Page 2649 of 3419
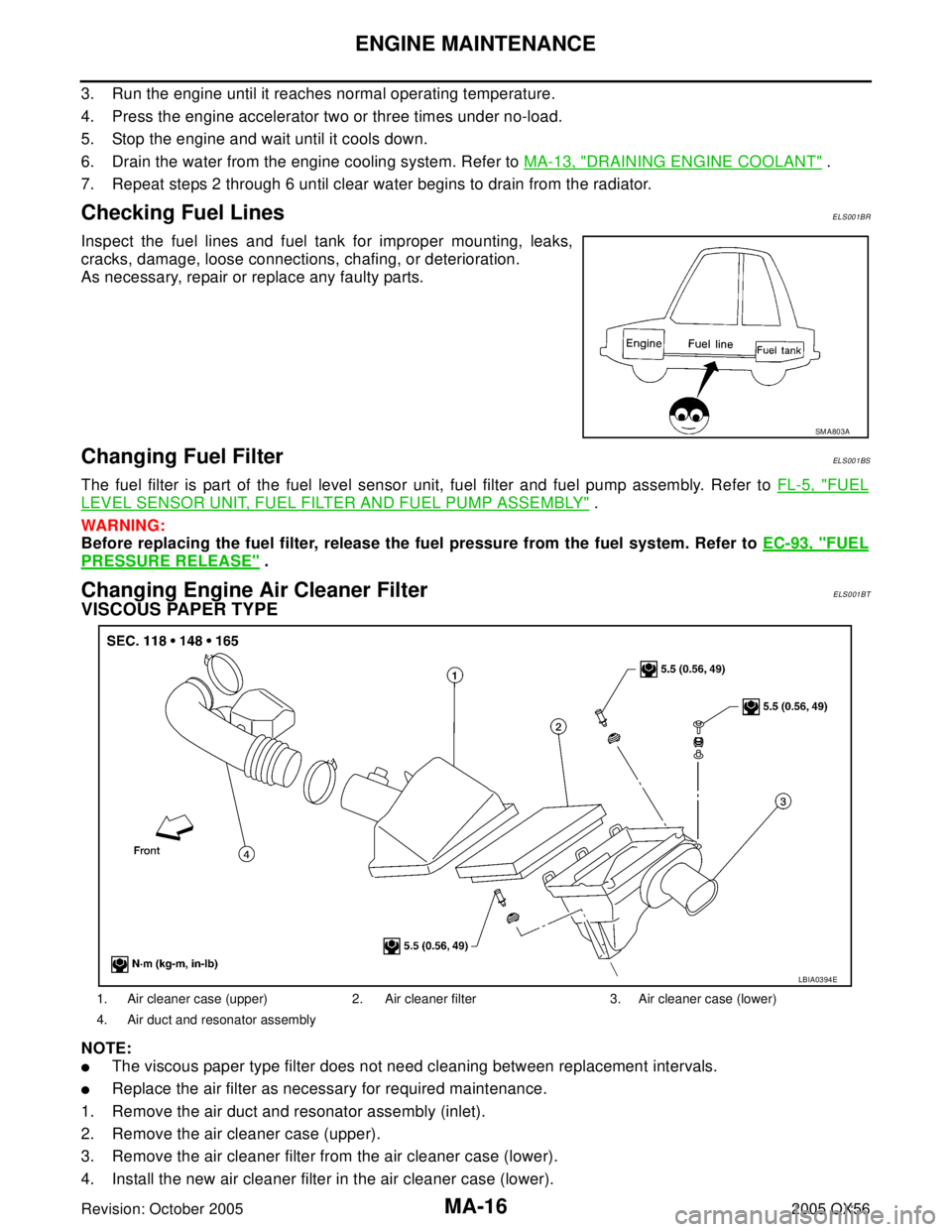
MA-16
ENGINE MAINTENANCE
Revision: October 20052005 QX56
3. Run the engine until it reaches normal operating temperature.
4. Press the engine accelerator two or three times under no-load.
5. Stop the engine and wait until it cools down.
6. Drain the water from the engine cooling system. Refer to MA-13, "
DRAINING ENGINE COOLANT" .
7. Repeat steps 2 through 6 until clear water begins to drain from the radiator.
Checking Fuel LinesELS001BR
Inspect the fuel lines and fuel tank for improper mounting, leaks,
cracks, damage, loose connections, chafing, or deterioration.
