Page 1969 of 3419
EM-66Revision: October 2005
CYLINDER HEAD
2005 QX56
2. Remove the valve guide using suitable tool.
CAUTION:
Cylinder head contains heat. When working, wear protec-
tive equipment to avoid getting burned.
3. Ream the cylinder head valve guide hole using suitable tool.
4. Heat the cylinder head to 110° to 130°C (230° to 266°F) by
soaking it in heated oil.
5. Press the valve guide from the camshaft side to the dimensions
as shown.
CAUTION:
Cylinder head contains heat. When working, wear protec-
tive equipment to avoid getting burned.
6. Ream the cylinder head valve guide hole using suitable tool.
SEM 93 1C
Valve guide hole diameter:
Standard
Intake and exhaust : 9.975 - 9.996 mm (0.3927 -
0.3935 in)
Oversize (service)
Intake and exhaust : 10.175 - 10.196 mm
(0.4006 - 0.4014 in)
SEM 93 2C
SEM 00 8A
KBIA2530E
Valve guide hole diameter:
Intake and exhaust : 6.000 - 6.018 mm
(0.2362 - 0.2369 in)
SEM 93 2C
Page 1970 of 3419
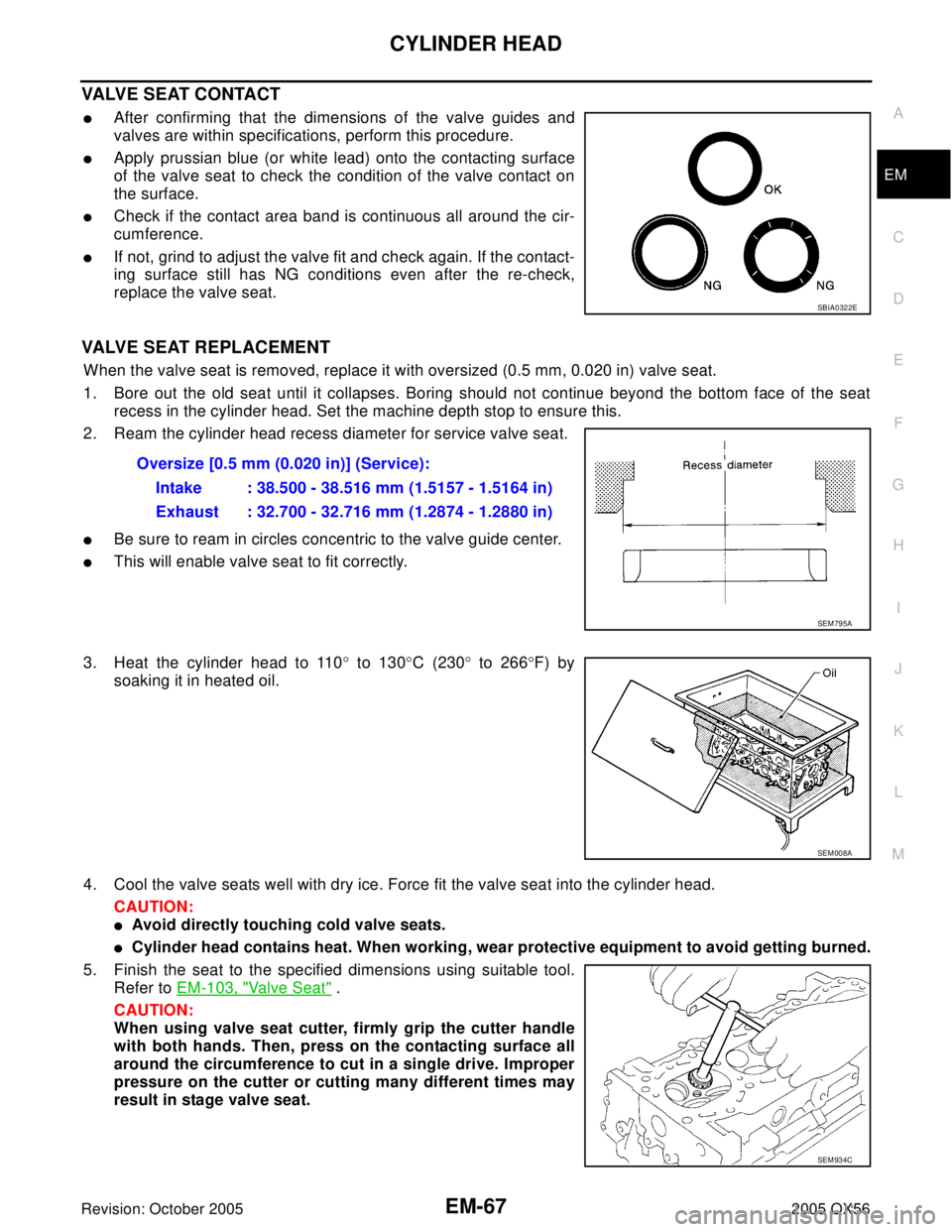
CYLINDER HEAD
EM-67
C
D
E
F
G
H
I
J
K
L
MA
EM
Revision: October 20052005 QX56
VALVE SEAT CONTACT
After confirming that the dimensions of the valve guides and
valves are within specifications, perform this procedure.
