Page 2865 of 3419
RFD-18
REAR FINAL DRIVE ASSEMBLY
Revision: October 20052005 QX56
4. Drive the pinion mate shaft lock pin out from the drive gear side
using a suitable punch.
INSPECTION
Contact Surfaces
1. Clean the disassembled parts in a suitable solvent and blow dry using compressed air.
2. If the following surfaces are burred or scratched, smooth them using an oil stone.
Differential case
Side gear
Pinion mate gear
Pinion mate shaft
Bearing
1. Thoroughly clean the bearing.
2. Check the bearing for wear, scratches, pitting, or flaking.
3. Check the tapered roller bearing for smooth rotation. If dam-
aged, replace the outer race and inner race as a set.
ADJUSTMENT OF DIFFERENTIAL CASE
Thrust Washer Selection
1. Install the side gears, pinion mate gears, and thrust washers into
the differential case.
SPD0 25
SPD7 15
SPD5 52
Page 2866 of 3419
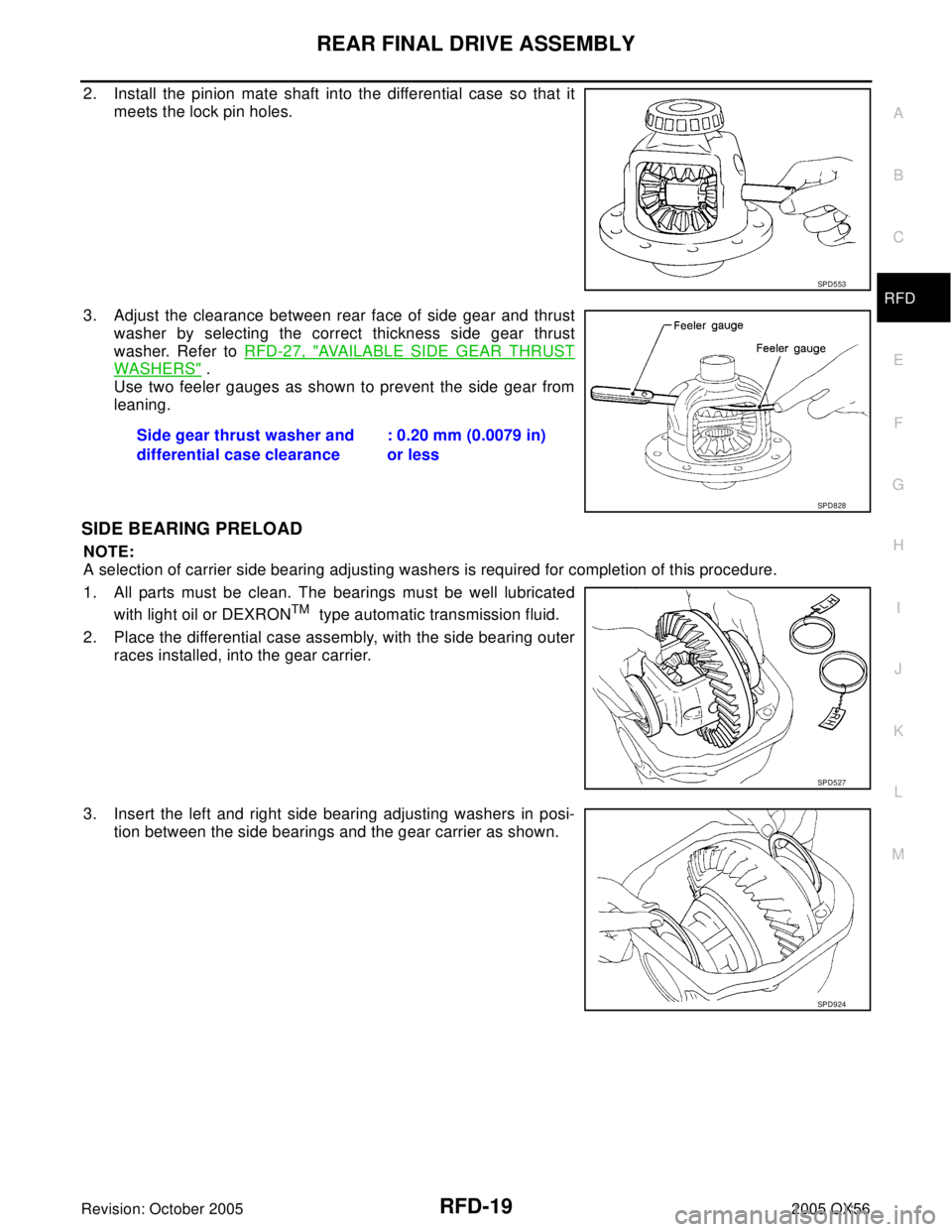
REAR FINAL DRIVE ASSEMBLY
RFD-19
C
E
F
G
H
I
J
K
L
MA
B
RFD
Revision: October 20052005 QX56
2. Install the pinion mate shaft into the differential case so that it
meets the lock pin holes.
