Page 449 of 4462
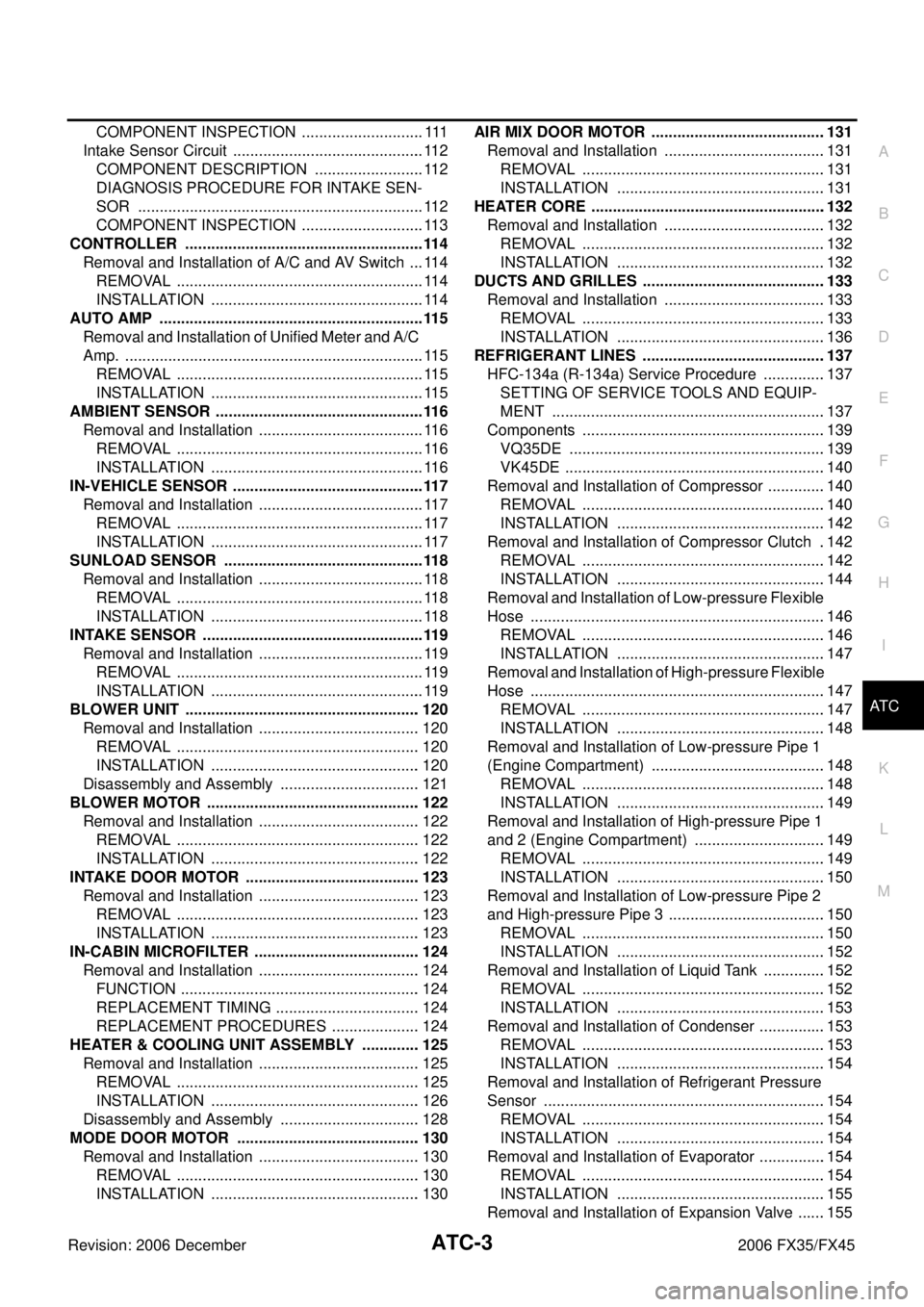
ATC-3
C
D E
F
G H
I
K L
M A
B
AT C
Revision: 2006 December 2006 FX35/FX45 COMPONENT INSPECTION ...........................
. . 111
Intake Sensor Circuit ........................................... .. 112
COMPONENT DESCRIPTION ........................ .. 112
DIAGNOSIS PROCEDURE FOR INTAKE SEN-
SOR ................................................................. .. 112
COMPONENT INSPECTION ........................... .. 113
CONTROLLER ...................................................... ..114
Removal and Installation of A/C and AV Switch .. .. 114
REMOVAL ........................................................ .. 114
INSTALLATION ................................................ .. 114
AUTO AMP ............................................................ ..115
Removal and Installation of Unified Meter and A/C
Amp. .................................................................... .. 115
REMOVAL ........................................................ .. 115
INSTALLATION ................................................ .. 115
AMBIENT SENSOR ............................................... ..116
Removal and Installation ..................................... .. 116
REMOVAL ........................................................ .. 116
INSTALLATION ................................................ .. 116
IN-VEHICLE SENSOR ........................................... ..117
Removal and Installation ..................................... .. 117
REMOVAL ........................................................ .. 117
INSTALLATION ................................................ .. 117
SUNLOAD SENSOR ............................................. ..118
Removal and Installation ..................................... .. 118
REMOVAL ........................................................ .. 118
INSTALLATION ................................................ .. 118
INTAKE SENSOR .................................................. ..119
Removal and Installation ..................................... .. 119
REMOVAL ........................................................ .. 119
INSTALLATION ................................................ .. 119
BLOWER UNIT ...................................................... . 120
Removal and Installation ..................................... . 120
REMOVAL ........................................................ . 120
INSTALLATION ................................................ . 120
Disassembly and Assembly ................................ . 121
BLOWER MOTOR ................................................. . 122
Removal and Installation ..................................... . 122
REMOVAL ........................................................ . 122
INSTALLATION ................................................ . 122
INTAKE DOOR MOTOR ........................................ . 123
Removal and Installation ..................................... . 123
REMOVAL ........................................................ . 123
INSTALLATION ................................................ . 123
IN-CABIN MICROFILTER ...................................... . 124
Removal and Installation ..................................... . 124
FUNCTION ....................................................... . 124
REPLACEMENT TIMING ................................. . 124
REPLACEMENT PROCEDURES .................... . 124
HEATER & COOLING UNIT ASSEMBLY ............. . 125
Removal and Installation ..................................... . 125
REMOVAL ........................................................ . 125
INSTALLATION ................................................ . 126
Disassembly and Assembly ................................ . 128
MODE DOOR MOTOR .......................................... . 130
Removal and Installation ..................................... . 130
REMOVAL ........................................................ . 130
INSTALLATION ................................................ . 130 AIR MIX DOOR MOTOR ........................................
