Page 1297 of 4647
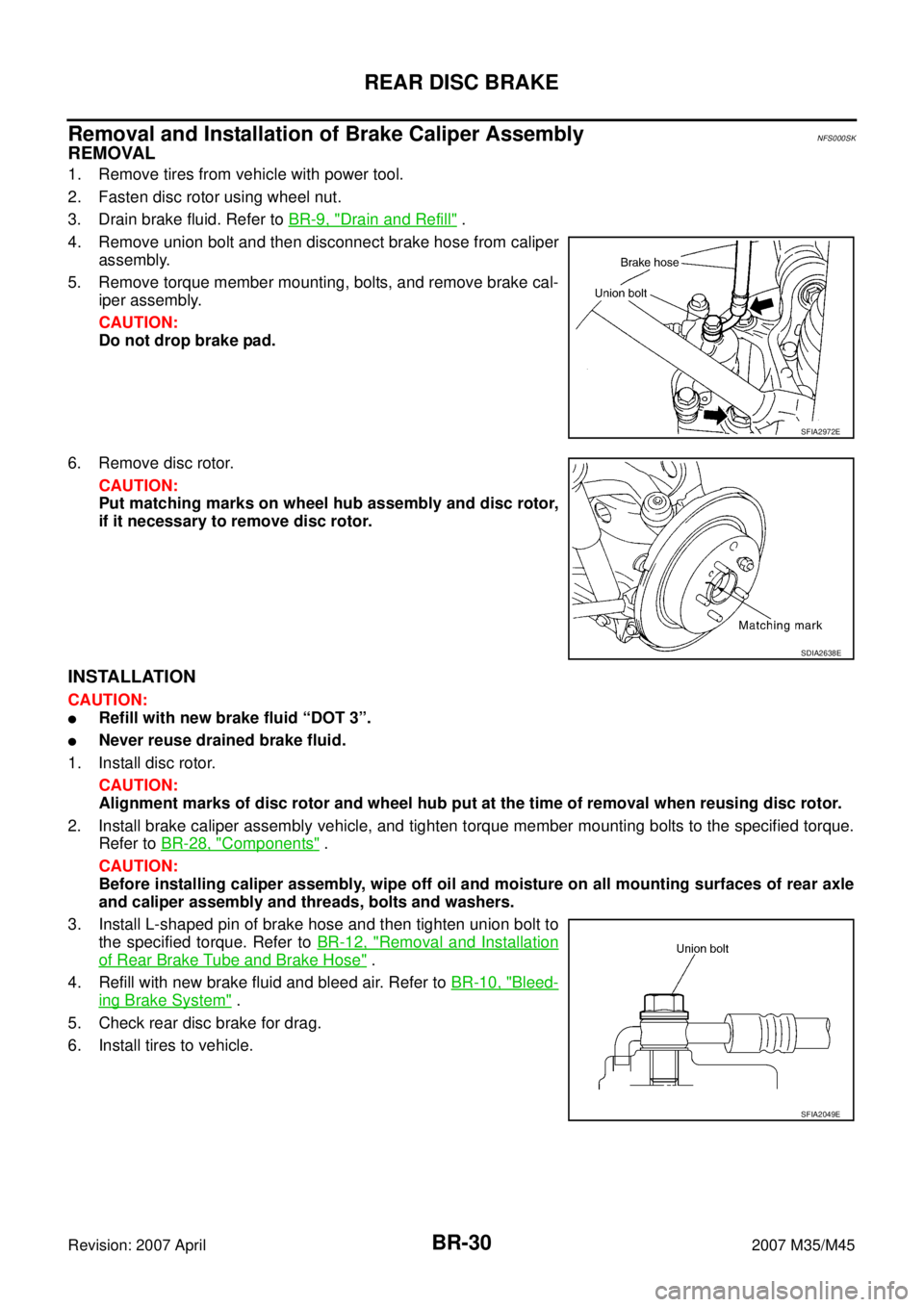
BR-30
REAR DISC BRAKE
Revision: 2007 April2007 M35/M45
Removal and Installation of Brake Caliper AssemblyNFS000SK
REMOVAL
1. Remove tires from vehicle with power tool.
2. Fasten disc rotor using wheel nut.
3. Drain brake fluid. Refer to BR-9, "
Drain and Refill" .
4. Remove union bolt and then disconnect brake hose from caliper
assembly.
5. Remove torque member mounting, bolts, and remove brake cal-
iper assembly.
CAUTION:
Do not drop brake pad.
6. Remove disc rotor.
CAUTION:
Put matching marks on wheel hub assembly and disc rotor,
if it necessary to remove disc rotor.
INSTALLATION
CAUTION:
Refill with new brake fluid “DOT 3”.
Never reuse drained brake fluid.
1. Install disc rotor.
CAUTION:
Alignment marks of disc rotor and wheel hub put at the time of removal when reusing disc rotor.
2. Install brake caliper assembly vehicle, and tighten torque member mounting bolts to the specified torque.
Refer to BR-28, "
Components" .
CAUTION:
Before installing caliper assembly, wipe off oil and moisture on all mounting surfaces of rear axle
and caliper assembly and threads, bolts and washers.
3. Install L-shaped pin of brake hose and then tighten union bolt to
the specified torque. Refer to BR-12, "
Removal and Installation
of Rear Brake Tube and Brake Hose" .
4. Refill with new brake fluid and bleed air. Refer to BR-10, "
Bleed-
ing Brake System" .
