Page 3193 of 3419
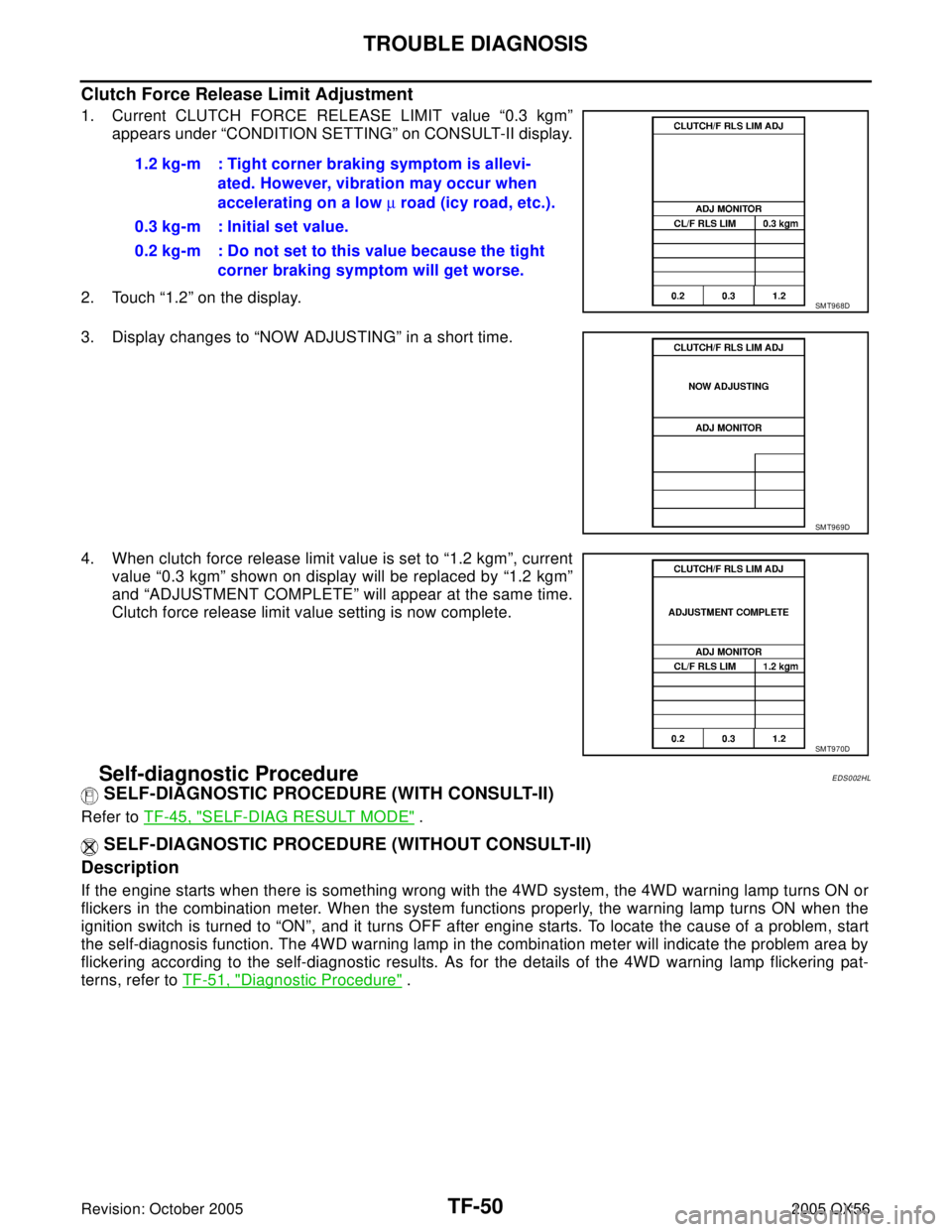
TF-50
TROUBLE DIAGNOSIS
Revision: October 20052005 QX56
Clutch Force Release Limit Adjustment
1. Current CLUTCH FORCE RELEASE LIMIT value “0.3 kgm”
appears under “CONDITION SETTING” on CONSULT-II display.
2. Touch “1.2” on the display.
3. Display changes to “NOW ADJUSTING” in a short time.
4. When clutch force release limit value is set to “1.2 kgm”, current
value “0.3 kgm” shown on display will be replaced by “1.2 kgm”
and “ADJUSTMENT COMPLETE” will appear at the same time.
Clutch force release limit value setting is now complete.
Self-diagnostic ProcedureEDS002HL
SELF-DIAGNOSTIC PROCEDURE (WITH CONSULT-II)
Refer to TF-45, "SELF-DIAG RESULT MODE" .
SELF-DIAGNOSTIC PROCEDURE (WITHOUT CONSULT-II)
Description
If the engine starts when there is something wrong with the 4WD system, the 4WD warning lamp turns ON or
flickers in the combination meter. When the system functions properly, the warning lamp turns ON when the
ignition switch is turned to “ON”, and it turns OFF after engine starts. To locate the cause of a problem, start
the self-diagnosis function. The 4WD warning lamp in the combination meter will indicate the problem area by
flickering according to the self-diagnostic results. As for the details of the 4WD warning lamp flickering pat-
terns, refer to TF-51, "
Diagnostic Procedure" . 1.2 kg-m : Tight corner braking symptom is allevi-
ated. However, vibration may occur when
accelerating on a low µ road (icy road, etc.).
0.3 kg-m : Initial set value.
0.2 kg-m : Do not set to this value because the tight
corner braking symptom will get worse.