Apply prussian blue (or white lead) onto the contacting surface
of the valve seat to check the condition of the valve contact on
the surface.
Check if the contact area band is continuous all around the cir-
cumference.
If not, grind to adjust the valve fit and check again. If the contact-
ing surface still has NG conditions even after the re-check,
replace the valve seat.
VALVE SEAT REPLACEMENT
When the valve seat is removed, replace it with oversized (0.5 mm, 0.020 in) valve seat.
1. Bore out the old seat until it collapses. Boring should not continue beyond the bottom face of the seat
recess in the cylinder head. Set the machine depth stop to ensure this.
2. Ream the cylinder head recess diameter for service valve seat.
Be sure to ream in circles concentric to the valve guide center.
This will enable valve seat to fit correctly.
3. Heat the cylinder head to 110° to 130°C (230° to 266°F) by
soaking it in heated oil.
4. Cool the valve seats well with dry ice. Force fit the valve seat into the cylinder head.
CAUTION:
Avoid directly touching cold valve seats.
Cylinder head contains heat. When working, wear protective equipment to avoid getting burned.
5. Finish the seat to the specified dimensions using suitable tool.
Refer to EM-103, "
Valve Seat" .
CAUTION:
When using valve seat cutter, firmly grip the cutter handle
with both hands. Then, press on the contacting surface all