3. Adjust the clearance between rear face of side gear and thrust
washer by selecting the correct thickness side gear thrust
washer. Refer to RFD-27, "
AVAILABLE SIDE GEAR THRUST
WASHERS" .
Use two feeler gauges as shown to prevent the side gear from
leaning.
SIDE BEARING PRELOAD
NOTE:
A selection of carrier side bearing adjusting washers is required for completion of this procedure.
1. All parts must be clean. The bearings must be well lubricated
with light oil or DEXRON
TM type automatic transmission fluid.
2. Place the differential case assembly, with the side bearing outer
races installed, into the gear carrier.
3. Insert the left and right side bearing adjusting washers in posi-
tion between the side bearings and the gear carrier as shown.
SPD5 53
Side gear thrust washer and
differential case clearance: 0.20 mm (0.0079 in)
or less
SPD8 28
SPD5 27
SPD9 24
Page 2867 of 3419

RFD-20
REAR FINAL DRIVE ASSEMBLY
Revision: October 20052005 QX56
4. Install the side bearing caps in their original locations marked
during disassembly, and tighten the bearing cap bolts to specifi-
cation.
5. Turn the carrier several times to seat the bearings.
6. Measure the turning force of the carrier at the drive gear retain-
ing bolts using a suitable spring gauge.
7. If the turning force is not within the specification, adjust the turn-
ing force.
If the turning force is less than specification, install thicker
washers.
If the turning force is greater than specification, install thinner
washers.
Select the correct washer size to adjust the turning force.
Refer to RFD-28, "
SIDE BEARING ADJUSTING WASHERS"
.
8. Record the selected washer thickness required for the correct
carrier side bearing preload.
9. Remove the differential case assembly from the gear carrier
using Tool. Save the selected side bearing adjusting washers for
assembly.
TOOTH CONTACT
NOTE:
Checking the gear tooth contact pattern is necessary to verify that there is the correct tooth contact between
the drive gear and the drive pinion.
Hypoid gears which are not positioned properly may be noisy or have a short service life. Check the gear tooth
contact pattern to obtain the best contact for low noise and long service life.Bearing cap bolts : 93 N·m (9.5 kg-m, 69 ft.-lb)
SPD5 26
Drive gear bolt pulling force : 29.4 - 147 N (3 - 15 kg-f,
22 - 108 lb-f)
SPD1 94 A
SPD7 72
Tool number : HT72400000
S-PD3 44
Page 2868 of 3419
REAR FINAL DRIVE ASSEMBLY
RFD-21
C
E
F
G
H
I
J
K
L
MA
B
RFD
Revision: October 20052005 QX56
1. Thoroughly clean the drive gear and drive pinion teeth.
2. Lightly apply a mixture of powdered ferric oxide and oil or the
equivalent. Apply it to 3 or 4 teeth of the drive gear drive side.
3. Use your hand to hold the companion flange steady and rotate
the drive gear in both directions.
4. Check the tooth contact as shown.
ASSEMBLY OF DIFFERENTIAL CASE ASSEMBLY
1. Install the pinion mate shaft lock pin using a suitable punch as
shown.
The lock pin must be flush with the case.
