to the specified
torque, measure the connecting rod large end inside diameter.
Refer to EM-82, "
ASSEMBLY" .
If measurement exceeds the standard, replace connecting rod.
CONNECTING ROD BUSHING OIL CLEARANCE (SMALL END)
Connecting Rod Inside Diameter (Small End)
Measure inside diameter of bushing using suitable tool.Limit:
Bend: 0.15 mm (0.0059 in) per 100 mm (3.94 in) length
To r s i o n : 0.30 mm (0.0118 in) per 100 mm (3.94 in) length
SEM003F
SEM038F
Standard : 57.000 - 57.013 mm (2.2441 - 2.2446 in)
PBIC1641E
Standard : 22.000 - 22.006 mm (0.8661 - 0.8664 in)
PBIC0120E
Page 1988 of 3383
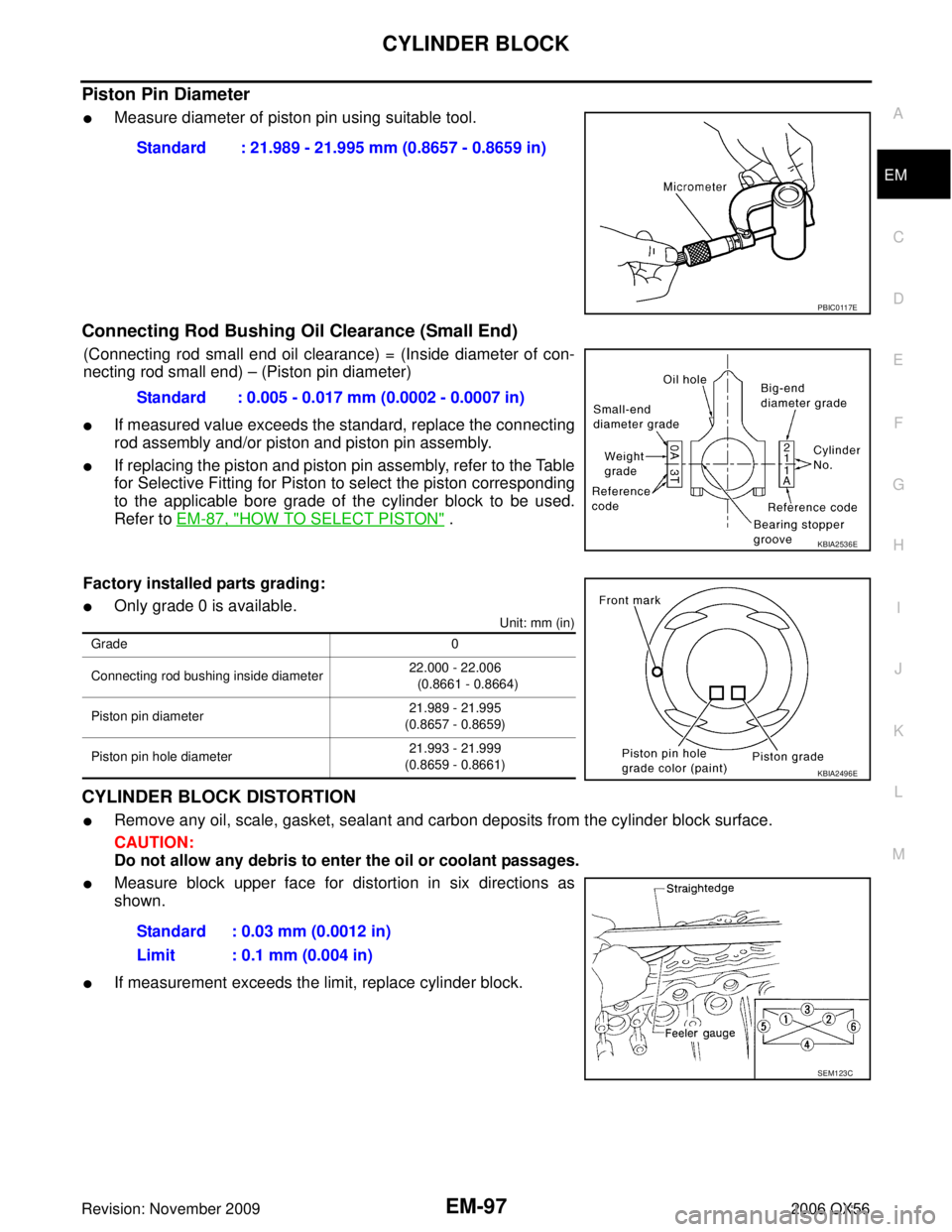
CYLINDER BLOCKEM-97
C
DE
F
G H
I
J
K L
M A
EM
Revision: November 2009 2006 QX56
Piston Pin Diameter
Measure diameter of piston pin using suitable tool.
