Page 1129 of 4462
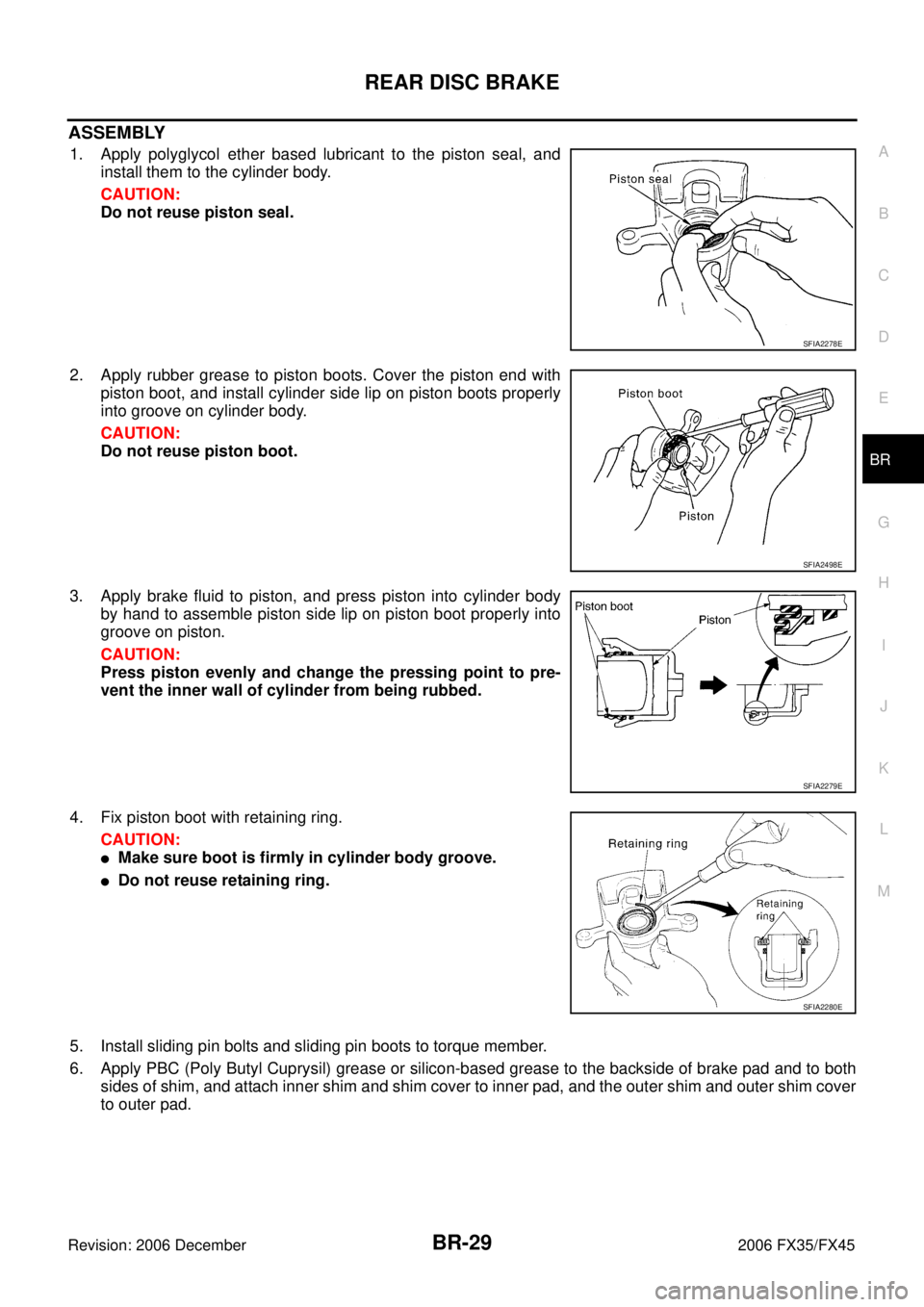
REAR DISC BRAKE BR-29
C
D E
G H
I
J
K L
M A
B
BR
Revision: 2006 December 2006 FX35/FX45
ASSEMBLY
1. Apply polyglycol ether based lubricant to the piston seal, and install them to the cylinder body.
CAUTION:
Do not reuse piston seal.
2. Apply rubber grease to piston boots. Cover the piston end with piston boot, and install cylinder side lip on piston boots properly
into groove on cylinder body.
CAUTION:
Do not reuse piston boot.
3. Apply brake fluid to piston, and press piston into cylinder body by hand to assemble piston side lip on piston boot properly into
groove on piston.
CAUTION:
Press piston evenly and change the pressing point to pre-
vent the inner wall of cylinder from being rubbed.
4. Fix piston boot with retaining ring. CAUTION:
Make sure boot is firmly in cylinder body groove.
Do not reuse retaining ring.
