Page 3177 of 4462

COIL SPRING AND STRUT FSU-11
C
D
F
G H
I
J
K L
M A
B
FSU
Revision: 2006 December 2006 FX35/FX45
COIL SPRING AND STRUTPFP:55302
Removal and InstallationNES000FS
REMOVAL
1. Remove tires from vehicle with power tool.
2. Remove brake hose lock plate. Then remove brake hose from strut assembly.
3. Remove wheel sensor harness from strut assembly. CAUTION:
Do not pull wheel sensor harness.
4. Remove stabilizer connecting rod upper nut with power tool, separate stabilizer connecting rod and strut assembly.
5. Remove fixing bolts and nuts between strut assembly and steer- ing knuckle with power tool.
6. Remove mounting nuts on mounting insulator bracket with power tool, then remove strut upper plate, strut spacer and strut
from vehicle.
INSTALLATION
Refer to FSU-8, "Removal and Installation" for tightening torque. Install in the reverse order of removal.
NOTE:
Refer to component parts location and do not reuse non-reusable parts.
After removing/installing or replacing suspension components, check wheel alignment. Refer to FSU-6,
"Wheel Alignment Inspection" .
After adjusting wheel alignment, adjust neutral position of steering angle sensor. Refer to BRC-6, "Adjust-
ment of Steering Angle Sensor Neutral Position" .
Check the following item after service.
–Installation condition of wheel sensor harness.
SEIA0328E
SEIA0329E
SEIA0330E
Page 3178 of 4462
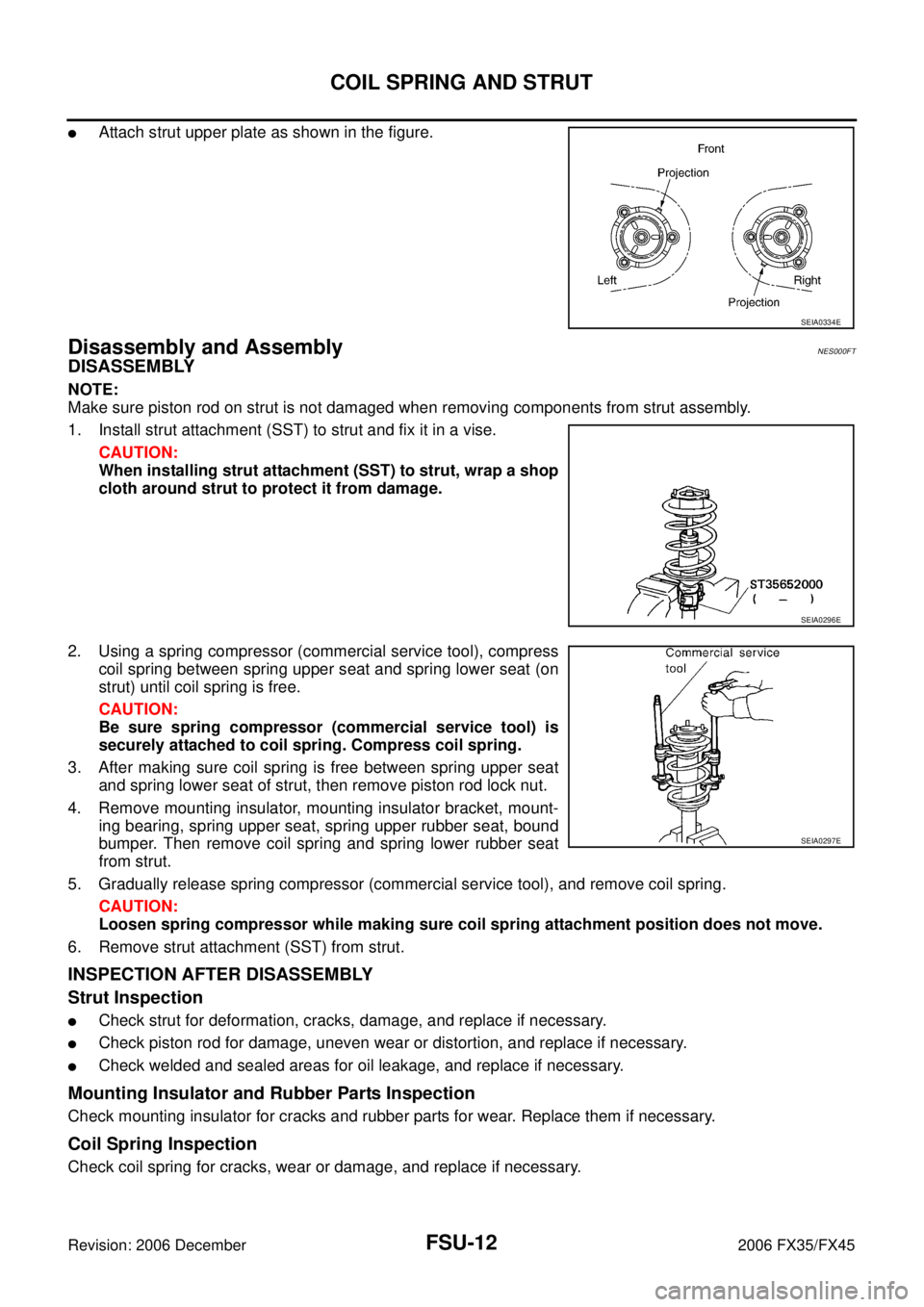
FSU-12
COIL SPRING AND STRUT
Revision: 2006 December 2006 FX35/FX45
Attach strut upper plate as shown in the figure.