around the circumference to cut in a single drive. Improper
pressure on the cutter or cutting many different times may
result in stage valve seat.
SBIA0322E
Oversize [0.5 mm (0.020 in)] (Service):
Intake : 38.500 - 38.516 mm (1.5157 - 1.5164 in)
Exhaust : 32.700 - 32.716 mm (1.2874 - 1.2880 in)
SEM 79 5A
SEM 00 8A
SEM 93 4C
Page 1971 of 3419
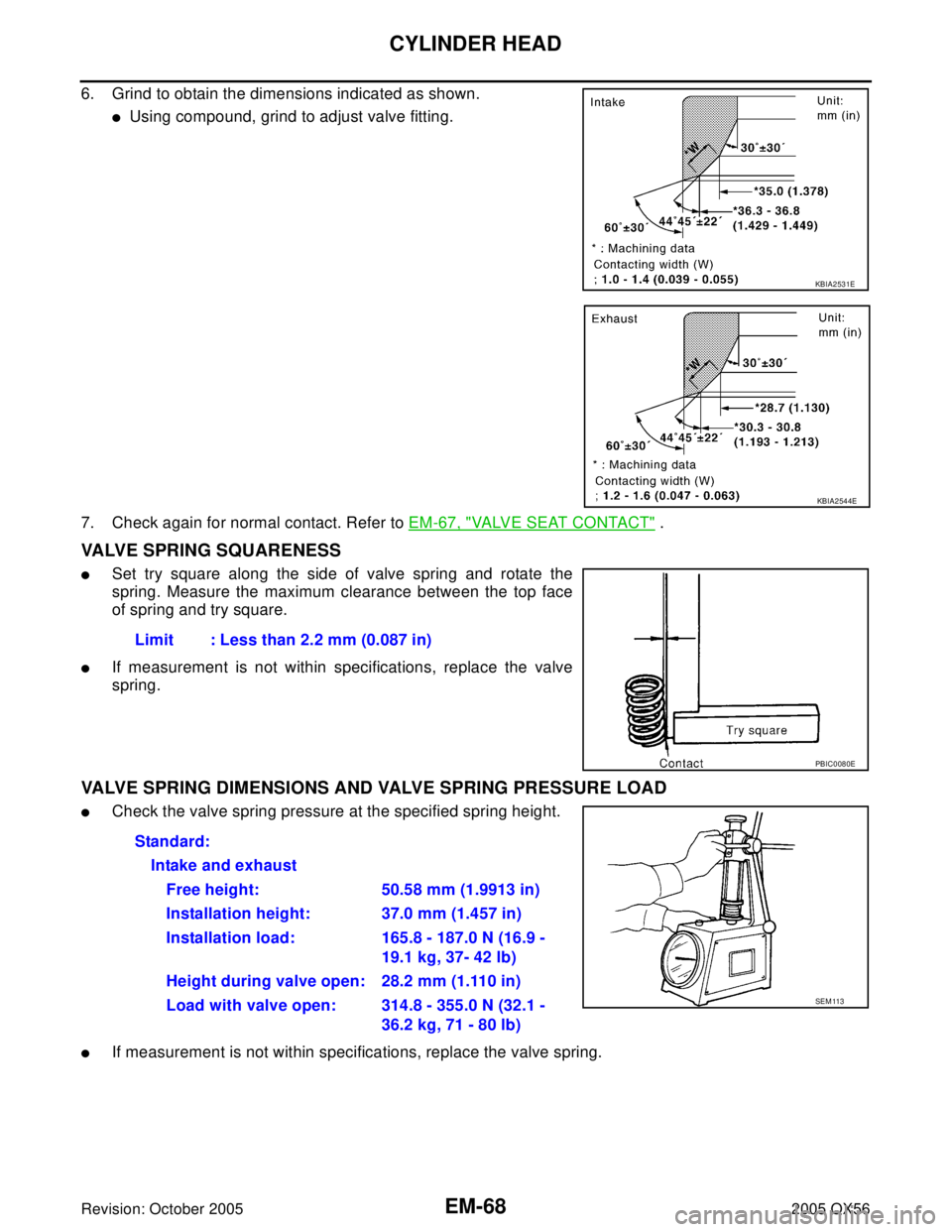
EM-68Revision: October 2005
CYLINDER HEAD
2005 QX56
6. Grind to obtain the dimensions indicated as shown.
Using compound, grind to adjust valve fitting.
7. Check again for normal contact. Refer to EM-67, "
VALVE SEAT CONTACT" .
VALVE SPRING SQUARENESS
Set try square along the side of valve spring and rotate the
spring. Measure the maximum clearance between the top face
of spring and try square.
If measurement is not within specifications, replace the valve
spring.
VALVE SPRING DIMENSIONS AND VALVE SPRING PRESSURE LOAD
Check the valve spring pressure at the specified spring height.
If measurement is not within specifications, replace the valve spring.
KBIA2531E
KBIA2544E
Limit : Less than 2.2 mm (0.087 in)
PBIC0080E
Standard:
Intake and exhaust
Free height: 50.58 mm (1.9913 in)
Installation height: 37.0 mm (1.457 in)
Installation load: 165.8 - 187.0 N (16.9 -
19.1 kg, 37- 42 lb)
Height during valve open: 28.2 mm (1.110 in)
Load with valve open: 314.8 - 355.0 N (32.1 -
36.2 kg, 71 - 80 lb)
SEM 113
Page 1972 of 3419