5. Install sliding pin bolts and sliding pin boots to torque member.
6. Apply PBC (Poly Butyl Cuprysil) grease or silicon-based grease to the backside of brake pad and to both sides of shim, and attach inner shim and shim cover to inner pad, and the outer shim and outer shim cover
to outer pad.
SFIA2278E
SFIA2498E
SFIA2279E
SFIA2280E
Page 1130 of 4462
BR-30
REAR DISC BRAKE
Revision: 2006 December 2006 FX35/FX45
7. Assembling shims and shim covers to pad. CAUTION:
When attaching pad retainer, install it firmly so that it does
not float up higher than torque member, as shown in the fig-
ure.
8. Install brake pad retainer and pad to torque member.
9. Install cylinder body. Tighten sliding pin bolts to the specified torque. Refer to BR-25, "
Components" .
10. After installing caliper assembly, refill with new brake fluid and bleed air. Refer to BR-10, "
Bleeding Brake System" .PFIA0273E
Page 1131 of 4462
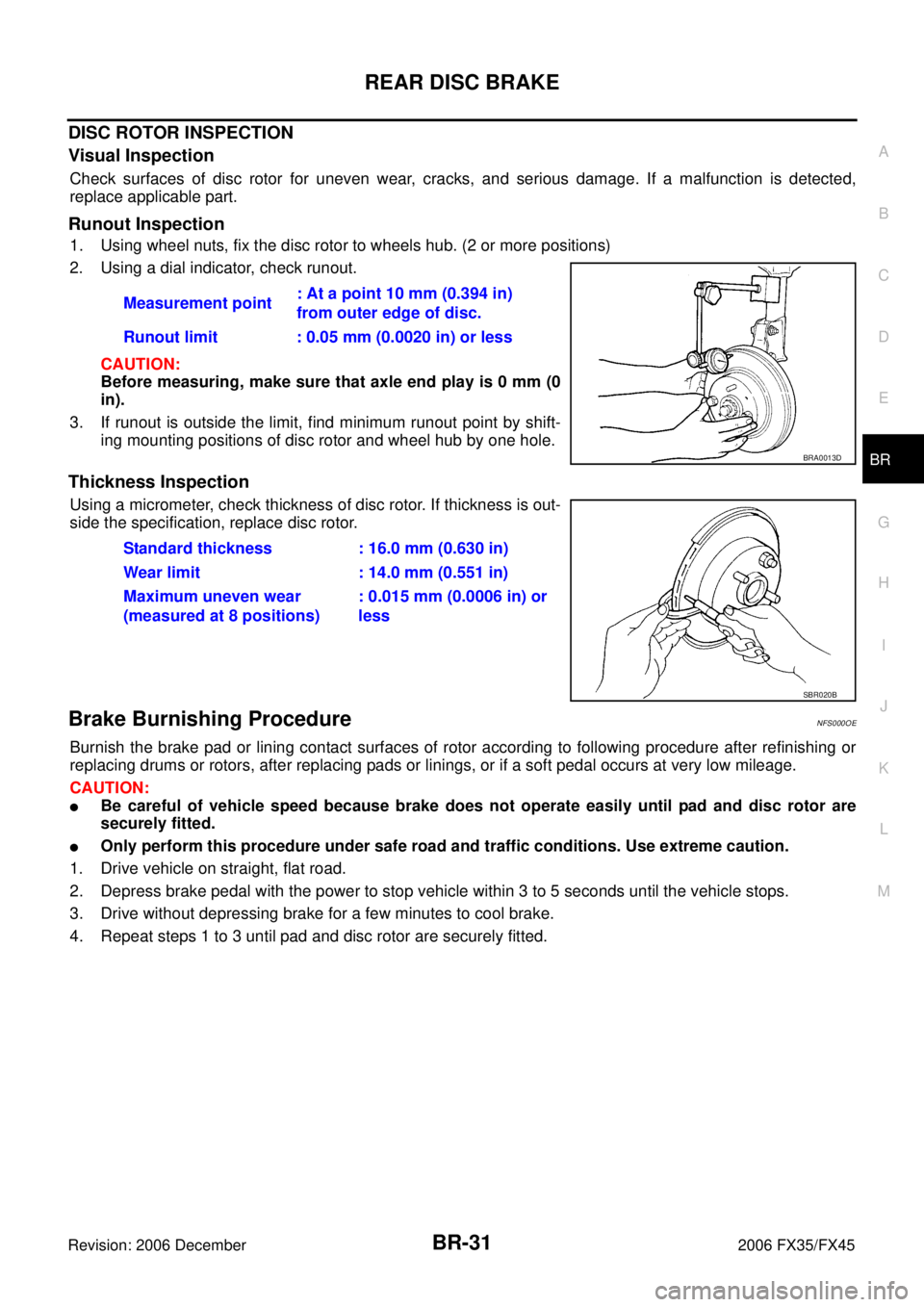
REAR DISC BRAKE BR-31
C
D E
G H
I
J
K L
M A
B
BR
Revision: 2006 December 2006 FX35/FX45
DISC ROTOR INSPECTION
Visual Inspection
Check surfaces of disc rotor for uneven wear, cracks, and serious damage. If a malfunction is detected,
replace applicable part.
