Page 953 of 3419
BL-186
BODY REPAIR
Revision: October 20052005 QX56
MEASUREMENT POINTS
WIIA0280E
Page 954 of 3419
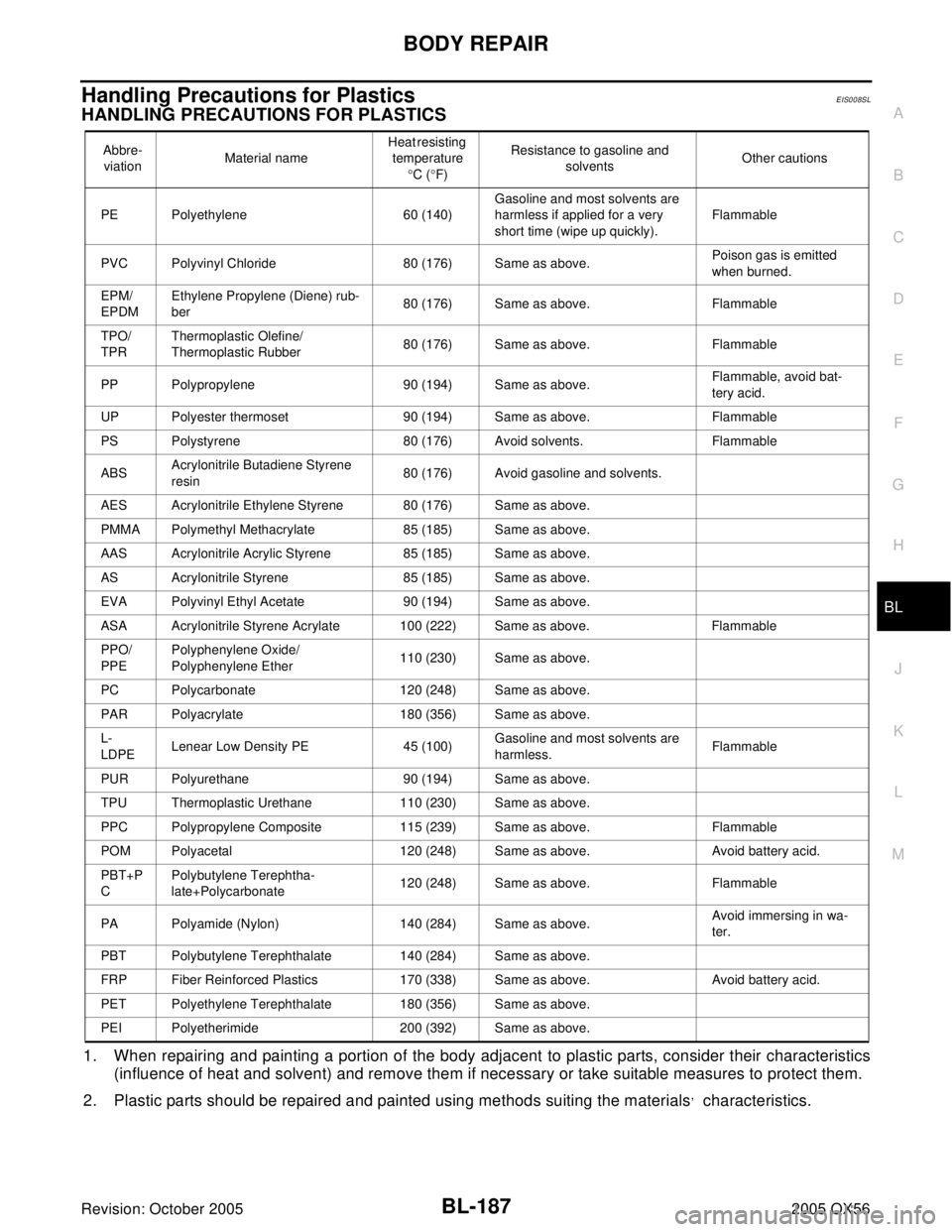
BODY REPAIR
BL-187
C
D
E
F
G
H
J
K
L
MA
B
BL
Revision: October 20052005 QX56
Handling Precautions for PlasticsEIS008SL
HANDLING PRECAUTIONS FOR PLASTICS
1. When repairing and painting a portion of the body adjacent to plastic parts, consider their characteristics
(influence of heat and solvent) and remove them if necessary or take suitable measures to protect them.
