Page 2801 of 3419
PS-34
SERVICE DATA AND SPECIFICATIONS (SDS)
Revision: October 20052005 QX56
Inspection After Installation
Steering Outer Socket and Inner SocketEGS000UP
Unit: mm (in) Range “A”61.3 mm (2.41 in)
Tilt mechanism range (Manual tilt) 3° per notch at 5 steps
WGIA0083E
Tie-rod ball joint outer socketSwinging torque 0.3 − 2.9 N·m (0.03 − 0.29 kg-m, 3 − 25 in-lb)
Measurement on spring balanceMeasuring point: cotter pin hole of stud4.84 − 46.7 N (0.50 − 4.7 kg, 4 − 34 lb)
Rotating torque 0.3 − 2.9 N·m (0.03 − 0.29 kg-m, 3 − 25 in-lb)
Axial end play 0.5 mm (0.020 in) or less
Tie-rod ball joint inner socketSwinging torque 1.0 − 7.8 N·m (0.11 − 0.79 kg-m, 9 − 69 in-lb)
Measurement on spring balance
Measuring point: "L" mark see above,
"L"=83.2 mm (3.276 in).12.1 − 93.7 N (1.3 − 9.5 kg, 9 − 69 lb)
Axial end play 0.2 mm (0.08 in) or less
SGIA0358E
Inner socket length “L” 115.2 (4.54)
SGIA0167E
Page 2802 of 3419
SERVICE DATA AND SPECIFICATIONS (SDS)
PS-35
C
D
E
F
H
I
J
K
L
MA
B
PS
Revision: October 20052005 QX56
Steering GearEGS0014O
Oil PumpEGS000UR
Steering FluidEGS000US
Steering gear modelPR26AM
Rack neutral position, dimension “L” (rack stroke) 85.5 mm (3.36 in)
Rack sliding forceAt the neutral point:
Range within ± 11.5 mm
(±0.453 in) from the neutral
position
(in power ON)Area average value 250.1 − 308.9 N (25.5 − 31.5 kg, 56.2 − 69.5 lb)
Area minimum value 200 N (20.4 kg, 45 lb)
Allowable variation 98 N (10 kg, 22 lb) or less
STC0034D
Relief oil pressure
9.0 − 9.8 mPa (91.77 − 99.93 kg/cm2 , 1305.34 − 1421.37 psi)
Fluid capacity
Approx. 1.0 (1-1/8 US qt, 7/8 Imp qt)
Page 2803 of 3419
PS-36
SERVICE DATA AND SPECIFICATIONS (SDS)
Revision: October 20052005 QX56
Page 2804 of 3419
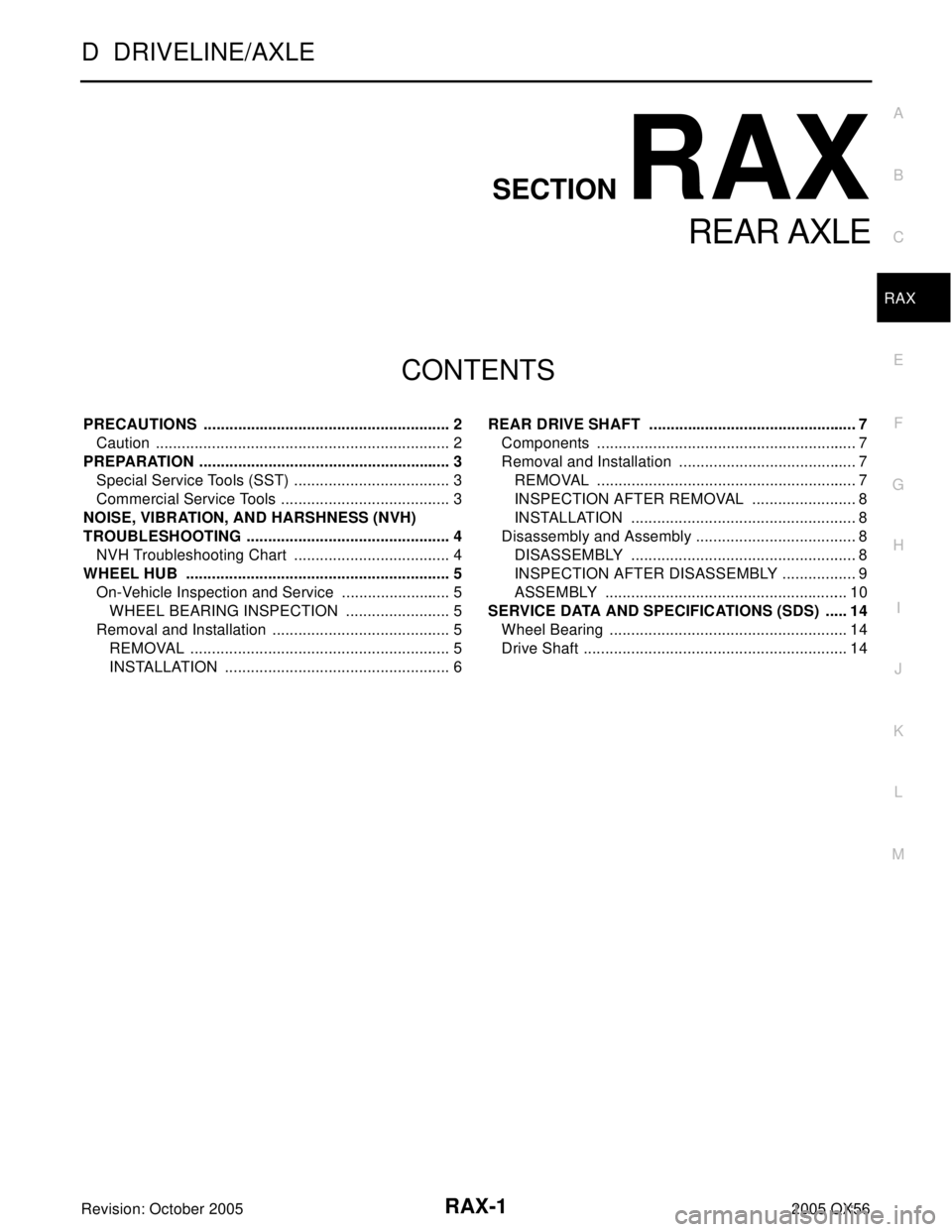
RAX-1
REAR AXLE
D DRIVELINE/AXLE
CONTENTS
C
E
F
G
H
I
J
K
L
M
SECTION RAX
A
B
RAX
Revision: October 20052005 QX56 PRECAUTIONS .......................................................... 2
