Page 1233 of 4647
BL-300
BODY REPAIR
Revision: 2007 April2007 M35/M45
Measurement Points
SIIA2466E
Page 1234 of 4647
BODY REPAIR
BL-301
C
D
E
F
G
H
J
K
L
MA
B
BL
Revision: 2007 April2007 M35/M45
REAR BODY
Measurement
SIIA2467E
Page 1235 of 4647
BL-302
BODY REPAIR
Revision: 2007 April2007 M35/M45
Measurement Points
SIIA2468E
Page 1236 of 4647

BODY REPAIR
BL-303
C
D
E
F
G
H
J
K
L
MA
B
BL
Revision: 2007 April2007 M35/M45
Handling Precautions for PlasticsNIS00213
HANDLING PRECAUTIONS FOR PLASTICS
1. When repairing and painting a portion of the body adjacent to plastic parts, consider their characteristics
(influence of heat and solvent) and remove them if necessary or take suitable measures to protect them.
2. Plastic parts should be repaired and painted using methods suiting the materials′ characteristics.
Abbre-
viationMaterial nameHeat
resisting
temperature
°C(°F)Resistance to gasoline and
solventsOther cautions
PE Polyethylene 60(140)Gasoline and most solvents are
harmless if applied for a very
short time (wipe up quickly).Flammable
PVC Poly Vinyl Chloride 80(176) Same as above.Poison gas is emitted
when burned.
EPM/
EPDMEthylene Propylene (Diene)
copolymer80(176) Same as above. Flammable
TPO Thermoplastic Olefine 80(176) Same as above. Flammable
PP Polypropylene 90(194) Same as above.Flammable, avoid
battery acid.
UP Unsaturated Polyester 90(194) Same as above. Flammable
PS Polystyrene 80(176) Avoid solvents. Flammable
ABS Acrylonitrile Butadiene Styrene 80(176) Avoid gasoline and solvents.
AES Acrylonitrile Ethylene Styrene 80(176) Same as above.
PMMA Poly Methyl Methacrylate 85(185) Same as above.
EVAC Ethylene Vinyl Acetate 90(194) Same as above.
ASA Acrylonitrile Styrene Acrylate 100(222) Same as above. Flammable
PPE Poly Phenylene Ether 110(230) Same as above.
PC Polycarbonate 120(248) Same as above.
PAR Polyarylate 180(356) Same as above.
PUR Polyurethane 90(194) Same as above.
POM Poly Oxymethylene 120(248) Same as above. Avoid battery acid.
PBT+
PCPoly Butylene Terephthalate +
Polycarbonate120(248) Same as above. Flammable
PA Polyamide 140(284) Same as above.Avoid immersing in
water.
PBT Poly Butylene Terephthalate 140(284) Same as above.
PET Polyester 180(356) Same as above.
PEI Polyetherimide 200(392) Same as above.
Page 1237 of 4647
BL-304
BODY REPAIR
Revision: 2007 April2007 M35/M45
LOCATION OF PLASTIC PARTS
SIIA2737E
Page 1238 of 4647
BODY REPAIR
BL-305
C
D
E
F
G
H
J
K
L
MA
B
BL
Revision: 2007 April2007 M35/M45
SIIA2470E
Page 1239 of 4647
BL-306
BODY REPAIR
Revision: 2007 April2007 M35/M45
Precautions in Repairing High Strength SteelNIS00214
High strength steel is used for body panels in order to reduce vehicle weight.
Accordingly, precautions in repairing automotive bodies made of high strength steel are described below:
HIGH STRENGTH STEEL (HSS) USED IN NISSAN VEHICLES
SP130 is the most commonly used HSS.