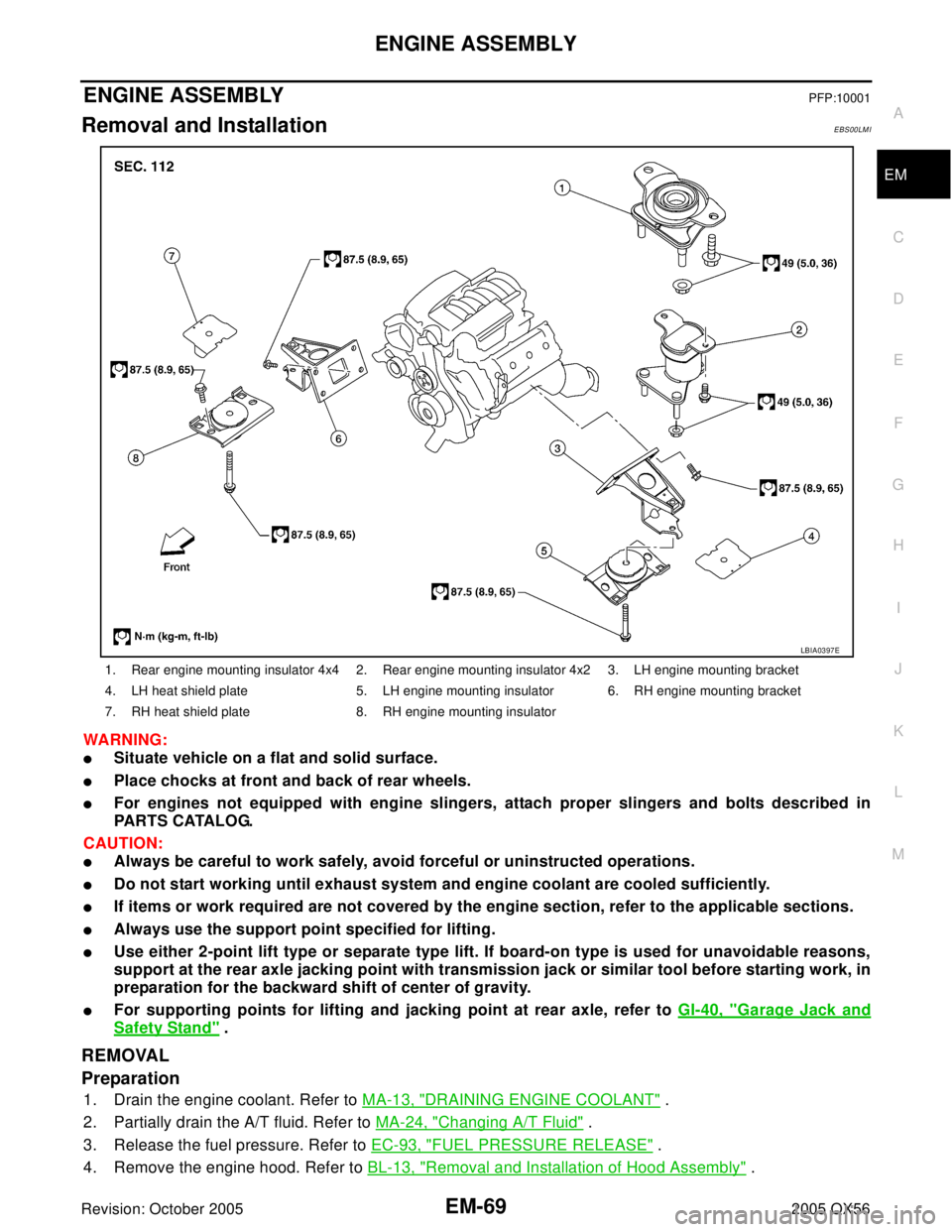
ENGINE ASSEMBLY
EM-69
C
D
E
F
G
H
I
J
K
L
MA
EM
Revision: October 20052005 QX56
ENGINE ASSEMBLYPFP:10001
Removal and InstallationEBS00LMI
WA RN ING:
Situate vehicle on a flat and solid surface.
Place chocks at front and back of rear wheels.
For engines not equipped with engine slingers, attach proper slingers and bolts described in
PA R T S C ATA L O G.
CAUTION:
Always be careful to work safely, avoid forceful or uninstructed operations.
Do not start working until exhaust system and engine coolant are cooled sufficiently.
If items or work required are not covered by the engine section, refer to the applicable sections.
Always use the support point specified for lifting.
Use either 2-point lift type or separate type lift. If board-on type is used for unavoidable reasons,
support at the rear axle jacking point with transmission jack or similar tool before starting work, in
preparation for the backward shift of center of gravity.
For supporting points for lifting and jacking point at rear axle, refer to GI-40, "Garage Jack and
Safety Stand" .
REMOVAL
Preparation
1. Drain the engine coolant. Refer to MA-13, "DRAINING ENGINE COOLANT" .
2. Partially drain the A/T fluid. Refer to MA-24, "
Changing A/T Fluid" .
3. Release the fuel pressure. Refer to EC-93, "
FUEL PRESSURE RELEASE" .
4. Remove the engine hood. Refer to BL-13, "
Removal and Installation of Hood Assembly" .