5. Check rear disc brake for drag.
6. Install tires to vehicle.
SFIA2972E
SDIA2638E
SFIA2049E
Page 1298 of 4647
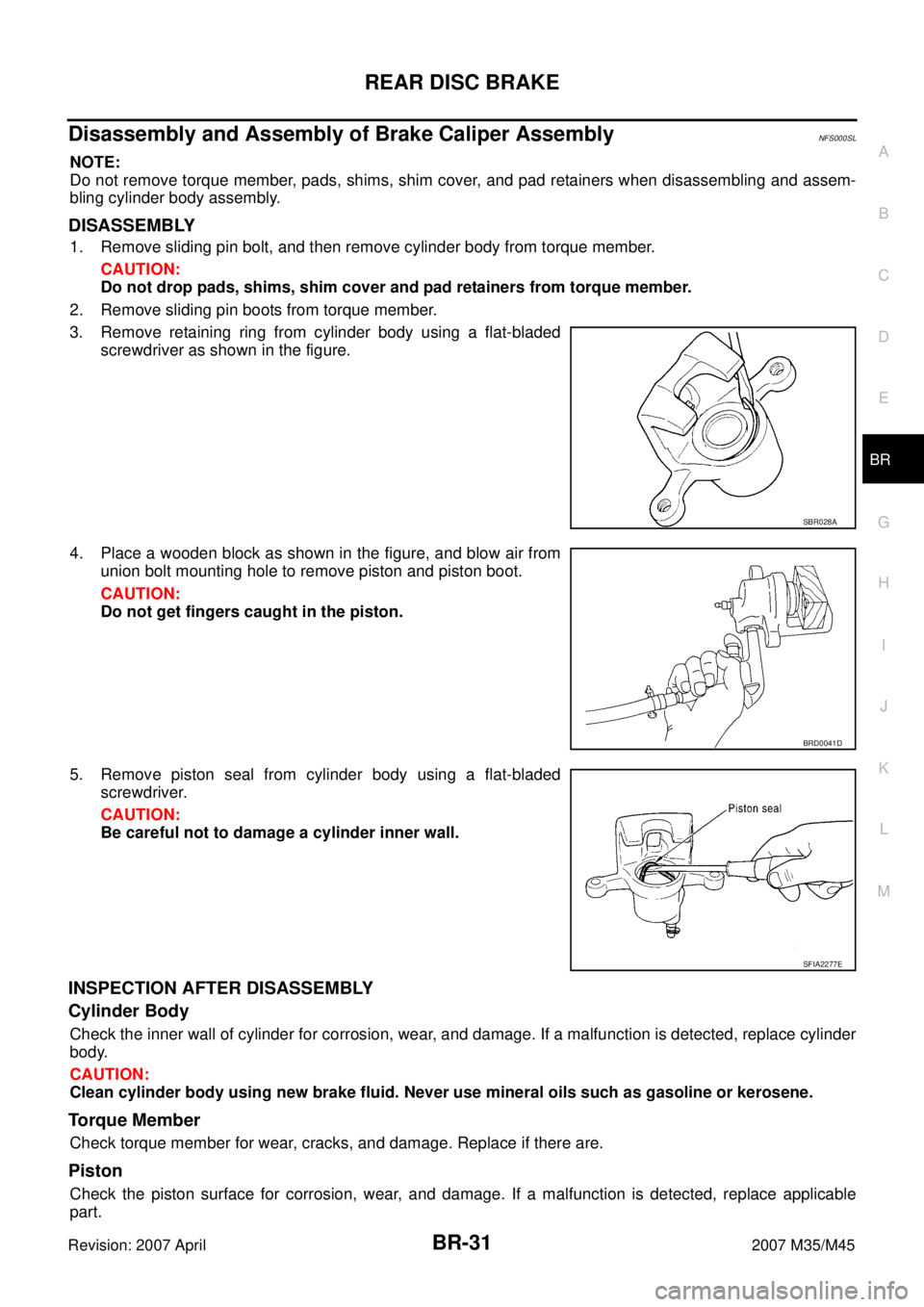
REAR DISC BRAKE
BR-31
C
D
E
G
H
I
J
K
L
MA
B
BR
Revision: 2007 April2007 M35/M45
Disassembly and Assembly of Brake Caliper AssemblyNFS000SL
NOTE:
Do not remove torque member, pads, shims, shim cover, and pad retainers when disassembling and assem-
bling cylinder body assembly.
DISASSEMBLY
1. Remove sliding pin bolt, and then remove cylinder body from torque member.
CAUTION:
Do not drop pads, shims, shim cover and pad retainers from torque member.
2. Remove sliding pin boots from torque member.
3. Remove retaining ring from cylinder body using a flat-bladed
screwdriver as shown in the figure.
4. Place a wooden block as shown in the figure, and blow air from
union bolt mounting hole to remove piston and piston boot.
CAUTION:
Do not get fingers caught in the piston.
5. Remove piston seal from cylinder body using a flat-bladed
screwdriver.
CAUTION:
Be careful not to damage a cylinder inner wall.
INSPECTION AFTER DISASSEMBLY
Cylinder Body
Check the inner wall of cylinder for corrosion, wear, and damage. If a malfunction is detected, replace cylinder
body.
CAUTION:
Clean cylinder body using new brake fluid. Never use mineral oils such as gasoline or kerosene.
To r q u e M e m b e r
Check torque member for wear, cracks, and damage. Replace if there are.
Piston
Check the piston surface for corrosion, wear, and damage. If a malfunction is detected, replace applicable
part.
