Page 1769 of 3371
EC-578Revision: August 2007
DTC P2138 APP SENSOR
2004 QX56
Wiring DiagramUBS00HCW
BBWA11 70 E
Page 1770 of 3371
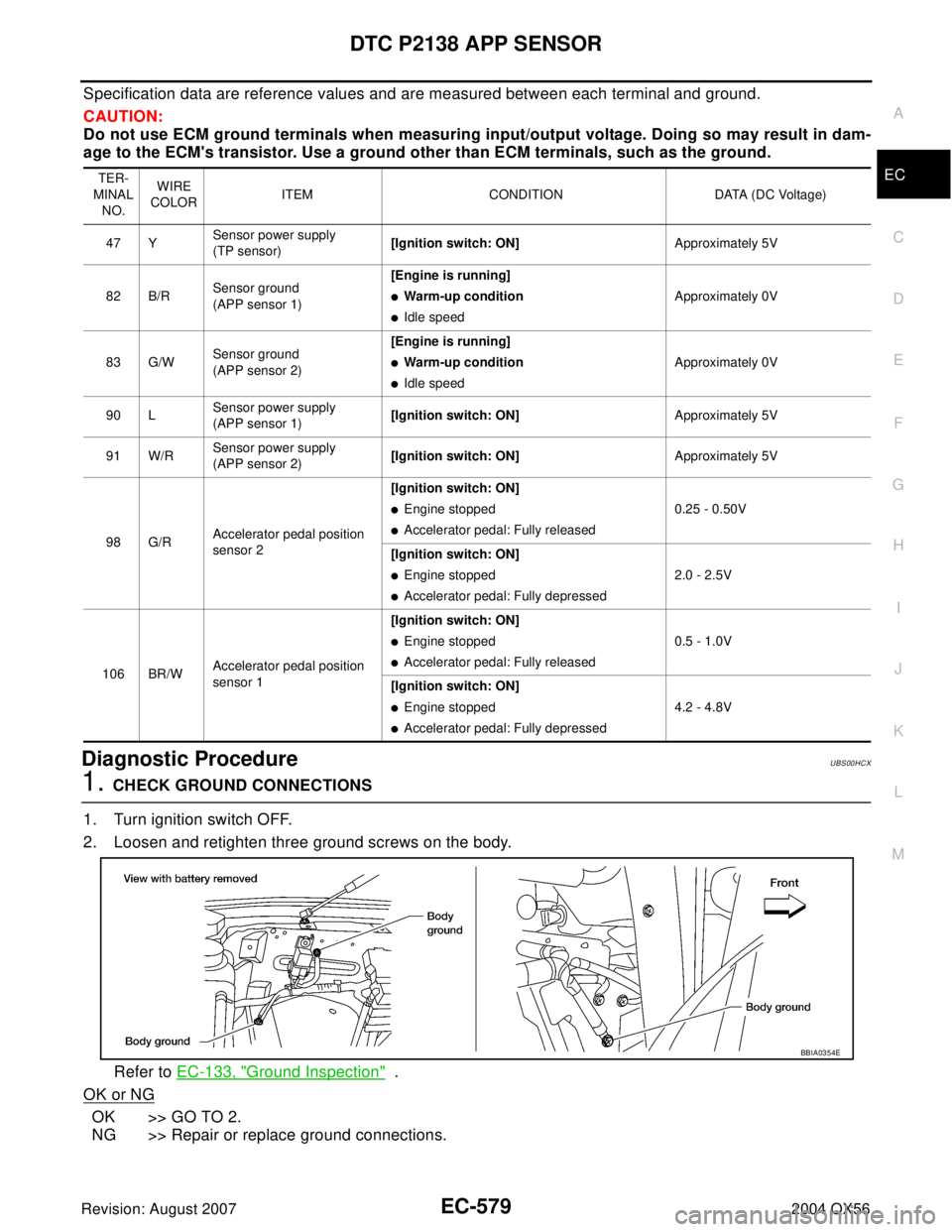
DTC P2138 APP SENSOR
EC-579
C
D
E
F
G
H
I
J
K
L
MA
EC
Revision: August 20072004 QX56
Specification data are reference values and are measured between each terminal and ground.