1. Rear engine mounting insulator 4x4 2. Rear engine mounting insulator 4x2 3. LH engine mounting bracket
4. LH heat shield plate 5. LH engine mounting insulator 6. RH engine mounting bracket
7. RH heat shield plate 8. RH engine mounting insulator
LBIA0397E
Page 1973 of 3419
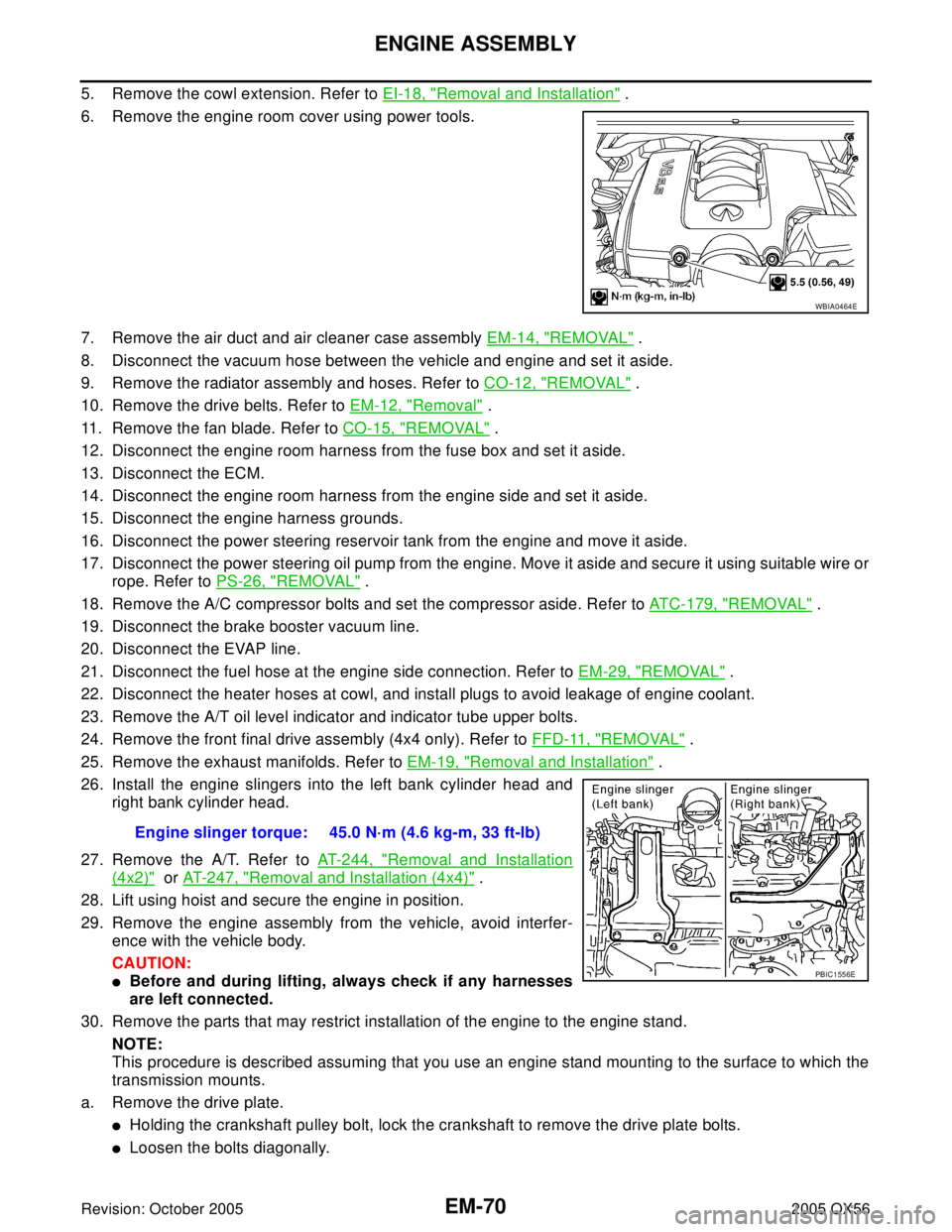
EM-70Revision: October 2005
ENGINE ASSEMBLY
2005 QX56
5. Remove the cowl extension. Refer to EI-18, "Removal and Installation" .
6. Remove the engine room cover using power tools.
7. Remove the air duct and air cleaner case assembly EM-14, "
REMOVAL" .
