Page 2753 of 3371
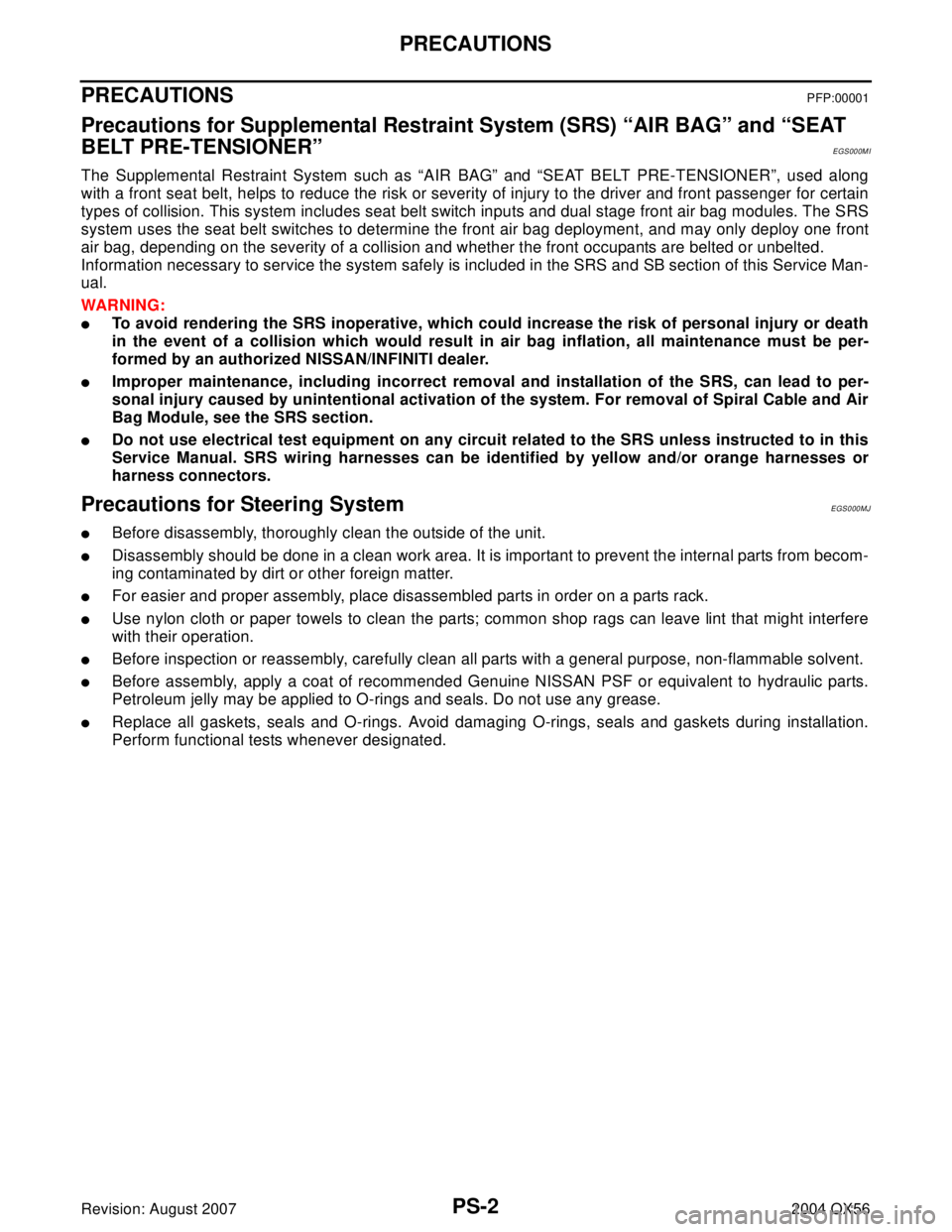
PS-2
PRECAUTIONS
Revision: August 20072004 QX56
PRECAUTIONSPFP:00001
Precautions for Supplemental Restraint System (SRS) “AIR BAG” and “SEAT
BELT PRE-TENSIONER”
EGS000MI
The Supplemental Restraint System such as “AIR BAG” and “SEAT BELT PRE-TENSIONER”, used along
with a front seat belt, helps to reduce the risk or severity of injury to the driver and front passenger for certain
types of collision. This system includes seat belt switch inputs and dual stage front air bag modules. The SRS
system uses the seat belt switches to determine the front air bag deployment, and may only deploy one front
air bag, depending on the severity of a collision and whether the front occupants are belted or unbelted.
