Page 3217 of 3419
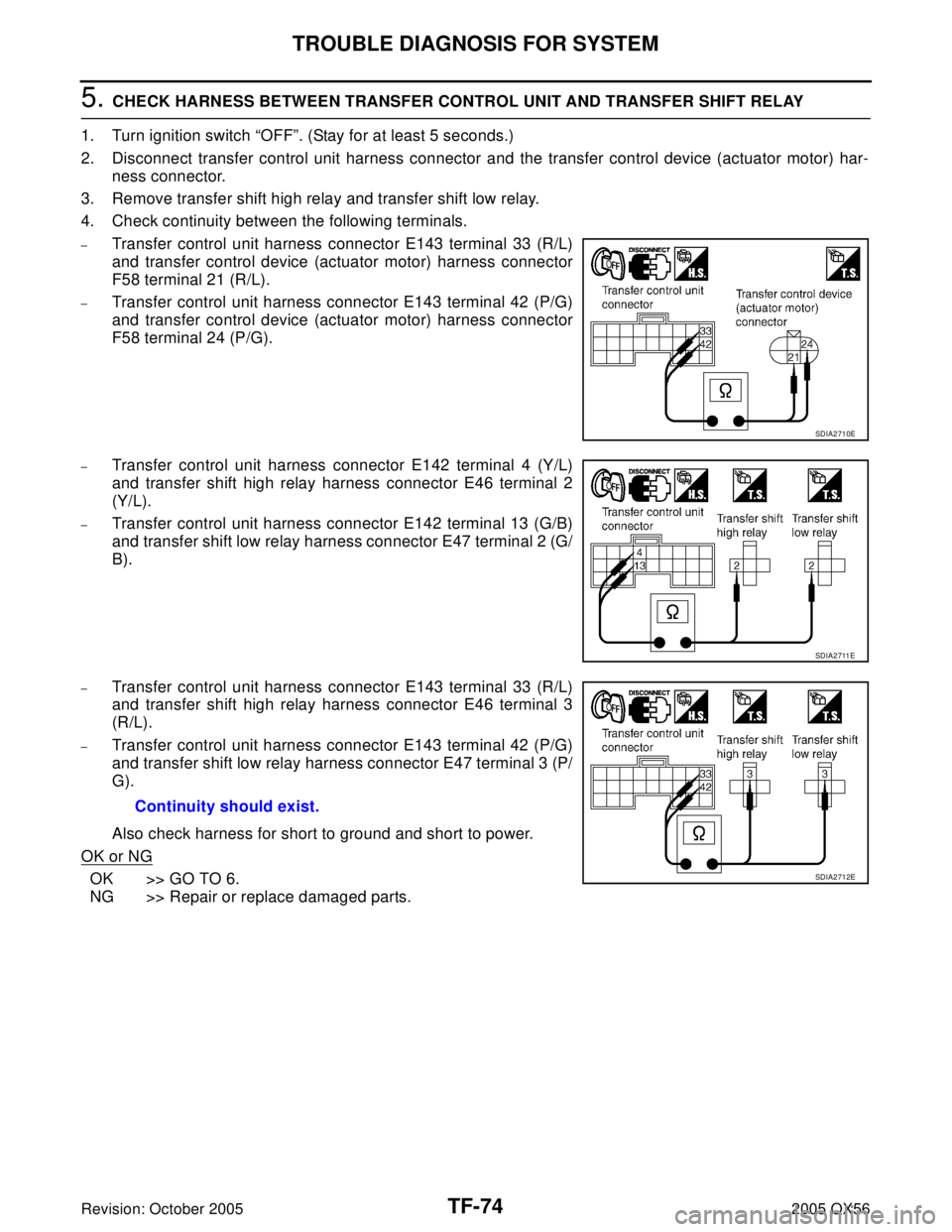
TF-74
TROUBLE DIAGNOSIS FOR SYSTEM
Revision: October 20052005 QX56
5. CHECK HARNESS BETWEEN TRANSFER CONTROL UNIT AND TRANSFER SHIFT RELAY
1. Turn ignition switch “OFF”. (Stay for at least 5 seconds.)
2. Disconnect transfer control unit harness connector and the transfer control device (actuator motor) har-
ness connector.
3. Remove transfer shift high relay and transfer shift low relay.
4. Check continuity between the following terminals.
–Transfer control unit harness connector E143 terminal 33 (R/L)
and transfer control device (actuator motor) harness connector
F58 terminal 21 (R/L).
–Transfer control unit harness connector E143 terminal 42 (P/G)
and transfer control device (actuator motor) harness connector
F58 terminal 24 (P/G).
–Transfer control unit harness connector E142 terminal 4 (Y/L)
and transfer shift high relay harness connector E46 terminal 2
(Y/L).
–Transfer control unit harness connector E142 terminal 13 (G/B)
and transfer shift low relay harness connector E47 terminal 2 (G/
B).
–Transfer control unit harness connector E143 terminal 33 (R/L)
and transfer shift high relay harness connector E46 terminal 3
(R/L).
–Transfer control unit harness connector E143 terminal 42 (P/G)
and transfer shift low relay harness connector E47 terminal 3 (P/
G).
Also check harness for short to ground and short to power.
OK or NG
OK >> GO TO 6.
NG >> Repair or replace damaged parts.
SDIA2710E
SDIA2 711 E
Continuity should exist.