.131
Removal and Installation ..................................... .131
REMOVAL ........................................................ .131
INSTALLATION ................................................ .131
HEATER CORE ...................................................... .132
Removal and Installation ..................................... .132
REMOVAL ........................................................ .132
INSTALLATION ................................................ .132
DUCTS AND GRILLES .......................................... .133
Removal and Installation ..................................... .133
REMOVAL ........................................................ .133
INSTALLATION ................................................ .136
REFRIGERANT LINES .......................................... .137
HFC-134a (R-134a) Service Procedure .............. .137
SETTING OF SERVICE TOOLS AND EQUIP-
MENT ............................................................... .137
Components ........................................................ .139
VQ35DE ........................................................... .139
VK45DE ............................................................ .140
Removal and Installation of Compressor ............. .140
REMOVAL ........................................................ .140
INSTALLATION ................................................ .142
Removal and Installation of Compressor Clutch . .142
REMOVAL ........................................................ .142
INSTALLATION ................................................ .144
Removal and Installation of Low-pressure Flexible
Hose .................................................................... .146
REMOVAL ........................................................ .146
INSTALLATION ................................................ .147
Removal and Installation of High-pressure Flexible
Hose .................................................................... .147
REMOVAL ........................................................ .147
INSTALLATION ................................................ .148
Removal and Installation of Low-pressure Pipe 1
(Engine Compartment) ........................................ .148
REMOVAL ........................................................ .148
INSTALLATION ................................................ .149
Removal and Installation of High-pressure Pipe 1
and 2 (Engine Compartment) .............................. .149
REMOVAL ........................................................ .149
INSTALLATION ................................................ .150
Removal and Installation of Low-pressure Pipe 2
and High-pressure Pipe 3 .................................... .150
REMOVAL ........................................................ .150
INSTALLATION ................................................ .152
Removal and Installation of Liquid Tank .............. .152
REMOVAL ........................................................ .152
INSTALLATION ................................................ .153
Removal and Installation of Condenser ............... .153
REMOVAL ........................................................ .153
INSTALLATION ................................................ .154
Removal and Installation of Refrigerant Pressure
Sensor ................................................................. .154
REMOVAL ........................................................ .154
INSTALLATION ................................................ .154
Removal and Installation of Evaporator ............... .154
REMOVAL ........................................................ .154
INSTALLATION ................................................ .155
Removal and Installation of Expansion Valve ...... .155
Page 450 of 4462
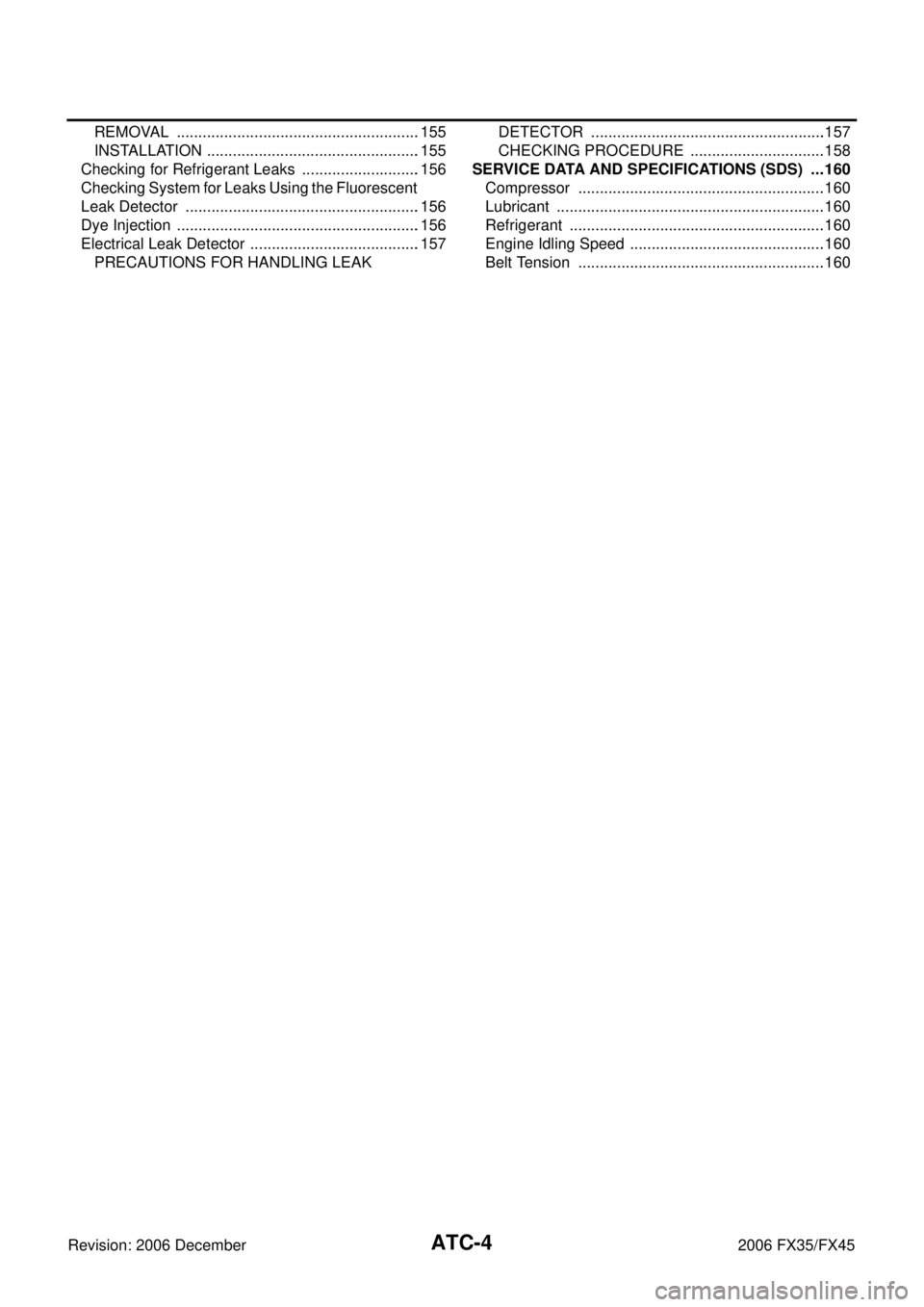
ATC-4Revision: 2006 December 2006 FX35/FX45 REMOVAL ........................................................
