Page 2769 of 3383
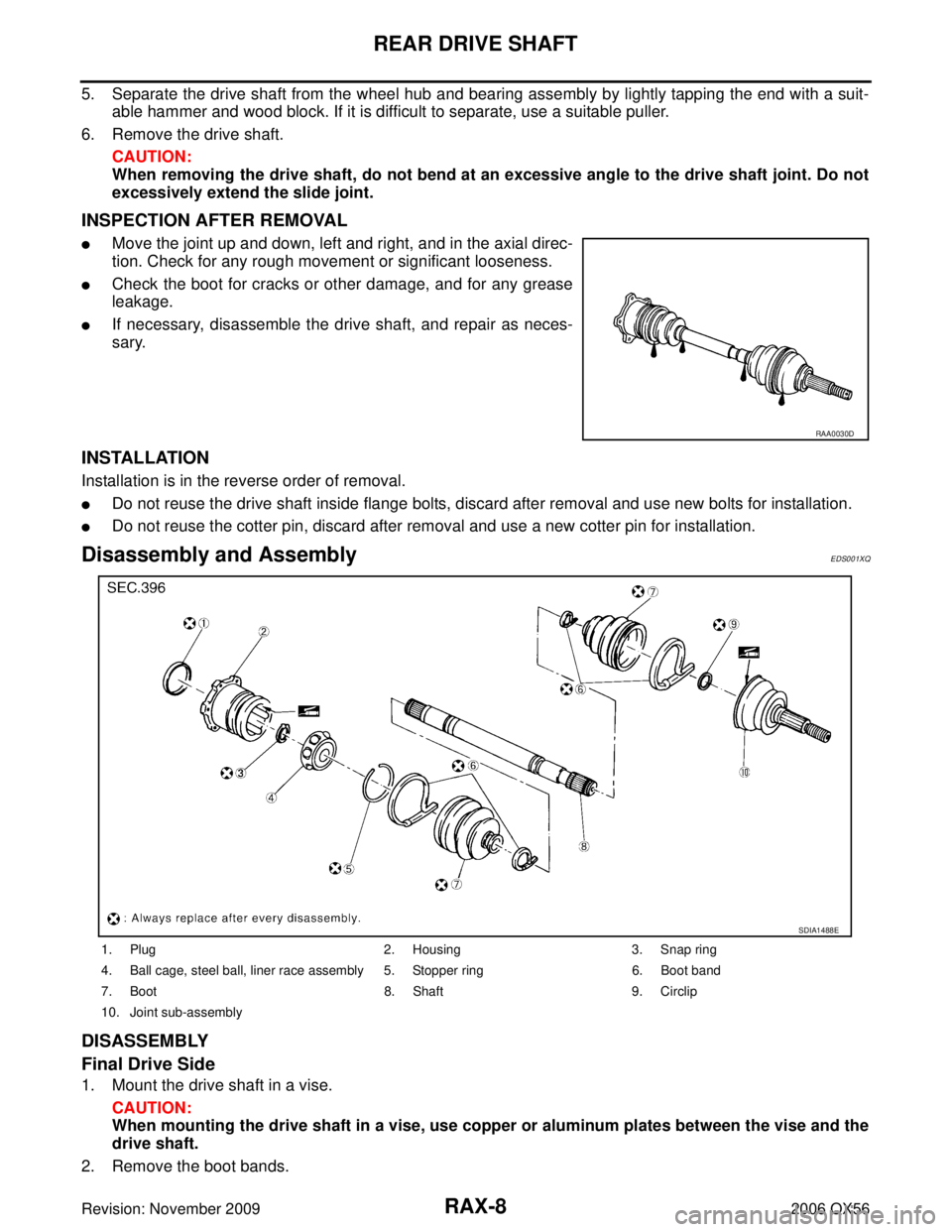
RAX-8
REAR DRIVE SHAFT
Revision: November 20092006 QX56
5. Separate the drive shaft from the wheel hub and bearing assembly by lightly tapping the end with a suit-
able hammer and wood block. If it is difficult to separate, use a suitable puller.
6. Remove the drive shaft. CAUTION:
When removing the drive shaft, do not bend at an excessive angle to the drive shaft joint. Do not
excessively extend the slide joint.
INSPECTION AFTER REMOVAL
Move the joint up and down, left and right, and in the axial direc-
tion. Check for any rough movement or significant looseness.
Check the boot for cracks or other damage, and for any grease
leakage.