As necessary, repair or replace any faulty parts.
Changing Fuel FilterELS001BS
The fuel filter is part of the fuel level sensor unit, fuel filter and fuel pump assembly. Refer to FL-5, "FUEL
LEVEL SENSOR UNIT, FUEL FILTER AND FUEL PUMP ASSEMBLY" .
WAR NIN G:
Before replacing the fuel filter, release the fuel pressure from the fuel system. Refer to EC-93, "
FUEL
PRESSURE RELEASE" .
Changing Engine Air Cleaner FilterELS001BT
VISCOUS PAPER TYPE
NOTE:
The viscous paper type filter does not need cleaning between replacement intervals.
Replace the air filter as necessary for required maintenance.
1. Remove the air duct and resonator assembly (inlet).
2. Remove the air cleaner case (upper).
3. Remove the air cleaner filter from the air cleaner case (lower).
4. Install the new air cleaner filter in the air cleaner case (lower).
SM A80 3A
1. Air cleaner case (upper) 2. Air cleaner filter 3. Air cleaner case (lower)
4. Air duct and resonator assembly
LBIA0394E
Page 2650 of 3419
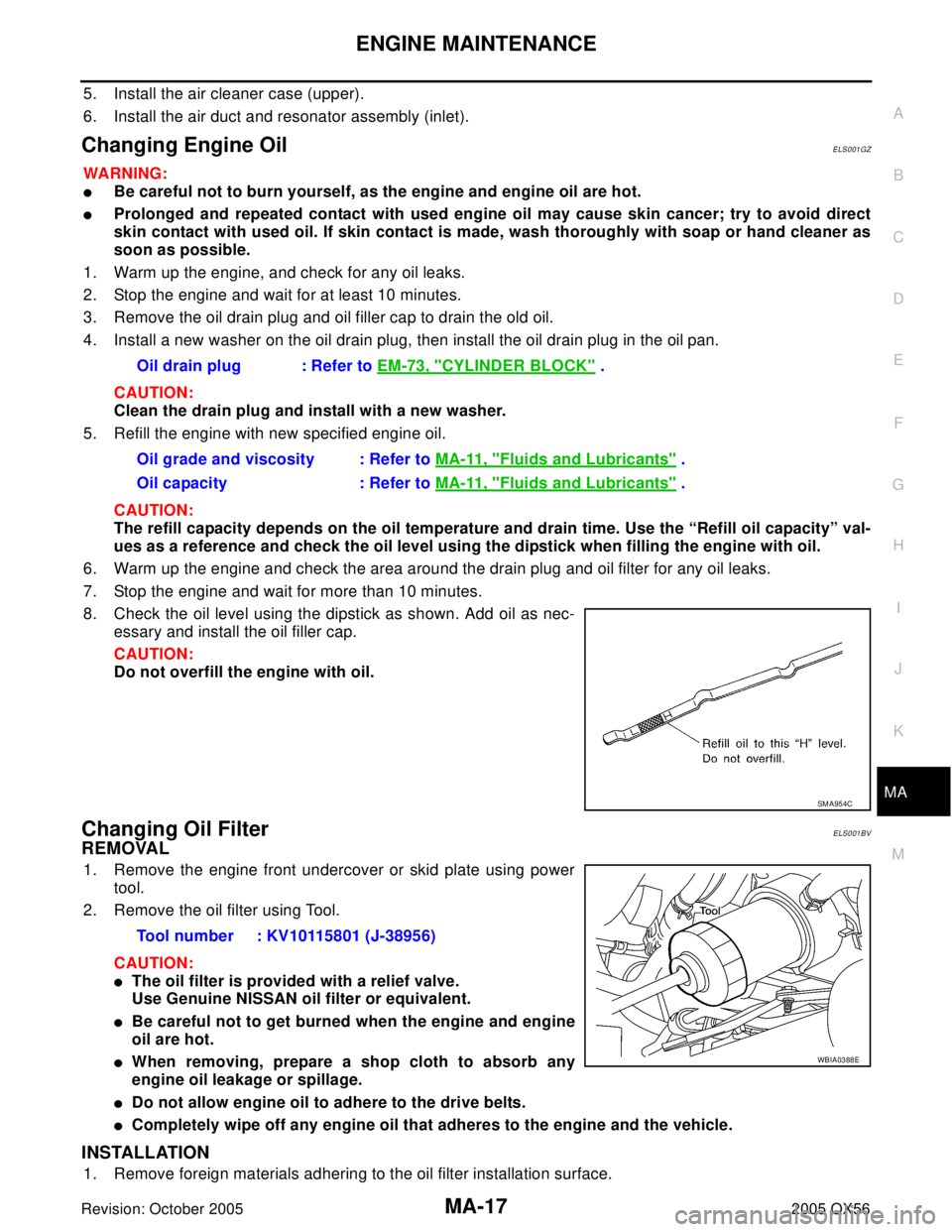
ENGINE MAINTENANCE
MA-17
C
D
E
F
G
H
I
J
K
MA
B
MA
Revision: October 20052005 QX56
5. Install the air cleaner case (upper).
6. Install the air duct and resonator assembly (inlet).
Changing Engine OilELS001GZ
WA RN ING:
Be careful not to burn yourself, as the engine and engine oil are hot.
Prolonged and repeated contact with used engine oil may cause skin cancer; try to avoid direct
skin contact with used oil. If skin contact is made, wash thoroughly with soap or hand cleaner as
soon as possible.
1. Warm up the engine, and check for any oil leaks.
2. Stop the engine and wait for at least 10 minutes.
3. Remove the oil drain plug and oil filler cap to drain the old oil.
4. Install a new washer on the oil drain plug, then install the oil drain plug in the oil pan.