.155
INSTALLATION ................................................. .155
Checking for Refrigerant Leaks ........................... .156
Checking System for Leaks Using the Fluorescent
Leak Detector ...................................................... .156
Dye Injection ........................................................ .156
Electrical Leak Detector ....................................... .157
PRECAUTIONS FOR HANDLING LEAK DETECTOR ......................................................
.157
CHECKING PROCEDURE ............................... .158
SERVICE DATA AND SPECIFICATIONS (SDS) ... .160
Compressor ......................................................... .160
Lubricant .............................................................. .160
Refrigerant ........................................................... .160
Engine Idling Speed ............................................. .160
Belt Tension ......................................................... .160
Page 451 of 4462
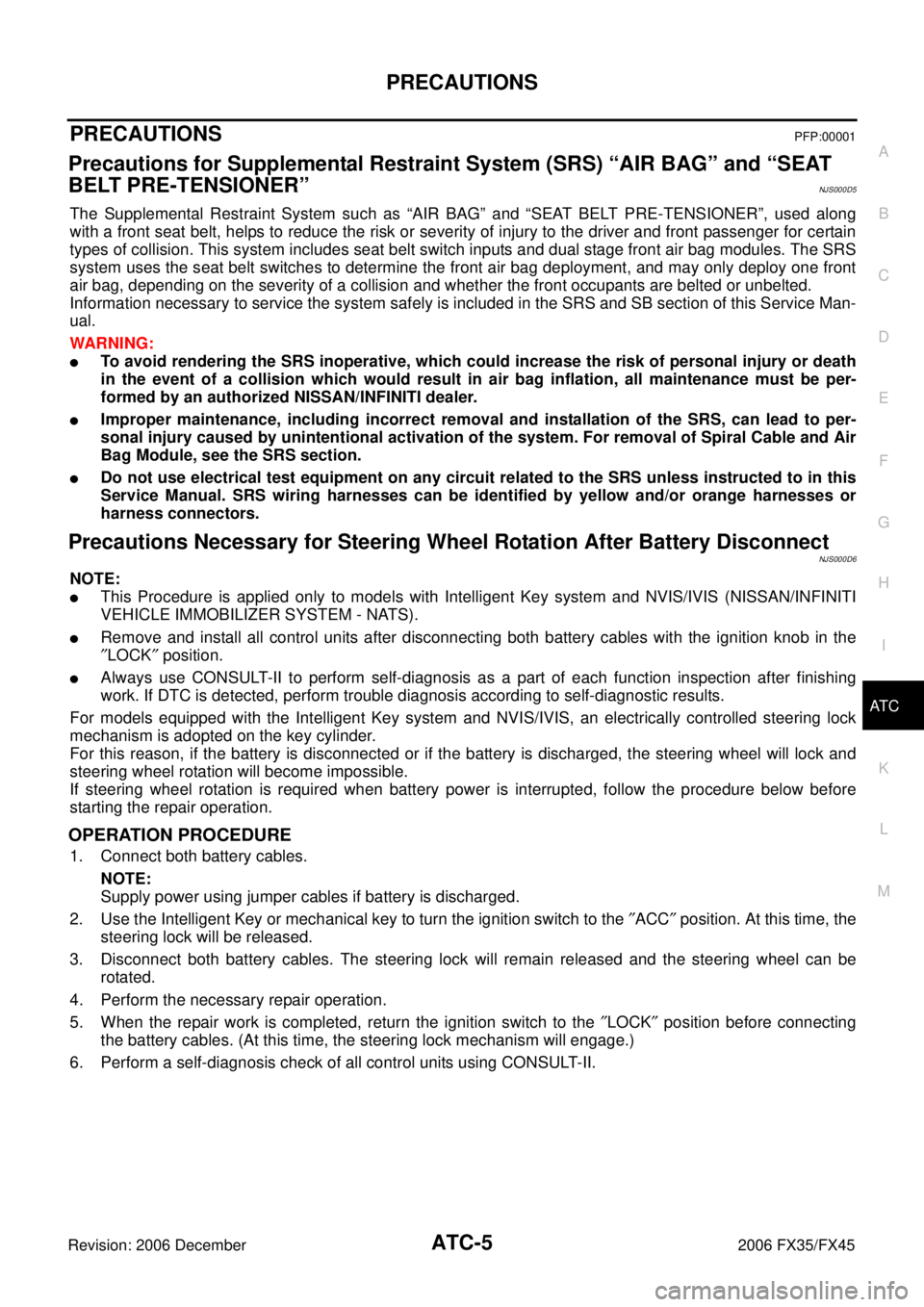
PRECAUTIONS ATC-5
C
D E
F
G H
I
K L
M A
B
AT C
Revision: 2006 December 2006 FX35/FX45
PRECAUTIONSPFP:00001
Precautions for Supplemental Restraint System (SRS) “AIR BAG” and “SEAT
BELT PRE-TENSIONER”
NJS000D5
The Supplemental Restraint System such as “AIR BAG” and “SEAT BELT PRE-TENSIONER”, used along
with a front seat belt, helps to reduce the risk or severity of injury to the driver and front passenger for certain
types of collision. This system includes seat belt switch inputs and dual stage front air bag modules. The SRS
system uses the seat belt switches to determine the front air bag deployment, and may only deploy one front
air bag, depending on the severity of a collision and whether the front occupants are belted or unbelted.