SDIA2712E
Page 3218 of 3419
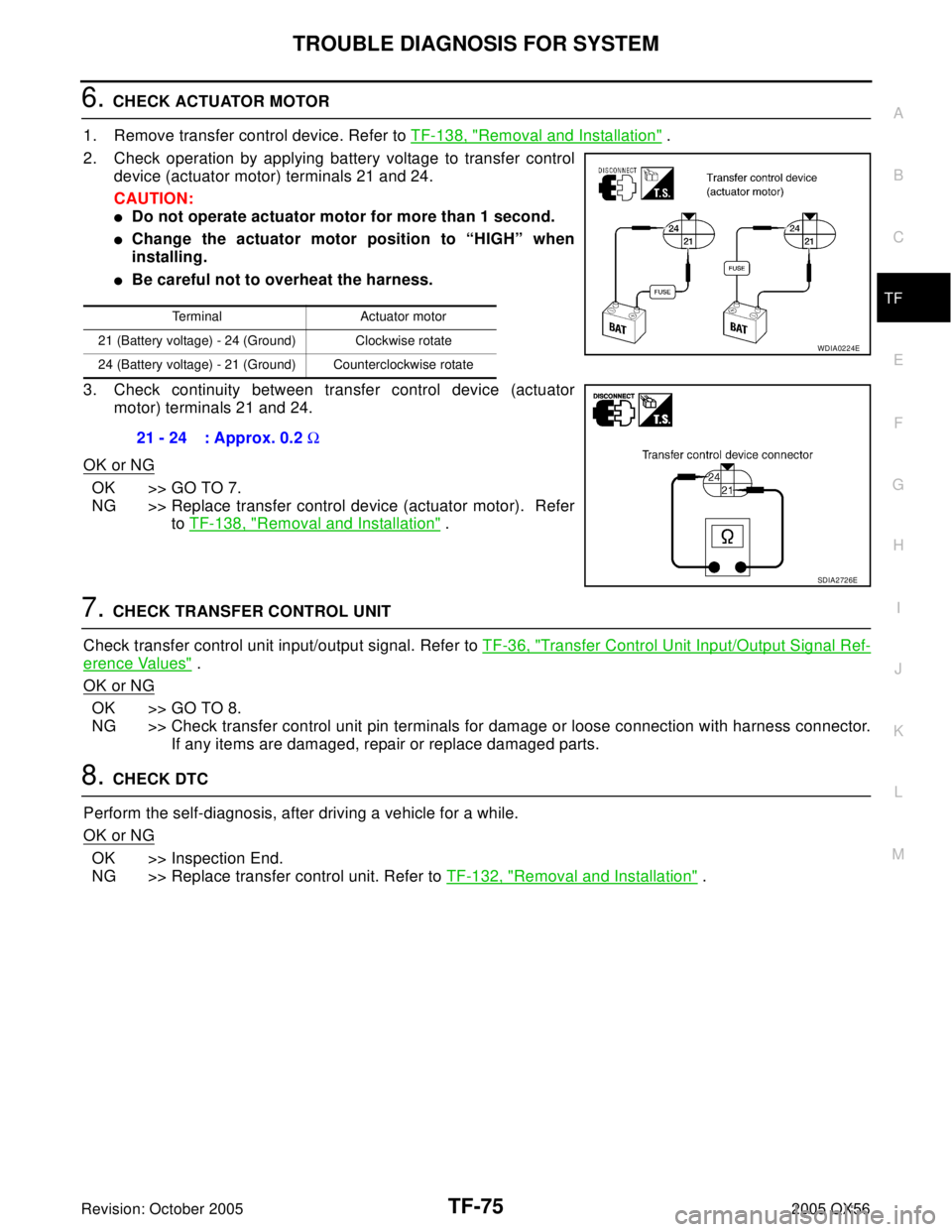
TROUBLE DIAGNOSIS FOR SYSTEM
TF-75
C
E
F
G
H
I
J
K
L
MA
B
TF
Revision: October 20052005 QX56
6. CHECK ACTUATOR MOTOR
1. Remove transfer control device. Refer to TF-138, "
Removal and Installation" .
2. Check operation by applying battery voltage to transfer control
device (actuator motor) terminals 21 and 24.
CAUTION:
Do not operate actuator motor for more than 1 second.
Change the actuator motor position to “HIGH” when
installing.
Be careful not to overheat the harness.
3. Check continuity between transfer control device (actuator
motor) terminals 21 and 24.
OK or NG
OK >> GO TO 7.
NG >> Replace transfer control device (actuator motor). Refer
to TF-138, "
Removal and Installation" .
7. CHECK TRANSFER CONTROL UNIT
Check transfer control unit input/output signal. Refer to TF-36, "
Transfer Control Unit Input/Output Signal Ref-
erence Values" .
OK or NG
OK >> GO TO 8.
NG >> Check transfer control unit pin terminals for damage or loose connection with harness connector.
If any items are damaged, repair or replace damaged parts.
8. CHECK DTC
Perform the self-diagnosis, after driving a vehicle for a while.
OK or NG
OK >> Inspection End.
NG >> Replace transfer control unit. Refer to TF-132, "
Removal and Installation" .
