Page 4025 of 4647
PS-44
HYDRAULIC LINE
Revision: 2007 April2007 M35/M45
Removal and InstallationNGS000DL
CAUTION:
Securely insert harness connector to pressure sensor.
Insert hose securely until it contacts tube spool (Do not
apply fluid).
Install eye-bolt with eye-joint (assembled to high-pressure
hose) protrusion facing with pump side cutout, and then
tighten it to the specified torque after tightening by hand.
Refer to GI-11, "Components" , and the followings for the symbols in the figure.
: Apply power steering fluid.
SGIA0514E
SGIA0515E
Page 4026 of 4647
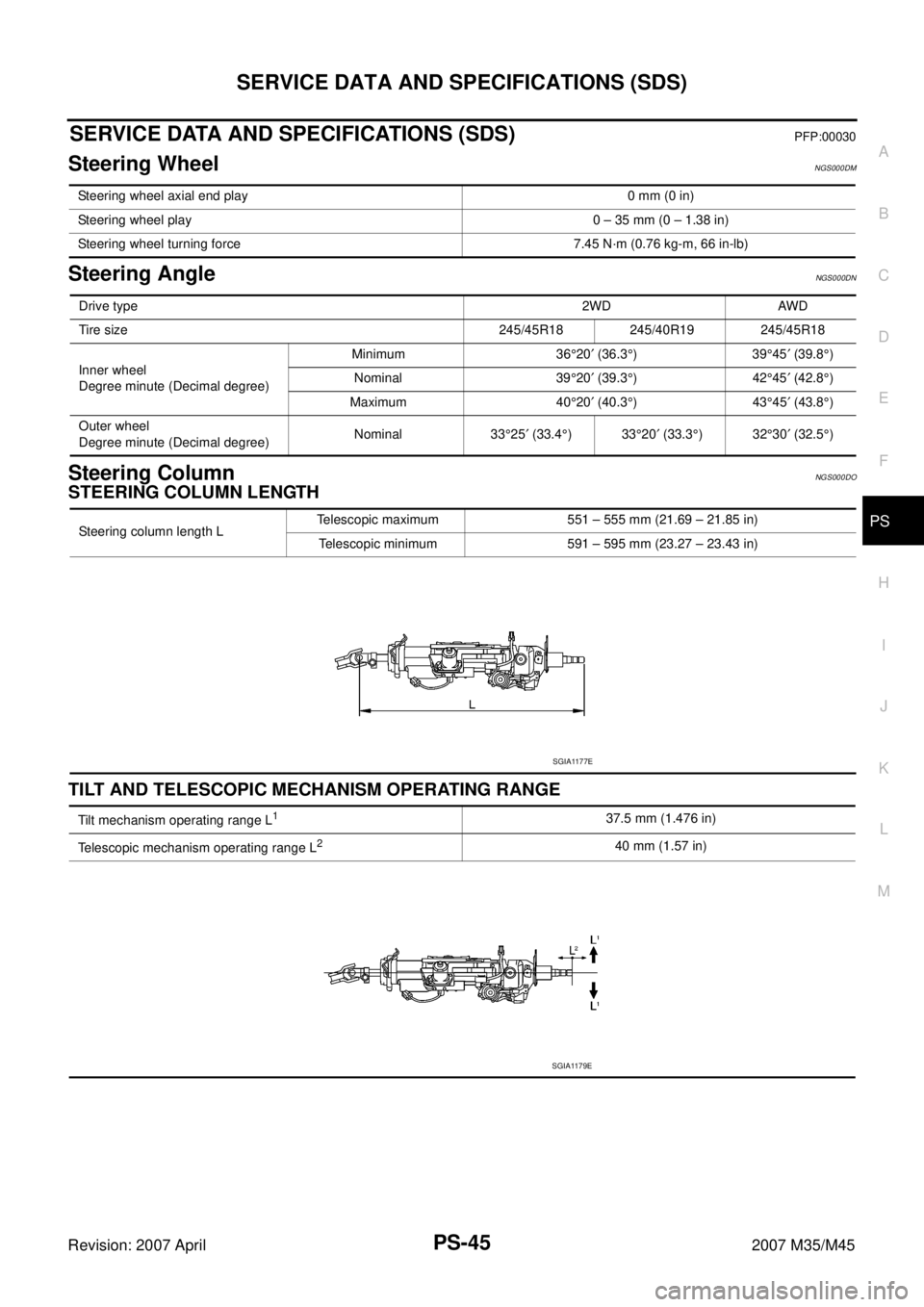
SERVICE DATA AND SPECIFICATIONS (SDS)
PS-45
C
D
E
F
H
I
J
K
L
MA
B
PS
Revision: 2007 April2007 M35/M45
SERVICE DATA AND SPECIFICATIONS (SDS)PFP:00030
Steering WheelNGS000DM
Steering AngleNGS000DN
Steering ColumnNGS000DO
STEERING COLUMN LENGTH
TILT AND TELESCOPIC MECHANISM OPERATING RANGE
Steering wheel axial end play 0 mm (0 in)
Steering wheel play 0 – 35 mm (0 – 1.38 in)
Steering wheel turning force 7.45 N·m (0.76 kg-m, 66 in-lb)
Drive type2WD AWD
Tire size 245/45R18 245/40R19 245/45R18
Inner wheel
Degree minute (Decimal degree)Minimum 36°20′ (36.3°)39°45′ (39.8°)
Nominal 39°20′ (39.3°)42°45′ (42.8°)
Maximum 40°20′ (40.3°)43°45′ (43.8°)
Outer wheel
Degree minute (Decimal degree)Nominal 33°25′ (33.4°)33°20′ (33.3°)32°30′ (32.5°)