SBR028A
BRD0041D
SFIA2277E
Page 1299 of 4647
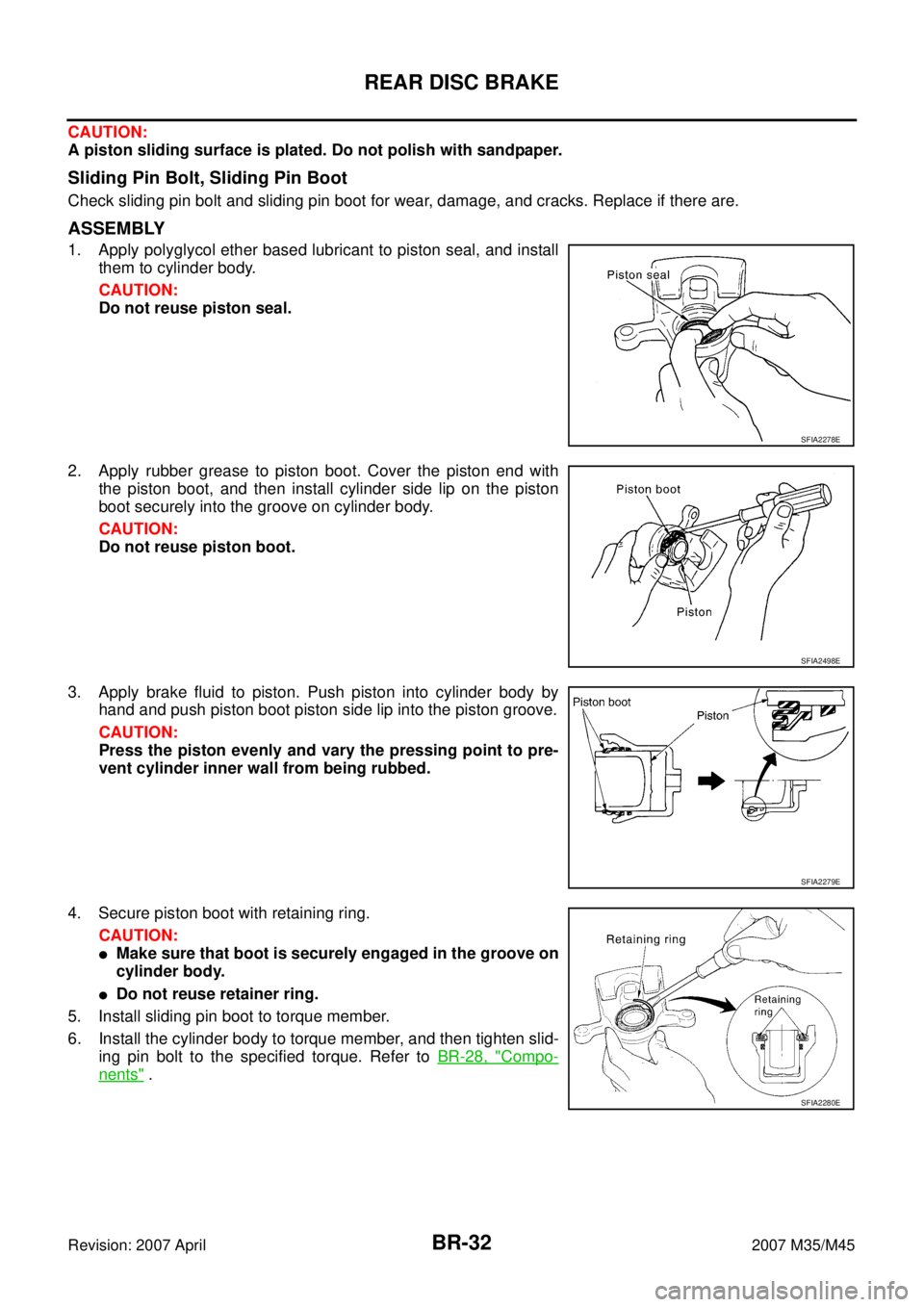
BR-32
REAR DISC BRAKE
Revision: 2007 April2007 M35/M45
CAUTION:
A piston sliding surface is plated. Do not polish with sandpaper.
Sliding Pin Bolt, Sliding Pin Boot
Check sliding pin bolt and sliding pin boot for wear, damage, and cracks. Replace if there are.
ASSEMBLY
1. Apply polyglycol ether based lubricant to piston seal, and install
them to cylinder body.
CAUTION:
Do not reuse piston seal.
2. Apply rubber grease to piston boot. Cover the piston end with
the piston boot, and then install cylinder side lip on the piston
boot securely into the groove on cylinder body.
CAUTION:
Do not reuse piston boot.
3. Apply brake fluid to piston. Push piston into cylinder body by
hand and push piston boot piston side lip into the piston groove.
CAUTION:
Press the piston evenly and vary the pressing point to pre-
vent cylinder inner wall from being rubbed.
4. Secure piston boot with retaining ring.
CAUTION:
Make sure that boot is securely engaged in the groove on
cylinder body.
Do not reuse retainer ring.
5. Install sliding pin boot to torque member.
6. Install the cylinder body to torque member, and then tighten slid-
ing pin bolt to the specified torque. Refer to BR-28, "
Compo-
nents" .