Runout Inspection
1. Using wheel nuts, fix the disc rotor to wheels hub. (2 or more positions)
2. Using a dial indicator, check runout.
CAUTION:
Before measuring, make sure that axle end play is 0 mm (0
in).
3. If runout is outside the limit, find minimum runout point by shift- ing mounting positions of disc rotor and wheel hub by one hole.
Thickness Inspection
Using a micrometer, check thickness of disc rotor. If thickness is out-
side the specification, replace disc rotor.
Brake Burnishing ProcedureNFS000OE
Burnish the brake pad or lining contact surfaces of rotor according to following procedure after refinishing or
replacing drums or rotors, after replacing pads or linings, or if a soft pedal occurs at very low mileage.
CAUTION:
Be careful of vehicle speed because brake does not operate easily until pad and disc rotor are
securely fitted.
Only perform this procedure under safe road and traffic conditions. Use extreme caution.
1. Drive vehicle on straight, flat road.
2. Depress brake pedal with the power to stop vehicle within 3 to 5 seconds until the vehicle stops.
3. Drive without depressing brake for a few minutes to cool brake.
4. Repeat steps 1 to 3 until pad and disc rotor are securely fitted. Measurement point
: At a point 10 mm (0.394 in)
from outer edge of disc.
Runout limit : 0.05 mm (0.0020 in) or less
BRA0013D
Standard thickness : 16.0 mm (0.630 in)
Wear limit : 14.0 mm (0.551 in)
Maximum uneven wear
(measured at 8 positions) : 0.015 mm (0.0006 in) or
less
SBR020B
Page 1132 of 4462
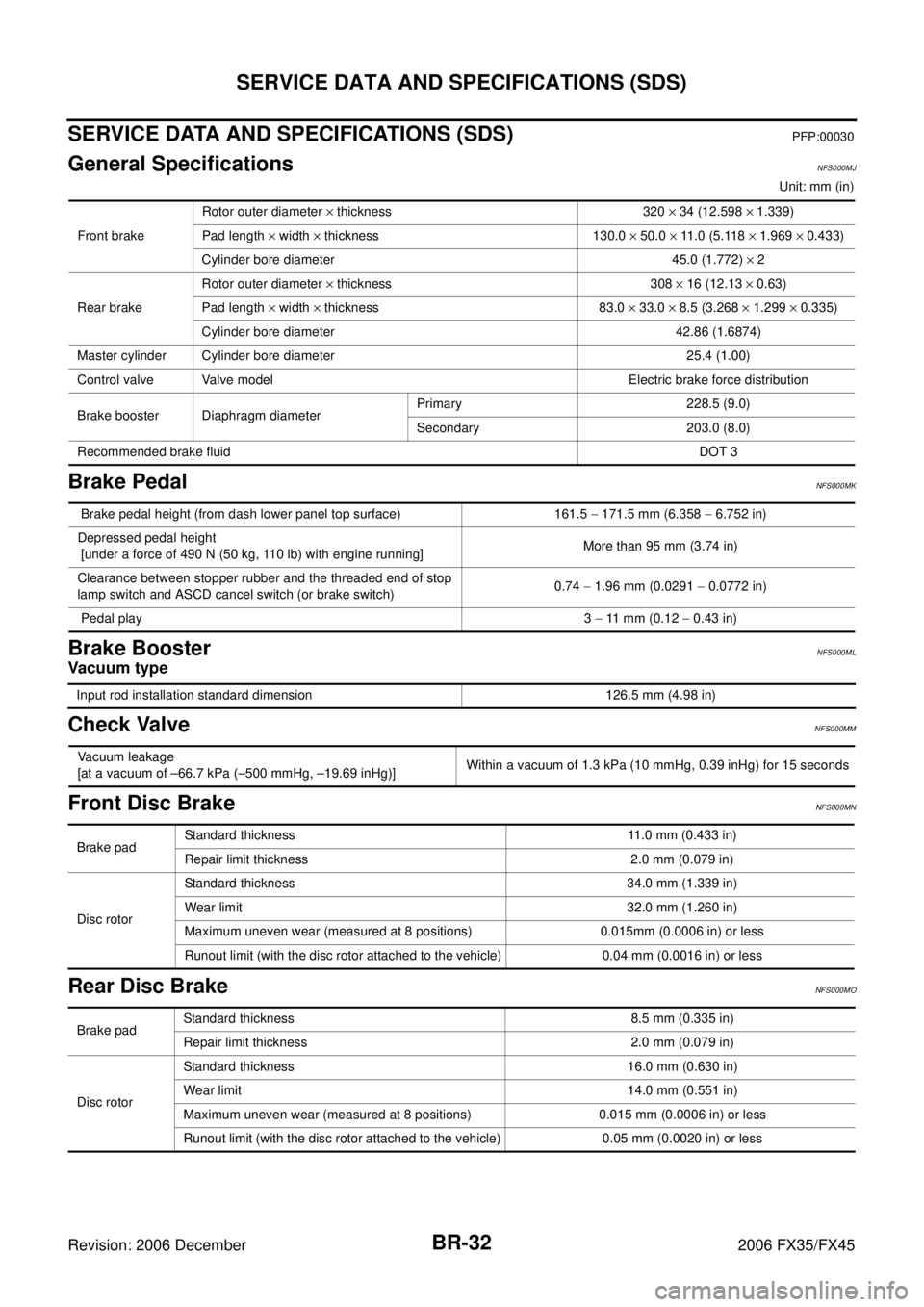
BR-32
SERVICE DATA AND SPECIFICATIONS (SDS)
Revision: 2006 December 2006 FX35/FX45
SERVICE DATA AND SPECIFICATIONS (SDS)PFP:00030
General SpecificationsNFS000MJ
Unit: mm (in)
Brake PedalNFS000MK
Brake BoosterNFS000ML
Vacuum type
Check ValveNFS000MM
Front Disc BrakeNFS000MN
Rear Disc BrakeNFS000MO
Front brake Rotor outer diameter
× thickness 320 × 34 (12.598 × 1.339)
Pad length × width × thickness 130.0 × 50.0 × 11.0 (5.118 × 1.969 × 0.433)
Cylinder bore diameter 45.0 (1.772) × 2
Rear brake Rotor outer diameter
× thickness 308 × 16 (12.13 × 0.63)
Pad length × width × thickness 83.0 × 33.0 × 8.5 (3.268 × 1.299 × 0.335)