Terminal Actuator motor
21 (Battery voltage) - 24 (Ground) Clockwise rotate
24 (Battery voltage) - 21 (Ground) Counterclockwise rotate
21 - 24 : Approx. 0.2 Ω
WDIA0224E
SDIA2726E
Page 3219 of 3419
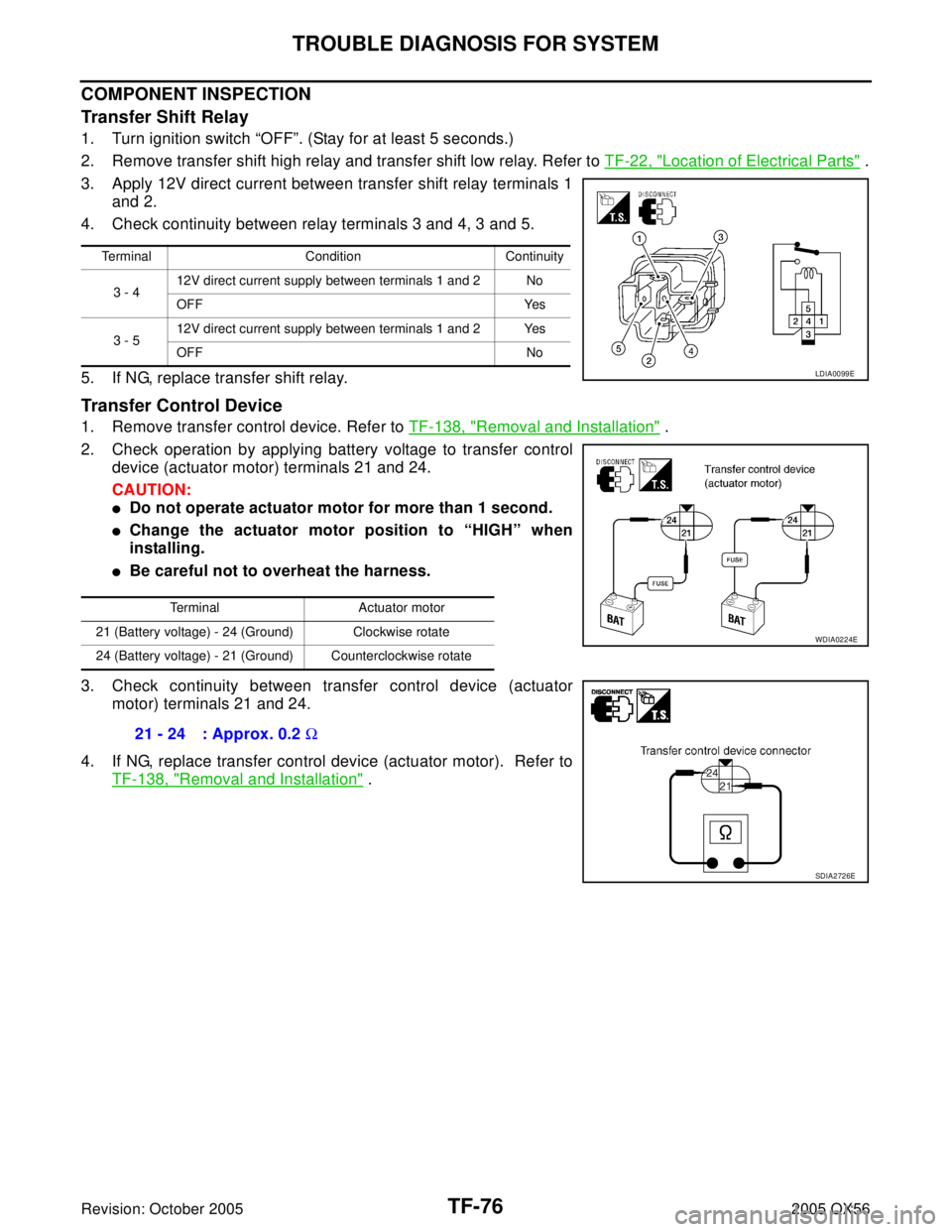
TF-76
TROUBLE DIAGNOSIS FOR SYSTEM
Revision: October 20052005 QX56
COMPONENT INSPECTION
Transfer Shift Relay
1. Turn ignition switch “OFF”. (Stay for at least 5 seconds.)
2. Remove transfer shift high relay and transfer shift low relay. Refer to TF-22, "
Location of Electrical Parts" .
3. Apply 12V direct current between transfer shift relay terminals 1
and 2.
4. Check continuity between relay terminals 3 and 4, 3 and 5.
5. If NG, replace transfer shift relay.
Transfer Control Device
1. Remove transfer control device. Refer to TF-138, "Removal and Installation" .
2. Check operation by applying battery voltage to transfer control
device (actuator motor) terminals 21 and 24.
CAUTION:
Do not operate actuator motor for more than 1 second.
Change the actuator motor position to “HIGH” when
installing.
Be careful not to overheat the harness.
3. Check continuity between transfer control device (actuator
motor) terminals 21 and 24.
4. If NG, replace transfer control device (actuator motor). Refer to
TF-138, "
Removal and Installation" .
