Page 1905 of 3419
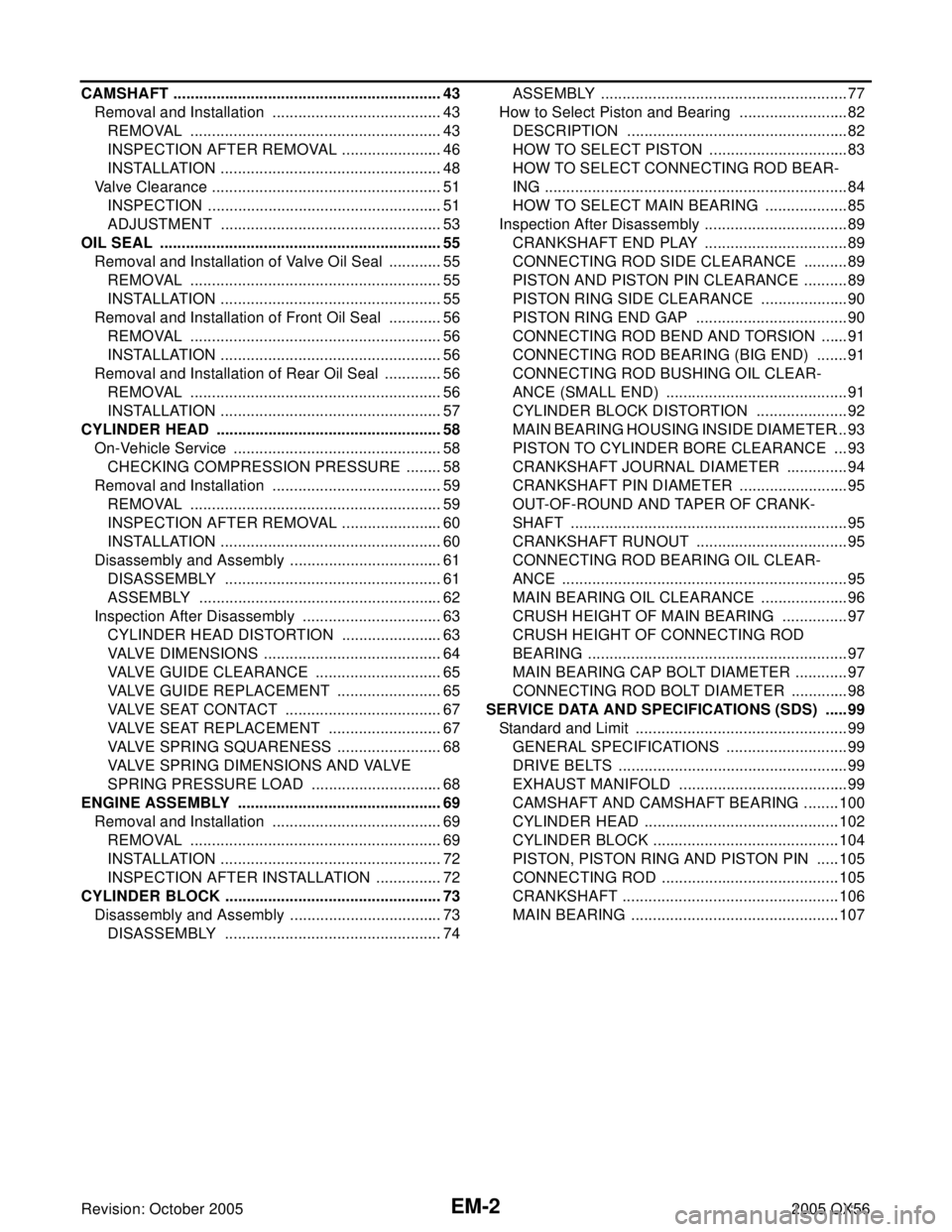
EM-2Revision: October 20052005 QX56 CAMSHAFT ............................................................... 43
Removal and Installation ........................................ 43
REMOVAL ........................................................... 43
INSPECTION AFTER REMOVAL ........................ 46
INSTALLATION .................................................... 48
Valve Clearance ...................................................... 51
INSPECTION ....................................................... 51
ADJUSTMENT .................................................... 53
OIL SEAL .................................................................. 55
Removal and Installation of Valve Oil Seal ............. 55
REMOVAL ........................................................... 55
INSTALLATION .................................................... 55
Removal and Installation of Front Oil Seal ............. 56
REMOVAL ........................................................... 56
INSTALLATION .................................................... 56
Removal and Installation of Rear Oil Seal .............. 56
REMOVAL ........................................................... 56
INSTALLATION .................................................... 57
CYLINDER HEAD ..................................................... 58
On-Vehicle Service ................................................. 58
CHECKING COMPRESSION PRESSURE ......... 58
Removal and Installation ........................................ 59
REMOVAL ........................................................... 59
INSPECTION AFTER REMOVAL ........................ 60
INSTALLATION .................................................... 60
Disassembly and Assembly .................................... 61
DISASSEMBLY ................................................... 61
ASSEMBLY ......................................................... 62