CAUTION:
Clean the drain plug and install with a new washer.
5. Refill the engine with new specified engine oil.
CAUTION:
The refill capacity depends on the oil temperature and drain time. Use the “Refill oil capacity” val-
ues as a reference and check the oil level using the dipstick when filling the engine with oil.
6. Warm up the engine and check the area around the drain plug and oil filter for any oil leaks.
7. Stop the engine and wait for more than 10 minutes.
8. Check the oil level using the dipstick as shown. Add oil as nec-
essary and install the oil filler cap.
CAUTION:
Do not overfill the engine with oil.
Changing Oil FilterELS001BV
REMOVAL
1. Remove the engine front undercover or skid plate using power
tool.
2. Remove the oil filter using Tool.
CAUTION:
The oil filter is provided with a relief valve.
Use Genuine NISSAN oil filter or equivalent.
Be careful not to get burned when the engine and engine
oil are hot.
When removing, prepare a shop cloth to absorb any
engine oil leakage or spillage.
Do not allow engine oil to adhere to the drive belts.
Completely wipe off any engine oil that adheres to the engine and the vehicle.
INSTALLATION
1. Remove foreign materials adhering to the oil filter installation surface.Oil drain plug : Refer to EM-73, "
CYLINDER BLOCK" .
Oil grade and viscosity : Refer to MA-11, "
Fluids and Lubricants" .
Oil capacity : Refer to MA-11, "
Fluids and Lubricants" .
SM A95 4C
Tool number : KV10115801 (J-38956)
WBIA0388E
Page 2651 of 3419
MA-18
ENGINE MAINTENANCE
Revision: October 20052005 QX56
2. Apply engine oil to the oil seal circumference of the new oil filter.
3. Screw the oil filter manually until it touches the installation sur-
face, then tighten it by 2/3 turn. Or tighten to specification.
