Page 4081 of 4462
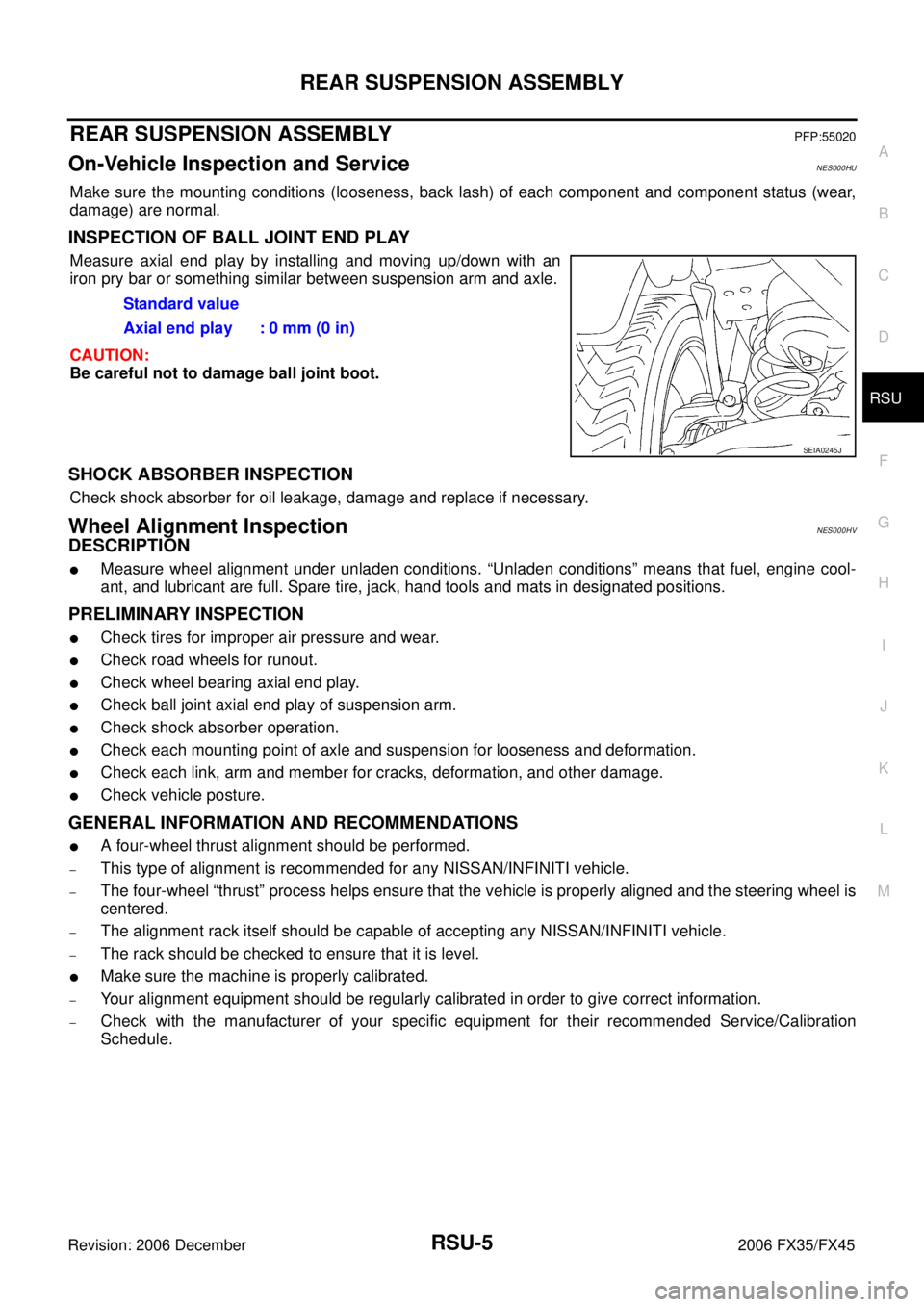
REAR SUSPENSION ASSEMBLY RSU-5
C
D
F
G H
I
J
K L
M A
B
RSU
Revision: 2006 December 2006 FX35/FX45
REAR SUSPENSION ASSEMBLYPFP:55020
On-Vehicle Inspection and ServiceNES000HU
Make sure the mounting conditions (looseness, back lash) of each component and component status (wear,
damage) are normal.