SMT968D
SMT969D
SMT970D
Page 3194 of 3419
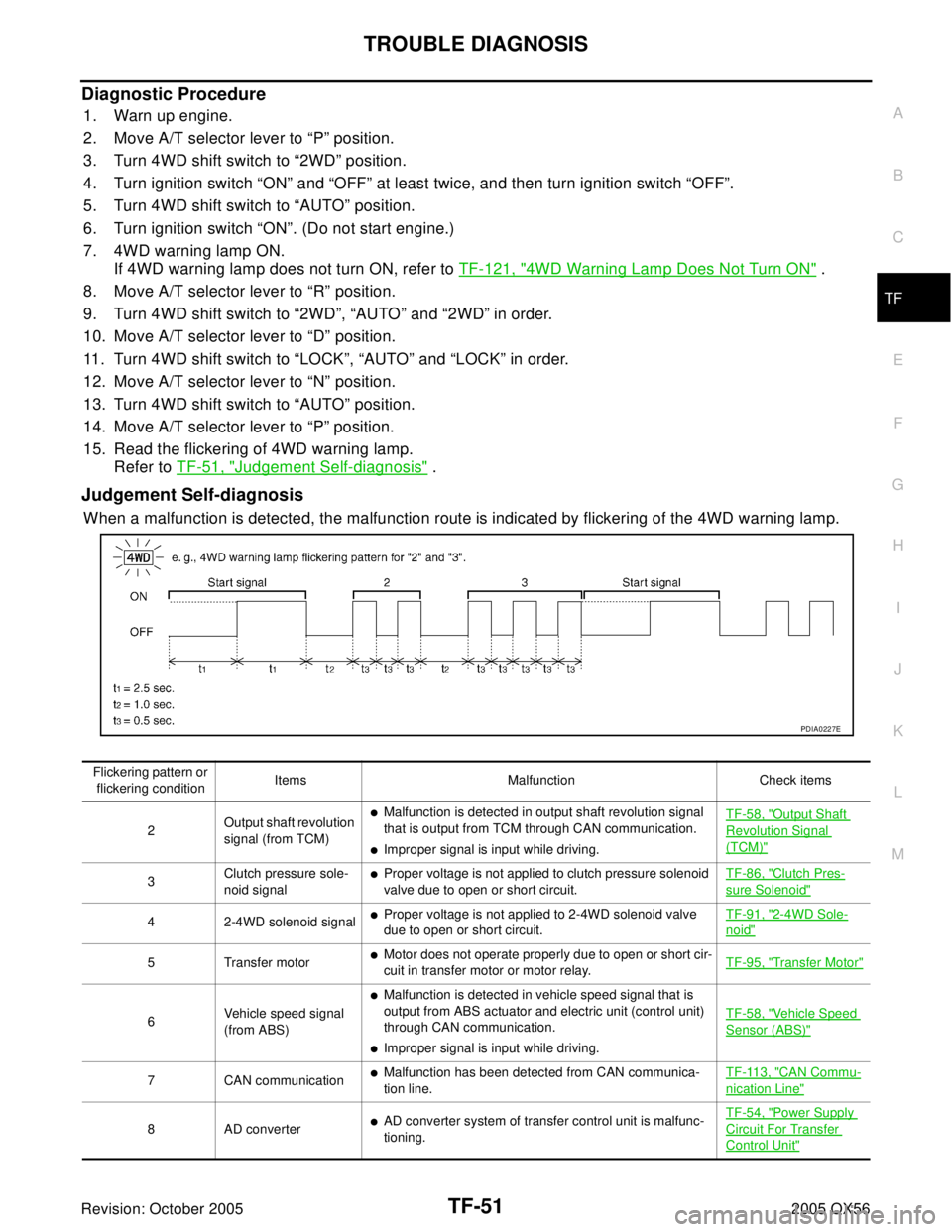
TROUBLE DIAGNOSIS
TF-51
C
E
F
G
H
I
J
K
L
MA
B
TF
Revision: October 20052005 QX56
Diagnostic Procedure
1. Warn up engine.
2. Move A/T selector lever to “P” position.
3. Turn 4WD shift switch to “2WD” position.
4. Turn ignition switch “ON” and “OFF” at least twice, and then turn ignition switch “OFF”.
5. Turn 4WD shift switch to “AUTO” position.
6. Turn ignition switch “ON”. (Do not start engine.)
7. 4WD warning lamp ON.
If 4WD warning lamp does not turn ON, refer to TF-121, "
4WD Warning Lamp Does Not Turn ON" .
8. Move A/T selector lever to “R” position.
9. Turn 4WD shift switch to “2WD”, “AUTO” and “2WD” in order.
10. Move A/T selector lever to “D” position.
11. Turn 4WD shift switch to “LOCK”, “AUTO” and “LOCK” in order.
12. Move A/T selector lever to “N” position.
13. Turn 4WD shift switch to “AUTO” position.
14. Move A/T selector lever to “P” position.
15. Read the flickering of 4WD warning lamp.
Refer to TF-51, "
Judgement Self-diagnosis" .
Judgement Self-diagnosis
When a malfunction is detected, the malfunction route is indicated by flickering of the 4WD warning lamp.
PDIA0227E
Flickering pattern or
flickering conditionItems Malfunction Check items
2Output shaft revolution
signal (from TCM)
Malfunction is detected in output shaft revolution signal
that is output from TCM through CAN communication.
Improper signal is input while driving.TF-58, "
Output Shaft
Revolution Signal
(TCM)"
3Clutch pressure sole-
noid signalProper voltage is not applied to clutch pressure solenoid
valve due to open or short circuit.TF-86, "Clutch Pres-
sure Solenoid"
4 2-4WD solenoid signalProper voltage is not applied to 2-4WD solenoid valve
due to open or short circuit.TF-91, "2-4WD Sole-
noid"
5 Transfer motorMotor does not operate properly due to open or short cir-
cuit in transfer motor or motor relay.TF-95, "Tran s fe r Mo to r"
6Vehicle speed signal
(from ABS)
Malfunction is detected in vehicle speed signal that is
output from ABS actuator and electric unit (control unit)
through CAN communication.