Information necessary to service the system safely is included in the SRS and SB section of this Service Man-
ual.
WARNING:
To avoid rendering the SRS inoperative, which could increase the risk of personal injury or death
in the event of a collision which would result in air bag inflation, all maintenance must be per-
formed by an authorized NISSAN/INFINITI dealer.
Improper maintenance, including incorrect removal and installation of the SRS, can lead to per-
sonal injury caused by unintentional activation of the system. For removal of Spiral Cable and Air
Bag Module, see the SRS section.
Do not use electrical test equipment on any circuit related to the SRS unless instructed to in this
Service Manual. SRS wiring harnesses can be identified by yellow and/or orange harnesses or
harness connectors.
Precautions Necessary for Steering Wheel Rotation After Battery DisconnectNJS000D6
NOTE:
This Procedure is applied only to models with Intelligent Key system and NVIS/IVIS (NISSAN/INFINITI
VEHICLE IMMOBILIZER SYSTEM - NATS).
Remove and install all control units after disconnecting both battery cables with the ignition knob in the
″ LOCK ″ position.
Always use CONSULT-II to perform self-diagnosis as a part of each function inspection after finishing
work. If DTC is detected, perform trouble diagnosis according to self-diagnostic results.
For models equipped with the Intelligent Key system and NVIS/IVIS, an electrically controlled steering lock
mechanism is adopted on the key cylinder.
For this reason, if the battery is disconnected or if the battery is discharged, the steering wheel will lock and
steering wheel rotation will become impossible.
If steering wheel rotation is required when battery power is interrupted, follow the procedure below before
starting the repair operation.
OPERATION PROCEDURE
1. Connect both battery cables.
NOTE:
Supply power using jumper cables if battery is discharged.
2. Use the Intelligent Key or mechanical key to turn the ignition switch to the ″ACC ″ position. At this time, the
steering lock will be released.
3. Disconnect both battery cables. The steering lock will remain released and the steering wheel can be rotated.
4. Perform the necessary repair operation.
5. When the repair work is completed, return the ignition switch to the ″LOCK ″ position before connecting
the battery cables. (At this time, the steering lock mechanism will engage.)
6. Perform a self-diagnosis check of all control units using CONSULT-II.
Page 452 of 4462
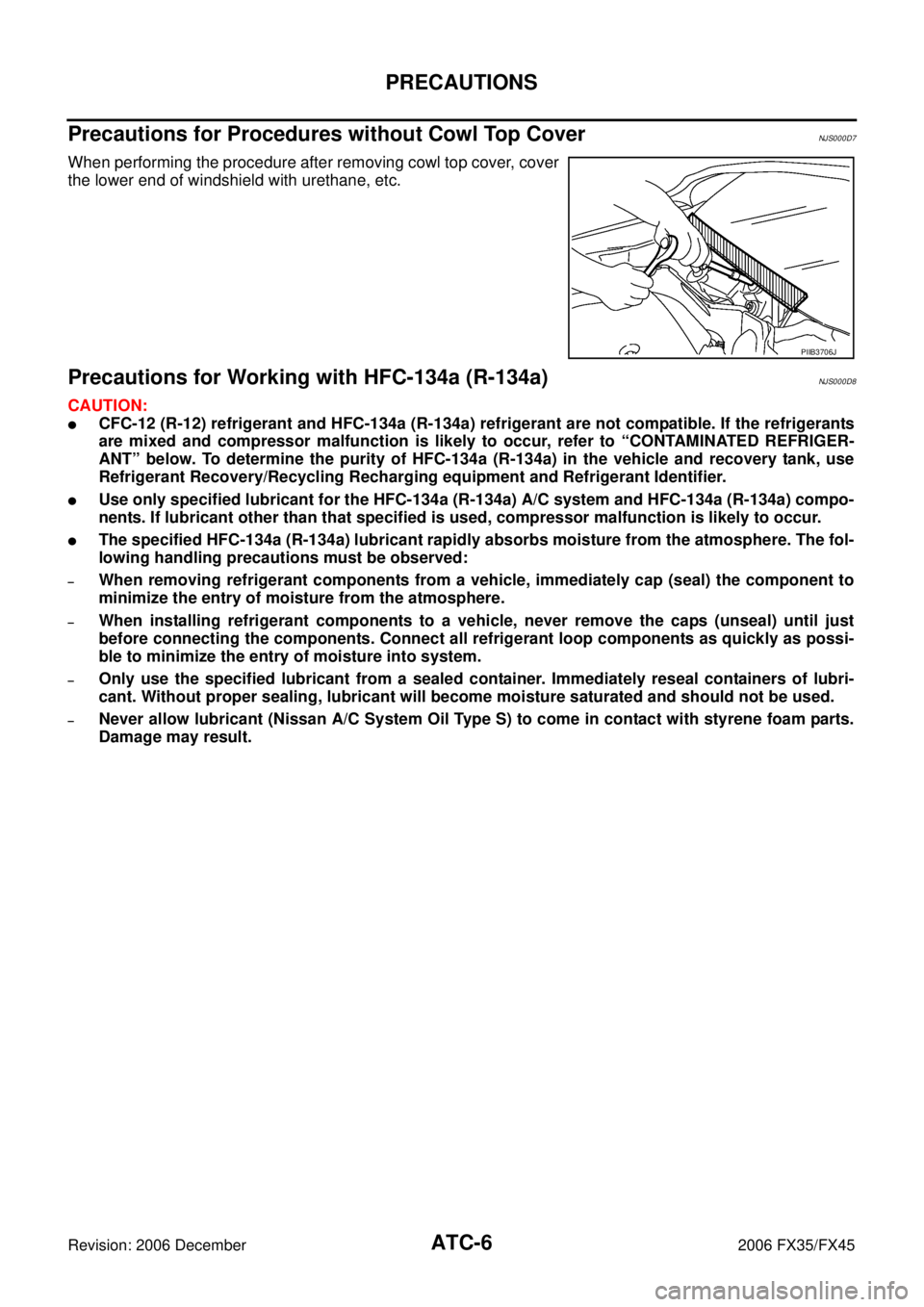
ATC-6
PRECAUTIONS
Revision: 2006 December 2006 FX35/FX45
Precautions for Procedures without Cowl Top CoverNJS000D7
When performing the procedure after removing cowl top cover, cover
the lower end of windshield with urethane, etc.