If necessary, disassemble the drive shaft, and repair as neces-
sary.
INSTALLATION
Installation is in the reverse order of removal.
Do not reuse the drive shaft inside flange bolts, discard after removal and use new bolts for installation.
Do not reuse the cotter pin, discard after removal and use a new cotter pin for installation.
Disassembly and AssemblyEDS001XQ
DISASSEMBLY
Final Drive Side
1. Mount the drive shaft in a vise.CAUTION:
When mounting the drive shaft in a vise, use copper or aluminum plates between the vise and the
drive shaft.
2. Remove the boot bands.
RAA0030D
1. Plug 2. Housing3. Snap ring
4. Ball cage, steel ball, liner race assembly 5. Stopper ring 6. Boot band
7. Boot 8. Shaft9. Circlip
10. Joint sub-assembly
SDIA1488E
Page 2770 of 3383
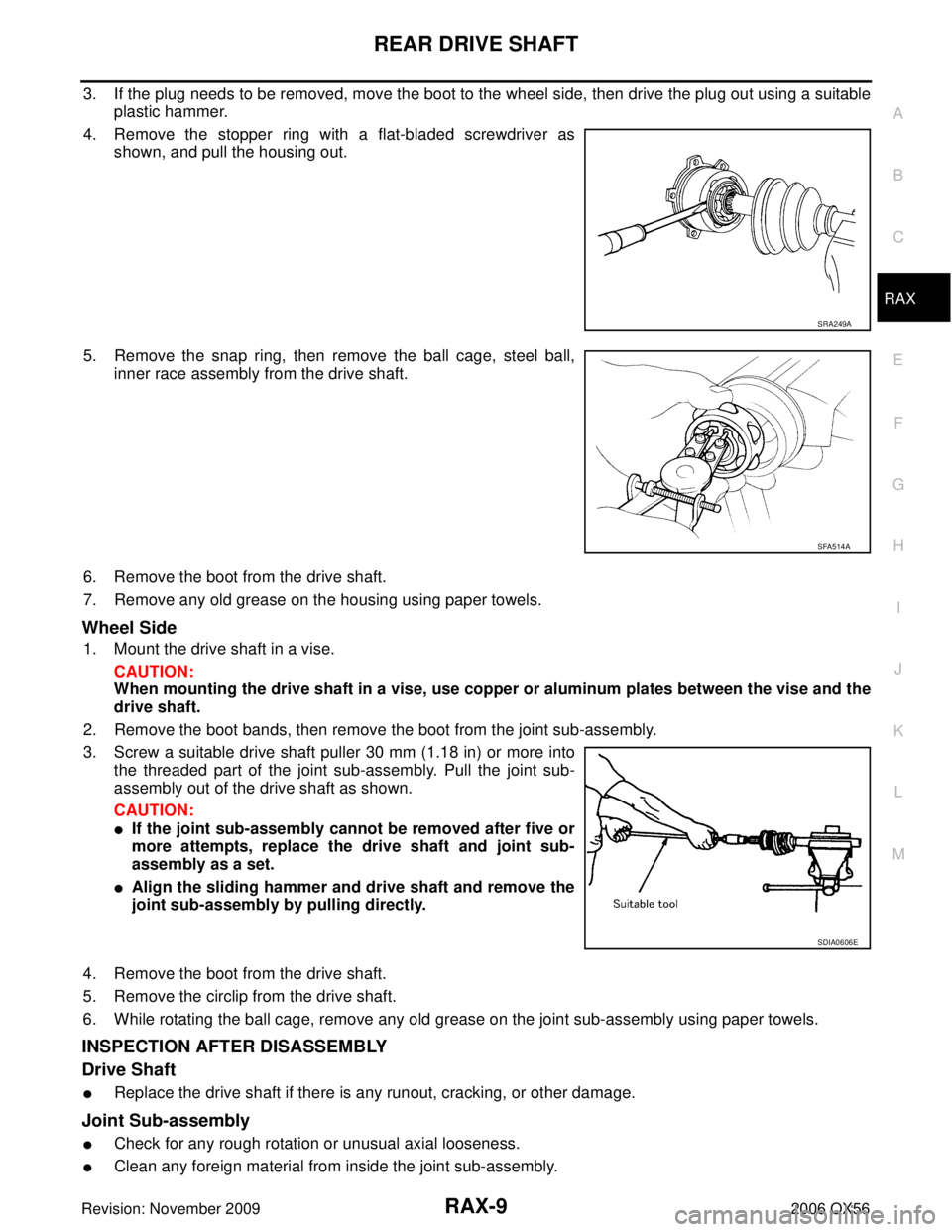
REAR DRIVE SHAFTRAX-9
CE F
G H
I
J
K L
M A
B
RAX
Revision: November 2009 2006 QX56
3. If the plug needs to be removed, move the boot to the wheel side, then drive the plug out using a suitable
plastic hammer.