CAUTION:
Do not use ECM ground terminals when measuring input/output voltage. Doing so may result in dam-
age to the ECM's transistor. Use a ground other than ECM terminals, such as the ground.
Diagnostic ProcedureUBS00HCX
1. CHECK GROUND CONNECTIONS
1. Turn ignition switch OFF.
2. Loosen and retighten three ground screws on the body.
Refer to EC-133, "
Ground Inspection" .
OK or NG
OK >> GO TO 2.
NG >> Repair or replace ground connections.
TER-
MINAL
NO.WIRE
COLOR ITEM CONDITION DATA (DC Voltage)
47 YSensor power supply
(TP sensor)[Ignition switch: ON]Approximately 5V
82 B/RSensor ground
(APP sensor 1)[Engine is running]
Warm-up condition
Idle speedApproximately 0V
83 G/WSensor ground
(APP sensor 2)[Engine is running]
Warm-up condition
Idle speedApproximately 0V
90 LSensor power supply
(APP sensor 1)[Ignition switch: ON]Approximately 5V
91 W/RSensor power supply
(APP sensor 2)[Ignition switch: ON]Approximately 5V
98 G/RAccelerator pedal position
sensor 2[Ignition switch: ON]
Engine stopped
Accelerator pedal: Fully released0.25 - 0.50V
[Ignition switch: ON]
Engine stopped
Accelerator pedal: Fully depressed2.0 - 2.5V
106 BR/WAccelerator pedal position
sensor 1[Ignition switch: ON]
Engine stopped
