Page 2041 of 3371
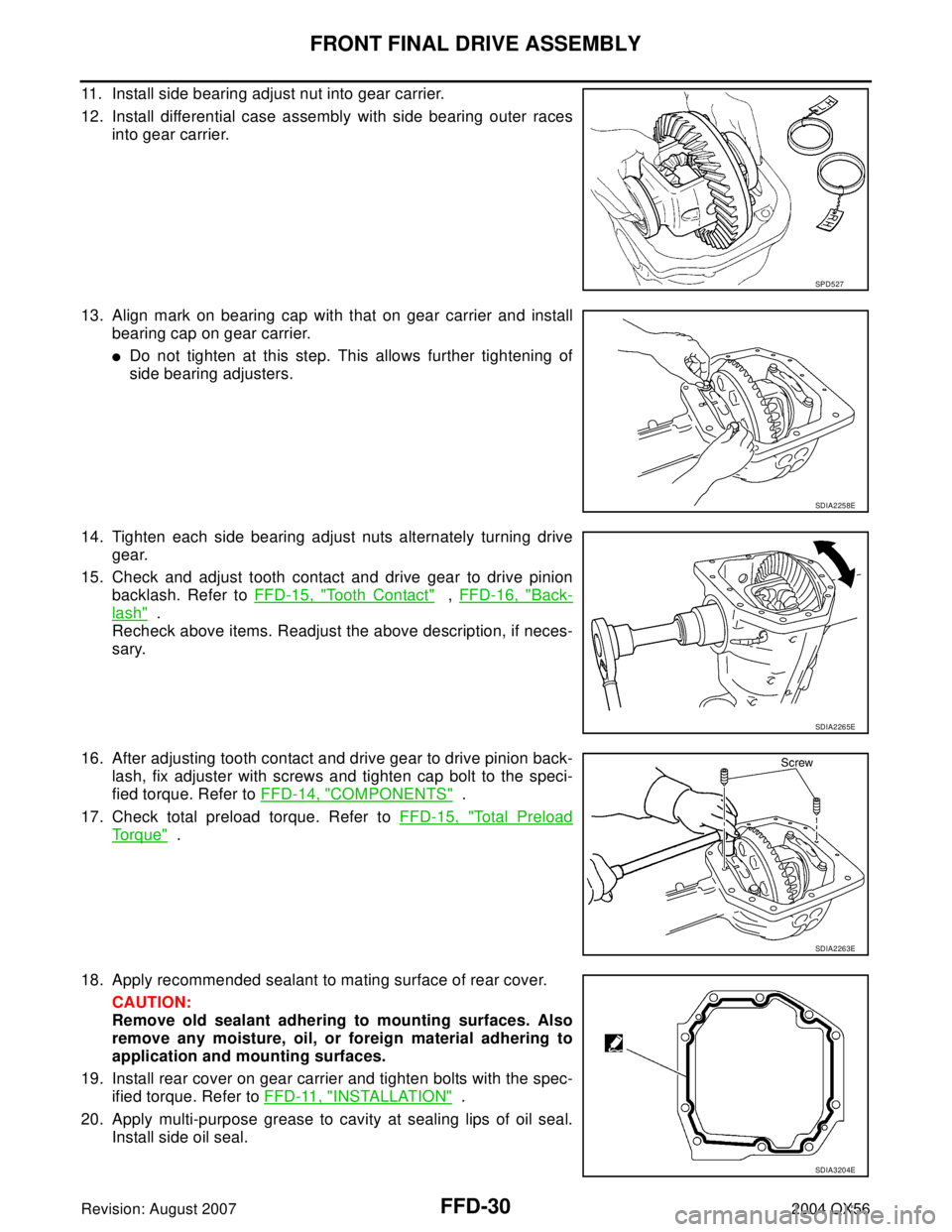
FFD-30
FRONT FINAL DRIVE ASSEMBLY
Revision: August 20072004 QX56
11. Install side bearing adjust nut into gear carrier.
12. Install differential case assembly with side bearing outer races
into gear carrier.
