Page 3073 of 4647
FFD-18
FRONT FINAL DRIVE ASSEMBLY
Revision: 2007 April2007 M35/M45
4. If tooth contact is improperly adjusted, follow the procedure
below to adjust the pinion height (dimension X).
PDIA0667E
SDIA0517E
Page 3074 of 4647
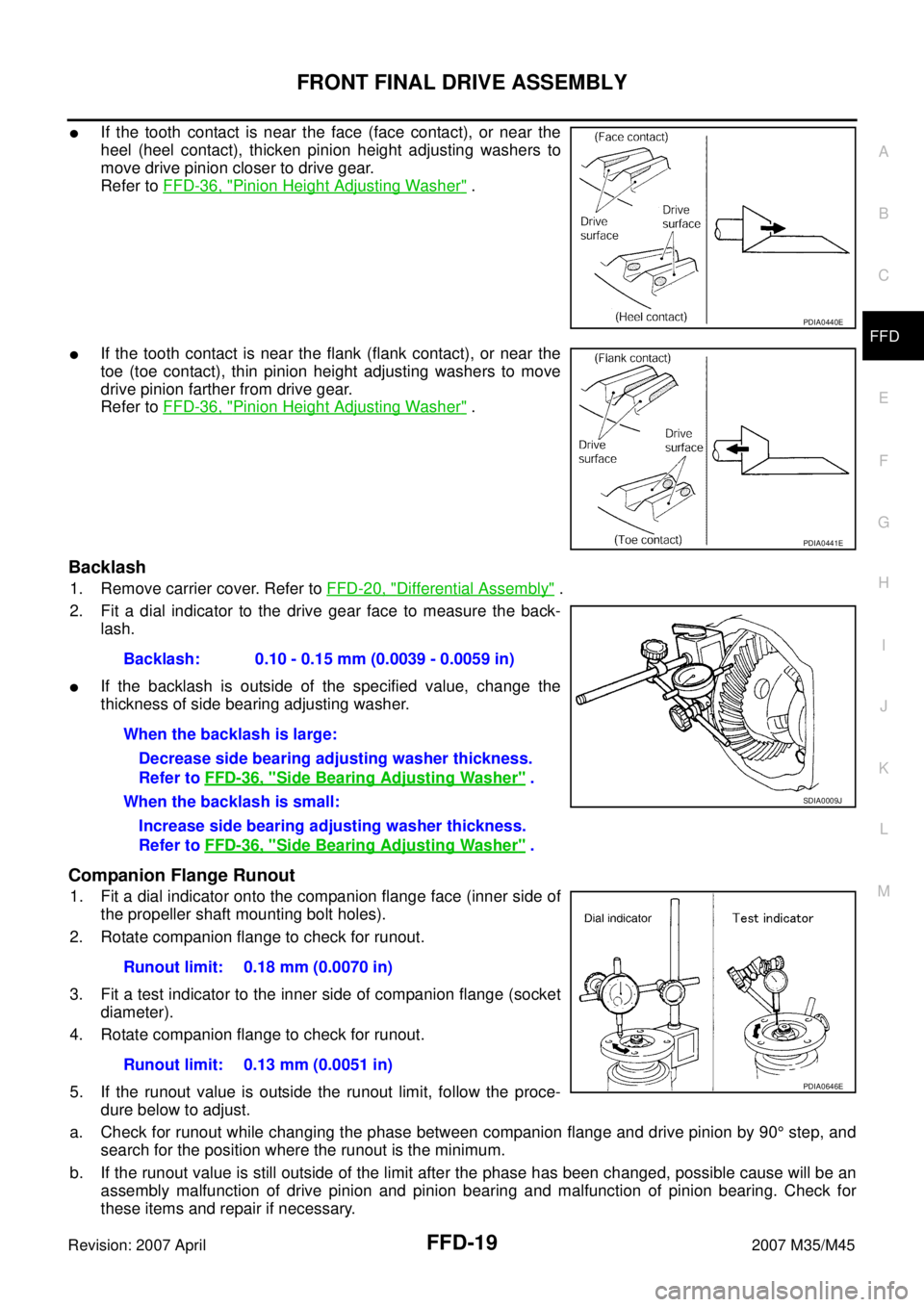
FRONT FINAL DRIVE ASSEMBLY
FFD-19
C
E
F
G
H
I
J
K
L
MA
B
FFD
Revision: 2007 April2007 M35/M45
If the tooth contact is near the face (face contact), or near the
heel (heel contact), thicken pinion height adjusting washers to
move drive pinion closer to drive gear.