4. Remove the stopper ring with a flat-bladed screwdriver as shown, and pull the housing out.
5. Remove the snap ring, then remove the ball cage, steel ball, inner race assembly from the drive shaft.
6. Remove the boot from the drive shaft.
7. Remove any old grease on the housing using paper towels.
Wheel Side
1. Mount the drive shaft in a vise. CAUTION:
When mounting the drive shaft in a vise, use copper or aluminum plates between the vise and the
drive shaft.
2. Remove the boot bands, then remove the boot from the joint sub-assembly.
3. Screw a suitable drive shaft puller 30 mm (1.18 in) or more into the threaded part of the joint sub-assembly. Pull the joint sub-
assembly out of the drive shaft as shown.
CAUTION:
If the joint sub-assembly cannot be removed after five or
more attempts, replace the drive shaft and joint sub-
assembly as a set.
Align the sliding hammer and drive shaft and remove the
joint sub-assembly by pulling directly.
4. Remove the boot from the drive shaft.
5. Remove the circlip from the drive shaft.
6. While rotating the ball cage, remove any old grease on the joint sub-assembly using paper towels.
INSPECTION AFTER DISASSEMBLY
Drive Shaft
Replace the drive shaft if there is any runout, cracking, or other damage.
Joint Sub-assembly
Check for any rough rotation or unusual axial looseness.
Clean any foreign material from inside the joint sub-assembly.
SRA249A
SFA514A
SDIA0606E
Page 2771 of 3383
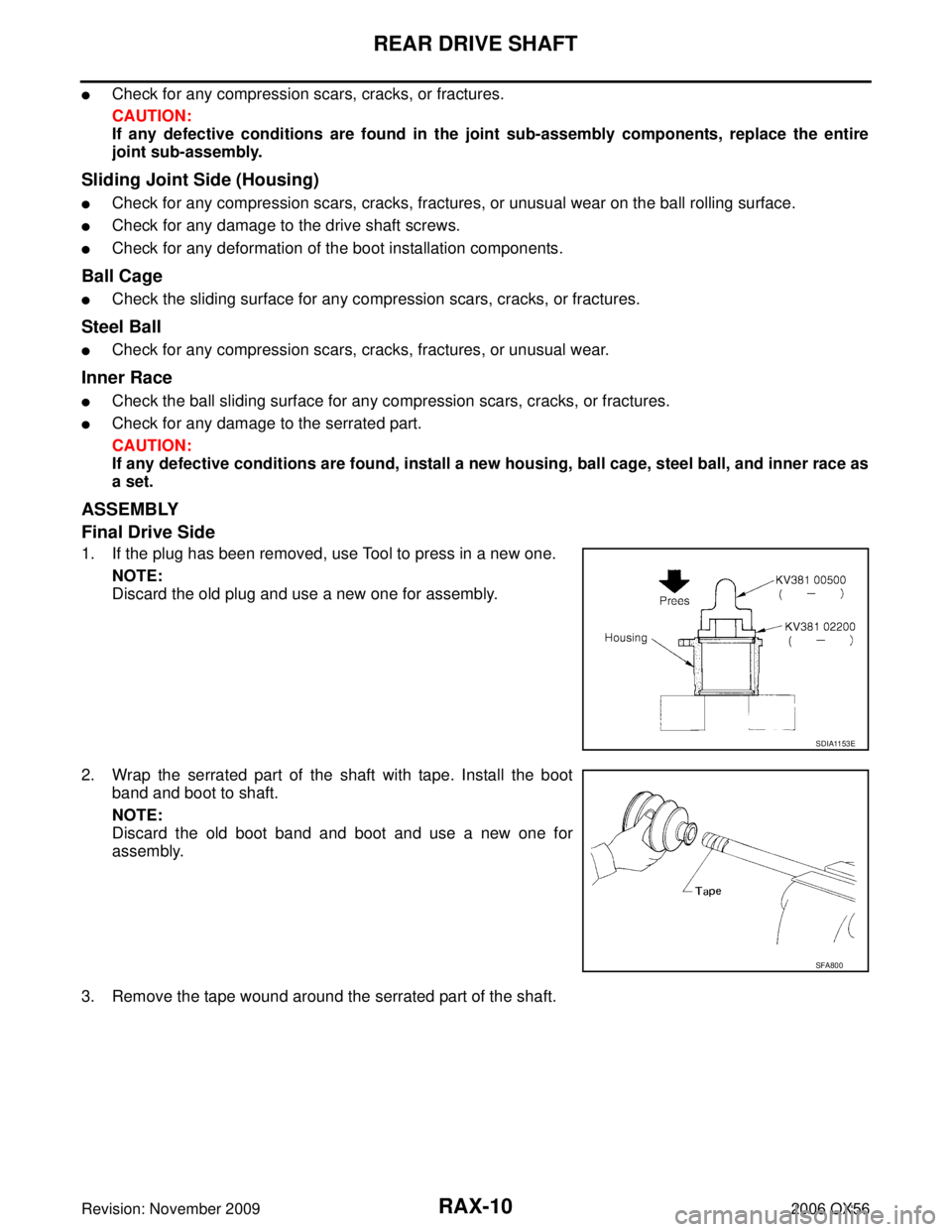