Information necessary to service the system safely is included in the SRS and SB section of this Service Man-
ual.
WAR NIN G:
To avoid rendering the SRS inoperative, which could increase the risk of personal injury or death
in the event of a collision which would result in air bag inflation, all maintenance must be per-
formed by an authorized NISSAN/INFINITI dealer.
Improper maintenance, including incorrect removal and installation of the SRS, can lead to per-
sonal injury caused by unintentional activation of the system. For removal of Spiral Cable and Air
Bag Module, see the SRS section.
Do not use electrical test equipment on any circuit related to the SRS unless instructed to in this
Service Manual. SRS wiring harnesses can be identified by yellow and/or orange harnesses or
harness connectors.
Precautions for Steering SystemEGS000MJ
Before disassembly, thoroughly clean the outside of the unit.
Disassembly should be done in a clean work area. It is important to prevent the internal parts from becom-
ing contaminated by dirt or other foreign matter.
For easier and proper assembly, place disassembled parts in order on a parts rack.
Use nylon cloth or paper towels to clean the parts; common shop rags can leave lint that might interfere
with their operation.
Before inspection or reassembly, carefully clean all parts with a general purpose, non-flammable solvent.
Before assembly, apply a coat of recommended Genuine NISSAN PSF or equivalent to hydraulic parts.
Petroleum jelly may be applied to O-rings and seals. Do not use any grease.
Replace all gaskets, seals and O-rings. Avoid damaging O-rings, seals and gaskets during installation.
Perform functional tests whenever designated.
Page 2754 of 3371
PREPARATION
PS-3
C
D
E
F
H
I
J
K
L
MA
B
PS
Revision: August 20072004 QX56
PREPARATIONPFP:00002
Special Service Tools (SST)EGS000MK
The actual shapes of Kent-Moore tools may differ from those of special service tools illustrated here.
Tool number
(Kent-Moore No.)
Tool nameDescription
ST3127 S000
(See J-25765-A)
Preload gauge
1. GG9103000
(J25765-A)
Torque wrench
2. HT62940000
( — )
Socket adapter
3. HT62900000
( — )
Socket adapterInspecting of pinion rotating torque and rota-
tional torque for ball joint
HT72520000
(J-25730-A)
Ball joint removerRemoving steering outer socket
—
(J-46213)
Rear cover wrenchRemoving rear cover
a: 21.6 mm (0.850 in)
b: 34.9 mm (1.374 in)
KV48104400
( — )
Teflon ring correcting toolInstalling of rack Teflon ring
a: 50 mm (1.97 in) dia.
b: 36 mm (1.42 in) dia.
c: 100 mm (3.94 in)
KV48103400
( — )
Torque adapterInspecting rotational torque
S-NT541
NT146
SGIA0516E
S-NT550
ZZA0824D
Page 2755 of 3371
PS-4
PREPARATION
Revision: August 20072004 QX56
Commercial Service ToolsEGS000ML
1. KV48105300-4 and 5295262U10
( — )
Connector A and O-ring
2. KV48105300-3 and 5295262U00
( — )
Eye-bolt and O-ring
3. KV48103500
(J26357 and J26357-10)
Pressure gauge and shut-off valve
4. KV48105300-1 and 5295262U00
( — )
Connector B and O-ring
5. KV48105300-2
( — )
NutMeasuring oil pump relief pressure
KV481J0010
(J-1859A)
Steering wheel pullerRemoving steering wheel
KV481J0020
(J-42578)
Steering wheel puller legsRemoving steering wheel
KV40107300
(—)Crimping boot bands
—
(J-44372)
Spring gaugeMeasuring steering wheel turning force Tool number
(Kent-Moore No.)