4. Inspect the engine for oil leakage.
5. Install the engine front undercover using power tool.
INSPECTION AFTER INSTALLATION
1. Check the engine oil level.
2. Start the engine and check for engine oil leakage.
3. Stop engine and wait for 10 minutes.
4. Check the engine oil level and add engine oil as required.
Changing Spark PlugsELS001BW
SM A01 0
Oil filter : 17.7 N·m (1.8 kg-m, 13 ft-lb)
SM A22 9B
SM A95 4C
1. Ignition coil 2. Spark plug
KBIA2505E
Page 2652 of 3419
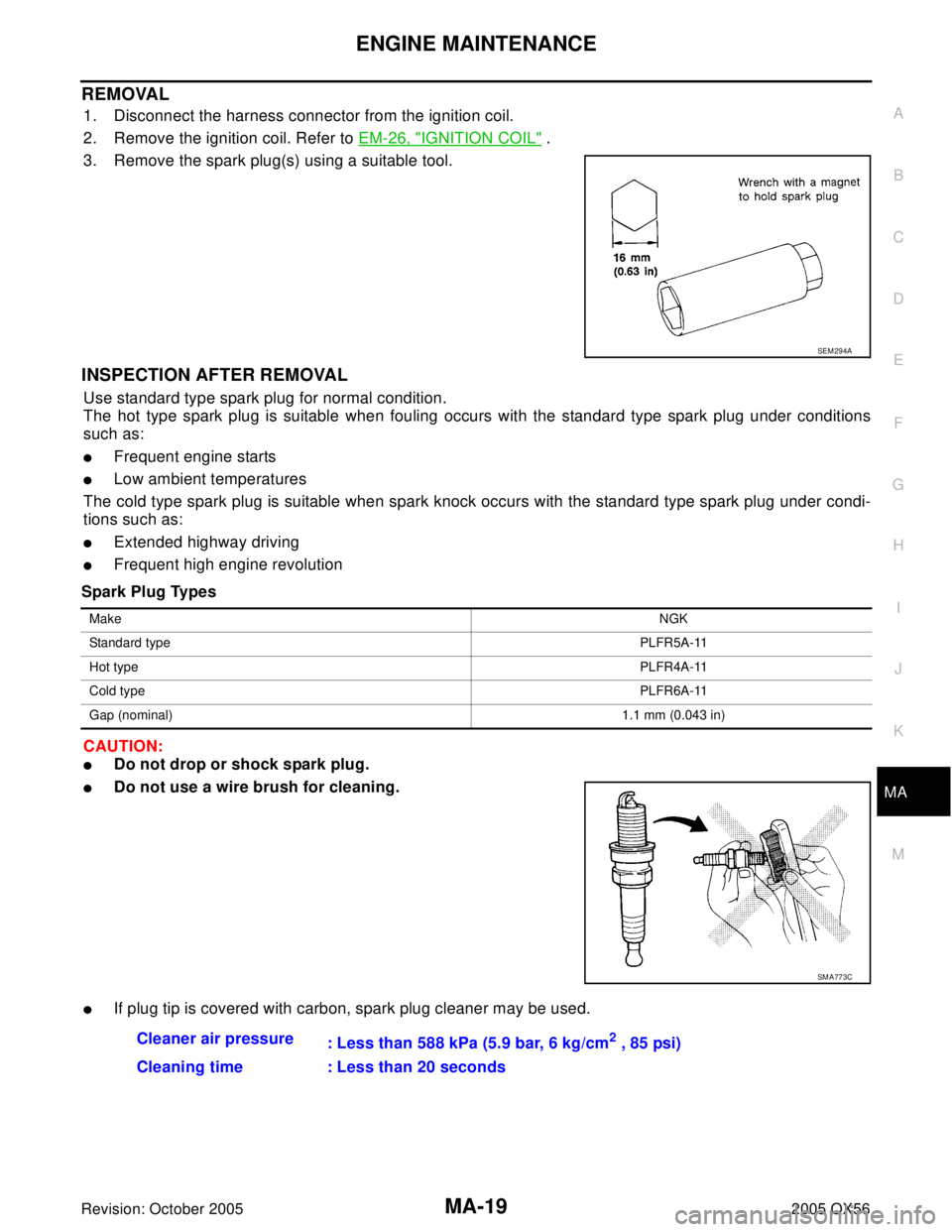
ENGINE MAINTENANCE
MA-19
C
D
E
F
G
H
I
J
K
MA
B
MA
Revision: October 20052005 QX56
REMOVAL
1. Disconnect the harness connector from the ignition coil.
2. Remove the ignition coil. Refer to EM-26, "
IGNITION COIL" .
3. Remove the spark plug(s) using a suitable tool.
INSPECTION AFTER REMOVAL
Use standard type spark plug for normal condition.
The hot type spark plug is suitable when fouling occurs with the standard type spark plug under conditions
such as:
Frequent engine starts
Low ambient temperatures
The cold type spark plug is suitable when spark knock occurs with the standard type spark plug under condi-
tions such as:
Extended highway driving
Frequent high engine revolution
Spark Plug Types
CAUTION:
Do not drop or shock spark plug.
Do not use a wire brush for cleaning.
If plug tip is covered with carbon, spark plug cleaner may be used.