2. Place the differential case on the drive gear.
SPD3 57
SDIA0813E
SDIA1910E
SPD0 30
Page 2869 of 3419
RFD-22
REAR FINAL DRIVE ASSEMBLY
Revision: October 20052005 QX56
3. Apply genuine medium strength locking sealant or equivalent as
shown. Refer to GI-45, "
Recommended Chemical Products and
Sealants" .
Tighten the drive gear bolts in a criss-cross pattern to specifi-
cation.
4. Press-fit the side bearing inner races on the differential case
using Tools.
INSTALLATION OF DRIVE PINION ASSEMBLY
1. Press-fit the pinion front and rear bearing outer races using
Tools.
2. Select pinion height adjusting washer. Refer to RFD-27, "
Drive Pinion Height Adjustment" . Drive gear bolts
Step 1 : 78.5 N·m (8.0 kg-m, 58 ft-lb)
Step 2 : 34° degrees
SPD5 54
Tool number A: KV38100200
B: ST33081000
SPD3 53
Tool number A: ST15310000
B: ST35325000
C: ST30621000
SPD9 92
Page 2870 of 3419
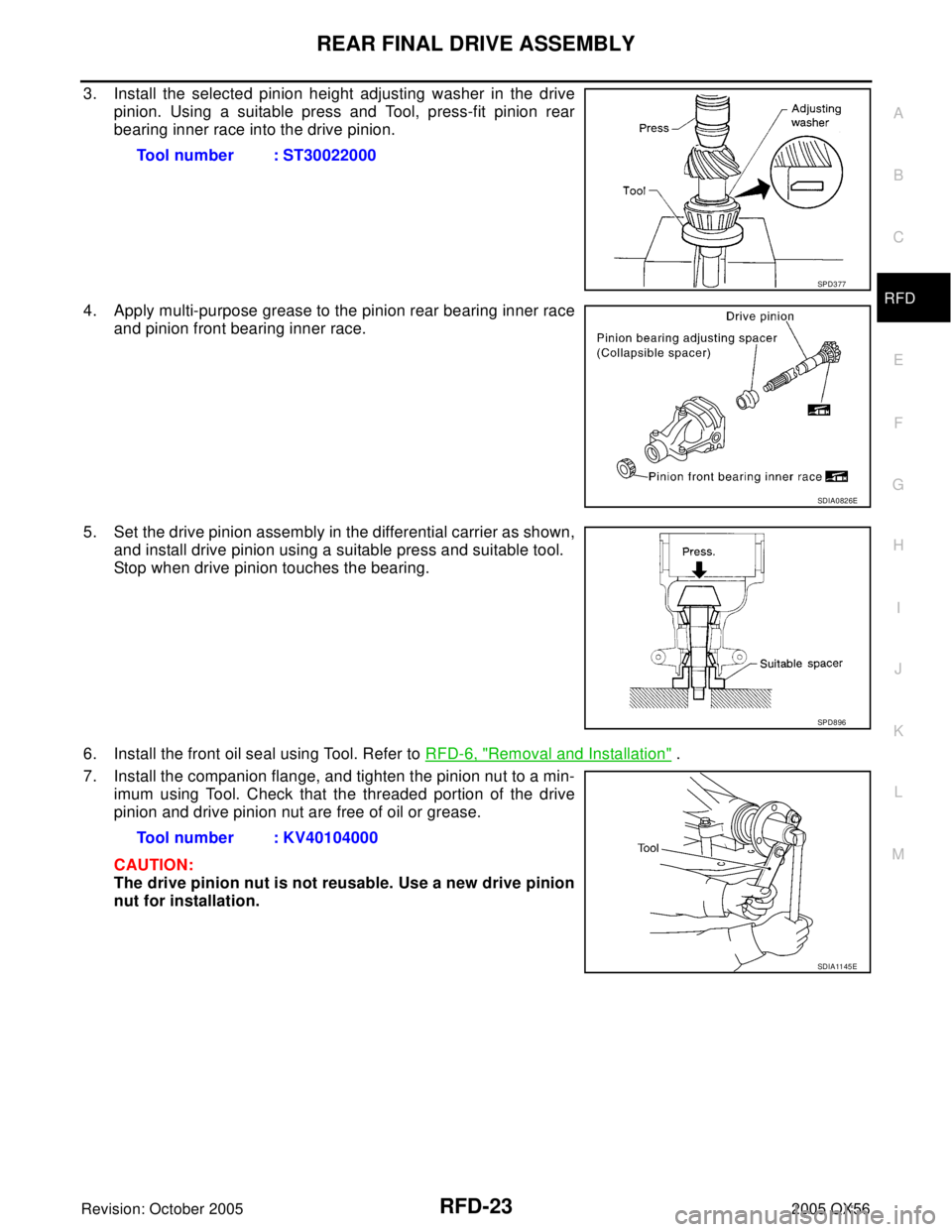
REAR FINAL DRIVE ASSEMBLY
RFD-23
C
E
F
G
H
I
J
K
L
MA
B
RFD
Revision: October 20052005 QX56
3. Install the selected pinion height adjusting washer in the drive
pinion. Using a suitable press and Tool, press-fit pinion rear
bearing inner race into the drive pinion.