Precautions for Working with HFC-134a (R-134a)NJS000D8
CAUTION:
CFC-12 (R-12) refrigerant and HFC-134a (R-134a) refrigerant are not compatible. If the refrigerants
are mixed and compressor malfunction is likely to occur, refer to “CONTAMINATED REFRIGER-
ANT” below. To determine the purity of HFC-134a (R-134a) in the vehicle and recovery tank, use
Refrigerant Recovery/Recycling Recharging equipment and Refrigerant Identifier.
Use only specified lubricant for the HFC-134a (R-134a) A/C system and HFC-134a (R-134a) compo-
nents. If lubricant other than that specified is used, compressor malfunction is likely to occur.
The specified HFC-134a (R-134a) lubricant rapidly absorbs moisture from the atmosphere. The fol-
lowing handling precautions must be observed:
–When removing refrigerant components from a vehicle, immediately cap (seal) the component to
minimize the entry of moisture from the atmosphere.
–When installing refrigerant components to a vehicle, never remove the caps (unseal) until just
before connecting the components. Connect all refrigerant loop components as quickly as possi-
ble to minimize the entry of moisture into system.
–Only use the specified lubricant from a sealed container. Immediately reseal containers of lubri-
cant. Without proper sealing, lubricant will become moisture saturated and should not be used.
–Never allow lubricant (Nissan A/C System Oil Type S) to come in contact with styrene foam parts.
Damage may result.
PIIB3706J
Page 453 of 4462
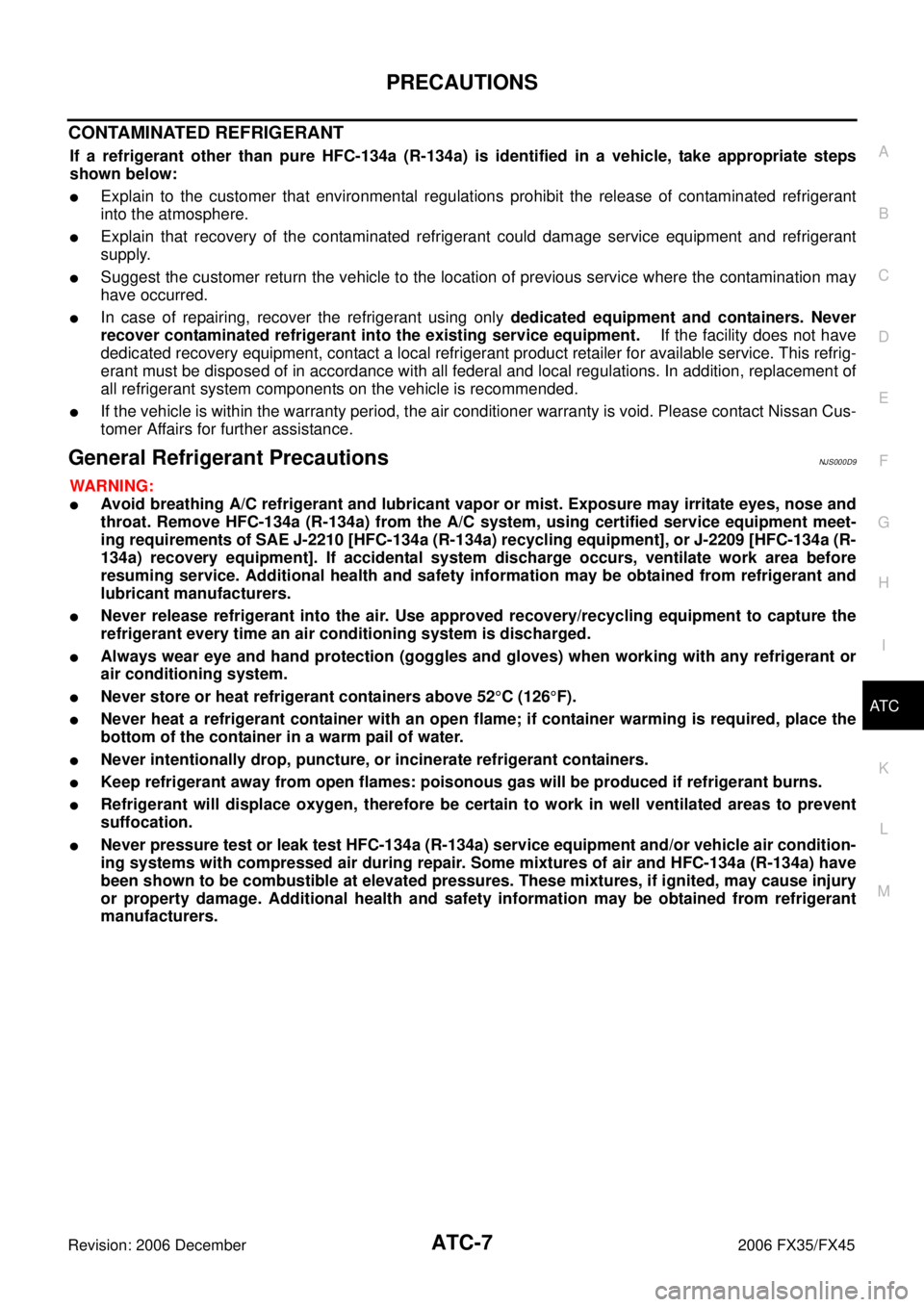
PRECAUTIONS ATC-7
C
D E
F
G H
I
K L
M A
B
AT C
Revision: 2006 December 2006 FX35/FX45
CONTAMINATED REFRIGERANT
If a refrigerant other than pure HFC-134a (R-134a) is identified in a vehicle, take appropriate steps
shown below:
Explain to the customer that environmental regulations prohibit the release of contaminated refrigerant
into the atmosphere.