Caution ..................................................................... 2
PREPARATION ........................................................... 3
Special Service Tools (SST) ..................................... 3
Commercial Service Tools ........................................ 3
NOISE, VIBRATION, AND HARSHNESS (NVH)
TROUBLESHOOTING ................................................ 4
NVH Troubleshooting Chart ..................................... 4
WHEEL HUB .............................................................. 5
On-Vehicle Inspection and Service .......................... 5
WHEEL BEARING INSPECTION ......................... 5
Removal and Installation .......................................... 5
REMOVAL ............................................................. 5
INSTALLATION ..................................................... 6REAR DRIVE SHAFT ................................................. 7
Components ............................................................. 7
Removal and Installation .......................................... 7
REMOVAL ............................................................. 7
INSPECTION AFTER REMOVAL ......................... 8
INSTALLATION ..................................................... 8
Disassembly and Assembly ...................................... 8
DISASSEMBLY ..................................................... 8
INSPECTION AFTER DISASSEMBLY .................. 9
ASSEMBLY ......................................................... 10
SERVICE DATA AND SPECIFICATIONS (SDS) ...... 14
Wheel Bearing ........................................................ 14
Drive Shaft .............................................................. 14
Page 2805 of 3419
RAX-2
PRECAUTIONS
Revision: October 20052005 QX56
PRECAUTIONSPFP:00001
CautionEDS001XJ
Observe the following precautions when disassembling and servicing drive shaft.
Perform work in a location which is as dust-free as possible.