Improper signal is input while driving.TF-58, "
Vehicle Speed
Sensor (ABS)"
7 CAN communicationMalfunction has been detected from CAN communica-
tion line.TF-113, "CAN Commu-
nication Line"
8 AD converterAD converter system of transfer control unit is malfunc-
tioning.TF-54, "Power Supply
Circuit For Transfer
Control Unit"
Page 3195 of 3419
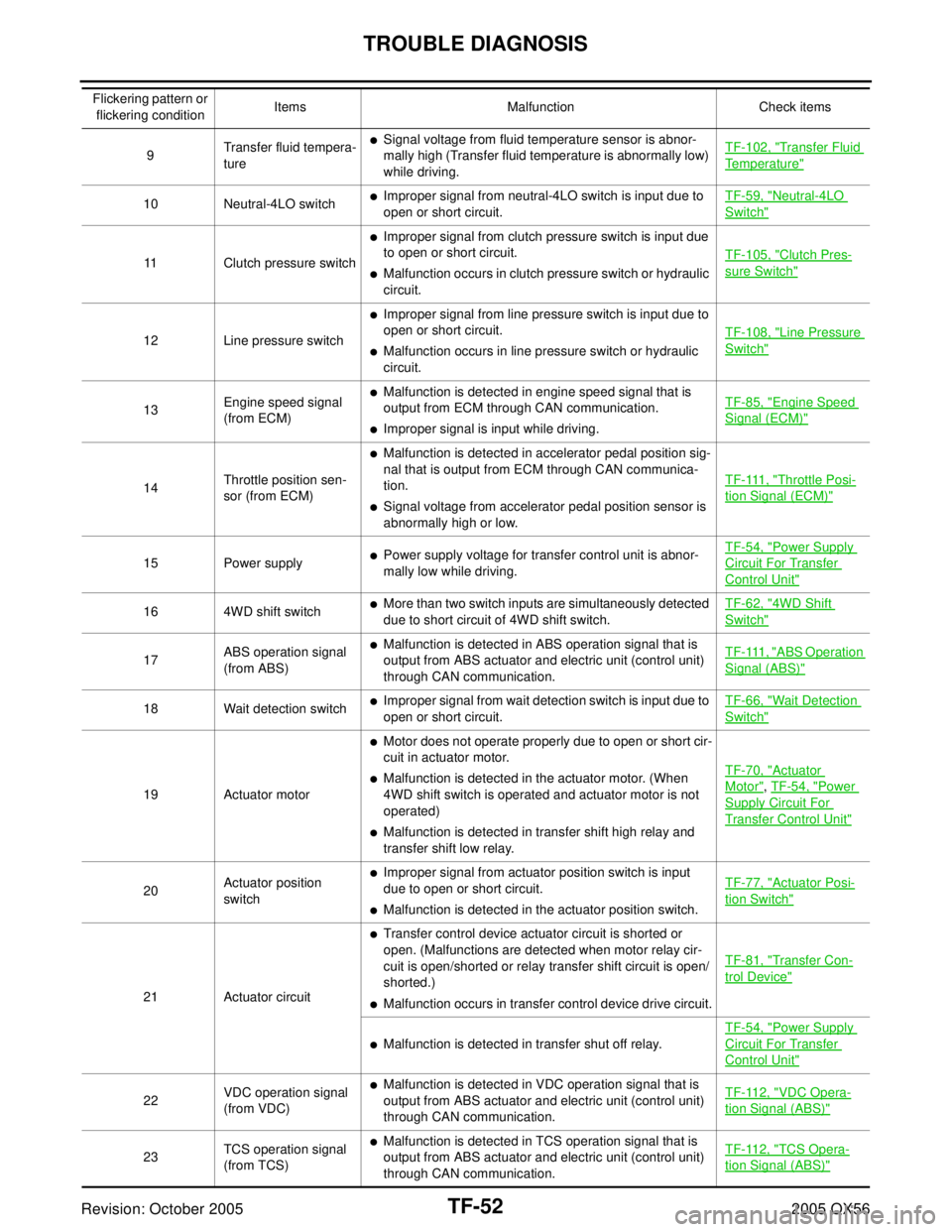
TF-52
TROUBLE DIAGNOSIS
Revision: October 20052005 QX56
9Transfer fluid tempera-
ture
Signal voltage from fluid temperature sensor is abnor-
mally high (Transfer fluid temperature is abnormally low)
while driving.TF-102, "Transfer Fluid
Temperature"
10 Neutral-4LO switchImproper signal from neutral-4LO switch is input due to
open or short circuit.TF-59, "Neutral-4LO
Switch"
11 Clutch pressure switch
Improper signal from clutch pressure switch is input due
to open or short circuit.
Malfunction occurs in clutch pressure switch or hydraulic
circuit.TF-105, "
Clutch Pres-
sure Switch"
12 Line pressure switch
Improper signal from line pressure switch is input due to
open or short circuit.
Malfunction occurs in line pressure switch or hydraulic
circuit.TF-108, "
Line Pressure
Switch"
13Engine speed signal
(from ECM)
Malfunction is detected in engine speed signal that is
output from ECM through CAN communication.
Improper signal is input while driving.TF-85, "
Engine Speed
Signal (ECM)"
14Throttle position sen-
sor (from ECM)
Malfunction is detected in accelerator pedal position sig-
nal that is output from ECM through CAN communica-
tion.
Signal voltage from accelerator pedal position sensor is
abnormally high or low.T F - 111 , "
Throttle Posi-
tion Signal (ECM)"
15 Power supplyPower supply voltage for transfer control unit is abnor-
mally low while driving.TF-54, "Power Supply
Circuit For Transfer
Control Unit"
16 4WD shift switchMore than two switch inputs are simultaneously detected
due to short circuit of 4WD shift switch.TF-62, "4WD Shift
Switch"
17ABS operation signal
(from ABS)
Malfunction is detected in ABS operation signal that is
output from ABS actuator and electric unit (control unit)
through CAN communication.T F - 111 , "ABS Operation
Signal (ABS)"
18 Wait detection switchImproper signal from wait detection switch is input due to
open or short circuit.TF-66, "Wait Detection
Switch"
19 Actuator motor
Motor does not operate properly due to open or short cir-
cuit in actuator motor.