INSPECTION OF BALL JOINT END PLAY
Measure axial end play by installing and moving up/down with an
iron pry bar or something similar between suspension arm and axle.
CAUTION:
Be careful not to damage ball joint boot.
SHOCK ABSORBER INSPECTION
Check shock absorber for oil leakage, damage and replace if necessary.
Wheel Alignment InspectionNES000HV
DESCRIPTION
Measure wheel alignment under unladen conditions. “Unladen conditions” means that fuel, engine cool-
ant, and lubricant are full. Spare tire, jack, hand tools and mats in designated positions.
PRELIMINARY INSPECTION
Check tires for improper air pressure and wear.
Check road wheels for runout.
Check wheel bearing axial end play.
Check ball joint axial end play of suspension arm.
Check shock absorber operation.
Check each mounting point of axle and suspension for looseness and deformation.
Check each link, arm and member for cracks, deformation, and other damage.
Check vehicle posture.
GENERAL INFORMATION AND RECOMMENDATIONS
A four-wheel thrust alignment should be performed.
–This type of alignment is recommended for any NISSAN/INFINITI vehicle.
–The four-wheel “thrust” process helps ensure that the vehicle is properly aligned and the steering wheel is
centered.
–The alignment rack itself should be capable of accepting any NISSAN/INFINITI vehicle.
–The rack should be checked to ensure that it is level.
Make sure the machine is properly calibrated.
–Your alignment equipment should be regularly calibrated in order to give correct information.
–Check with the manufacturer of your specific equipment for their recommended Service/Calibration
Schedule. Standard value