SP150 HSS is used only on parts that require much more strength.Tensile strength Nissan/Infiniti designation Major applicable parts
373 N/mm
2
(38kg/mm2 ,54klb/sq in)SP130
Front & rear side member assembly
Front side member closing plate assembly
Front strut housing
Lower dash
Rear seat crossmember
Other reinforcements
785-1350 N/mm
2
(80-138kg/mm2 , 114-196klb/sq in)SP150
Center pillar reinforcement
(Component part)
Outer roof side rail reinforcement
(Component part)
Page 1240 of 4647
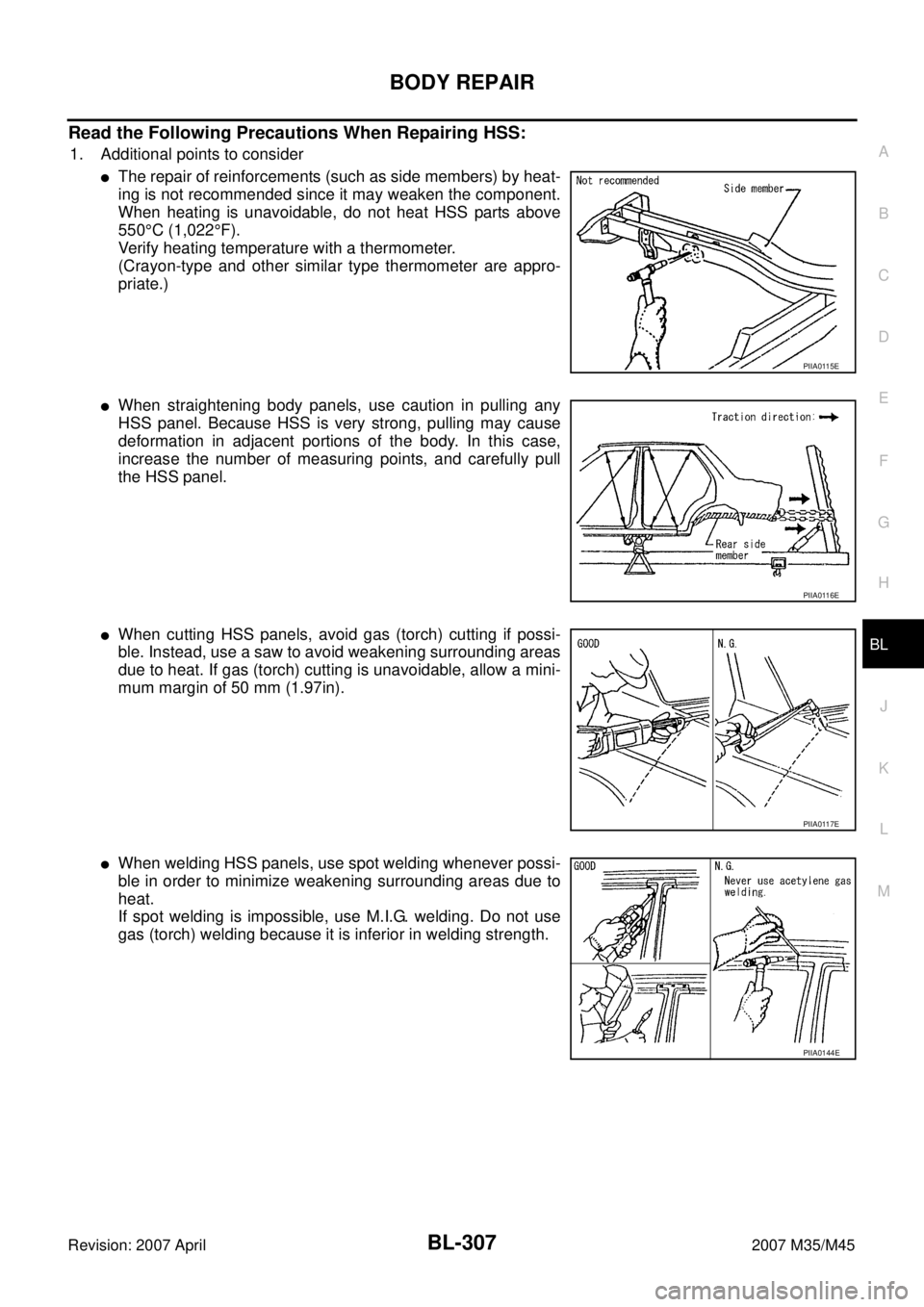
BODY REPAIR
BL-307
C
D
E
F
G
H
J
K
L
MA
B
BL
Revision: 2007 April2007 M35/M45
Read the Following Precautions When Repairing HSS:
1. Additional points to consider
The repair of reinforcements (such as side members) by heat-
ing is not recommended since it may weaken the component.
When heating is unavoidable, do not heat HSS parts above
550°C (1,022°F).
Verify heating temperature with a thermometer.
(Crayon-type and other similar type thermometer are appro-
priate.)
When straightening body panels, use caution in pulling any
HSS panel. Because HSS is very strong, pulling may cause
deformation in adjacent portions of the body. In this case,
increase the number of measuring points, and carefully pull
the HSS panel.
When cutting HSS panels, avoid gas (torch) cutting if possi-
ble. Instead, use a saw to avoid weakening surrounding areas
due to heat. If gas (torch) cutting is unavoidable, allow a mini-
mum margin of 50 mm (1.97in).
When welding HSS panels, use spot welding whenever possi-
ble in order to minimize weakening surrounding areas due to
heat.
If spot welding is impossible, use M.I.G. welding. Do not use
gas (torch) welding because it is inferior in welding strength.
PIIA0115E
PIIA0116E
PIIA0117E
PIIA0144E