4. Apply multi-purpose grease to the pinion rear bearing inner race
and pinion front bearing inner race.
5. Set the drive pinion assembly in the differential carrier as shown,
and install drive pinion using a suitable press and suitable tool.
Stop when drive pinion touches the bearing.
6. Install the front oil seal using Tool. Refer to RFD-6, "
Removal and Installation" .
7. Install the companion flange, and tighten the pinion nut to a min-
imum using Tool. Check that the threaded portion of the drive
pinion and drive pinion nut are free of oil or grease.
CAUTION:
The drive pinion nut is not reusable. Use a new drive pinion
nut for installation. Tool number : ST30022000
SPD3 77
SDIA0826E
SPD8 96
Tool number : KV40104000
SDIA11 45 E
Page 2871 of 3419
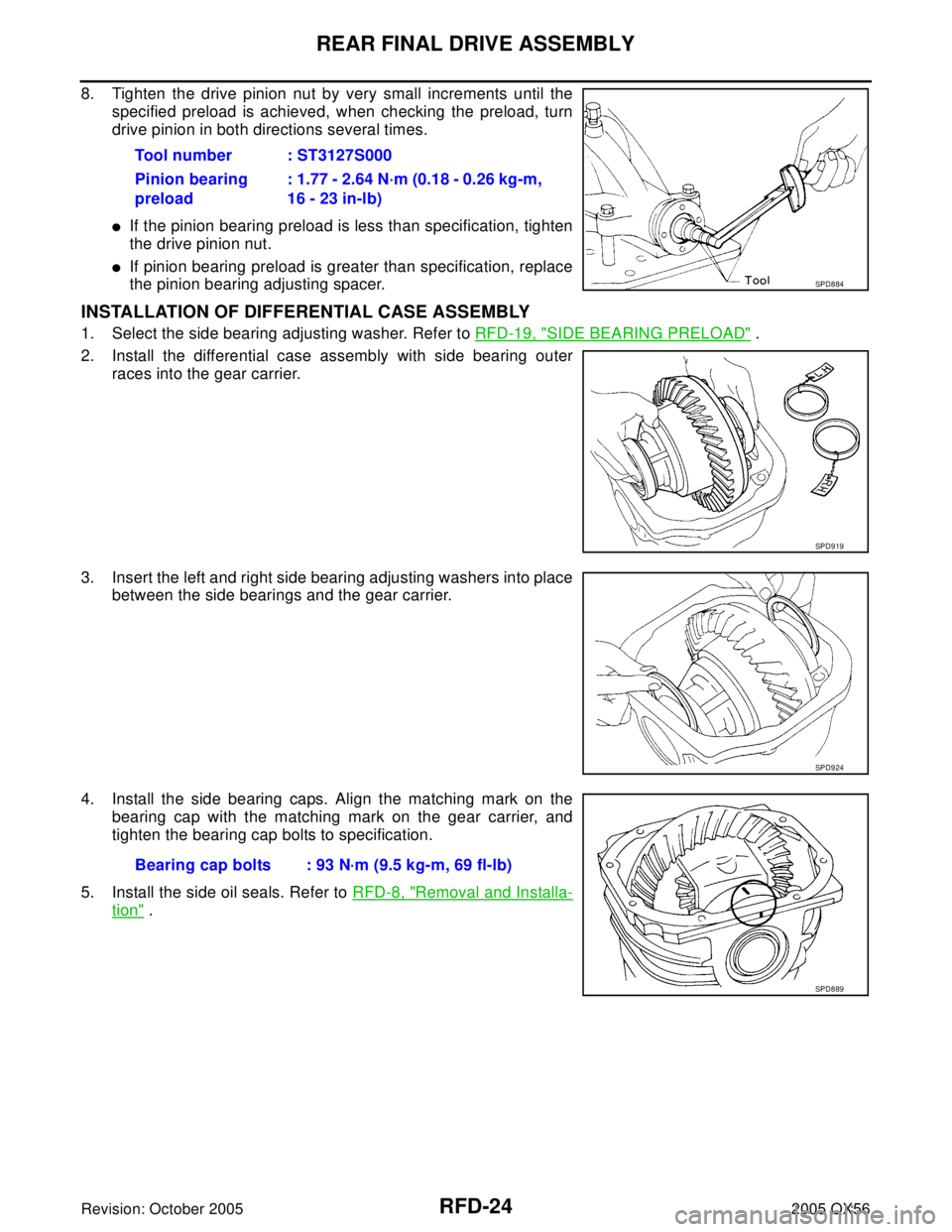
RFD-24
REAR FINAL DRIVE ASSEMBLY
Revision: October 20052005 QX56
8. Tighten the drive pinion nut by very small increments until the
specified preload is achieved, when checking the preload, turn
drive pinion in both directions several times.
If the pinion bearing preload is less than specification, tighten
the drive pinion nut.
If pinion bearing preload is greater than specification, replace
the pinion bearing adjusting spacer.
INSTALLATION OF DIFFERENTIAL CASE ASSEMBLY
1. Select the side bearing adjusting washer. Refer to RFD-19, "SIDE BEARING PRELOAD" .
