Page 2073 of 3371
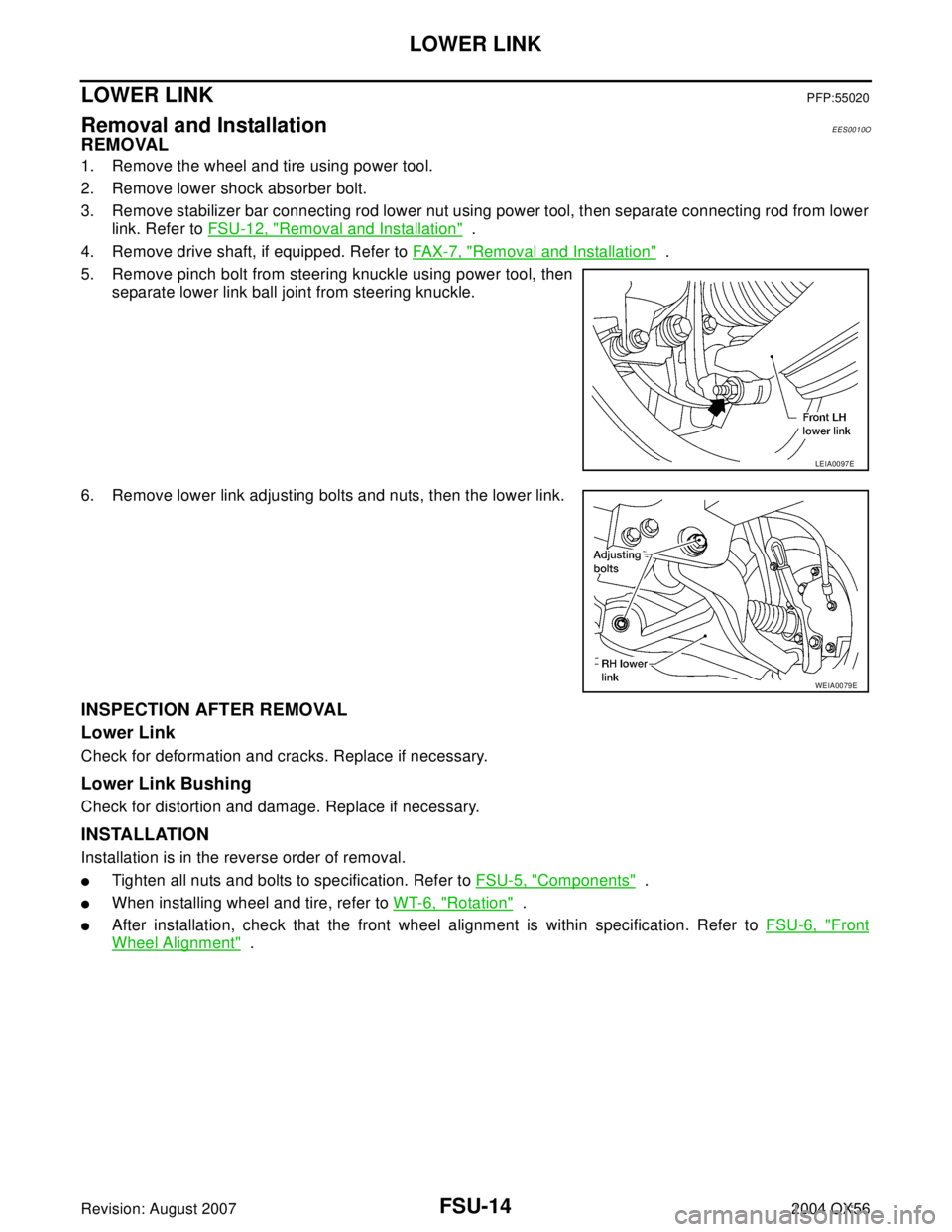
FSU-14
LOWER LINK
Revision: August 20072004 QX56
LOWER LINKPFP:55020
Removal and InstallationEES0010O
REMOVAL
1. Remove the wheel and tire using power tool.
2. Remove lower shock absorber bolt.
3. Remove stabilizer bar connecting rod lower nut using power tool, then separate connecting rod from lower
link. Refer to FSU-12, "
Removal and Installation" .