Axial end play : 0 mm (0 in)
SEIA0245J
Page 4082 of 4462
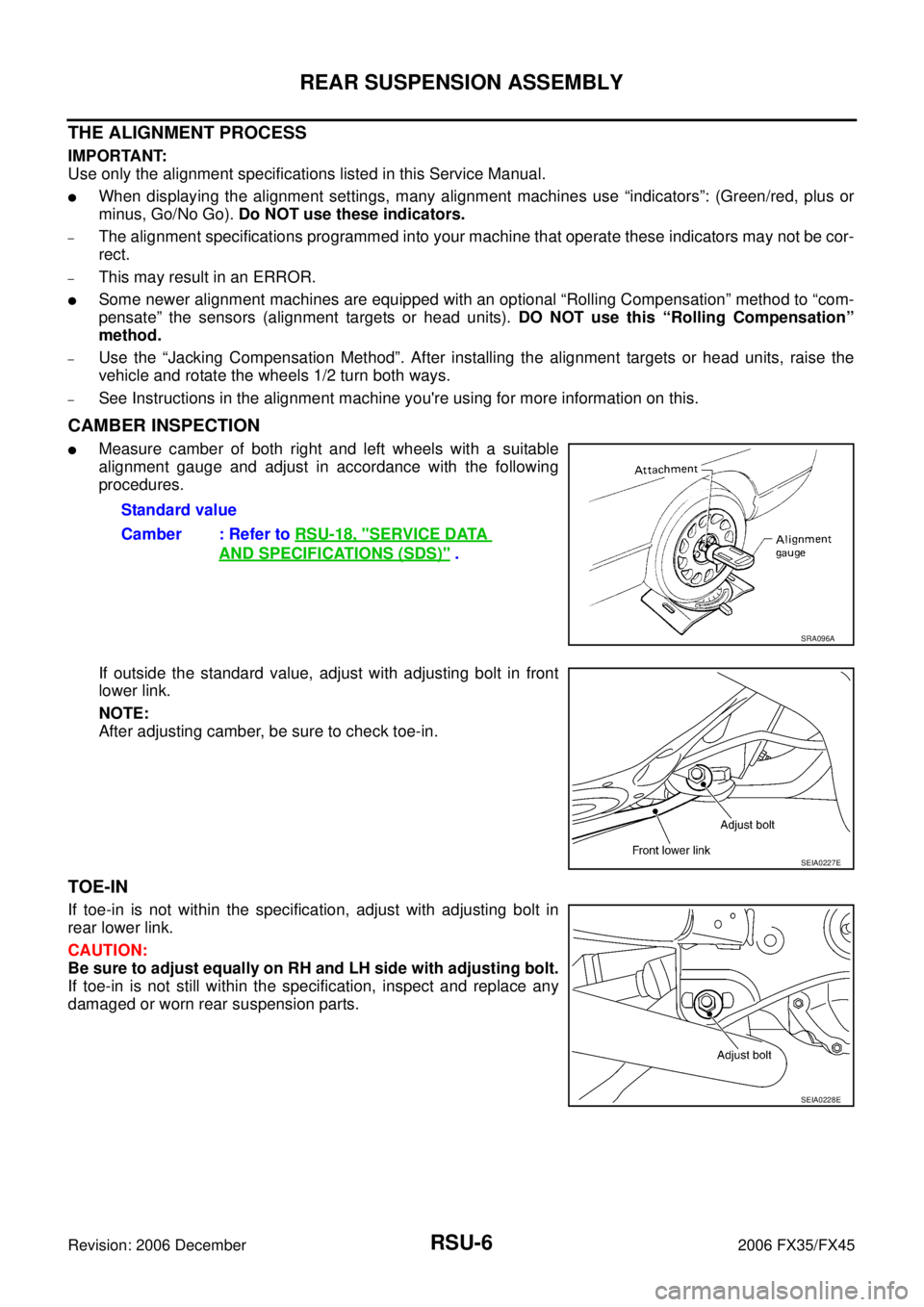
RSU-6
REAR SUSPENSION ASSEMBLY
Revision: 2006 December 2006 FX35/FX45
THE ALIGNMENT PROCESS
IMPORTANT:
Use only the alignment specifications listed in this Service Manual.
When displaying the alignment settings, many alignment machines use “indicators”: (Green/red, plus or
minus, Go/No Go). Do NOT use these indicators.
–The alignment specifications programmed into your machine that operate these indicators may not be cor-
rect.
–This may result in an ERROR.
Some newer alignment machines are equipped with an optional “Rolling Compensation” method to “com-
pensate” the sensors (alignment targets or head units). DO NOT use this “Rolling Compensation”
method.
–Use the “Jacking Compensation Method”. After installing the alignment targets or head units, raise the
vehicle and rotate the wheels 1/2 turn both ways.
–See Instructions in the alignment machine you're using for more information on this.
CAMBER INSPECTION
Measure camber of both right and left wheels with a suitable
alignment gauge and adjust in accordance with the following
procedures.
If outside the standard value, adjust with adjusting bolt in front
lower link.
NOTE:
After adjusting camber, be sure to check toe-in.
TOE-IN
If toe-in is not within the specification, adjust with adjusting bolt in
rear lower link.
CAUTION:
Be sure to adjust equally on RH and LH side with adjusting bolt.
If toe-in is not still within the specification, inspect and replace any
damaged or worn rear suspension parts. Standard value
Camber : Refer to RSU-18, "
SERVICE DATA
AND SPECIFICATIONS (SDS)" .