Accelerator pedal: Fully released0.5 - 1.0V
[Ignition switch: ON]
Engine stopped
Accelerator pedal: Fully depressed4.2 - 4.8V
BBIA0354E
Page 1771 of 3371
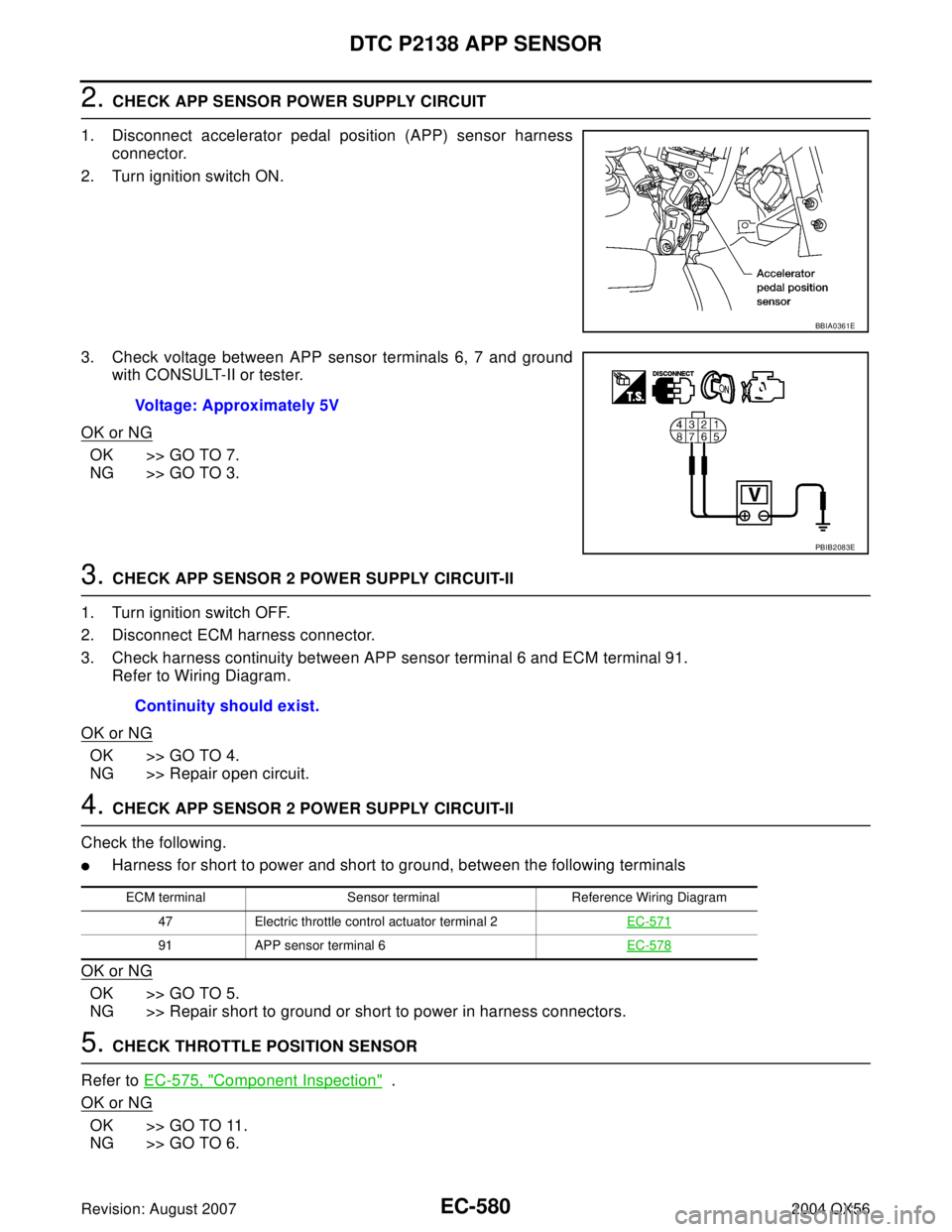
EC-580Revision: August 2007
DTC P2138 APP SENSOR
2004 QX56
2. CHECK APP SENSOR POWER SUPPLY CIRCUIT
1. Disconnect accelerator pedal position (APP) sensor harness
connector.
2. Turn ignition switch ON.
3. Check voltage between APP sensor terminals 6, 7 and ground
with CONSULT-II or tester.
OK or NG
OK >> GO TO 7.
NG >> GO TO 3.
3. CHECK APP SENSOR 2 POWER SUPPLY CIRCUIT-II
1. Turn ignition switch OFF.
2. Disconnect ECM harness connector.
3. Check harness continuity between APP sensor terminal 6 and ECM terminal 91.
Refer to Wiring Diagram.
OK or NG
OK >> GO TO 4.
NG >> Repair open circuit.
4. CHECK APP SENSOR 2 POWER SUPPLY CIRCUIT-II
Check the following.
Harness for short to power and short to ground, between the following terminals
OK or NG
OK >> GO TO 5.
NG >> Repair short to ground or short to power in harness connectors.
5. CHECK THROTTLE POSITION SENSOR
Refer to EC-575, "
Component Inspection" .
OK or NG
OK >> GO TO 11.
NG >> GO TO 6.
BBIA0361E
Voltage: Approximately 5V
PBIB2083E
Continuity should exist.