Refer to FFD-36, "
Pinion Height Adjusting Washer" .
If the tooth contact is near the flank (flank contact), or near the
toe (toe contact), thin pinion height adjusting washers to move
drive pinion farther from drive gear.
Refer to FFD-36, "
Pinion Height Adjusting Washer" .
Backlash
1. Remove carrier cover. Refer to FFD-20, "Differential Assembly" .
2. Fit a dial indicator to the drive gear face to measure the back-
lash.
If the backlash is outside of the specified value, change the
thickness of side bearing adjusting washer.
Companion Flange Runout
1. Fit a dial indicator onto the companion flange face (inner side of
the propeller shaft mounting bolt holes).
2. Rotate companion flange to check for runout.
3. Fit a test indicator to the inner side of companion flange (socket
diameter).
4. Rotate companion flange to check for runout.
5. If the runout value is outside the runout limit, follow the proce-
dure below to adjust.
a. Check for runout while changing the phase between companion flange and drive pinion by 90° step, and
search for the position where the runout is the minimum.
b. If the runout value is still outside of the limit after the phase has been changed, possible cause will be an
assembly malfunction of drive pinion and pinion bearing and malfunction of pinion bearing. Check for
these items and repair if necessary.
PDIA0440E
PDIA0441E
Backlash: 0.10 - 0.15 mm (0.0039 - 0.0059 in)
When the backlash is large:
Decrease side bearing adjusting washer thickness.
Refer to FFD-36, "
Side Bearing Adjusting Washer" .
When the backlash is small:
Increase side bearing adjusting washer thickness.
Refer to FFD-36, "
Side Bearing Adjusting Washer" .
SDIA0009J
Runout limit: 0.18 mm (0.0070 in)
Runout limit: 0.13 mm (0.0051 in)
PDIA0646E
Page 3075 of 4647
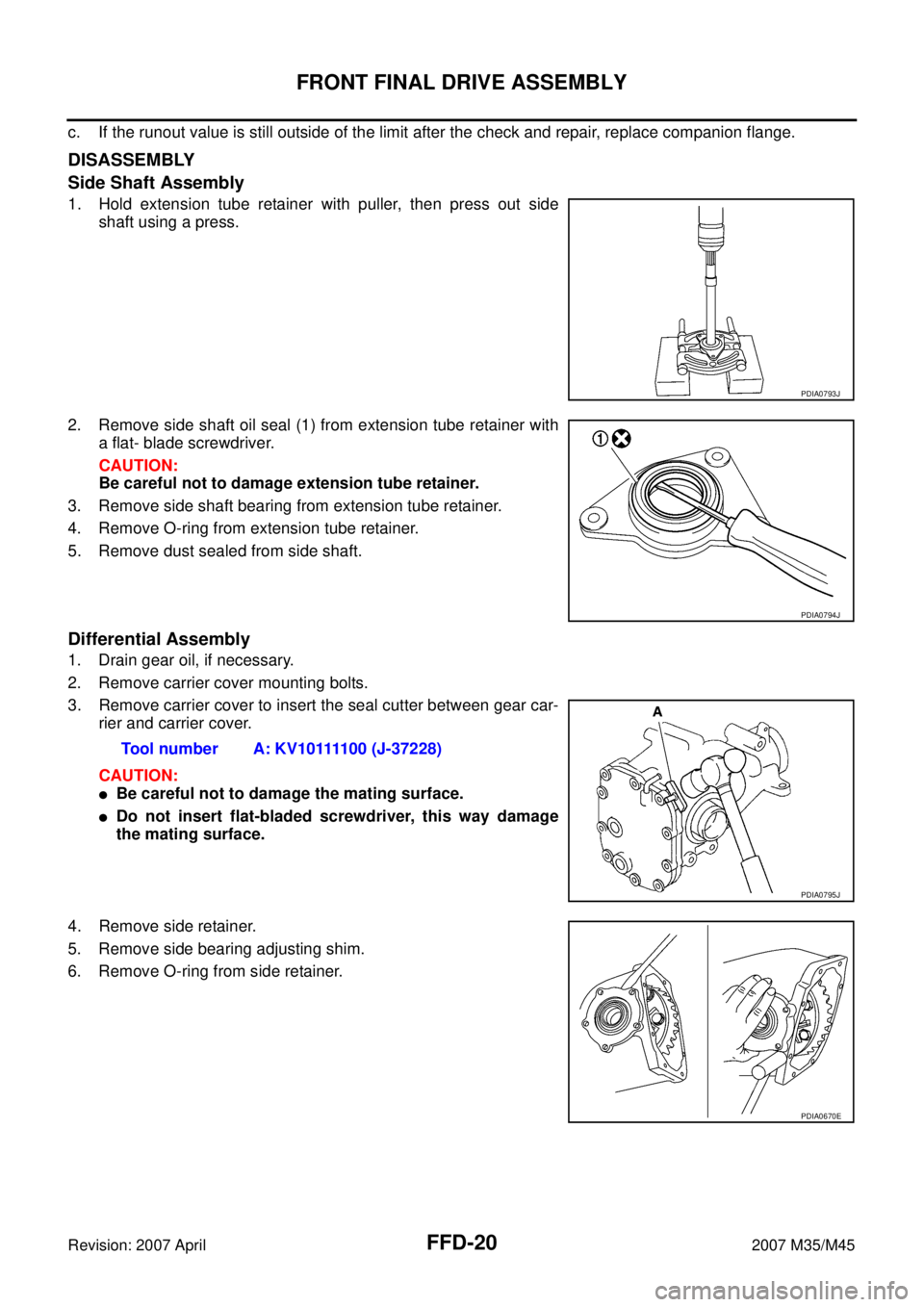
FFD-20
FRONT FINAL DRIVE ASSEMBLY
Revision: 2007 April2007 M35/M45
c. If the runout value is still outside of the limit after the check and repair, replace companion flange.
DISASSEMBLY
Side Shaft Assembly
1. Hold extension tube retainer with puller, then press out side