Cylinder bore diameter 42.86 (1.6874)
Master cylinder Cylinder bore diameter 25.4 (1.00)
Control valve Valve model Electric brake force distribution
Brake booster Diaphragm diameter Primary 228.5 (9.0)
Secondary 203.0 (8.0)
Recommended brake fluid DOT 3
Brake pedal height (from dash lower panel top surface) 161.5 − 171.5 mm (6.358 − 6.752 in)
Depressed pedal height
[under a force of 490 N (50 kg, 110 lb) with engine running] More than 95 mm (3.74 in)
Clearance between stopper rubber and the threaded end of stop
lamp switch and ASCD cancel switch (or brake switch) 0.74
− 1.96 mm (0.0291 − 0.0772 in)
Pedal play 3 − 11 mm (0.12 − 0.43 in)
Input rod installation standard dimension 126.5 mm (4.98 in)
Vacuum leakage
[at a vacuum of –66.7 kPa (–500 mmHg, –19.69 inHg)] Within a vacuum of 1.3 kPa (10 mmHg, 0.39 inHg) for 15 seconds
Brake pad Standard thickness 11.0 mm (0.433 in)
Repair limit thickness 2.0 mm (0.079 in)
Disc rotor Standard thickness 34.0 mm (1.339 in)
Wear limit 32.0 mm (1.260 in)
Maximum uneven wear (measured at 8 positions) 0.015mm (0.0006 in) or less
Runout limit (with the disc rotor attached to the vehicle) 0.04 mm (0.0016 in) or less
Brake pad Standard thickness 8.5 mm (0.335 in)
Repair limit thickness 2.0 mm (0.079 in)
Disc rotor Standard thickness 16.0 mm (0.630 in)
Wear limit 14.0 mm (0.551 in)
Maximum uneven wear (measured at 8 positions) 0.015 mm (0.0006 in) or less
Runout limit (with the disc rotor attached to the vehicle) 0.05 mm (0.0020 in) or less
Page 1133 of 4462
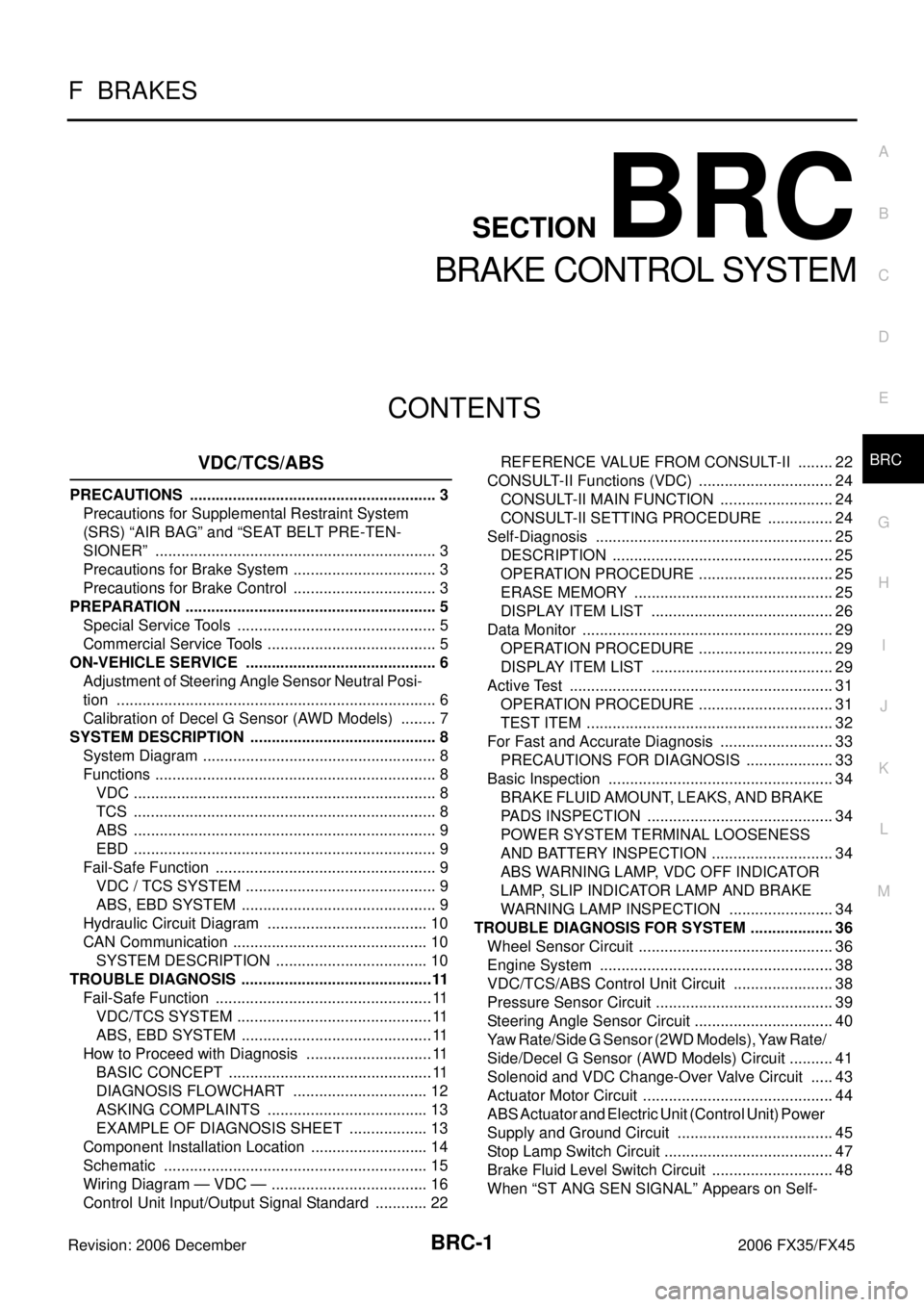
BRC-1
BRAKE CONTROL SYSTEM
F BRAKES
CONTENTS
C
D E
G H
I
J
K L
M
SECTION BRC
A
B
BRC
Revision: 2006 December 2006 FX35/FX45
BRAKE CONTROL SYSTEM
VDC/TCS/ABS
PRECAUTIONS ..................................................... ..... 3
Precautions for Supplemental Restraint System
(SRS) “AIR BAG” and “SEAT BELT PRE-TEN-
SIONER” ............................................................. ..... 3
Precautions for Brake System ............................. ..... 3
Precautions for Brake Control ............................. ..... 3
PREPARATION ...................................................... ..... 5