Explain that recovery of the contaminated refrigerant could damage service equipment and refrigerant
supply.
Suggest the customer return the vehicle to the location of previous service where the contamination may
have occurred.
In case of repairing, recover the refrigerant using only dedicated equipment and containers. Never
recover contaminated refrigerant into the existing service equipment. If the facility does not have
dedicated recovery equipment, contact a local refrigerant product retailer for available service. This refrig-
erant must be disposed of in accordance with all federal and local regulations. In addition, replacement of
all refrigerant system components on the vehicle is recommended.
If the vehicle is within the warranty period, the air conditioner warranty is void. Please contact Nissan Cus-
tomer Affairs for further assistance.
General Refrigerant PrecautionsNJS000D9
WARNING:
Avoid breathing A/C refrigerant and lubricant vapor or mist. Exposure may irritate eyes, nose and
throat. Remove HFC-134a (R-134a) from the A/C system, using certified service equipment meet-
ing requirements of SAE J-2210 [HFC-134a (R-134a) recycling equipment], or J-2209 [HFC-134a (R-
134a) recovery equipment]. If accidental system discharge occurs, ventilate work area before
resuming service. Additional health and safety information may be obtained from refrigerant and
lubricant manufacturers.
Never release refrigerant into the air. Use approved recovery/recycling equipment to capture the
refrigerant every time an air conditioning system is discharged.
Always wear eye and hand protection (goggles and gloves) when working with any refrigerant or
air conditioning system.
Never store or heat refrigerant containers above 52 °C (126 °F).
Never heat a refrigerant container with an open flame; if container warming is required, place the
bottom of the container in a warm pail of water.
Never intentionally drop, puncture, or incinerate refrigerant containers.
Keep refrigerant away from open flames: poisonous gas will be produced if refrigerant burns.
Refrigerant will displace oxygen, therefore be certain to work in well ventilated areas to prevent
suffocation.
Never pressure test or leak test HFC-134a (R-134a) service equipment and/or vehicle air condition-
ing systems with compressed air during repair. Some mixtures of air and HFC-134a (R-134a) have
been shown to be combustible at elevated pressures. These mixtures, if ignited, may cause injury
or property damage. Additional health and safety information may be obtained from refrigerant
manufacturers.
Page 454 of 4462
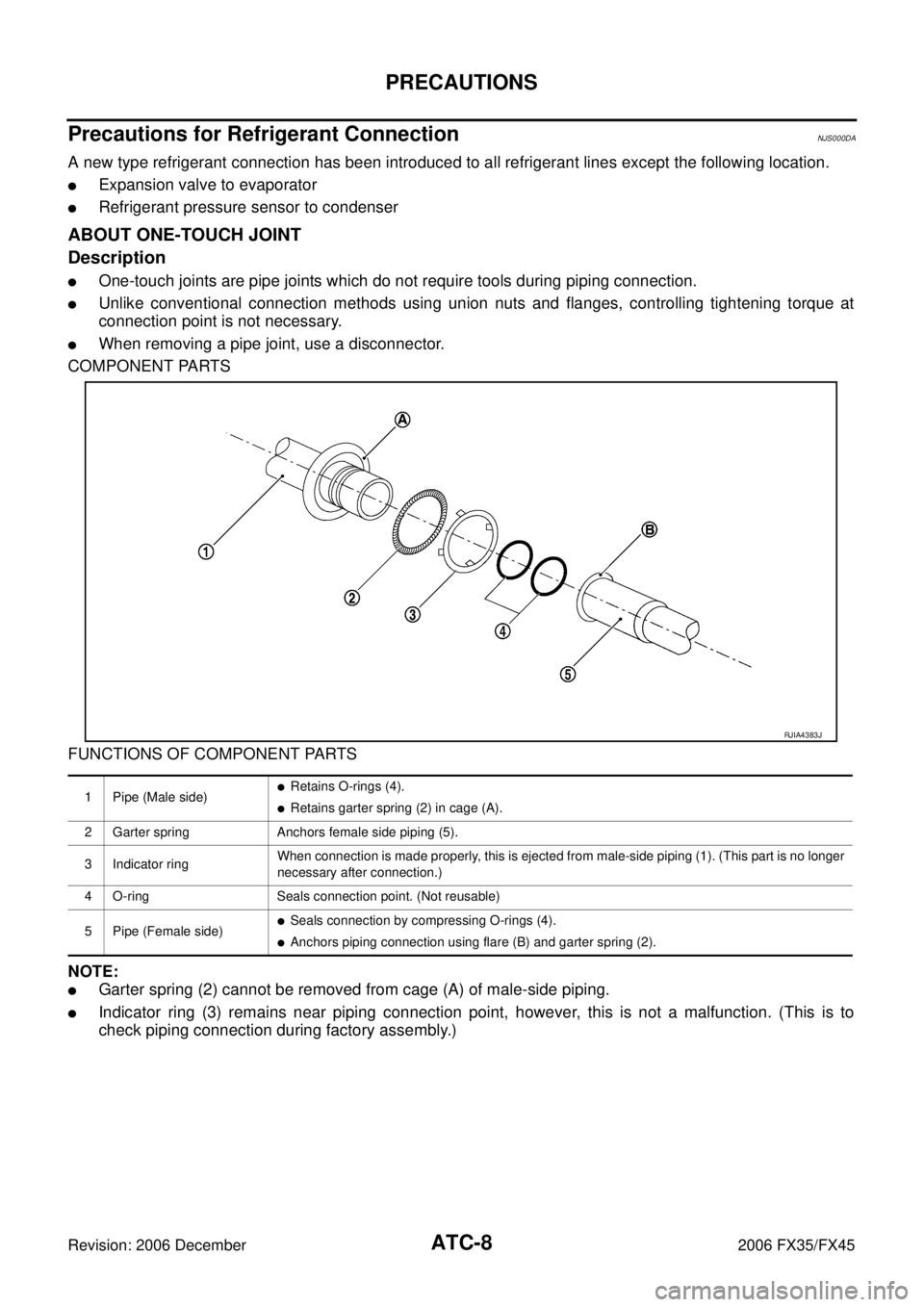
ATC-8
PRECAUTIONS
Revision: 2006 December 2006 FX35/FX45
Precautions for Refrigerant ConnectionNJS000DA
A new type refrigerant connection has been introduced to all refrigerant lines except the following location.