shaft using a press.
2. Remove side shaft oil seal (1) from extension tube retainer with
a flat- blade screwdriver.
CAUTION:
Be careful not to damage extension tube retainer.
3. Remove side shaft bearing from extension tube retainer.
4. Remove O-ring from extension tube retainer.
5. Remove dust sealed from side shaft.
Differential Assembly
1. Drain gear oil, if necessary.
2. Remove carrier cover mounting bolts.
3. Remove carrier cover to insert the seal cutter between gear car-
rier and carrier cover.
CAUTION:
Be careful not to damage the mating surface.
Do not insert flat-bladed screwdriver, this way damage
the mating surface.
4. Remove side retainer.
5. Remove side bearing adjusting shim.
6. Remove O-ring from side retainer.
PDIA0793J
PDIA0794J
Tool number A: KV10111100 (J-37228)
PDIA0795J
PDIA0670E
Page 3076 of 4647
FRONT FINAL DRIVE ASSEMBLY
FFD-21
C
E
F
G
H
I
J
K
L
MA
B
FFD
Revision: 2007 April2007 M35/M45
7. Remove differential case assembly from gear carrier.
8. Remove side oil seal (right side) from side retainer.
9. Remove side bearing outer race with puller.
10. Remove O-ring from gear carrier.
11. Remove side oil seal (left side) from gear carrier.
12. Remove side bearing outer race with puller.
PDIA0671E
PDIA0672E
Tool number A: KV381054S0 (J-34286)
PDIA0796J
Tool number A: KV381054S0 (J-34286)
PDIA0797J
Page 3077 of 4647
FFD-22
FRONT FINAL DRIVE ASSEMBLY
Revision: 2007 April2007 M35/M45
13. Remove side bearing inner race.
To prevent damage to bearing, engage puller jaws in groove
().
CAUTION:
To prevent damage to the side bearing and drive gear,
place copper plates between these parts and vise.
It is not necessary to remove side bearing inner race
except it is replaced.
14. For proper reinstallation, paint matching marks on one differen-
tial case assembly.
CAUTION:
For matching marks, use paint. Do not damage differential
case and drive gear.
15. Remove drive gear mounting bolts.
16. Tap drive gear off differential case assembly with a soft hammer.
CAUTION:
Tap evenly all around to keep drive gear from bending.