Terminal Condition Continuity
3 - 412V direct current supply between terminals 1 and 2 No
OFF Yes
3 - 512V direct current supply between terminals 1 and 2 Yes
OFF No
LDIA0099E
Terminal Actuator motor
21 (Battery voltage) - 24 (Ground) Clockwise rotate
24 (Battery voltage) - 21 (Ground) Counterclockwise rotate
21 - 24 : Approx. 0.2 Ω
WDIA0224E
SDIA2726E
Page 3220 of 3419
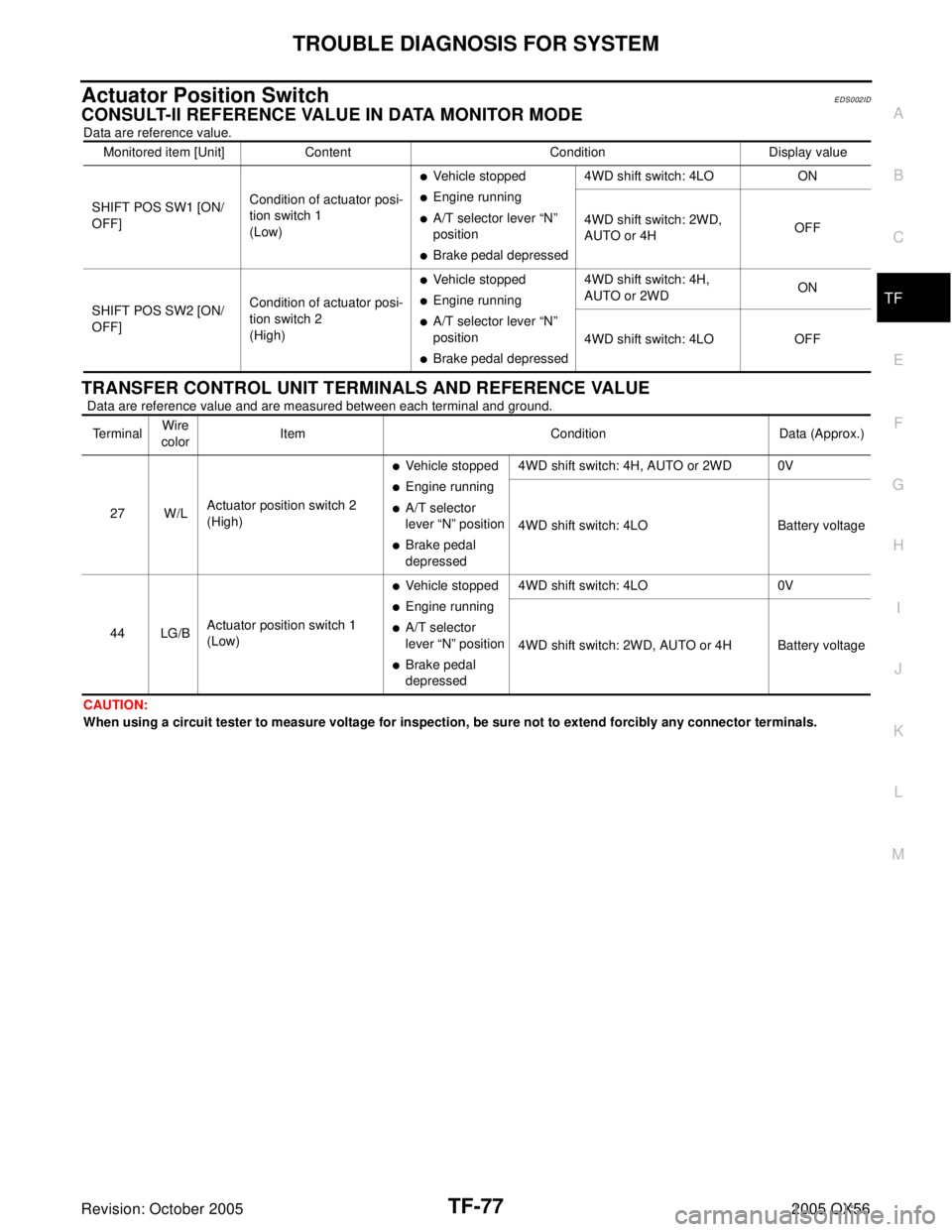
TROUBLE DIAGNOSIS FOR SYSTEM
TF-77
C
E
F
G
H
I
J
K
L
MA
B
TF
Revision: October 20052005 QX56
Actuator Position SwitchEDS002ID
CONSULT-II REFERENCE VALUE IN DATA MONITOR MODE
Data are reference value.
TRANSFER CONTROL UNIT TERMINALS AND REFERENCE VALUE
Data are reference value and are measured between each terminal and ground.
CAUTION:
When using a circuit tester to measure voltage for inspection, be sure not to extend forcibly any connector terminals.Monitored item [Unit] Content Condition Display value
SHIFT POS SW1 [ON/
OFF]Condition of actuator posi-
tion switch 1
(Low)
Vehicle stopped
Engine running
A/T selector lever “N”
position
Brake pedal depressed4WD shift switch: 4LO ON
4WD shift switch: 2WD,
AUTO or 4HOFF
SHIFT POS SW2 [ON/
OFF]Condition of actuator posi-
tion switch 2
(High)
Vehicle stopped
Engine running
A/T selector lever “N”
position
Brake pedal depressed4WD shift switch: 4H,
AUTO or 2WDON
4WD shift switch: 4LO OFF
Te r m i n a lWire
colorItem Condition Data (Approx.)