13. Align mark on bearing cap with that on gear carrier and install
bearing cap on gear carrier.
Do not tighten at this step. This allows further tightening of
side bearing adjusters.
14. Tighten each side bearing adjust nuts alternately turning drive
gear.
15. Check and adjust tooth contact and drive gear to drive pinion
backlash. Refer to FFD-15, "
Tooth Contact" , FFD-16, "Back-
lash" .
Recheck above items. Readjust the above description, if neces-
sary.
16. After adjusting tooth contact and drive gear to drive pinion back-
lash, fix adjuster with screws and tighten cap bolt to the speci-
fied torque. Refer to FFD-14, "
COMPONENTS" .
17. Check total preload torque. Refer to FFD-15, "
Total Preload
To r q u e" .
18. Apply recommended sealant to mating surface of rear cover.
CAUTION:
Remove old sealant adhering to mounting surfaces. Also
remove any moisture, oil, or foreign material adhering to
application and mounting surfaces.
19. Install rear cover on gear carrier and tighten bolts with the spec-
ified torque. Refer to FFD-11, "
INSTALLATION" .
20. Apply multi-purpose grease to cavity at sealing lips of oil seal.
Install side oil seal.
SPD5 27
SDIA2258E
SDIA2265E
SDIA2263E
SDIA3204E
Page 2042 of 3371
FRONT FINAL DRIVE ASSEMBLY
FFD-31
C
E
F
G
H
I
J
K
L
MA
B
FFD
Revision: August 20072004 QX56
21. Install new O-ring and extension tube.
CAUTION:
If the extension tube is being replaced, install a new axle
shaft bearing.
22. Install side shaft and side flange.
SDIA3205E
Page 2043 of 3371
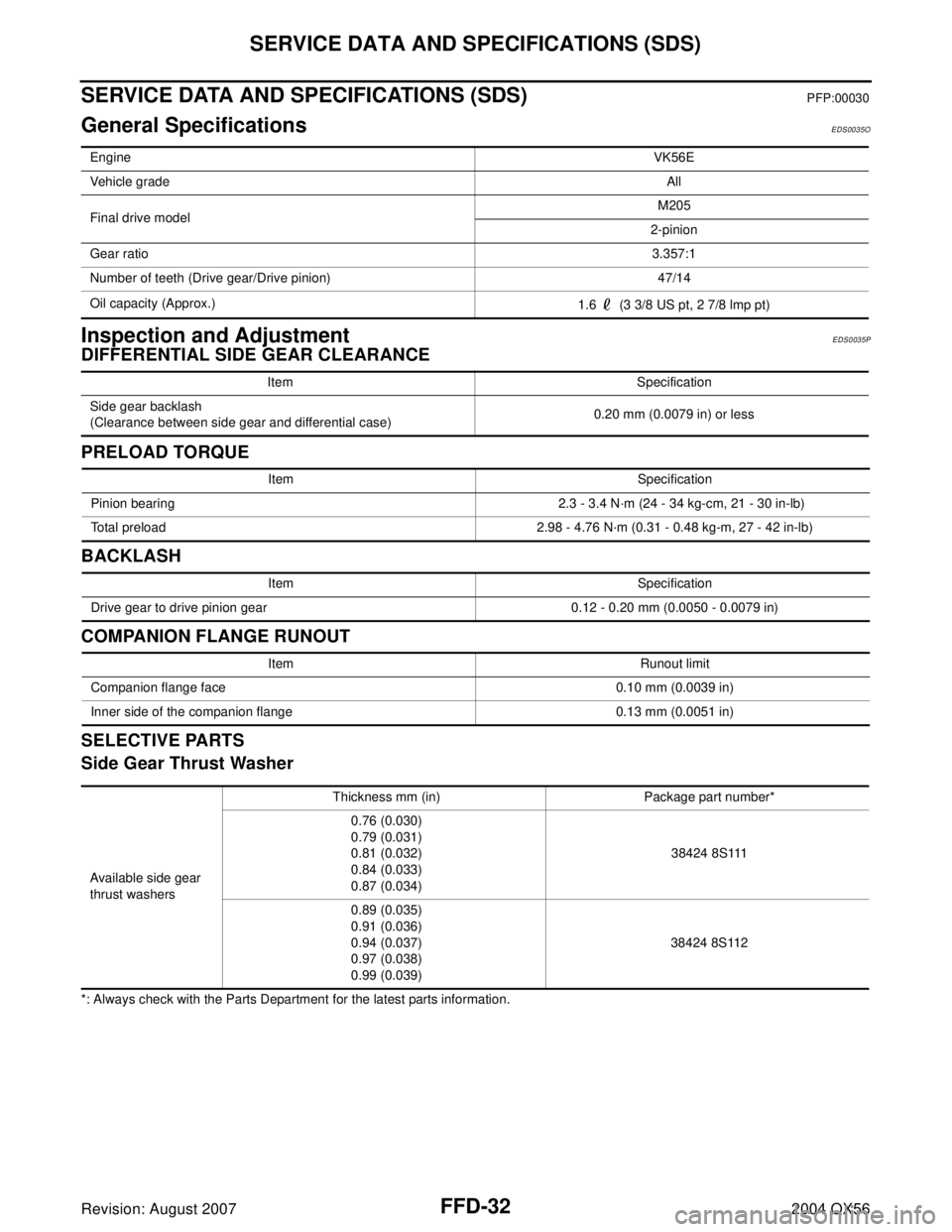
FFD-32
SERVICE DATA AND SPECIFICATIONS (SDS)
Revision: August 20072004 QX56
SERVICE DATA AND SPECIFICATIONS (SDS)PFP:00030
General SpecificationsEDS0035O
Inspection and AdjustmentEDS0035P
DIFFERENTIAL SIDE GEAR CLEARANCE
PRELOAD TORQUE
BACKLASH
COMPANION FLANGE RUNOUT
SELECTIVE PARTS
Side Gear Thrust Washer
*: Always check with the Parts Department for the latest parts information.EngineVK56E
Vehicle gradeAll
Final drive modelM205
2-pinion
Gear ratio3.357:1
Number of teeth (Drive gear/Drive pinion) 47/14
Oil capacity (Approx.)
1.6 (3 3/8 US pt, 2 7/8 lmp pt)
Item Specification
Side gear backlash
(Clearance between side gear and differential case)0.20 mm (0.0079 in) or less
Item Specification
Pinion bearing 2.3 - 3.4 N·m (24 - 34 kg-cm, 21 - 30 in-lb)
Total preload 2.98 - 4.76 N·m (0.31 - 0.48 kg-m, 27 - 42 in-lb)
Item Specification
Drive gear to drive pinion gear 0.12 - 0.20 mm (0.0050 - 0.0079 in)
Item Runout limit
Companion flange face 0.10 mm (0.0039 in)
Inner side of the companion flange 0.13 mm (0.0051 in)
Available side gear
thrust washersThickness mm (in) Package part number*
0.76 (0.030)
0.79 (0.031)
0.81 (0.032)
0.84 (0.033)
0.87 (0.034)38424 8S111
0.89 (0.035)
0.91 (0.036)
0.94 (0.037)