Inspection After Disassembly ................................. 63
CYLINDER HEAD DISTORTION ........................ 63
VALVE DIMENSIONS .......................................... 64
VALVE GUIDE CLEARANCE .............................. 65
VALVE GUIDE REPLACEMENT ......................... 65
VALVE SEAT CONTACT ..................................... 67
VALVE SEAT REPLACEMENT ........................... 67
VALVE SPRING SQUARENESS ......................... 68
VALVE SPRING DIMENSIONS AND VALVE
SPRING PRESSURE LOAD ............................... 68
ENGINE ASSEMBLY ................................................ 69
Removal and Installation ........................................ 69
REMOVAL ........................................................... 69
INSTALLATION .................................................... 72
INSPECTION AFTER INSTALLATION ................ 72
CYLINDER BLOCK ................................................... 73
Disassembly and Assembly .................................... 73
DISASSEMBLY ................................................... 74ASSEMBLY ..........................................................77
How to Select Piston and Bearing ..........................82
DESCRIPTION ....................................................82
HOW TO SELECT PISTON .................................83
HOW TO SELECT CONNECTING ROD BEAR-
ING .......................................................................84
HOW TO SELECT MAIN BEARING ....................85
Inspection After Disassembly ..................................89
CRANKSHAFT END PLAY ..................................89
CONNECTING ROD SIDE CLEARANCE ...........89
PISTON AND PISTON PIN CLEARANCE ...........89
PISTON RING SIDE CLEARANCE .....................90
PISTON RING END GAP ....................................90
CONNECTING ROD BEND AND TORSION .......91
CONNECTING ROD BEARING (BIG END) ........91
CONNECTING ROD BUSHING OIL CLEAR-
ANCE (SMALL END) ...........................................91