Steering column length LTelescopic maximum 551 – 555 mm (21.69 – 21.85 in)
Telescopic minimum 591 – 595 mm (23.27 – 23.43 in)
SGIA1177E
Tilt mechanism operating range L137.5 mm (1.476 in)
Telescopic mechanism operating range L
240 mm (1.57 in)
SGIA1179E
Page 4027 of 4647
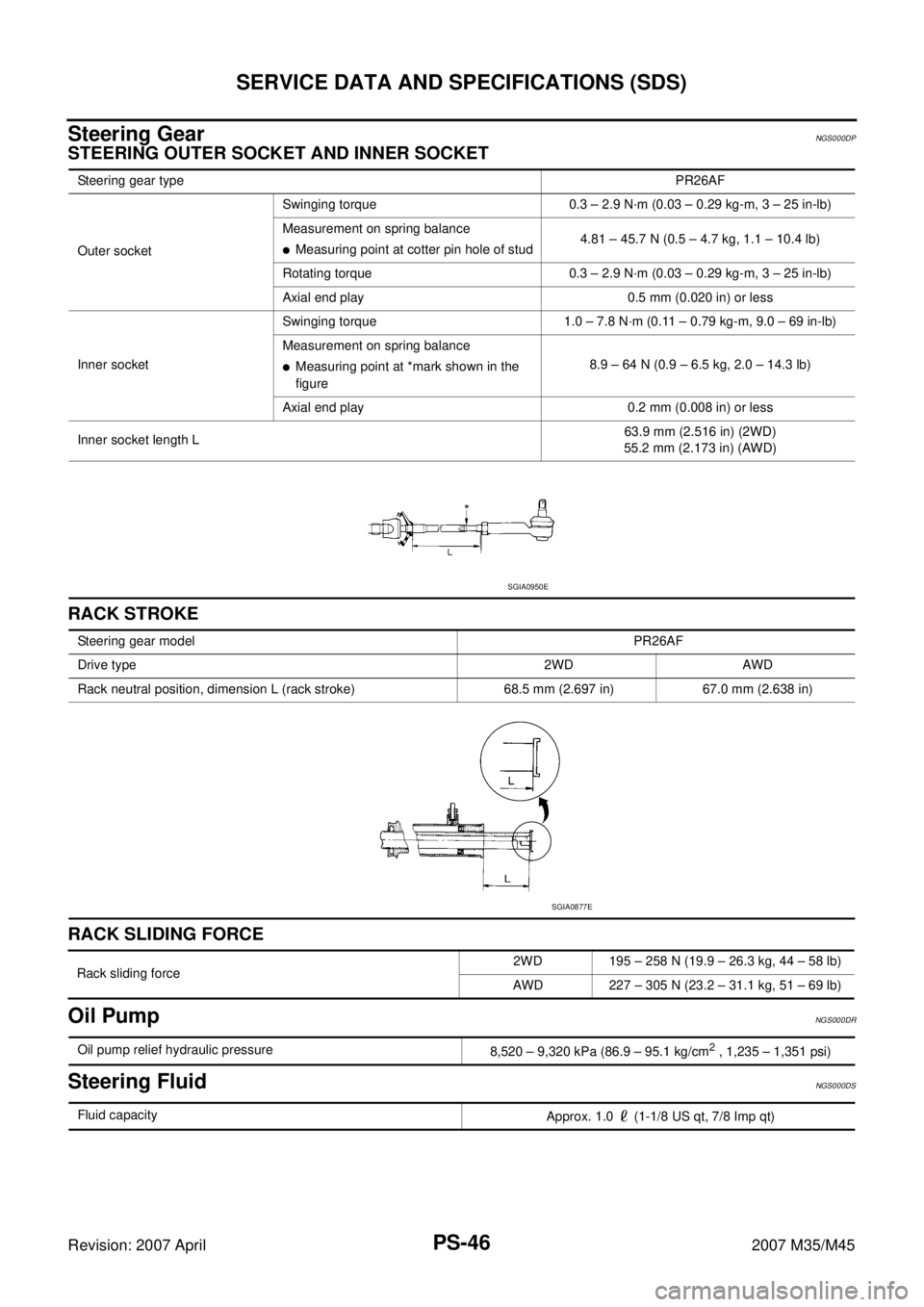
PS-46
SERVICE DATA AND SPECIFICATIONS (SDS)
Revision: 2007 April2007 M35/M45
Steering GearNGS000DP
STEERING OUTER SOCKET AND INNER SOCKET
RACK STROKE
RACK SLIDING FORCE
Oil PumpNGS000DR
Steering FluidNGS000DS
Steering gear typePR26AF
Outer socketSwinging torque 0.3 – 2.9 N·m (0.03 – 0.29 kg-m, 3 – 25 in-lb)
Measurement on spring balance
Measuring point at cotter pin hole of stud4.81 – 45.7 N (0.5 – 4.7 kg, 1.1 – 10.4 lb)
Rotating torque 0.3 – 2.9 N·m (0.03 – 0.29 kg-m, 3 – 25 in-lb)
Axial end play 0.5 mm (0.020 in) or less
Inner socketSwinging torque 1.0 – 7.8 N·m (0.11 – 0.79 kg-m, 9.0 – 69 in-lb)
Measurement on spring balance
Measuring point at *mark shown in the
figure8.9 – 64 N (0.9 – 6.5 kg, 2.0 – 14.3 lb)
Axial end play 0.2 mm (0.008 in) or less
Inner socket length L63.9 mm (2.516 in) (2WD)
55.2 mm (2.173 in) (AWD)
SGIA0950E
Steering gear modelPR26AF
Drive type 2WD AWD
Rack neutral position, dimension L (rack stroke) 68.5 mm (2.697 in) 67.0 mm (2.638 in)
SGIA0877E