SFIA2278E
SFIA2498E
SFIA2279E
SFIA2280E
Page 1300 of 4647
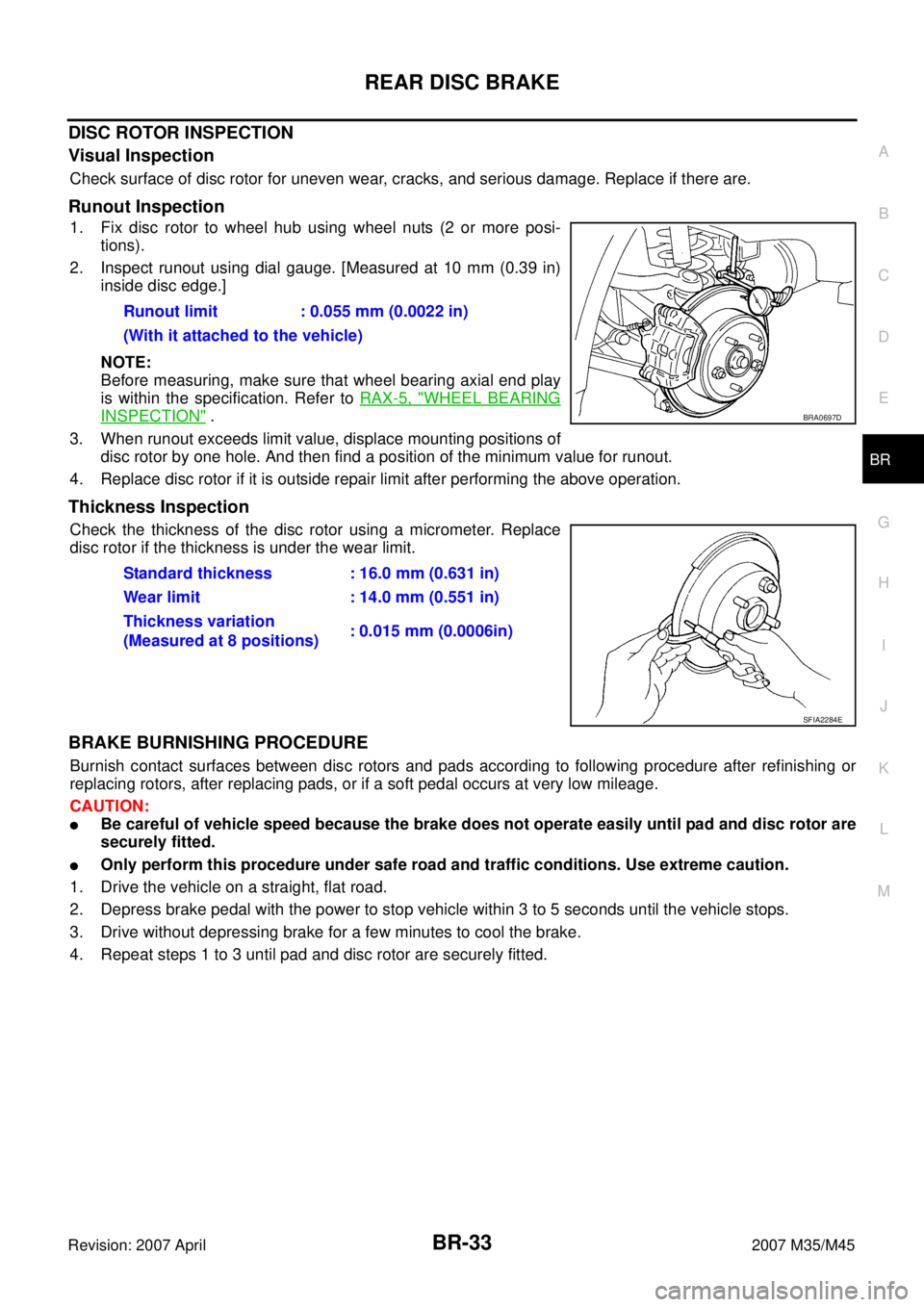
REAR DISC BRAKE
BR-33
C
D
E
G
H
I
J
K
L
MA
B
BR
Revision: 2007 April2007 M35/M45
DISC ROTOR INSPECTION
Visual Inspection
Check surface of disc rotor for uneven wear, cracks, and serious damage. Replace if there are.
Runout Inspection
1. Fix disc rotor to wheel hub using wheel nuts (2 or more posi-
tions).
2. Inspect runout using dial gauge. [Measured at 10 mm (0.39 in)
inside disc edge.]
NOTE:
Before measuring, make sure that wheel bearing axial end play
is within the specification. Refer to RAX-5, "
WHEEL BEARING
INSPECTION" .
3. When runout exceeds limit value, displace mounting positions of
disc rotor by one hole. And then find a position of the minimum value for runout.
4. Replace disc rotor if it is outside repair limit after performing the above operation.
Thickness Inspection
Check the thickness of the disc rotor using a micrometer. Replace
disc rotor if the thickness is under the wear limit.
BRAKE BURNISHING PROCEDURE
Burnish contact surfaces between disc rotors and pads according to following procedure after refinishing or
replacing rotors, after replacing pads, or if a soft pedal occurs at very low mileage.
CAUTION:
Be careful of vehicle speed because the brake does not operate easily until pad and disc rotor are
securely fitted.
Only perform this procedure under safe road and traffic conditions. Use extreme caution.