8. Disconnect the vacuum hose between the vehicle and engine and set it aside.
9. Remove the radiator assembly and hoses. Refer to CO-12, "
REMOVAL" .
10. Remove the drive belts. Refer to EM-12, "
Removal" .
11. Remove the fan blade. Refer to CO-15, "
REMOVAL" .
12. Disconnect the engine room harness from the fuse box and set it aside.
13. Disconnect the ECM.
14. Disconnect the engine room harness from the engine side and set it aside.
15. Disconnect the engine harness grounds.
16. Disconnect the power steering reservoir tank from the engine and move it aside.
17. Disconnect the power steering oil pump from the engine. Move it aside and secure it using suitable wire or
rope. Refer to PS-26, "
REMOVAL" .
18. Remove the A/C compressor bolts and set the compressor aside. Refer to ATC-179, "
REMOVAL" .
19. Disconnect the brake booster vacuum line.
20. Disconnect the EVAP line.
21. Disconnect the fuel hose at the engine side connection. Refer to EM-29, "
REMOVAL" .
22. Disconnect the heater hoses at cowl, and install plugs to avoid leakage of engine coolant.
23. Remove the A/T oil level indicator and indicator tube upper bolts.
24. Remove the front final drive assembly (4x4 only). Refer to FFD-11, "
REMOVAL" .
25. Remove the exhaust manifolds. Refer to EM-19, "
Removal and Installation" .
26. Install the engine slingers into the left bank cylinder head and
right bank cylinder head.
27. Remove the A/T. Refer to AT-244, "
Removal and Installation
(4x2)" or AT-247, "Removal and Installation (4x4)" .
28. Lift using hoist and secure the engine in position.
29. Remove the engine assembly from the vehicle, avoid interfer-
ence with the vehicle body.
CAUTION:
Before and during lifting, always check if any harnesses
are left connected.