Disassembly and AssemblyNES000FT
DISASSEMBLY
NOTE:
Make sure piston rod on strut is not damaged when removing components from strut assembly.
1. Install strut attachment (SST) to strut and fix it in a vise. CAUTION:
When installing strut attachment (SST) to strut, wrap a shop
cloth around strut to protect it from damage.
2. Using a spring compressor (commercial service tool), compress coil spring between spring upper seat and spring lower seat (on
strut) until coil spring is free.
CAUTION:
Be sure spring compressor (commercial service tool) is
securely attached to coil spring. Compress coil spring.
3. After making sure coil spring is free between spring upper seat and spring lower seat of strut, then remove piston rod lock nut.
4. Remove mounting insulator, mounting insulator bracket, mount- ing bearing, spring upper seat, spring upper rubber seat, bound
bumper. Then remove coil spring and spring lower rubber seat
from strut.
5. Gradually release spring compressor (commercial service tool), and remove coil spring. CAUTION:
Loosen spring compressor while making sure coil spring attachment position does not move.
6. Remove strut attachment (SST) from strut.
INSPECTION AFTER DISASSEMBLY
Strut Inspection
Check strut for deformation, cracks, damage, and replace if necessary.
Check piston rod for damage, uneven wear or distortion, and replace if necessary.
Check welded and sealed areas for oil leakage, and replace if necessary.
Mounting Insulator and Rubber Parts Inspection
Check mounting insulator for cracks and rubber parts for wear. Replace them if necessary.
Coil Spring Inspection
Check coil spring for cracks, wear or damage, and replace if necessary.
SEIA0334E
SEIA0296E
SEIA0297E
Page 3179 of 4462
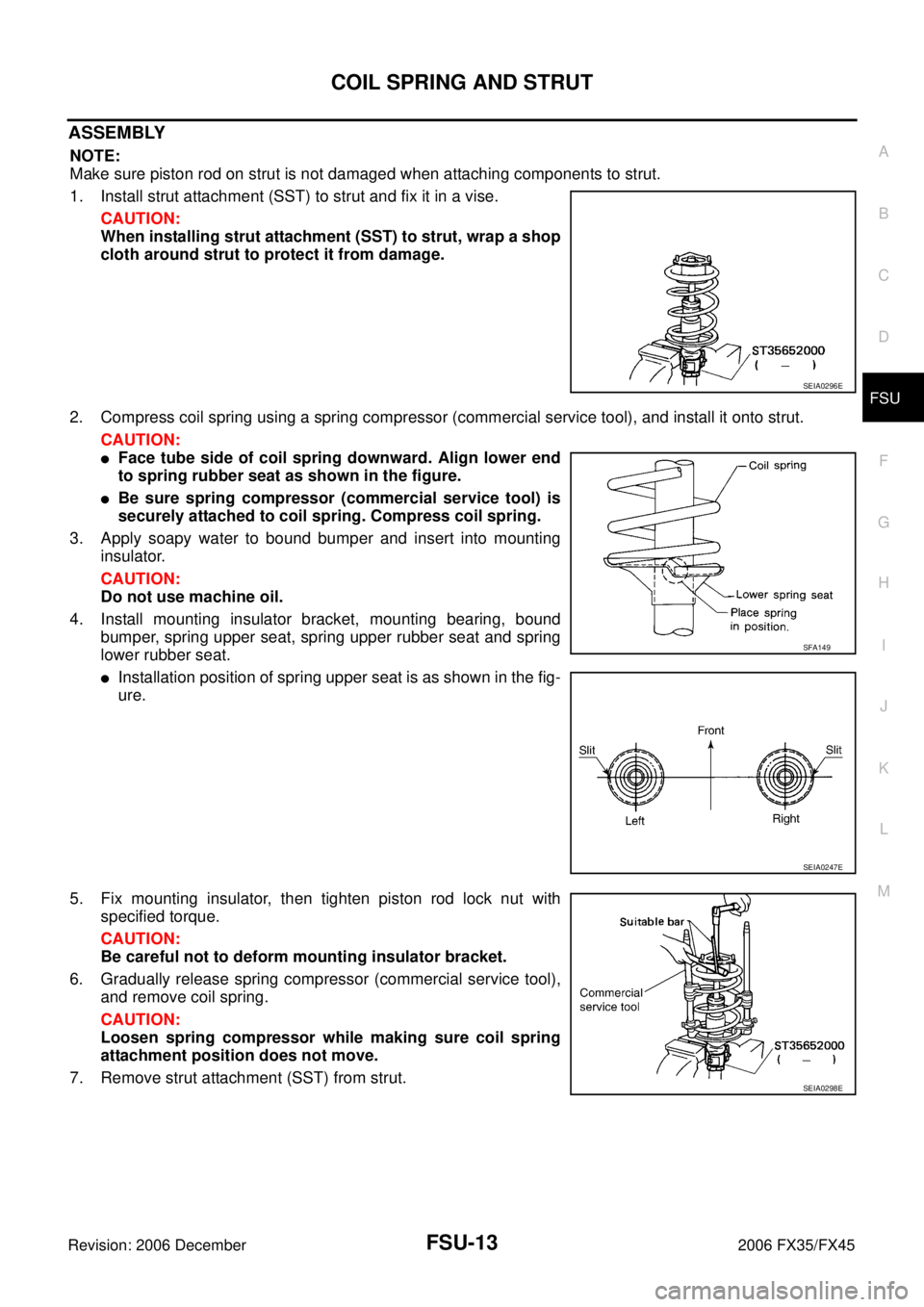
COIL SPRING AND STRUT FSU-13
C
D
F
G H
I
J
K L
M A
B
FSU
Revision: 2006 December 2006 FX35/FX45
ASSEMBLY
NOTE:
Make sure piston rod on strut is not damaged when attaching components to strut.
1. Install strut attachment (SST) to strut and fix it in a vise.
CAUTION:
When installing strut attachment (SST) to strut, wrap a shop
cloth around strut to protect it from damage.
2. Compress coil spring using a spring compressor (commercial service tool), and install it onto strut. CAUTION:
Face tube side of coil spring downward. Align lower end
to spring rubber seat as shown in the figure.
Be sure spring compressor (commercial service tool) is
securely attached to coil spring. Compress coil spring.
3. Apply soapy water to bound bumper and insert into mounting insulator.
CAUTION:
Do not use machine oil.
4. Install mounting insulator bracket, mounting bearing, bound bumper, spring upper seat, spring upper rubber seat and spring
lower rubber seat.
Installation position of spring upper seat is as shown in the fig-
ure.
5. Fix mounting insulator, then tighten piston rod lock nut with specified torque.
CAUTION:
Be careful not to deform mounting insulator bracket.
6. Gradually release spring compressor (commercial service tool), and remove coil spring.
CAUTION:
Loosen spring compressor while making sure coil spring
attachment position does not move.
7. Remove strut attachment (SST) from strut.
SEIA0296E
SFA149
SEIA0247E
SEIA0298E
Page 3180 of 4462
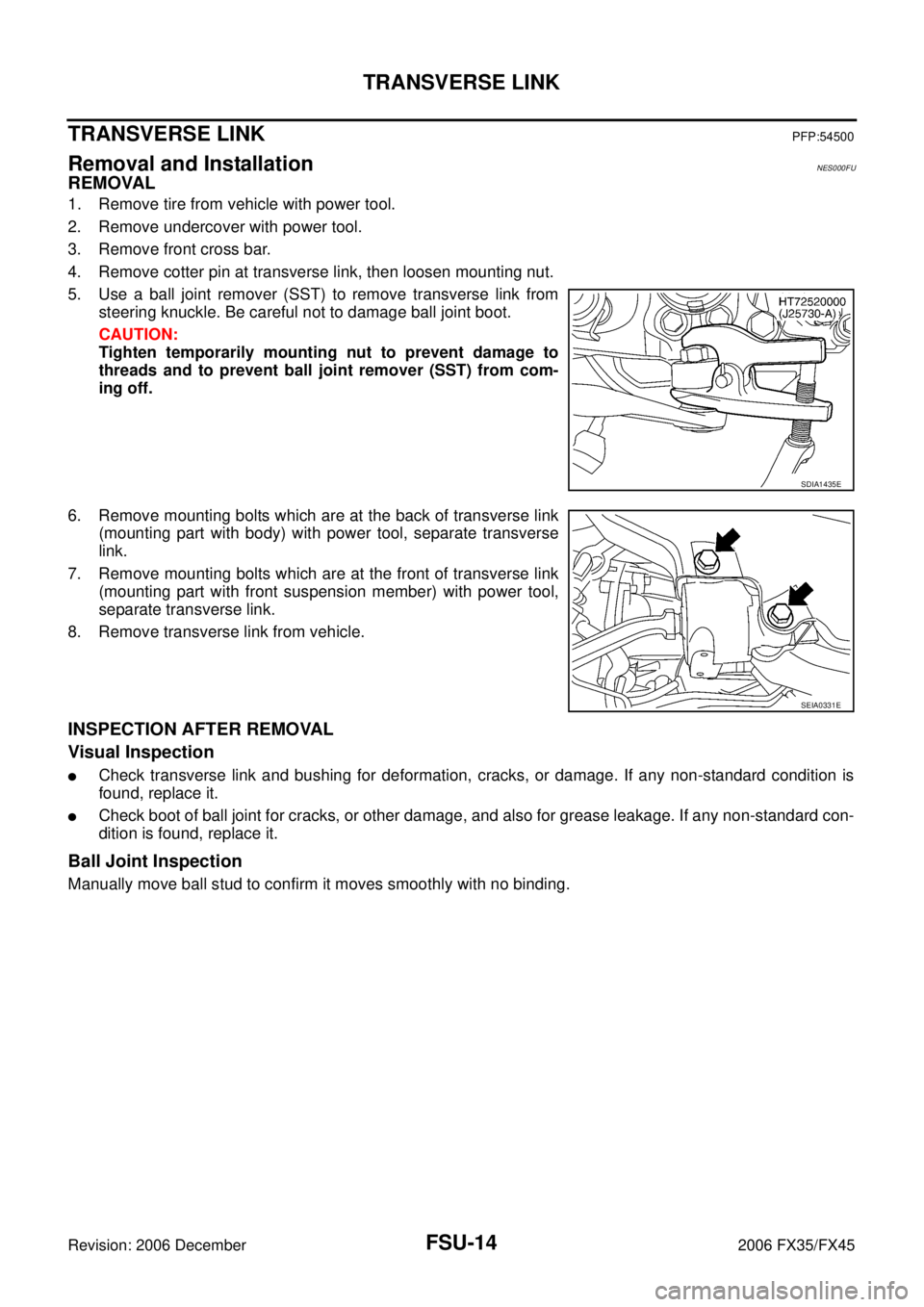
FSU-14
TRANSVERSE LINK
Revision: 2006 December 2006 FX35/FX45
TRANSVERSE LINKPFP:54500
Removal and InstallationNES000FU
REMOVAL
1. Remove tire from vehicle with power tool.
2. Remove undercover with power tool.
3. Remove front cross bar.
4. Remove cotter pin at transverse link, then loosen mounting nut.
5. Use a ball joint remover (SST) to remove transverse link from steering knuckle. Be careful not to damage ball joint boot.
CAUTION:
Tighten temporarily mounting nut to prevent damage to
threads and to prevent ball joint remover (SST) from com-
ing off.
6. Remove mounting bolts which are at the back of transverse link (mounting part with body) with power tool, separate transverse
link.
7. Remove mounting bolts which are at the front of transverse link (mounting part with front suspension member) with power tool,
separate transverse link.
8. Remove transverse link from vehicle.
INSPECTION AFTER REMOVAL
Visual Inspection
Check transverse link and bushing for deformation, cracks, or damage. If any non-standard condition is
found, replace it.
Check boot of ball joint for cracks, or other damage, and also for grease leakage. If any non-standard con-
dition is found, replace it.
Ball Joint Inspection
Manually move ball stud to confirm it moves smoothly with no binding.