SEM 29 4A
MakeNGK
Standard typePLFR5A-11
Hot typePLFR4A-11
Cold typePLFR6A-11
Gap (nominal)1.1 mm (0.043 in)
SM A77 3C
Cleaner air pressure
: Less than 588 kPa (5.9 bar, 6 kg/cm2 , 85 psi)
Cleaning time : Less than 20 seconds
Page 2653 of 3419
MA-20
ENGINE MAINTENANCE
Revision: October 20052005 QX56
Checking and adjusting plug gap is not required between
change intervals.
INSTALLATION
Installation is in the reverse order of removal.
Checking EVAP Vapor LinesELS001BX
1. Visually inspect the EVAP vapor lines for improper attachment, cracks, damage, loose connections, chaf-
ing, or deterioration.
2. Inspect the vacuum relief valve of the fuel tank filler cap for clogging and sticking. Refer to EC-37, "
How to
Detect Fuel Vapor Leakage" .
SM A80 6CA
Page 2654 of 3419
CHASSIS AND BODY MAINTENANCE
MA-21
C
D
E
F
G
H
I
J
K
MA
B
MA
Revision: October 20052005 QX56
CHASSIS AND BODY MAINTENANCEPFP:00100
Changing In-cabin MicrofilterELS001UY
1. Remove the two lower glove box hinge pins to remove the glove
box from the instrument panel and let it hang from the cord.
2. Remove the screw and remove the in-cabin microfilter cover.
3. Remove the in-cabin microfilters from the front heater and cool-
ing unit assembly housing.
4. Insert the first new in-cabin microfilter into the front heater and
cooling unit assembly housing and slide it over to the right.
Insert the second new in-cabin microfilter into the front heater
and cooling unit assembly housing.
NOTE:
The in-cabin microfilters are marked with air flow arrows. The
end of the microfilter with the arrow should face the rear of the
vehicle. The arrows should point downward.
5. Install the in-cabin microfilter cover.
WLIA0027E
LJIA0134E