1. Drive the vehicle on a straight, flat road.
2. Depress brake pedal with the power to stop vehicle within 3 to 5 seconds until the vehicle stops.
3. Drive without depressing brake for a few minutes to cool the brake.
4. Repeat steps 1 to 3 until pad and disc rotor are securely fitted.Runout limit : 0.055 mm (0.0022 in)
(With it attached to the vehicle)
BRA0697D
Standard thickness : 16.0 mm (0.631 in)
Wear limit : 14.0 mm (0.551 in)
Thickness variation
(Measured at 8 positions): 0.015 mm (0.0006in)
SFIA2284E
Page 1301 of 4647
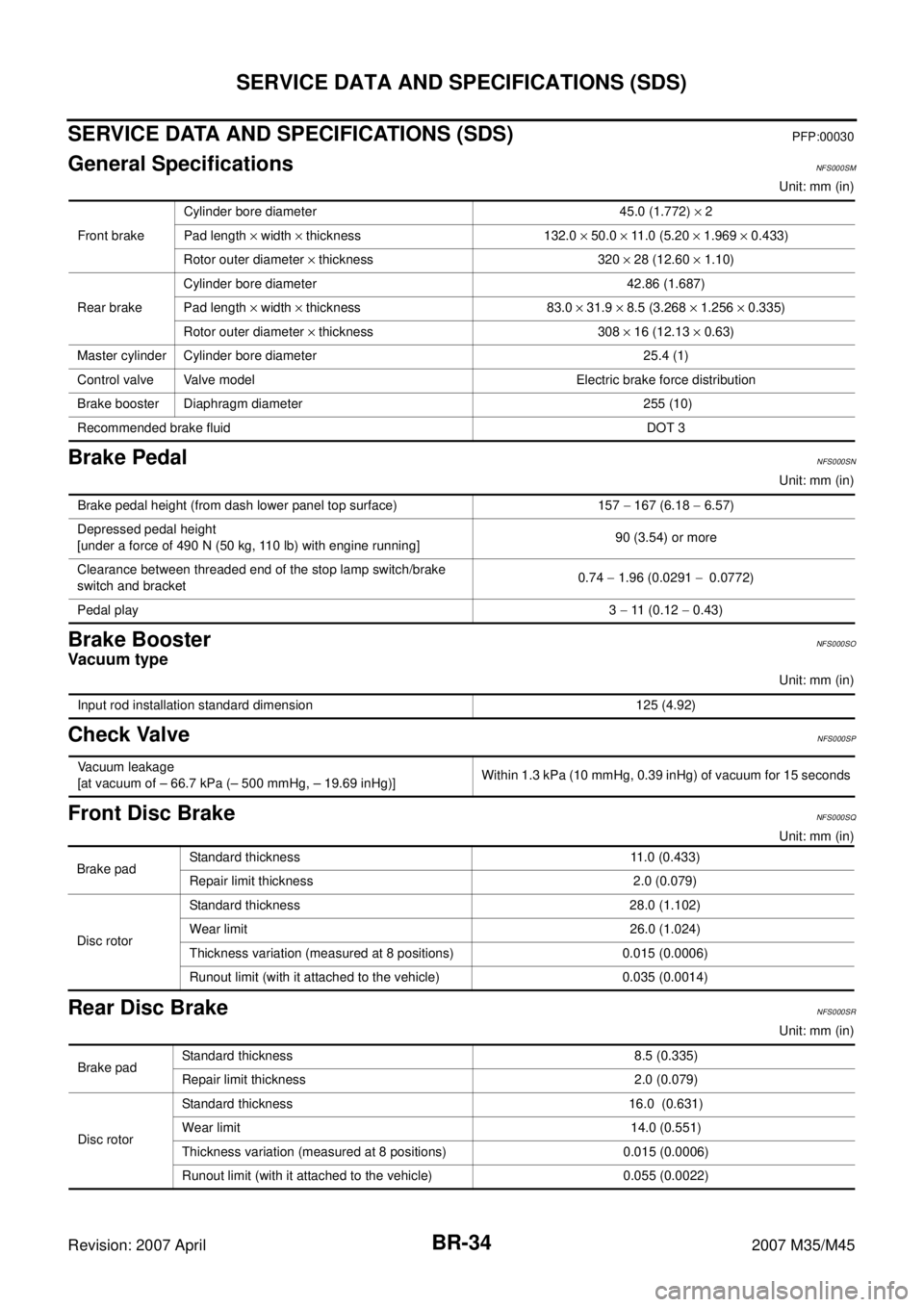
BR-34
SERVICE DATA AND SPECIFICATIONS (SDS)
Revision: 2007 April2007 M35/M45
SERVICE DATA AND SPECIFICATIONS (SDS)PFP:00030
General SpecificationsNFS000SM
Unit: mm (in)
Brake PedalNFS000SN
Unit: mm (in)
Brake BoosterNFS000SO
Vacuum type
Unit: mm (in)
Check ValveNFS000SP
Front Disc BrakeNFS000SQ
Unit: mm (in)
Rear Disc BrakeNFS000SR
Unit: mm (in) Front brakeCylinder bore diameter 45.0 (1.772) × 2
Pad length × width × thickness 132.0 × 50.0 × 11.0 (5.20 × 1.969 × 0.433)
Rotor outer diameter × thickness 320 × 28 (12.60 × 1.10)
Rear brake Cylinder bore diameter 42.86 (1.687)
Pad length × width × thickness 83.0 × 31.9 × 8.5 (3.268 × 1.256 × 0.335)
Rotor outer diameter × thickness 308 × 16 (12.13 × 0.63)
Master cylinder Cylinder bore diameter 25.4 (1)
Control valve Valve model Electric brake force distribution
Brake booster Diaphragm diameter 255 (10)
Recommended brake fluid DOT 3
Brake pedal height (from dash lower panel top surface) 157 − 167 (6.18 − 6.57)
Depressed pedal height
[under a force of 490 N (50 kg, 110 lb) with engine running]90 (3.54) or more
Clearance between threaded end of the stop lamp switch/brake
switch and bracket 0.74 − 1.96 (0.0291 −0.0772)
Pedal play3 − 11 (0.12 − 0.43)
Input rod installation standard dimension 125 (4.92)
Vacuum leakage
[at vacuum of – 66.7 kPa (– 500 mmHg, – 19.69 inHg)]Within 1.3 kPa (10 mmHg, 0.39 inHg) of vacuum for 15 seconds
Brake padStandard thickness 11.0 (0.433)
Repair limit thickness 2.0 (0.079)
Disc rotorStandard thickness 28.0 (1.102)
Wear limit 26.0 (1.024)
Thickness variation (measured at 8 positions) 0.015 (0.0006)
Runout limit (with it attached to the vehicle) 0.035 (0.0014)
Brake padStandard thickness 8.5 (0.335)
Repair limit thickness 2.0 (0.079)
Disc rotorStandard thickness 16.0 (0.631)
Wear limit 14.0 (0.551)
Thickness variation (measured at 8 positions) 0.015 (0.0006)
Runout limit (with it attached to the vehicle) 0.055 (0.0022)
Page 1302 of 4647
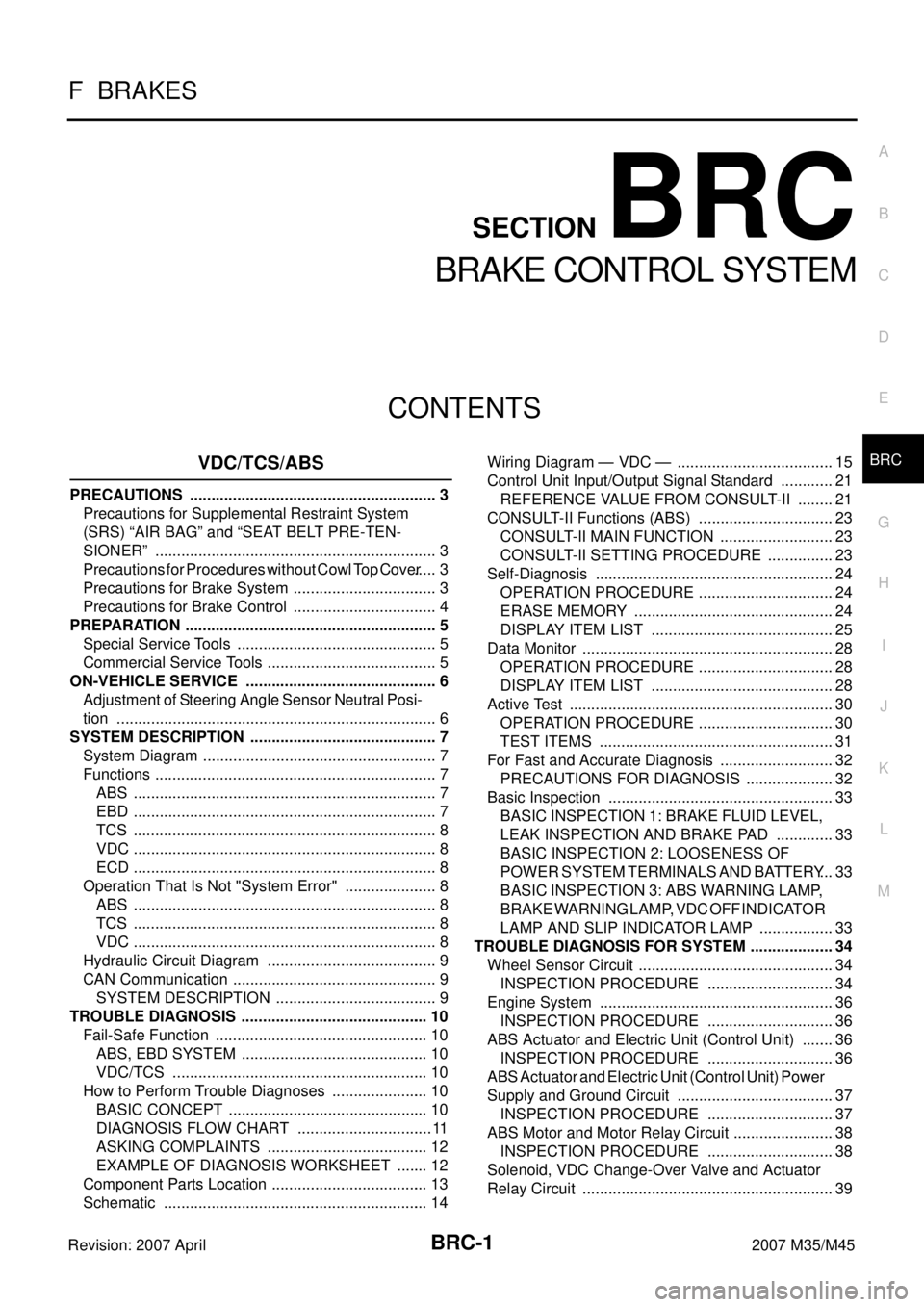
BRC-1
BRAKE CONTROL SYSTEM
F BRAKES
CONTENTS
C
D
E
G
H
I
J
K
L
M
SECTION BRC
A
B
BRC
Revision: 2007 April2007 M35/M45
BRAKE CONTROL SYSTEM
VDC/TCS/ABS
PRECAUTIONS .......................................................... 3
Precautions for Supplemental Restraint System
(SRS) “AIR BAG” and “SEAT BELT PRE-TEN-
SIONER” .................................................................. 3
Precautions for Procedures without Cowl Top Cover ..... 3
Precautions for Brake System .................................. 3
Precautions for Brake Control .................................. 4
PREPARATION ........................................................... 5
Special Service Tools ............................................... 5
Commercial Service Tools ........................................ 5
ON-VEHICLE SERVICE ............................................. 6
Adjustment of Steering Angle Sensor Neutral Posi-
tion ........................................................................... 6
SYSTEM DESCRIPTION ............................................ 7