27 W/LActuator position switch 2
(High)
Vehicle stopped
Engine running
A/T selector
lever “N” position
Brake pedal
depressed4WD shift switch: 4H, AUTO or 2WD 0V
4WD shift switch: 4LO Battery voltage
44 LG/BActuator position switch 1
(Low)
Vehicle stopped
Engine running
A/T selector
lever “N” position
Brake pedal
depressed4WD shift switch: 4LO 0V
4WD shift switch: 2WD, AUTO or 4H Battery voltage
Page 3221 of 3419
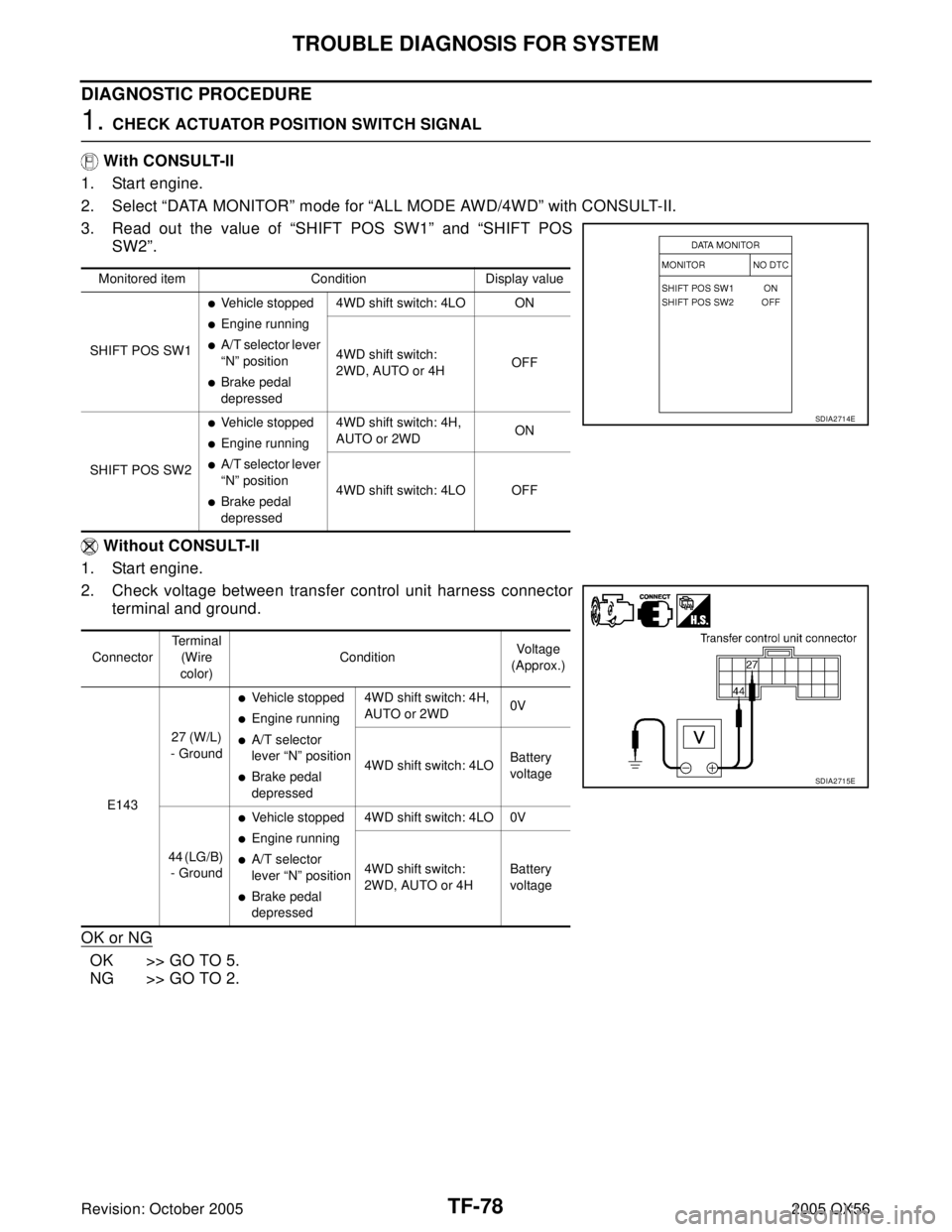
TF-78
TROUBLE DIAGNOSIS FOR SYSTEM
Revision: October 20052005 QX56
DIAGNOSTIC PROCEDURE
1. CHECK ACTUATOR POSITION SWITCH SIGNAL
With CONSULT-II
1. Start engine.
2. Select “DATA MONITOR” mode for “ALL MODE AWD/4WD” with CONSULT-II.
3. Read out the value of “SHIFT POS SW1” and “SHIFT POS
SW2”.
Without CONSULT-II
1. Start engine.
2. Check voltage between transfer control unit harness connector
terminal and ground.
OK or NG
OK >> GO TO 5.
NG >> GO TO 2.
Monitored item Condition Display value
SHIFT POS SW1
Vehicle stopped
Engine running
A/T selector lever
“N” position
Brake pedal
depressed4WD shift switch: 4LO ON
4WD shift switch:
2WD, AUTO or 4HOFF
SHIFT POS SW2
Vehicle stopped
Engine running
A/T selector lever
“N” position
Brake pedal
depressed4WD shift switch: 4H,
AUTO or 2WDON
4WD shift switch: 4LO OFF
ConnectorTerminal
(Wire
color)ConditionVoltage
(Approx.)