LJIA0148E
LJIA0134E
Page 2655 of 3419
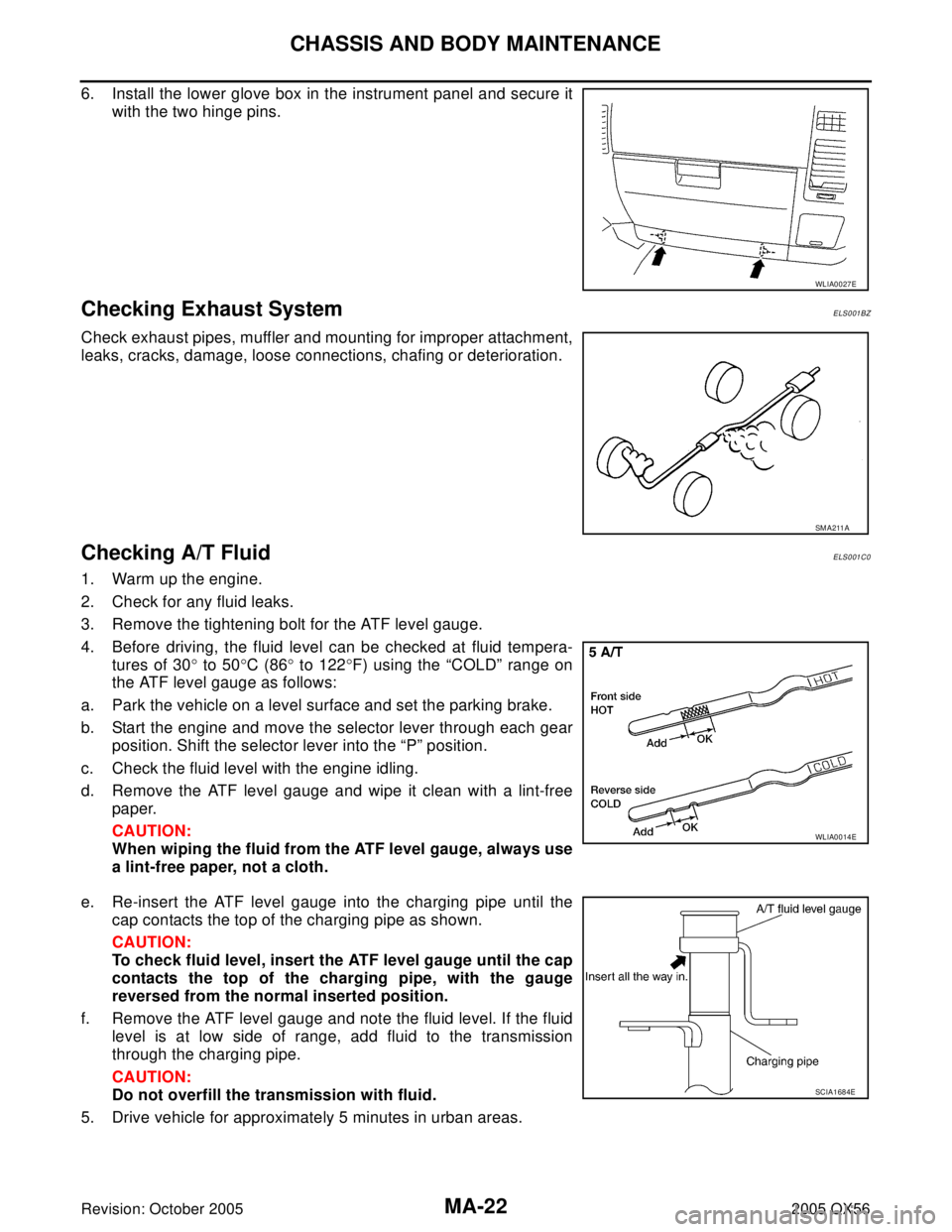
MA-22
CHASSIS AND BODY MAINTENANCE
Revision: October 20052005 QX56
6. Install the lower glove box in the instrument panel and secure it
with the two hinge pins.
Checking Exhaust SystemELS001BZ
Check exhaust pipes, muffler and mounting for improper attachment,
leaks, cracks, damage, loose connections, chafing or deterioration.
Checking A/T FluidELS001C0
1. Warm up the engine.
2. Check for any fluid leaks.
3. Remove the tightening bolt for the ATF level gauge.
4. Before driving, the fluid level can be checked at fluid tempera-
tures of 30° to 50°C (86° to 122°F) using the “COLD” range on
the ATF level gauge as follows:
a. Park the vehicle on a level surface and set the parking brake.
b. Start the engine and move the selector lever through each gear
position. Shift the selector lever into the “P” position.
c. Check the fluid level with the engine idling.
d. Remove the ATF level gauge and wipe it clean with a lint-free
paper.
CAUTION:
When wiping the fluid from the ATF level gauge, always use
a lint-free paper, not a cloth.
e. Re-insert the ATF level gauge into the charging pipe until the
cap contacts the top of the charging pipe as shown.
CAUTION:
To check fluid level, insert the ATF level gauge until the cap
contacts the top of the charging pipe, with the gauge
reversed from the normal inserted position.
f. Remove the ATF level gauge and note the fluid level. If the fluid
level is at low side of range, add fluid to the transmission
through the charging pipe.
CAUTION:
Do not overfill the transmission with fluid.
5. Drive vehicle for approximately 5 minutes in urban areas.
WLIA0027E
SM A211 A
WLIA0014E
SCIA1684E