SRA096A
SEIA0227E
SEIA0228E
Page 4083 of 4462
REAR SUSPENSION ASSEMBLY RSU-7
C
D
F
G H
I
J
K L
M A
B
RSU
Revision: 2006 December 2006 FX35/FX45
Removal and installationNES000HY
COMPONENTS
PEIA0054E
Page 4084 of 4462
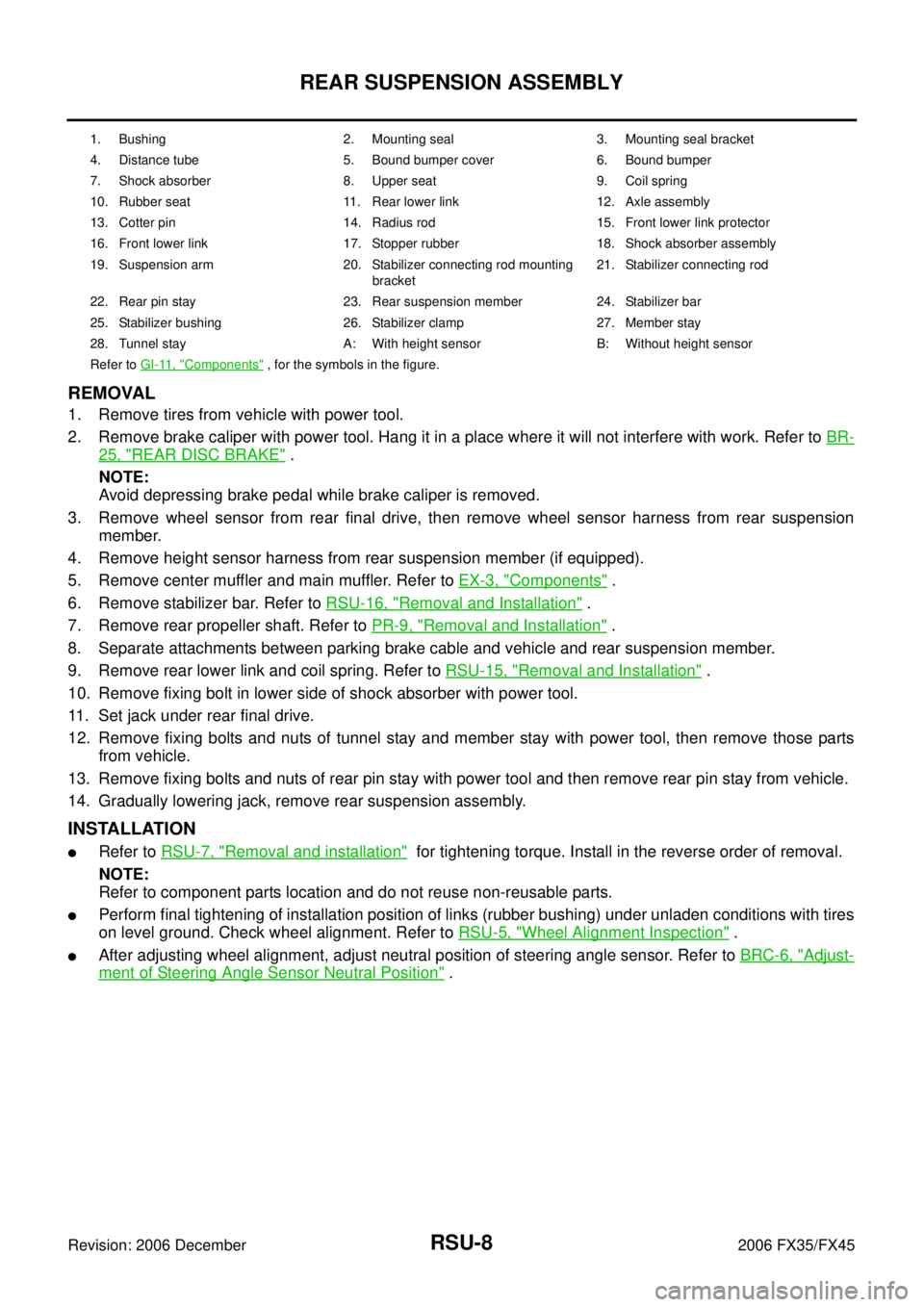
RSU-8
REAR SUSPENSION ASSEMBLY
Revision: 2006 December 2006 FX35/FX45
REMOVAL
1. Remove tires from vehicle with power tool.
2. Remove brake caliper with power tool. Hang it in a place where it will not interfere with work. Refer to BR-
25, "REAR DISC BRAKE" .