Tool nameDescription
SGIA0427E
LHIA0043E
LHIA0044E
ZZA1229D
LST024
Tool nameDescription
Power toolRemoving nuts and bolts
PBIC0190E
Page 2756 of 3371
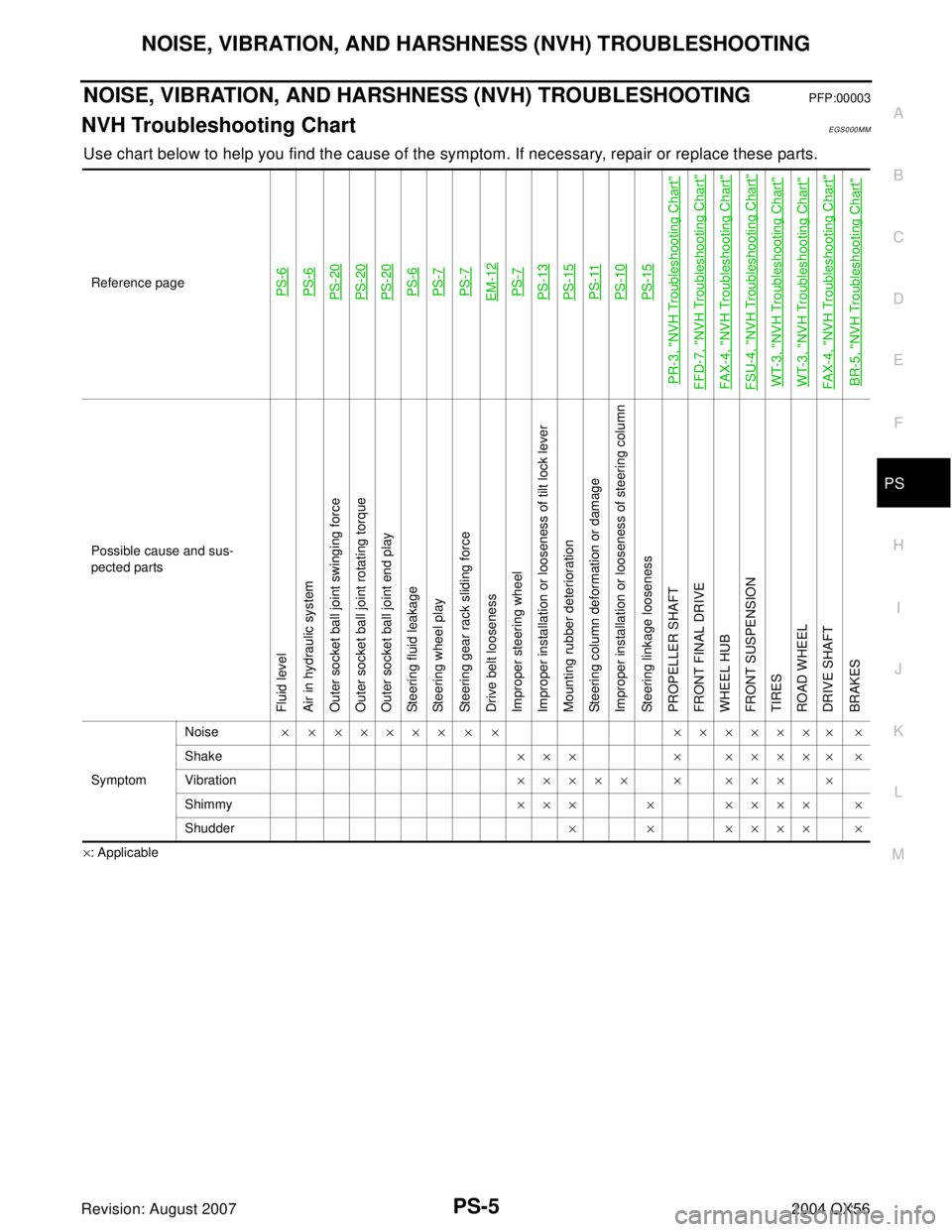
NOISE, VIBRATION, AND HARSHNESS (NVH) TROUBLESHOOTING
PS-5
C
D
E
F
H
I
J
K
L
MA
B
PS
Revision: August 20072004 QX56
NOISE, VIBRATION, AND HARSHNESS (NVH) TROUBLESHOOTINGPFP:00003
NVH Troubleshooting ChartEGS000MM
Use chart below to help you find the cause of the symptom. If necessary, repair or replace these parts.