Page 2656 of 3419
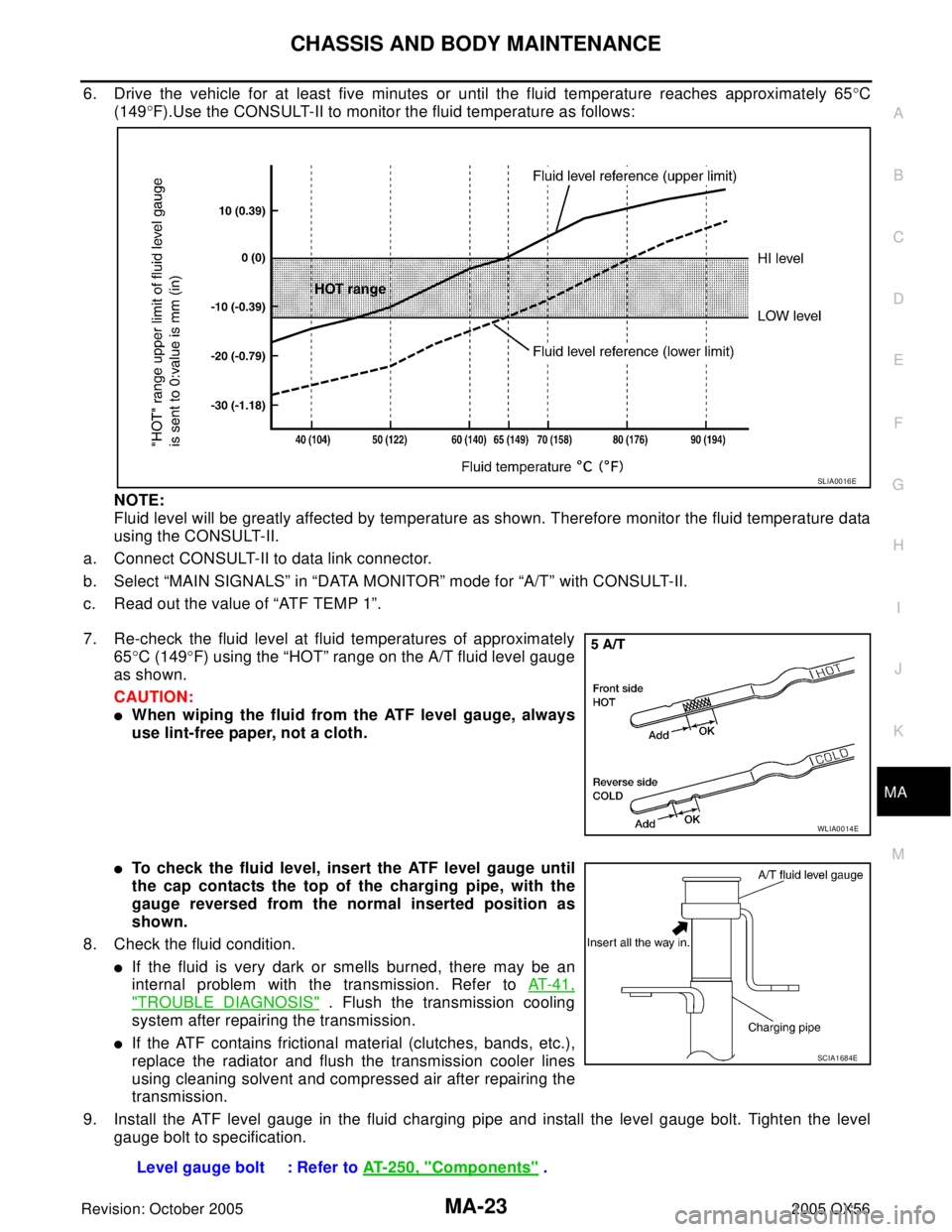
CHASSIS AND BODY MAINTENANCE
MA-23
C
D
E
F
G
H
I
J
K
MA
B
MA
Revision: October 20052005 QX56
6. Drive the vehicle for at least five minutes or until the fluid temperature reaches approximately 65°C
(149°F).Use the CONSULT-II to monitor the fluid temperature as follows:
NOTE:
Fluid level will be greatly affected by temperature as shown. Therefore monitor the fluid temperature data
using the CONSULT-II.
a. Connect CONSULT-II to data link connector.
b. Select “MAIN SIGNALS” in “DATA MONITOR” mode for “A/T” with CONSULT-II.
c. Read out the value of “ATF TEMP 1”.
7. Re-check the fluid level at fluid temperatures of approximately
65°C (149°F) using the “HOT” range on the A/T fluid level gauge
as shown.
CAUTION:
When wiping the fluid from the ATF level gauge, always
use lint-free paper, not a cloth.
To check the fluid level, insert the ATF level gauge until
the cap contacts the top of the charging pipe, with the
gauge reversed from the normal inserted position as
shown.
8. Check the fluid condition.
If the fluid is very dark or smells burned, there may be an
internal problem with the transmission. Refer to AT - 4 1 ,
"TROUBLE DIAGNOSIS" . Flush the transmission cooling
system after repairing the transmission.
If the ATF contains frictional material (clutches, bands, etc.),
replace the radiator and flush the transmission cooler lines
using cleaning solvent and compressed air after repairing the
transmission.
9. Install the ATF level gauge in the fluid charging pipe and install the level gauge bolt. Tighten the level
gauge bolt to specification.
SLIA0016E
WLIA0014E
Level gauge bolt : Refer to AT-250, "Components" .
SCIA1684E