Connecting Rod Bushing Oil Clearance (Small End)
(Connecting rod small end oil clearance) = (Inside diameter of con-
necting rod small end) – (Piston pin diameter)
If measured value exceeds the standard, replace the connecting
rod assembly and/or piston and piston pin assembly.
If replacing the piston and piston pin assembly, refer to the Table
for Selective Fitting for Piston to select the piston corresponding
to the applicable bore grade of the cylinder block to be used.
Refer to EM-87, "
HOW TO SELECT PISTON" .
Factory installed parts grading:
Only grade 0 is available.
Unit: mm (in)
CYLINDER BLOCK DISTORTION
Remove any oil, scale, gasket, sealant and carbon deposits from the cylinder block surface.
CAUTION:
Do not allow any debris to enter the oil or coolant passages.
Measure block upper face for distortion in six directions as
shown.
If measurement exceeds the limit, replace cylinder block. Standard : 21.989 - 21.995 mm (0.8657 - 0.8659 in)
PBIC0117E
Standard : 0.005 - 0.017 mm (0.0002 - 0.0007 in)
KBIA2536E
Grade
0
Connecting rod bushing inside diameter 22.000 - 22.006
(0.8661 - 0.8664)
Piston pin diameter 21.989 - 21.995
(0.8657 - 0.8659)
Piston pin hole diameter 21.993 - 21.999
(0.8659 - 0.8661)
KBIA2496E
Standard : 0.03 mm (0.0012 in)
Limit : 0.1 mm (0.004 in)
SEM123C
Page 1989 of 3383
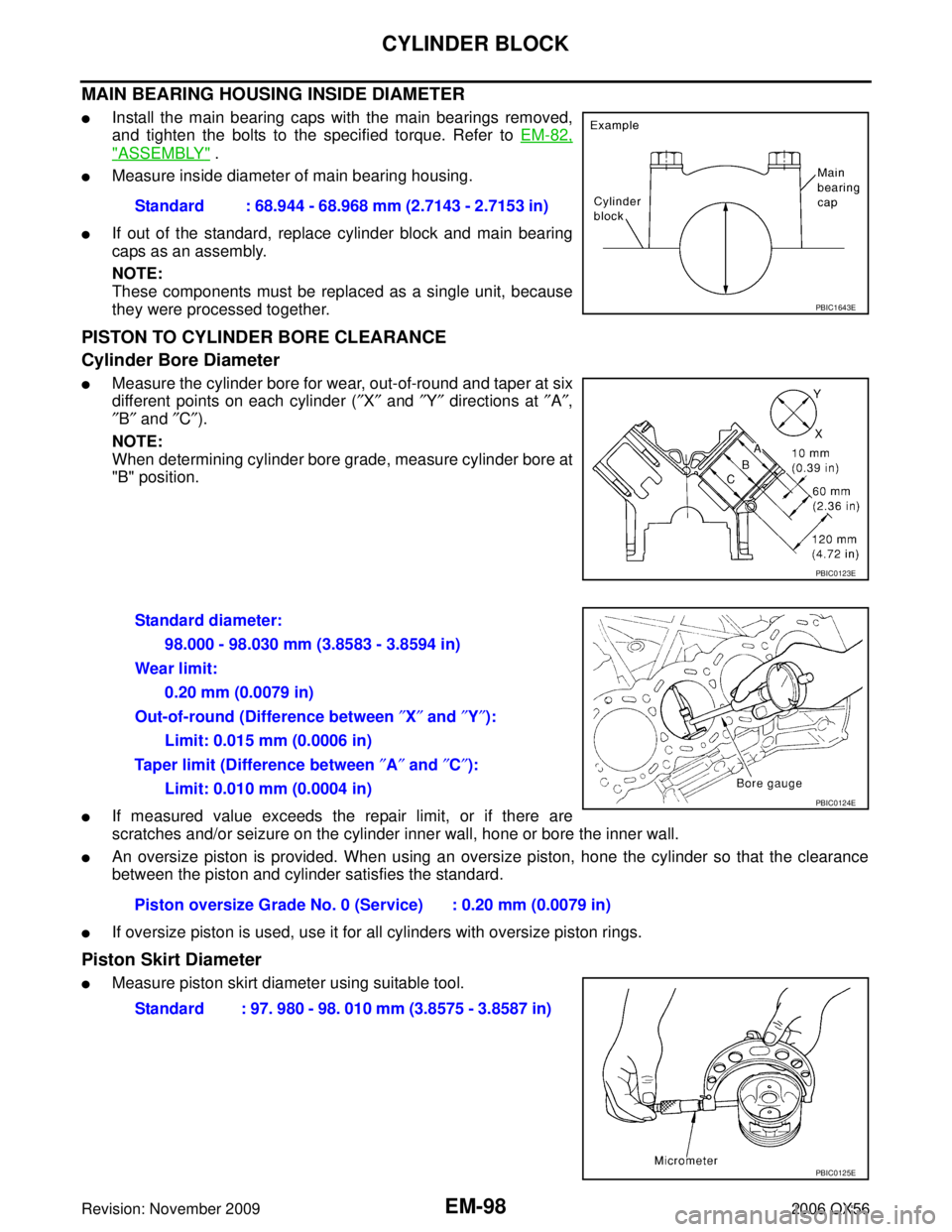