SDIA1435E
SEIA0331E
Page 3181 of 4462
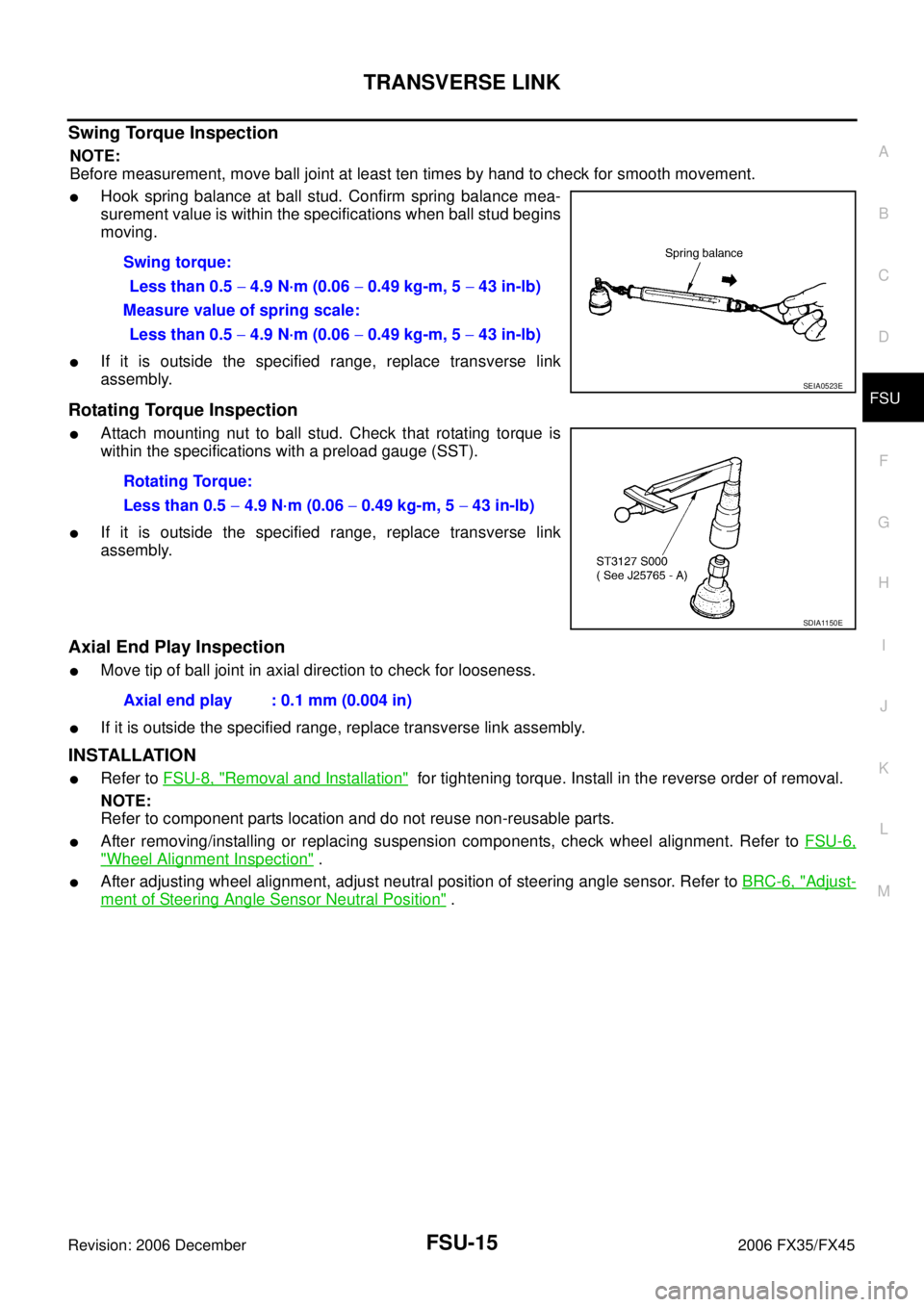
TRANSVERSE LINK FSU-15
C
D
F
G H
I
J
K L
M A
B
FSU
Revision: 2006 December 2006 FX35/FX45
Swing Torque Inspection
NOTE:
Before measurement, move ball joint at least ten times by hand to check for smooth movement.
Hook spring balance at ball stud. Confirm spring balance mea-
surement value is within the specifications when ball stud begins
moving.
If it is outside the specified range, replace transverse link
assembly.
Rotating Torque Inspection
Attach mounting nut to ball stud. Check that rotating torque is
within the specifications with a preload gauge (SST).
If it is outside the specified range, replace transverse link
assembly.
Axial End Play Inspection
Move tip of ball joint in axial direction to check for looseness.
If it is outside the specified range, replace transverse link assembly.
INSTALLATION
Refer to FSU-8, "Removal and Installation" for tightening torque. Install in the reverse order of removal.
NOTE:
Refer to component parts location and do not reuse non-reusable parts.
After removing/installing or replacing suspension components, check wheel alignment. Refer to FSU-6,
"Wheel Alignment Inspection" .
After adjusting wheel alignment, adjust neutral position of steering angle sensor. Refer to BRC-6, "Adjust-
ment of Steering Angle Sensor Neutral Position" .