×: ApplicableReference page
PS-6PS-6PS-20PS-20PS-20PS-6PS-7PS-7EM-12PS-7PS-13PS-15PS-11PS-10PS-15
PR-3, "
NVH Troubleshooting Chart
"
FFD-7, "
NVH Troubleshooting Chart
"
FA X-4, "
NVH Troubleshooting Chart
"
FSU-4, "
NVH Troubleshooting Chart
"
WT-3, "
NVH Troubleshooting Chart
"
WT-3, "
NVH Troubleshooting Chart
"
FA X-4, "
NVH Troubleshooting Chart
"
BR-5, "
NVH Troubleshooting Chart
"
Possible cause and sus-
pected parts
Fluid level
Air in hydraulic system
Outer socket ball joint swinging force
Outer socket ball joint rotating torque
Outer socket ball joint end play
Steering fluid leakage
Steering wheel play
Steering gear rack sliding force
Drive belt looseness
Improper steering wheel
Improper installation or looseness of tilt lock lever
Mounting rubber deterioration
Steering column deformation or damage
Improper installation or looseness of steering column
Steering linkage looseness
PROPELLER SHAFT
FRONT FINAL DRIVE
WHEEL HUB
FRONT SUSPENSION
TIRES
ROAD WHEEL
DRIVE SHAFT
BRAKES
SymptomNoise× × ××××× × × ××××××× ×
Shake××× × ××××× ×
Vibration××××× × ××× ×
Shimmy××× × ×××× ×
Shudder× × ×××× ×
Page 2757 of 3371
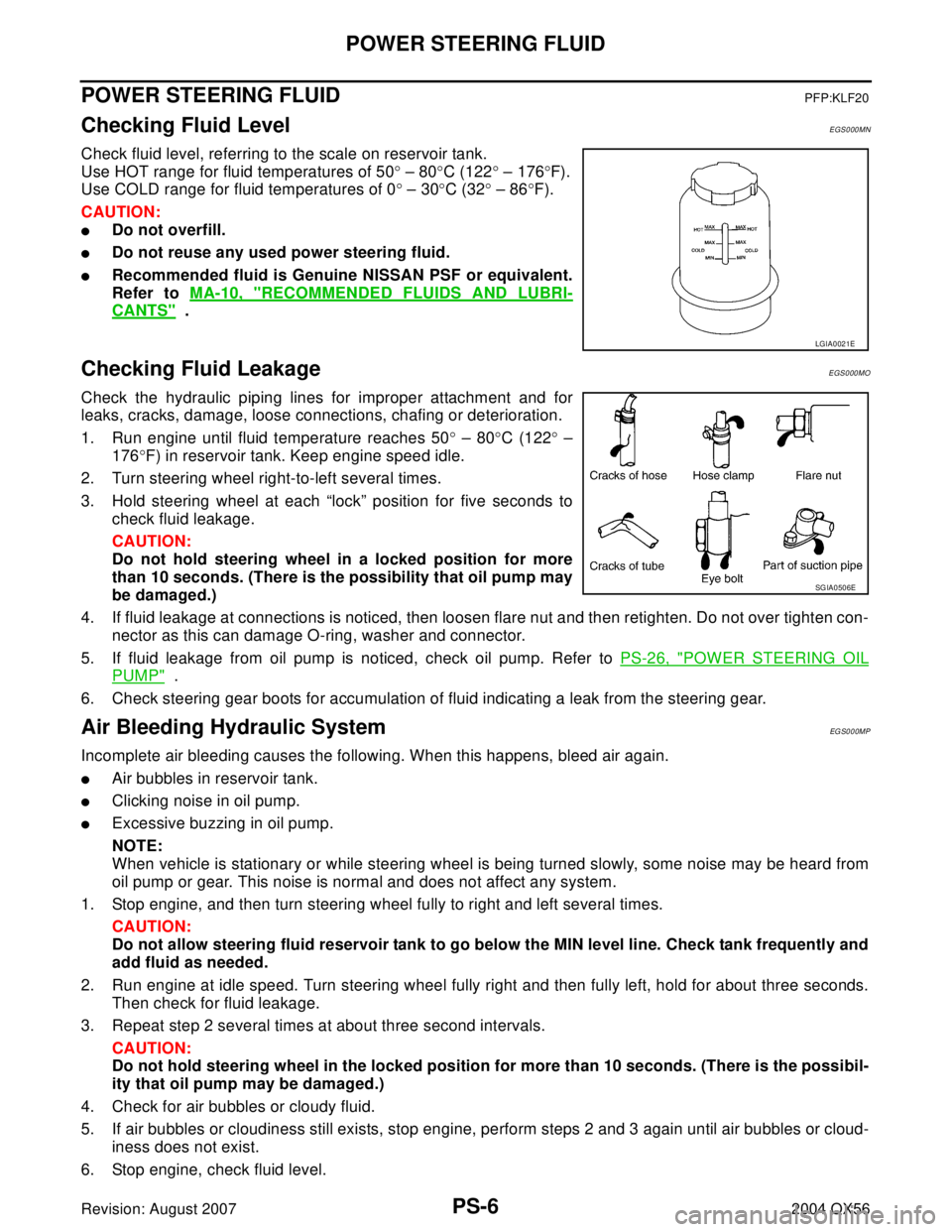
PS-6
POWER STEERING FLUID
Revision: August 20072004 QX56
POWER STEERING FLUIDPFP:KLF20
Checking Fluid LevelEGS000MN
Check fluid level, referring to the scale on reservoir tank.
Use HOT range for fluid temperatures of 50° – 80°C (122° – 176°F).
Use COLD range for fluid temperatures of 0° – 30°C (32° – 86°F).
CAUTION:
Do not overfill.
Do not reuse any used power steering fluid.
Recommended fluid is Genuine NISSAN PSF or equivalent.
Refer to MA-10, "
RECOMMENDED FLUIDS AND LUBRI-
CANTS" .
Checking Fluid LeakageEGS000MO
Check the hydraulic piping lines for improper attachment and for
leaks, cracks, damage, loose connections, chafing or deterioration.
1. Run engine until fluid temperature reaches 50° – 80°C (122° –