2. Plastic parts should be repaired and painted using methods suiting the materials
, characteristics.
Abbre-
viationMaterial nameHeat resisting
temperature
°C (°F)Resistance to gasoline and
solventsOther cautions
PE Polyethylene 60 (140)Gasoline and most solvents are
harmless if applied for a very
short time (wipe up quickly).Flammable
PVC Polyvinyl Chloride 80 (176) Same as above.Poison gas is emitted
when burned.
EPM/
EPDMEthylene Propylene (Diene) rub-
ber80 (176) Same as above. Flammable
TPO/
TPRThermoplastic Olefine/
Thermoplastic Rubber80 (176) Same as above. Flammable
PP Polypropylene 90 (194) Same as above.Flammable, avoid bat-
tery acid.
UP Polyester thermoset 90 (194) Same as above. Flammable
PS Polystyrene 80 (176) Avoid solvents. Flammable
ABSAcrylonitrile Butadiene Styrene
resin80 (176) Avoid gasoline and solvents.
AES Acrylonitrile Ethylene Styrene 80 (176) Same as above.
PMMA Polymethyl Methacrylate 85 (185) Same as above.
AAS Acrylonitrile Acrylic Styrene 85 (185) Same as above.
AS Acrylonitrile Styrene 85 (185) Same as above.
EVA Polyvinyl Ethyl Acetate 90 (194) Same as above.
ASA Acrylonitrile Styrene Acrylate 100 (222) Same as above. Flammable
PPO/
PPEPolyphenylene Oxide/
Polyphenylene Ether110 (230) Same as above.
PC Polycarbonate 120 (248) Same as above.
PAR Polyacrylate 180 (356) Same as above.
L-
LDPELenear Low Density PE 45 (100)Gasoline and most solvents are
harmless.Flammable
PUR Polyurethane 90 (194) Same as above.
TPU Thermoplastic Urethane 110 (230) Same as above.
PPC Polypropylene Composite 115 (239) Same as above. Flammable
POM Polyacetal 120 (248) Same as above. Avoid battery acid.
PBT+P
CPolybutylene Terephtha-
late+Polycarbonate120 (248) Same as above. Flammable
PA Polyamide (Nylon) 140 (284) Same as above.Avoid immersing in wa-
ter.
PBT Polybutylene Terephthalate 140 (284) Same as above.
FRP Fiber Reinforced Plastics 170 (338) Same as above. Avoid battery acid.
PET Polyethylene Terephthalate 180 (356) Same as above.
PEI Polyetherimide 200 (392) Same as above.