RAX-10
REAR DRIVE SHAFT
Revision: November 20092006 QX56
Check for any compression scars, cracks, or fractures.
CAUTION:
If any defective conditions are found in the joint sub-assembly components, replace the entire
joint sub-assembly.
Sliding Joint Side (Housing)
Check for any compression scars, cracks, fractures, or unusual wear on the ball rolling surface.
Check for any damage to the drive shaft screws.
Check for any deformation of the boot installation components.
Ball Cage
Check the sliding surface for any compression scars, cracks, or fractures.
Steel Ball
Check for any compression scars, cracks, fractures, or unusual wear.
Inner Race
Check the ball sliding surface for any compression scars, cracks, or fractures.
Check for any damage to the serrated part.
CAUTION:
If any defective conditions are found, install a new housing, ball cage, steel ball, and inner race as
a set.
ASSEMBLY
Final Drive Side
1. If the plug has been removed, use Tool to press in a new one.
NOTE:
Discard the old plug and use a new one for assembly.
2. Wrap the serrated part of the shaft with tape. Install the boot band and boot to shaft.
NOTE:
Discard the old boot band and boot and use a new one for
assembly.
3. Remove the tape wound around the serrated part of the shaft.
SDIA1153E
SFA800
Page 2772 of 3383
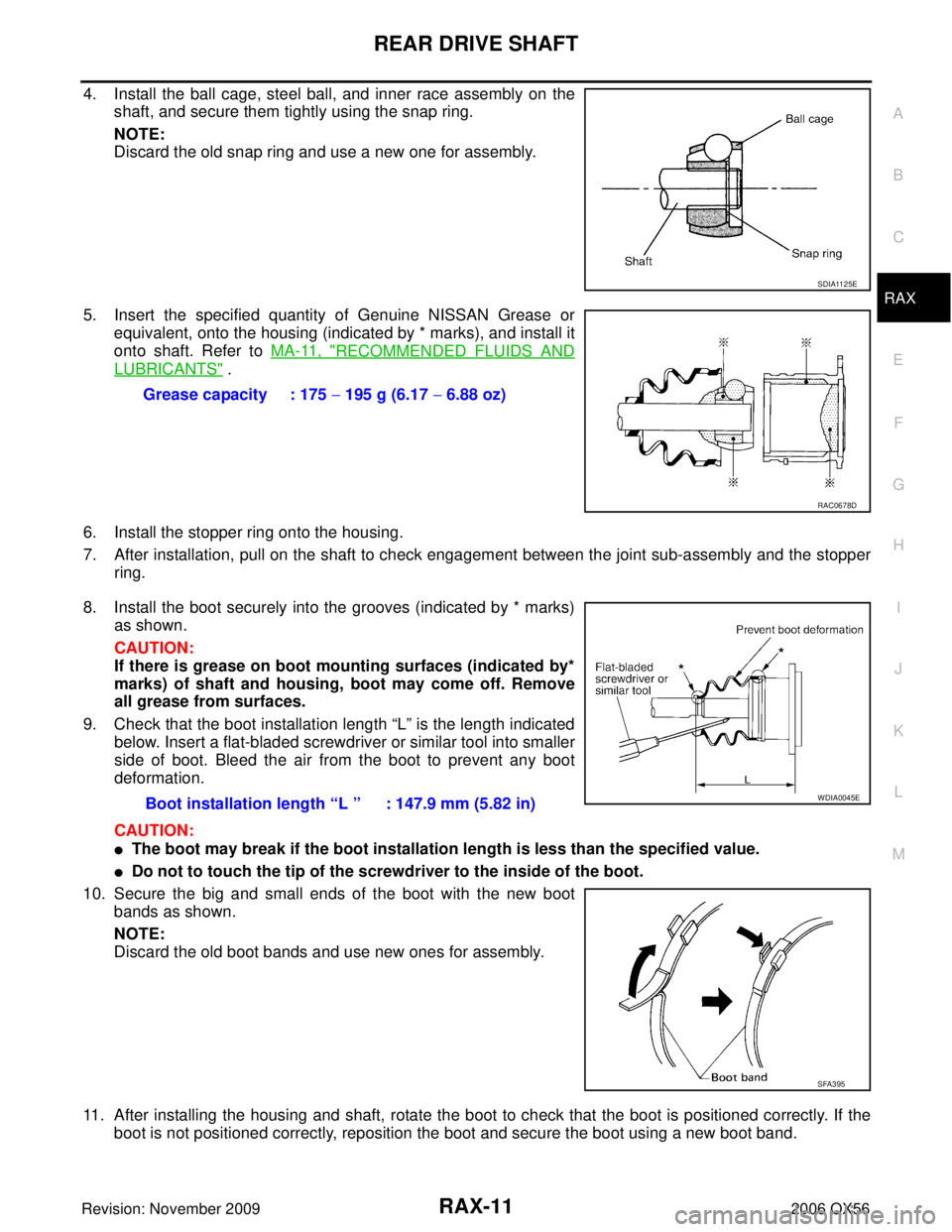
REAR DRIVE SHAFTRAX-11
CE F
G H
I
J
K L
M A
B
RAX
Revision: November 2009 2006 QX56