CYLINDER BLOCK DISTORTION ......................92
MAIN BEARING HOUSING INSIDE DIAMETER ...93
PISTON TO CYLINDER BORE CLEARANCE ....93
CRANKSHAFT JOURNAL DIAMETER ...............94
CRANKSHAFT PIN DIAMETER ..........................95
OUT-OF-ROUND AND TAPER OF CRANK-
SHAFT .................................................................95
CRANKSHAFT RUNOUT ....................................95
CONNECTING ROD BEARING OIL CLEAR-
ANCE ...................................................................95
MAIN BEARING OIL CLEARANCE .....................96
CRUSH HEIGHT OF MAIN BEARING ................97
CRUSH HEIGHT OF CONNECTING ROD
BEARING .............................................................97
MAIN BEARING CAP BOLT DIAMETER .............97
CONNECTING ROD BOLT DIAMETER ..............98
SERVICE DATA AND SPECIFICATIONS (SDS) ......99
Standard and Limit ..................................................99
GENERAL SPECIFICATIONS .............................99
DRIVE BELTS ......................................................99
EXHAUST MANIFOLD ........................................99
CAMSHAFT AND CAMSHAFT BEARING ......... 100
CYLINDER HEAD .............................................. 102
CYLINDER BLOCK ............................................ 104
PISTON, PISTON RING AND PISTON PIN ...... 105
CONNECTING ROD .......................................... 105
CRANKSHAFT ................................................... 106
MAIN BEARING ................................................. 107
Page 1906 of 3419
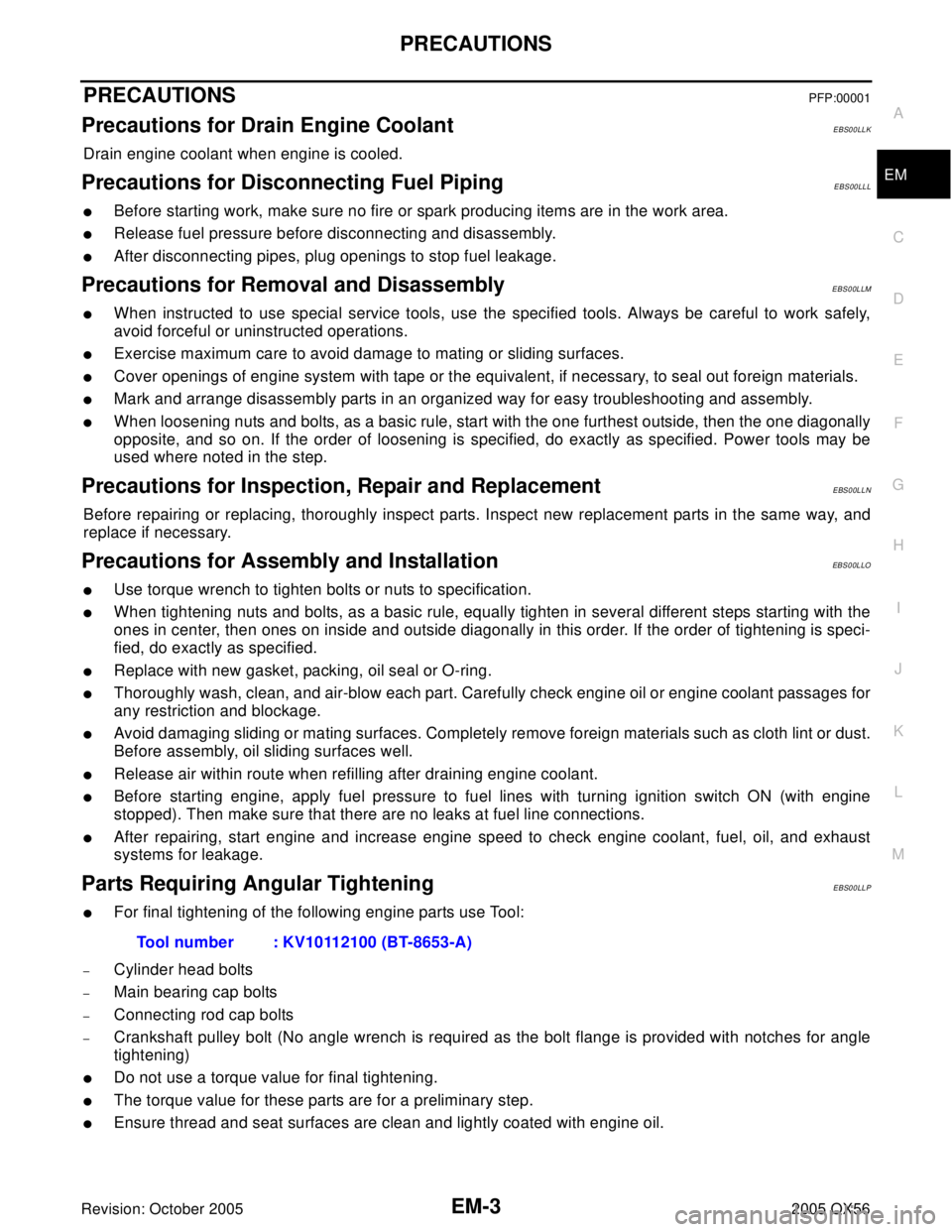
PRECAUTIONS
EM-3
C
D
E
F
G
H
I
J
K
L
MA
EM
Revision: October 20052005 QX56
PRECAUTIONSPFP:00001
Precautions for Drain Engine CoolantEBS00LLK
Drain engine coolant when engine is cooled.
Precautions for Disconnecting Fuel PipingEBS00LLL
Before starting work, make sure no fire or spark producing items are in the work area.
Release fuel pressure before disconnecting and disassembly.