Rack sliding force2WD 195 – 258 N (19.9 – 26.3 kg, 44 – 58 lb)
AWD 227 – 305 N (23.2 – 31.1 kg, 51 – 69 lb)
Oil pump relief hydraulic pressure
8,520 – 9,320 kPa (86.9 – 95.1 kg/cm2 , 1,235 – 1,351 psi)
Fluid capacity
Approx. 1.0 (1-1/8 US qt, 7/8 Imp qt)
Page 4028 of 4647
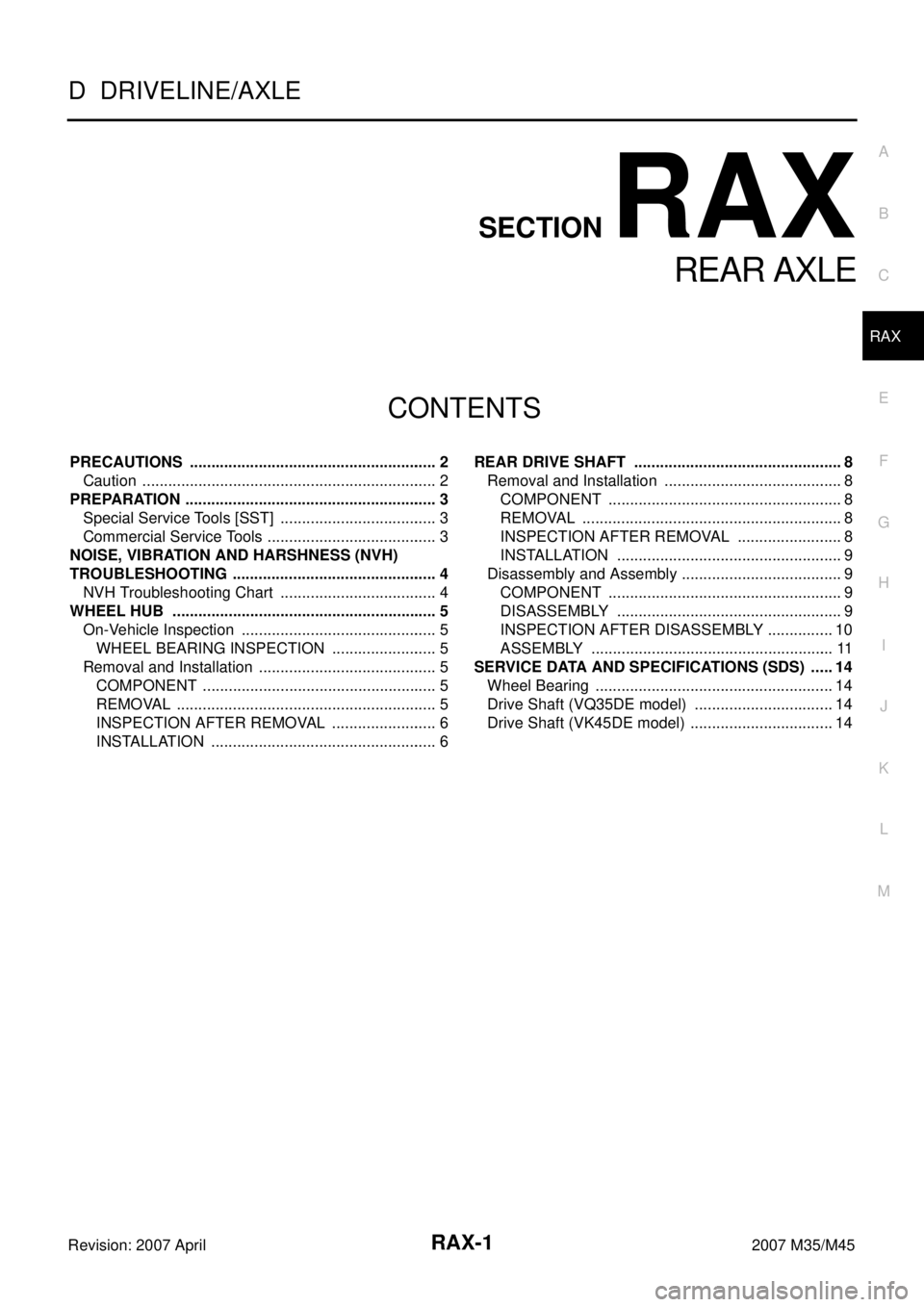
RAX-1
REAR AXLE
D DRIVELINE/AXLE
CONTENTS
C
E
F
G
H
I
J
K
L
M
SECTION RAX
A
B
RAX
Revision: 2007 April2007 M35/M45
REAR AXLE
PRECAUTIONS .......................................................... 2
Caution ..................................................................... 2
PREPARATION ........................................................... 3
Special Service Tools [SST] ..................................... 3
Commercial Service Tools ........................................ 3
NOISE, VIBRATION AND HARSHNESS (NVH)
TROUBLESHOOTING ................................................ 4
NVH Troubleshooting Chart ..................................... 4
WHEEL HUB .............................................................. 5
On-Vehicle Inspection .............................................. 5
WHEEL BEARING INSPECTION ......................... 5
Removal and Installation .......................................... 5
COMPONENT ....................................................... 5
REMOVAL ............................................................. 5
INSPECTION AFTER REMOVAL ......................... 6
INSTALLATION ..................................................... 6REAR DRIVE SHAFT ................................................. 8
Removal and Installation .......................................... 8
COMPONENT ....................................................... 8
REMOVAL ............................................................. 8
INSPECTION AFTER REMOVAL ......................... 8
INSTALLATION ..................................................... 9
Disassembly and Assembly ...................................... 9
COMPONENT ....................................................... 9
DISASSEMBLY ..................................................... 9
INSPECTION AFTER DISASSEMBLY ................ 10
ASSEMBLY ......................................................... 11
SERVICE DATA AND SPECIFICATIONS (SDS) ...... 14
Wheel Bearing ........................................................ 14
Drive Shaft (VQ35DE model) ................................. 14
Drive Shaft (VK45DE model) .................................. 14
Page 4029 of 4647
RAX-2
PRECAUTIONS
Revision: 2007 April2007 M35/M45
PRECAUTIONSPFP:00001
CautionNDS000FM
Observe the following precautions when disassembling and assembling drive shaft.