NOTE:
Avoid depressing brake pedal while brake caliper is removed.
3. Remove wheel sensor from rear final drive, then remove wheel sensor harness from rear suspension member.
4. Remove height sensor harness from rear suspension member (if equipped).
5. Remove center muffler and main muffler. Refer to EX-3, "
Components" .
6. Remove stabilizer bar. Refer to RSU-16, "
Removal and Installation" .
7. Remove rear propeller shaft. Refer to PR-9, "
Removal and Installation" .
8. Separate attachments between parking brake cable and vehicle and rear suspension member.
9. Remove rear lower link and coil spring. Refer to RSU-15, "
Removal and Installation" .
10. Remove fixing bolt in lower side of shock absorber with power tool.
11. Set jack under rear final drive.
12. Remove fixing bolts and nuts of tunnel stay and member stay with power tool, then remove those parts from vehicle.
13. Remove fixing bolts and nuts of rear pin stay with power tool and then remove rear pin stay from vehicle.
14. Gradually lowering jack, remove rear suspension assembly.
INSTALLATION
Refer to RSU-7, "Removal and installation" for tightening torque. Install in the reverse order of removal.
NOTE:
Refer to component parts location and do not reuse non-reusable parts.
Perform final tightening of installation position of links (rubber bushing) under unladen conditions with tires
on level ground. Check wheel alignment. Refer to RSU-5, "
Wheel Alignment Inspection" .
After adjusting wheel alignment, adjust neutral position of steering angle sensor. Refer to BRC-6, "Adjust-
ment of Steering Angle Sensor Neutral Position" .
1. Bushing 2. Mounting seal 3. Mounting seal bracket
4. Distance tube 5. Bound bumper cover 6. Bound bumper
7. Shock absorber 8. Upper seat 9. Coil spring
10. Rubber seat 11. Rear lower link 12. Axle assembly
13. Cotter pin 14. Radius rod 15. Front lower link protector