30. Remove the parts that may restrict installation of the engine to the engine stand.
NOTE:
This procedure is described assuming that you use an engine stand mounting to the surface to which the
transmission mounts.
a. Remove the drive plate.
Holding the crankshaft pulley bolt, lock the crankshaft to remove the drive plate bolts.
Loosen the bolts diagonally.
WBIA0464E
Engine slinger torque: 45.0 N·m (4.6 kg-m, 33 ft-lb)
PBIC1556E
Page 1974 of 3419
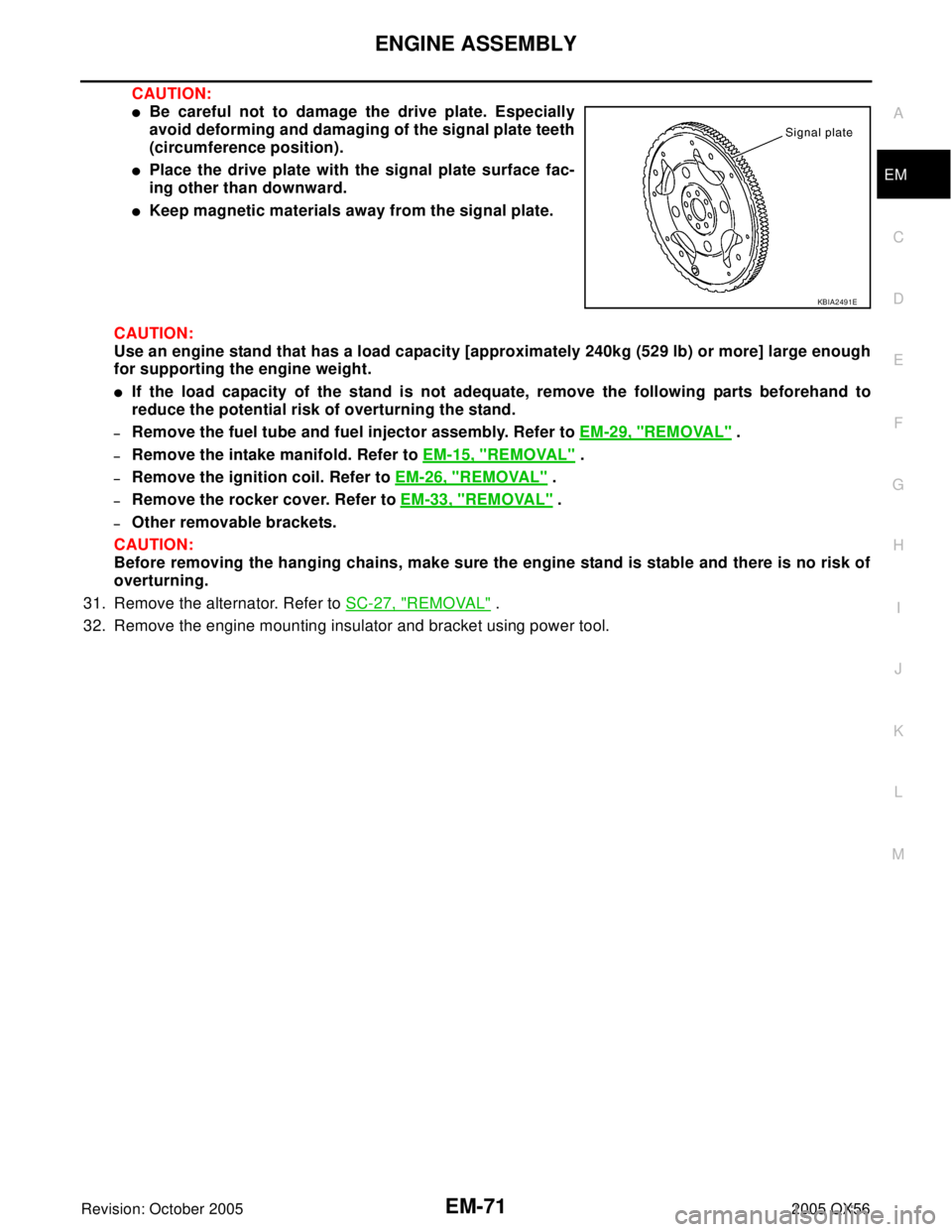
ENGINE ASSEMBLY
EM-71
C
D
E
F
G
H
I
J
K
L
MA
EM
Revision: October 20052005 QX56
CAUTION:
Be careful not to damage the drive plate. Especially
avoid deforming and damaging of the signal plate teeth
(circumference position).
Place the drive plate with the signal plate surface fac-
ing other than downward.
Keep magnetic materials away from the signal plate.
CAUTION:
Use an engine stand that has a load capacity [approximately 240kg (529 lb) or more] large enough
for supporting the engine weight.
If the load capacity of the stand is not adequate, remove the following parts beforehand to
reduce the potential risk of overturning the stand.
–Remove the fuel tube and fuel injector assembly. Refer to EM-29, "REMOVAL" .
–Remove the intake manifold. Refer to EM-15, "REMOVAL" .
–Remove the ignition coil. Refer to EM-26, "REMOVAL" .
–Remove the rocker cover. Refer to EM-33, "REMOVAL" .
–Other removable brackets.
CAUTION:
Before removing the hanging chains, make sure the engine stand is stable and there is no risk of
overturning.
31. Remove the alternator. Refer to SC-27, "
REMOVAL" .
32. Remove the engine mounting insulator and bracket using power tool.
KBIA2491E
Page 1975 of 3419
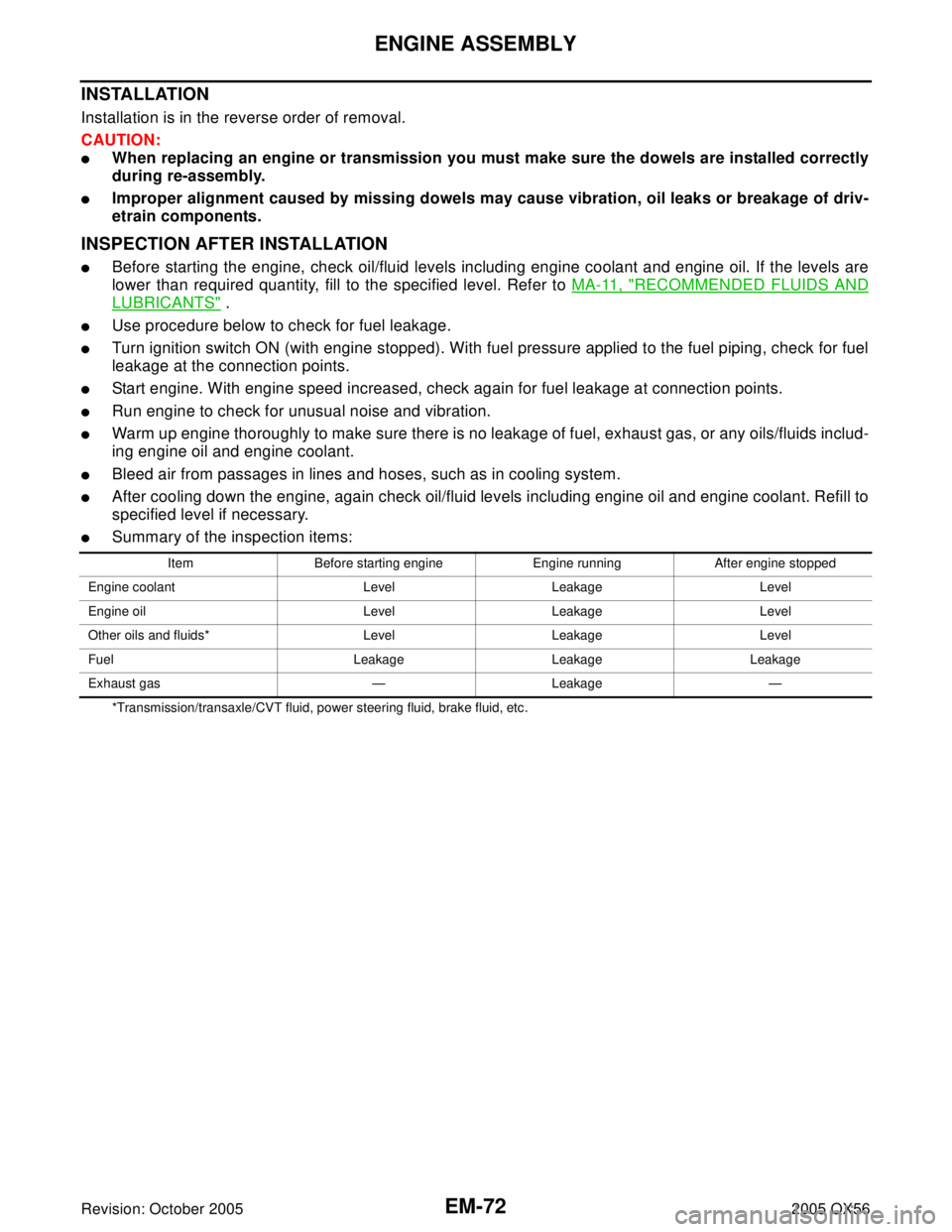
EM-72Revision: October 2005
ENGINE ASSEMBLY