Expansion valve to evaporator
Refrigerant pressure sensor to condenser
ABOUT ONE-TOUCH JOINT
Description
One-touch joints are pipe joints which do not require tools during piping connection.
Unlike conventional connection methods using union nuts and flanges, controlling tightening torque at
connection point is not necessary.
When removing a pipe joint, use a disconnector.
COMPONENT PARTS
FUNCTIONS OF COMPONENT PARTS
NOTE:
Garter spring (2) cannot be removed from cage (A) of male-side piping.
Indicator ring (3) remains near piping connection point, however, this is not a malfunction. (This is to
check piping connection during factory assembly.)
1 Pipe (Male side)Retains O-rings (4).
Retains garter spring (2) in cage (A).
2 Garter spring Anchors female side piping (5).
3 Indicator ring When connection is made properly, this is ejected from male-side piping (1). (This part is no longer
necessary after connection.)
4 O-ring Seals connection point. (Not reusable)
5 Pipe (Female side)
Seals connection by compressing O-rings (4).
Anchors piping connection using flare (B) and garter spring (2).
RJIA4383J
Page 455 of 4462
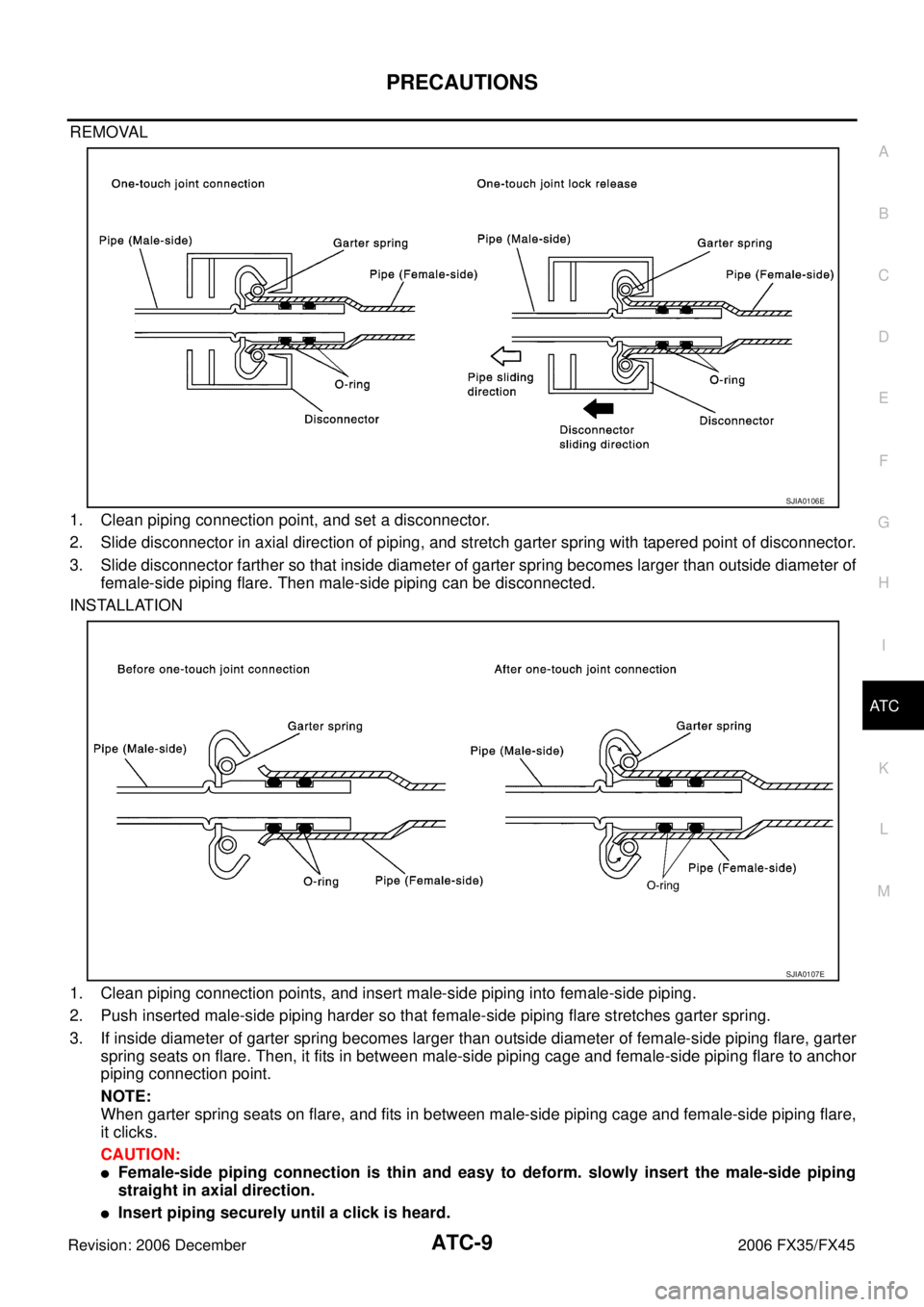
PRECAUTIONS ATC-9
C
D E
F
G H
I
K L
M A
B
AT C
Revision: 2006 December 2006 FX35/FX45
REMOVAL
1. Clean piping connection point, and set a disconnector.
2. Slide disconnector in axial direction of piping, and stretch garter spring with tapered point of disconnector.
3. Slide disconnector farther so that inside diameter of garter spring becomes larger than outside diameter of female-side piping flare. Then male-side piping can be disconnected.