4. Remove drive shaft, if equipped. Refer to FAX-7, "
Removal and Installation" .
5. Remove pinch bolt from steering knuckle using power tool, then
separate lower link ball joint from steering knuckle.
6. Remove lower link adjusting bolts and nuts, then the lower link.
INSPECTION AFTER REMOVAL
Lower Link
Check for deformation and cracks. Replace if necessary.
Lower Link Bushing
Check for distortion and damage. Replace if necessary.
INSTALLATION
Installation is in the reverse order of removal.
Tighten all nuts and bolts to specification. Refer to FSU-5, "Components" .
When installing wheel and tire, refer to WT-6, "Rotation" .
After installation, check that the front wheel alignment is within specification. Refer to FSU-6, "Front
Wheel Alignment" .
LEIA0097E
WEIA0079E
Page 2074 of 3371
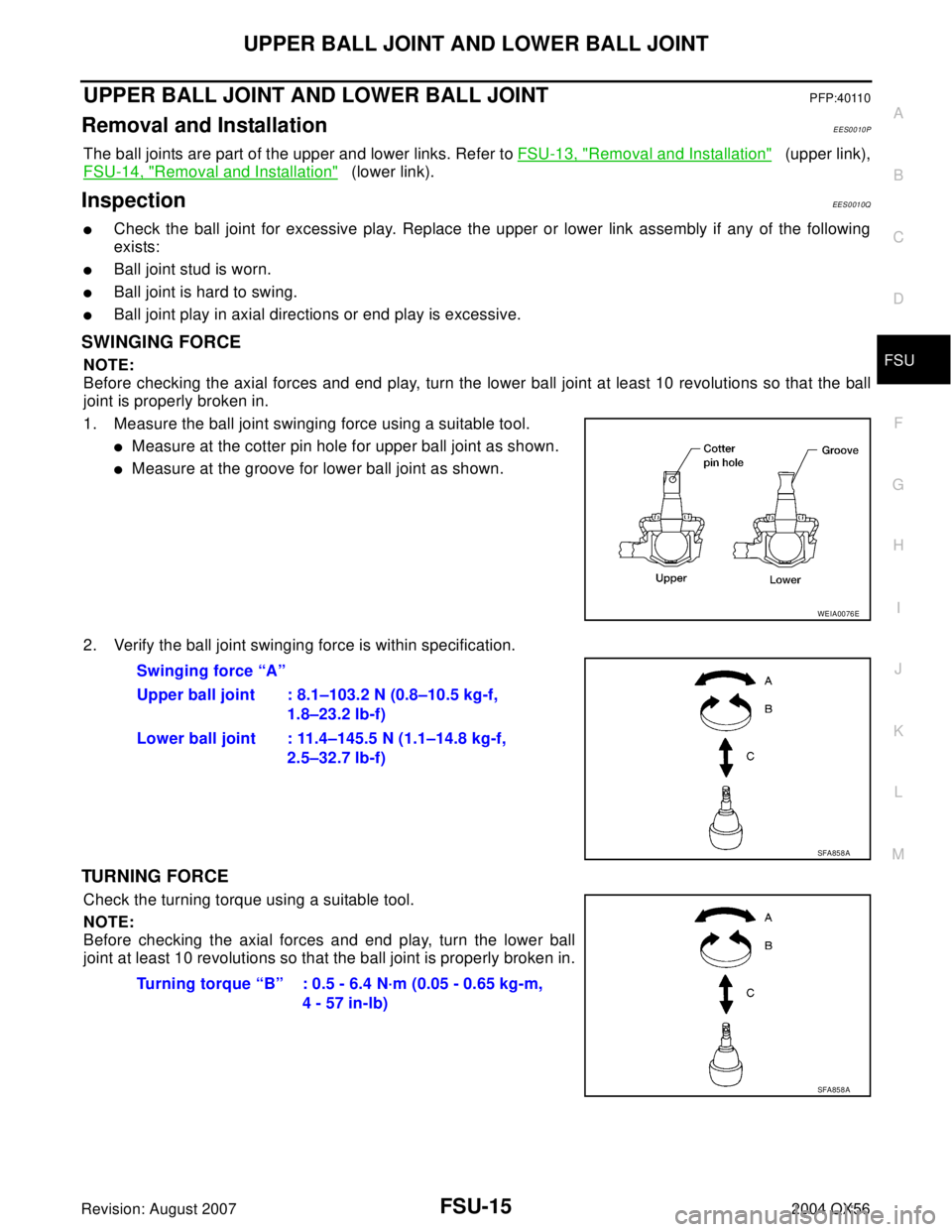
UPPER BALL JOINT AND LOWER BALL JOINT
FSU-15
C
D
F
G
H
I
J
K
L
MA
B
FSU
Revision: August 20072004 QX56
UPPER BALL JOINT AND LOWER BALL JOINTPFP:40110
Removal and InstallationEES0010P
The ball joints are part of the upper and lower links. Refer to FSU-13, "Removal and Installation" (upper link),
FSU-14, "
Removal and Installation" (lower link).