Joint sub-assembly does not disassemble because it is non-overhaul parts.
Perform work in a location which is as dust-free as possible.
Before disassembling and assembling, clean the outside of parts.
Prevention of the entry of foreign objects must be taken into account during disassembly of the service
location.
Disassembled parts must be carefully reassembled in the correct order. If work is interrupted, a clean
cover must be placed over parts.
Paper shop cloths must be used. Fabric shop cloths must not be used because of the danger of lint adher-
ing to parts.
Disassembled parts (except for rubber parts) should be cleaned with kerosene which shall be removed by
blowing with air or wiping with paper shop cloths.
Page 4030 of 4647
PREPARATION
RAX-3
C
E
F
G
H
I
J
K
L
MA
B
RAX
Revision: 2007 April2007 M35/M45
PREPARATIONPFP:00002
Special Service Tools [SST]NDS000FN
The actual shapes of Kent-Moore tools may differ from those of special service tools illustrated here.
Commercial Service ToolsNDS000FO
Tool number
(Kent-Moore No.)
Tool nameDescription
KV38100500
(—)
Drift
a: 80 mm (3.15 in) dia.
b: 60 mm (2.36 in) dia.Installing drive shaft plug
KV38102200
(—)
Drift
a: 90 mm (3.54 in) dia.
b: 31 mm (1.22 in) dia.Installing drive shaft plug
ZZA0701D
ZZA0920D
Tool nameDescription