INSTALLATION
1. Clean piping connection points, and insert male-side piping into female-side piping.
2. Push inserted male-side piping harder so that female-side piping flare stretches garter spring.
3. If inside diameter of garter spring becomes larger than outside diameter of female-side piping flare, garter spring seats on flare. Then, it fits in between male-side piping cage and female-side piping flare to anchor
piping connection point.
NOTE:
When garter spring seats on flare, and fits in between male-side piping cage and female-side piping flare,
it clicks.
CAUTION:
Female-side piping connection is thin and easy to deform. slowly insert the male-side piping
straight in axial direction.
Insert piping securely until a click is heard.
SJIA0106E
SJIA0107E
Page 456 of 4462
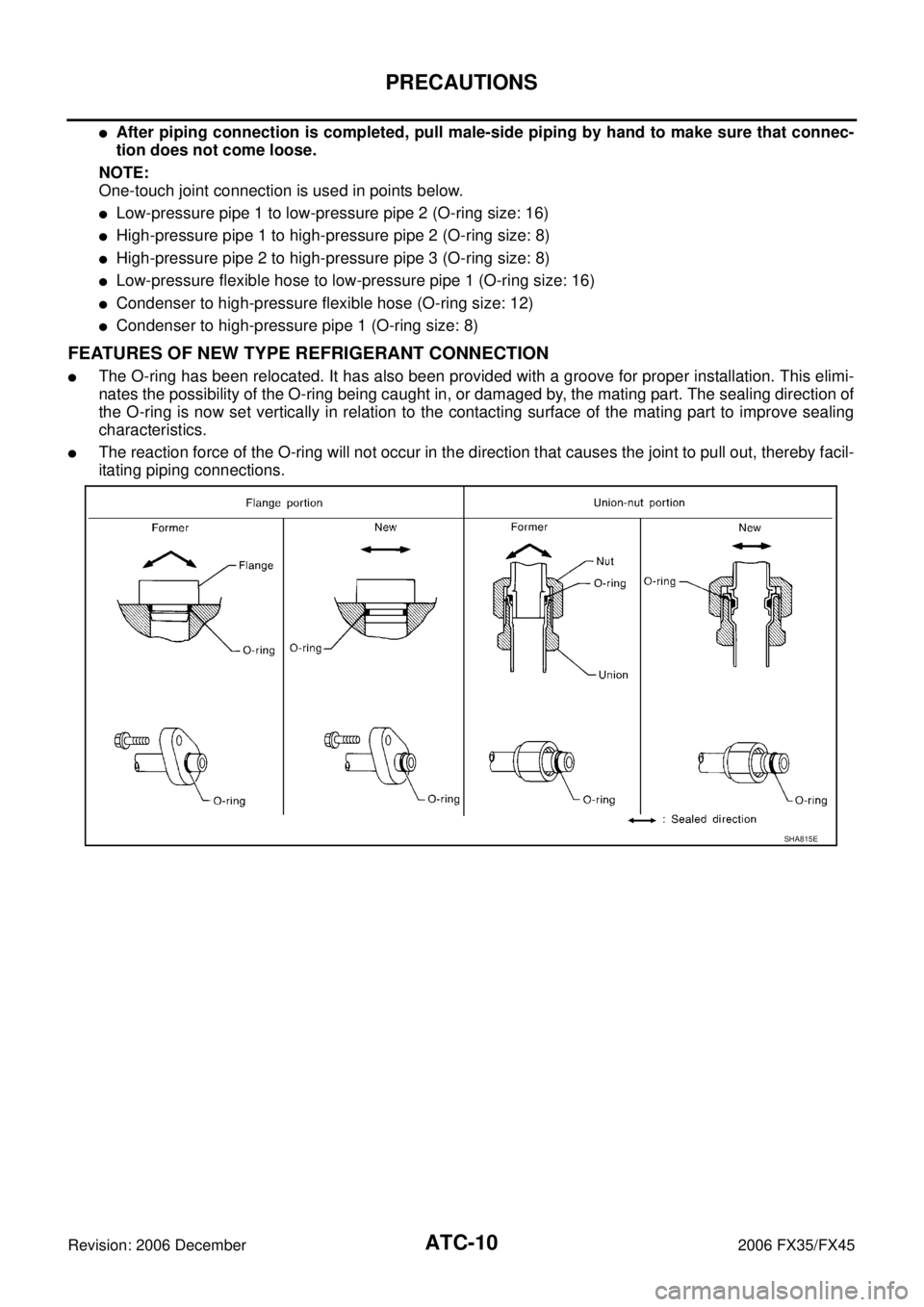
ATC-10
PRECAUTIONS
Revision: 2006 December 2006 FX35/FX45
After piping connection is completed, pull male-side piping by hand to make sure that connec-
tion does not come loose.
NOTE:
One-touch joint connection is used in points below.
Low-pressure pipe 1 to low-pressure pipe 2 (O-ring size: 16)
High-pressure pipe 1 to high-pressure pipe 2 (O-ring size: 8)
High-pressure pipe 2 to high-pressure pipe 3 (O-ring size: 8)
Low-pressure flexible hose to low-pressure pipe 1 (O-ring size: 16)
Condenser to high-pressure flexible hose (O-ring size: 12)
Condenser to high-pressure pipe 1 (O-ring size: 8)
FEATURES OF NEW TYPE REFRIGERANT CONNECTION
The O-ring has been relocated. It has also been provided with a groove for proper installation. This elimi-
nates the possibility of the O-ring being caught in, or damaged by, the mating part. The sealing direction of
the O-ring is now set vertically in relation to the contacting surface of the mating part to improve sealing
characteristics.
The reaction force of the O-ring will not occur in the direction that causes the joint to pull out, thereby facil-
itating piping connections.
SHA815E