176°F) in reservoir tank. Keep engine speed idle.
2. Turn steering wheel right-to-left several times.
3. Hold steering wheel at each “lock” position for five seconds to
check fluid leakage.
CAUTION:
Do not hold steering wheel in a locked position for more
than 10 seconds. (There is the possibility that oil pump may
be damaged.)
4. If fluid leakage at connections is noticed, then loosen flare nut and then retighten. Do not over tighten con-
nector as this can damage O-ring, washer and connector.
5. If fluid leakage from oil pump is noticed, check oil pump. Refer to PS-26, "
POWER STEERING OIL
PUMP" .
6. Check steering gear boots for accumulation of fluid indicating a leak from the steering gear.
Air Bleeding Hydraulic SystemEG S0 0 0MP
Incomplete air bleeding causes the following. When this happens, bleed air again.
Air bubbles in reservoir tank.
Clicking noise in oil pump.
Excessive buzzing in oil pump.
NOTE:
When vehicle is stationary or while steering wheel is being turned slowly, some noise may be heard from
oil pump or gear. This noise is normal and does not affect any system.
1. Stop engine, and then turn steering wheel fully to right and left several times.
CAUTION:
Do not allow steering fluid reservoir tank to go below the MIN level line. Check tank frequently and
add fluid as needed.
2. Run engine at idle speed. Turn steering wheel fully right and then fully left, hold for about three seconds.
Then check for fluid leakage.
3. Repeat step 2 several times at about three second intervals.
CAUTION:
Do not hold steering wheel in the locked position for more than 10 seconds. (There is the possibil-
ity that oil pump may be damaged.)
4. Check for air bubbles or cloudy fluid.
5. If air bubbles or cloudiness still exists, stop engine, perform steps 2 and 3 again until air bubbles or cloud-
iness does not exist.