After disconnecting pipes, plug openings to stop fuel leakage.
Precautions for Removal and DisassemblyEBS00LLM
When instructed to use special service tools, use the specified tools. Always be careful to work safely,
avoid forceful or uninstructed operations.
Exercise maximum care to avoid damage to mating or sliding surfaces.
Cover openings of engine system with tape or the equivalent, if necessary, to seal out foreign materials.
Mark and arrange disassembly parts in an organized way for easy troubleshooting and assembly.
When loosening nuts and bolts, as a basic rule, start with the one furthest outside, then the one diagonally
opposite, and so on. If the order of loosening is specified, do exactly as specified. Power tools may be
used where noted in the step.
Precautions for Inspection, Repair and ReplacementEBS00LLN
Before repairing or replacing, thoroughly inspect parts. Inspect new replacement parts in the same way, and
replace if necessary.
Precautions for Assembly and InstallationEBS00LLO
Use torque wrench to tighten bolts or nuts to specification.
When tightening nuts and bolts, as a basic rule, equally tighten in several different steps starting with the
ones in center, then ones on inside and outside diagonally in this order. If the order of tightening is speci-
fied, do exactly as specified.
Replace with new gasket, packing, oil seal or O-ring.
Thoroughly wash, clean, and air-blow each part. Carefully check engine oil or engine coolant passages for
any restriction and blockage.
Avoid damaging sliding or mating surfaces. Completely remove foreign materials such as cloth lint or dust.
Before assembly, oil sliding surfaces well.
Release air within route when refilling after draining engine coolant.
Before starting engine, apply fuel pressure to fuel lines with turning ignition switch ON (with engine
stopped). Then make sure that there are no leaks at fuel line connections.
After repairing, start engine and increase engine speed to check engine coolant, fuel, oil, and exhaust
systems for leakage.
Parts Requiring Angular TighteningEBS00LLP