Before disassembling and servicing, clean the outside of parts.
Prevention of the entry of foreign objects must be taken into account during disassembly of the service
location.
Disassembled parts must be carefully reassembled in the correct order. If work is interrupted, a clean
cover must be placed over parts.
Paper shop cloths must be used. Fabric shop cloths must not be used because of the danger of lint adher-
ing to parts.
Disassembled parts (except for rubber parts) should be cleaned with kerosene which shall be removed by
blowing with air or wiping with paper shop cloths.
Page 2806 of 3419
PREPARATION
RAX-3
C
E
F
G
H
I
J
K
L
MA
B
RAX
Revision: October 20052005 QX56
PREPARATIONPFP:00002
Special Service Tools (SST)EDS001XK
The actual shapes of the Kent-Moore tools may differ from those of the special service tools illustrated here.
Commercial Service ToolsEDS001XL
Tool number
(Kent-Moore No.)
Tool nameDescription
KV38100500
(—)
DriftInstalling drive shaft plug
a: 80 mm (3.15 in) dia.
b: 60 mm (2.36 in) dia.
KV38102200
(—)
DriftInstalling drive shaft plug
a: 90 mm (3.54 in) dia.
b: 31 mm (1.22 in) dia.
ZZA0701D
ZZA0920D
Tool nameDescription
Power toolsRemoving bolts and nuts
PBIC0190E
Page 2807 of 3419
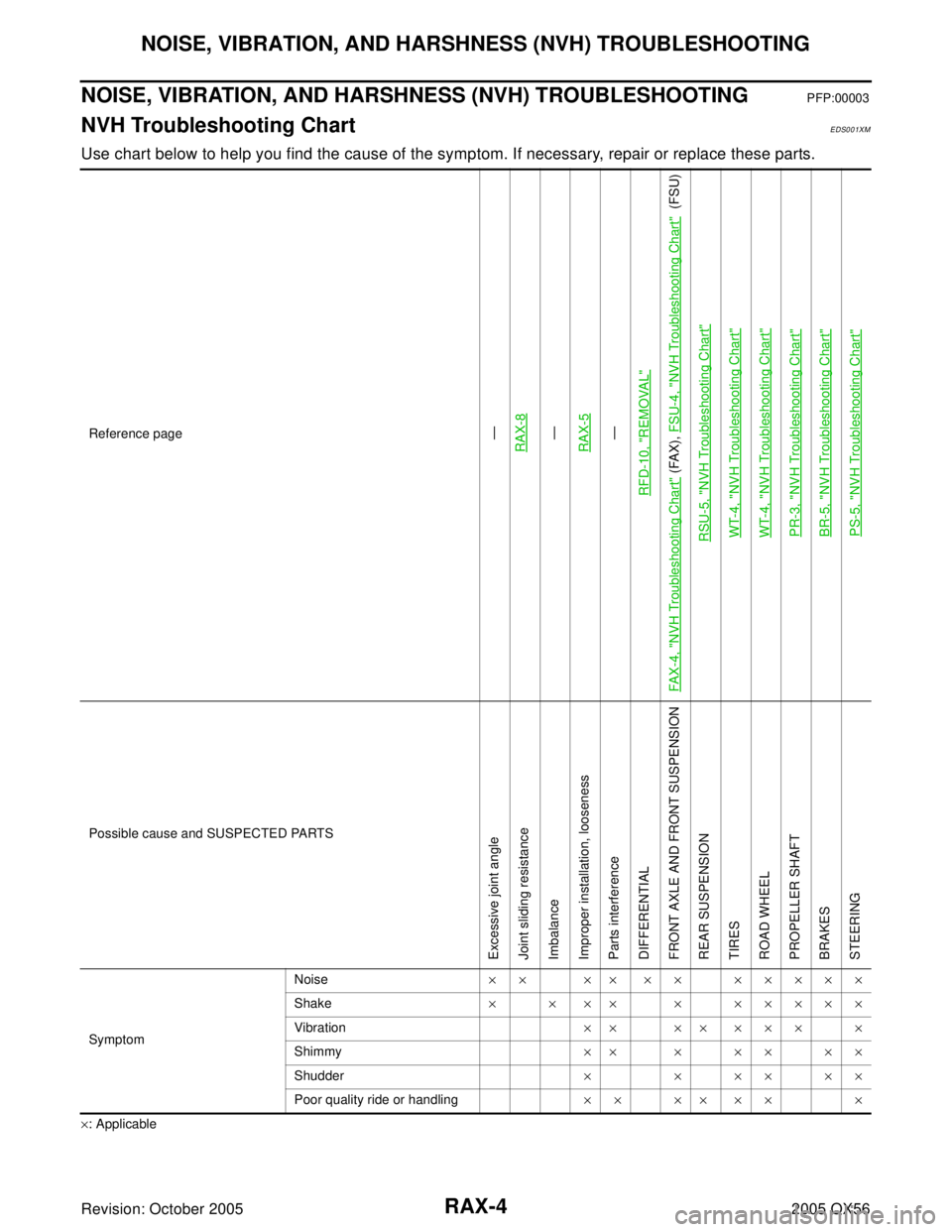
RAX-4
NOISE, VIBRATION, AND HARSHNESS (NVH) TROUBLESHOOTING