System Diagram ....................................................... 7
Functions .................................................................. 7
ABS ....................................................................... 7
EBD ....................................................................... 7
TCS ....................................................................... 8
VDC ....................................................................... 8
ECD ....................................................................... 8
Operation That Is Not "System Error" ...................... 8
ABS ....................................................................... 8
TCS ....................................................................... 8
VDC ....................................................................... 8
Hydraulic Circuit Diagram ........................................ 9
CAN Communication ................................................ 9
SYSTEM DESCRIPTION ...................................... 9
TROUBLE DIAGNOSIS ............................................ 10
Fail-Safe Function .................................................. 10
ABS, EBD SYSTEM ............................................ 10
VDC/TCS ............................................................ 10
How to Perform Trouble Diagnoses ....................... 10
BASIC CONCEPT ............................................... 10
DIAGNOSIS FLOW CHART ................................ 11
ASKING COMPLAINTS ...................................... 12
EXAMPLE OF DIAGNOSIS WORKSHEET ........ 12
Component Parts Location ..................................... 13
Schematic .............................................................. 14Wiring Diagram — VDC — ..................................... 15
Control Unit Input/Output Signal Standard ............. 21
REFERENCE VALUE FROM CONSULT-II ......... 21
CONSULT-II Functions (ABS) ................................ 23
CONSULT-II MAIN FUNCTION ........................... 23
CONSULT-II SETTING PROCEDURE ................ 23
Self-Diagnosis ........................................................ 24
OPERATION PROCEDURE ................................ 24
ERASE MEMORY ............................................... 24
DISPLAY ITEM LIST ........................................... 25
Data Monitor ........................................................... 28
OPERATION PROCEDURE ................................ 28
DISPLAY ITEM LIST ........................................... 28
Active Test .............................................................. 30
OPERATION PROCEDURE ................................ 30
TEST ITEMS ....................................................... 31
For Fast and Accurate Diagnosis ........................... 32
PRECAUTIONS FOR DIAGNOSIS ..................... 32
Basic Inspection ..................................................... 33
BASIC INSPECTION 1: BRAKE FLUID LEVEL,
LEAK INSPECTION AND BRAKE PAD .............. 33
BASIC INSPECTION 2: LOOSENESS OF
POWER SYSTEM TERMINALS AND BATTERY ... 33
BASIC INSPECTION 3: ABS WARNING LAMP,
BRAKE WARNING LAMP, VDC OFF INDICATOR
LAMP AND SLIP INDICATOR LAMP .................. 33
TROUBLE DIAGNOSIS FOR SYSTEM .................... 34
Wheel Sensor Circuit .............................................. 34
INSPECTION PROCEDURE .............................. 34
Engine System ....................................................... 36
INSPECTION PROCEDURE .............................. 36
ABS Actuator and Electric Unit (Control Unit) ........ 36