ECM terminal Sensor terminal Reference Wiring Diagram
47 Electric throttle control actuator terminal 2EC-571
91 APP sensor terminal 6EC-578
Page 1772 of 3371
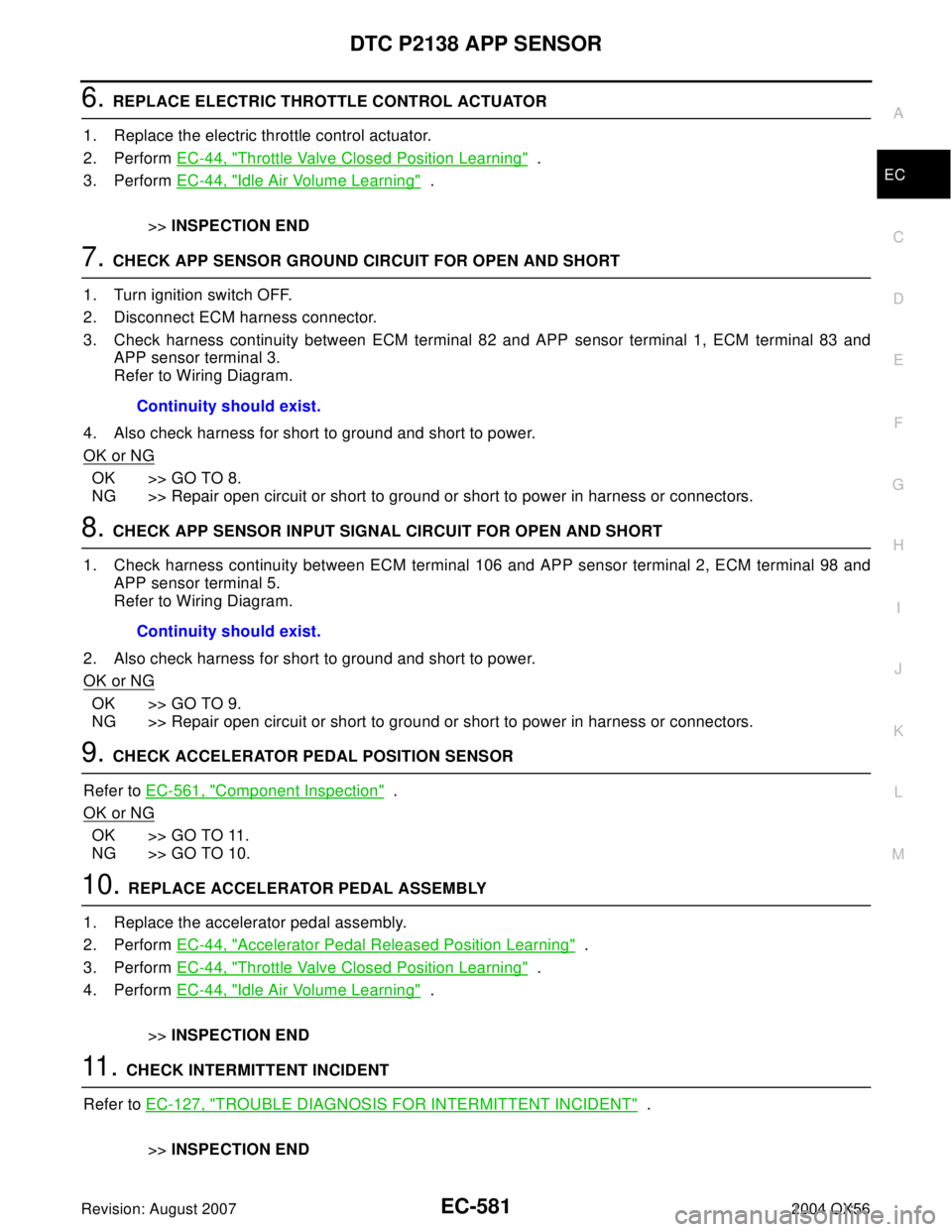
DTC P2138 APP SENSOR
EC-581
C
D
E
F
G
H
I
J
K
L
MA
EC
Revision: August 20072004 QX56
6. REPLACE ELECTRIC THROTTLE CONTROL ACTUATOR
1. Replace the electric throttle control actuator.
2. Perform EC-44, "
Throttle Valve Closed Position Learning" .
3. Perform EC-44, "
Idle Air Volume Learning" .
>>INSPECTION END
7. CHECK APP SENSOR GROUND CIRCUIT FOR OPEN AND SHORT
1. Turn ignition switch OFF.
2. Disconnect ECM harness connector.
3. Check harness continuity between ECM terminal 82 and APP sensor terminal 1, ECM terminal 83 and
APP sensor terminal 3.
Refer to Wiring Diagram.
4. Also check harness for short to ground and short to power.
OK or NG
OK >> GO TO 8.
NG >> Repair open circuit or short to ground or short to power in harness or connectors.