2005 QX56
INSTALLATION
Installation is in the reverse order of removal.
CAUTION:
When replacing an engine or transmission you must make sure the dowels are installed correctly
during re-assembly.
Improper alignment caused by missing dowels may cause vibration, oil leaks or breakage of driv-
etrain components.
INSPECTION AFTER INSTALLATION
Before starting the engine, check oil/fluid levels including engine coolant and engine oil. If the levels are
lower than required quantity, fill to the specified level. Refer to MA-11, "
RECOMMENDED FLUIDS AND
LUBRICANTS" .
Use procedure below to check for fuel leakage.
Turn ignition switch ON (with engine stopped). With fuel pressure applied to the fuel piping, check for fuel
leakage at the connection points.
Start engine. With engine speed increased, check again for fuel leakage at connection points.
Run engine to check for unusual noise and vibration.
Warm up engine thoroughly to make sure there is no leakage of fuel, exhaust gas, or any oils/fluids includ-
ing engine oil and engine coolant.
Bleed air from passages in lines and hoses, such as in cooling system.
After cooling down the engine, again check oil/fluid levels including engine oil and engine coolant. Refill to
specified level if necessary.
Summary of the inspection items:
*Transmission/transaxle/CVT fluid, power steering fluid, brake fluid, etc.Item Before starting engine Engine running After engine stopped
Engine coolant Level Leakage Level
Engine oil Level Leakage Level
Other oils and fluids* Level Leakage Level
Fuel Leakage Leakage Leakage
Exhaust gas — Leakage —
Page 1976 of 3419
CYLINDER BLOCK
EM-73
C
D
E
F
G
H
I
J
K
L
MA
EM
Revision: October 20052005 QX56
CYLINDER BLOCKPFP:11010
Disassembly and AssemblyEBS00LMJ
WBIA0471E