Malfunction is detected in the actuator motor. (When
4WD shift switch is operated and actuator motor is not
operated)
Malfunction is detected in transfer shift high relay and
transfer shift low relay.TF-70, "
Actuator
Motor", TF-54, "Power
Supply Circuit For
Transfer Control Unit"
20Actuator position
switch
Improper signal from actuator position switch is input
due to open or short circuit.
Malfunction is detected in the actuator position switch.TF-77, "
Actuator Posi-
tion Switch"
21 Actuator circuit
Transfer control device actuator circuit is shorted or
open. (Malfunctions are detected when motor relay cir-
cuit is open/shorted or relay transfer shift circuit is open/
shorted.)
Malfunction occurs in transfer control device drive circuit.TF-81, "
Transfer Con-
trol Device"
Malfunction is detected in transfer shut off relay.TF-54, "
Power Supply
Circuit For Transfer
Control Unit"
22VDC operation signal
(from VDC)
Malfunction is detected in VDC operation signal that is
output from ABS actuator and electric unit (control unit)
through CAN communication.TF-112, "VDC Opera-
tion Signal (ABS)"
23TCS operation signal
(from TCS)
Malfunction is detected in TCS operation signal that is
output from ABS actuator and electric unit (control unit)
through CAN communication.TF-112, "TCS Opera-
tion Signal (ABS)"
Flickering pattern or
flickering conditionItems Malfunction Check items
Page 3196 of 3419
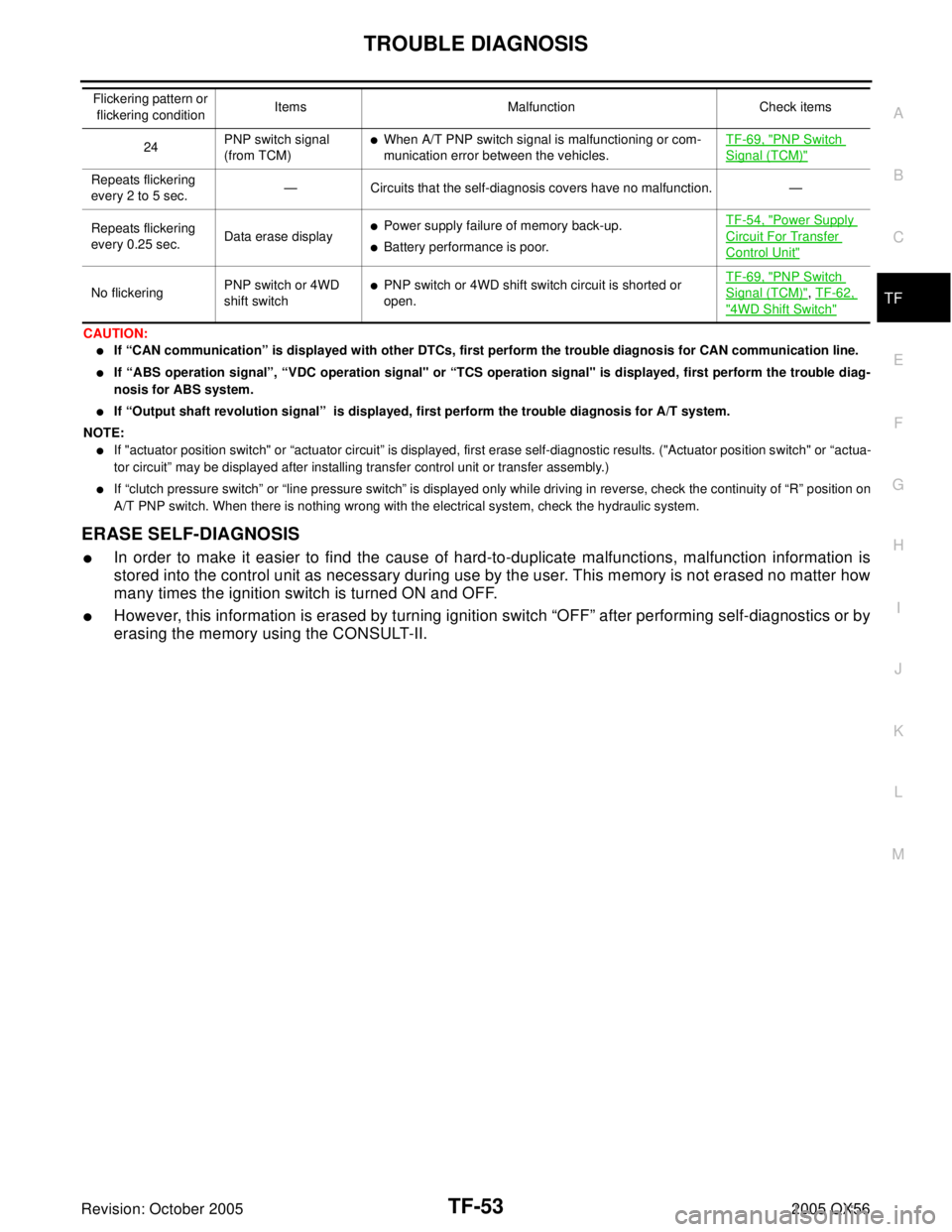
TROUBLE DIAGNOSIS
TF-53
C
E
F
G
H
I
J
K
L
MA
B
TF
Revision: October 20052005 QX56
CAUTION:
If “CAN communication” is displayed with other DTCs, first perform the trouble diagnosis for CAN communication line.
If “ABS operation signal”, “VDC operation signal" or “TCS operation signal" is displayed, first perform the trouble diag-
nosis for ABS system.
If “Output shaft revolution signal” is displayed, first perform the trouble diagnosis for A/T system.
NOTE:
If "actuator position switch" or “actuator circuit” is displayed, first erase self-diagnostic results. ("Actuator position switch" or “actua-
tor circuit” may be displayed after installing transfer control unit or transfer assembly.)