0.97 (0.038)
0.99 (0.039)38424 8S112
Page 2044 of 3371
SERVICE DATA AND SPECIFICATIONS (SDS)
FFD-33
C
E
F
G
H
I
J
K
L
MA
B
FFD
Revision: August 20072004 QX56
Pinion Height Adjusting Washer
*: Always check with the Parts Department for the latest parts information.Available drive pinion
height adjusting
washersThickness mm (in) Package part number*
1.22 (0.048)
1.24 (0.049)
1.27 (0.050)
1.30 (0.051)
1.32 (0.052)38154 8S111
1.35 (0.053)
1.37 (0.054)
1.40 (0.055)
1.42 (0.056)
1.45 (0.057)38154 8S112
1.47 (0.058)
1.50 (0.059)
1.52 (0.060)
1.55 (0.061)
1.57 (0.062)38154 8S113
1.60 (0.063)
1.63 (0.064)
1.65 (0.065)
1.68 (0.066)
1.70 (0.067)38154 8S114
1.73 (0.068)
1.75 (0.069)
1.78 (0.070)
1.80 (0.071)
1.83 (0.072)38154 8S115
Page 2045 of 3371
FFD-34
SERVICE DATA AND SPECIFICATIONS (SDS)
Revision: August 20072004 QX56
Page 2046 of 3371
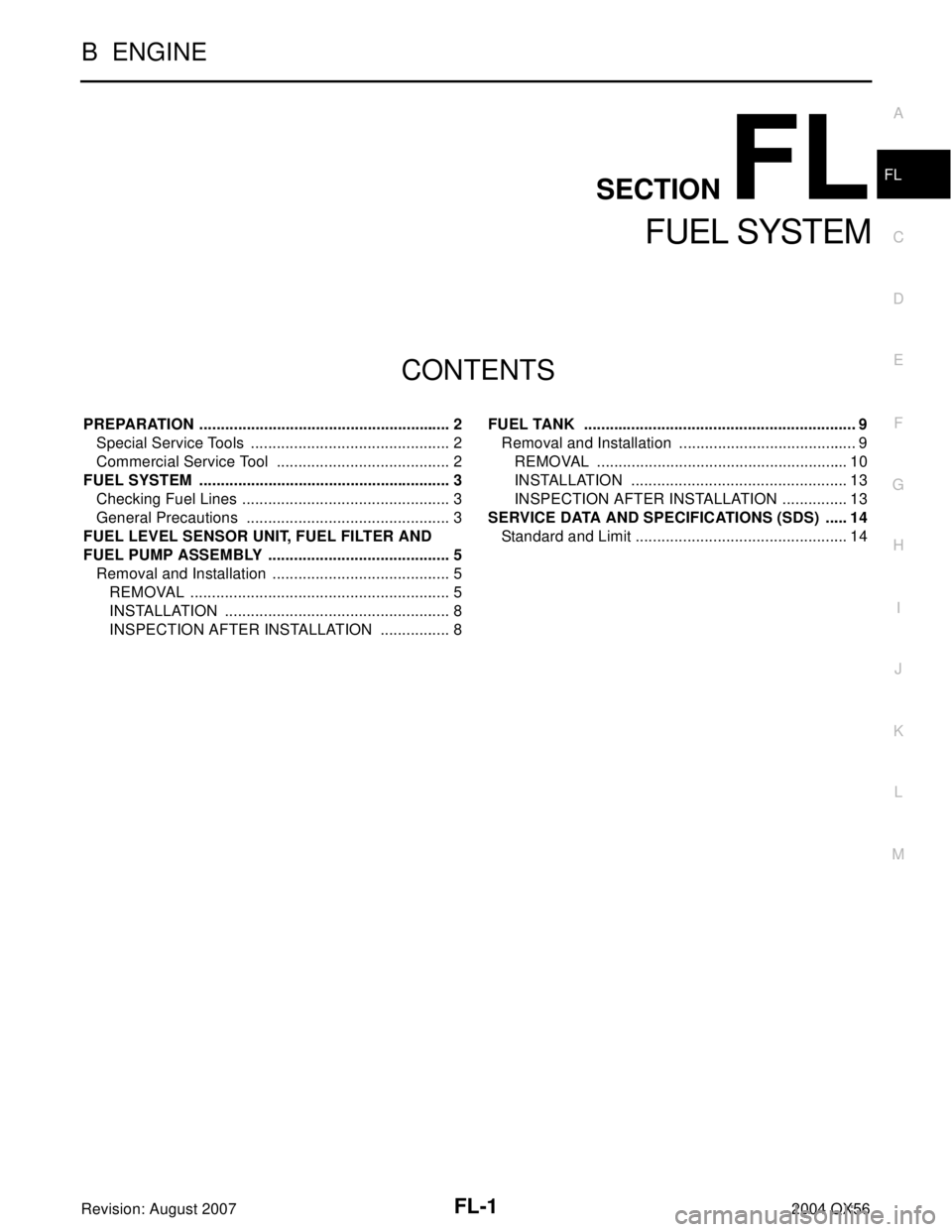
FL-1
FUEL SYSTEM
B ENGINE
CONTENTS
C
D
E
F
G
H
I
J
K
L
M
SECTION FL
A
FL
Revision: August 20072004 QX56 PREPARATION ........................................................... 2
Special Service Tools ............................................... 2
Commercial Service Tool ......................................... 2
FUEL SYSTEM ........................................................... 3
Checking Fuel Lines ................................................. 3