For final tightening of the following engine parts use Tool:
–Cylinder head bolts
–Main bearing cap bolts
–Connecting rod cap bolts
–Crankshaft pulley bolt (No angle wrench is required as the bolt flange is provided with notches for angle
tightening)
Do not use a torque value for final tightening.
The torque value for these parts are for a preliminary step.
Ensure thread and seat surfaces are clean and lightly coated with engine oil. Tool number : KV10112100 (BT-8653-A)
Page 1907 of 3419
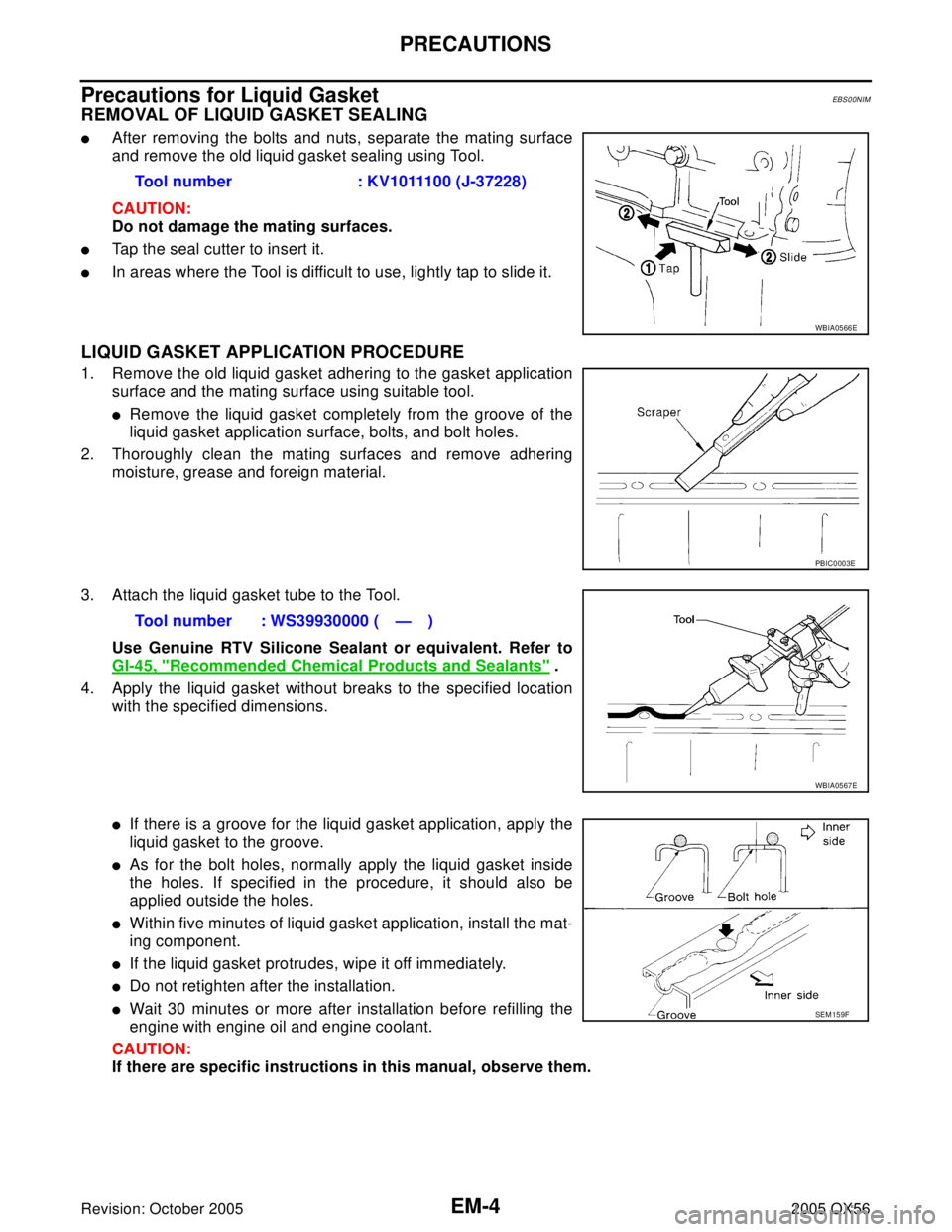
EM-4Revision: October 2005
PRECAUTIONS
2005 QX56
Precautions for Liquid GasketEBS00NIM
REMOVAL OF LIQUID GASKET SEALING
After removing the bolts and nuts, separate the mating surface
and remove the old liquid gasket sealing using Tool.
CAUTION:
Do not damage the mating surfaces.
Tap the seal cutter to insert it.
In areas where the Tool is difficult to use, lightly tap to slide it.
LIQUID GASKET APPLICATION PROCEDURE
1. Remove the old liquid gasket adhering to the gasket application
surface and the mating surface using suitable tool.
Remove the liquid gasket completely from the groove of the
liquid gasket application surface, bolts, and bolt holes.
2. Thoroughly clean the mating surfaces and remove adhering
moisture, grease and foreign material.
3. Attach the liquid gasket tube to the Tool.
Use Genuine RTV Silicone Sealant or equivalent. Refer to
GI-45, "
Recommended Chemical Products and Sealants" .
4. Apply the liquid gasket without breaks to the specified location
with the specified dimensions.
If there is a groove for the liquid gasket application, apply the
liquid gasket to the groove.
As for the bolt holes, normally apply the liquid gasket inside
the holes. If specified in the procedure, it should also be
applied outside the holes.
Within five minutes of liquid gasket application, install the mat-
ing component.
If the liquid gasket protrudes, wipe it off immediately.
Do not retighten after the installation.
Wait 30 minutes or more after installation before refilling the
engine with engine oil and engine coolant.