6. Stop engine, check fluid level.
LGIA0021E
SGIA0506E
Page 2758 of 3371
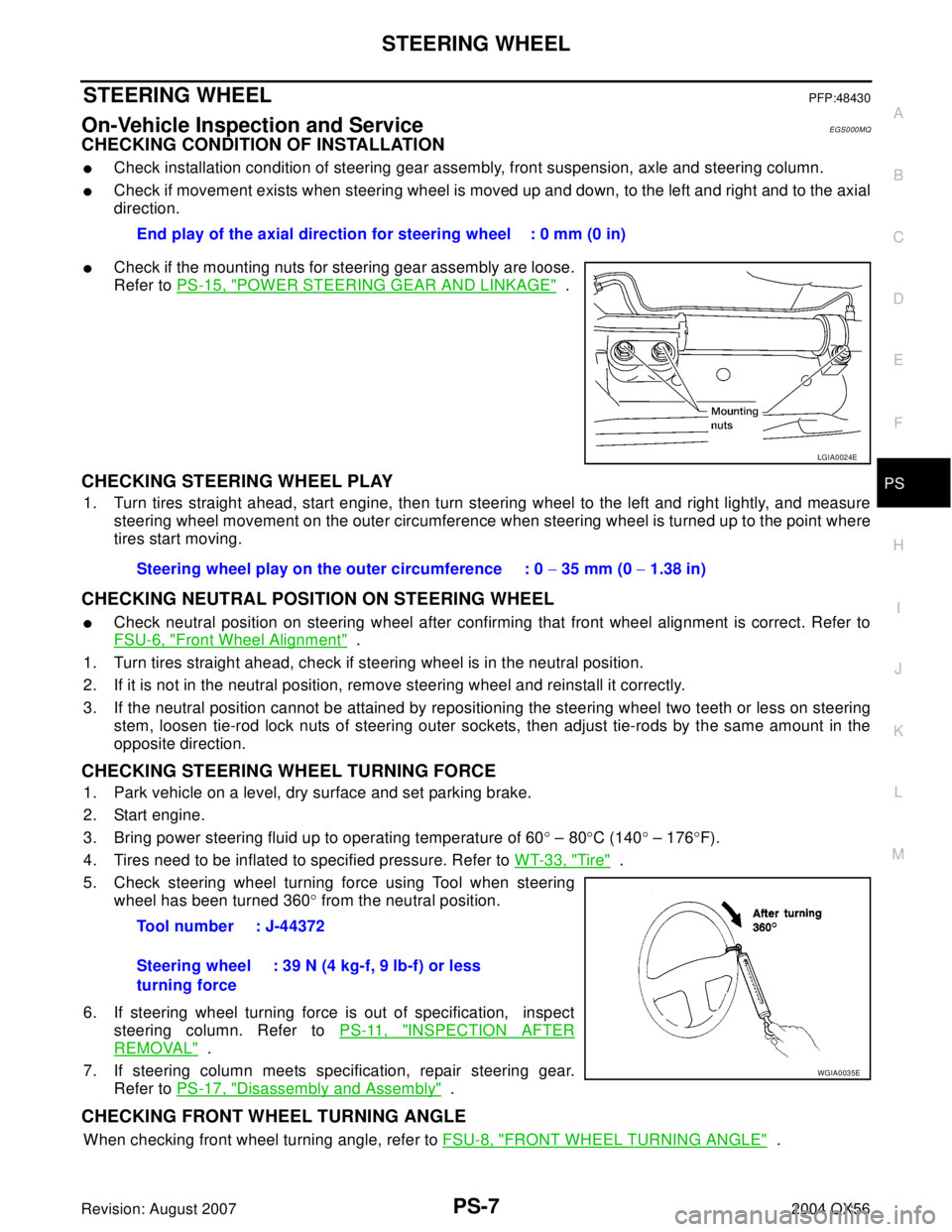
STEERING WHEEL
PS-7
C
D
E
F
H
I
J
K
L
MA
B
PS
Revision: August 20072004 QX56
STEERING WHEELPFP:48430
On-Vehicle Inspection and ServiceEGS000MQ
CHECKING CONDITION OF INSTALLATION
Check installation condition of steering gear assembly, front suspension, axle and steering column.