E14327 (W/L)
- Ground
Vehicle stopped
Engine running
A/T selector
lever “N” position
Brake pedal
depressed4WD shift switch: 4H,
AUTO or 2WD0V
4WD shift switch: 4LOBattery
voltage
44 (LG/B)
- Ground
Vehicle stopped
Engine running
A/T selector
lever “N” position
Brake pedal
depressed4WD shift switch: 4LO 0V
4WD shift switch:
2WD, AUTO or 4HBattery
voltage
SDIA2714E
SDIA2715E
Page 3222 of 3419
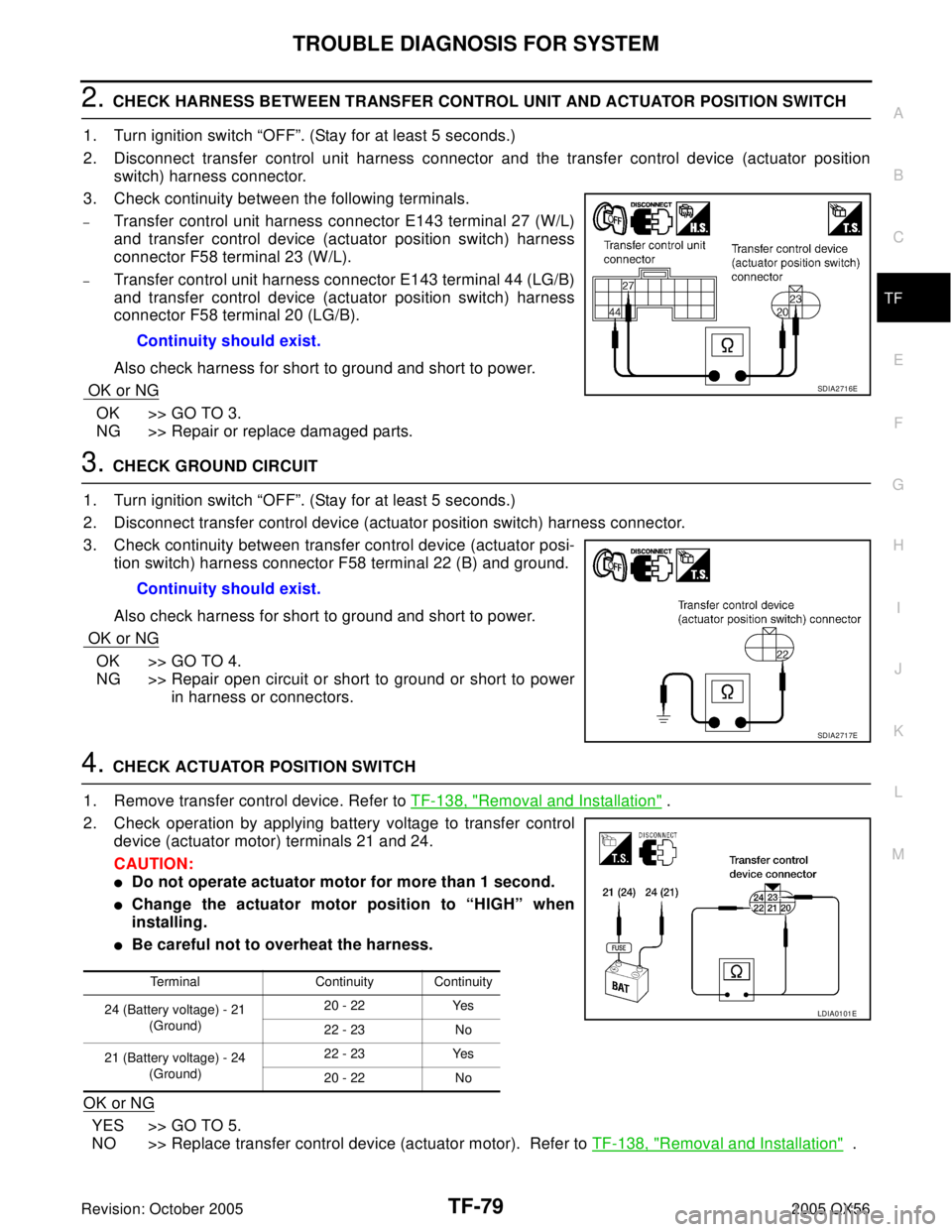
TROUBLE DIAGNOSIS FOR SYSTEM
TF-79
C
E
F
G
H
I
J
K
L
MA
B
TF
Revision: October 20052005 QX56
2. CHECK HARNESS BETWEEN TRANSFER CONTROL UNIT AND ACTUATOR POSITION SWITCH
1. Turn ignition switch “OFF”. (Stay for at least 5 seconds.)
2. Disconnect transfer control unit harness connector and the transfer control device (actuator position
switch) harness connector.
3. Check continuity between the following terminals.
–Transfer control unit harness connector E143 terminal 27 (W/L)
and transfer control device (actuator position switch) harness
connector F58 terminal 23 (W/L).
–Transfer control unit harness connector E143 terminal 44 (LG/B)
and transfer control device (actuator position switch) harness
connector F58 terminal 20 (LG/B).
Also check harness for short to ground and short to power.
OK or NG
OK >> GO TO 3.
NG >> Repair or replace damaged parts.
3. CHECK GROUND CIRCUIT
1. Turn ignition switch “OFF”. (Stay for at least 5 seconds.)
2. Disconnect transfer control device (actuator position switch) harness connector.
3. Check continuity between transfer control device (actuator posi-
tion switch) harness connector F58 terminal 22 (B) and ground.
Also check harness for short to ground and short to power.
OK or NG
OK >> GO TO 4.
NG >> Repair open circuit or short to ground or short to power
in harness or connectors.
4. CHECK ACTUATOR POSITION SWITCH
1. Remove transfer control device. Refer to TF-138, "
Removal and Installation" .
2. Check operation by applying battery voltage to transfer control
device (actuator motor) terminals 21 and 24.
CAUTION:
Do not operate actuator motor for more than 1 second.
Change the actuator motor position to “HIGH” when
installing.
Be careful not to overheat the harness.
OK or NG
YES >> GO TO 5.
NO >> Replace transfer control device (actuator motor). Refer to TF-138, "
Removal and Installation" . Continuity should exist.
SDIA2716E
Continuity should exist.