EM-98Revision: November 2009
CYLINDER BLOCK
2006 QX56
MAIN BEARING HOUSING INSIDE DIAMETER
Install the main bearing caps with the main bearings removed,
and tighten the bolts to the specified torque. Refer to EM-82,
"ASSEMBLY" .
Measure inside diameter of main bearing housing.
If out of the standard, replace cylinder block and main bearing
caps as an assembly.
NOTE:
These components must be replaced as a single unit, because
they were processed together.
PISTON TO CYLINDER BORE CLEARANCE
Cylinder Bore Diameter
Measure the cylinder bore for wear, out-of-round and taper at six
different points on each cylinder (″X″ and ″ Y″ directions at ″ A″,
″ B″ and ″C ″).
NOTE:
When determining cylinder bore grade, measure cylinder bore at
"B" position.
If measured value exceeds the repair limit, or if there are
scratches and/or seizure on the cylinder inner wall, hone or bore the inner wall.
An oversize piston is provided. When using an oversize piston, hone the cylinder so that the clearance
between the piston and cylinder satisfies the standard.
If oversize piston is used, use it for all cylinders with oversize piston rings.
Piston Skirt Diameter
Measure piston skirt diameter using suitable tool. Standard : 68.944 - 68.968 mm (2.7143 - 2.7153 in)
PBIC1643E
PBIC0123E
Standard diameter:
98.000 - 98.030 mm (3.8583 - 3.8594 in)
Wear limit: 0.20 mm (0.0079 in)