Check if movement exists when steering wheel is moved up and down, to the left and right and to the axial
direction.
Check if the mounting nuts for steering gear assembly are loose.
Refer to PS-15, "
POWER STEERING GEAR AND LINKAGE" .
CHECKING STEERING WHEEL PLAY
1. Turn tires straight ahead, start engine, then turn steering wheel to the left and right lightly, and measure
steering wheel movement on the outer circumference when steering wheel is turned up to the point where
tires start moving.
CHECKING NEUTRAL POSITION ON STEERING WHEEL
Check neutral position on steering wheel after confirming that front wheel alignment is correct. Refer to
FSU-6, "
Front Wheel Alignment" .
1. Turn tires straight ahead, check if steering wheel is in the neutral position.
2. If it is not in the neutral position, remove steering wheel and reinstall it correctly.
3. If the neutral position cannot be attained by repositioning the steering wheel two teeth or less on steering
stem, loosen tie-rod lock nuts of steering outer sockets, then adjust tie-rods by the same amount in the
opposite direction.
CHECKING STEERING WHEEL TURNING FORCE
1. Park vehicle on a level, dry surface and set parking brake.
2. Start engine.
3. Bring power steering fluid up to operating temperature of 60° – 80°C (140° – 176°F).
4. Tires need to be inflated to specified pressure. Refer to WT-33, "
Tire" .
5. Check steering wheel turning force using Tool when steering
wheel has been turned 360° from the neutral position.
6. If steering wheel turning force is out of specification, inspect
steering column. Refer to PS-11, "
INSPECTION AFTER
REMOVAL" .
7. If steering column meets specification, repair steering gear.
Refer to PS-17, "
Disassembly and Assembly" .
CHECKING FRONT WHEEL TURNING ANGLE
When checking front wheel turning angle, refer to FSU-8, "FRONT WHEEL TURNING ANGLE" . End play of the axial direction for steering wheel : 0 mm (0 in)
LGIA0024E
Steering wheel play on the outer circumference : 0 − 35 mm (0 − 1.38 in)
Tool number : J-44372
Steering wheel
turning force: 39 N (4 kg-f, 9 lb-f) or less
WGIA0035E
Page 2759 of 3371
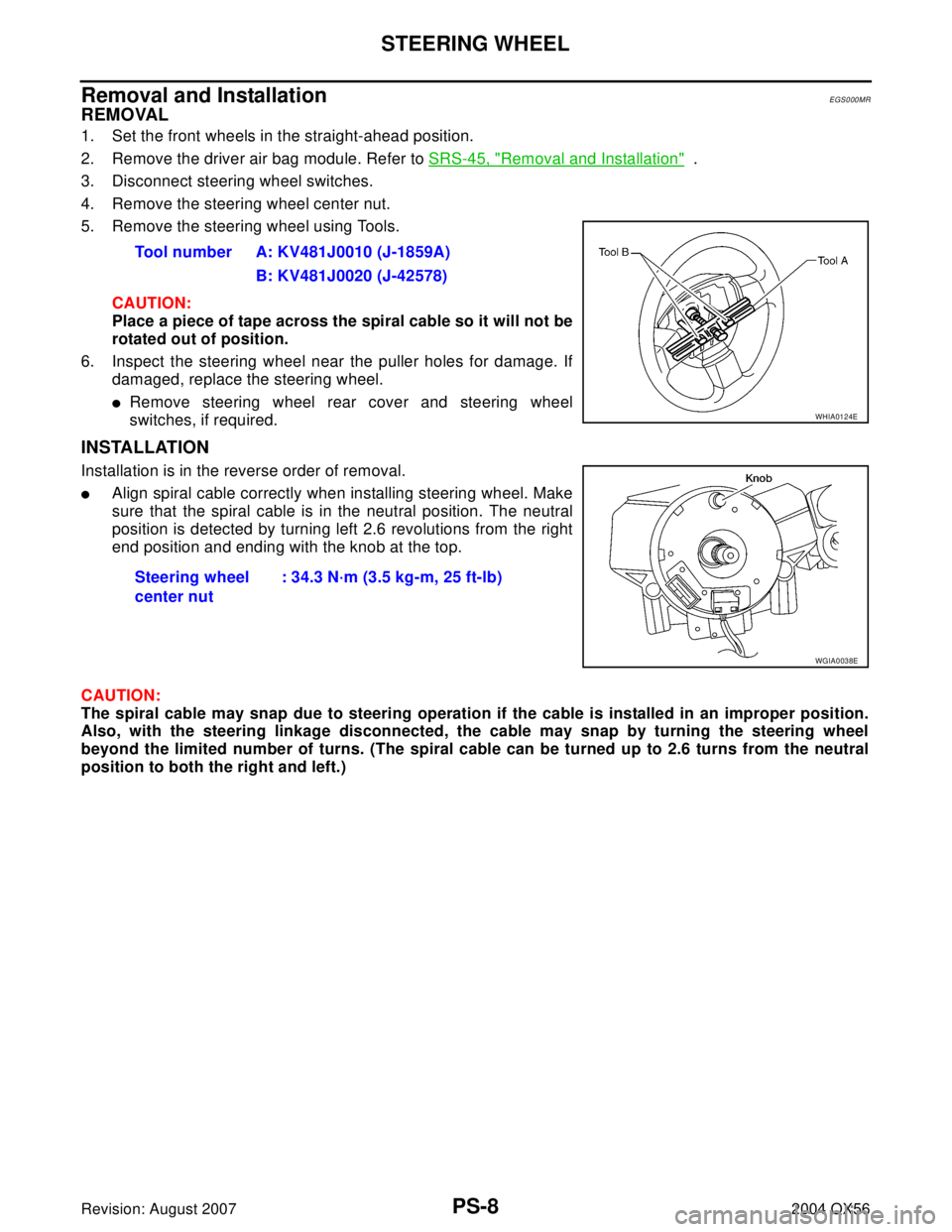