Revision: October 20052005 QX56
NOISE, VIBRATION, AND HARSHNESS (NVH) TROUBLESHOOTINGPFP:00003
NVH Troubleshooting ChartEDS001XM
Use chart below to help you find the cause of the symptom. If necessary, repair or replace these parts.
×: ApplicableReference page
—
RAX-8—
RAX-5—
RFD-10, "REMOVAL
"
FAX -4, "
NVH Troubleshooting Chart
" (FAX), FSU-4, "
NVH Troubleshooting Chart
" (FSU)
RSU-5, "
NVH Troubleshooting Chart
"
WT-4, "
NVH Troubleshooting Chart
"
WT-4, "
NVH Troubleshooting Chart
"
PR-3, "
NVH Troubleshooting Chart
"
BR-5, "
NVH Troubleshooting Chart
"
PS-5, "
NVH Troubleshooting Chart
"
Possible cause and SUSPECTED PARTS
Excessive joint angle
Joint sliding resistance
Imbalance
Improper installation, looseness
Parts interference
DIFFERENTIAL
FRONT AXLE AND FRONT SUSPENSION
REAR SUSPENSION
TIRES
ROAD WHEEL
PROPELLER SHAFT
BRAKES
STEERING
SymptomNoise×× ×× ×× ×××××
Shake× × ×× × ×××××
Vibration×× ×× × × × ×
Shimmy×× ×××××
Shudder× × ×× ××
Poor quality ride or handling×× ×× ×× ×
Page 2808 of 3419
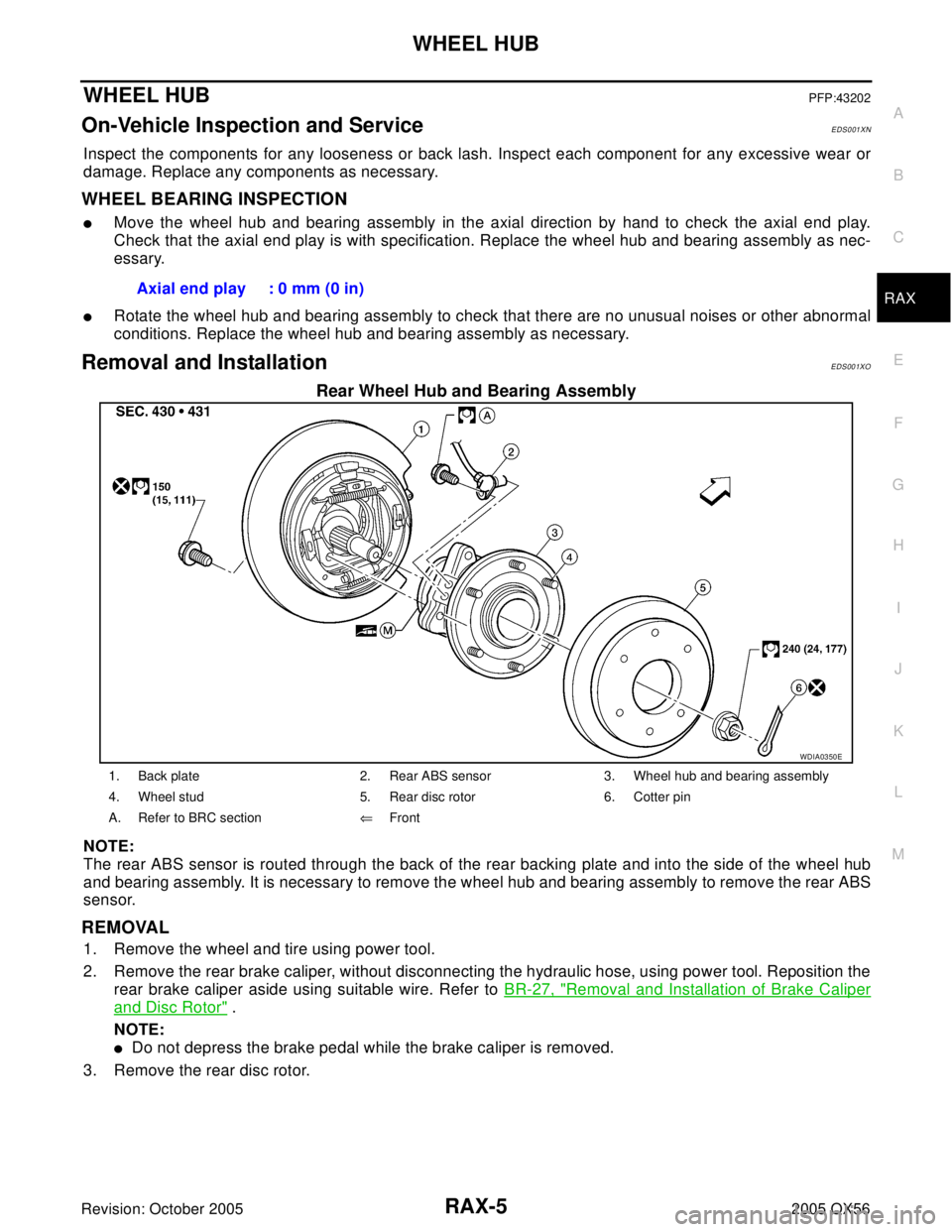
WHEEL HUB
RAX-5
C
E
F
G
H
I
J
K
L
MA
B
RAX
Revision: October 20052005 QX56
WHEEL HUBPFP:43202
On-Vehicle Inspection and ServiceEDS001XN
Inspect the components for any looseness or back lash. Inspect each component for any excessive wear or