Out-of-round (Difference between ″X″ and ″Y″ ):
Limit: 0.015 mm (0.0006 in)
Taper limit (Difference between ″A ″ and ″ C″):
Limit: 0.010 mm (0.0004 in)
Piston oversize Grade No. 0 (Service) : 0.20 mm (0.0079 in)
PBIC0124E
Standard : 97. 980 - 98. 010 mm (3.8575 - 3.8587 in)
PBIC0125E
Page 1990 of 3383
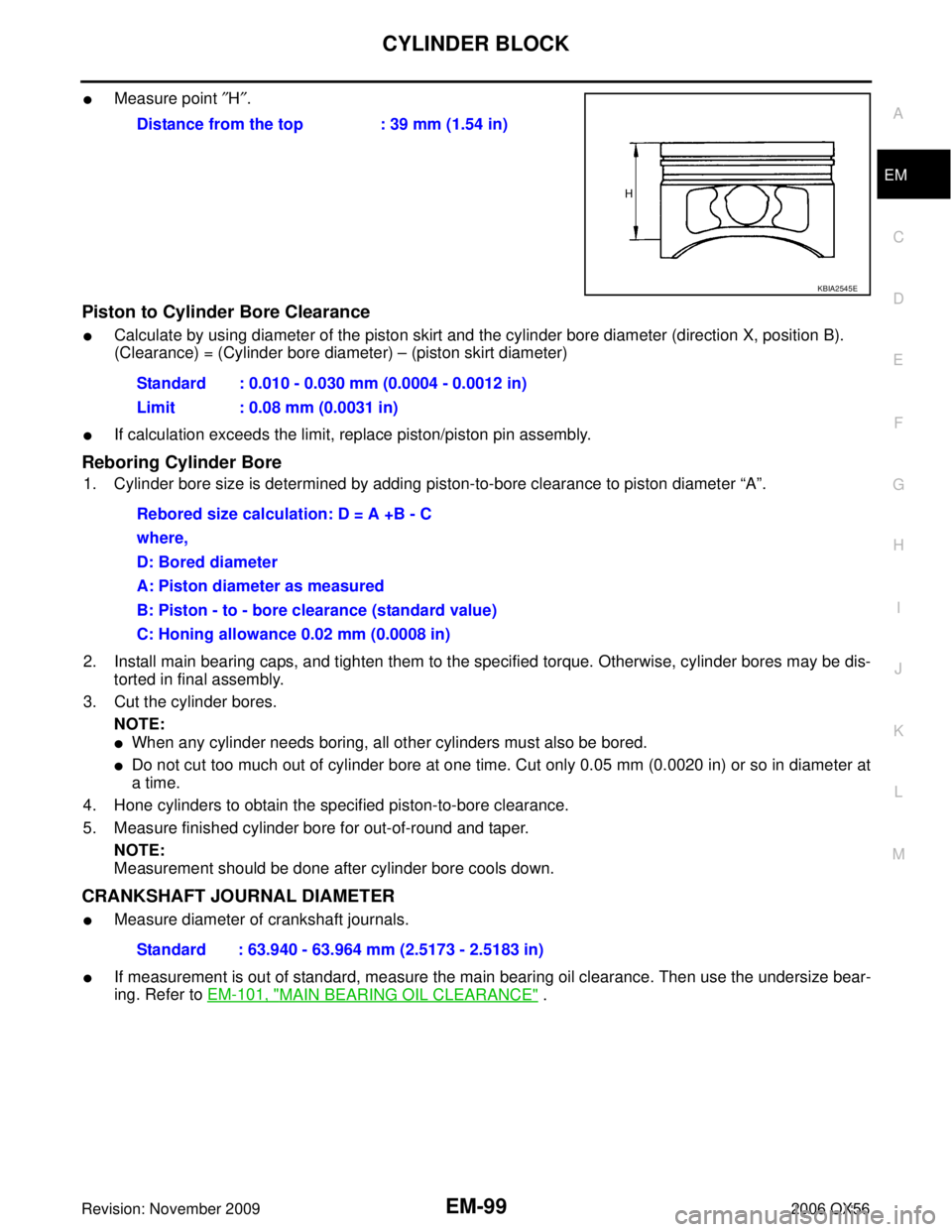
CYLINDER BLOCKEM-99
C
DE
F
G H
I
J
K L
M A
EM
Revision: November 2009 2006 QX56
Measure point ″H ″.
Piston to Cylinder Bore Clearance
Calculate by using diameter of the piston skirt and the cylinder bore diameter (direction X, position B).
(Clearance) = (Cylinder bore diameter) – (piston skirt diameter)
If calculation exceeds the limit, replace piston/piston pin assembly.
Reboring Cylinder Bore
1. Cylinder bore size is determined by adding piston-to-bore clearance to piston diameter “A”.
2. Install main bearing caps, and tighten them to the specified torque. Otherwise, cylinder bores may be dis- torted in final assembly.
3. Cut the cylinder bores. NOTE:
When any cylinder needs boring, all other cylinders must also be bored.
Do not cut too much out of cylinder bore at one time. Cut only 0.05 mm (0.0020 in) or so in diameter at
a time.
4. Hone cylinders to obtain the specified piston-to-bore clearance.
5. Measure finished cylinder bore for out-of-round and taper. NOTE:
Measurement should be done after cylinder bore cools down.