PS-8
STEERING WHEEL
Revision: August 20072004 QX56
Removal and InstallationEGS000MR
REMOVAL
1. Set the front wheels in the straight-ahead position.
2. Remove the driver air bag module. Refer to SRS-45, "
Removal and Installation" .
3. Disconnect steering wheel switches.
4. Remove the steering wheel center nut.
5. Remove the steering wheel using Tools.
CAUTION:
Place a piece of tape across the spiral cable so it will not be
rotated out of position.
6. Inspect the steering wheel near the puller holes for damage. If
damaged, replace the steering wheel.
Remove steering wheel rear cover and steering wheel
switches, if required.
INSTALLATION
Installation is in the reverse order of removal.
Align spiral cable correctly when installing steering wheel. Make
sure that the spiral cable is in the neutral position. The neutral
position is detected by turning left 2.6 revolutions from the right
end position and ending with the knob at the top.
CAUTION:
The spiral cable may snap due to steering operation if the cable is installed in an improper position.
Also, with the steering linkage disconnected, the cable may snap by turning the steering wheel
beyond the limited number of turns. (The spiral cable can be turned up to 2.6 turns from the neutral
position to both the right and left.)Tool number A: KV481J0010 (J-1859A)
B: KV481J0020 (J-42578)
WHIA0124E
Steering wheel
center nut : 34.3 N·m (3.5 kg-m, 25 ft-lb)
WGIA0038E
Page 2760 of 3371
TILT SYSTEM
PS-9
C
D
E
F
H
I
J
K
L
MA
B
PS
Revision: August 20072004 QX56
TILT SYSTEMPFP:48810
Removal and InstallationEGS000N8
TILT MOTOR AND TILT SENSOR
Removal
1. Remove the steering column cover and lower driver instrument panel. Refer to IP-10, "INSTRUMENT
PANEL ASSEMBLY" .
2. Remove knee protector.
3. Disconnect the tilt sensor electrical connector.
4. Remove the two tilt sensor screws and the tilt sensor.
5. Disconnect the tilt motor electrical connector.
6. Remove the tilt motor bolt and the tilt motor.
Installation
Installation is in reverse order of removal.
NOTE:
Make sure the tab in the tilt sensor is engaged in the bracket on the tilt motor.
LGIA0022E
1. Tilt sensor 2. Tilt motor
LGIA0026E