CAUTION:
If there are specific instructions in this manual, observe them.Tool number : KV1011100 (J-37228)
WBIA0566E
PBIC0003E
Tool number : WS39930000 ( — )
WBIA0567E
SEM 15 9F
Page 1908 of 3419
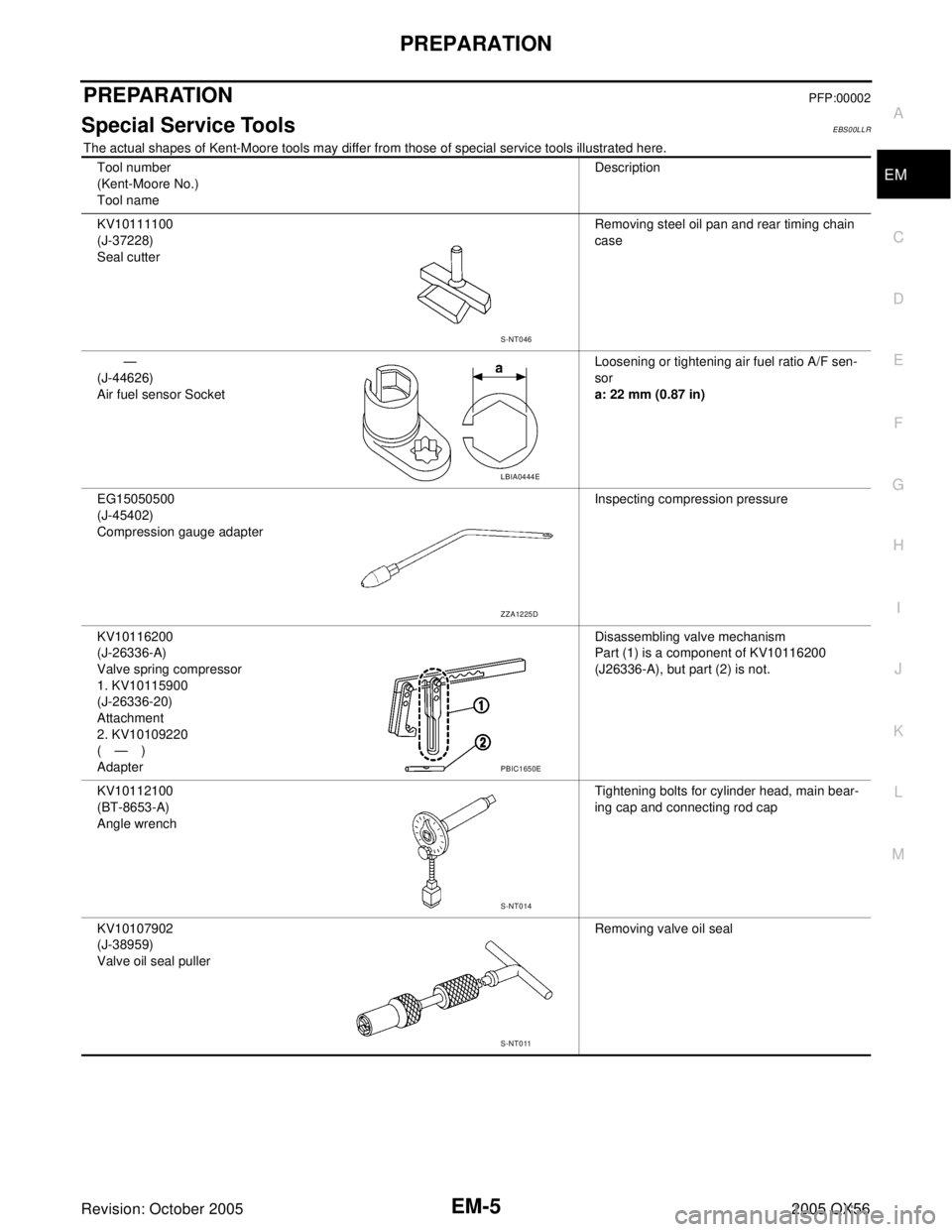
PREPARATION
EM-5
C
D
E
F
G
H
I
J
K
L
MA
EM
Revision: October 20052005 QX56
PREPARATIONPFP:00002
Special Service ToolsEBS00LLR
The actual shapes of Kent-Moore tools may differ from those of special service tools illustrated here.
Tool number
(Kent-Moore No.)
Tool nameDescription
KV10111100
(J-37228)
Seal cutterRemoving steel oil pan and rear timing chain
case
—
(J-44626)
Air fuel sensor SocketLoosening or tightening air fuel ratio A/F sen-
sor
a: 22 mm (0.87 in)
EG15050500
(J-45402)
Compression gauge adapterInspecting compression pressure
KV10116200
(J-26336-A)
Valve spring compressor
1. KV10115900
(J-26336-20)
Attachment
2. KV10109220
(—)
AdapterDisassembling valve mechanism
Part (1) is a component of KV10116200
(J26336-A), but part (2) is not.