CRANKSHAFT JOURNAL DIAMETER
Measure diameter of crankshaft journals.
If measurement is out of standard, measure the main bearing oil clearance. Then use the undersize bear-
ing. Refer to EM-101, "
MAIN BEARING OIL CLEARANCE" .
Distance from the top : 39 mm (1.54 in)
KBIA2545E
Standard : 0.010 - 0.030 mm (0.0004 - 0.0012 in)
Limit : 0.08 mm (0.0031 in)
Rebored size calculation: D = A +B - C
where,
D: Bored diameter
A: Piston diameter as measured
B: Piston - to - bore clearance (standard value)
C: Honing allowance 0.02 mm (0.0008 in)
Standard : 63.940 - 63.964 mm (2.5173 - 2.5183 in)
Page 1991 of 3383
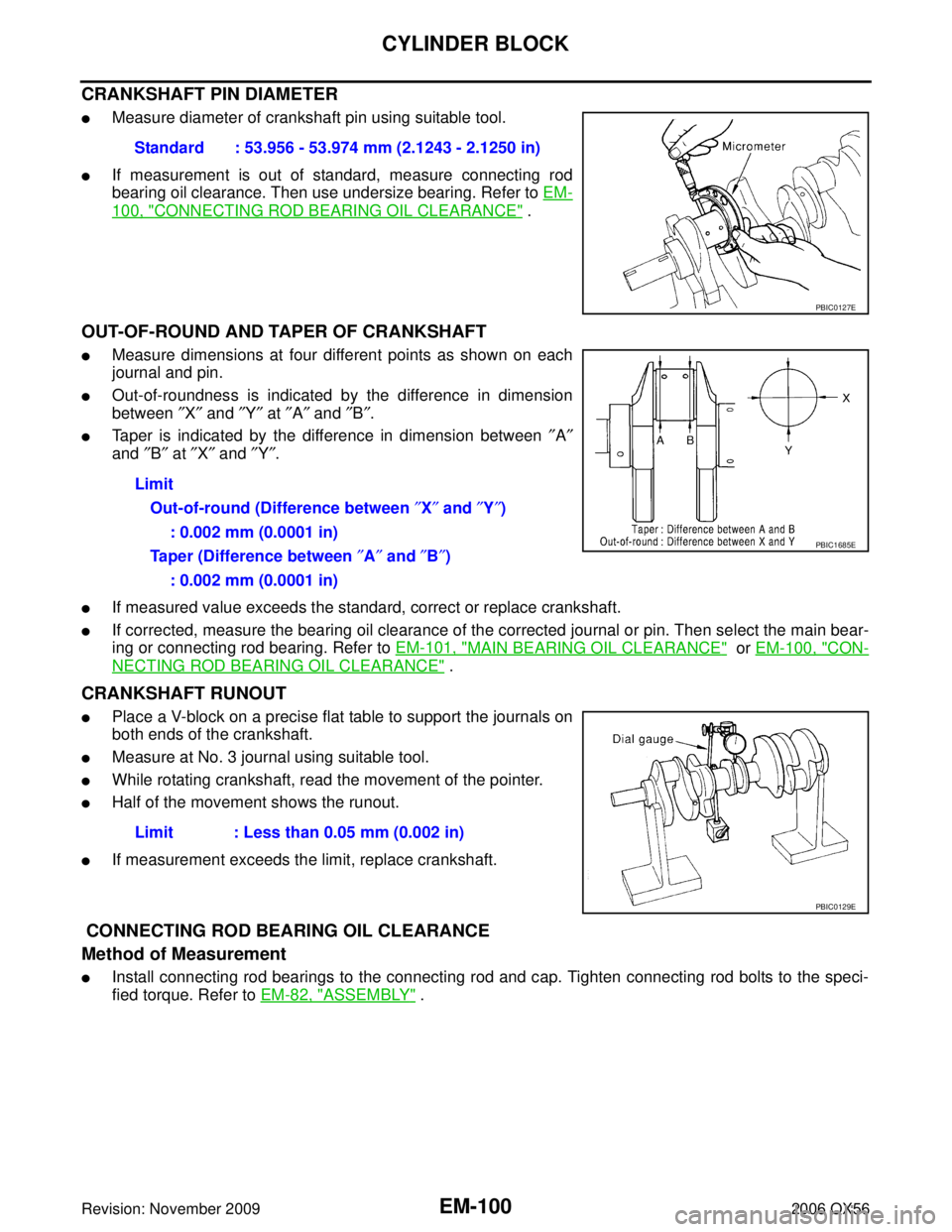
EM-100Revision: November 2009
CYLINDER BLOCK
2006 QX56
CRANKSHAFT PIN DIAMETER
Measure diameter of crankshaft pin using suitable tool.