Swing torque:
Less than 0.5 − 4.9 N·m (0.06 − 0.49 kg-m, 5 − 43 in-lb)
Measure value of spring scale: Less than 0.5 − 4.9 N·m (0.06 − 0.49 kg-m, 5 − 43 in-lb)
SEIA0523E
Rotating Torque:
Less than 0.5 − 4.9 N·m (0.06 − 0.49 kg-m, 5 − 43 in-lb)
SDIA1150E
Axial end play : 0.1 mm (0.004 in)
Page 3182 of 4462

FSU-16
STABILIZER BAR
Revision: 2006 December 2006 FX35/FX45
STABILIZER BARPFP:54611
Removal and InstallationNES000FV
REMOVAL
1. Remove tires from vehicle with power tool.
2. Remove undercover with power tool.
3. Remove stabilizer connecting rod lower nut with power tool, sep- arate stabilizer bar and stabilizer connecting rod.
4. Remove stabilizer clamp mounting bolts and nuts with power tool.
5. Remove stabilizer bar, stabilizer clamp, stabilizer bushing from vehicle.
6. Remove stabilizer connecting rod upper nut with power tool, separate stabilizer connecting rod and strut.
INSPECTION AFTER REMOVAL
Check stabilizer bar, stabilizer connecting rod, stabilizer bushing and stabilizer clamp deformation, cracks and
damage, and replace if necessary.
INSTALLATION
Refer to FSU-8, "Removal and Installation" for tightening torque. Install in the reverse order of removal.
NOTE:
Refer to component parts location and do not reuse non-reusable parts.
After removing/installing or replacing suspension components, check wheel alignment. Refer to FSU-6,
"Wheel Alignment Inspection" .
After adjusting wheel alignment, adjust neutral position of steering angle sensor. Refer to BRC-6, "Adjust-
ment of Steering Angle Sensor Neutral Position" .
Stabilizer bar uses pillow ball type connecting rod. Position ball
joint with case on pillow ball head parallel to stabilizer bar.