InspectionEES0010Q
Check the ball joint for excessive play. Replace the upper or lower link assembly if any of the following
exists:
Ball joint stud is worn.
Ball joint is hard to swing.
Ball joint play in axial directions or end play is excessive.
SWINGING FORCE
NOTE:
Before checking the axial forces and end play, turn the lower ball joint at least 10 revolutions so that the ball
joint is properly broken in.
1. Measure the ball joint swinging force using a suitable tool.
Measure at the cotter pin hole for upper ball joint as shown.
Measure at the groove for lower ball joint as shown.
2. Verify the ball joint swinging force is within specification.
TURNING FORCE
Check the turning torque using a suitable tool.
NOTE:
Before checking the axial forces and end play, turn the lower ball
joint at least 10 revolutions so that the ball joint is properly broken in.
WEIA0076E
Swinging force “A”
Upper ball joint : 8.1–103.2 N (0.8–10.5 kg-f,
1.8–23.2 lb-f)
Lower ball joint : 11.4–145.5 N (1.1–14.8 kg-f,
2.5–32.7 lb-f)
SFA858A
Turning torque “B” : 0.5 - 6.4 N·m (0.05 - 0.65 kg-m,
4 - 57 in-lb)
SFA858A
Page 2075 of 3371
FSU-16
UPPER BALL JOINT AND LOWER BALL JOINT
Revision: August 20072004 QX56
VERTICAL END PLAY
Measure the vertical end play using a suitable tool.
Check dust cover for damage. Replace it and the cover clamp if
necessary.
NOTE:
Before checking the axial forces and end play, turn the lower ball
joint at least 10 revolutions so that the ball joint is properly broken in.
Vertical end play “C” : 0 mm (0 in)
SFA858A
Page 2076 of 3371
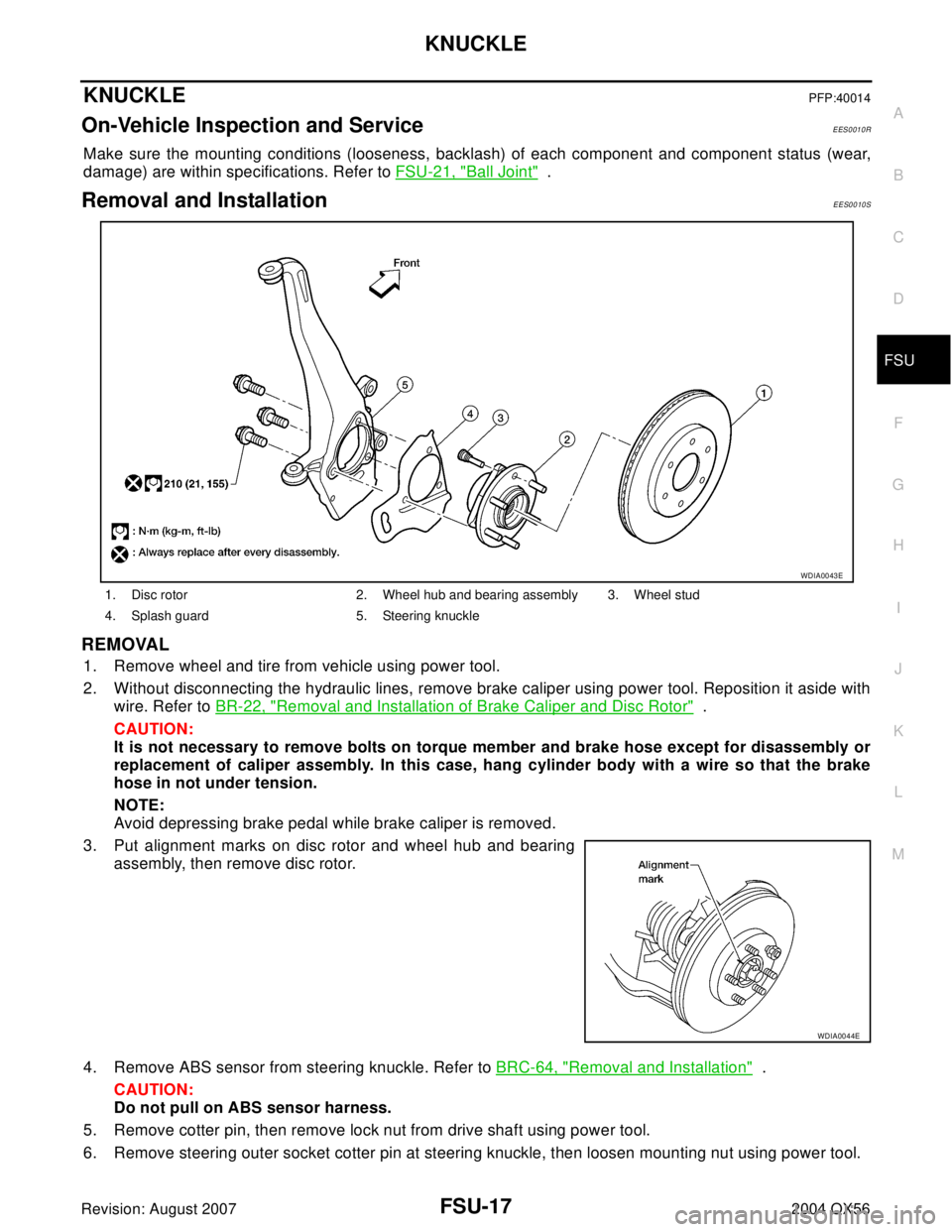
KNUCKLE
FSU-17
C
D
F
G
H
I
J
K
L
MA
B
FSU
Revision: August 20072004 QX56
KNUCKLEPFP:40014
On-Vehicle Inspection and ServiceEES0010R
Make sure the mounting conditions (looseness, backlash) of each component and component status (wear,
damage) are within specifications. Refer to FSU-21, "
Ball Joint" .
Removal and InstallationEES0010S
REMOVAL
1. Remove wheel and tire from vehicle using power tool.
2. Without disconnecting the hydraulic lines, remove brake caliper using power tool. Reposition it aside with
wire. Refer to BR-22, "
Removal and Installation of Brake Caliper and Disc Rotor" .
CAUTION:
It is not necessary to remove bolts on torque member and brake hose except for disassembly or
replacement of caliper assembly. In this case, hang cylinder body with a wire so that the brake
hose in not under tension.
NOTE:
Avoid depressing brake pedal while brake caliper is removed.
3. Put alignment marks on disc rotor and wheel hub and bearing
assembly, then remove disc rotor.
4. Remove ABS sensor from steering knuckle. Refer to BRC-64, "
Removal and Installation" .
CAUTION:
Do not pull on ABS sensor harness.