damage. Replace any components as necessary.
WHEEL BEARING INSPECTION
Move the wheel hub and bearing assembly in the axial direction by hand to check the axial end play.
Check that the axial end play is with specification. Replace the wheel hub and bearing assembly as nec-
essary.
Rotate the wheel hub and bearing assembly to check that there are no unusual noises or other abnormal
conditions. Replace the wheel hub and bearing assembly as necessary.
Removal and InstallationEDS001XO
Rear Wheel Hub and Bearing Assembly
NOTE:
The rear ABS sensor is routed through the back of the rear backing plate and into the side of the wheel hub
and bearing assembly. It is necessary to remove the wheel hub and bearing assembly to remove the rear ABS
sensor.
REMOVAL
1. Remove the wheel and tire using power tool.
2. Remove the rear brake caliper, without disconnecting the hydraulic hose, using power tool. Reposition the
rear brake caliper aside using suitable wire. Refer to BR-27, "
Removal and Installation of Brake Caliper
and Disc Rotor" .
NOTE:
Do not depress the brake pedal while the brake caliper is removed.
3. Remove the rear disc rotor.Axial end play : 0 mm (0 in)
WDIA0350E
1. Back plate 2. Rear ABS sensor 3. Wheel hub and bearing assembly
4. Wheel stud 5. Rear disc rotor 6. Cotter pin
A. Refer to BRC section⇐Front