Power tool
Removing wheel nuts
Removing brake caliper assembly
Removing suspension links
Removing drive shaft
PBIC0190E
Page 4031 of 4647
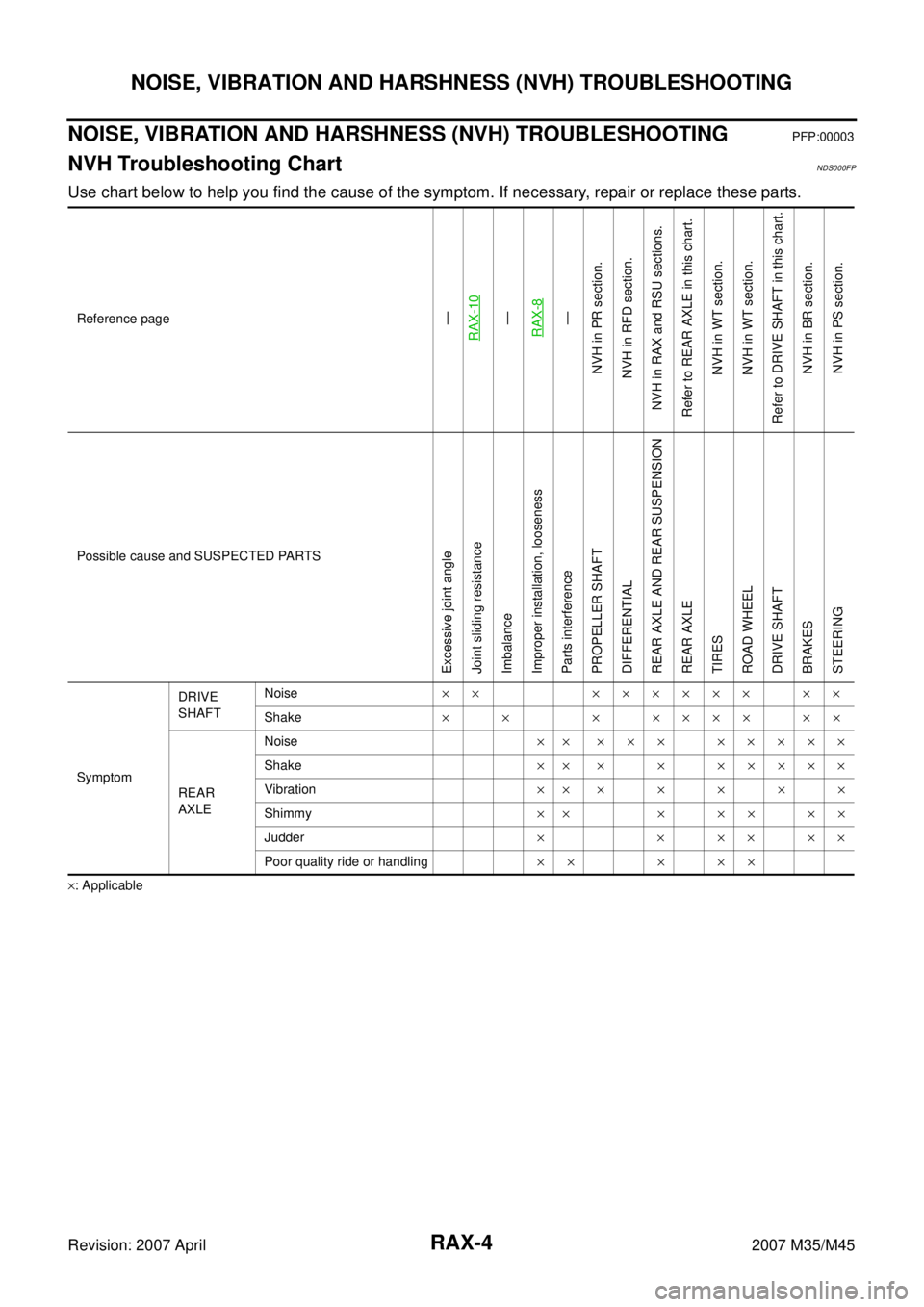
RAX-4
NOISE, VIBRATION AND HARSHNESS (NVH) TROUBLESHOOTING
Revision: 2007 April2007 M35/M45
NOISE, VIBRATION AND HARSHNESS (NVH) TROUBLESHOOTINGPFP:00003
NVH Troubleshooting ChartNDS000FP
Use chart below to help you find the cause of the symptom. If necessary, repair or replace these parts.
×: ApplicableReference page
—
RAX-10—
RAX-8—
NVH in PR section.
NVH in RFD section.
NVH in RAX and RSU sections.
Refer to REAR AXLE in this chart.
NVH in WT section.
NVH in WT section.
Refer to DRIVE SHAFT in this chart.
NVH in BR section.
NVH in PS section.
Possible cause and SUSPECTED PARTS
Excessive joint angle
Joint sliding resistance
Imbalance
Improper installation, looseness
Parts interference
PROPELLER SHAFT
DIFFERENTIAL
REAR AXLE AND REAR SUSPENSION
REAR AXLE
TIRES
ROAD WHEEL
DRIVE SHAFT
BRAKES
STEERING
SymptomDRIVE
SHAFTNoise×× ×××××× ××
Shake×× ×××××××
REAR
AXLENoise×× ××× ×××××
Shake×××××××××
Vibration×××××××
Shimmy×× ×××××
Judder× × ×× ××
Poor quality ride or handling×× × ××
Page 4032 of 4647
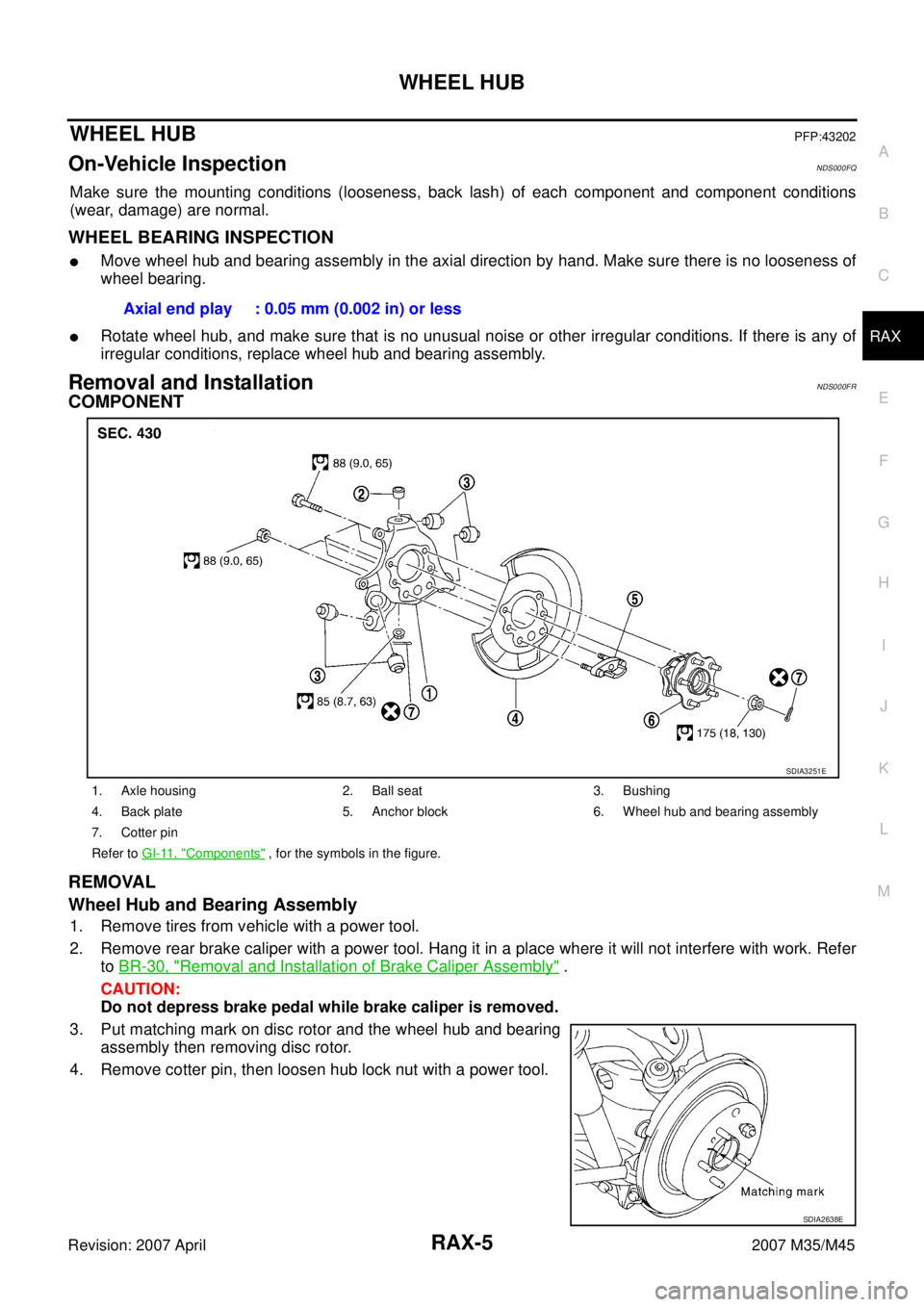
WHEEL HUB
RAX-5
C
E
F
G
H
I
J
K
L
MA
B
RAX
Revision: 2007 April2007 M35/M45