4. Install the ball cage, steel ball, and inner race assembly on the
shaft, and secure them tightly using the snap ring.
NOTE:
Discard the old snap ring and use a new one for assembly.
5. Insert the specified quantity of Genuine NISSAN Grease or equivalent, onto the housing (indicated by * marks), and install it
onto shaft. Refer to MA-11, "
RECOMMENDED FLUIDS AND
LUBRICANTS" .
6. Install the stopper ring onto the housing.
7. After installation, pull on the shaft to check engagement between the joint sub-assembly and the stopper ring.
8. Install the boot securely into the grooves (indicated by * marks) as shown.
CAUTION:
If there is grease on boot mounting surfaces (indicated by*
marks) of shaft and housing, boot may come off. Remove
all grease from surfaces.
9. Check that the boot installation length “L” is the length indicated below. Insert a flat-bladed screwdriver or similar tool into smaller
side of boot. Bleed the air from the boot to prevent any boot
deformation.
CAUTION:
The boot may break if the boot installation length is less than the specified value.
Do not to touch the tip of the screwdriver to the inside of the boot.
10. Secure the big and small ends of the boot with the new boot bands as shown.
NOTE:
Discard the old boot bands and use new ones for assembly.
11. After installing the housing and shaft, rotate the boot to check that the boot is positioned correctly. If the boot is not positioned correctly, reposition the boot and secure the boot using a new boot band.