INSPECTION PROCEDURE .............................. 36
ABS Actuator and Electric Unit (Control Unit) Power
Supply and Ground Circuit ..................................... 37
INSPECTION PROCEDURE .............................. 37
ABS Motor and Motor Relay Circuit ........................ 38
INSPECTION PROCEDURE .............................. 38
Solenoid, VDC Change-Over Valve and Actuator
Relay Circuit ........................................................... 39
Page 1303 of 4647
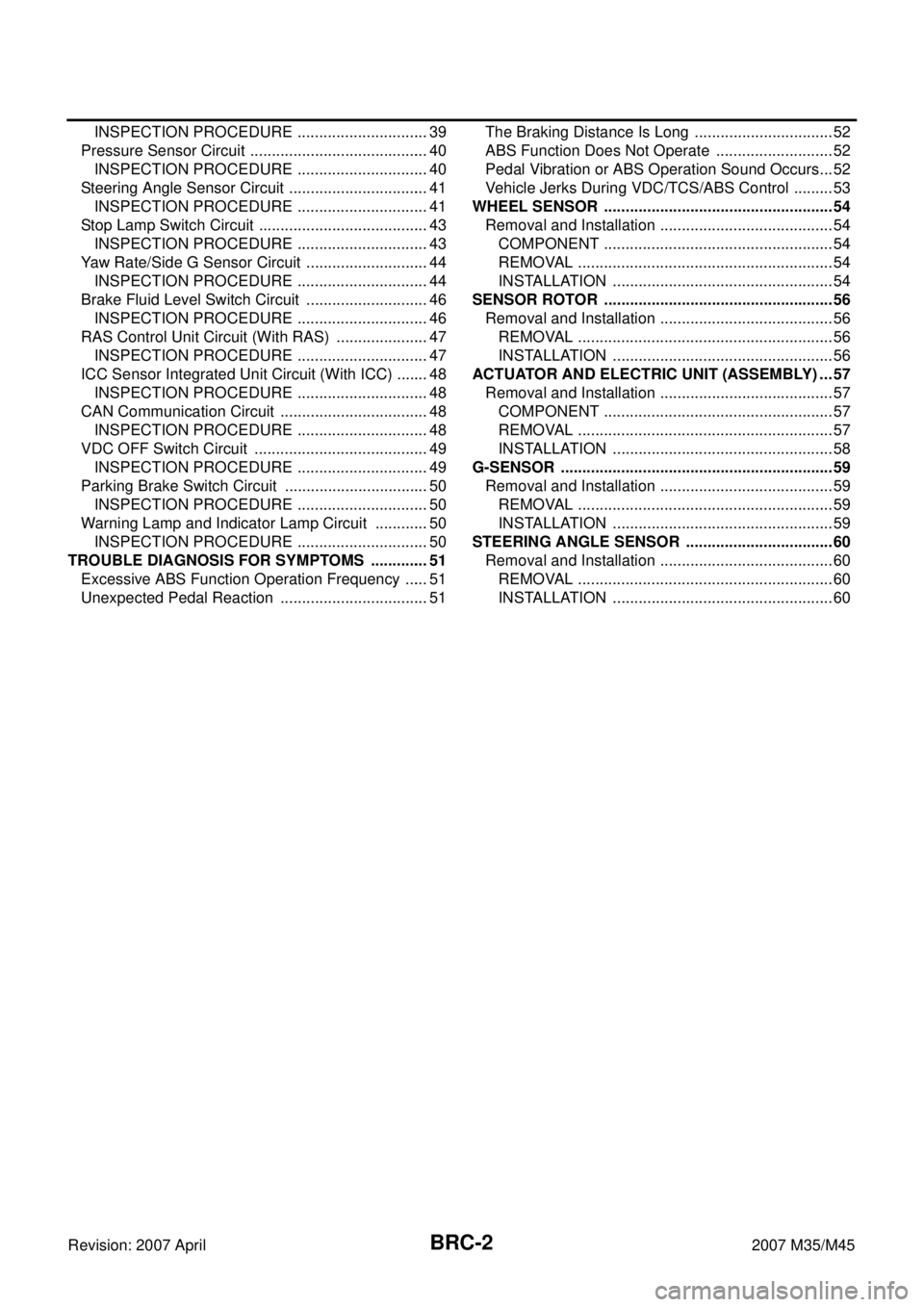
BRC-2Revision: 2007 April2007 M35/M45 INSPECTION PROCEDURE ............................... 39
Pressure Sensor Circuit .......................................... 40
INSPECTION PROCEDURE ............................... 40
Steering Angle Sensor Circuit ................................. 41
INSPECTION PROCEDURE ............................... 41
Stop Lamp Switch Circuit ........................................ 43
INSPECTION PROCEDURE ............................... 43
Yaw Rate/Side G Sensor Circuit ............................. 44
INSPECTION PROCEDURE ............................... 44
Brake Fluid Level Switch Circuit ............................. 46
INSPECTION PROCEDURE ............................... 46
RAS Control Unit Circuit (With RAS) ...................... 47
INSPECTION PROCEDURE ............................... 47
ICC Sensor Integrated Unit Circuit (With ICC) ........ 48
INSPECTION PROCEDURE ............................... 48
CAN Communication Circuit ................................... 48
INSPECTION PROCEDURE ............................... 48
VDC OFF Switch Circuit ......................................... 49
INSPECTION PROCEDURE ............................... 49
Parking Brake Switch Circuit .................................. 50
INSPECTION PROCEDURE ............................... 50
Warning Lamp and Indicator Lamp Circuit ............. 50
INSPECTION PROCEDURE ............................... 50
TROUBLE DIAGNOSIS FOR SYMPTOMS .............. 51
Excessive ABS Function Operation Frequency ...... 51
Unexpected Pedal Reaction ................................... 51The Braking Distance Is Long ................................. 52
ABS Function Does Not Operate ............................ 52
Pedal Vibration or ABS Operation Sound Occurs ... 52
Vehicle Jerks During VDC/TCS/ABS Control .......... 53
WHEEL SENSOR ...................................................... 54
Removal and Installation ......................................... 54
COMPONENT ...................................................... 54
REMOVAL ............................................................ 54
INSTALLATION .................................................... 54
SENSOR ROTOR ...................................................... 56
Removal and Installation ......................................... 56
REMOVAL ............................................................ 56
INSTALLATION .................................................... 56
ACTUATOR AND ELECTRIC UNIT (ASSEMBLY) ... 57
Removal and Installation ......................................... 57
COMPONENT ...................................................... 57
REMOVAL ............................................................ 57
INSTALLATION .................................................... 58
G-SENSOR ................................................................ 59
Removal and Installation ......................................... 59
REMOVAL ............................................................ 59
INSTALLATION .................................................... 59