If “clutch pressure switch” or “line pressure switch” is displayed only while driving in reverse, check the continuity of “R” position on
A/T PNP switch. When there is nothing wrong with the electrical system, check the hydraulic system.
ERASE SELF-DIAGNOSIS
In order to make it easier to find the cause of hard-to-duplicate malfunctions, malfunction information is
stored into the control unit as necessary during use by the user. This memory is not erased no matter how
many times the ignition switch is turned ON and OFF.
However, this information is erased by turning ignition switch “OFF” after performing self-diagnostics or by
erasing the memory using the CONSULT-II.
24PNP switch signal
(from TCM)When A/T PNP switch signal is malfunctioning or com-
munication error between the vehicles.TF-69, "PNP Switch
Signal (TCM)"
Repeats flickering
every 2 to 5 sec.— Circuits that the self-diagnosis covers have no malfunction. —
Repeats flickering
every 0.25 sec.Data erase display
Power supply failure of memory back-up.
Battery performance is poor.TF-54, "
Power Supply
Circuit For Transfer
Control Unit"
No flickeringPNP switch or 4WD
shift switchPNP switch or 4WD shift switch circuit is shorted or
open.TF-69, "PNP Switch
Signal (TCM)", TF-62,
"4WD Shift Switch"
Flickering pattern or
flickering conditionItems Malfunction Check items
Page 3197 of 3419
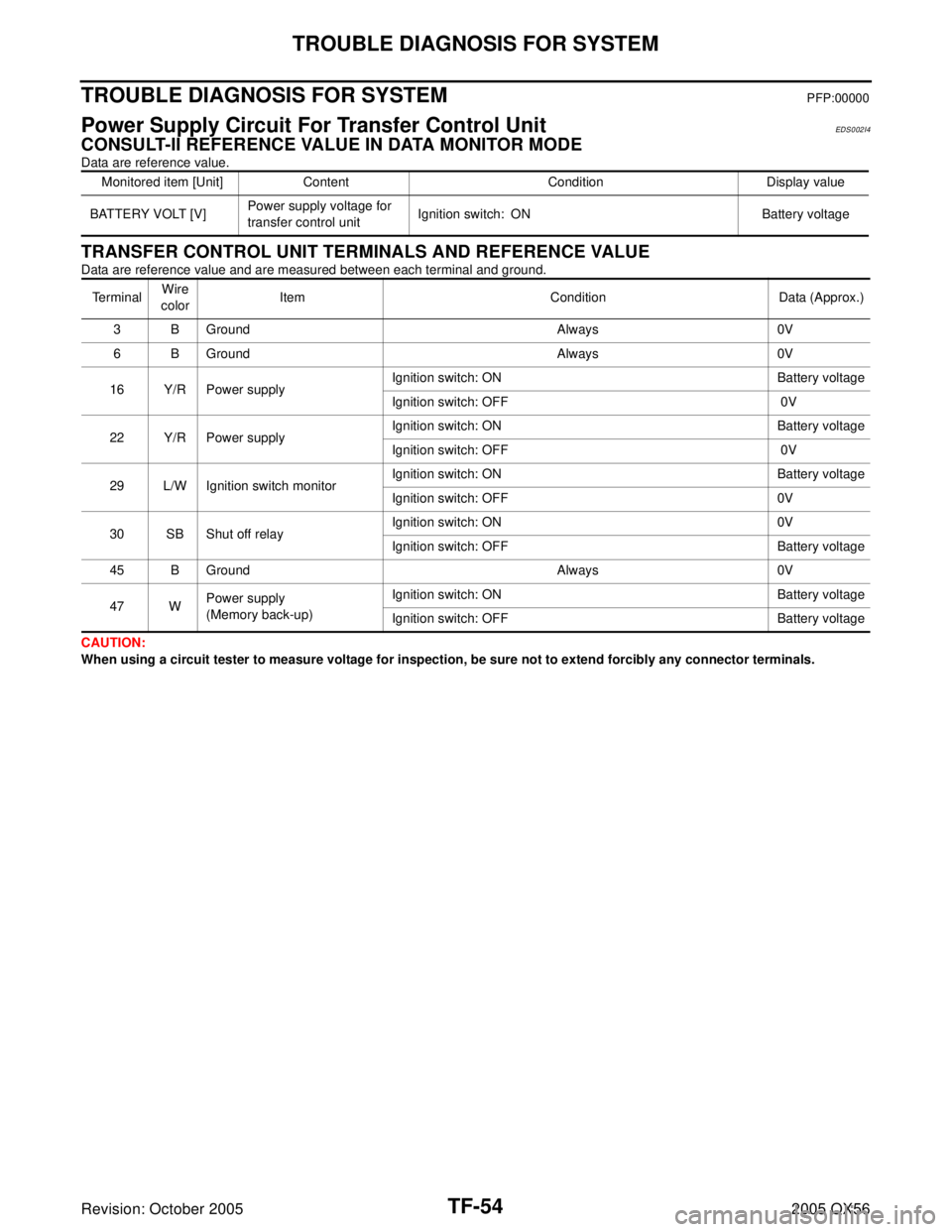
TF-54
TROUBLE DIAGNOSIS FOR SYSTEM
Revision: October 20052005 QX56
TROUBLE DIAGNOSIS FOR SYSTEMPFP:00000
Power Supply Circuit For Transfer Control UnitEDS0 02 I4
CONSULT-II REFERENCE VALUE IN DATA MONITOR MODE
Data are reference value.
TRANSFER CONTROL UNIT TERMINALS AND REFERENCE VALUE
Data are reference value and are measured between each terminal and ground.
CAUTION:
When using a circuit tester to measure voltage for inspection, be sure not to extend forcibly any connector terminals.Monitored item [Unit] Content Condition Display value
BATTERY VOLT [V]Power supply voltage for
transfer control unitIgnition switch: ON Battery voltage
Te r m i n a lWire
colorItem Condition Data (Approx.)