5. Remove cotter pin, then remove lock nut from drive shaft using power tool.
6. Remove steering outer socket cotter pin at steering knuckle, then loosen mounting nut using power tool.
1. Disc rotor 2. Wheel hub and bearing assembly 3. Wheel stud
4. Splash guard 5. Steering knuckle
WDIA0043E
WDIA0044E
Page 2077 of 3371
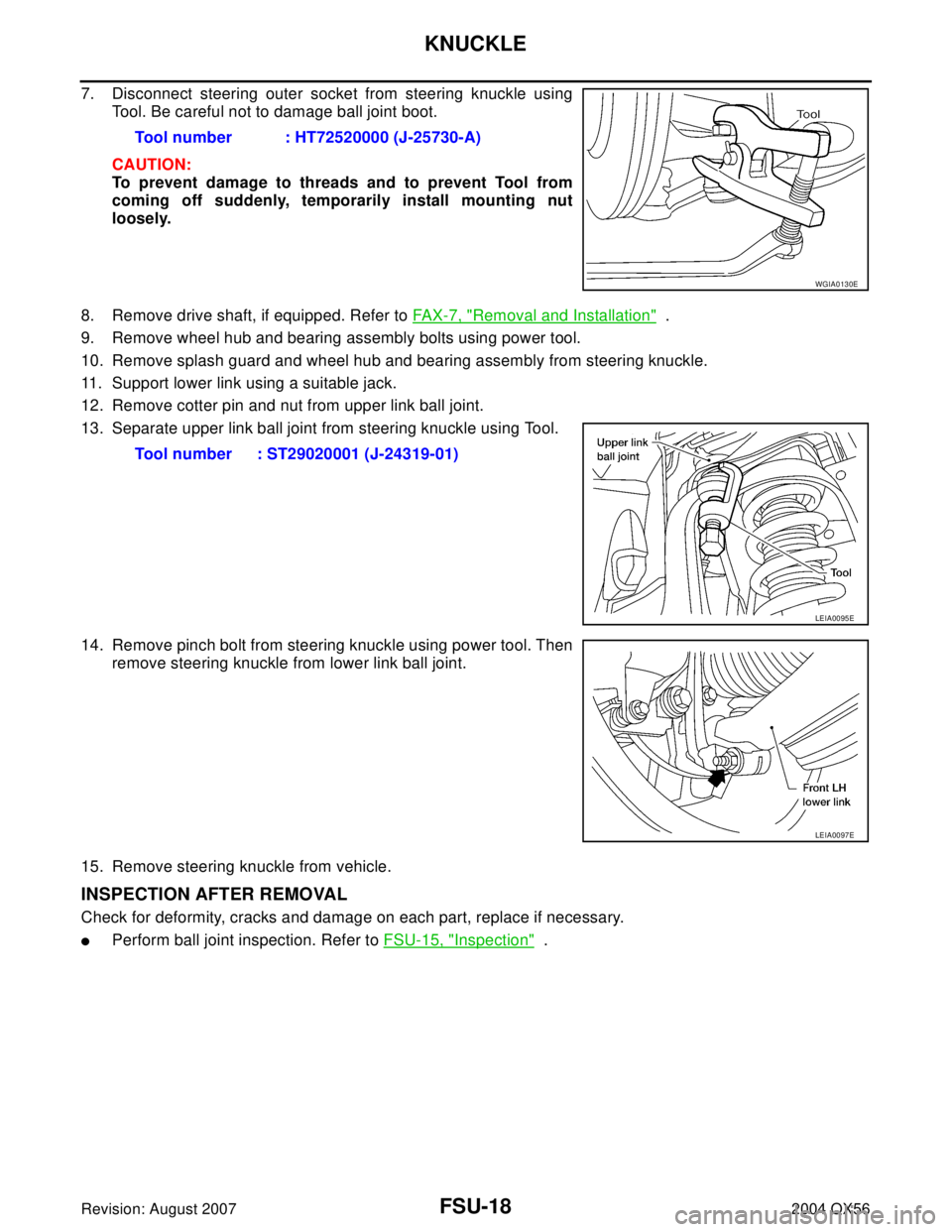
FSU-18
KNUCKLE
Revision: August 20072004 QX56
7. Disconnect steering outer socket from steering knuckle using
Tool. Be careful not to damage ball joint boot.
CAUTION:
To prevent damage to threads and to prevent Tool from
coming off suddenly, temporarily install mounting nut
loosely.
8. Remove drive shaft, if equipped. Refer to FAX-7, "
Removal and Installation" .
9. Remove wheel hub and bearing assembly bolts using power tool.
10. Remove splash guard and wheel hub and bearing assembly from steering knuckle.
11. Support lower link using a suitable jack.
12. Remove cotter pin and nut from upper link ball joint.
13. Separate upper link ball joint from steering knuckle using Tool.
14. Remove pinch bolt from steering knuckle using power tool. Then
remove steering knuckle from lower link ball joint.
15. Remove steering knuckle from vehicle.
INSPECTION AFTER REMOVAL
Check for deformity, cracks and damage on each part, replace if necessary.