STEERING ANGLE SENSOR ................................... 60
Removal and Installation ......................................... 60
REMOVAL ............................................................ 60
INSTALLATION .................................................... 60
Page 1304 of 4647
![INFINITI M35 2007 Factory Service Manual PRECAUTIONS
BRC-3
[VDC/TCS/ABS]
C
D
E
G
H
I
J
K
L
MA
B
BRC
Revision: 2007 April2007 M35/M45
[VDC/TCS/ABS]PRECAUTIONSPFP:00001
Precautions for Supplemental Restraint System (SRS) “AIR BAG” and “S INFINITI M35 2007 Factory Service Manual PRECAUTIONS
BRC-3
[VDC/TCS/ABS]
C
D
E
G
H
I
J
K
L
MA
B
BRC
Revision: 2007 April2007 M35/M45
[VDC/TCS/ABS]PRECAUTIONSPFP:00001
Precautions for Supplemental Restraint System (SRS) “AIR BAG” and “S](/manual-img/42/57024/w960_57024-1303.png)
PRECAUTIONS
BRC-3
[VDC/TCS/ABS]
C
D
E
G
H
I
J
K
L
MA
B
BRC
Revision: 2007 April2007 M35/M45
[VDC/TCS/ABS]PRECAUTIONSPFP:00001
Precautions for Supplemental Restraint System (SRS) “AIR BAG” and “SEAT
BELT PRE-TENSIONER”
NFS000PY
The Supplemental Restraint System such as “AIR BAG” and “SEAT BELT PRE-TENSIONER”, used along
with a front seat belt, helps to reduce the risk or severity of injury to the driver and front passenger for certain
types of collision. This system includes seat belt switch inputs and dual stage front air bag modules. The SRS
system uses the seat belt switches to determine the front air bag deployment, and may only deploy one front
air bag, depending on the severity of a collision and whether the front occupants are belted or unbelted.
Information necessary to service the system safely is included in the SRS and SB section of this Service Man-
ual.
WARNING:
To avoid rendering the SRS inoperative, which could increase the risk of personal injury or death
in the event of a collision which would result in air bag inflation, all maintenance must be per-
formed by an authorized NISSAN/INFINITI dealer.
Improper maintenance, including incorrect removal and installation of the SRS, can lead to per-
sonal injury caused by unintentional activation of the system. For removal of Spiral Cable and Air
Bag Module, see the SRS section.
Do not use electrical test equipment on any circuit related to the SRS unless instructed to in this
Service Manual. SRS wiring harnesses can be identified by yellow and/or orange harnesses or
harness connectors.
Precautions for Procedures without Cowl Top CoverNFS000PZ
When performing the procedure after removing cowl top cover, cover
the lower end of windshield with urethane, etc.
Precautions for Brake SystemNFS000Q0
Recommended fluid is brake fluid “DOT 3”. Refer to MA-12, "RECOMMENDED FLUIDS AND LUBRI-
CANTS" .
Do not reuse drained brake fluid.
Be careful not to splash brake fluid on painted surface of body. If brake fluid is splashed on painted sur-
faces of body immediately wipe off then with cloth and then wash it away with water.
Do not use mineral oils such as gasoline or kerosene. They will ruin rubber parts of the hydraulic system.
Use a flare nut wrench when removing flare nuts, and use a flare
nut crowfoot and torque wrench when tighten brake tube flare
nuts.
When installing brake tubes, be sure to check torque.
Brake system is an important safety part. If a brake fluid leak is
detected, always disassemble the affected part. If a malfunction
is detected, replace part with a new one.
Before working, turn ignition switch OFF and disconnect con-
nectors of ABS actuator and electric unit (control unit) or battery
negative terminal.
WARNING:
Clean brake pads and shoes with a waste cloth, then wipe with a dust collector.
PIIB3706J
SBR686C