SDIA1125E
Grease capacity : 175 − 195 g (6.17 − 6.88 oz)
RAC0678D
Boot installation length “L ” : 147.9 mm (5.82 in)WDIA0045E
SFA395
Page 2773 of 3383
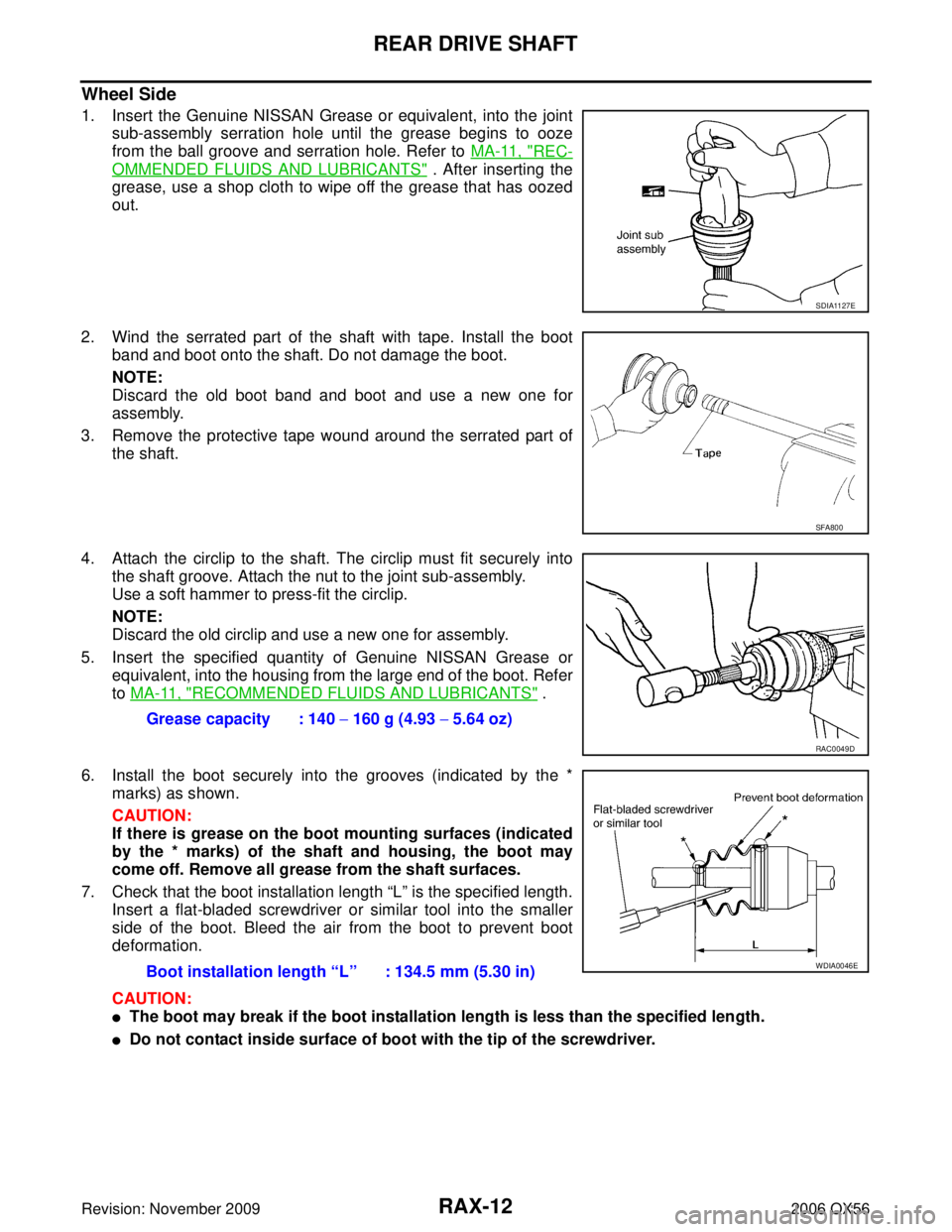
RAX-12
REAR DRIVE SHAFT
Revision: November 20092006 QX56
Wheel Side
1. Insert the Genuine NISSAN Grease or equivalent, into the joint
sub-assembly serration hole until the grease begins to ooze
from the ball groove and serration hole. Refer to MA-11, "
REC-
OMMENDED FLUIDS AND LUBRICANTS" . After inserting the
grease, use a shop cloth to wipe off the grease that has oozed
out.
2. Wind the serrated part of the shaft with tape. Install the boot band and boot onto the shaft. Do not damage the boot.
NOTE:
Discard the old boot band and boot and use a new one for
assembly.
3. Remove the protective tape wound around the serrated part of the shaft.
4. Attach the circlip to the shaft. The circlip must fit securely into the shaft groove. Attach the nut to the joint sub-assembly.
Use a soft hammer to press-fit the circlip.
NOTE:
Discard the old circlip and use a new one for assembly.
5. Insert the specified quantity of Genuine NISSAN Grease or equivalent, into the housing from the large end of the boot. Refer
to MA-11, "
RECOMMENDED FLUIDS AND LUBRICANTS" .
6. Install the boot securely into the grooves (indicated by the * marks) as shown.
CAUTION:
If there is grease on the boot mounting surfaces (indicated
by the * marks) of the shaft and housing, the boot may
come off. Remove all grease from the shaft surfaces.
7. Check that the boot installation length “L” is the specified length. Insert a flat-bladed screwdriver or similar tool into the smaller
side of the boot. Bleed the air from the boot to prevent boot
deformation.