3 B Ground Always 0V
6 B Ground Always 0V
16 Y/R Power supplyIgnition switch: ON Battery voltage
Ignition switch: OFF 0V
22 Y/R Power supplyIgnition switch: ON Battery voltage
Ignition switch: OFF 0V
29 L/W Ignition switch monitorIgnition switch: ON Battery voltage
Ignition switch: OFF 0V
30 SB Shut off relayIgnition switch: ON 0V
Ignition switch: OFF Battery voltage
45 B Ground Always 0V
47 WPower supply
(Memory back-up)Ignition switch: ON Battery voltage
Ignition switch: OFF Battery voltage
Page 3198 of 3419
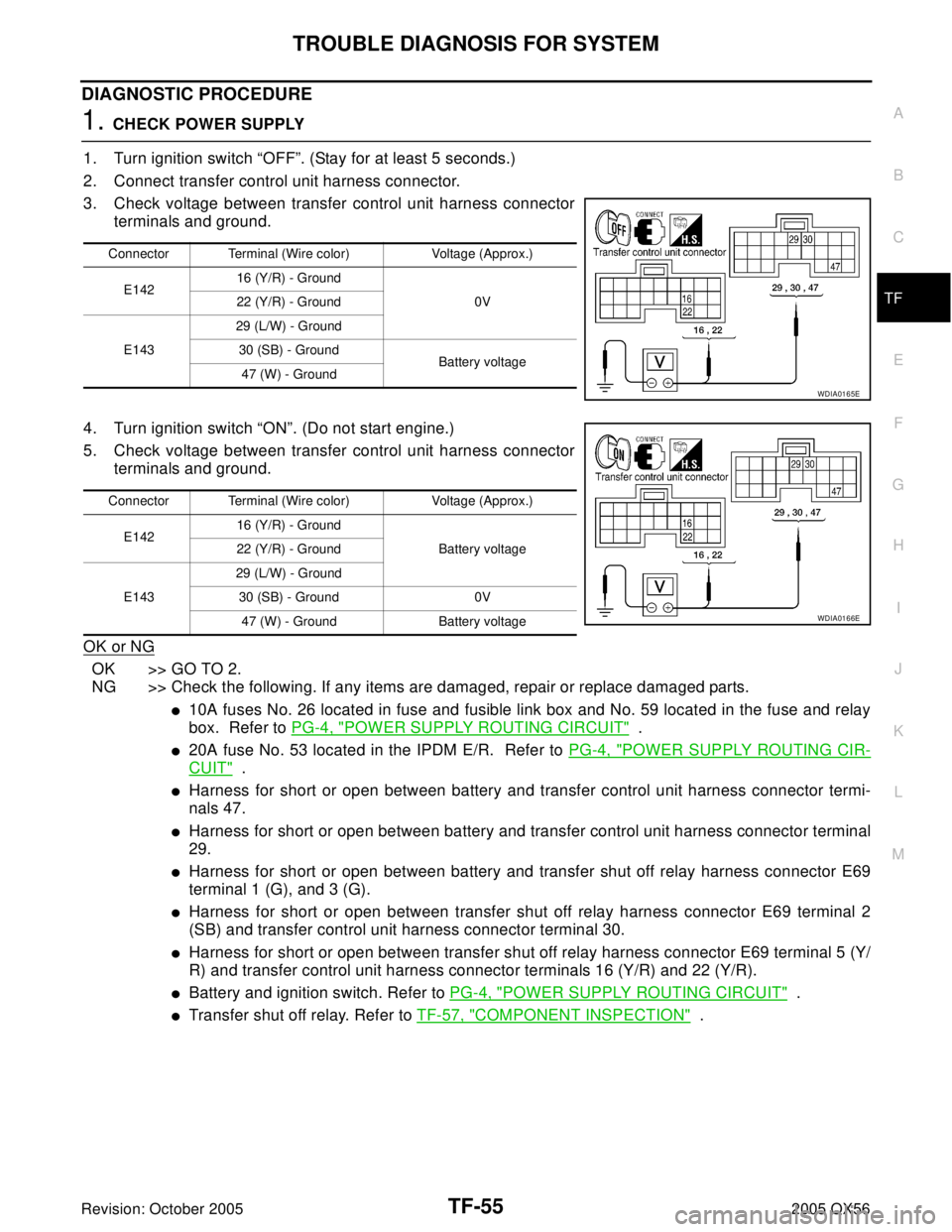
TROUBLE DIAGNOSIS FOR SYSTEM
TF-55
C
E
F
G
H
I
J
K
L
MA
B
TF
Revision: October 20052005 QX56
DIAGNOSTIC PROCEDURE
1. CHECK POWER SUPPLY
1. Turn ignition switch “OFF”. (Stay for at least 5 seconds.)
2. Connect transfer control unit harness connector.
3. Check voltage between transfer control unit harness connector
terminals and ground.
4. Turn ignition switch “ON”. (Do not start engine.)
5. Check voltage between transfer control unit harness connector
terminals and ground.
OK or NG
OK >> GO TO 2.
NG >> Check the following. If any items are damaged, repair or replace damaged parts.
10A fuses No. 26 located in fuse and fusible link box and No. 59 located in the fuse and relay
box. Refer to PG-4, "
POWER SUPPLY ROUTING CIRCUIT" .
20A fuse No. 53 located in the IPDM E/R. Refer to PG-4, "POWER SUPPLY ROUTING CIR-
CUIT" .
Harness for short or open between battery and transfer control unit harness connector termi-
nals 47.
Harness for short or open between battery and transfer control unit harness connector terminal
29.
Harness for short or open between battery and transfer shut off relay harness connector E69
terminal 1 (G), and 3 (G).
Harness for short or open between transfer shut off relay harness connector E69 terminal 2
(SB) and transfer control unit harness connector terminal 30.
Harness for short or open between transfer shut off relay harness connector E69 terminal 5 (Y/
R) and transfer control unit harness connector terminals 16 (Y/R) and 22 (Y/R).