General Precautions ................................................ 3
FUEL LEVEL SENSOR UNIT, FUEL FILTER AND
FUEL PUMP ASSEMBLY ........................................... 5
Removal and Installation .......................................... 5
REMOVAL ............................................................. 5
INSTALLATION ..................................................... 8
INSPECTION AFTER INSTALLATION ................. 8FUEL TANK ................................................................ 9
Removal and Installation .......................................... 9
REMOVAL ........................................................... 10
INSTALLATION ................................................... 13
INSPECTION AFTER INSTALLATION ................ 13
SERVICE DATA AND SPECIFICATIONS (SDS) ...... 14
Standard and Limit .................................................. 14
Page 2047 of 3371
FL-2Revision: August 2007
PREPARATION
2004 QX56
PREPARATIONPFP:00002
Special Service ToolsEBS00IKL
The actual shapes of the Kent-Moore tools may differ from those of the special tools illustrated here.
Commercial Service ToolEBS00IKM
Tool number
(Kent-Moore No.)
Tool nameDescription
—
(J-46536)
Fuel tank lock ring toolRemoving and installing fuel tank lock ring
LBIA0398E
Tool nameDescription
Power toolLoosening bolts and nuts
PBIC0190E
Page 2048 of 3371
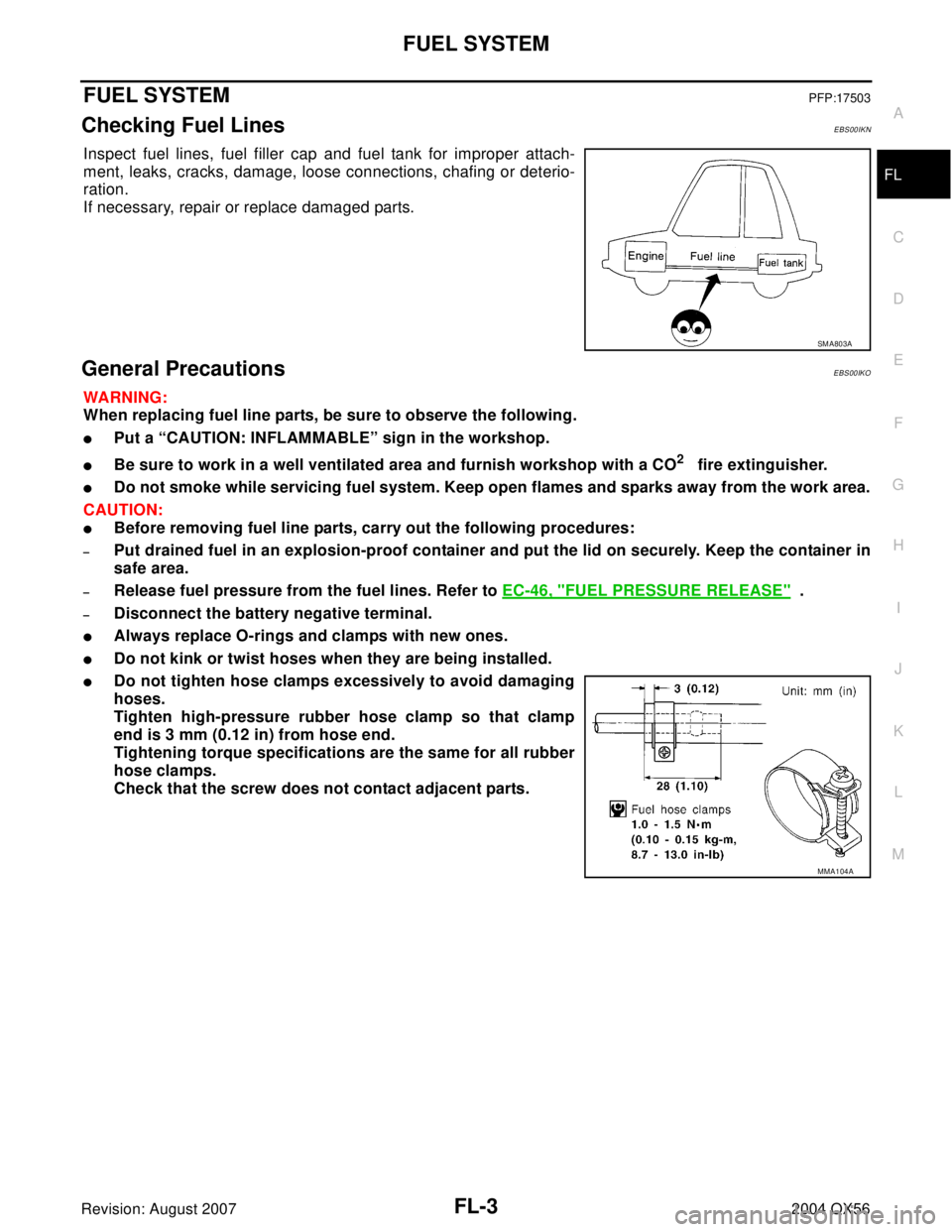