Special Service Tools .......................................... ..... 5
Commercial Service Tools ................................... ..... 5
ON-VEHICLE SERVICE ........................................ ..... 6
Adjustment of Steering Angle Sensor Neutral Posi-
tion ...................................................................... ..... 6
Calibration of Decel G Sensor (AWD Models) .... ..... 7
SYSTEM DESCRIPTION ....................................... ..... 8
System Diagram .................................................. ..... 8
Functions ............................................................. ..... 8
VDC .................................................................. ..... 8
TCS .................................................................. ..... 8
ABS .................................................................. ..... 9
EBD .................................................................. ..... 9
Fail-Safe Function ............................................... ..... 9
VDC / TCS SYSTEM ........................................ ..... 9
ABS, EBD SYSTEM ......................................... ..... 9
Hydraulic Circuit Diagram ................................... ... 10
CAN Communication ........................................... ... 10
SYSTEM DESCRIPTION ................................. ... 10
TROUBLE DIAGNOSIS ......................................... ....11
Fail-Safe Function ............................................... .... 11
VDC/TCS SYSTEM .......................................... .... 11
ABS, EBD SYSTEM ......................................... .... 11
How to Proceed with Diagnosis .......................... .... 11
BASIC CONCEPT ............................................ .... 11
DIAGNOSIS FLOWCHART ............................. ... 12
ASKING COMPLAINTS ................................... ... 13
EXAMPLE OF DIAGNOSIS SHEET ................ ... 13
Component Installation Location ......................... ... 14
Schematic ........................................................... ... 15
Wiring Diagram — VDC — .................................. ... 16
Control Unit Input/Output Signal Standard .......... ... 22 REFERENCE VALUE FROM CONSULT-II ......