Battery and ignition switch. Refer to PG-4, "POWER SUPPLY ROUTING CIRCUIT" .
Transfer shut off relay. Refer to TF-57, "COMPONENT INSPECTION" .
Connector Terminal (Wire color) Voltage (Approx.)
E14216 (Y/R) - Ground
0V 22 (Y/R) - Ground
E14329 (L/W) - Ground
30 (SB) - Ground
Battery voltage
47 (W) - Ground
WDIA0165E
Connector Terminal (Wire color) Voltage (Approx.)
E14216 (Y/R) - Ground
Battery voltage 22 (Y/R) - Ground
E14329 (L/W) - Ground
30 (SB) - Ground 0V
47 (W) - Ground Battery voltage
WDIA0166E
Page 3199 of 3419
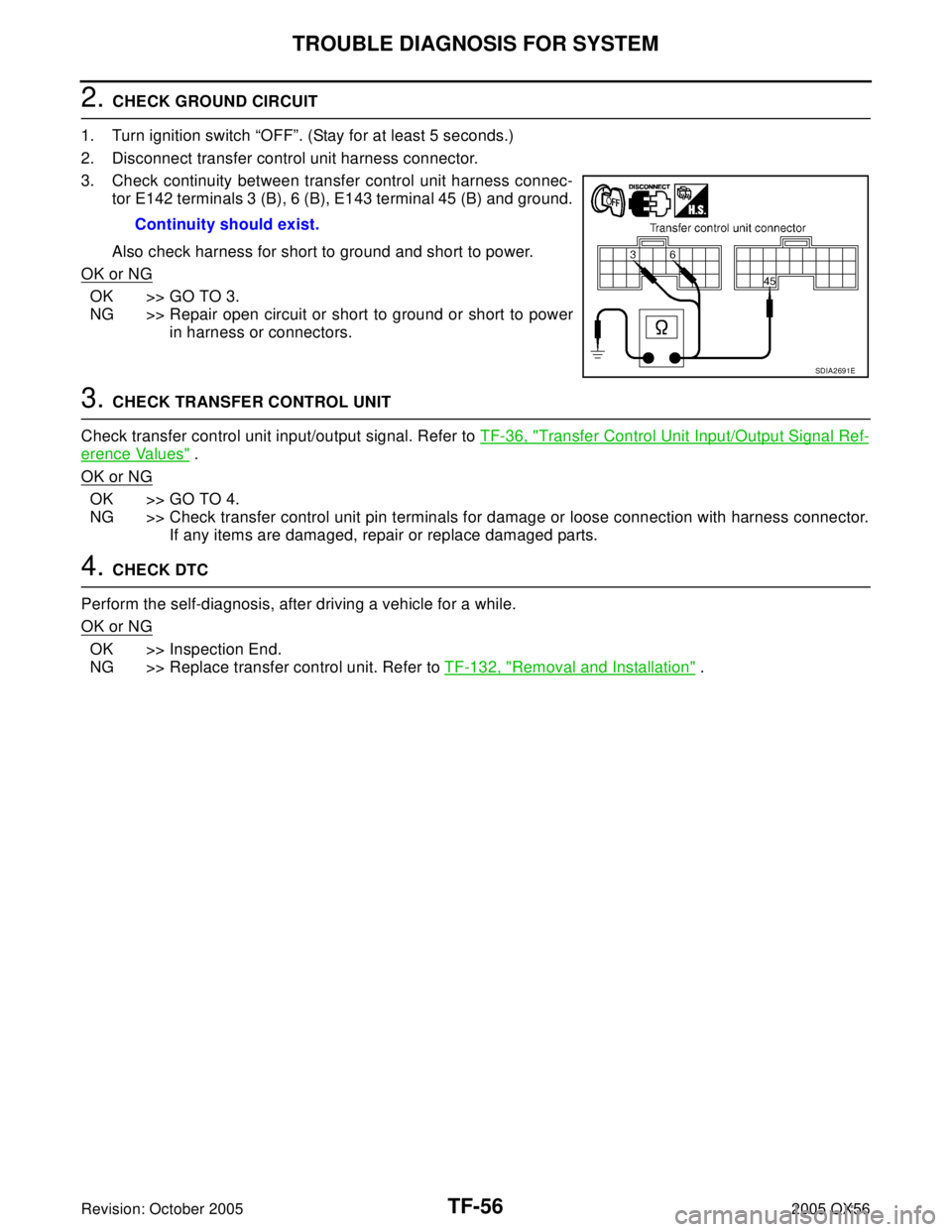
TF-56
TROUBLE DIAGNOSIS FOR SYSTEM
Revision: October 20052005 QX56
2. CHECK GROUND CIRCUIT
1. Turn ignition switch “OFF”. (Stay for at least 5 seconds.)
2. Disconnect transfer control unit harness connector.
3. Check continuity between transfer control unit harness connec-
tor E142 terminals 3 (B), 6 (B), E143 terminal 45 (B) and ground.
Also check harness for short to ground and short to power.
OK or NG
OK >> GO TO 3.
NG >> Repair open circuit or short to ground or short to power
in harness or connectors.
3. CHECK TRANSFER CONTROL UNIT
Check transfer control unit input/output signal. Refer to TF-36, "
Transfer Control Unit Input/Output Signal Ref-
erence Values" .
OK or NG
OK >> GO TO 4.
NG >> Check transfer control unit pin terminals for damage or loose connection with harness connector.
If any items are damaged, repair or replace damaged parts.
4. CHECK DTC
Perform the self-diagnosis, after driving a vehicle for a while.
OK or NG
OK >> Inspection End.
NG >> Replace transfer control unit. Refer to TF-132, "
Removal and Installation" . Continuity should exist.