17. Remove lock pin of pinion mate shaft with a punch from drive
gear side.
18. Remove pinion mate shaft.Tool number A: ST33051001 (J-22888-20)
B: ST33061000 (J-8107-2)
PDIA0758J
PDIA0496E
PDIA0759J
SDIA0031J
Page 3078 of 4647
FRONT FINAL DRIVE ASSEMBLY
FFD-23
C
E
F
G
H
I
J
K
L
MA
B
FFD
Revision: 2007 April2007 M35/M45
19. Turn pinion mate gear, then remove pinion mate gears, pinion
mate thrust washers, side gears and side gear thrust washers
from differential case.
Drive Pinion Assembly
1. Remove differential assembly. Refer to FFD-20, "Differential Assembly" .
2. Remove drive pinion lock nut with a flange wrench.
3. Put matching mark (B) on the end of drive pinion. The matching
mark should be in line with the matching mark (A) on companion
flange (1).
CAUTION:
For matching mark, use paint. Do not damage companion
flange and drive pinion.
NOTE:
The matching mark (A) on the final drive companion flange (1)
indicates the maximum vertical runout position.
When replacing companion flange, matching mark is not neces-
sary.
4. Remove companion flange using the suitable puller.
SDIA0032J
PDIA0798J
PDIA0799J
SDIA1132E
Page 3079 of 4647
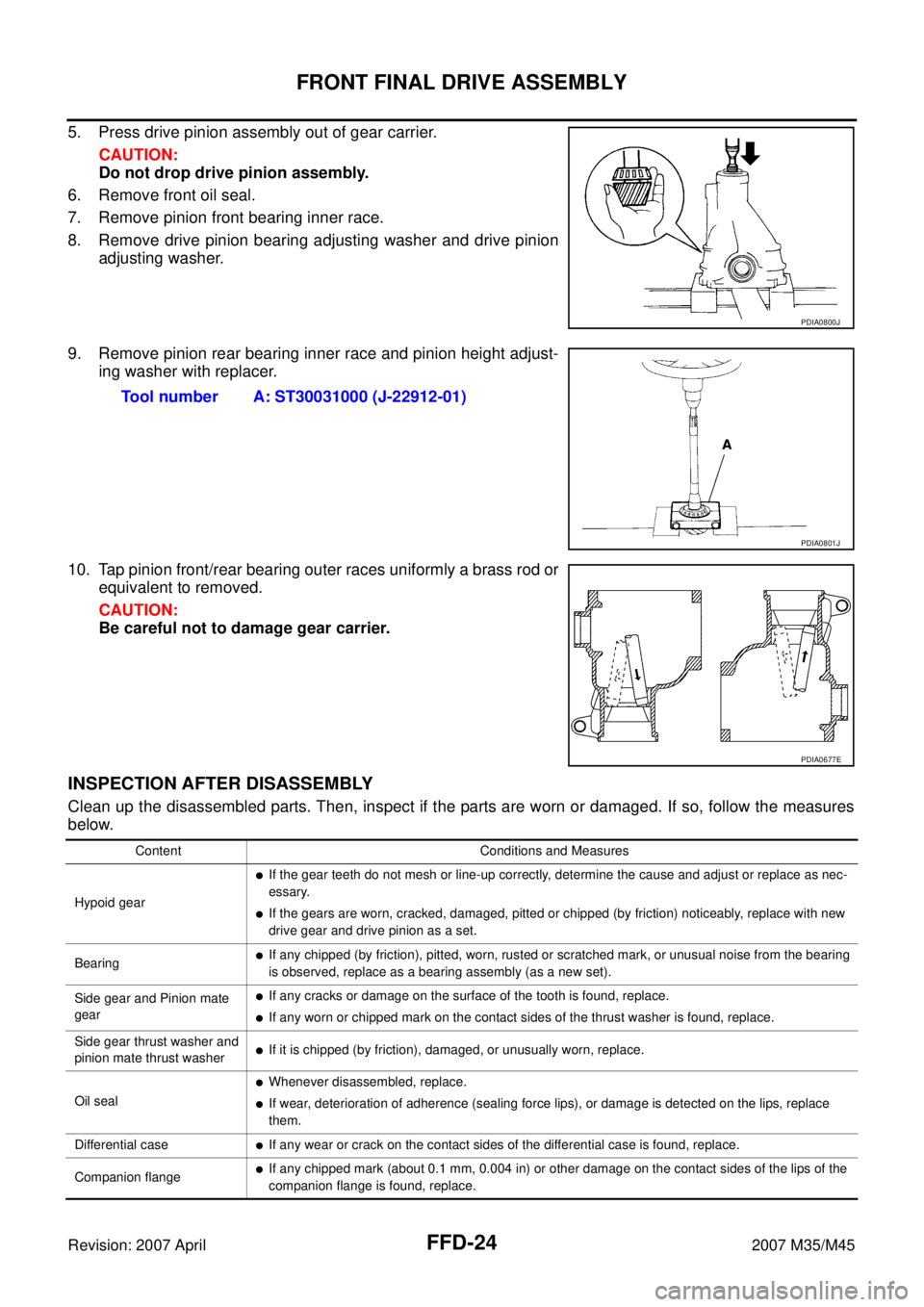
FFD-24
FRONT FINAL DRIVE ASSEMBLY
Revision: 2007 April2007 M35/M45
5. Press drive pinion assembly out of gear carrier.
CAUTION:
Do not drop drive pinion assembly.
6. Remove front oil seal.
7. Remove pinion front bearing inner race.
8. Remove drive pinion bearing adjusting washer and drive pinion
adjusting washer.
9. Remove pinion rear bearing inner race and pinion height adjust-
ing washer with replacer.