... 22
CONSULT-II Functions (VDC) ............................. ... 24
CONSULT-II MAIN FUNCTION ........................ ... 24
CONSULT-II SETTING PROCEDURE ............. ... 24
Self-Diagnosis ..................................................... ... 25
DESCRIPTION ................................................. ... 25
OPERATION PROCEDURE ............................. ... 25
ERASE MEMORY ............................................ ... 25
DISPLAY ITEM LIST ........................................ ... 26
Data Monitor ........................................................ ... 29
OPERATION PROCEDURE ............................. ... 29
DISPLAY ITEM LIST ........................................ ... 29
Active Test ........................................................... ... 31
OPERATION PROCEDURE ............................. ... 31
TEST ITEM ....................................................... ... 32
For Fast and Accurate Diagnosis ........................ ... 33
PRECAUTIONS FOR DIAGNOSIS .................. ... 33
Basic Inspection .................................................. ... 34
BRAKE FLUID AMOUNT, LEAKS, AND BRAKE
PADS INSPECTION ......................................... ... 34
POWER SYSTEM TERMINAL LOOSENESS
AND BATTERY INSPECTION .......................... ... 34
ABS WARNING LAMP, VDC OFF INDICATOR
LAMP, SLIP INDICATOR LAMP AND BRAKE
WARNING LAMP INSPECTION ...................... ... 34
TROUBLE DIAGNOSIS FOR SYSTEM ................. ... 36
Wheel Sensor Circuit ........................................... ... 36
Engine System .................................................... ... 38
VDC/TCS/ABS Control Unit Circuit ..................... ... 38
Pressure Sensor Circuit ....................................... ... 39
Steering Angle Sensor Circuit .............................. ... 40
Yaw Rate/Side G Sensor (2WD Models), Yaw Rate/
Side/Decel G Sensor (AWD Models) Circuit ........ ... 41
Solenoid and VDC Change-Over Valve Circuit ... ... 43
Actuator Motor Circuit .......................................... ... 44
ABS Actuator and Electric Unit (Control Unit) Power
Supply and Ground Circuit .................................. ... 45
Stop Lamp Switch Circuit ..................................... ... 47
Brake Fluid Level Switch Circuit .......................... ... 48
When “ST ANG SEN SIGNAL” Appears on Self-
Page 1134 of 4462
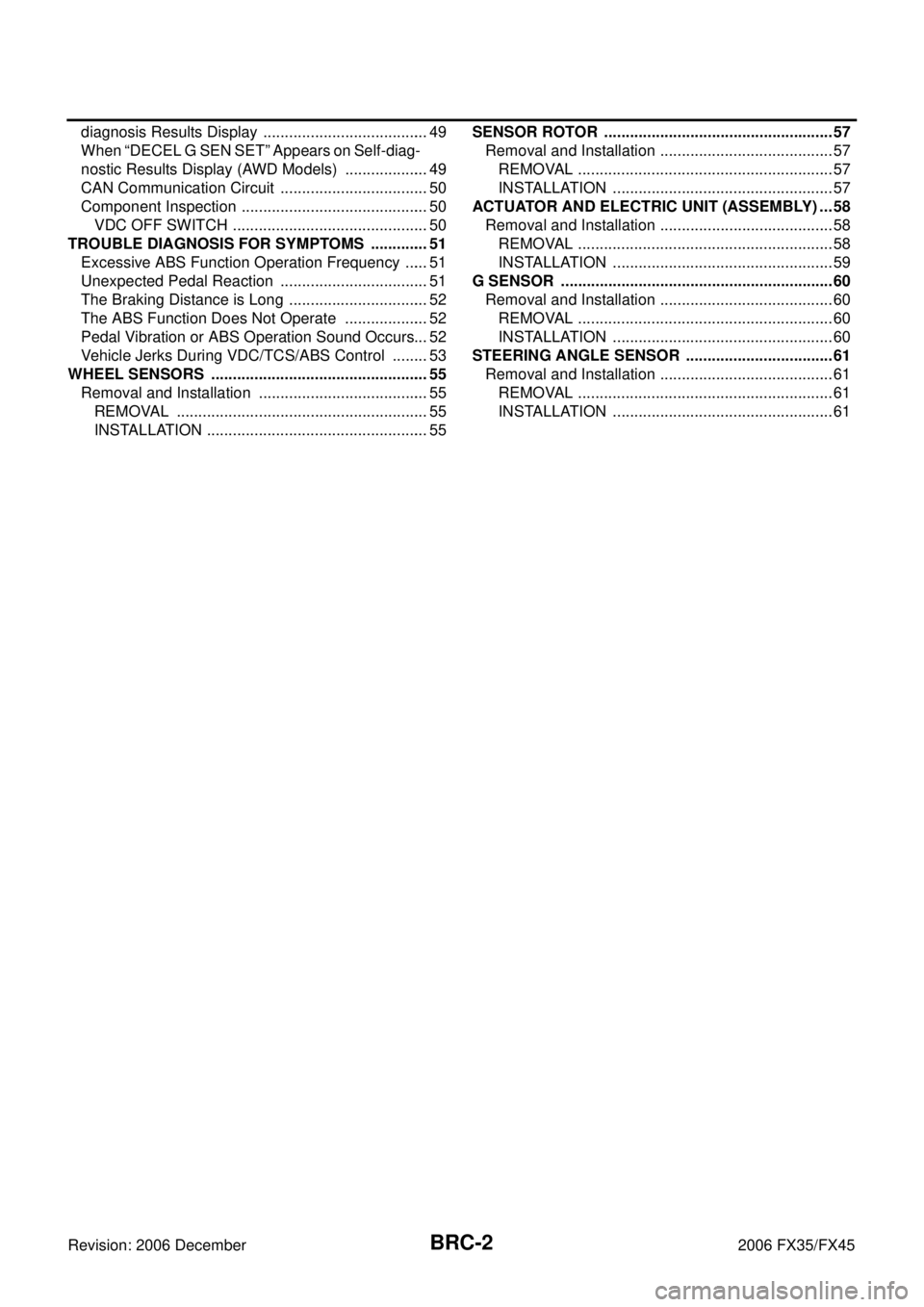
BRC-2Revision: 2006 December 2006 FX35/FX45 diagnosis Results Display ....................................