SEIA0335E
SEIA0330E
SFA449BB
Page 3183 of 4462
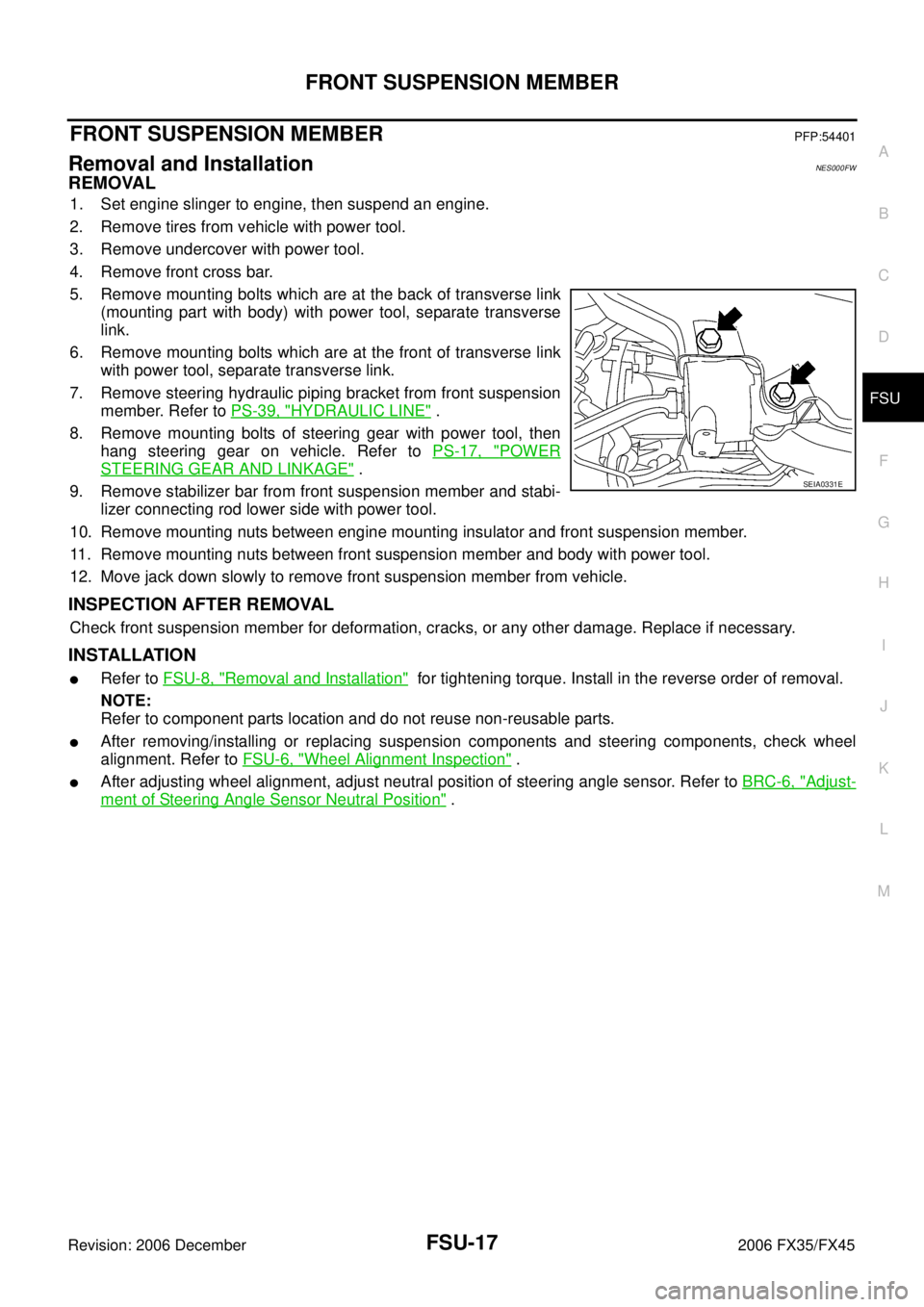
FRONT SUSPENSION MEMBER FSU-17
C
D
F
G H
I
J
K L
M A
B
FSU
Revision: 2006 December 2006 FX35/FX45
FRONT SUSPENSION MEMBERPFP:54401
Removal and InstallationNES000FW
REMOVAL
1. Set engine slinger to engine, then suspend an engine.
2. Remove tires from vehicle with power tool.
3. Remove undercover with power tool.
4. Remove front cross bar.
5. Remove mounting bolts which are at the back of transverse link (mounting part with body) with power tool, separate transverse
link.
6. Remove mounting bolts which are at the front of transverse link with power tool, separate transverse link.
7. Remove steering hydraulic piping bracket from front suspension member. Refer to PS-39, "
HYDRAULIC LINE" .
8. Remove mounting bolts of steering gear with power tool, then hang steering gear on vehicle. Refer to PS-17, "
POWER
STEERING GEAR AND LINKAGE" .
9. Remove stabilizer bar from front suspension member and stabi- lizer connecting rod lower side with power tool.
10. Remove mounting nuts between engine mounting insulator and front suspension member.
11. Remove mounting nuts between front suspension member and body with power tool.
12. Move jack down slowly to remove front suspension member from vehicle.