10. Tap pinion front/rear bearing outer races uniformly a brass rod or
equivalent to removed.
CAUTION:
Be careful not to damage gear carrier.
INSPECTION AFTER DISASSEMBLY
Clean up the disassembled parts. Then, inspect if the parts are worn or damaged. If so, follow the measures
below.
PDIA0800J
Tool number A: ST30031000 (J-22912-01)
PDIA0801J
PDIA0677E
Content Conditions and Measures
Hypoid gear
If the gear teeth do not mesh or line-up correctly, determine the cause and adjust or replace as nec-
essary.
If the gears are worn, cracked, damaged, pitted or chipped (by friction) noticeably, replace with new
drive gear and drive pinion as a set.
Bearing
If any chipped (by friction), pitted, worn, rusted or scratched mark, or unusual noise from the bearing
is observed, replace as a bearing assembly (as a new set).
Side gear and Pinion mate
gear
If any cracks or damage on the surface of the tooth is found, replace.
If any worn or chipped mark on the contact sides of the thrust washer is found, replace.
Side gear thrust washer and
pinion mate thrust washer
If it is chipped (by friction), damaged, or unusually worn, replace.
Oil seal
Whenever disassembled, replace.
If wear, deterioration of adherence (sealing force lips), or damage is detected on the lips, replace
them.
Differential case
If any wear or crack on the contact sides of the differential case is found, replace.
Companion flange
If any chipped mark (about 0.1 mm, 0.004 in) or other damage on the contact sides of the lips of the
companion flange is found, replace.
Page 3080 of 4647
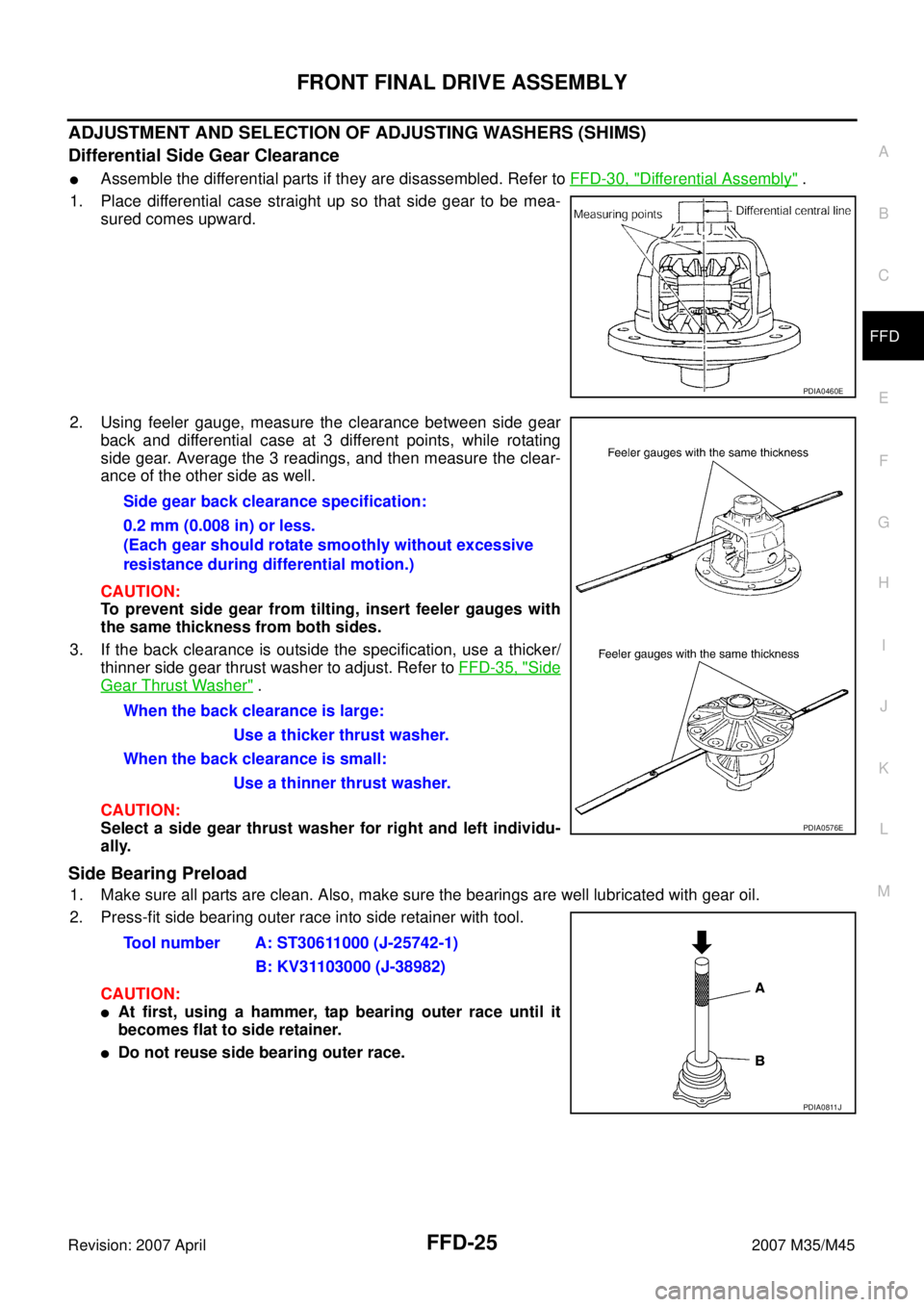
FRONT FINAL DRIVE ASSEMBLY