If measurement is out of standard, measure connecting rod
bearing oil clearance. Then use undersize bearing. Refer to EM-
100, "CONNECTING ROD BEARING OIL CLEARANCE" .
OUT-OF-ROUND AND TAPER OF CRANKSHAFT
Measure dimensions at four different points as shown on each
journal and pin.
Out-of-roundness is indicated by the difference in dimension
between ″X″ and ″Y″ at ″A″ and ″B″ .
Taper is indicated by the difference in dimension between ″A″
and ″B″ at ″X″ and ″Y″ .
If measured value exceeds the standard, correct or replace crankshaft.
If corrected, measure the bearing oil clearance of the corrected journal or pin. Then select the main bear-
ing or connecting rod bearing. Refer to EM-101, "
MAIN BEARING OIL CLEARANCE" or EM-100, "CON-
NECTING ROD BEARING OIL CLEARANCE" .
CRANKSHAFT RUNOUT
Place a V-block on a precise flat table to support the journals on
both ends of the crankshaft.
Measure at No. 3 journal using suitable tool.
While rotating crankshaft, read the movement of the pointer.
Half of the movement shows the runout.
If measurement exceeds the limit, replace crankshaft.
CONNECTING ROD BEARING OIL CLEARANCE
Method of Measurement
Install connecting rod bearings to the connecting rod and cap. Tighten connecting rod bolts to the speci-
fied torque. Refer to EM-82, "
ASSEMBLY" .
Standard : 53.956 - 53.974 mm (2.1243 - 2.1250 in)
PBIC0127E
Limit
Out-of-round (Difference between ″X″ and ″Y″ )
: 0.002 mm (0.0001 in)
Taper (Difference between ″A ″ and ″B ″)
: 0.002 mm (0.0001 in)
PBIC1685E
Limit : Less than 0.05 mm (0.002 in)
PBIC0129E
Page 1992 of 3383
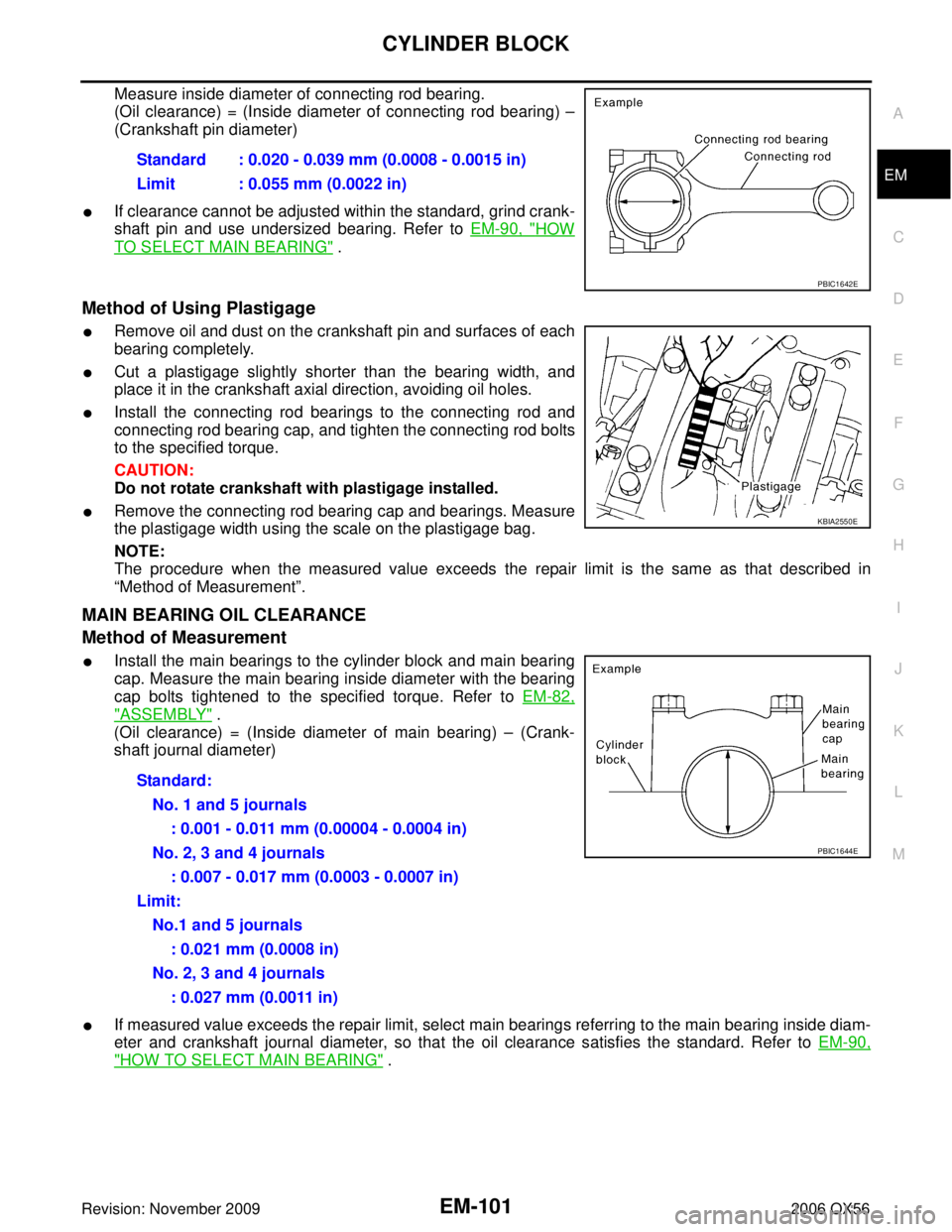
CYLINDER BLOCKEM-101
C
DE
F
G H
I
J
K L
M A
EM
Revision: November 2009 2006 QX56
Measure inside diameter of connecting rod bearing.
(Oil clearance) = (Inside diameter of connecting rod bearing) –