SDIA2691E
Page 3200 of 3419
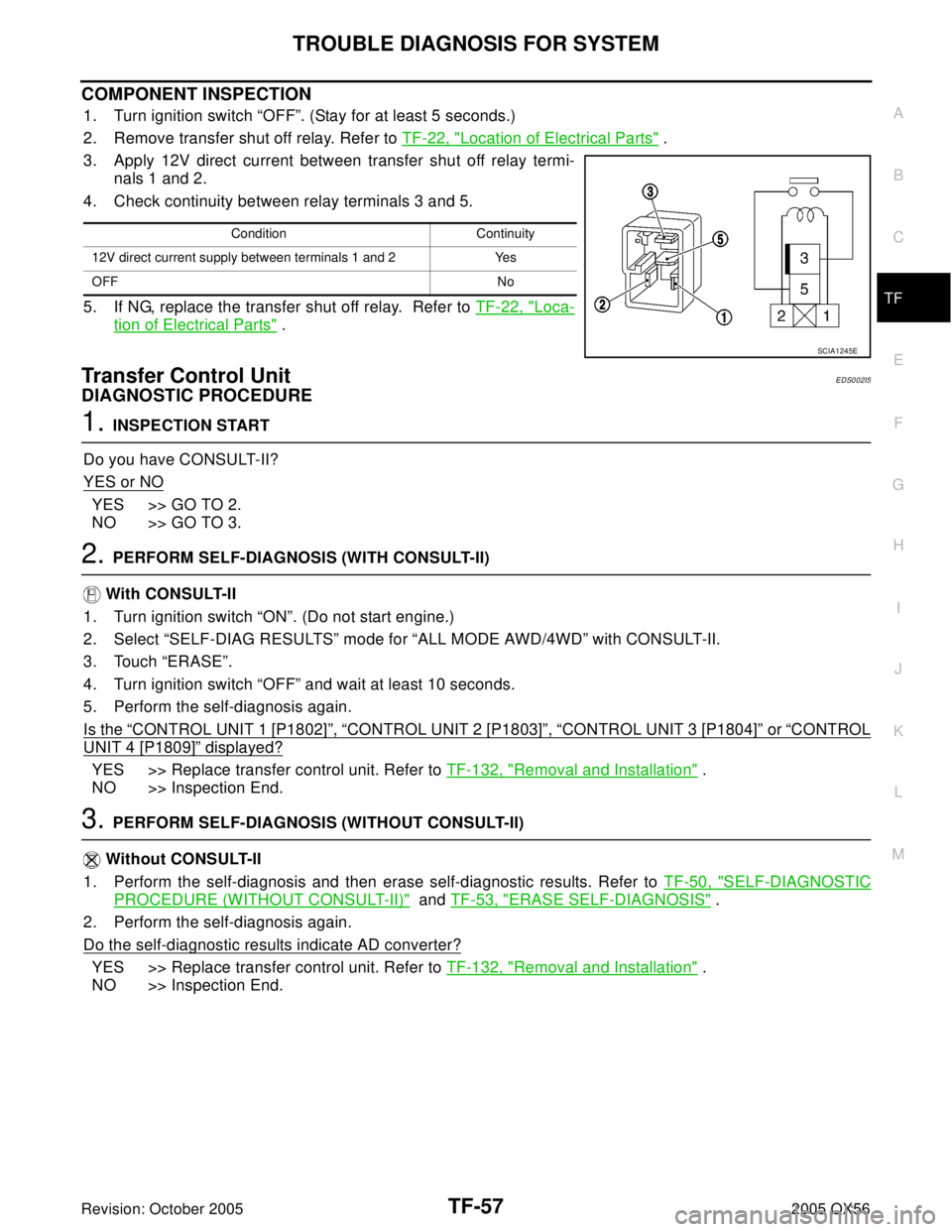
TROUBLE DIAGNOSIS FOR SYSTEM
TF-57
C
E
F
G
H
I
J
K
L
MA
B
TF
Revision: October 20052005 QX56
COMPONENT INSPECTION
1. Turn ignition switch “OFF”. (Stay for at least 5 seconds.)
2. Remove transfer shut off relay. Refer to TF-22, "
Location of Electrical Parts" .
3. Apply 12V direct current between transfer shut off relay termi-
nals 1 and 2.
4. Check continuity between relay terminals 3 and 5.
5. If NG, replace the transfer shut off relay. Refer to TF-22, "
Loca-
tion of Electrical Parts" .
Transfer Control UnitEDS002I5
DIAGNOSTIC PROCEDURE
1. INSPECTION START
Do you have CONSULT-II?
YES or NO
YES >> GO TO 2.
NO >> GO TO 3.
2. PERFORM SELF-DIAGNOSIS (WITH CONSULT-II)
With CONSULT-II
1. Turn ignition switch “ON”. (Do not start engine.)
2. Select “SELF-DIAG RESULTS” mode for “ALL MODE AWD/4WD” with CONSULT-II.
3. Touch “ERASE”.
4. Turn ignition switch “OFF” and wait at least 10 seconds.
5. Perform the self-diagnosis again.
Is the
“CONTROL UNIT 1 [P1802]”, “CONTROL UNIT 2 [P1803]”, “CONTROL UNIT 3 [P1804]” or “CONTROL
UNIT 4 [P1809]” displayed?
YES >> Replace transfer control unit. Refer to TF-132, "Removal and Installation" .
NO >> Inspection End.
3. PERFORM SELF-DIAGNOSIS (WITHOUT CONSULT-II)
Without CONSULT-II
1. Perform the self-diagnosis and then erase self-diagnostic results. Refer to TF-50, "
SELF-DIAGNOSTIC
PROCEDURE (WITHOUT CONSULT-II)" and TF-53, "ERASE SELF-DIAGNOSIS" .
2. Perform the self-diagnosis again.
Do the self-diagnostic results indicate AD converter?
YES >> Replace transfer control unit. Refer to TF-132, "Removal and Installation" .
NO >> Inspection End.
Condition Continuity
12V direct current supply between terminals 1 and 2 Yes
OFF No
SCIA1245E