Perform ball joint inspection. Refer to FSU-15, "Inspection" . Tool number : HT72520000 (J-25730-A)
WGIA0130E
Tool number : ST29020001 (J-24319-01)
LEIA0095E
LEIA0097E
Page 2078 of 3371
KNUCKLE
FSU-19
C
D
F
G
H
I
J
K
L
MA
B
FSU
Revision: August 20072004 QX56
INSTALLATION
Installation is in the reverse order of removal.
Refer to FSU-5, "Components" for tightening torques.
When installing disc rotor on wheel hub and bearing assembly,
align the marks.
(When not using the alignment mark, refer to BR-25, "
DISC
ROTOR INSPECTION" .)
When installing wheel and tire, refer to WT-6, "Rotation" .
WDIA0044E
Page 2079 of 3371
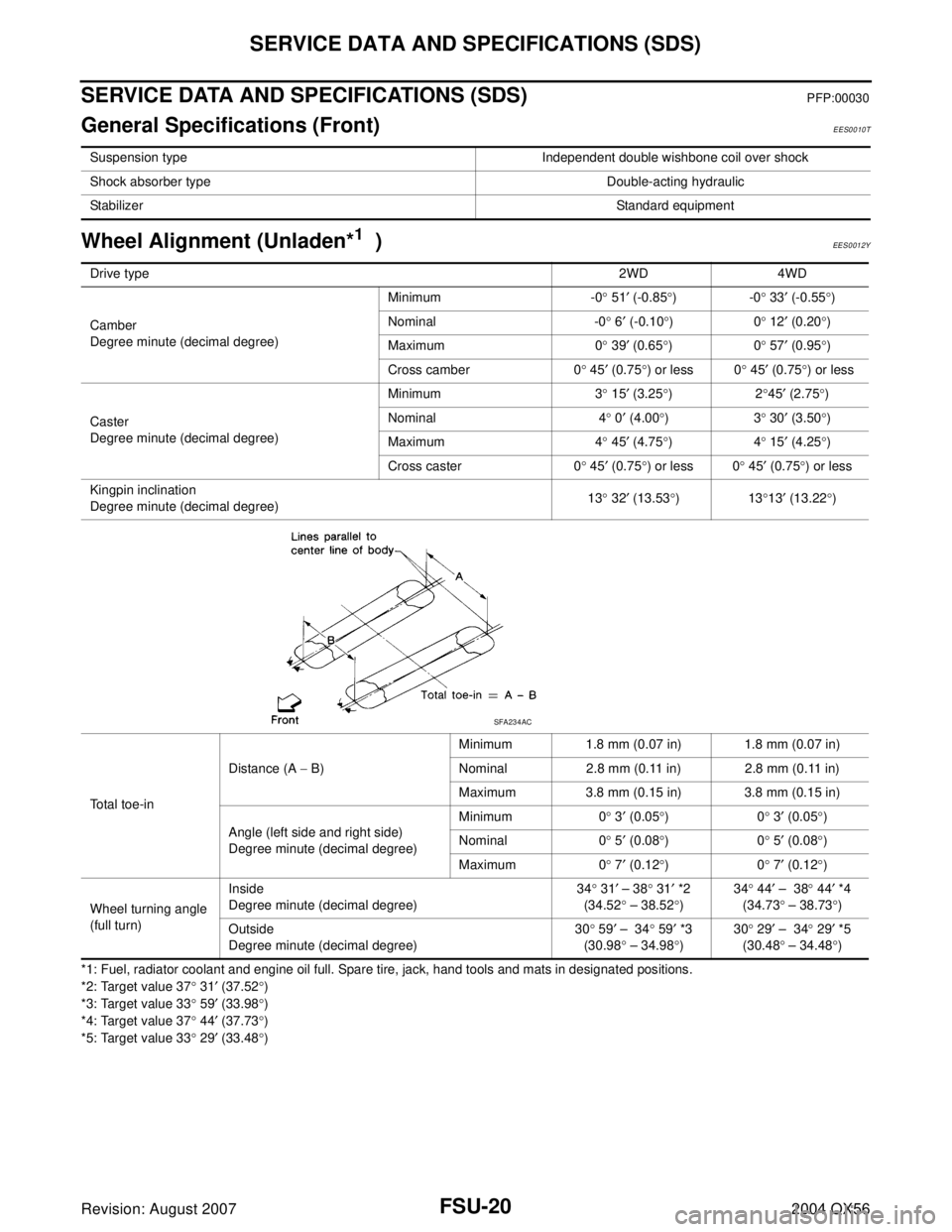
FSU-20
SERVICE DATA AND SPECIFICATIONS (SDS)
Revision: August 20072004 QX56
SERVICE DATA AND SPECIFICATIONS (SDS)PFP:00030
General Specifications (Front)EES0010T
Wheel Alignment (Unladen*1 )EES0012Y
*1: Fuel, radiator coolant and engine oil full. Spare tire, jack, hand tools and mats in designated positions.