SDIA2717E
Terminal Continuity Continuity
24 (Battery voltage) - 21
(Ground)20 - 22 Yes
22 - 23 No
21 (Battery voltage) - 24
(Ground)22 - 23 Yes
20 - 22 No
LDIA0101E
Page 3223 of 3419
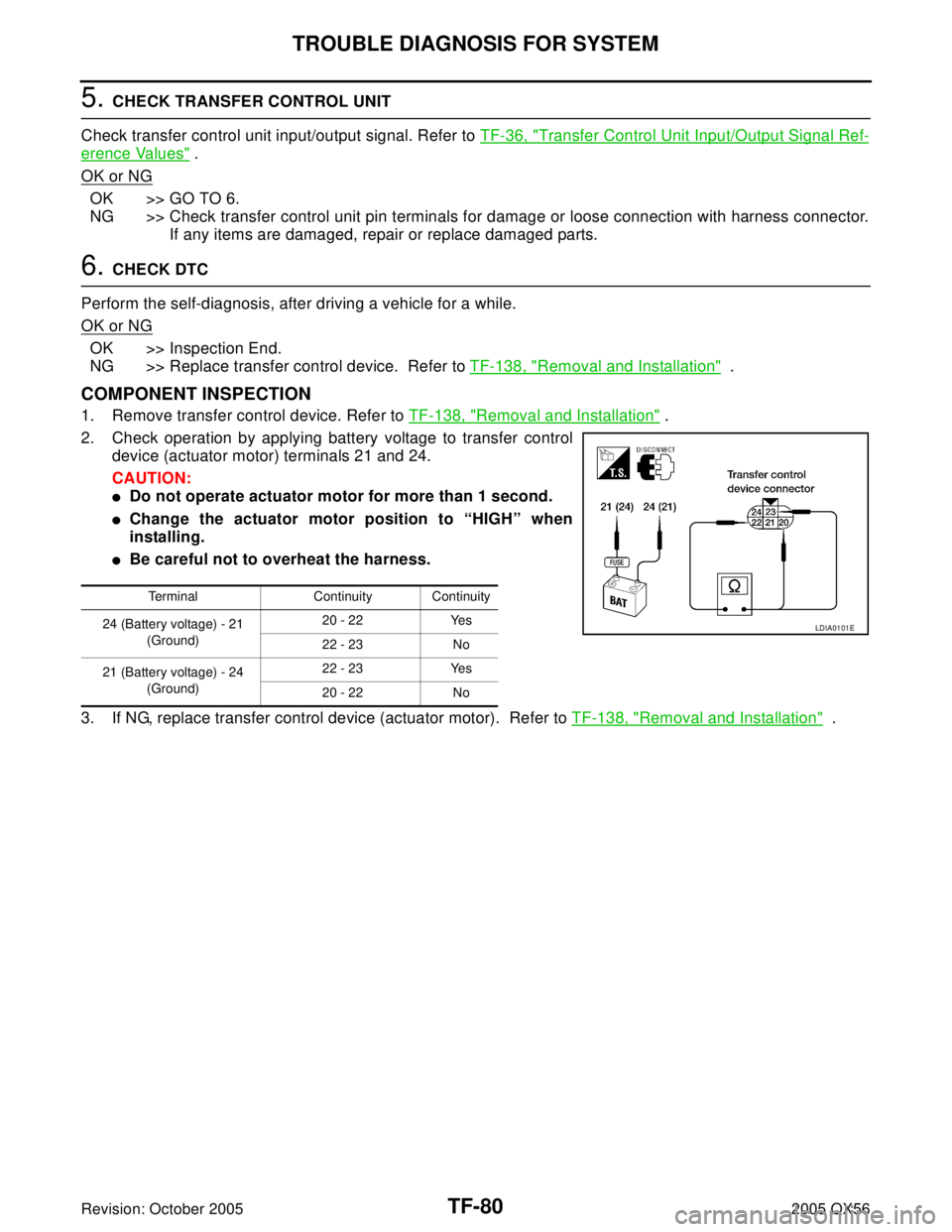
TF-80
TROUBLE DIAGNOSIS FOR SYSTEM
Revision: October 20052005 QX56
5. CHECK TRANSFER CONTROL UNIT
Check transfer control unit input/output signal. Refer to TF-36, "
Transfer Control Unit Input/Output Signal Ref-
erence Values" .
OK or NG
OK >> GO TO 6.
NG >> Check transfer control unit pin terminals for damage or loose connection with harness connector.
If any items are damaged, repair or replace damaged parts.
6. CHECK DTC
Perform the self-diagnosis, after driving a vehicle for a while.
OK or NG
OK >> Inspection End.
NG >> Replace transfer control device. Refer to TF-138, "
Removal and Installation" .
COMPONENT INSPECTION
1. Remove transfer control device. Refer to TF-138, "Removal and Installation" .
2. Check operation by applying battery voltage to transfer control
device (actuator motor) terminals 21 and 24.
CAUTION:
Do not operate actuator motor for more than 1 second.
Change the actuator motor position to “HIGH” when
installing.
Be careful not to overheat the harness.
3. If NG, replace transfer control device (actuator motor). Refer to TF-138, "
Removal and Installation" .