CAUTION:
The boot may break if the boot installation length is less than the specified length.
Do not contact inside surface of boot with the tip of the screwdriver.
SDIA1127E
SFA800
Grease capacity : 140 − 160 g (4.93 − 5.64 oz)
RAC0049D
Boot installation length “L” : 134.5 mm (5.30 in)WDIA0046E
Page 2774 of 3383
REAR DRIVE SHAFTRAX-13
CE F
G H
I
J
K L
M A
B
RAX
Revision: November 2009 2006 QX56
8. Secure the big and small ends of the boot using new boot bands
as shown.
NOTE:
Discard the old boot bands and use new ones for assembly.
9. After installing the joint sub-assembly and shaft, rotate the boot to check that it is positioned correctly. If the boot is not positioned correctly, reposition the boot and secure the boot using a new boot band.
SFA395
Page 2775 of 3383
RAX-14
SERVICE DATA AND SPECIFICATIONS (SDS)
Revision: November 20092006 QX56
SERVICE DATA AND SPECIFICATIONS (SDS)PFP:00030
Wheel BearingEDS001XR
Drive ShaftEDS001XS
Measurement of spring scaleLess than 26.6 N (2.7 kg, 5.95 lb)
Axial end play 0 mm (0 in)
JointWheel sideFinal drive side
Grease capacity 140
− 160 g
(4.93 − 5.64 oz) 175
− 195 g
(6.17 − 6.88 oz)
Boot installed length 134.5 mm (5.30 in)147.9 mm (5.82 in)
Page 2776 of 3383
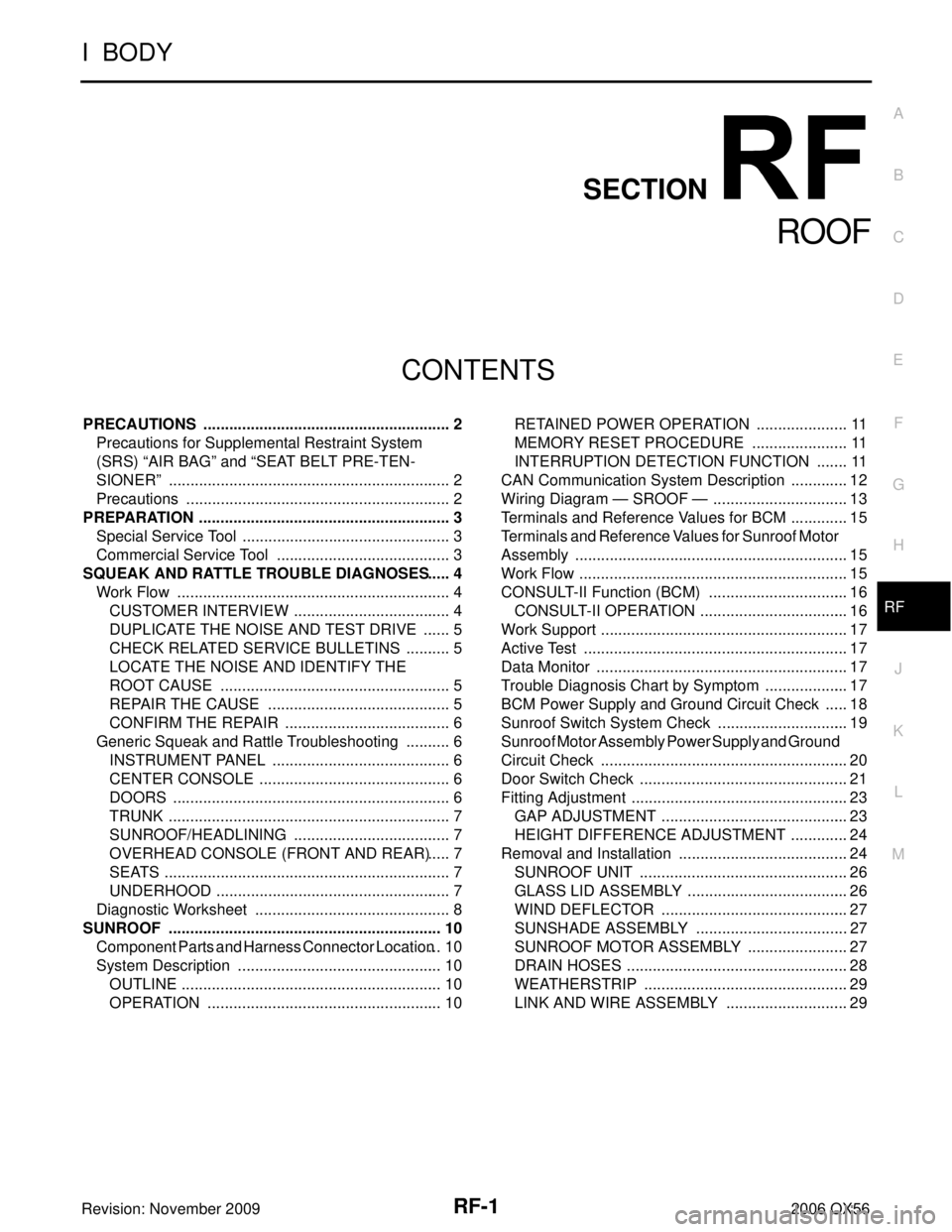
RF-1
ROOF
I BODY
CONTENTS
C
DE
F
G H
J
K L
M
SECTION
A
B
RF
Revision: November 2009 2006 QX56
PRECAUTIONS .....................................................