Page 955 of 3419
BL-188
BODY REPAIR
Revision: October 20052005 QX56
LOCATION OF PLASTIC PARTS
LIIA1441E
Page 956 of 3419
BODY REPAIR
BL-189
C
D
E
F
G
H
J
K
L
MA
B
BL
Revision: October 20052005 QX56LIIA1061E
Page 957 of 3419
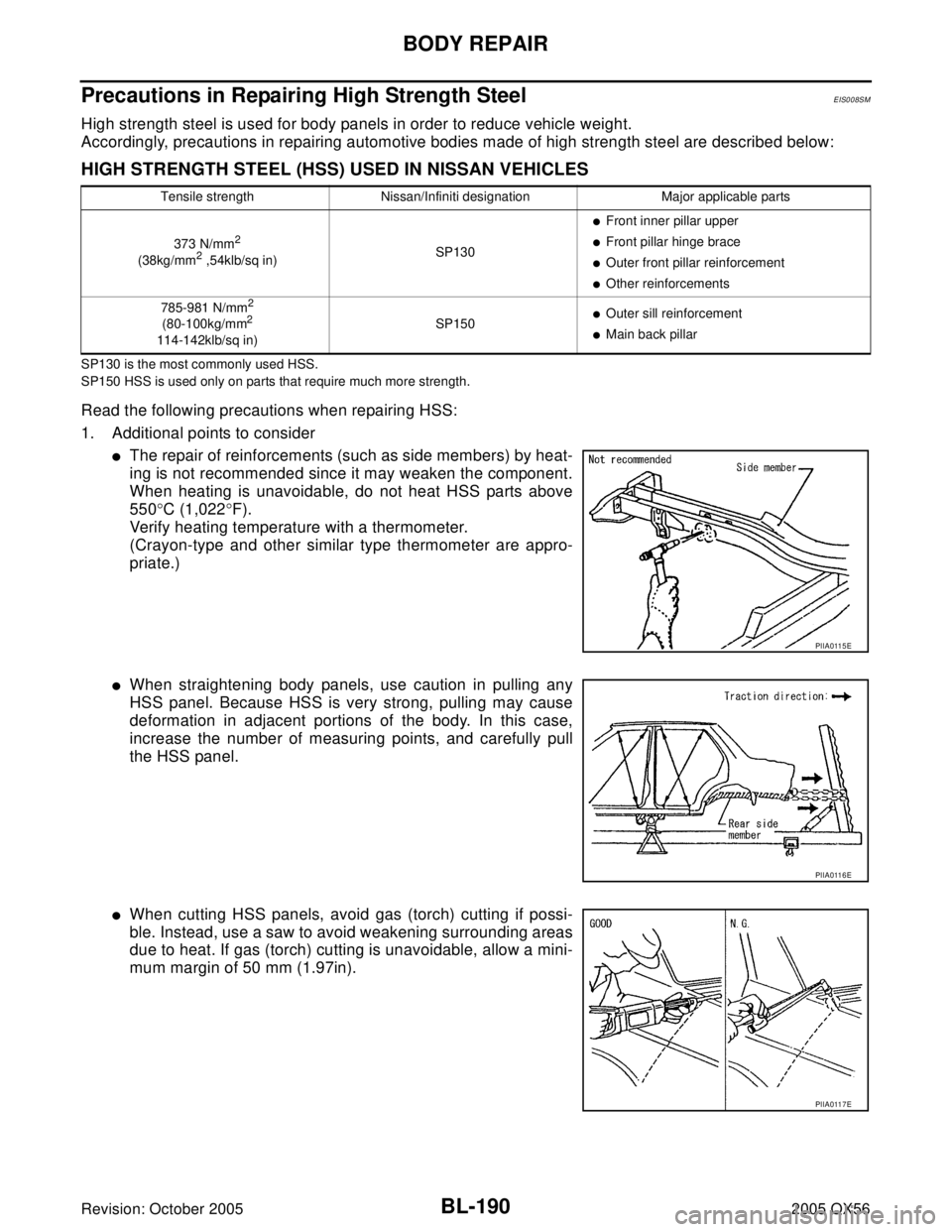
BL-190
BODY REPAIR
Revision: October 20052005 QX56
Precautions in Repairing High Strength SteelEIS008SM
High strength steel is used for body panels in order to reduce vehicle weight.
Accordingly, precautions in repairing automotive bodies made of high strength steel are described below:
HIGH STRENGTH STEEL (HSS) USED IN NISSAN VEHICLES
SP130 is the most commonly used HSS.
SP150 HSS is used only on parts that require much more strength.
Read the following precautions when repairing HSS:
1. Additional points to consider
The repair of reinforcements (such as side members) by heat-
ing is not recommended since it may weaken the component.
When heating is unavoidable, do not heat HSS parts above
550°C (1,022°F).
Verify heating temperature with a thermometer.
(Crayon-type and other similar type thermometer are appro-
priate.)
When straightening body panels, use caution in pulling any
HSS panel. Because HSS is very strong, pulling may cause
deformation in adjacent portions of the body. In this case,
increase the number of measuring points, and carefully pull
the HSS panel.