WHEEL HUBPFP:43202
On-Vehicle Inspection NDS000FQ
Make sure the mounting conditions (looseness, back lash) of each component and component conditions
(wear, damage) are normal.
WHEEL BEARING INSPECTION
Move wheel hub and bearing assembly in the axial direction by hand. Make sure there is no looseness of
wheel bearing.
Rotate wheel hub, and make sure that is no unusual noise or other irregular conditions. If there is any of
irregular conditions, replace wheel hub and bearing assembly.
Removal and InstallationNDS000FR
COMPONENT
REMOVAL
Wheel Hub and Bearing Assembly
1. Remove tires from vehicle with a power tool.
2. Remove rear brake caliper with a power tool. Hang it in a place where it will not interfere with work. Refer
to BR-30, "
Removal and Installation of Brake Caliper Assembly" .
CAUTION:
Do not depress brake pedal while brake caliper is removed.
3. Put matching mark on disc rotor and the wheel hub and bearing
assembly then removing disc rotor.
4. Remove cotter pin, then loosen hub lock nut with a power tool.Axial end play : 0.05 mm (0.002 in) or less
1. Axle housing 2. Ball seat 3. Bushing
4. Back plate 5. Anchor block 6. Wheel hub and bearing assembly
7. Cotter pin
Refer to GI-11, "
Components" , for the symbols in the figure.
SDIA3251E
SDIA2638E