... 49
When “DECEL G SEN SET” Appears on Self-diag-
nostic Results Display (AWD Models) ................. ... 49
CAN Communication Circuit ................................ ... 50
Component Inspection ......................................... ... 50
VDC OFF SWITCH ........................................... ... 50
TROUBLE DIAGNOSIS FOR SYMPTOMS ........... ... 51
Excessive ABS Function Operation Frequency ... ... 51
Unexpected Pedal Reaction ................................ ... 51
The Braking Distance is Long .............................. ... 52
The ABS Function Does Not Operate ................. ... 52
Pedal Vibration or ABS Operation Sound Occurs ... 52
Vehicle Jerks During VDC/TCS/ABS Control ...... ... 53
WHEEL SENSORS ................................................ ... 55
Removal and Installation ..................................... ... 55
REMOVAL ........................................................ ... 55
INSTALLATION ................................................. ... 55 SENSOR ROTOR ...................................................
... 57
Removal and Installation ...................................... ... 57
REMOVAL ......................................................... ... 57
INSTALLATION ................................................. ... 57
ACTUATOR AND ELECTRIC UNIT (ASSEMBLY) ... 58 Removal and Installation ...................................... ... 58
REMOVAL ......................................................... ... 58
INSTALLATION ................................................. ... 59
G SENSOR ............................................................. ... 60
Removal and Installation ...................................... ... 60
REMOVAL ......................................................... ... 60
INSTALLATION ................................................. ... 60
STEERING ANGLE SENSOR ................................ ... 61
Removal and Installation ...................................... ... 61
REMOVAL ......................................................... ... 61
INSTALLATION ................................................. ... 61
Page 1135 of 4462
![INFINITI FX35 2006 Service Manual PRECAUTIONS BRC-3
[VDC/TCS/ABS]
C
D E
G H
I
J
K L
M A
B
BRC
Revision: 2006 December 2006 FX35/FX45
[VDC/TCS/ABS]PRECAUTIONSPFP:00001
Precautions for Supplemental Restraint System (SRS) “ INFINITI FX35 2006 Service Manual PRECAUTIONS BRC-3
[VDC/TCS/ABS]
C
D E
G H
I
J
K L
M A
B
BRC
Revision: 2006 December 2006 FX35/FX45
[VDC/TCS/ABS]PRECAUTIONSPFP:00001
Precautions for Supplemental Restraint System (SRS) “](/manual-img/42/57019/w960_57019-1134.png)
PRECAUTIONS BRC-3
[VDC/TCS/ABS]
C
D E
G H
I
J
K L
M A
B
BRC
Revision: 2006 December 2006 FX35/FX45
[VDC/TCS/ABS]PRECAUTIONSPFP:00001
Precautions for Supplemental Restraint System (SRS) “AIR BAG” and “SEAT
BELT PRE-TENSIONER”
NFS000MW
The Supplemental Restraint System such as “AIR BAG” and “SEAT BELT PRE-TENSIONER”, used along
with a front seat belt, helps to reduce the risk or severity of injury to the driver and front passenger for certain
types of collision. This system includes seat belt switch inputs and dual stage front air bag modules. The SRS
system uses the seat belt switches to determine the front air bag deployment, and may only deploy one front
air bag, depending on the severity of a collision and whether the front occupants are belted or unbelted.
Information necessary to service the system safely is included in the SRS and SB section of this Service Man-
ual.