When cutting HSS panels, avoid gas (torch) cutting if possi-
ble. Instead, use a saw to avoid weakening surrounding areas
due to heat. If gas (torch) cutting is unavoidable, allow a mini-
mum margin of 50 mm (1.97in).
Tensile strength Nissan/Infiniti designation Major applicable parts
373 N/mm
2
(38kg/mm2 ,54klb/sq in)SP130
Front inner pillar upper
Front pillar hinge brace
Outer front pillar reinforcement
Other reinforcements
785-981 N/mm
2
(80-100kg/mm2
114-142klb/sq in)SP150
Outer sill reinforcement
Main back pillar
PIIA0115E
PIIA0116E
PIIA0117E
Page 958 of 3419
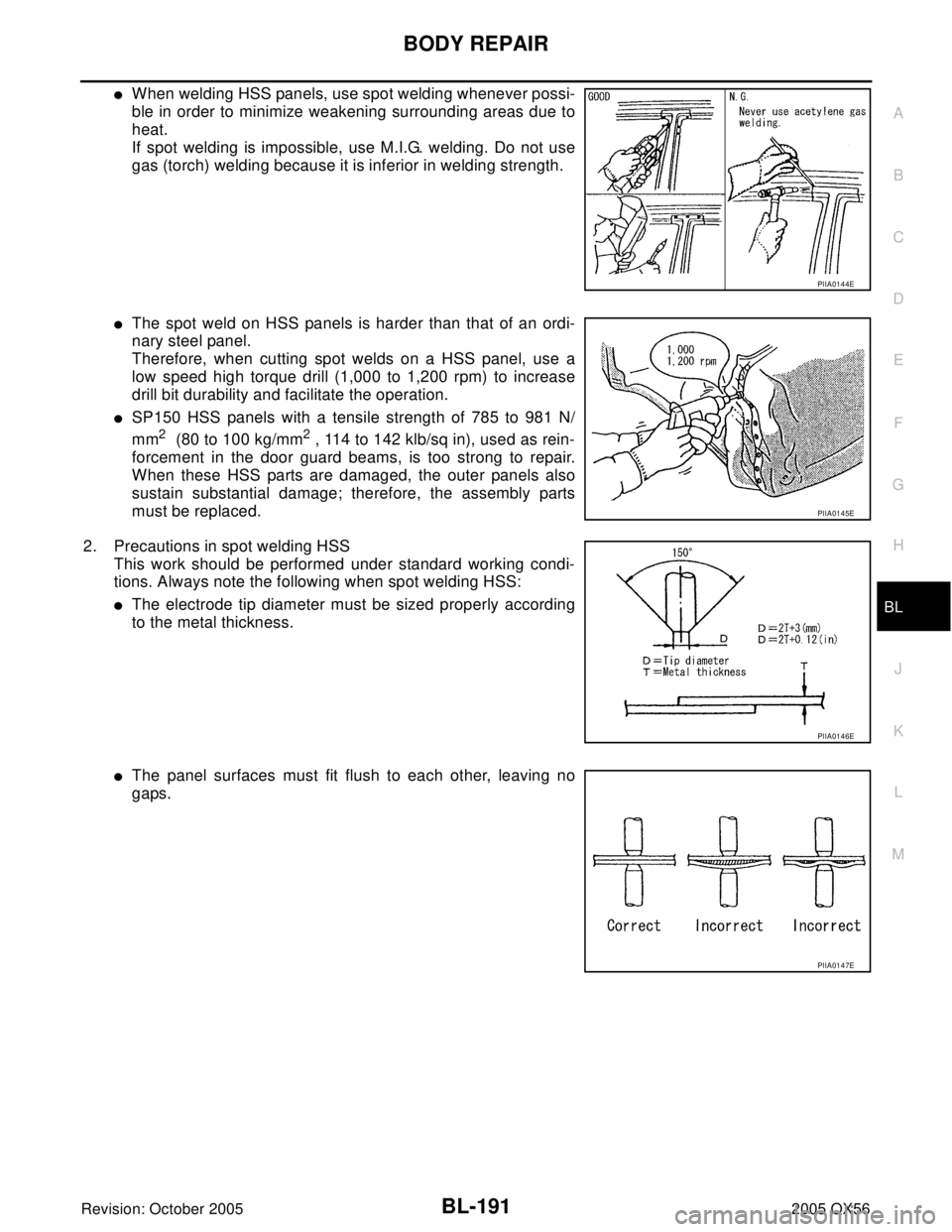
BODY REPAIR
BL-191
C
D
E
F
G
H
J
K
L
MA
B
BL
Revision: October 20052005 QX56
When welding HSS panels, use spot welding whenever possi-
ble in order to minimize weakening surrounding areas due to
heat.