FUEL SYSTEM
FL-3
C
D
E
F
G
H
I
J
K
L
MA
FL
Revision: August 20072004 QX56
FUEL SYSTEMPFP:17503
Checking Fuel LinesEBS00IKN
Inspect fuel lines, fuel filler cap and fuel tank for improper attach-
ment, leaks, cracks, damage, loose connections, chafing or deterio-
ration.
If necessary, repair or replace damaged parts.
General PrecautionsEBS00IKO
WA RN ING:
When replacing fuel line parts, be sure to observe the following.
Put a “CAUTION: INFLAMMABLE” sign in the workshop.
Be sure to work in a well ventilated area and furnish workshop with a CO2 fire extinguisher.
Do not smoke while servicing fuel system. Keep open flames and sparks away from the work area.
CAUTION:
Before removing fuel line parts, carry out the following procedures:
–Put drained fuel in an explosion-proof container and put the lid on securely. Keep the container in
safe area.
–Release fuel pressure from the fuel lines. Refer to EC-46, "FUEL PRESSURE RELEASE" .
–Disconnect the battery negative terminal.
Always replace O-rings and clamps with new ones.
Do not kink or twist hoses when they are being installed.
Do not tighten hose clamps excessively to avoid damaging
hoses.
Tighten high-pressure rubber hose clamp so that clamp
end is 3 mm (0.12 in) from hose end.
Tightening torque specifications are the same for all rubber
hose clamps.
Check that the screw does not contact adjacent parts.
SM A80 3A
MMA104A