INSPECTION AFTER REMOVAL
Check front suspension member for deformation, cracks, or any other damage. Replace if necessary.
INSTALLATION
Refer to FSU-8, "Removal and Installation" for tightening torque. Install in the reverse order of removal.
NOTE:
Refer to component parts location and do not reuse non-reusable parts.
After removing/installing or replacing suspension components and steering components, check wheel
alignment. Refer to FSU-6, "
Wheel Alignment Inspection" .
After adjusting wheel alignment, adjust neutral position of steering angle sensor. Refer to BRC-6, "Adjust-
ment of Steering Angle Sensor Neutral Position" .
SEIA0331E
Page 3184 of 4462
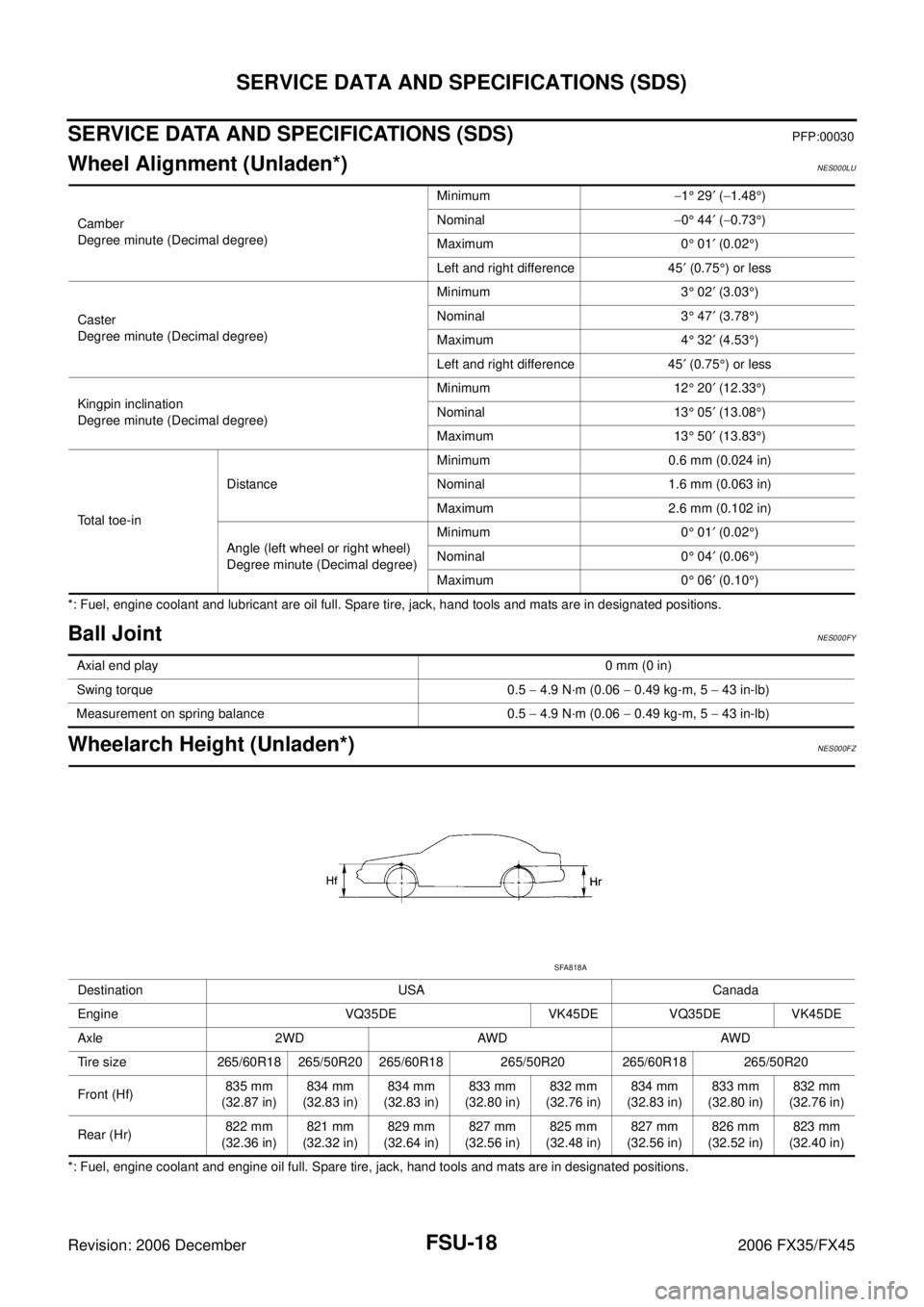
FSU-18
SERVICE DATA AND SPECIFICATIONS (SDS)
Revision: 2006 December 2006 FX35/FX45
SERVICE DATA AND SPECIFICATIONS (SDS)PFP:00030
Wheel Alignment (Unladen*)NES000LU
*: Fuel, engine coolant and lubricant are oil full. Spare tire, jack, hand tools and mats are in designated positions.
Ball JointNES000FY
Wheelarch Height (Unladen*)NES000FZ
*: Fuel, engine coolant and engine oil full. Spare tire, jack, hand tools and mats are in designated positions. Camber
Degree minute (Decimal degree) Minimum
−1 ° 29 ′ ( −1.48 °)