16. Front lower link 17. Stopper rubber 18. Shock absorber assembly
19. Suspension arm 20. Stabilizer connecting rod mounting bracket 21. Stabilizer connecting rod
22. Rear pin stay 23. Rear suspension member 24. Stabilizer bar
25. Stabilizer bushing 26. Stabilizer clamp 27. Member stay
28. Tunnel stay A: With height sensor B: Without height sensor
Refer to GI-11, "
Components" , for the symbols in the figure.
Page 4085 of 4462
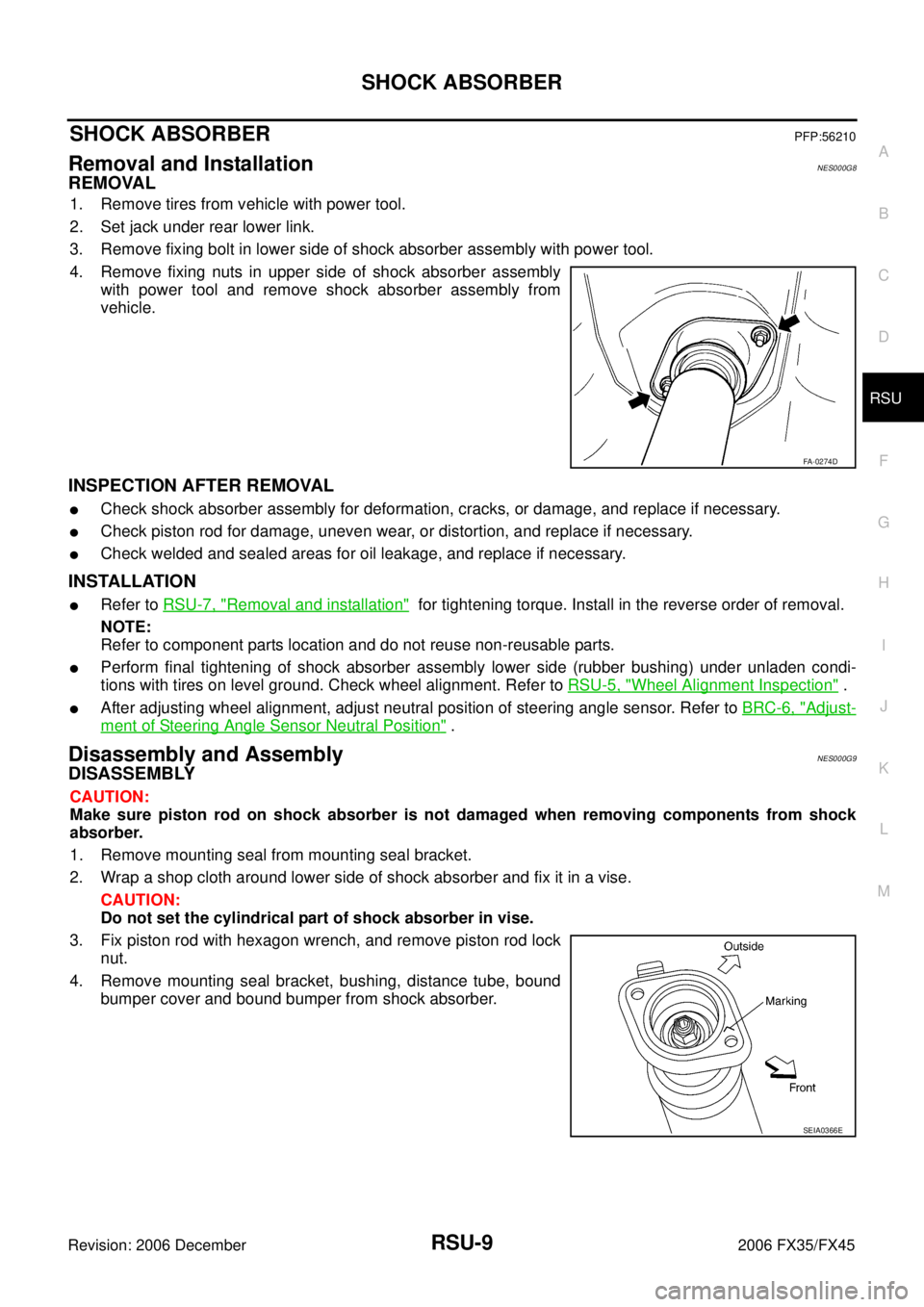
SHOCK ABSORBER RSU-9
C
D
F
G H
I
J
K L
M A
B
RSU
Revision: 2006 December 2006 FX35/FX45
SHOCK ABSORBERPFP:56210
Removal and InstallationNES000G8
REMOVAL
1. Remove tires from vehicle with power tool.
2. Set jack under rear lower link.
3. Remove fixing bolt in lower side of shock absorber assembly with power tool.
4. Remove fixing nuts in upper side of shock absorber assembly with power tool and remove shock absorber assembly from
vehicle.
INSPECTION AFTER REMOVAL
Check shock absorber assembly for deformation, cracks, or damage, and replace if necessary.
Check piston rod for damage, uneven wear, or distortion, and replace if necessary.
Check welded and sealed areas for oil leakage, and replace if necessary.
INSTALLATION
Refer to RSU-7, "Removal and installation" for tightening torque. Install in the reverse order of removal.
NOTE:
Refer to component parts location and do not reuse non-reusable parts.
Perform final tightening of shock absorber assembly lower side (rubber bushing) under unladen condi-
tions with tires on level ground. Check wheel alignment. Refer to RSU-5, "
Wheel Alignment Inspection" .
After adjusting wheel alignment, adjust neutral position of steering angle sensor. Refer to BRC-6, "Adjust-
ment of Steering Angle Sensor Neutral Position" .
Disassembly and AssemblyNES000G9
DISASSEMBLY
CAUTION:
Make sure piston rod on shock absorber is not damaged when removing components from shock
absorber.