Terminal Continuity Continuity
24 (Battery voltage) - 21
(Ground)20 - 22 Yes
22 - 23 No
21 (Battery voltage) - 24
(Ground)22 - 23 Yes
20 - 22 No
LDIA0101E
Page 3224 of 3419
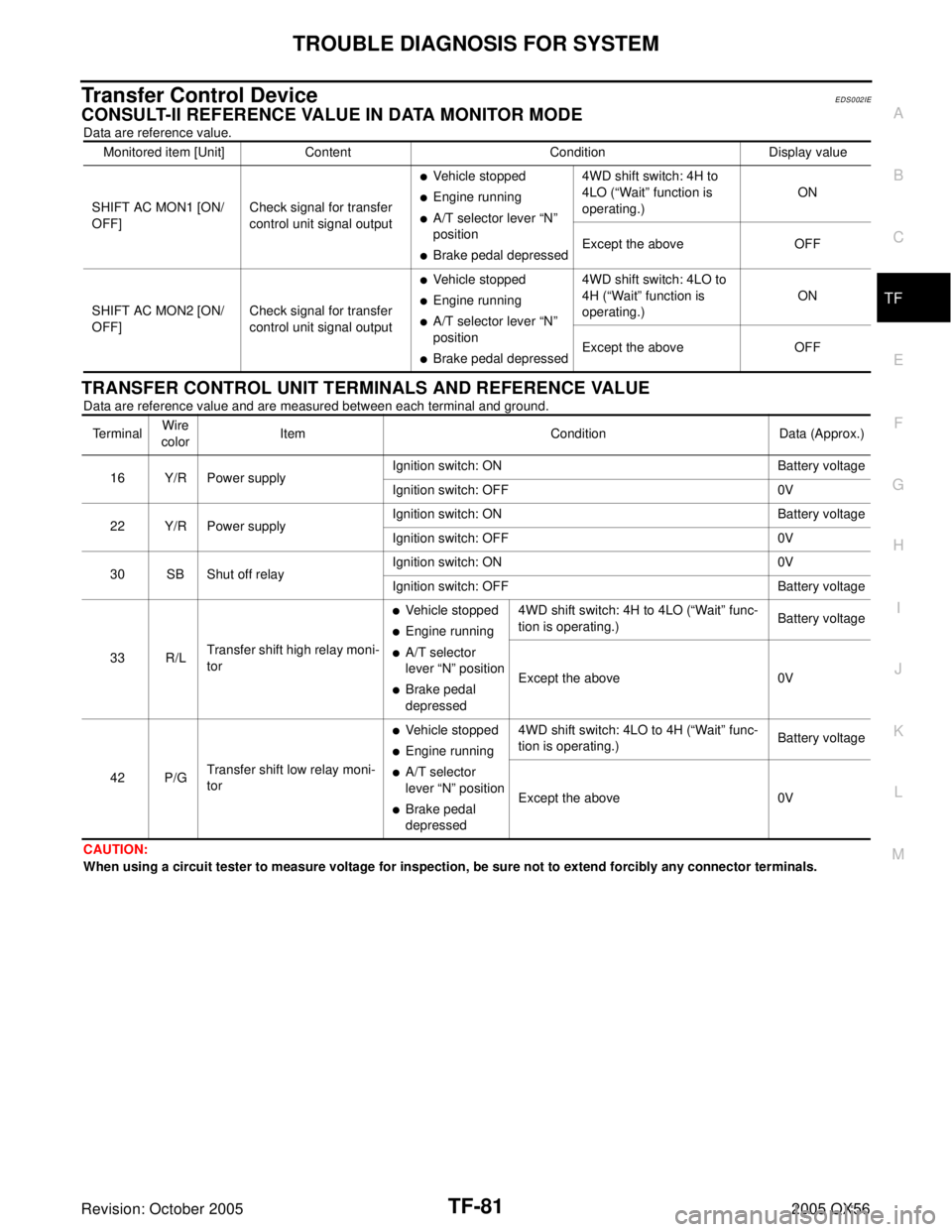
TROUBLE DIAGNOSIS FOR SYSTEM
TF-81
C
E
F
G
H
I
J
K
L
MA
B
TF
Revision: October 20052005 QX56
Transfer Control DeviceEDS002IE
CONSULT-II REFERENCE VALUE IN DATA MONITOR MODE
Data are reference value.
TRANSFER CONTROL UNIT TERMINALS AND REFERENCE VALUE
Data are reference value and are measured between each terminal and ground.
CAUTION:
When using a circuit tester to measure voltage for inspection, be sure not to extend forcibly any connector terminals.Monitored item [Unit] Content Condition Display value
SHIFT AC MON1 [ON/
OFF]Check signal for transfer
control unit signal output
Vehicle stopped
Engine running
A/T selector lever “N”
position
Brake pedal depressed4WD shift switch: 4H to
4LO (“Wait” function is
operating.)ON
Except the above OFF
SHIFT AC MON2 [ON/
OFF]Check signal for transfer
control unit signal output
Vehicle stopped
Engine running
A/T selector lever “N”
position
Brake pedal depressed4WD shift switch: 4LO to
4H (“Wait” function is
operating.)ON
Except the above OFF
Te r m i n a lWire
colorItem Condition Data (Approx.)
16 Y/R Power supplyIgnition switch: ON Battery voltage
Ignition switch: OFF 0V
22 Y/R Power supplyIgnition switch: ON Battery voltage
Ignition switch: OFF 0V
30 SB Shut off relayIgnition switch: ON 0V
Ignition switch: OFF Battery voltage
33 R/LTransfer shift high relay moni-
tor
Vehicle stopped
Engine running
A/T selector
lever “N” position
Brake pedal
depressed4WD shift switch: 4H to 4LO (“Wait” func-
tion is operating.)Battery voltage
Except the above 0V
42 P/GTransfer shift low relay moni-
tor
Vehicle stopped
Engine running
A/T selector
lever “N” position
Brake pedal
depressed4WD shift switch: 4LO to 4H (“Wait” func-
tion is operating.)Battery voltage
Except the above 0V