Nominal −0 ° 44 ′ ( −0.73 °)
Maximum 0 ° 01 ′ (0.02 °)
Left and right difference 45 ′ (0.75 °) or less
Caster
Degree minute (Decimal degree) Minimum 3
° 02 ′ (3.03 °)
Nominal 3 ° 47 ′ (3.78 °)
Maximum 4 ° 32 ′ (4.53 °)
Left and right difference 45 ′ (0.75 °) or less
Kingpin inclination
Degree minute (Decimal degree) Minimum 12
° 20 ′ (12.33 °)
Nominal 13 ° 05 ′ (13.08 °)
Maximum 13 ° 50 ′ (13.83 °)
Total toe-in Distance
Minimum 0.6 mm (0.024 in)
Nominal 1.6 mm (0.063 in)
Maximum 2.6 mm (0.102 in)
Angle (left wheel or right wheel)
Degree minute (Decimal degree) Minimum 0
° 01 ′ (0.02 °)
Nominal 0 ° 04 ′ (0.06 °)
Maximum 0 ° 06 ′ (0.10 °)
Axial end play 0 mm (0 in)
Swing torque 0.5 − 4.9 N·m (0.06 − 0.49 kg-m, 5 − 43 in-lb)
Measurement on spring balance 0.5 − 4.9 N·m (0.06 − 0.49 kg-m, 5 − 43 in-lb)
Destination USA Canada
Engine VQ35DE VK45DE VQ35DE VK45DE
Axle 2WD AWD AWD
Tire size 265/60R18 265/50R20 265/60R18 265/50R20 265/60R18 265/50R20
Front (Hf) 835 mm
(32.87 in) 834 mm
(32.83 in) 834 mm
(32.83 in) 833 mm
(32.80 in) 832 mm
(32.76 in) 834 mm
(32.83 in) 833 mm
(32.80 in) 832 mm
(32.76 in)
Rear (Hr) 822 mm
(32.36 in) 821 mm
(32.32 in) 829 mm
(32.64 in) 827 mm
(32.56 in) 825 mm
(32.48 in) 827 mm
(32.56 in) 826 mm
(32.52 in) 823 mm
(32.40 in)
SFA818A