*2: Target value 37° 31′ (37.52°)
*3: Target value 33° 59′ (33.98°)
*4: Target value 37° 44′ (37.73°)
*5: Target value 33° 29′ (33.48°) Suspension type Independent double wishbone coil over shock
Shock absorber type Double-acting hydraulic
StabilizerStandard equipment
Drive type2WD 4WD
Camber
Degree minute (decimal degree)Minimum -0° 51′ (-0.85°)-0° 33′ (-0.55°)
Nominal -0° 6′ (-0.10°)0° 12′ (0.20°)
Maximum 0° 39′ (0.65°)0° 57′ (0.95°)
Cross camber 0° 45′ (0.75°) or less 0° 45′ (0.75°) or less
Caster
Degree minute (decimal degree)Minimum 3° 15′ (3.25°)2°45′ (2.75°)
Nominal 4° 0′ (4.00°)3° 30′ (3.50°)
Maximum 4° 45′ (4.75°)4° 15′ (4.25°)
Cross caster 0° 45′ (0.75°) or less 0° 45′ (0.75°) or less
Kingpin inclination
Degree minute (decimal degree)13° 32′ (13.53°)13°13′ (13.22°)
Total toe-inDistance (A − B)Minimum 1.8 mm (0.07 in) 1.8 mm (0.07 in)
Nominal 2.8 mm (0.11 in) 2.8 mm (0.11 in)
Maximum 3.8 mm (0.15 in) 3.8 mm (0.15 in)
Angle (left side and right side)
Degree minute (decimal degree)Minimum 0° 3′ (0.05°)0° 3′ (0.05°)
Nominal 0° 5′ (0.08°)0° 5′ (0.08°)
Maximum 0° 7′ (0.12°)0° 7′ (0.12°)
Wheel turning angle
(full turn)Inside
Degree minute (decimal degree)34° 31′ – 38° 31′ *2
(34.52° – 38.52°)34° 44′ – 38° 44′ *4
(34.73° – 38.73°)
Outside
Degree minute (decimal degree)30° 59′ – 34° 59′ *3
(30.98° – 34.98°)30° 29′ – 34° 29′ *5
(30.48° – 34.48°)
SFA234AC
Page 2080 of 3371
SERVICE DATA AND SPECIFICATIONS (SDS)
FSU-21
C
D
F
G
H
I
J
K
L
MA
B
FSU
Revision: August 20072004 QX56
Ball JointEES0013H
*1 Measure at cotter pin hole
*2 Measure at groove
Wheelarch Height (Unladen*1 )EES0010W
Unit: mm (in)
*1: Fuel, radiator coolant and engine oil full. Spare tire, jack, hand tools and mats in designated positions.
*2: Confirm level using Consult-II, register 1103. Set rear wheel arch height to “0” if necessary.Swinging force “A”Upper ball joint 8.1 – 103.2 N (0.8 – 10.5 kg-f, 1.8 – 23.2 lb-f) *1
Lower ball joint 11.4 – 145.5 N (1.1 – 14.8 kg-f, 2.5 – 32.7 lb-f) *2
Turning torque “B” 0.5 - 6.4 N·m (0.05 - 0.65 kg-m, 4 - 57 in-lb)
Vertical end play “C”0 mm (0 in)
SFA858AWEIA0076E
Suspension type
Air leveling*2
Applied model 2WD 4WD
Front wheelarch height (Hf)913
(35.94)931
(36.65)
Rear wheelarch height (Hr)912
(35.91)932
(36.69)
LEIA0085E