1. Remove mounting seal from mounting seal bracket.
2. Wrap a shop cloth around lower side of shock absorber and fix it in a vise.
CAUTION:
Do not set the cylindrical part of shock absorber in vise.
3. Fix piston rod with hexagon wrench, and remove piston rod lock nut.
4. Remove mounting seal bracket, bushing, distance tube, bound bumper cover and bound bumper from shock absorber.
FA-0274D
SEIA0366E
Page 4086 of 4462
RSU-10
SHOCK ABSORBER
Revision: 2006 December 2006 FX35/FX45
INSPECTION AFTER DISASSEMBLY
Bound Bumper and Bushing
Check bound bumper and bushing for cracks, deformation or other damage. Replace if necessary.
ASSEMBLY
Refer to RSU-7, "Removal and installation" for tightening torque. Assembly in the reverse order of disas-
sembly.
NOTE:
Refer to component parts location and do not reuse non-reusable parts.
Make sure piston rod on shock absorber is not damaged when attaching components to shock
absorber.
Page 4087 of 4462
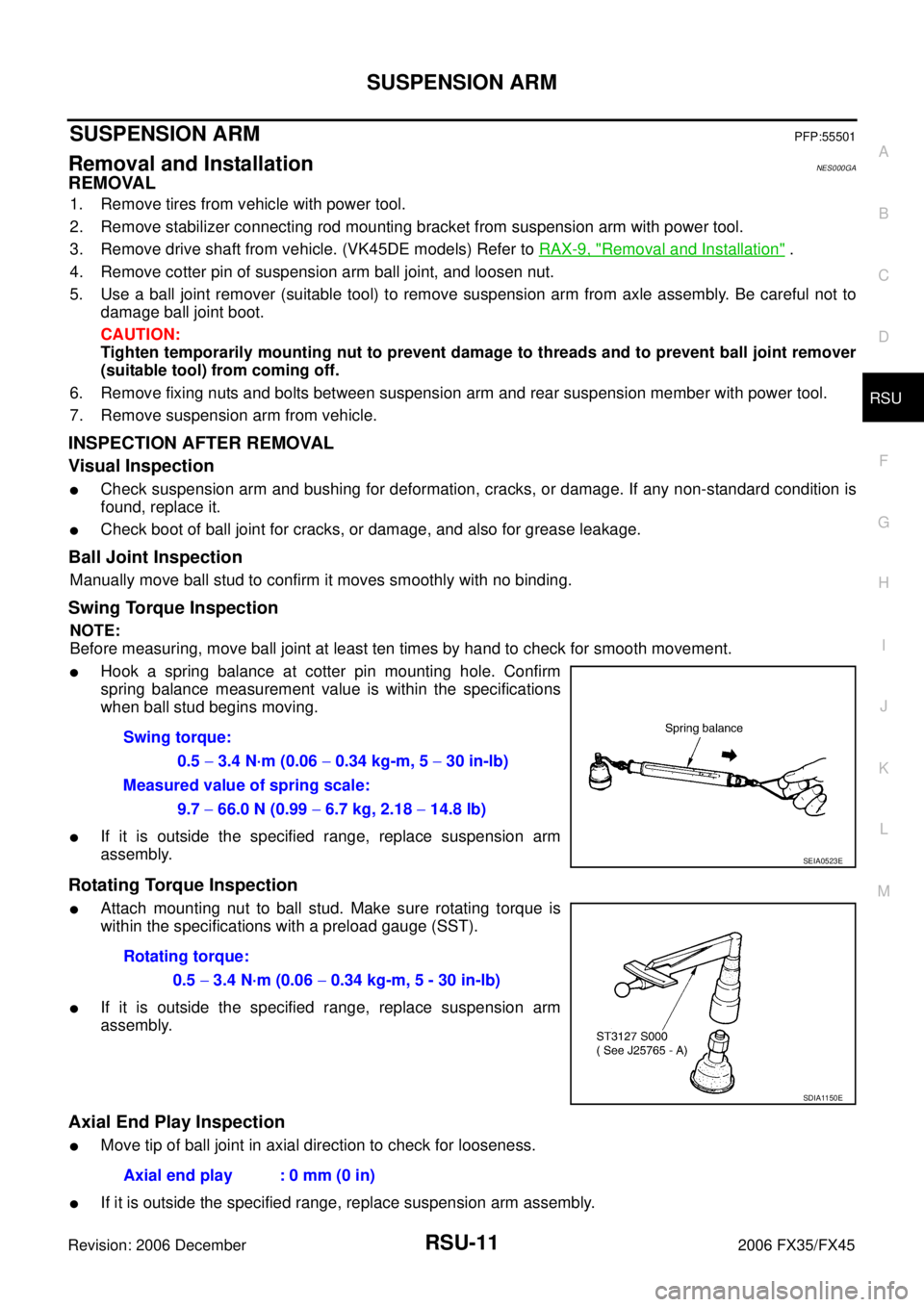
SUSPENSION ARM RSU-11
C
D
F
G H
I
J
K L
M A
B
RSU
Revision: 2006 December 2006 FX35/FX45
SUSPENSION ARMPFP:55501
Removal and InstallationNES000GA
REMOVAL
1. Remove tires from vehicle with power tool.
2. Remove stabilizer connecting rod mounting bracket from suspension arm with power tool.
3. Remove drive shaft from vehicle. (VK45DE models) Refer to RAX-9, "
Removal and Installation" .
4. Remove cotter pin of suspension arm ball joint, and loosen nut.
5. Use a ball joint remover (suitable tool) to remove suspension arm from axle assembly. Be careful not to damage ball joint boot.
CAUTION:
Tighten temporarily mounting nut to prevent damage to threads and to prevent ball joint remover
(suitable tool) from coming off.
6. Remove fixing nuts and bolts between suspension arm and rear suspension member with power tool.
7. Remove suspension arm from vehicle.
INSPECTION AFTER REMOVAL
Visual Inspection