If spot welding is impossible, use M.I.G. welding. Do not use
gas (torch) welding because it is inferior in welding strength.
The spot weld on HSS panels is harder than that of an ordi-
nary steel panel.
Therefore, when cutting spot welds on a HSS panel, use a
low speed high torque drill (1,000 to 1,200 rpm) to increase
drill bit durability and facilitate the operation.
SP150 HSS panels with a tensile strength of 785 to 981 N/
mm
2 (80 to 100 kg/mm2 , 114 to 142 klb/sq in), used as rein-
forcement in the door guard beams, is too strong to repair.
When these HSS parts are damaged, the outer panels also
sustain substantial damage; therefore, the assembly parts
must be replaced.
2. Precautions in spot welding HSS
This work should be performed under standard working condi-
tions. Always note the following when spot welding HSS:
The electrode tip diameter must be sized properly according
to the metal thickness.
The panel surfaces must fit flush to each other, leaving no
gaps.
PIIA0144E
PIIA0145E
PIIA0146E
PIIA0147E
Page 959 of 3419
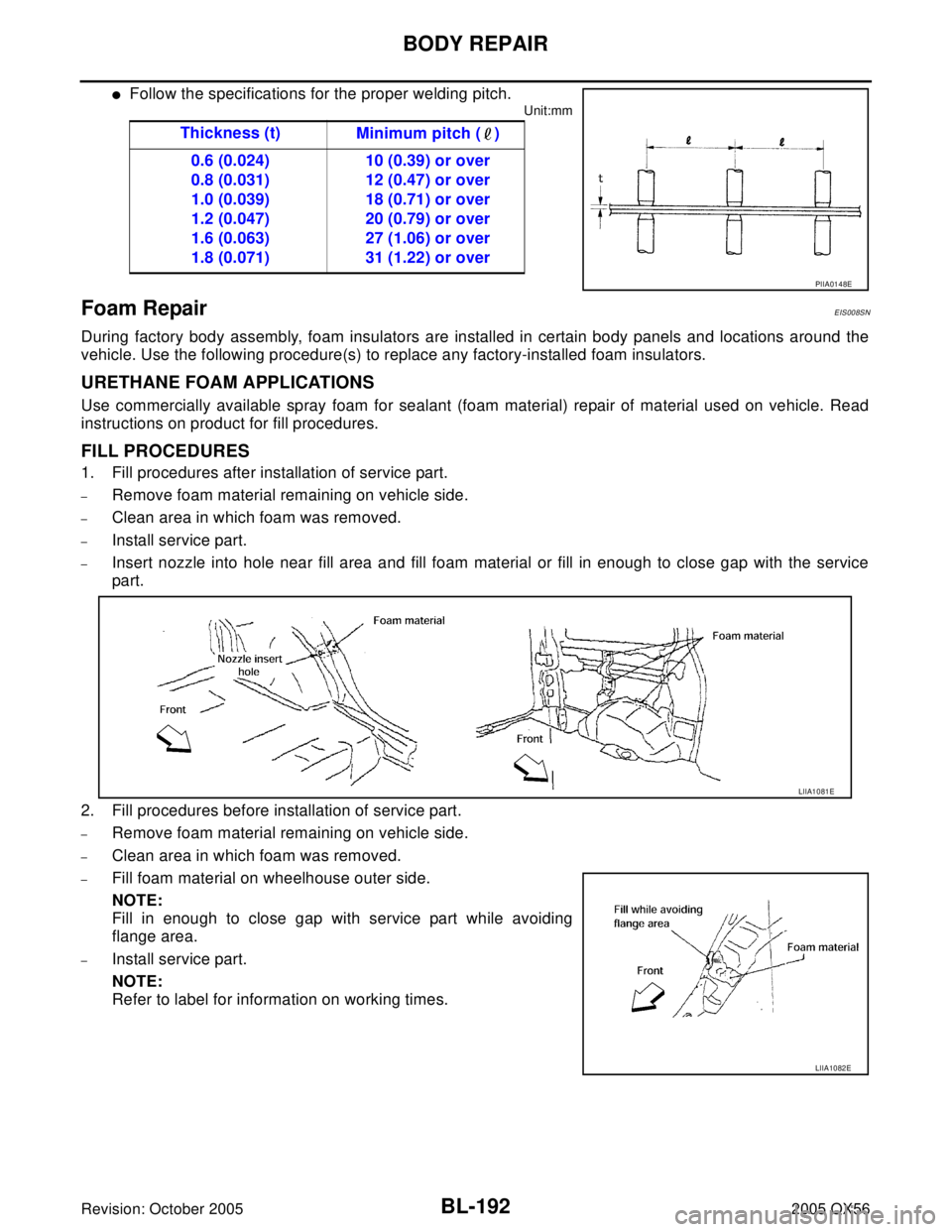
BL-192
BODY REPAIR
Revision: October 20052005 QX56
Follow the specifications for the proper welding pitch.
Unit:mm
Foam RepairEIS008SN
During factory body assembly, foam insulators are installed in certain body panels and locations around the
vehicle. Use the following procedure(s) to replace any factory-installed foam insulators.
URETHANE FOAM APPLICATIONS
Use commercially available spray foam for sealant (foam material) repair of material used on vehicle. Read
instructions on product for fill procedures.
FILL PROCEDURES
1. Fill procedures after installation of service part.
–Remove foam material remaining on vehicle side.