..... 2
Precautions for Supplemental Restraint System
(SRS) “AIR BAG” and “SEAT BELT PRE-TEN-
SIONER” ............................................................. ..... 2
Precautions ......................................................... ..... 2
PREPARATION ...................................................... ..... 3
Special Service Tool ............................................ ..... 3
Commercial Service Tool .................................... ..... 3
SQUEAK AND RATTLE TROUBLE DIAGNOSES ..... 4
Work Flow ................................................................ 4 CUSTOMER INTERVIEW ................................ ..... 4
DUPLICATE THE NOISE AND TEST DRIVE .. ..... 5
CHECK RELATED SERVICE BULLETINS ...... ..... 5
LOCATE THE NOISE AND IDENTIFY THE
ROOT CAUSE ................................................. ..... 5
REPAIR THE CAUSE ...................................... ..... 5
CONFIRM THE REPAIR .................................. ..... 6
Generic Squeak and Rattle Troubleshooting ...... ..... 6
INSTRUMENT PANEL ..................................... ..... 6
CENTER CONSOLE ........................................ ..... 6
DOORS ............................................................ ..... 6
TRUNK ............................................................. ..... 7
SUNROOF/HEADLINING ................................ ..... 7
OVERHEAD CONSOLE (FRONT AND REAR) ..... 7
SEATS .............................................................. ..... 7
UNDERHOOD .................................................. ..... 7
Diagnostic Worksheet ......................................... ..... 8
SUNROOF ............................................................. ... 10
Component Parts and Harness Connector Location ... 10
System Description ............................................. ... 10
OUTLINE .......................................................... ... 10
OPERATION .................................................... ... 10RETAINED POWER OPERATION ...................
... 11
MEMORY RESET PROCEDURE .................... ... 11
INTERRUPTION DETECTION FUNCTION ..... ... 11
CAN Communication System Description ........... ... 12
Wiring Diagram — SROOF — ................................ 13
Terminals and Reference Values for BCM ........... ... 15
Terminals and Reference Values for Sunroof Motor
Assembly ............................................................. ... 15
Work Flow ............................................................... 15
CONSULT-II Function (BCM) .............................. ... 16
CONSULT-II OPERATION ................................ ... 16
Work Support ....................................................... ... 17
Active Test .............................................................. 17
Data Monitor ........................................................... 17
Trouble Diagnosis Chart by Symptom ................. ... 17
BCM Power Supply and Ground Circuit Check ... ... 18
Sunroof Switch System Check ............................ ... 19
Sunroof Motor Assembly Power Supply and Ground
Circuit Check ....................................................... ... 20
Door Switch Check ................................................. 21
Fitting Adjustment ................................................ ... 23
GAP ADJUSTMENT ......................................... ... 23
HEIGHT DIFFERENCE ADJUSTMENT ........... ... 24
Removal and Installation ..................................... ... 24
SUNROOF UNIT .............................................. ... 26
GLASS LID ASSEMBLY ................................... ... 26
WIND DEFLECTOR ......................................... ... 27
SUNSHADE ASSEMBLY .................................... 27
SUNROOF MOTOR ASSEMBLY ..................... ... 27
DRAIN HOSES ................................................. ... 28
WEATHERSTRIP ............................................. ... 29
LINK AND WIRE ASSEMBLY .......................... ... 29