(Crankshaft pin diameter)
If clearance cannot be adjusted within the standard, grind crank-
shaft pin and use undersized bearing. Refer to EM-90, "
HOW
TO SELECT MAIN BEARING" .
Method of Using Plastigage
Remove oil and dust on the crankshaft pin and surfaces of each
bearing completely.
Cut a plastigage slightly shorter than the bearing width, and
place it in the crankshaft axial direction, avoiding oil holes.
Install the connecting rod bearings to the connecting rod and
connecting rod bearing cap, and tighten the connecting rod bolts
to the specified torque.
CAUTION:
Do not rotate crankshaft with plastigage installed.
Remove the connecting rod bearing cap and bearings. Measure
the plastigage width using the scale on the plastigage bag.
NOTE:
The procedure when the measured value exceeds the repair limit is the same as that described in
“Method of Measurement”.
MAIN BEARING OIL CLEARANCE
Method of Measurement
Install the main bearings to the cylinder block and main bearing
cap. Measure the main bearing inside diameter with the bearing
cap bolts tightened to the specified torque. Refer to EM-82,
"ASSEMBLY" .
(Oil clearance) = (Inside diameter of main bearing) – (Crank-
shaft journal diameter)
If measured value exceeds the repair limit, select main bearings referring to the main bearing inside diam-
eter and crankshaft journal diameter, so that the oil clearance satisfies the standard. Refer to EM-90,
"HOW TO SELECT MAIN BEARING" .
Standard : 0.020 - 0.039 mm (0.0008 - 0.0015 in)
Limit : 0.055 mm (0.0022 in)
PBIC1642E
KBIA2550E
Standard:
No. 1 and 5 journals : 0.001 - 0.011 mm (0.00004 - 0.0004 in)
No. 2, 3 and 4 journals : 0.007 - 0.017 mm (0.0003 - 0.0007 in)
Limit: No.1 and 5 journals : 0.021 mm (0.0008 in)
No. 2, 3 and 4 journals : 0.027 mm (0.0011 in)
PBIC1644E