WARNING:
To avoid rendering the SRS inoperative, which could increase the risk of personal injury or death
in the event of a collision which would result in air bag inflation, all maintenance must be per-
formed by an authorized NISSAN/INFINITI dealer.
Improper maintenance, including incorrect removal and installation of the SRS, can lead to per-
sonal injury caused by unintentional activation of the system. For removal of Spiral Cable and Air
Bag Module, see the SRS section.
Do not use electrical test equipment on any circuit related to the SRS unless instructed to in this
Service Manual. SRS wiring harnesses can be identified by yellow and/or orange harnesses or
harness connectors.
Precautions for Brake SystemNFS000MX
Recommended fluid is brake fluid “DOT 3”. Refer to MA-12, "RECOMMENDED FLUIDS AND LUBRI-
CANTS" .
Do not reuse drained brake fluid.
Be careful not to splash brake fluid on painted areas such as body. If brake fluid is splashed, wipe it off
and flush area with water immediately.
Do not use mineral oils such as gasoline or kerosene to clean. They will ruin rubber parts and cause
improper operation.
Using a flare nut crowfoot and torque wrench, securely tighten
brake tube flare nuts.
Brake system is an important safety part. If a brake fluid leak is
detected, always disassemble the affected part. If a malfunction
is detected, replace part with a new one.
Before working, turn ignition switch OFF and disconnect electri-
cal connectors of ABS actuator and electric unit (control unit) or
battery negative terminal.
When installing brake piping, be sure to check torque.
WARNING:
Clean brake pads and shoes with a waste cloth, then wipe with
a dust collector.
Precautions for Brake ControlNFS000MY
During VDC/TCS/ABS operation, brake pedal lightly vibrates and a mechanical noise may be heard. This
is normal.
Just after starting vehicle after turning ignition switch ON, brake pedal may vibrate or motor operating
noise may be heard from engine room. This is a normal status of operation check.
Stopping distance may be longer than that of vehicles without ABS when vehicle drives on rough, gravel,
or snow-covered (fresh, deep snow) roads.
When an error is indicated by ABS or another warning lamp, collect all necessary information from cus-
tomer (what symptoms are present under what conditions) and check for simple causes before starting
diagnostic servicing. Besides electrical system inspection, check booster operation, brake fluid level, and
fluid leaks.
If tire size and type are used in an improper combination, or brake pads are not Genuine NISSAN parts,
stopping distance or steering stability may deteriorate.
SBR686C
Page 1136 of 4462
![INFINITI FX35 2006 Service Manual BRC-4
[VDC/TCS/ABS]
PRECAUTIONS
Revision: 2006 December 2006 FX35/FX45
If there is a radio, antenna, or antenna lead-in wire (including wiring) near control module, VDC/TCS/ABS
function may have a m INFINITI FX35 2006 Service Manual BRC-4
[VDC/TCS/ABS]
PRECAUTIONS
Revision: 2006 December 2006 FX35/FX45
If there is a radio, antenna, or antenna lead-in wire (including wiring) near control module, VDC/TCS/ABS
function may have a m](/manual-img/42/57019/w960_57019-1135.png)
BRC-4
[VDC/TCS/ABS]
PRECAUTIONS
Revision: 2006 December 2006 FX35/FX45
If there is a radio, antenna, or antenna lead-in wire (including wiring) near control module, VDC/TCS/ABS
function may have a malfunction or error.
If aftermarket parts (car stereo, CD player, etc.) have been installed, check for incidents such as harness
pinches, open circuits, and improper wiring.
If the following components are replaced with non-genuine components or converted, VDC OFF indicator
lamp and SLIP indicator lamp may turn on or the VDC system may not operate properly. Components
related to suspension (shock absorber, strut, spring, bushing, etc.), Tires, wheels (exclude specified size),
components related to brake (pad, rotor, caliper, etc.), components related to engine (muffler, ECM, etc.),
components related to body reinforcement (roll bar, tower bar, etc.).
Driving in the condition of breakage or excessive wear of suspension, tires or components related to the
brakes may cause VDC OFF indicator lamp and SLIP indicator lamp turn on, and the VDC system may
not operate properly.
When the TCS or VDC is activated by sudden acceleration or sudden turn, some noise may occur. The
noise is a result of the normal operation of the TCS and VDC.
When driving on roads which have extreme slopes (such as mountainous roads) or high banks (such as
sharp carves on a freeway), the VDC may not operate normally, or VDC OFF indicator lamp and SLIP
indicator lamp may turn on. However, this is not a malfunction, if normal operation can be resumed after
restarting engine.
Sudden turns (such as spin turns, acceleration turns), drifting, etc. When VDC function is OFF (VDC OFF
SW ON) may cause the G sensor system indicate a malfunction. However, this is not a malfunction, if nor-
mal operation can be resumed after restarting engine.
Change 4 tires at a time. Be sure to use specified-size tires that have the same brand name and pattern.
Wheel sensor errors can be detected be self-diagnosis when tires have wide abrasion variations or the
size is different from the genuine tires.