FFD-25
C
E
F
G
H
I
J
K
L
MA
B
FFD
Revision: 2007 April2007 M35/M45
ADJUSTMENT AND SELECTION OF ADJUSTING WASHERS (SHIMS)
Differential Side Gear Clearance
Assemble the differential parts if they are disassembled. Refer to FFD-30, "Differential Assembly" .
1. Place differential case straight up so that side gear to be mea-
sured comes upward.
2. Using feeler gauge, measure the clearance between side gear
back and differential case at 3 different points, while rotating
side gear. Average the 3 readings, and then measure the clear-
ance of the other side as well.
CAUTION:
To prevent side gear from tilting, insert feeler gauges with
the same thickness from both sides.
3. If the back clearance is outside the specification, use a thicker/
thinner side gear thrust washer to adjust. Refer to FFD-35, "
Side
Gear Thrust Washer" .
CAUTION:
Select a side gear thrust washer for right and left individu-
ally.
Side Bearing Preload
1. Make sure all parts are clean. Also, make sure the bearings are well lubricated with gear oil.
2. Press-fit side bearing outer race into side retainer with tool.
CAUTION:
At first, using a hammer, tap bearing outer race until it
becomes flat to side retainer.
Do not reuse side bearing outer race.
PDIA0460E
Side gear back clearance specification:
0.2 mm (0.008 in) or less.
(Each gear should rotate smoothly without excessive
resistance during differential motion.)
When the back clearance is large:
Use a thicker thrust washer.
When the back clearance is small:
Use a thinner thrust washer.
PDIA0576E
Tool number A: ST30611000 (J-25742-1)
B: KV31103000 (J-38982)
PDIA0811J