Check suspension arm and bushing for deformation, cracks, or damage. If any non-standard condition is
found, replace it.
Check boot of ball joint for cracks, or damage, and also for grease leakage.
Ball Joint Inspection
Manually move ball stud to confirm it moves smoothly with no binding.
Swing Torque Inspection
NOTE:
Before measuring, move ball joint at least ten times by hand to check for smooth movement.
Hook a spring balance at cotter pin mounting hole. Confirm
spring balance measurement value is within the specifications
when ball stud begins moving.
If it is outside the specified range, replace suspension arm
assembly.
Rotating Torque Inspection
Attach mounting nut to ball stud. Make sure rotating torque is
within the specifications with a preload gauge (SST).
If it is outside the specified range, replace suspension arm
assembly.
Axial End Play Inspection
Move tip of ball joint in axial direction to check for looseness.
If it is outside the specified range, replace suspension arm assembly. Swing torque:
0.5 − 3.4 N·m (0.06 − 0.34 kg-m, 5 − 30 in-lb)
Measured value of spring scale:
9.7 − 66.0 N (0.99 − 6.7 kg, 2.18 − 14.8 lb)
SEIA0523E
Rotating torque:
0.5 − 3.4 N·m (0.06 − 0.34 kg-m, 5 - 30 in-lb)
SDIA1150E
Axial end play : 0 mm (0 in)
Page 4088 of 4462
RSU-12
SUSPENSION ARM
Revision: 2006 December 2006 FX35/FX45
INSTALLATION
Refer to RSU-7, "Removal and installation" for tightening torque. Install in the reverse order of removal.
NOTE:
Refer to component parts location and do not reuse non-reusable parts.
Perform final tightening of rear suspension member installation position (rubber bushing) under unladen
conditions with tires on level ground. Check wheel alignment. Refer to RSU-5, "
Wheel Alignment Inspec-
tion" .
After adjusting wheel alignment, adjust neutral position of steering angle sensor. Refer to BRC-6, "Adjust-
ment of Steering Angle Sensor Neutral Position" .