–Clean area in which foam was removed.
–Install service part.
–Insert nozzle into hole near fill area and fill foam material or fill in enough to close gap with the service
part.
2. Fill procedures before installation of service part.
–Remove foam material remaining on vehicle side.
–Clean area in which foam was removed.
–Fill foam material on wheelhouse outer side.
NOTE:
Fill in enough to close gap with service part while avoiding
flange area.
–Install service part.
NOTE:
Refer to label for information on working times.Thickness (t)
Minimum pitch ( )
0.6 (0.024)
0.8 (0.031)
1.0 (0.039)
1.2 (0.047)
1.6 (0.063)
1.8 (0.071)10 (0.39) or over
12 (0.47) or over
18 (0.71) or over
20 (0.79) or over
27 (1.06) or over
31 (1.22) or over
PIIA0148E
LIIA1081E
LIIA1082E
Page 960 of 3419
BODY REPAIR
BL-193
C
D
E
F
G
H
J
K
L
MA
B
BL
Revision: October 20052005 QX56
Replacement OperationsEIS008SO
DESCRIPTION
This section is prepared for technicians who have attained a high level of skill and experience in repairing col-
lision-damaged vehicles and also use modern service tools and equipment. Persons unfamiliar with body
repair techniques should not attempt to repair collision-damaged vehicles by using this section.
Technicians are also encouraged to read Body Repair Manual (Fundamentals) in order to ensure that the orig-
inal functions and quality of the vehicle can be maintained. The Body Repair Manual (Fundamentals) contains
additional information, including cautions and warnings, that are not including in this manual. Technicians
should refer to both manuals to ensure proper repairs.
Please note that this information is prepared for worldwide usage, and as such, certain procedures may not
apply in some regions or countries.