KV10112100
(BT-8653-A)
Angle wrenchTightening bolts for cylinder head, main bear-
ing cap and connecting rod cap
KV10107902
(J-38959)
Valve oil seal pullerRemoving valve oil seal
S-NT046
LBIA0444E
ZZA1225D
PBIC1650E
S-NT014
S-NT011
Page 1909 of 3419
EM-6Revision: October 2005
PREPARATION
2005 QX56
KV10115600
(J-38958)
Valve oil seal driftInstalling valve oil seal
Use side A.
a: 20 (0.79) dia. d: 8 (0.31) dia.
b: 13 (0.51) dia. e: 10.7 (0.421) dia.
c: 10.3 (0.406) dia. f: 5 (0.20) dia.
Unit: mm (in)
EM03470000
(J-8037)
Piston ring compressorInstalling piston assembly into cylinder bore
ST16610001
(J-23907)
Pilot bushing pullerRemoving crankshaft pilot bushing
WS39930000
(—)
Tube presserPressing the tube of liquid gasket
—
(J-47245)
Ring gear stopperRemoving and installing crankshaft pulley
—
(J-45488)
Quick connector releaseRemoving fuel tube quick connectors in en-
gine room Tool number
(Kent-Moore No.)
Tool nameDescription
S-NT603
S-NT044
S-NT045
S-NT052
LBIA0451E
PBIC0198E
Page 1910 of 3419
PREPARATION
EM-7
C
D
E
F
G
H
I
J
K
L
MA
EM
Revision: October 20052005 QX56
Commercial Service ToolsEBS00LLS
(Kent-Moore No.)
Tool nameDescription
Power toolLoosening bolts and nuts
Spark plug wrench Removing and installing spark plug
(J-24239-01)
Cylinder head bolt wrenchLoosening and tightening cylinder head bolt,
and use with angle wrench [SST:
KV10112100 (BT-8653-A)]
a: 13 (0.51) dia.
b: 12 (0.47)
c: 10 (0.39)
Unit: mm (in)
Valve seat cutter set Finishing valve seat dimensions
Pulley pullerRemoving crankshaft pulley
Piston ring expander Removing and installing piston ring
Valve guide drift Removing and installing valve guide
Intake & Exhaust:
a: 9.5 mm (0.374 in) dia.
b: 5.5 mm (0.217 in) dia.
PBIC0190E
S-NT047
NT583
S-NT048
ZZA0010D
S-NT030
S-NT015
Page 1911 of 3419
EM-8Revision: October 2005
PREPARATION
2005 QX56
Valve guide reamer 1: Reaming valve guide hole
2: Reaming hole for oversize valve guide
Intake & Exhaust:
d
1 : 6.0 mm (0.236 in) dia.
d
2 : 10.175 - 10.196 mm (0.4006 - 0.4014 in)
dia.
Front oil seal drift Installing front oil seal
Rear oil seal drift Installing rear oil seal
(J-43897-18)
(J-43897-12)
Oxygen sensor thread cleanerReconditioning the exhaust system threads
before installing a new A/F sensor and heated
oxygen sensor (Use with anti-seize lubricant
shown below.)
a: J-43897-18 (18 mm dia.) for zirconia
heated oxygen sensor
b: J-43897-12 (12 mm dia.) for titania heat-
ed oxygen sensor
Anti-seize lubricant (Permatex 133AR
or equivalent meeting MIL specifica-
tion MIL-A-907)Lubricating A/F sensors and heated oxygen
sensor thread cleaning tool when recondition-
ing exhaust system threads (Kent-Moore No.)
Tool nameDescription
S-NT016
ZZA0012D
ZZA0025D
AEM488
AEM489
Page 1912 of 3419
NOISE, VIBRATION, AND HARSHNESS (NVH) TROUBLESHOOTING
EM-9
C
D
E
F
G
H
I
J
K
L
MA
EM
Revision: October 20052005 QX56
NOISE, VIBRATION, AND HARSHNESS (NVH) TROUBLESHOOTINGPFP:00003
NVH Troubleshooting —Engine NoiseEBS00LLT
KBIA2503E