8. CHECK APP SENSOR INPUT SIGNAL CIRCUIT FOR OPEN AND SHORT
1. Check harness continuity between ECM terminal 106 and APP sensor terminal 2, ECM terminal 98 and
APP sensor terminal 5.
Refer to Wiring Diagram.
2. Also check harness for short to ground and short to power.
OK or NG
OK >> GO TO 9.
NG >> Repair open circuit or short to ground or short to power in harness or connectors.
9. CHECK ACCELERATOR PEDAL POSITION SENSOR
Refer to EC-561, "
Component Inspection" .
OK or NG
OK >> GO TO 11.
NG >> GO TO 10.
10. REPLACE ACCELERATOR PEDAL ASSEMBLY
1. Replace the accelerator pedal assembly.
2. Perform EC-44, "
Accelerator Pedal Released Position Learning" .
3. Perform EC-44, "
Throttle Valve Closed Position Learning" .
4. Perform EC-44, "
Idle Air Volume Learning" .
>>INSPECTION END
11 . CHECK INTERMITTENT INCIDENT
Refer to EC-127, "
TROUBLE DIAGNOSIS FOR INTERMITTENT INCIDENT" .
>>INSPECTION END Continuity should exist.
Continuity should exist.
Page 1773 of 3371
EC-582Revision: August 2007
DTC P2138 APP SENSOR
2004 QX56
Component InspectionUBS00HCY
ACCELERATOR PEDAL POSITION SENSOR
1. Reconnect all harness connectors disconnected.
2. Turn ignition switch ON.
3. Check voltage between ECM terminals 106 (APP sensor 1 sig-
nal), 98 (APP sensor 2 signal) and ground under the following
conditions.
4. If NG, replace accelerator pedal assembly and go to next step.
5. Perform EC-44, "
Accelerator Pedal Released Position Learning" .
6. Perform EC-44, "
Throttle Valve Closed Position Learning" .
7. Perform EC-44, "
Idle Air Volume Learning" .
Removal and InstallationUBS00HCZ
ACCELERATOR PEDAL
Refer to ACC-2, "ACCELERATOR CONTROL SYSTEM" .
Terminal Accelerator pedal Voltage
106
(Accelerator pedal position
sensor 1)Fully released 0.5 - 1.0V
Fully depressed 4.2 - 4.8V
98
(Accelerator pedal position
sensor 2)Fully released 0.25 - 0.5V
Fully depressed 2.0 - 2.5V
MBIB0023E
Page 1774 of 3371
IGNITION SIGNAL
EC-583
C
D
E
F
G
H
I
J
K
L
MA
EC
Revision: August 20072004 QX56
IGNITION SIGNALPFP:22448
Component DescriptionUBS00HD0
IGNITION COIL & POWER TRANSISTOR
The ignition signal from the ECM is sent to and amplified by the power transistor. The power transistor turns
on and off the ignition coil primary circuit. This ON/OFF operation induces the proper high voltage in the coil
secondary circuit.
BBIA0359E
Page 1775 of 3371
EC-584Revision: August 2007
IGNITION SIGNAL
2004 QX56
Wiring DiagramUBS00HD1
BBWA1710E
Page 1776 of 3371
IGNITION SIGNAL
EC-585
C
D
E
F
G
H
I
J
K
L
MA
EC
Revision: August 20072004 QX56
Specification data are reference values and are measured between each terminal and ground.
CAUTION:
Do not use ECM ground terminals when measuring input/output voltage. Doing so may result in dam-
age to the ECM's transistor. Use a ground other than ECM terminals, such as the ground.
TER-
MINAL
NO.WIRE
COLORITEM CONDITION DATA (DC Voltage)
111 W / BECM relay
(Self shut-off)[Engine is running]
[Ignition switch: OFF]
For a few seconds after turning ignition
switch OFF0 - 1.5V
[Ignition switch: OFF]
More than a few seconds after turning igni-
tion switch OFFBATTERY VOLTAGE
(11 - 14V)
11 9
120BR
BRPower supply for ECM[Ignition switch: ON]BATTERY VOLTAGE
(11 - 14V)