2. Install the differential case assembly with side bearing outer
races into the gear carrier.
3. Insert the left and right side bearing adjusting washers into place
between the side bearings and the gear carrier.
4. Install the side bearing caps. Align the matching mark on the
bearing cap with the matching mark on the gear carrier, and
tighten the bearing cap bolts to specification.
5. Install the side oil seals. Refer to RFD-8, "
Removal and Installa-
tion" . Tool number : ST3127S000
Pinion bearing
preload: 1.77 - 2.64 N·m (0.18 - 0.26 kg-m,
16 - 23 in-lb)
SPD8 84
SPD9 19
SPD9 24
Bearing cap bolts : 93 N·m (9.5 kg-m, 69 fl-lb)
SPD8 89
Page 2872 of 3419
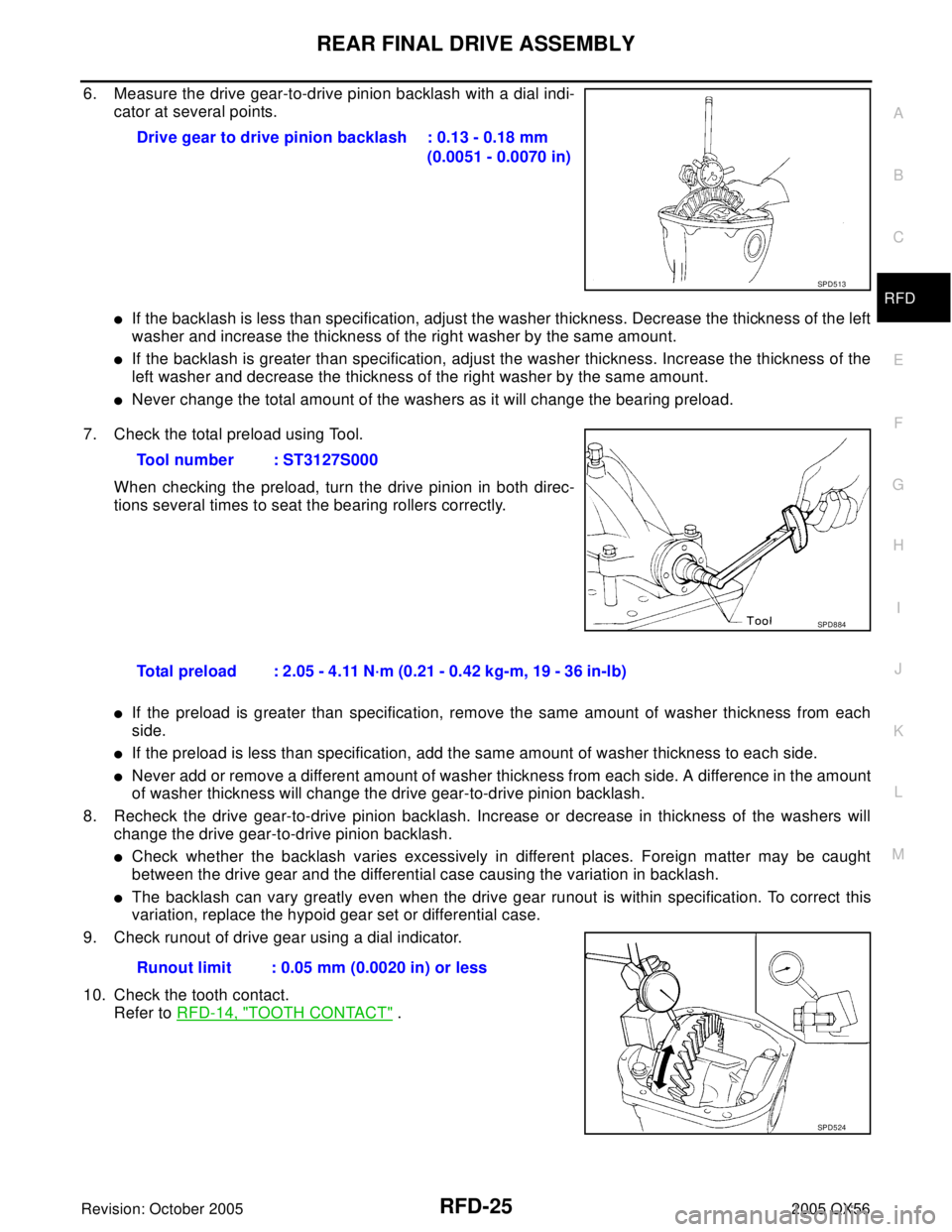
REAR FINAL DRIVE ASSEMBLY
RFD-25
C
E
F
G
H
I
J
K
L
MA
B
RFD
Revision: October 20052005 QX56
6. Measure the drive gear-to-drive pinion backlash with a dial indi-
cator at several points.
If the backlash is less than specification, adjust the washer thickness. Decrease the thickness of the left
washer and increase the thickness of the right washer by the same amount.
If the backlash is greater than specification, adjust the washer thickness. Increase the thickness of the
left washer and decrease the thickness of the right washer by the same amount.
Never change the total amount of the washers as it will change the bearing preload.
7. Check the total preload using Tool.
When checking the preload, turn the drive pinion in both direc-
tions several times to seat the bearing rollers correctly.
If the preload is greater than specification, remove the same amount of washer thickness from each
side.
If the preload is less than specification, add the same amount of washer thickness to each side.
Never add or remove a different amount of washer thickness from each side. A difference in the amount
of washer thickness will change the drive gear-to-drive pinion backlash.
8. Recheck the drive gear-to-drive pinion backlash. Increase or decrease in thickness of the washers will
change the drive gear-to-drive pinion backlash.
Check whether the backlash varies excessively in different places. Foreign matter may be caught
between the drive gear and the differential case causing the variation in backlash.
The backlash can vary greatly even when the drive gear runout is within specification. To correct this
variation, replace the hypoid gear set or differential case.
9. Check runout of drive gear using a dial indicator.
10. Check the tooth contact.
Refer to RFD-14, "
TOOTH CONTACT" . Drive gear to drive pinion backlash : 0.13 - 0.18 mm
(0.0051 - 0.0070 in)
SPD5 13
Tool number : ST3127S000
SPD8 84
Total preload : 2.05 - 4.11 N·m (0.21 - 0.42 kg-m, 19 - 36 in-lb)
Runout limit : 0.05 mm (0.0020 in) or less
SPD5 24